Home > Potting Compound > Connector Potting Compound
Connector Potting Compound
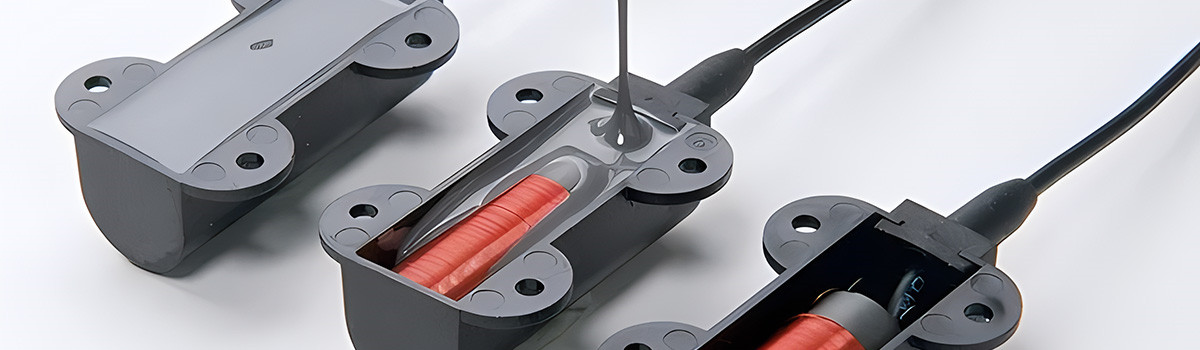
In the realm of electrical engineering and manufacturing, the significance of connector potting compound cannot be overstated. This versatile material plays a pivotal role in safeguarding electrical connections against environmental hazards while enhancing their durability and reliability. In this comprehensive guide, we delve into the depths of connector potting compound, examining its composition, applications, benefits, and key considerations.
Table of Contents
ToggleWhat is Connector Potting Compound?
The connector potting compound is a specialized material used in electrical engineering to protect and stabilize electrical connections. It is a sealant that fills the voids and gaps around connectors, wires, and other electrical components. This compound is typically made of epoxy resin, silicone, or polyurethane, each offering unique properties suited for different applications.
The primary function of connector potting compound is to safeguard electrical connections from environmental factors such as moisture, dust, chemicals, and vibrations. By enclosing the connection, you lower the chance of corrosion, short circuits, and other types of damage by constructing a barrier that keeps impurities out.
One of its main benefits is the capacity of connector potting compounds to improve the mechanical stability of electrical connections. Encasing the components in a solid, protective material prevents them from shifting or coming loose due to external forces such as vibrations or mechanical stress. It ensures the integrity of the connection and prolongs the lifespan of the entire electrical system.
Furthermore, connector potting compounds can improve the thermal conductivity of electrical connections, aiding in heat dissipation and temperature management. It is especially crucial in high-performance applications where excessive heat buildup can degrade the performance or even cause failure of electronic components.
The versatility of connector potting compound extends to its compatibility with various types of connectors and substrates. Potting compounds can be customized to meet the unique needs of multiple applications, regardless of whether the connections are wire-to-wire, wire-to-board, or board-to-board. It can also be customized to adhere to other surfaces such as metals, plastics, or ceramics, ensuring optimal performance and reliability.
Connector potting compounds not only reduce electrical equipment size but also provide stabilizing and protective properties. Eliminating the need for bulky enclosures or housings allows for more compact designs without compromising performance or safety.
Overall, connector potting compounds ensure electrical connections’ reliability, durability, and performance in various applications. From consumer electronics to industrial machinery, its ability to provide protection against environmental hazards and enhance mechanical stability makes it an essential component in modern electrical engineering.
How Does Connector Potting Compound Work?
Connector potting compound is a versatile material used in various industries to protect, provide insulation, and stabilize electrical connectors. Understanding its functionality is crucial for ensuring the reliability and durability of electronic devices and systems. Let’s explore how connector potting compounds work and their significance in different applications.
Key Characteristics:
- Thermal Conductivity:High thermal conductivity is a common feature of connector potting materials, facilitating effective heat dissipation from electronic components.
- Electrical Insulation:They possess excellent electrical insulation properties, safeguarding connectors against short circuits and other electrical failures.
- Chemical Resistance:These protective coatings resist chemicals and environmental factors, ensuring long-term reliability even in harsh operating conditions.
- Mechanical Stability:Provides mechanical stability to connectors, preventing damage from vibrations, shock, and physical stress.
Working Mechanism:
- Encapsulation:The connector potting compound encapsulates electrical connectors, forming a protective barrier around them.
- Sealing:It seals connectors, preventing ingress of moisture, dust, and other contaminants that could compromise performance.
- Elimination of Air Pockets:Ensures complete coverage and eliminates air pockets, enhancing the reliability of connections.
- Thermal Management: Facilitates efficient heat transfer away from connectors, preventing overheating and prolonging component lifespan.
Significance in Applications:
- Electronics:Protective coatings keep sensors, control units, and circuit board connectors safe in the automotive, aerospace, and consumer electronics sectors.
- Outdoor Equipment: This is essential for outdoor equipment such as LED lighting fixtures, solar panels, and surveillance cameras, providing weatherproofing and durability.
- Industrial Machinery: Ensures reliable performance of connectors in industrial machinery, including robots, manufacturing equipment, and power distribution systems.
- Medical Devices:Maintaining electrical integrity and sterility in sensitive healthcare environments is critical for medical devices and equipment.
- Marine and Aerospace: This is vital in marine and aerospace applications where connectors are exposed to extreme temperatures, moisture, and vibrations.
What Are the Key Components of Connector Potting Compound?
The connector potting compound is a crucial material used in various industries, providing protection and stability to electrical connections. This compound, composed of several vital components, ensures the durability and reliability of connectors in diverse applications. Let’s delve into the essential ingredients that make up connector potting compound:
Resins:
- Epoxy Resins:Known for their excellent adhesion and mechanical properties, they form the backbone of connector potting compounds. They offer high strength and resistance to moisture and chemicals, enhancing the connection’s overall durability.
