High Voltage Potting Compound
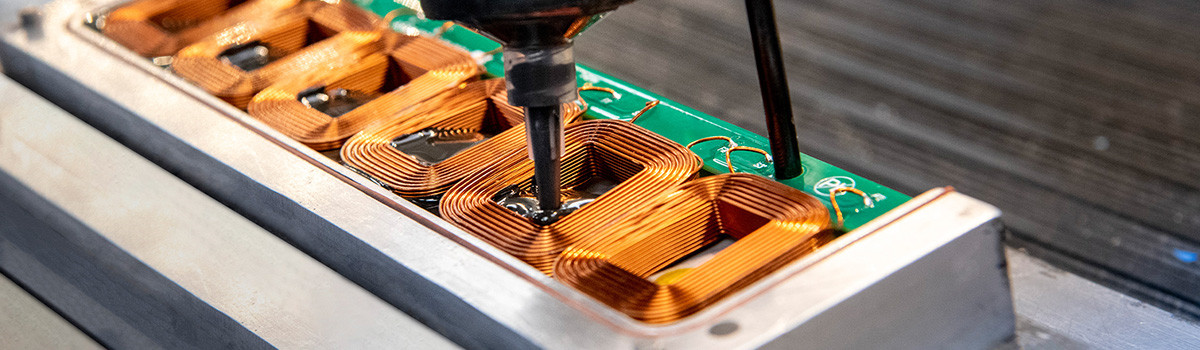
High-voltage potting compounds are crucial in various industries where electrical insulation and protection against high voltage are paramount. These compounds are specially formulated to encapsulate electronic components, providing insulation, protection against environmental factors, and mechanical support. Whether in power distribution systems, automotive electronics, or aerospace applications, the suitable potting compound ensures the reliability and longevity of electrical systems operating at high voltages. This category delves into the essential aspects, applications, and considerations surrounding high-voltage potting compounds.
Table of Contents
ToggleEssential Details You Should Have in Your Arsenal:
What are high-voltage potting compounds?
High-voltage potting compounds are specialized materials used to encapsulate electronic components and assemblies, providing electrical insulation and protection from environmental factors such as moisture, dust, and chemicals. These compounds are designed to withstand high voltages without breakdown or leakage, making them crucial for applications where electrical insulation is paramount.
These compounds typically consist of a thermosetting resin, such as epoxy or silicone, and various additives, such as fillers, hardeners, and modifiers. The resin provides the main insulation properties, while the additives impart additional characteristics such as thermal conductivity, flame resistance, and flexibility.
One of the primary functions of high-voltage potting compounds is to prevent electrical arcing and corona discharge, which can occur when high voltages are applied across small gaps or irregularities in the insulation material. By completely encapsulating the components, these compounds eliminate such gaps and provide a uniform dielectric barrier, thereby minimizing the risk of electrical breakdown.
High-voltage potting compounds also offer excellent resistance to tracking and surface erosion, which can occur due to the formation of conductive paths on the surface of the insulation material when exposed to contaminants or high-humidity environments. This helps maintain the integrity of the insulation over time and ensures reliable performance in demanding operating conditions.
In addition to their electrical insulation properties, high-voltage potting compounds may also provide mechanical reinforcement, protecting delicate components from mechanical shock and vibration. This is particularly important in applications where the electronic assemblies may be subjected to harsh environments or handling during transportation and installation.
Overall, high-voltage potting compounds are critical in ensuring the reliability and safety of electronic systems operating at elevated voltages. Their ability to provide robust electrical insulation, environmental protection, and mechanical support makes them indispensable in various industries, including power generation, transportation, telecommunications, and aerospace.
How do high-voltage potting compounds differ from standard potting compounds?
High-voltage and standard potting compounds serve the same primary purpose: encapsulating electronic components to protect them from environmental factors like moisture, dust, and vibration. However, they differ significantly in their formulations and properties, primarily due to the specific requirements imposed by high-voltage applications.
- Dielectric Strength: The most crucial difference lies in dielectric strength. High-voltage potting compounds are formulated to withstand much higher electric fields without breaking down. They have significantly higher dielectric strength compared to standard potting compounds. Dielectric strength is the maximum electric field a material can withstand without electrical breakdown occurring, typically measured in volts per unit thickness.
- Insulation Properties: High-voltage potting compounds must provide superior insulation properties to prevent electrical leakage and breakdown. They are engineered to have low conductivity to isolate high-voltage components effectively. Standard potting compounds may have less stringent requirements for insulation since they are used in lower-voltage applications.
- Thermal Conductivity: While both types of potting compounds offer thermal protection to some extent, high-voltage potting compounds often prioritize thermal conductivity. Effective heat dissipation is critical in high-voltage applications to prevent overheating and maintain component reliability. Therefore, high-voltage potting compounds may have formulations that facilitate better heat transfer than standard compounds.
- Material Compatibility: High-voltage potting compounds may need to be compatible with a broader range of materials commonly found in high-voltage systems, such as insulating materials, conductive traces, and various substrates. Compatibility considerations are crucial to ensure encapsulated electronics’ long-term reliability and performance.
- Testing and Certification: High-voltage potting compounds typically undergo more rigorous testing and certification processes to meet specific industry standards and safety regulations for high-voltage applications. This includes testing for dielectric strength, thermal properties, and long-term reliability under high voltage stress.
High-voltage potting compounds are specially formulated to withstand the unique challenges posed by high-voltage environments. They offer superior dielectric strength, insulation properties, thermal conductivity, and material compatibility and often undergo more stringent testing and certification compared to standard potting compounds. These characteristics are essential for ensuring high-voltage electronic systems’ safety, reliability, and longevity.
What are the primary components of high-voltage potting compounds?
High-voltage potting compounds are essential for electrical applications to encapsulate and protect sensitive electronic components from environmental factors and electrical stress. These compounds are designed to withstand high voltages and provide insulation and mechanical support. The primary elements of high-voltage potting compounds typically include resins, fillers, curing agents, and additives.
- Resins: Resins serve as the primary matrix of the potting compound, providing mechanical strength, adhesion, and electrical insulation. Epoxy resins are commonly used due to their excellent electrical properties, chemical resistance, and adhesion to various substrates.
- Fillers: Fillers are added to the resin matrix to enhance mechanical properties, control thermal expansion, and reduce costs. Joint fillers include silica, alumina, glass fibers, and mineral fillers. These materials help improve the potting compound’s strength, stiffness, and thermal conductivity.
- Curing Agents: Curing agents or hardeners initiate the chemical reaction that transforms the liquid resin into a solid polymer network. Various curing agents such as amines, anhydrides, or catalysts are used depending on the specific application requirements. The choice of curing agent influences the potting compound’s cure time, temperature resistance, and final properties.
