Light-Curable Conformal Coating
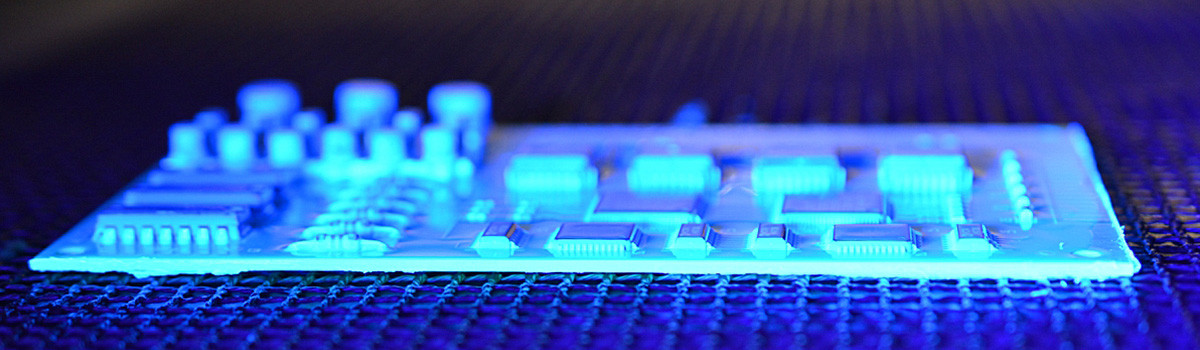
Light-curable conformal coatings are essential in various industries, offering protection and insulation for electronic components and assemblies. These coatings are applied in thin layers and cured using ultraviolet (UV) light, providing rapid and efficient encapsulation. Because they can conform to the intricate shapes of electronic devices, they ensure reliable performance in challenging environments. This category explores the intricacies of light-curable conformal coatings, from their composition and application methods to their advantages and applications across different industries.
Table of Contents
ToggleWhat are light-curable conformal coatings?
Light-curable conformal coatings are specialized materials used in electronics manufacturing to protect printed circuit boards (PCBs) and electronic components from environmental factors such as moisture, dust, chemicals, and temperature extremes. These coatings are applied in a liquid form and then cured using ultraviolet (UV) or visible light, providing a quick and efficient way to encapsulate and protect delicate electronic assemblies.
These coatings typically consist of oligomers, monomers, photoinitiators, and additives. When exposed to light of specific wavelengths, the photoinitiators in the coating initiate a polymerization reaction, causing the liquid material to solidify and form a protective film over the surface of the PCB or electronic component. This curing process occurs rapidly, often within seconds or minutes, depending on the intensity and wavelength of the light source.
One critical advantage of light-curable conformal coatings is their rapid curing time, which enables faster production cycles and increased throughput in manufacturing operations. Additionally, these coatings offer excellent adhesion to various substrates, including plastics, metals, and ceramics, ensuring reliable protection for electronic assemblies.
Moreover, light-curable conformal coatings provide uniform coverage and thickness, even on complex or irregularly shaped surfaces, thanks to their low viscosity and ability to flow into tight spaces before curing. This uniformity helps maintain the PCB’s electrical integrity and prevent issues such as corrosion, short circuits, and insulation breakdown.
Furthermore, these coatings often exhibit excellent chemical and mechanical resistance, safeguarding electronic assemblies from harsh operating environments in automotive, aerospace, medical, and industrial applications. They may also offer additional properties such as thermal conductivity, flame retardancy, and electrical insulation, depending on the specific formulation and requirements of the application.
Light-curable conformal coatings offer a versatile and efficient solution for protecting electronic assemblies. They combine rapid curing times, uniform coverage, and robust environmental resistance to ensure the reliability and longevity of electronic devices in various industries.
How do light-curable conformal coatings differ from traditional coatings?
Light-curable conformal coatings represent a significant advancement over traditional coatings due to their unique properties and application process. These coatings, often used in electronics manufacturing and other industries requiring precision protection, offer several key differences from their traditional counterparts.