- Silicone Resins:Silicone-based compounds provide flexibility and thermal stability, making them suitable for connectors exposed to extreme temperatures. They offer excellent electrical insulation properties crucial for maintaining signal integrity.
- Polyurethane Resins:Polyurethane-based compounds protect against environmental factors such as moisture, dust, and vibrations. They offer good adhesion to various substrates, ensuring a secure encapsulation of connectors.
Fillers:
- Inorganic Fillers:Materials like silica, alumina, and glass fibers are commonly added to improve the mechanical properties of connector potting compounds. They enhance dimensional stability, reduce shrinkage, and increase thermal conductivity.
- Organic Fillers:Carbon-based fillers such as graphite or carbon nanotubes may be incorporated to enhance electrical conductivity or provide EMI shielding capabilities.
Hardeners and Catalysts:
- Hardeners: Chemical agents like amines or anhydrides are added to initiate the resin’s curing process. They facilitate cross-linking reactions, transforming the liquid resin into a solid, durable material.
- Catalysts:Accelerators or catalysts speed up the curing process, reducing production time and increasing efficiency.
Plasticizers:
- Plasticizers are additions that increase the potting compound’s elongation and flexibility. They help prevent cracking or brittleness, especially in applications where the connector may undergo mechanical stress or vibration.
Adhesion Promoters:
- Adhesion promoters enhance the bond between the potting compound and the substrate, ensuring strong adhesion and preventing delamination over time. They are crucial for the reliable encapsulation of connectors in various environments.
What Types of Connectors Can Benefit from Potting Compound?
In electronics and electrical engineering, the integrity and durability of connections are paramount. Ensuring that connectors remain protected from environmental factors such as moisture, dust, and vibrations is essential for maintaining optimal performance. One effective solution to safeguard connectors is the use of potting compounds. These compounds, often epoxy-based, encapsulate connectors, providing them with a protective barrier. But which types of connectors can benefit the most from potting compounds? Let’s delve into the possibilities.
Industrial Connectors:
- Industrial connectors used in harsh environments, such as manufacturing plants or outdoor installations, are prone to exposure to moisture, chemicals, and temperature variations.
- Potting compounds offer excellent resistance to these environmental factors, ensuring the reliability and longevity of industrial connectors.
Automotive Connectors:
- In automotive applications, connectors are subjected to extreme conditions, including temperature fluctuations, engine vibrations, and exposure to chemicals and fluids.
- Potting compounds can provide automotive connectors with robust protection against these elements, preventing corrosion and ensuring consistent performance.
Marine Connectors:
- Connectors used in marine environments face constant exposure to saltwater, humidity, and corrosive agents.
- Potting compounds with high water resistance properties can effectively shield marine connectors from corrosion and degradation, extending their lifespan in harsh maritime conditions.
Aerospace Connectors:
- Aerospace connectors operate in demanding conditions characterized by high altitudes, temperature extremes, and radiation exposure.
- Potting compounds formulated to withstand extreme temperatures and provide excellent electrical insulation can enhance the reliability of aerospace connectors, which is critical for safety and mission success.
Outdoor Electronic Connectors:
- Connectors used in outdoor electronic applications, such as telecommunications and renewable energy systems, are susceptible to damage from UV exposure, moisture, and temperature variations.
- Potting compounds with UV-resistant properties can protect outdoor connectors from UV degradation while offering robust environmental sealing.
Why is Environmental Protection Important in Electrical Connections?
In electrical engineering, ensuring the durability and reliability of connections is paramount. One crucial aspect often overlooked is environmental protection, especially when using suitable materials like connector potting compounds. Let’s delve into why environmental protection holds such significance in electrical connections.
Prevents Corrosion:
- Environmental factors like moisture, dust, and chemicals can corrode electrical connections over time.
- Connector potting compounds act as a barrier, shielding connections from corrosive elements, thus prolonging their lifespan.
Enhances Insulation:
- Electrical connections exposed to harsh environments risk insulation breakdown.
- Potting compounds provide additional insulatioInsulationafeguarding connections from short circuits and electrical failures.
Improves Mechanical Strength:
- Vibrations and mechanical stress can weaken electrical connections, leading to intermittent failures.
- Potting compounds encapsulate connections, reinforcing mechanical strength and stability, even in demanding conditions.
Ensures Environmental Compliance:
- With growing environmental awareness, regulations regarding electrical components are becoming stricter.
- Using environmentally friendly potting compounds safeguards connections and ensures compliance with environmental standards.
Increases Reliability:
- Unprotected connections are prone to degradation, posing system failure or malfunction risks.
- Potting compounds provide a reliable solution, maintaining connection integrity even in extreme environments, thus enhancing overall system reliability.
Facilitates Longevity:
- Electrical systems installed in outdoor or industrial settings face continuous exposure to harsh conditions.
- Properly potted connections resist degradation, extending the Longevity of electrical systems and reducing maintenance costs.
Enables Versatility:
- Different applications require tailored solutions to withstand specific environmental challenges.
- Connector potting compounds are available in various formulas, providing Versatility to satisfy the unique requirements of diverse environments and sectors.
How Does Connector Potting Enhance Environmental Protection?
Connector potting compound plays a pivotal role in ensuring the durability and reliability of electronic connections in various industries. This specialized material is designed to encapsulate electrical connectors, providing enhanced environmental protection. But how exactly does connector potting achieve this feat?
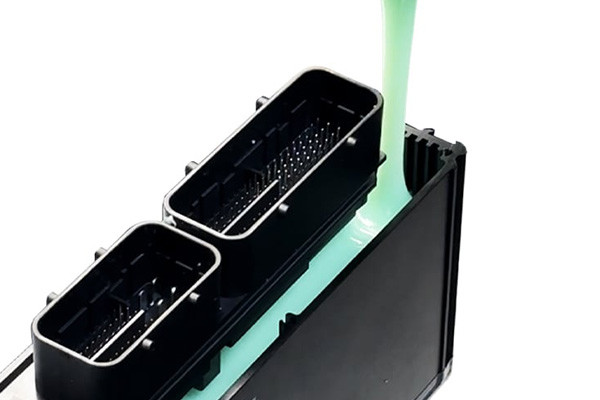
First, connector potting is a barrier against environmental elements such as moisture, dust, chemicals, and vibrations. These factors can compromise electrical connection integrity, leading to malfunctions or failures in electronic devices. Manufacturers can shield the connectors from external threats by encasing them in a protective compound, thus prolonging their lifespan and performance.