- Additives: Additives are incorporated into potting compounds to modify flexibility, flame resistance, thermal conductivity, or UV stability. Common additives include flame retardants, plasticizers, UV stabilizers, and colorants. These additives enhance the overall performance and reliability of the potting compound in challenging operating conditions.
In addition to these primary components, high-voltage potting compounds may contain solvents or diluents to adjust viscosity for easier processing or to facilitate air release during curing. Formulating potting compounds carefully is essential to achieve the desired electrical, mechanical, and thermal properties while ensuring compatibility with the encapsulated components and environmental conditions. Properly selecting and formulating these components is crucial to achieving optimal performance and reliability in high-voltage applications.
What factors determine the dielectric strength of high-voltage potting compounds?
The dielectric strength of high-voltage potting compounds, which refers to their ability to withstand electrical stress without breakdown, is influenced by various factors:
- Chemical Composition: The chemical composition of the potting compound plays a significant role in determining its dielectric strength. Compounds with high molecular weight and stable chemical structures tend to have better dielectric properties. Polar groups within the molecules can also enhance the compound’s ability to resist electrical breakdown.
- Insulator Fillers: Many high-voltage potting compounds incorporate insulating fillers such as silica, alumina, or glass beads. These fillers help to improve the mechanical strength and thermal conductivity of the compound while also influencing its dielectric properties. The size, shape, and distribution of these fillers within the matrix can affect the overall dielectric strength of the material.
- Cure Mechanism: The curing process of the potting compound can impact its dielectric strength. Proper curing ensures the formation of a dense and uniform polymer network, which enhances the material’s electrical insulation properties. Factors such as curing temperature, time, and curing agents can affect the final properties of the compound.
- Moisture Absorption: Moisture absorption can significantly degrade the dielectric strength of potting compounds, particularly in high-humidity environments. Proper encapsulation and sealing techniques are essential to prevent moisture ingress, which can compromise the material’s insulation properties over time.
- Thickness and Configuration: The thickness of the potting layer and the configuration of the components being potted also influence dielectric strength. Thicker layers may exhibit higher breakdown voltages, but the presence of voids or air gaps within the potting material can create localized areas of weakness.
- Testing Conditions: The dielectric strength of potting compounds is often evaluated using standardized testing methods such as ASTM D149. Testing conditions, including voltage waveform, frequency, and electrode geometry, can affect the measured dielectric strength values and should be carefully controlled to ensure accurate material comparisons.
A combination of material composition, processing parameters, environmental factors, and testing conditions determines the dielectric strength of high-voltage potting compounds. Optimizing these factors is essential to ensuring reliable electrical insulation in various applications.
What are the typical applications of high-voltage potting compounds?
High-voltage potting compounds find applications in various industries where electrical insulation and protection are critical. These compounds are specifically formulated to provide insulation, mechanical support, and environmental protection for high-voltage components. Here are some typical applications:
- Transformer Potting: High voltage transformers require insulation to prevent electrical arcing and to maintain proper electrical conductivity. Potting compounds encapsulate transformer windings, providing insulation against high voltages and environmental factors such as moisture and contaminants.
- High Voltage Capacitors: High voltage applications require robust insulation to prevent dielectric breakdown. Potting compounds are applied to encapsulate capacitor elements, ensuring reliable performance and longevity even under high voltage stress.
- Power Distribution Equipment: Components such as insulators, bushings, and connectors in power distribution systems require insulation to prevent electrical leakage and breakdown. Potting compounds provide a protective barrier around these components, enhancing their insulation properties and extending their service life.
- High Voltage Switchgear: Switchgear equipment used in high voltage transmission and distribution systems must withstand high electrical stresses. Potting compounds are employed to insulate and protect switchgear components, reducing the risk of electrical faults and enhancing overall system reliability.
- Electronic Components: High-voltage potting compounds encapsulate high-voltage resistors, diodes, and modules. This ensures electrical insulation and protects these components from environmental factors such as moisture, dust, and vibrations.
- Electric Motors and Generators: Potting compounds insulate coils and windings in high-voltage electric motors and generators. This insulation enhances the electrical performance of the motor or generator and protects it from moisture and other contaminants, extending its operational lifespan.
- High Voltage Cable Joints and Terminations: Cable joints and terminations in high voltage power cables require insulation to prevent electrical faults and ensure reliable operation. Potting compounds are applied to these joints and terminations to provide insulation and environmental protection, reducing the risk of cable failure.
High-voltage potting compounds play a crucial role in ensuring the reliable operation and longevity of various electrical components and systems operating under high-voltage conditions, ranging from transformers and capacitors to power distribution equipment and electronic components. Their ability to provide robust insulation and protection against environmental factors makes them indispensable in numerous industries where electrical reliability is paramount.
How do high-voltage potting compounds provide electrical insulation?
High-voltage potting compounds are crucial in electrical insulation by encapsulating electronic components, creating a barrier against electrical currents, and preventing short circuits or electrical leakage. These compounds are formulated to possess specific properties that enhance their insulating capabilities.
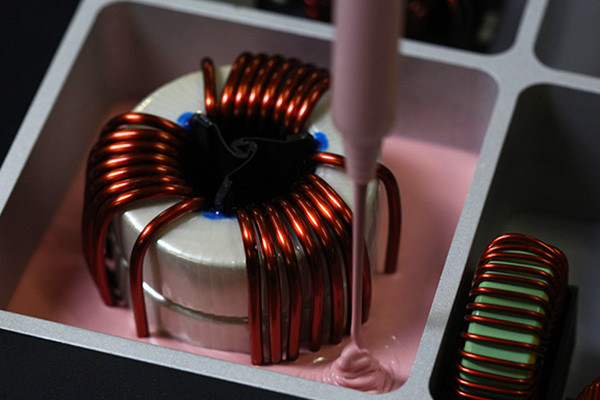
Firstly, high-voltage potting compounds typically consist of polymer matrices, such as epoxies, silicones, or polyurethanes, which are excellent insulators. These polymers have high dielectric strengths, which can withstand high electric fields without breaking down. This property is essential for preventing electrical breakdown or arcing within the encapsulated components.
Moreover, the formulation of these compounds involves the incorporation of fillers or additives that further enhance their insulation properties. Joint fillers include ceramics, such as alumina or silica, which increase the compound’s resistance to electrical current flow. Additionally, fillers can improve thermal conductivity, mechanical strength, and resistance to environmental factors like moisture and chemicals, ensuring long-term reliability.
Furthermore, high-voltage potting compounds undergo curing after application, forming a solid, homogeneous mass around the electronic components. This curing process eliminates voids or air pockets within the encapsulant, which could otherwise act as pathways for electrical conduction. The potting compound effectively isolates the components from external electrical influences by surrounding them.