- Curing Method: One of the most significant distinctions is the curing method. Traditional coatings often rely on heat, air drying, or chemical reactions to cure and form a protective layer. In contrast, light-curable coatings use ultraviolet (UV) or visible light to initiate a rapid polymerization reaction, instantly solidifying the coating upon exposure. This curing mechanism allows for faster processing times and increased throughput in manufacturing operations.
- Speed and Efficiency: Light-curable coatings offer unparalleled speed and efficiency in application. Because they cure rapidly upon exposure to light, there is no need for extended drying or curing times. This reduces manufacturing cycle times and minimizes the risk of defects, such as dust or debris settling onto the coating surface during the curing process.
- Precision and Control: Light-curable coatings provide exceptional precision and control during application. Manufacturers can precisely target the areas requiring coating, ensuring uniform coverage and avoiding overspray or waste. Additionally, the curing process can be tailored to specific requirements, allowing for adjustments in intensity, duration, and wavelength of the light source to optimize curing conditions for different substrates and coating formulations.
- Chemical Resistance and Performance: Despite their rapid curing process, light-curable coatings offer comparable or even superior performance to traditional coatings regarding chemical resistance, durability, and protection against environmental factors such as moisture, abrasion, and corrosion. These coatings can be formulated to meet various industry standards and specifications, ensuring reliable long-term performance in demanding applications.
- Environmental Considerations: Light-curable coatings often have lower VOC (volatile organic compound) emissions than traditional solvent-based coatings, making them more environmentally friendly. Their rapid curing process also consumes less energy, reducing their environmental footprint.
Light-curable conformal coatings offer a revolutionary approach to protective coating applications, combining speed, precision, and performance advantages unmatched by traditional coating methods.
What are the primary components of light-curable conformal coatings?
Light-curable conformal coatings are used in various industries, including electronics, automotive, aerospace, and medical devices, to protect delicate components from environmental factors such as moisture, dust, chemicals, and temperature extremes. These coatings offer several advantages over traditional coatings, including rapid curing times, low VOC emissions, and superior performance characteristics. The primary components of light-curable conformal coatings typically include:
- Resins: Resins form the backbone of the coating and provide adhesion, flexibility, and chemical resistance. Typical resins in light-curable conformal coatings include acrylics, epoxies, urethanes, and silicones. Each resin type offers properties tailored to the application requirements, such as thermal stability, moisture resistance, or flexibility.
- Photoinitiators: Photoinitiators are compounds that initiate the curing process when exposed to light of a specific wavelength. They absorb energy from the light source and generate reactive species that facilitate cross-linking of the resin molecules, forming a solid coating. Photoinitiators are crucial for achieving rapid curing times and ensuring uniform curing throughout the coating thickness.
- Additives: Various additives may be incorporated into light-curable conformal coatings to modify their properties and enhance performance. Antioxidants, UV stabilizers, and hindered amine light stabilizers (HALS) can improve resistance to degradation caused by exposure to UV radiation and other environmental factors. Additionally, fillers such as silica or talc may be included to enhance mechanical properties or control the viscosity of the coating.
- Solvents: Some formulations of light-curable conformal coatings may contain small amounts of solvents to adjust viscosity, improve wetting, or aid in the application process. However, solvents are minimized in these coatings to reduce VOC emissions and environmental impact.
- Pigments and dyes: Pigments and dyes may be added to light-curable conformal coatings to provide color or opacity. These additives can be used for aesthetic purposes or to enhance the visibility of coated components for quality control or identification purposes.
Overall, carefully selecting and formulating these primary components ensure that light-curable conformal coatings deliver the desired performance characteristics, such as adhesion, durability, and protection, while also meeting regulatory requirements and environmental considerations.
What role does UV light play in curing light-curable conformal coatings?
UV light is crucial in curing light-curable conformal coatings and catalyzing polymerization reactions. Light-curable conformal coatings typically comprise monomers, oligomers, photoinitiators, and additives. When exposed to UV light, these coatings undergo a photochemical reaction known as photopolymerization, transforming from a liquid state to a solid film.