One key benefit of connector potting is its ability to prevent moisture ingress. Moisture is a common enemy of electronic components, as it can cause corrosion, short circuits, and insulation breakdown. Connector potting compounds are formulated to create a watertight seal around the connectors, preventing moisture from seeping into the delicate internal circuitry. It is crucial for outdoor installations and automobile systems where electronics are subjected to hostile conditions.
In addition to moisture protection, connector potting compounds offer excellent dust and debris resistance. Dust particles accumulate on electrical connectors over time, leading to poor conductivity and signal interference. By encapsulating the connectors in a protective compound, manufacturers can ensure they remain clean and free from foreign contaminants, thus maintaining optimal performance in challenging operating conditions.
Furthermore, connector potting enhances the mechanical stability of electrical connections. Vibrations and mechanical shocks are typical in many industrial environments, and they can cause connectors to become loose or dislodged over time. By potting the connectors, manufacturers can create a solid, vibration-resistant enclosure that keeps the electrical contacts securely in place, even under extreme conditions.
Another advantage of connector potting is its chemical resistance properties. In specific applications, electronic connectors may come into contact with harsh chemicals or solvents that could damage them. Potting compounds are formulated to withstand exposure to various chemicals, ensuring the connectors remain protected and functional in chemically aggressive environments.
What Are the Common Environmental Hazards Faced by Electrical Connections?
Electrical connections are vital for various industries’ devices, systems, and equipment. However, they are often exposed to environmental hazards that can compromise their functionality and longevity. One effective solution to safeguard these connections is using a connector potting compound. Let’s delve into the common environmental hazards faced by electrical connections and how connector potting compounds mitigate them:
Moisture:
- Moisture significantly threatens electrical connections, causing corrosion, short circuits, and decreased insulation resistance.
- Connector potting compounds form a barrier against moisture ingress, preventing oxidation and maintaining electrical integrity.
Chemical Exposure:
- Chemicals in industrial environments or harsh operating conditions can degrade insulation materials and corrode conductors.
- Potting compounds offer resistance to a wide range of chemicals, including acids, solvents, and oils, ensuring the longevity of electrical connections.
Temperature Variations:
- Severe heat can cause expansion and contraction, weakening conductivity and loosening connections.
- Connector potting compounds provide thermal stability, maintaining connection integrity even in fluctuating temperatures.
Vibration and Mechanical Stress:
- Vibrations from machinery or transportation can cause wires and connections to loosen over time, leading to intermittent connections or failures.
- Potting compounds encapsulate connections, providing mechanical support and damping vibrations, enhancing reliability.
Dust and Debris:
- Dust, dirt, and debris accumulation can impede electrical conductivity and increase the risk of short circuits.
- Potting compounds create a sealed environment around connections, preventing the ingress of contaminants and maintaining optimal performance.
UV Radiation:
- Exposure to ultraviolet (UV) radiation can degrade insulation materials, leading to insulation breakdown and electrical failures.
- Some potting compounds are formulated with UV stabilizers to protect against UV radiation, extending the lifespan of electrical connections.
Can Connector Potting Compound Improve Electrical Connection Durability?
Electrical connections make power flow and communication possible in modern technologies. However, these connections are often exposed to harsh environments that can compromise their durability over time. One solution gaining traction in the industry is using connector potting compounds. But can it truly enhance electrical connection durability? Let’s delve deeper into this innovative approach.
What is a Connector Potting Compound?
- Connector potting compound is a specialized material used to encapsulate electrical connections.
- It is typically a two-part epoxy resin that cures to form a robust and protective enclosure around connectors.
- This compound effectively seals connections from moisture, dust, chemicals, and other environmental factors.
Critical Benefits of Connector Potting Compound:
- Enhanced Durability:Potting compounds shield connections from environmental stressors by providing a protective barrier extending their lifespan.
- Improved Reliability:Potting eliminates the risk of corrosion and short circuits, ensuring consistent performance even in challenging conditions.
- Vibration Resistance:The encapsulation provided by the potting compound prevents connections from loosening due to vibration, which is crucial in applications subjected to mechanical stress.
- Thermal Management:Some potting compounds offer thermal conductivity properties, dissipating heat away from connections and reducing the risk of overheating.
- Customizable Properties:Potting compounds offer versatility in performance and design and are available in various formulas to meet the demands of different applications.
Applications of Connector Potting Compound:
- Automotive Electronics:The potting compound protects connectors in vehicles from moisture, temperature fluctuations, and vibration, ensuring reliable operation.
- Industrial Equipment:Electrical connections in industrial machinery are often exposed to harsh conditions, making potting compounds essential for maintaining performance and longevity.
- Aerospace and Defense:Critical electronic systems in aerospace and defense applications require robust protection against extreme environments, making potting compounds necessary.
- Consumer Electronics:Potting compounds can enhance the durability of connectors in consumer electronics, such as smartphones and wearables, improving product reliability.
What Factors Should Be Considered When Selecting Connector Potting Compound?
The connector potting compound is crucial in ensuring electronic connections’ durability and reliability. It is vital in protecting connectors from environmental factors such as moisture, dust, and vibration. However, selecting the suitable potting compound involves considering several factors to ensure optimal performance. Here are the key considerations:
Environmental Conditions:
The environmental conditions to which the connectors will be exposed play a significant role in determining the type of potting compound required. Factors, including UV radiation, chemical exposure, humidity levels, and temperature fluctuations, must be carefully evaluated. Choosing a potting compound with appropriate resistance to these conditions is essential for long-term reliability.