In addition to their inherent insulating properties, high-voltage potting compounds provide mechanical protection to the encapsulated components. They shield delicate electronic parts from physical damage, vibration, and environmental hazards, further ensuring the integrity of the insulation over time.
Overall, high-voltage potting compounds offer comprehensive electrical insulation by combining the insulating properties of polymers with tailored formulations and curing processes. These mechanisms create a robust barrier that effectively isolates electronic components, safeguarding them from electrical hazards and maintaining the reliability of electrical systems.
What environmental conditions can high-voltage potting compounds withstand?
High-voltage potting compounds are designed to withstand various environmental conditions, ensuring encapsulated electronic components’ long-term reliability and performance in diverse applications. These compounds are formulated to provide protection against different environmental factors, including temperature extremes, moisture, chemicals, and mechanical stress.
Temperature Extremes: High-voltage potting compounds exhibit excellent thermal stability, allowing them to withstand extreme temperatures encountered in hot and cold environments. Depending on the specific formulation, they are engineered to maintain their electrical and mechanical properties over a broad temperature range, from sub-zero temperatures to elevated temperatures exceeding 100°C or even higher. This thermal resilience ensures that the encapsulated components remain insulated and operational under challenging thermal conditions.
Moisture Resistance: Moisture ingress can compromise the insulation properties of electronic components and lead to electrical failures. High-voltage potting compounds are formulated to provide robust moisture resistance, preventing water or humidity from penetrating the encapsulated area. This is achieved through the use of moisture-resistant polymers and additives, as well as through effective curing processes that eliminate voids where moisture could accumulate.
Chemical Resistance: In many applications, electronic components may be exposed to corrosive chemicals or solvents that could degrade conventional materials. High-voltage potting compounds are engineered to resist various chemicals, including acids, bases, oils, and solvents. This chemical resistance helps maintain the integrity of the encapsulation and ensures the long-term performance of the protected components in harsh chemical environments.
Mechanical Protection: Besides electrical insulation, high-voltage potting compounds provide mechanical protection to encapsulated components. They shield sensitive electronics from mechanical stresses such as vibration, shock, and impact. By encapsulating the elements in a sturdy matrix, these compounds prevent physical damage and ensure the reliability of the electronics, even in rugged operating conditions.
High-voltage potting compounds protect comprehensively against environmental factors, including temperature extremes, moisture, chemicals, and mechanical stress. They are suitable for various demanding applications across industries such as automotive, aerospace, industrial automation, and renewable energy.
What are the advantages of using high-voltage potting compounds in electronic assemblies?
High-voltage potting compounds offer several advantages when used in electronic assemblies, particularly in applications where insulation and protection against electrical hazards are critical. Here are the key advantages:
- Electrical Insulation: High voltage potting compounds provide excellent electrical insulation properties, preventing current leakage and breakdown even under high voltage stress. This insulation is crucial for maintaining the integrity and safety of electronic circuits, especially in high-voltage applications like power distribution systems or electric vehicle components.
- Dielectric Strength: These compounds possess high dielectric strength, which can withstand electric field stress without electrical breakdown. This property ensures the reliable operation of electronic assemblies in environments with high voltage fluctuations or surges, reducing the risk of short circuits or component damage.
- Protection Against Moisture and Contaminants: Potting compounds form a protective barrier around electronic components, sealing them from moisture, dust, chemicals, and other contaminants. This protection enhances the reliability and longevity of the assembly, especially in harsh or outdoor environments where exposure to environmental elements is a concern.
- Mechanical Stability: High voltage potting compounds offer excellent mechanical stability, providing structural support to delicate electronic components and preventing damage from vibrations, shocks, or thermal expansion/contraction cycles. This stability is crucial for maintaining the assembly’s integrity over time, reducing the risk of mechanical failure or performance degradation.
- Thermal Management: Some high-voltage potting compounds have good thermal conductivity properties, allowing efficient heat dissipation generated by electronic components. Effective thermal management helps prevent overheating, which can degrade performance and reliability, particularly in high-power applications or densely packed assemblies.
- Ease of Application: Many high-voltage potting compounds are designed for easy application, either by casting, molding, or dispensing methods. This simplifies manufacturing and enables efficient encapsulation of complex or irregularly shaped components, reducing assembly time and labor costs.
- Customization: Potting compounds come in various formulations with different properties, such as cure time, flexibility, and thermal conductivity. This allows engineers to select a compound tailored to the specific requirements of their application, ensuring optimal performance and reliability.
High-voltage potting compounds offer a range of advantages, including electrical insulation, dielectric strength, environmental protection, mechanical stability, thermal management, ease of application, and customization, making them essential for ensuring the reliability and safety of electronic assemblies operating under high-voltage conditions.
Are there any limitations or drawbacks to using high-voltage potting compounds?
High-voltage potting compounds are commonly used in electrical applications to encapsulate and protect components from environmental factors and mechanical stress. While they offer several advantages, such as excellent electrical insulation properties and resistance to moisture and chemicals, there are also limitations and drawbacks associated with their use.
- Cost: High-voltage potting compounds can be expensive compared to other encapsulation methods. The materials may have a higher upfront cost, and specialized equipment may be required for application, increasing overall expenses.
- Viscosity and Handling: Some high-voltage potting compounds have high viscosity, making them difficult to handle and apply, especially in intricate or densely packed assemblies. Proper mixing and application techniques are crucial to ensure uniform coverage and avoid voids or air pockets.
- Curing Time: Many high-voltage potting compounds require curing or setting time after application. This can prolong production lead times and may not be suitable for applications requiring quick turnaround times.
- Thermal Conductivity: High-voltage potting compounds provide excellent electrical insulation but may not always offer optimal thermal conductivity. In applications where heat dissipation is critical, such as in power electronics, the low thermal conductivity of some potting compounds could lead to overheating and reduced component lifespan.
- Mechanical Properties: The mechanical properties of high-voltage potting compounds, such as hardness and flexibility, vary depending on the formulation. In applications subject to mechanical stress or vibration, selecting the appropriate compound with suitable mechanical properties is crucial to prevent cracking or delamination over time.
- Compatibility: Compatibility with other materials used in the assembly is essential to prevent adverse chemical reactions or degradation over time. When selecting a potting compound, it’s crucial to consider factors such as thermal expansion coefficients and chemical compatibility.
- Repairability: Once components are encapsulated with high-voltage potting compounds, repair or replacement can be challenging and require specialized tools or processes. This lack of repairability could increase maintenance costs or lead to component replacement instead of repair.