The process begins with the absorption of UV photons by the photoinitiator molecules within the coating. These molecules then undergo a photochemical reaction, splitting into reactive species, typically free radicals or cations. These reactive species initiate the polymerization of the monomers and oligomers in the coating formulation.
UV light is the energy source that activates the photoinitiators and triggers the polymerization reaction. The wavelength of UV light used for curing typically falls within the range of 200 to 400 nanometers, with specific formulations requiring particular wavelengths for optimal curing efficiency. UV light in this range possesses sufficient energy to promote the necessary chemical reactions without causing significant heat buildup or damaging the substrate.
Various factors, including the intensity and wavelength of the UV light source, the formulation of the coating material, the presence of oxygen, and the thickness of the coating layer, influence the efficiency of UV curing. UV intensity directly affects the polymerization rate, with higher intensities leading to faster curing times. The coating formulation must also be carefully designed to ensure compatibility with the chosen photoinitiator and UV wavelength range.
Furthermore, oxygen inhibition can hinder the curing process by scavenging reactive species and slowing down polymerization. To mitigate this effect, inert atmospheres or oxygen-blocking coatings may be utilized. Moreover, the thickness of the coating layer must be controlled to ensure uniform curing throughout the material, as excessive thickness can impede the penetration of UV light and result in incomplete curing.
UV light plays a fundamental role in curing light-curable conformal coatings by initiating photopolymerization reactions. Through the activation of photoinitiators, UV light triggers the conversion of liquid coatings into solid films, offering rapid curing, improved productivity, and enhanced performance in various industrial applications.
What are the advantages of using light-curable conformal coatings?
Light-curable conformal coatings offer several advantages compared to traditional ones, making them increasingly popular in various industries. Here are some key benefits:
- Rapid Cure Time: One of the primary advantages of light-curable conformal coatings is their rapid cure time. These coatings cure almost instantly when exposed to UV light, significantly reducing processing time compared to traditional coatings that require hours or days to cure. This rapid curing enables faster production cycles and increased throughput, enhancing productivity and efficiency in manufacturing processes.
- Improved Process Control: Light-curable coatings provide better process control due to their instant curing mechanism. Manufacturers can precisely control the application and curing process, ensuring consistent coating thickness and quality across batches. This level of control minimizes variability and reduces the likelihood of defects, ultimately improving product reliability and performance.
- Energy Efficiency: UV-curable coatings require minimal energy for curing compared to heat-curable alternatives. Since the curing process relies on UV light, there is no need for elevated temperatures or lengthy heating cycles, resulting in lower energy consumption and reduced operational costs. This makes light-curable coatings an environmentally friendly option while contributing to manufacturers’ cost savings.
- Low Volatile Organic Compounds (VOCs): Light-curable conformal coatings typically have fewer VOC emissions than solvent-based coatings. This is advantageous from environmental and occupational health perspectives, as it helps reduce air pollution and minimizes workers’ exposure to harmful chemicals. The lower VOC content also simplifies compliance with regulatory standards and enhances workplace safety.
- Enhanced Product Performance: Light-curable coatings offer excellent adhesion properties and protection against various environmental factors such as moisture, chemicals, and abrasion. They form durable, high-quality coatings that maintain their integrity over time, ensuring coated components or products’ long-term reliability and performance. Additionally, these coatings often exhibit superior clarity, which is desirable for applications where visual inspection or transparency is essential.
The advantages of light-curable conformal coatings include rapid cure time, improved process control, energy efficiency, low VOC emissions, and enhanced product performance. These benefits make them a preferred choice for manufacturers seeking to optimize production processes, reduce costs, and meet stringent quality and environmental standards.
Are there any limitations or challenges associated with these coatings?
While coatings offer numerous benefits such as protection, aesthetics, and functionality, they also come with limitations and challenges that need to be addressed:
- Durability: One of the primary challenges with coatings is ensuring their durability over time. Environmental factors such as UV radiation, moisture, temperature fluctuations, and chemical exposure can degrade coatings, losing protective properties and aesthetic appeal. Developing coatings with enhanced durability remains a significant challenge for researchers and manufacturers.