Compatibility with Connector Materials:
Compatibility between the potting compound and the materials used in the connectors is critical to prevent adverse reactions or degradation. Certain potting compounds may be needed for various materials, including metals, ceramics, and plastics, to assure compatibility and avoid problems like delamination or corrosion.
Thermal Properties:
Connector assemblies often experience temperature variations during operation. Therefore, selecting a potting compound with suitable thermal conductivity and stability is essential to prevent overheating or thermal stress. The needs of the application should be considered while evaluating thermal parameters like thermal conductivity and coefficient of thermal expansion.
Mechanical Strength:
Connectors may be subjected to mechanical stresses such as shock and vibration, especially in industrial or automotive applications. The potting compound should provide adequate mechanical strength to protect the connectors from physical damage and maintain electrical continuity under such conditions.
Electrical Insulation:
Proper electrical insulation is crucial to prevent short circuits or leakage currents that could compromise the functionality of electronic devices. The potting compound should have high dielectric strength and low electrical conductivity to effectively insulate the connectors.
Application Method:
Consideration should be given to the method of potting application, whether manual or automated. Depending on factors such as viscosity, cure time, and pot life, some potting compounds may be more suitable for specific application methods.
Regulatory Compliance:
Compliance with regulatory standards and certifications may be necessary depending on the industry and application. It’s essential to select potting compounds that meet relevant industry standards for safety, environmental impact, and performance, such as UL, RoHS, or REACH.
Are There Different Formulations Available for Different Applications?
Connector potting compounds are multipurpose materials intended to enclose and shield electronic components, especially connectors, from external elements like moisture, vibration, and temperature changes. By creating a barrier around the connection, these compounds enhance durability and reliability, extending the lifespan of electronic devices.
- Formulation Variations: Yes, various compositions of connection potting compounds are made to meet the unique needs of multiple applications. These formulations differ in chemical composition, physical properties, and performance characteristics, allowing for customization based on specific requirements.
- Environmental Considerations: Specific applications, such as outdoor electronics or those exposed to harsh environments, require potting compounds with excellent resistance to moisture, UV radiation, and extreme temperatures. Formulations with high weather ability and environmental resistance are ideal for such scenarios.
- Thermal Management: Thermally conductive potting compounds are preferred in applications where heat dissipation is a concern. These formulations efficiently transfer heat away from sensitive components, preventing overheating and ensuring optimal performance even in demanding thermal conditions.
- Flexibility and Shock Absorption: Flexible potting compounds with good shock-absorbing properties are essential for applications subject to mechanical stress or vibration. By offering protection and cushioning against impact, these formulas lower the possibility of harming fragile electronic components.
- Electrical Insulation: In critical electrical insulation scenarios, potting compounds with high dielectric strength and insulating properties are indispensable. These formulations prevent electrical leakage and short circuits, maintaining the integrity of connections in sensitive electronic systems.
- Chemical Resistance: Specific industrial or automotive applications may expose electronic components to chemicals or solvents. In such cases, potting compounds with robust chemical resistance offer reliable protection against corrosion and degradation, ensuring long-term performance even in challenging chemical environments.
How Does Connector Potting Compound Aid in Vibration Dampening?
In the realm of electronics, the integrity of connections is paramount. Vibrations from machines, moving vehicles, and other sources are a severe risk to the stability of electrical connections. Connector potting compound emerges as a solution to this challenge, providing a robust method to safeguard connections against the detrimental effects of vibrations. Let’s delve into how connector potting compound aids in vibration dampening:
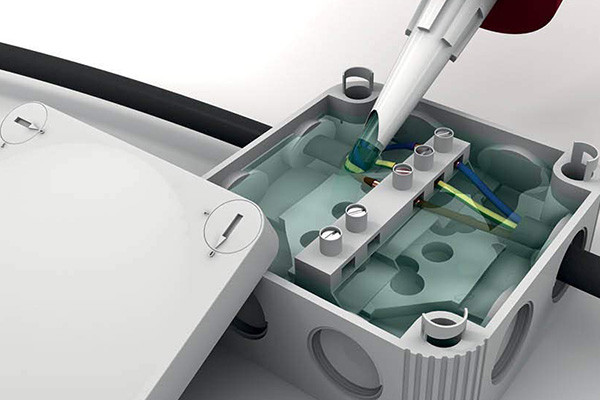
Enhanced Mechanical Stability:
- Connector potting compound envelops electrical connections, forming a protective barrier against external elements.
- It fills voids and crevices, immobilizing components and preventing movement that could lead to connection failure.
Absorption of Vibrational Energy:
- The resilient nature of potting compounds allows them to absorb and dissipate vibrational energy.
- This absorption capability reduces the transmission of vibrations to sensitive electrical components, preserving their functionality.
Protection Against Environmental Factors:
- Connector potting compounds provide insulation against moisture, dust, and other environmental contaminants.
- Sealing connections prevent corrosion and degradation from exposure to these elements, further enhancing the reliability of electronic systems.
Customized Formulations:
- Manufacturers offer a variety of potting compounds tailored to specific application requirements.
- Formulations can be adjusted to accommodate temperature extremes, chemical exposure, and desired flexibility, ensuring optimal performance in diverse environments.
Compatibility with Various Substrates:
- Connector potting compounds exhibit compatibility with a wide range of substrates commonly used in electronic assemblies, including metals, plastics, and ceramics.
- This versatility enables their use across various industries and applications, from automotive electronics to aerospace systems.
Simplified Manufacturing Processes:
- Potting compounds can be applied using automated dispensing equipment, streamlining the manufacturing process.
- Their self-leveling characteristics guarantee consistent coverage and reduce the need for manual intervention, boosting production efficiency and consistency.
Long-Term Reliability:
- Connector potting compounds contribute to the long-term reliability of electronic devices by mitigating the effects of vibrations.
- Components encapsulated with these compounds are less prone to failure, resulting in improved product lifespan and reduced maintenance costs.