While high-voltage potting compounds offer excellent electrical insulation and environmental protection, factors such as cost, viscosity, curing time, thermal conductivity, mechanical properties, compatibility, and repairability should be carefully considered to ensure they are suitable for the specific application.
How are high-voltage potting compounds applied in manufacturing processes?
High-voltage potting compounds play a crucial role in various manufacturing processes, particularly in industries dealing with electronics, electrical equipment, and power systems. These compounds encapsulate and insulate components, protecting environmental factors, mechanical stress, and electrical insulation. The application of high-voltage potting compounds involves several steps to ensure effective encapsulation and insulation:
- Surface Preparation: Before applying the potting compound, the surfaces of the components or devices must be thoroughly cleaned and prepared. This involves removing any contaminants, residues, or moisture that could affect the adhesion or performance of the potting material.
- Mold Preparation: In many cases, manufacturers use molds or enclosures to contain the potting compound during curing. These molds must be prepared by applying release agents to prevent the potting material from sticking to the mold surfaces.
- Mixing: High voltage potting compounds typically come in two-part formulations—resin and hardener. Properly mixing these components is crucial to ensure uniformity and optimal curing properties. This is often done using specialized equipment to maintain accurate ratios and minimize air entrapment.
- Application: The mixed potting compound is then applied to the components or devices manually or using automated dispensing equipment. Careful attention is paid to ensure complete coverage and proper encapsulation of critical areas, such as electrical connections and sensitive components.
- Curing: Once applied, the potting compound undergoes a curing process to harden and form a solid encapsulation. Curing can occur at ambient temperature or may require elevated temperatures depending on the specific formulation of the potting material. Manufacturers often use curing ovens or other controlled environments to facilitate the curing process.
- Post-Curing Inspection: After curing, the encapsulated components undergo inspection to ensure that the potting compound has formed a secure bond and there are no defects such as voids, cracks, or delamination. Any imperfections are addressed promptly to maintain product quality and reliability.
- Testing: Finally, encapsulated components may undergo various electrical and mechanical tests to verify their performance and reliability under high voltage conditions. This includes insulation resistance, dielectric strength, thermal cycling, and vibration resistance tests.
The application of high-voltage potting compounds in manufacturing processes involves careful preparation, precise mixing, thorough application, controlled curing, and rigorous testing to ensure the integrity and reliability of encapsulated components in demanding electrical and electronic applications.
What considerations are essential when selecting a high-voltage potting compound?
Selecting the suitable high-voltage potting compound is critical to ensuring the long-term performance and reliability of encapsulated electronic or electrical components. Several key considerations must be taken into account during the selection process:
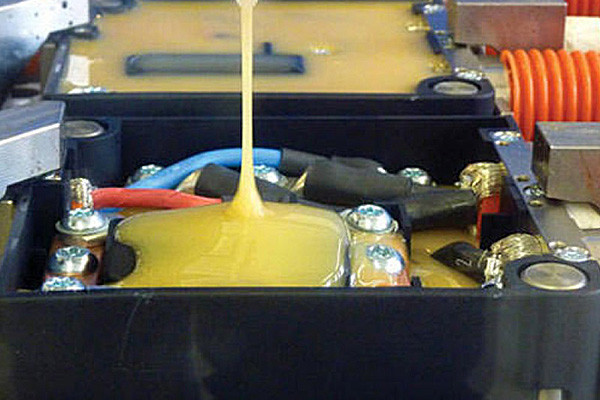
- Dielectric Strength: Perhaps the most crucial consideration for high voltage applications, dielectric strength refers to the material’s ability to withstand electrical stress without breaking down. A potting compound with high dielectric strength is essential to prevent electrical arcing and insulation failure.
- Thermal Stability: High voltage components can generate significant heat during operation. Thus, choosing a potting compound with excellent thermal stability is essential to withstand elevated temperatures without degrading or losing its insulating properties.
- Chemical Resistance: Encapsulated components may be exposed to various chemicals, solvents, or environmental conditions. A potting compound that exhibits resistance to these substances ensures long-term durability and protection against corrosion or degradation.
- Flexibility vs. Rigidity: Depending on the application, flexibility or rigidity may be desired. Flexible potting compounds can absorb mechanical stress and vibration, making them suitable for applications subject to movement or shock. On the other hand, rigid compounds offer better structural support and protection against physical damage.
- Curing Time and Process: The curing time and process of the potting compound should align with the manufacturing requirements. Some applications may necessitate fast-curing materials for rapid production cycles, while others may require longer curing times for optimal performance.
- Adhesion to Substrates: The potting compound must adhere well to the substrate material to ensure proper encapsulation and prevent delamination or voids. Compatibility with various substrate materials such as metals, plastics, or ceramics is essential.
- Environmental Considerations: Factors such as moisture resistance, UV stability, and resistance to environmental extremes (e.g., humidity temperature fluctuations) should be evaluated based on the application’s operating environment.
- Regulatory Compliance: Compliance with industry standards and regulations, such as UL (Underwriters Laboratories) or IPC (Association Connecting Electronics Industries) specifications, ensures that the encapsulated components meet safety and performance requirements.
By carefully considering these factors, manufacturers can select the most suitable high-voltage potting compound for their specific application, ensuring optimal performance, reliability, and longevity of encapsulated electronic or electrical devices.
Can high-voltage potting compounds be customized for specific applications?
Yes, high-voltage potting compounds can be customized for specific applications, offering tailored solutions to meet the unique requirements of various industries and electronic devices. Potting compounds are materials encapsulating or protecting electronic components, particularly those subjected to high voltage, extreme temperatures, or harsh environmental conditions. Customization of these compounds involves several considerations:
- Electrical Properties: High voltage applications demand materials with excellent electrical insulation properties to prevent electrical leakage or breakdown. Custom formulations can be adjusted to meet specific dielectric strength, insulation resistance, and thermal conductivity requirements.
- Mechanical Strength: Potting compounds must provide sufficient mechanical support and structural integrity to protect delicate electronic components from physical damage due to vibration, shock, or thermal expansion. Customization allows for adjusting the compound’s hardness, flexibility, and impact resistance to suit the application.
- Thermal Performance: Effective heat dissipation is critical in high-voltage applications to prevent overheating and ensure optimal performance and reliability of electronic components. Custom formulations can be engineered to enhance thermal conductivity and stability, dissipating heat efficiently and maintaining operational temperatures within safe limits.
- Chemical Compatibility: Depending on the application, potting compounds may come into contact with various chemicals or environmental factors. Customization allows the selection of materials that resist corrosion, moisture ingress, and chemical exposure, ensuring long-term reliability and durability.