- Adhesion: Proper coating adhesion to the substrate is crucial for its effectiveness. Poor adhesion can result in coating delamination, leading to corrosion, peeling, and reduced performance. Achieving strong and durable adhesion, especially on diverse substrates, remains challenging in coating technology.
- Environmental Impact: Many traditional coatings contain volatile organic compounds (VOCs) and hazardous chemicals that pose environmental and health risks. Developing environmentally friendly coatings with low VOC emissions and sustainable raw materials is a challenge the coating industry faces. Additionally, the disposal of coating waste and the environmental impact of coating production processes must be addressed.
- Cost: Cost-effectiveness is a significant consideration in coating selection. Due to advanced materials and manufacturing processes, high-performance coatings often come with a higher price tag. Balancing performance with cost remains a challenge for industries seeking to implement coatings on a large scale.
- Application Techniques: Achieving uniform coating thickness and coverage can be challenging, particularly on complex surfaces or hard-to-reach areas. Optimizing application techniques to ensure consistent coating quality while minimizing waste and overspray is an ongoing challenge for coating applicators.
- Regulatory Compliance: Compliance with stringent regulatory standards regarding health, safety, and environmental impact poses challenges for coating manufacturers. Keeping up with evolving regulations and ensuring that coatings meet or exceed regulatory requirements adds complexity to the development and production process.
Addressing these limitations and challenges requires collaborative efforts among researchers, manufacturers, and regulatory bodies to advance coating technology toward improved performance, sustainability, and safety.
How do you apply light-curable conformal coatings to electronic components?
Applying light-curable conformal coatings to electronic components involves several steps to ensure proper protection and adhesion. Here’s a concise guide:
- Preparation: Begin by preparing the electronic components. Clean them thoroughly to remove dust, oils, or residues. This can be done using solvents or specialized cleaning solutions. Ensure the components are dehydrated before proceeding.
- Masking: Mask off any areas that should not be coated. Components like connectors, switches, or sensitive areas might need protection from the conformal coating. Masking ensures these areas remain untouched during the coating process.
- Application: Apply the light-curable conformal coating evenly over the electronic components. This can be done using various methods, including spraying, dipping, or brushing, depending on the equipment and the nature of the components. Ensure a uniform coating thickness to provide consistent protection.
- Curing: After applying the coating, cure it using a suitable light source. Light-curable coatings typically cure quickly when exposed to UV or visible light. The curing process initiates a chemical reaction in the coating, causing it to harden and adhere to the surface of the components. Ensure adequate exposure to the light source for complete curing.
- Inspection: Once cured, inspect the coated components for defects or irregularities. Check for proper coverage and adhesion of the coating. Address any areas that may require touch-up or rework.
- Post-cure Handling: Some coatings may require additional post-curing steps to ensure optimal performance. Follow the manufacturer’s recommendations for any specific post-cure procedures.
- Testing: Conduct testing to verify the effectiveness of the coating in protecting environmental factors such as moisture, chemicals, and mechanical stress. This may involve subjecting the coated components to simulated environmental conditions and assessing their performance.
- Finalization: Finalize the coated components for assembly or further processing after testing. Remove any masking materials and ensure proper labeling or documentation of the coated parts for future reference.
Following these steps, you can effectively apply light-curable conformal coatings to electronic components, enhancing their durability and reliability in various operating environments.
What are the curing mechanisms involved in light-curable conformal coatings?
Light-curable conformal coatings utilize photopolymerization as the primary curing mechanism. Photopolymerization involves using light, typically ultraviolet (UV) or visible light, to initiate a chemical reaction that transforms liquid monomers into a solid polymer network. This process offers several advantages, including rapid curing, precise control over curing time, and curing complex geometries without generating heat.