Can Potting Compound Improve Resistance to Chemicals and Solvents?
In various industrial and electronic applications, ensuring the longevity and reliability of components is crucial. One method that has gained prominence is using connector potting compound. This specialized material enhances mechanical stability and plays a pivotal role in safeguarding against the detrimental effects of chemicals and solvents. Let’s delve into how potting compound contributes to improved resistance and durability:
Chemical Resistance Enhancement:
- Barrier Formation:A potting compound creates a protective barrier around electronic components, shielding them from direct contact with chemicals and solvents.
- Chemical Inertness:Many potting compounds are formulated to be chemically inert, meaning they do not react with common chemicals or solvents, thereby preserving the integrity of the encapsulated components.
- Resistance to Corrosion:By preventing corrosive agents from reaching sensitive parts, potting compound helps mitigate the risk of corrosion, ensuring prolonged functionality of electronic devices.
Solvent Resistance Enhancement:
- Sealant Properties:The potting compound acts as an effective sealant, sealing off vulnerable areas and preventing solvent infiltration.
- Preventing Swelling:Certain solvents have the potential to cause swelling or degradation of electronic materials. Potting compounds can impede such effects by providing a robust barrier against solvent penetration.
- Maintaining Structural Integrity:Solvent exposure can weaken materials over time, compromising their structural integrity. Potting compounds reinforce the components, minimizing the risk of damage due to solvent exposure.
Advantages of Potting Compound:
- Versatility:Potting compounds are available in various formulations to suit specific application requirements, offering versatility in addressing different chemical and solvent challenges.
- Long-Term Protection:The encapsulation provided by the potting compound ensures long-term protection against chemical and solvent exposure, extending the lifespan of electronic devices and components.
- Enhanced Reliability:By fortifying components against chemical and solvent-related damage, potting compound enhances the overall reliability of electronic systems, reducing the likelihood of premature failure.
- Cost-Effectiveness:Investing in potting compounds upfront might result in significant cost savings by reducing the need for frequent component replacements or repairs caused by solvent or chemical damage.
Is Connector Potting Compound Suitable for Outdoor Applications?
The connector potting compound is critical in ensuring the longevity and performance of electrical connections, particularly in outdoor environments. The reliability and endurance of connectors can be significantly impacted by the potting compound choice, whether in industrial settings, automotive applications, or even outdoor electrical devices. But is connector potting compound genuinely suitable for outdoor applications?
Connector potting compounds are materials used to encapsulate electrical connectors, providing insulation, protection against environmental factors, and mechanical support. They are typically formulated to withstand moisture, temperature variations, UV exposure, and chemical exposure. However, not all potting compounds are created equal, and choosing the right one for outdoor use requires careful consideration.
One of the primary challenges in outdoor applications is exposure to moisture. Water ingress can lead to corrosion, short circuits, and, ultimately, electrical system failure. High-quality connector potting compounds are designed to be waterproof, forming a barrier that prevents moisture from reaching the delicate electrical components within the connector. Silicone-based compounds, for instance, are known for their excellent water resistance properties, making them a popular choice for outdoor applications.
Furthermore, outdoor environments often subject electrical connectors to extreme temperatures. From scorching heat to cold, temperature fluctuations can cause materials to expand and contract, putting stress on the connectors. Connector potting compounds with thermal stability are essential to ensure that the encapsulated connectors remain intact and functional across a wide temperature range.
UV exposure is another consideration for outdoor applications. Certain materials can deteriorate with prolonged exposure to sunlight, resulting in brittleness, discoloration, and loss of mechanical qualities. Potting compounds with UV stabilizers can mitigate these effects, preserving the integrity of the connectors even in harsh sunlight.
Chemical exposure is also a concern in outdoor environments, particularly in industrial settings where connectors may come into contact with oils, solvents, or other harsh chemicals. Resilient potting compounds that resist chemical corrosion are crucial for ensuring the long-term reliability of outdoor electrical connections.
What Are Some Industry-Specific Applications of Connector Potting Compound?
Connector potting compound is a versatile material widely used in various industries for its excellent protective and insulating properties. This compound, typically made of epoxy or silicone, is crucial in safeguarding electrical connections from environmental factors such as moisture, chemicals, and mechanical stress. Let’s delve into some industry-specific applications where connector potting compounds are indispensable:
Automotive Industry:
- Sealing electrical connectors in vehicles to prevent corrosion and ensure reliable performance.
- This substance, usually silicone or epoxy, is essential for protecting electrical connections from the elements, including moisture, chemicals, and mechanical stress.
- Ensuring longevity and durability of electrical components in automotive systems.
Electronics Industry:
- Encapsulating sensitive electronic components like circuit boards, sensors, and connectors to shield them from moisture, dust, and other contaminants.
- Enhancing the reliability of electronic devices by providing insulation against electrical interference and preventing short circuits.
- Potting connectors in electronic gadgets, appliances, and industrial equipment help maintain signal integrity and prolong service life.
Aerospace and Defense Sector:
- Protecting critical electrical connections and components in aircraft, spacecraft, and military vehicles from the adverse effects of altitude, temperature variations, and exposure to chemicals.
- It ensures the integrity of communication systems, radar equipment, and avionics by potting connectors to withstand extreme operating conditions.
- It enhances the ruggedness and reliability of electronic assemblies used in defense applications through proper potting techniques.
Renewable Energy Systems:
- Sealing connectors and junction boxes in solar panels and wind turbines to prevent water ingress and corrosion, thus maintaining the efficiency and longevity of the systems.
- Potting electrical connections in battery packs and power inverters for solar and wind energy storage solutions to enhance safety and reliability. Protecting control systems and monitoring equipment in renewable energy installations from environmental hazards to ensure uninterrupted operation and performance.
Marine and Offshore Applications:
- Potting connectors and cables in marine vessels and offshore platforms enable them to withstand saltwater exposure, extreme weather conditions, and mechanical vibrations.
- It ensures the reliability of electrical systems on ships, submarines, and offshore installations by mitigating the risks of corrosion and water damage.