- Environmental Considerations: Different applications may require potting compounds to meet specific environmental standards, such as RoHS compliance or resistance to UV radiation. Custom formulations can be developed to address these requirements while maintaining performance characteristics.
- Application Method: Customized potting compounds can be formulated to accommodate specific application methods, whether through manual dispensing, injection molding, or automated processes, ensuring ease of use and efficient encapsulation of electronic components.
By working closely with manufacturers and leveraging expertise in material science and engineering, customized high-voltage potting compounds can be developed to address the precise needs and challenges of diverse applications, enhancing the performance, reliability, and longevity of electronic devices and systems.
What testing standards are applicable for evaluating high-voltage potting compounds?
Testing standards for high-voltage potting compounds are critical to ensure their performance, safety, and reliability in various electrical applications. Several standards apply specifically to the testing of these compounds:
- ASTM D149 – Standard Test Method for Dielectric Breakdown Voltage and Dielectric Strength of Solid Electrical Insulating Materials at Commercial Power Frequencies: This standard outlines procedures for determining the dielectric breakdown voltage and dielectric strength of solid electrical insulating materials, including potting compounds, under specific conditions.
- IEC 60243 – Electrical strength of insulating materials: This International Electrotechnical Commission (IEC) standard provides methods for determining the electrical strength of insulating materials, including potting compounds, through tests such as breakdown voltage measurement and tracking resistance.
- UL 746E – Polymeric Materials – Industrial Laminates, Filament Wound Tubing, Vulcanized Fiber, and Materials Used in Printed-Wiring Boards: This standard by Underwriters Laboratories (UL) covers the evaluation of electrical insulating materials, including potting compounds, for specific applications and performance characteristics.
- IEC 60085 – Electrical insulation – Thermal evaluation and designation: This standard specifies methods for the thermal assessment and designation of electrical insulation materials, which are essential for assessing the thermal properties of potting compounds under high voltage conditions.
- IEEE Std 383™-2015 – IEEE Standard for Qualifying Class 1E Electrical Cables, Field Splices, and Connections for Nuclear Power Generating Stations: While primarily focused on nuclear power applications, this IEEE standard guides testing electrical insulation materials, including potting compounds, for reliability and safety in high-voltage environments.
These standards encompass various tests, such as dielectric strength, thermal evaluation, tracking resistance, and mechanical properties assessment. Adhering to these standards ensures that high-voltage potting compounds meet necessary performance criteria and safety requirements for their intended applications, thereby reducing risks of electrical failures and ensuring operational reliability.
What role do thermal properties play in high-voltage potting compounds?
Thermal properties are critical in high-voltage potting compounds, especially when electrical components are subjected to high temperatures or thermal cycling. Potting compounds encapsulate and protect electronic components from environmental factors such as moisture, dust, and vibration while providing electrical insulation. Here’s how thermal properties are significant in these compounds:
- Heat Dissipation: High voltage components often generate heat during operation. Effective heat dissipation is crucial to prevent overheating, which can degrade the performance and lifespan of electronic devices. Potting compounds with good thermal conductivity help transfer heat away from the components, reducing the risk of thermal damage.
- Thermal Stability: High voltage environments can subject potting materials to significant temperature variations. Thermal stability ensures that the potting compound maintains its structural integrity and electrical properties over a wide temperature range. Compounds with low coefficients of thermal expansion (CTE) are less prone to cracking or delamination when exposed to temperature fluctuations.
- Dielectric Strength at Elevated Temperatures: Dielectric strength refers to a material’s ability to withstand high electric fields without electrical breakdown. Maintaining dielectric strength at elevated temperatures is crucial for preventing electrical failures in high-voltage applications. Potting compounds with high thermal stability often exhibit good dielectric properties even at elevated temperatures, ensuring reliable insulation.
- Thermal Cycling Resistance: Electronic devices may undergo thermal cycling as they experience repeated heating and cooling cycles during operation. Potting compounds with good thermal cycling resistance can withstand these fluctuations without undergoing significant dimensional changes or loss of properties, thus ensuring long-term reliability.
- Compatibility with Other Materials: High-voltage potting compounds must also be compatible with the encapsulated materials, such as metals, plastics, or ceramics. Mismatched thermal expansion coefficients between the potting compound and the encapsulated components can lead to mechanical stress and potential damage over time.
Thermal properties such as thermal conductivity, stability, dielectric strength, resistance to thermal cycling, and compatibility with other materials are crucial considerations in the selection and performance of high-voltage potting compounds. These properties ensure effective heat management, electrical insulation, and long-term reliability of electronic devices operating in demanding environments.
How do high-voltage potting compounds resist moisture and other contaminants?
High-voltage potting compounds are specially formulated materials that protect electronic components and devices from environmental factors such as moisture and contaminants while providing electrical insulation. These compounds typically comprise a polymer matrix, fillers, and additives tailored to meet specific performance requirements.
One primary mechanism by which high-voltage potting compounds resist moisture and contaminants is their encapsulation properties. When applied, these compounds form a protective barrier around the electronic components, sealing them from the external environment. This barrier prevents moisture ingress, which can lead to corrosion, short circuits, and other electrical failures.
The polymer matrix used in these compounds plays a crucial role in their moisture resistance. Epoxy resins or silicone rubbers are typically chosen for their excellent dielectric properties and resistance to environmental stressors. These polymers have inherently low water absorption rates, making them suitable for applications where moisture ingress must be minimized.
Fillers are added to high-voltage potting compounds to enhance their mechanical strength, thermal conductivity, and resistance to moisture penetration. Joint fillers include silica, alumina, and various mineral fillers. These fillers help to reinforce the polymer matrix, improving the overall durability and performance of the potting compound.
Additionally, additives such as antioxidants and UV stabilizers may be incorporated into the formulation to enhance resistance to environmental degradation further. Antioxidants help prevent oxidation and degradation of the polymer matrix, while UV stabilizers protect against the harmful effects of ultraviolet radiation, which can degrade the compound over time.
Furthermore, proper application techniques, such as vacuum or pressure, can help ensure that the potting compound fully encapsulates the electronic components, leaving no gaps or voids where moisture or contaminants could penetrate.
High-voltage potting compounds resist moisture and other contaminants through encapsulation, polymer matrix properties, filler reinforcement, and additives. By effectively sealing electronic components from the external environment, these compounds help prolong the lifespan and reliability of electrical devices operating in demanding conditions.
Are there any safety precautions when working with high-voltage potting compounds?