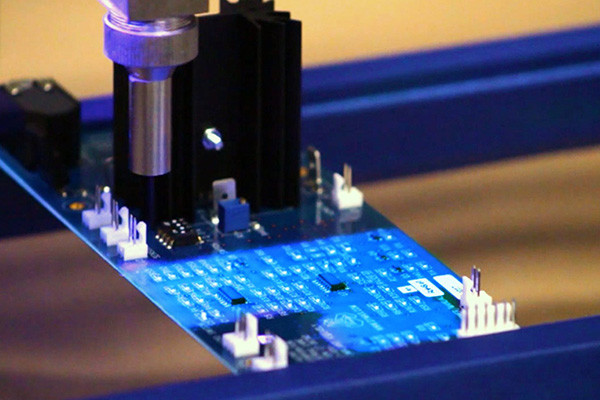
The curing process begins with applying the liquid conformal coating onto the substrate surface. This liquid typically consists of monomers, oligomers, photoinitiators, and additives. Photoinitiators are compounds that absorb light energy and undergo a photoreaction, generating reactive species such as free radicals or cations, which initiate polymerization. Upon exposure to light of the appropriate wavelength, photoinitiators absorb photons and transition to an excited state, leading to the cleavage of chemical bonds and the formation of reactive species.
Once the photoinitiator generates free radicals or cations, they polymerize the monomers and oligomers in the coating formulation. Monomers and oligomers contain reactive functional groups, such as double bonds (in acrylates) or epoxides, which undergo addition or ring-opening polymerization upon interaction with the reactive species. This results in covalent bonds between the monomers and oligomers, leading to the crosslinking and formation of a solid polymer network.
The curing process occurs rapidly, typically within seconds to minutes, depending on factors such as the intensity and wavelength of the light source, the formulation of the coating, and the thickness of the coating layer. After curing, the coating forms a durable and protective layer that adheres to the substrate surface, resisting environmental factors such as moisture, chemicals, and mechanical stress.
Light-curable conformal coatings utilize photopolymerization as the primary curing mechanism, initiating photoinitiators’ polymerization reactions upon light exposure. This process enables rapid and precise coating curing, forming a protective layer with excellent adhesion and durability.
Can light-curable conformal coatings be applied manually or only by automated methods?
Light-curable conformal coatings can be applied manually or by automated methods, providing flexibility in application depending on the manufacturing process’s specific requirements and the desired precision level.
Manual Application:
- Manual application involves using handheld dispensing equipment or spray guns to apply the conformal coating onto the substrate surface.
- This method offers simplicity and versatility, making it suitable for small-scale production or situations where automation may not be feasible or cost-effective.
- Operators can adjust the application parameters, such as spray pattern, flow rate, and coating thickness, to achieve the desired coverage and uniformity.
- However, manual application may be more prone to variations in coating thickness and consistency compared to automated methods, which could affect the performance and reliability of the coating.
Automated Application:
- Automated application systems utilize robotic dispensing equipment or conveyorized spray systems to apply the conformal coating with consistent quality and uniformity precisely.
- These systems are ideal for high-volume production environments where speed, accuracy, and repeatability are essential.
- Automated systems can be programmed to apply the coating with precise control over parameters such as deposition rate, coating thickness, and curing time.
- They are often integrated into inline manufacturing processes, allowing seamless integration with other production steps and minimizing cycle times.
- While automated application systems require upfront investment in equipment and setup, they offer efficiency, productivity, and quality control advantages.
Both manual and automated methods can be used to apply light-curable conformal coatings, each offering advantages and considerations. The choice between manual and computerized applications depends on factors such as production volume, process requirements, cost considerations, and the desired level of precision and consistency in coating application.
Are there different types of light-curable conformal coatings available in the market?
Yes, various types of light-curable conformal coatings are available in the market, each designed to meet specific performance requirements and application needs. These coatings offer advantages such as rapid curing, low volatility, and precise application control. Here are some common types:
- UV-Curable Conformal Coatings: These coatings are cured when exposed to ultraviolet (UV) light. They provide rapid curing times, allowing for faster processing and higher throughput in manufacturing. UV-curable coatings offer excellent chemical and abrasion resistance, making them suitable for demanding environments.