- Protecting underwater sensors, communication devices, and navigation equipment with robust potting solutions for marine exploration and offshore operations.
How Does Potting Compound Facilitate Heat Dissipation?
Potting compounds are indispensable materials in various industries, especially in electronics, where they play a crucial role in protecting sensitive components from environmental factors and mechanical stress. One of the lesser-known yet significant functions of potting compounds is their ability to facilitate heat dissipation. Let’s delve into how this is achieved:
Thermal Conductivity Enhancement:
- Potting compounds are formulated with high thermal conductivity materials, such as epoxy resins filled with thermally conductive fillers like ceramics or metals.
- These fillers help efficiently transfer heat away from the encapsulated components.
Heat Transfer Path Optimization:
- Encapsulating electronic components with potting compounds establishes a direct thermal path between the elements and the surrounding environment.
- This optimized heat transfer path ensures that heat generated by the components can quickly dissipate into the surroundings.
Elimination of Air Pockets:
- During potting, the compound fills all voids and crevices around the components, eliminating air pockets that can act as thermal insulators.
- It ensures better heat transfer and prevents the formation of hotspots that can lead to component failure.
Enhanced Surface Area:
- Potting compounds conform to the shape of the components, creating a larger surface area for heat dissipation.
- This increased surface area allows for a more efficient heat transfer to the surrounding environment.
Protection Against Environmental Factors:
- Potting compounds provide a protective barrier against environmental factors such as moisture, dust, and vibration, which can compromise the thermal performance of electronic components.
- Protecting the components ensures that potting compounds’ heat dissipation properties remain effective.
Improved Reliability and Longevity:
- Effective heat dissipation prolongs the lifespan of electronic components by preventing overheating, which can lead to premature failure.
- Potting compounds contribute to the overall reliability of electronic systems by maintaining optimal operating temperatures.
Can Connector Potting Compound Help in Miniaturization of Electronic Devices?
The relentless drive towards smaller, sleeker electronic devices has been a defining trend in recent years. From smartphones to wearables to medical implants, manufacturers are constantly seeking ways to shrink the size of their products without compromising on performance. One critical aspect of this miniaturization process involves effectively sealing and protecting electrical connectors, ensuring their functionality and durability in compact spaces. Enter connector potting compound – a material that may be key to overcoming some challenges of downsizing electronic devices.
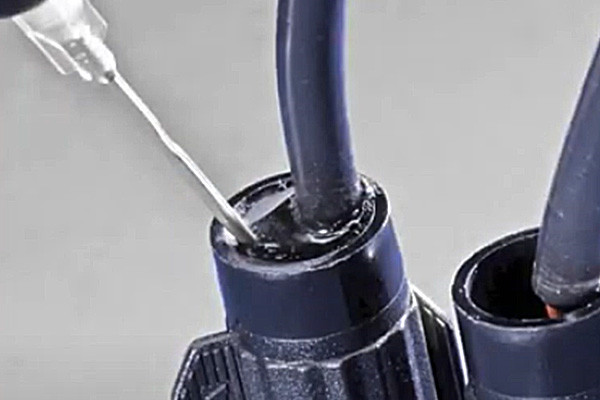
Connector potting compound is a specialized substance that encapsulates and protects electrical connectors. It typically consists of a polymer resin poured or injected into the housing of a connector, where it cures to form a solid, protective barrier. This barrier shields the connectors from environmental factors such as moisture, dust, and vibration, which can compromise their performance and longevity.
One of the primary ways connector potting compound contributes to miniaturization is by allowing for the design of smaller, more tightly packed electronic assemblies. By effectively sealing connectors and eliminating the need for additional enclosures or protective measures, manufacturers can reduce the overall footprint of their devices without sacrificing reliability. It is especially crucial in applications where space is at a premium, such as wearable gadgets and IoT devices.
Moreover, connector potting compounds can enhance the mechanical stability of electronic assemblies, thereby enabling the use of thinner and lighter materials. It is beneficial in sectors where reducing weight is a top concern, including the aircraft and automobile industries. The potting compound helps prevent damage to delicate components and ensures consistent performance under demanding conditions by securely anchoring connectors and dampening vibrations.
Another benefit of using connector potting compound is its ability to improve resistance to environmental stressors. Electronic devices are often subjected to harsh operating environments, including temperature extremes, humidity, and chemical exposure. Connectors may corrode, short circuit, or malfunction without adequate protection, leading to costly repairs or replacements. The potting compound acts as a barrier against these hazards, safeguarding connectors and extending the lifespan of electronic devices.
In addition to its protective properties, connector potting compounds can also enhance electrical insulation and conductivity, further optimizing the performance of electronic systems. By filling voids and eliminating air pockets around connectors, the potting compound helps maintain consistent electrical characteristics and reduces the risk of signal interference or leakage.
What Role Does Potting Compound Play in Sealing Against Moisture and Dust?
In various electronic applications, especially those exposed to harsh environments, the importance of effective sealing against moisture and dust cannot be overstated. One crucial component that aids in achieving this protection is the connector potting compound. Let’s examine its importance and function in guaranteeing the robustness and dependability of electronic equipment.
- Barrier Formation:The connector potting compound creates a robust barrier around electronic components, preventing moisture and dust ingress. This barrier is essential for maintaining the integrity of sensitive electronics, especially in outdoor or industrial settings where exposure to environmental elements is expected.
- Enhanced Durability:By encapsulating connectors and other delicate parts, the potting compound fortifies them against potential damage caused by moisture and dust infiltration. By greatly extending the lifespan of electrical devices, this durability improvement lowers the frequency of replacements and repairs.
- Prevention of Corrosion:Moisture can lead to corrosion of metal components within electronic devices, resulting in malfunction or complete failure. Connector potting compound acts as a protective shield, safeguarding against corrosive agents and maintaining the electrical conductivity of connections over time.
- Thermal Management:In addition to providing moisture and dust resistance, potting chemicals frequently include the ability to regulate temperature. They aid in the dissipation of heat produced by electronic components, maintaining ideal operating temperatures and averting overheating, which can worsen the lifespan and performance of devices.