Working with high-voltage potting compounds involves dealing with materials designed to encapsulate electrical components to protect them from environmental factors such as moisture, dust, and vibrations. However, handling these compounds with care is crucial due to the potential risks associated with high-voltage applications. Here are some safety precautions to consider:
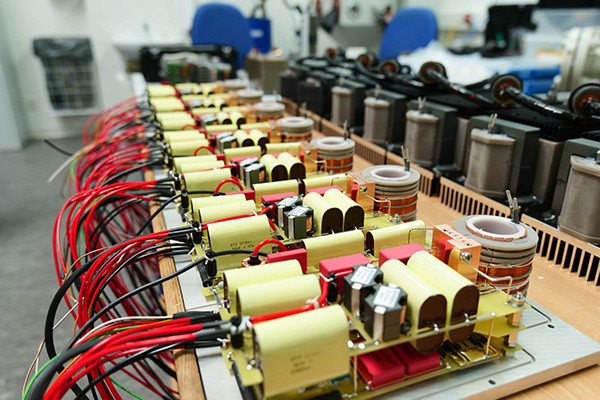
- Personal Protective Equipment (PPE):Always wear appropriate PPE, such as safety glasses, gloves, and protective clothing, to prevent direct contact with the compound. High-voltage gloves and face shields may be necessary when working with extremely high voltages.
- Ventilation:Ensure adequate ventilation in the working area to prevent inhalation of potentially harmful fumes emitted during the curing process of the potting compound. Work in well-ventilated areas or use local exhaust ventilation to remove fumes from the workspace.
- Avoid Skin Contact:High-voltage potting compounds can cause skin irritation or allergic reactions upon contact. Minimize skin exposure by wearing gloves and avoid direct contact with the compound. In case of skin contact, immediately wash the affected area with soap and water.
- Eye Protection:Wear safety goggles to protect your eyes from splashes or accidental contact with the potting compound. If the compound gets into the eyes, rinse thoroughly with water and seek medical attention promptly.
- Follow Manufacturer Guidelines:Adhere to the manufacturer’s instructions and recommendations regarding the handling, mixing, and applying the potting compound. Use the compound only for its intended purpose and within the specified temperature and humidity ranges.
- Grounding:Ensure that all equipment and surfaces are properly grounded to minimize the risk of electric shock when working with high-voltage components. Follow established electrical safety procedures and use insulated tools when necessary.
- Emergency Preparedness:Be prepared for emergencies by having a first aid kit, eye wash station, and fire extinguisher readily available in the work area. Train personnel on emergency response procedures and evacuation routes.
- Storage and Disposal:Store high-voltage potting compounds in a cool, dry place away from direct sunlight and ignition sources. Follow proper procedures for disposing of unused or expired compounds by local regulations.
By following these safety precautions, you can minimize the risks associated with working with high-voltage potting compounds and ensure a safe working environment for yourself and others involved in the process.
Can high-voltage potting compounds be removed or reworked?
High-voltage potting compounds are commonly used in electronics and electrical applications to encapsulate components, providing insulation and protection against environmental factors such as moisture, heat, and mechanical stress. These compounds typically consist of resins, fillers, and additives that withstand high voltages and temperatures.
Removing or reworking high-voltage potting compounds can be challenging due to their intended purpose of creating a durable, insulating barrier around components. However, under certain circumstances, removing or reworking the potting material may be necessary.
To remove high-voltage potting compounds, several methods can be employed depending on the specific compound and application:
- Chemical Solvents: Some potting compounds can be softened or dissolved using chemical solvents. However, care must be taken to ensure compatibility with the surrounding materials and to avoid damaging the components.
- Thermal Methods: Heating the potting material can soften it, making it easier to remove mechanically. This method requires precise control of temperature to prevent damage to the components.
- Mechanical Removal: Mechanical methods such as scraping, cutting, or grinding may be necessary to remove the potting material. Specialized tools and equipment may be required, and care must be taken to avoid damaging the components.
- Ultrasonic Removal: Ultrasonic techniques can break down and remove potting compounds without damaging the components. Ultrasonic energy is applied to the material, causing it to break apart and separate from the components.
- Abrasive Blasting: In some cases, abrasive blasting techniques such as sandblasting or bead blasting may be used to remove potting compounds. This method is more aggressive and may only be suitable for some applications.
Reworking high-voltage potting compounds is typically more challenging than removal and often involves replacing damaged components or reapplying the potting material after modifications. It requires careful planning and execution to maintain the integrity of the electrical system.
While high-voltage potting compounds are designed to provide durable insulation and protection, they can be removed or reworked using various methods, including chemical solvents, thermal techniques, mechanical removal, ultrasonic methods, and abrasive blasting. However, these processes require carefully considering the specific application and potential risks to the components involved.
What advancements have been made in high-voltage potting compound technology recently?
In recent years, high-voltage potting compound technology advancements have primarily focused on enhancing performance, durability, and safety across various applications, including electrical insulation, electronic components, and power distribution systems.
One notable advancement lies in developing new materials with improved dielectric properties. Engineers and researchers have explored novel formulations using epoxy resins, silicone compounds, and polyurethanes to achieve higher dielectric strength, reduced dielectric loss, and increased thermal stability. These materials offer better resistance to electrical breakdown under high voltages, ensuring enhanced reliability in demanding environments.
Furthermore, manufacturers have been refining the manufacturing processes to achieve more precise control over material properties and application techniques. This includes advancements in curing methods such as UV curing, which allows for faster processing times and better control over the curing process, leading to more consistent and reliable results.
Another area of progress is the development of eco-friendly and sustainable high-voltage potting compounds. With growing environmental concerns, there has been a shift towards using renewable and biodegradable materials in compound formulations, reducing the environmental impact while maintaining high performance.
In addition to material improvements, advancements in nanotechnology have also contributed to enhancing the properties of high-voltage potting compounds. Incorporating nano-sized fillers such as silica nanoparticles or nanoclays can improve mechanical strength, thermal conductivity, and dielectric properties, further enhancing the overall performance and reliability of the potting compounds.
Moreover, there have been efforts to integrate intelligent functionalities into potting compounds, such as self-healing properties or embedded sensors for real-time monitoring of electrical parameters and insulation health. These innovations enable predictive maintenance and enhance electrical systems’ overall safety and reliability.
Recent advancements in high-voltage potting compound technology have been driven by the need for higher performance, improved reliability, and sustainability, with continuous research and development efforts to push the boundaries of what is achievable in electrical insulation and protection applications.
How do cost considerations factor into the selection of high-voltage potting compounds?
Cost considerations are significant in selecting high-voltage potting compounds, as they directly impact a project’s overall budget or manufacturing process. Several factors related to cost influence the choice of potting compounds:
- Material Cost: The initial cost of the potting compound is a primary consideration. Different types of potting compounds vary in composition, such as silicone, epoxy, or polyurethane, and each may have a different price point based on raw material costs, manufacturing processes, and market demand.
- Application Efficiency: The efficiency of the application affects labor costs and productivity. Potting compounds that require complex mixing procedures or specialized equipment may incur higher labor costs than those that can be easily applied using standard methods. Compounds with longer curing times may tie up production resources for extended periods, affecting overall throughput and potentially increasing labor costs.
- Performance Requirements: Balancing cost with performance is crucial. While cheaper potting compounds may offer initial cost savings, they may not provide the necessary electrical insulation, thermal conductivity, or mechanical strength required for the application. Choosing a compound based on cost without considering performance requirements can lead to failures, warranty claims, and costly rework.
- Long-Term Durability: Consideration of the long-term durability of the potting compound is essential to avoid premature failure and associated costs. Cheaper compounds may degrade more quickly under environmental factors such as temperature fluctuations, humidity, or chemical exposure, leading to increased maintenance or replacement costs.
- Regulatory Compliance: Compliance with industry standards and regulations may be necessary, especially in applications where safety is paramount. Potting compounds that meet relevant regulatory requirements may have higher upfront costs due to additional testing and certification processes but can mitigate risks associated with non-compliance, such as fines or liability issues.
While cost considerations are important in selecting high-voltage potting compounds, they must be balanced with factors such as application efficiency, performance requirements, long-term durability, and regulatory compliance to ensure the overall effectiveness and reliability of the final product or application.
What future trends are anticipated in developing and using high-voltage potting compounds?
High-voltage potting compounds are crucial in various industries, especially in electrical and electronics applications where insulation and protection against high voltages are paramount. Several factors, including technological advancements, regulatory requirements, and market demands, shape anticipated future trends in the development and use of these compounds.
- Improved Dielectric Properties: Future high-voltage potting compounds are expected to exhibit enhanced dielectric properties to withstand higher voltages and reduce the risk of electrical breakdown. This involves the development of materials with higher dielectric strength and lower dielectric loss, allowing for more efficient and reliable insulation in high-voltage applications.
- Miniaturization and Higher Power Density: With the trend towards miniaturization and higher power density in electronic devices and power systems, a growing demand for high-voltage potting compounds can provide adequate insulation in smaller, more densely packed components. Future formulations may focus on achieving higher thermal conductivity while maintaining excellent electrical insulation properties to dissipate heat effectively in compact designs.
- Environmental Sustainability: Increasing environmental regulations and growing awareness of sustainability issues drive the demand for eco-friendly materials in all industries, including electronics. Future high-voltage potting compounds will be formulated using more sustainable ingredients and manufacturing processes, focusing on reducing environmental impact without compromising performance or reliability.
- Compatibility with Advanced Substrates: As new materials and substrates, such as wide bandgap semiconductors and advanced polymers, gain traction in high-voltage applications, there will be a need for potting compounds that are compatible with these materials. Future trends may involve the development of specialized formulations tailored to specific substrate materials to ensure optimal adhesion, thermal stability, and electrical insulation.
- Integration of Smart Technologies: With the rise of the Internet of Things (IoT) and smart devices, there is potential for high-voltage potting compounds to incorporate innovative features such as self-healing capabilities or embedded sensors for real-time monitoring of insulation integrity. These advancements can enhance predictive maintenance strategies and improve overall system reliability.
Future trends in high-voltage potting compounds are likely to focus on enhancing dielectric properties, adapting to evolving technological requirements, addressing environmental concerns, ensuring compatibility with advanced substrates, and integrating intelligent functionalities to meet the needs of modern electrical and electronics applications.
Conclusion:
High-voltage potting compounds are indispensable in modern electronics, providing essential insulation and protection for components operating in demanding environments. From enhancing reliability to ensuring safety, these compounds offer a range of benefits across various industries. As technology advances and applications evolve, the development of high-voltage potting compounds continues to play a vital role in meeting the ever-growing demands of electrical systems operating at high voltages.
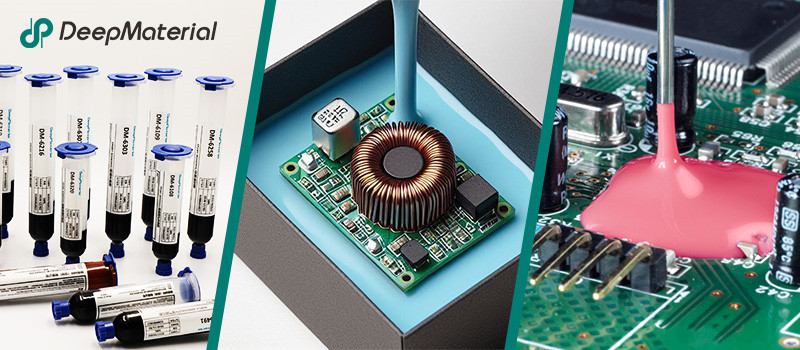
About DeepMaterial
DeepMaterial is a trusted supplier of encapsulant materials that are used in electronics manufacturing worldwide. From chip on board encapsulants such as glob top material to conformal coatings, underfills, low pressure molding, and potting solutions, DeepMaterial offers a full range of circuit board protection materials that effectively protect circuit boards while help reduce costs. More…Deepmaterial is a the manufacturer of epoxy adhesives including hardeners, metalbond, and metal filled resins. Structural, toughened medium viscosity, and non-sag adhesives are also offered. Some adhesives are resistant to thermal shock, chemical, vibration dampening, and impact. Suitable for metals, plastics, wood, and ceramics. Serves electronics, aerospace, automotive, tooling, marine, and construction industries. REACH and RoHS compliant. FDA approved. UL listed. Meets military specifications. We are the one of best adhesive manufacturers in China.
Blogs & News
Potting compounds are at the frontline of electronics assembly, delivering effective protection in challenging environmental conditions while improving mechanical strength and offering high electric insulation. Used within a variety of industries, electrical potting compounds are found within a broad range of consumer electronics, as well as used in applications across the automotive, aerospace, and other industries where electronic assemblies are prevalent.
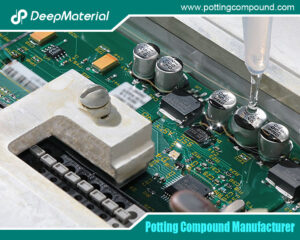
Silicone Potting Compound for Electronics
Silicone Potting Compound for Electronics In the rapidly evolving world of electronics, ensuring the reliability, durability, and performance of electronic components is paramount. One critical
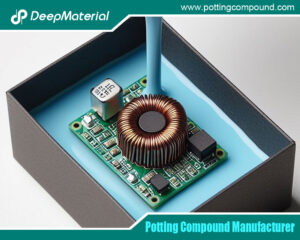
Potting Compound vs. Epoxy: A Comprehensive Comparison
Potting Compound vs. Epoxy: A Comprehensive Comparison In the world of electronics, manufacturing, and material encapsulation, two terms frequently come up: potting compounds and epoxy.