- Customization Options:Connector potting compounds come in various formulations to cater to specific application requirements. Whether achieving a certain level of flexibility, temperature resistance, or adhesion strength, manufacturers can choose the most suitable compound to meet their needs.
- Ease of Application:Many potting compounds are designed for easy application, allowing for efficient integration into the manufacturing process. These compounds offer versatility and compatibility with different production methods, whether through casting, encapsulation, or molding.
- Compliance with Standards:Potting compounds often comply with industry standards and environmental protection and safety regulations. It ensures that electronic devices meet the necessary criteria for reliability and performance, instilling confidence in end-users.
Are There Any Disadvantages or Limitations of Using Connector Potting Compound?
A connector potting compound encapsulates electrical connectors and components, providing insulation, protection against environmental factors, and mechanical stability. Typically composed of epoxy resins, silicones, or polyurethanes, these compounds are poured or injected into enclosures to form a protective barrier around delicate electronic parts.
Advantages of Connector Potting Compound
- Environmental Protection:One of the primary advantages of connector potting compound is its ability to shield electrical components from harsh environmental conditions such as moisture, dust, and chemicals. This safeguard guarantees the connections’ durability and dependability, particularly in outdoor or industrial environments.
- Mechanical Stability:Potting compounds enhance the mechanical strength of connectors, preventing damage from vibration, shock, and physical impact. This capability is handy in applications where connectors are handled or moved frequently.
- Electrical Insulation:Potting compounds provide excellent electrical insulation by fully encapsulating connectors, reducing the risk of short circuits and electrical failures. This insulation is vital for maintaining signal integrity and preventing leakage currents.
- Customization:Connector potting compounds come in various formulations, allowing customization based on specific application requirements. Engineers can choose compounds with different viscosities, cure times, and thermal properties to suit their needs.
Disadvantages and Limitations
- Rigidity:While connector potting compounds offer mechanical stability, they can also introduce rigidity. In applications where flexibility is crucial, such as cables or connectors subjected to frequent bending, the stiffness of the potting compound may stress the components.
- Repairability:Once connectors are potted, repairing or replacing individual components within the enclosure becomes challenging. This lack of repairability can be a significant drawback when maintenance or upgrades are necessary.
- Thermal Conductivity:Some potting compounds may have limited thermal conductivity, leading to heat buildup within the enclosure. In high-power applications, inadequate thermal management could compromise the performance and lifespan of electronic components.
- Cost and Complexity:Using connector potting compounds adds an extra step to the manufacturing process, which may increase production costs and complexity. Additionally, selecting the appropriate compound and ensuring proper application require expertise, further increasing overall expenses.
How Does Connector Potting Impact Manufacturing Processes?
The Connector potting compound is pivotal in various manufacturing processes, especially in industries reliant on electronic components. This specialized material shields connectors, cables, and electronic assemblies from external elements like moisture, dust, vibration, and heat stress. Understanding the significance of connector potting and its impact on manufacturing processes is essential for ensuring product quality and reliability.
Key Points:
- Enhanced Protection:Connector potting compounds provide a protective barrier around electronic components, shielding them from moisture, chemicals, and mechanical damage. This protection is crucial in applications exposed to harsh environments or demanding conditions.
- Improved Reliability:By encapsulating connectors and cables, potting compounds enhance the reliability and longevity of electronic devices. They help prevent corrosion, electrical shorts, and other issues that could compromise the equipment’s functionality.
- Streamlined Assembly:Connector potting simplifies the assembly process by providing a one-stop solution for sealing and protecting electronic components. It reduces the need for multiple components or complex assembly procedures, thus saving time and labor costs.
- Customized Solutions:Manufacturers can choose from various connector potting compounds tailored to specific application requirements. These compounds come in multiple formulations, viscosities, and cure times, allowing for customization based on operating temperature, flexibility, and chemical resistance.
- Cost-Effective Manufacturing:While initial investment in connector potting materials may seem higher, the long-term benefits outweigh the costs. Improved product reliability reduces the need for warranty repairs or replacements, ultimately saving manufacturers money in the long run.
- Ensured Compliance:Connector potting compounds often meet industry standards and regulatory requirements for environmental protection, electrical insulation, and flame resistance. Using compliant materials ensures that products meet quality standards and adhere to safety regulations.
Connector potting plays a crucial role in modern manufacturing processes, particularly within industries such as automotive, aerospace, telecommunications, and consumer electronics. Its ability to enhance protection, reliability, and efficiency makes it indispensable in producing electronic devices and assemblies.
What Future Trends Can We Expect in Connector Potting Technology?
In electronics and electrical engineering, the evolution of connector potting technology continues to push boundaries, driving advancements in various industries. As we look to the future, several trends are poised to shape the landscape of connector potting compounds, enhancing performance, durability, and versatility. Let’s delve into what we can expect from the future of connector potting technology.
Enhanced Material Innovations:
- Continued development of high-performance materials tailored for specific applications is essential.
- Integrating nanotechnology enhances material properties such as thermal conductivity and dielectric strength.
- Exploring eco-friendly and sustainable materials is essential to meet growing environmental concerns.
Advanced Formulation Techniques:
- Advanced formulation techniques are being adopted, such as 3D printing for customized potting solutions.
- The adoption of advanced formulation techniques, including 3D printing for customized potting solutions, is currently underway.
- Integrating additives enhances flexibility, adhesion, and resistance to harsh environments.
Miniaturization and Microelectronics:
- They are catering to the trend of miniaturization with ultra-thin and lightweight potting compounds.
- Developing specialized formulations for microelectronics enables the efficient encapsulation of tiny components.
- Integrating advanced encapsulation techniques for densely packed circuits in IoT devices and wearables.
IoT and Industry 4.0 Applications:
- Customized potting solutions for IoT sensors enable reliable performance in diverse environments.
- The development of ruggedized potting compounds for industrial IoT applications in harsh conditions is underway.