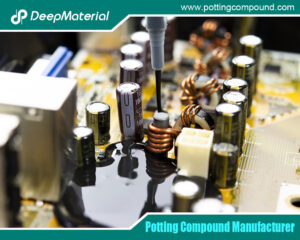
Potting Compound for PCB
Potting Compound for PCB A potting compound is a liquid or semi-liquid material that is poured or injected over a PCB or electronic assembly, then
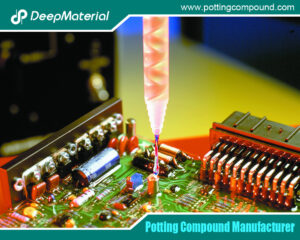
In – depth Analysis of the Curing Characteristics of Electronic Potting Compounds
In – depth Analysis of the Curing Characteristics of Electronic Potting Compounds Electronic potting compounds play a vital role in the electronics industry. They can
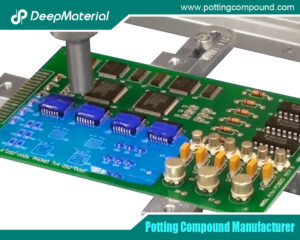
A Comprehensive Analysis of the Environmental Performance of Encapsulating Materials: From Regulations to Practices
A Comprehensive Analysis of the Environmental Performance of Encapsulating Materials: From Regulations to Practices In modern industrial manufacturing, encapsulating materials are widely used in numerous

A Comprehensive Analysis of PCB Encapsulation Quality Inspection: Innovative Application of Non-Destructive Testing Technologies
A Comprehensive Analysis of PCB Encapsulation Quality Inspection: Innovative Application of Non-Destructive Testing Technologies In the field of electronic manufacturing, the encapsulation process of printed
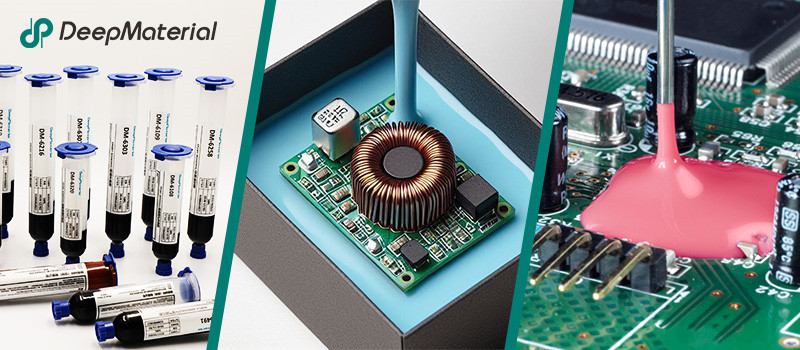
About DeepMaterial
DeepMaterial is a trusted supplier of encapsulant materials that are used in electronics manufacturing worldwide. From chip on board encapsulants such as glob top material to conformal coatings, underfills, low pressure molding, and potting solutions, DeepMaterial offers a full range of circuit board protection materials that effectively protect circuit boards while help reduce costs. More…Deepmaterial is a the manufacturer of epoxy adhesives including hardeners, metalbond, and metal filled resins. Structural, toughened medium viscosity, and non-sag adhesives are also offered. Some adhesives are resistant to thermal shock, chemical, vibration dampening, and impact. Suitable for metals, plastics, wood, and ceramics. Serves electronics, aerospace, automotive, tooling, marine, and construction industries. REACH and RoHS compliant. FDA approved. UL listed. Meets military specifications. We are the one of best adhesive manufacturers in China.
Blogs & News
Potting compounds are at the frontline of electronics assembly, delivering effective protection in challenging environmental conditions while improving mechanical strength and offering high electric insulation. Used within a variety of industries, electrical potting compounds are found within a broad range of consumer electronics, as well as used in applications across the automotive, aerospace, and other industries where electronic assemblies are prevalent.
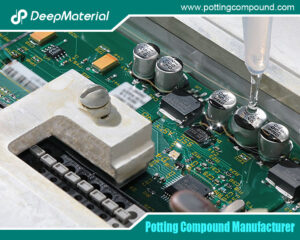
Silicone Potting Compound for Electronics
Silicone Potting Compound for Electronics In the rapidly evolving world of electronics, ensuring the reliability, durability, and performance of electronic components is paramount. One critical
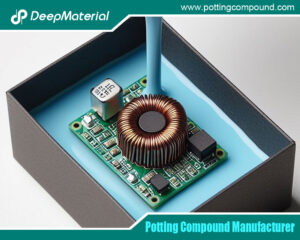
Potting Compound vs. Epoxy: A Comprehensive Comparison
Potting Compound vs. Epoxy: A Comprehensive Comparison In the world of electronics, manufacturing, and material encapsulation, two terms frequently come up: potting compounds and epoxy.
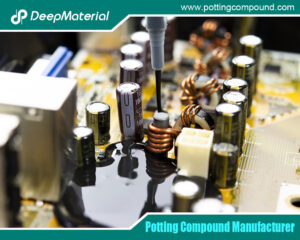
Potting Compound for PCB
Potting Compound for PCB A potting compound is a liquid or semi-liquid material that is poured or injected over a PCB or electronic assembly, then
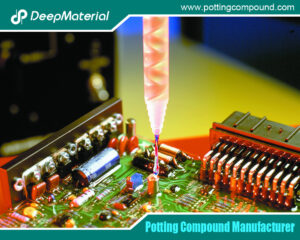
In – depth Analysis of the Curing Characteristics of Electronic Potting Compounds
In – depth Analysis of the Curing Characteristics of Electronic Potting Compounds Electronic potting compounds play a vital role in the electronics industry. They can
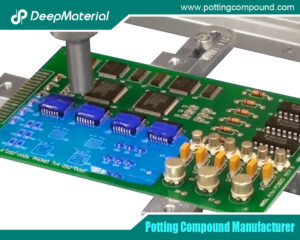
A Comprehensive Analysis of the Environmental Performance of Encapsulating Materials: From Regulations to Practices
A Comprehensive Analysis of the Environmental Performance of Encapsulating Materials: From Regulations to Practices In modern industrial manufacturing, encapsulating materials are widely used in numerous

A Comprehensive Analysis of PCB Encapsulation Quality Inspection: Innovative Application of Non-Destructive Testing Technologies
A Comprehensive Analysis of PCB Encapsulation Quality Inspection: Innovative Application of Non-Destructive Testing Technologies In the field of electronic manufacturing, the encapsulation process of printed