- Integrating intelligent features, such as self-healing properties, enhances durability and longevity.
Conductive and Thermally Conductive Compounds:
- Advancements in conductive potting compounds are enhancing electromagnetic interference (EMI) shielding.
- The development of thermally conductive potting materials aims to achieve efficient heat dissipation in high-power applications.
- Integrating hybrid materials, which combine electrical insulation with thermal conductivity, enables multifunctional applications.
Automation and Manufacturing Efficiency:
- The implementation of automated potting processes increases efficiency and consistency.
- The development of fast-curing formulations aims to reduce production cycle times.
- The integration of in-line quality control measures ensures reliability and consistency in performance.
Customization and Versatility:
- There is a growing demand for customizable potting solutions tailored to specific application requirements.
- The development of versatile materials aims to ensure compatibility with various substrates and environmental conditions.
- Adopting modular potting systems facilitates accommodating evolving design needs and rapid prototyping.
Conclusion
In conclusion, connector potting compound stands as an indispensable asset in the domain of electrical engineering, offering unparalleled protection, durability, and reliability to electrical connections across diverse applications. Its ability to withstand environmental challenges, enhance mechanical stability, and prolong the lifespan of electronic devices makes it a cornerstone in modern manufacturing practices. As technology continues to evolve, the role of connector potting compound is poised to expand, driving innovation and efficiency in electrical systems worldwide.
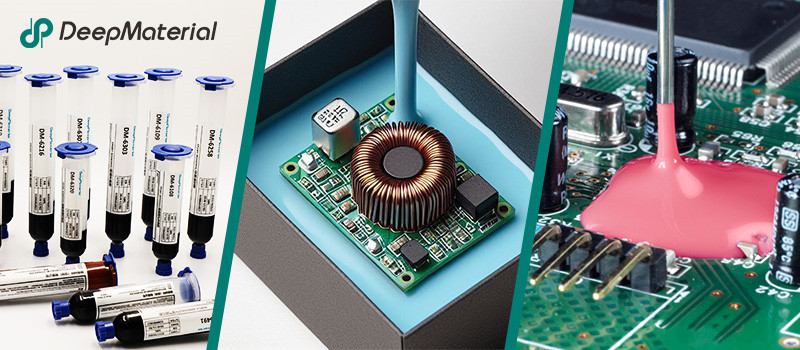
About DeepMaterial
DeepMaterial is a trusted supplier of encapsulant materials that are used in electronics manufacturing worldwide. From chip on board encapsulants such as glob top material to conformal coatings, underfills, low pressure molding, and potting solutions, DeepMaterial offers a full range of circuit board protection materials that effectively protect circuit boards while help reduce costs. More…Deepmaterial is a the manufacturer of epoxy adhesives including hardeners, metalbond, and metal filled resins. Structural, toughened medium viscosity, and non-sag adhesives are also offered. Some adhesives are resistant to thermal shock, chemical, vibration dampening, and impact. Suitable for metals, plastics, wood, and ceramics. Serves electronics, aerospace, automotive, tooling, marine, and construction industries. REACH and RoHS compliant. FDA approved. UL listed. Meets military specifications. We are the one of best adhesive manufacturers in China.
Blogs & News
Potting compounds are at the frontline of electronics assembly, delivering effective protection in challenging environmental conditions while improving mechanical strength and offering high electric insulation. Used within a variety of industries, electrical potting compounds are found within a broad range of consumer electronics, as well as used in applications across the automotive, aerospace, and other industries where electronic assemblies are prevalent.
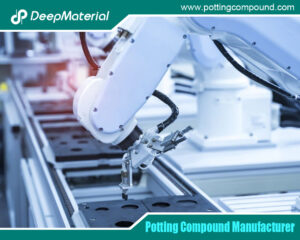
How To Choose Between Potting And Conformal Coating?
Protection of printed circuit boards (PCBs) is most often achieved with either potting or conformal coating. The selection of which method to use depends upon
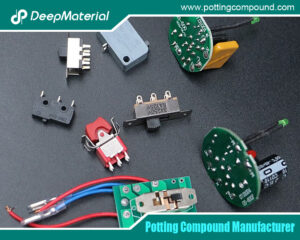
Why are Silicone Potting Compounds Used in Electronics Products?
Potting compounds are one of the key materials used to safeguard sensitive as well as critical electronics components from a variety of threats. Silicone-based potting
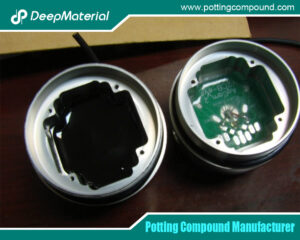
Potting compound for electronics
View Original In electronics, potting may be a process of filling an entire electronic assembly with a solid or gelatinous compound for top voltage assemblies
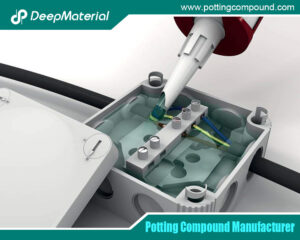
What Is Conformal Coating?
Conformal coatings are protective, non-conductive dielectric layers that are added to a circuit board or electronic device. thermally-conductive-potting The coating “conforms” to the object being
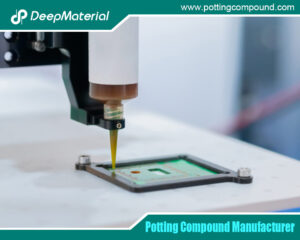
Electronics Potting & Encapsulation
No matter what the specific application or industry, protecting electronic components is crucial for ensuring long-lasting system durability and functionality. Available in various formats including
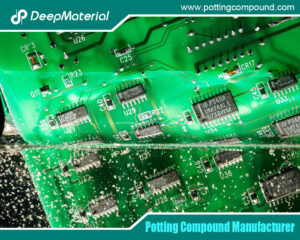
Encapsulation Considerations
If the potting material contains air inclusions or ‘voids’, then it may not be such an effective method of protection. Voids can reduce the insulation