- LED-Curable Conformal Coatings: Similar to UV-curable coatings, LED-curable coatings cure when exposed to specific wavelengths of light emitted by light-emitting diodes (LEDs). They offer energy efficiency and longer lifespan compared to traditional UV lamps.
- Visible Light-Curable Conformal Coatings: These coatings cure when exposed to visible light wavelengths, typically between 400 to 450 nanometers. They offer versatility in curing equipment and can be cured using conventional light sources, reducing the need for specialized UV lamps.
- Dual-Cure Conformal Coatings: These coatings utilize a combination of light curing and secondary curing mechanisms, such as thermal or moisture curing. Dual-cure coatings offer enhanced reliability by ensuring complete curing, even in areas shielded from light.
- Low-Intensity UV-Curable Conformal Coatings: These coatings cure under low-intensity UV light, offering improved compatibility with heat-sensitive substrates or components. They provide a balance between curing speed and substrate compatibility.
- Infrared (IR)-Curable Conformal Coatings: These coatings cure when exposed to infrared radiation, offering an alternative to UV curing for heat-sensitive substrates. IR-curable coatings provide efficient curing with minimal substrate heating.
- Hybrid Conformal Coatings: These coatings combine the benefits of light curing with other curing mechanisms, such as heat or moisture curing, to achieve specific performance requirements. Hybrid coatings offer versatility and tailored curing profiles.
Each type of light-curable conformal coating has advantages and limitations, and selection depends on factors such as substrate material, curing equipment availability, processing requirements, and environmental conditions. Manufacturers often choose coatings based on their specific application needs to achieve optimal performance and reliability.
How do you ensure proper adhesion of light-curable conformal coatings to substrates?
Ensuring proper adhesion of light-curable conformal coatings to substrates is crucial for achieving desired performance and reliability in electronic assemblies. Here’s a comprehensive guide:
- Surface Preparation: Proper surface preparation is essential for good adhesion. Thoroughly clean the substrate to remove dust, oils, and residues. Methods include solvent cleaning, plasma treatment, or sandblasting, depending on the substrate material.
- Surface Activation: Some substrates may require surface activation to enhance adhesion. Techniques like plasma treatment or corona discharge can increase surface energy and promote bonding.
- Adhesion Promoters: Apply adhesion promoters compatible with the substrate and the conformal coating. These promoters facilitate bonding between the coating and substrate, especially on difficult-to-adhere surfaces like plastics.
- Substrate Compatibility: Ensure the chosen conformal coating is compatible with the substrate. Conduct compatibility tests to verify adhesion and avoid delamination or poor bonding over time.
- Optimized Coating Process: Control the coating process parameters carefully. Factors such as curing time, intensity, distance of UV light source, and coating thickness influence adhesion. Follow manufacturer recommendations and conduct process validation to optimize adhesion.
- Proper Curing: Ensure thorough and uniform curing of the conformal coating. Incomplete curing can lead to adhesion failure. Monitor curing parameters closely, such as UV exposure time and intensity, to achieve the desired degree of cross-linking and bonding.
- Quality Assurance Testing: Implement quality control measures to assess adhesion strength. Adhesion testing methods include tape, cross-cuts, and pull-off adhesion tests. Perform these tests regularly to verify coating integrity and adherence to industry standards.
- Post-coating Inspection: Inspect coated substrates for any defects or inconsistencies affecting adhesion. Address any issues promptly to prevent adhesion failures in the field.
- Documentation and Record-keeping: Maintain detailed records of surface preparation, coating application parameters, curing processes, and adhesion test results. Documentation aids in troubleshooting adhesion issues and ensures consistency in future coating applications.
- Continuous Improvement: Continuously evaluate and improve the adhesion process. Incorporate feedback from adhesion tests, field performance, and technological advancements to enhance reliability over time.
By adhering to these practices, manufacturers can ensure proper adhesion of light-curable conformal coatings to substrates, enhancing the reliability and longevity of electronic assemblies.
What are the considerations for selecting the suitable light-curable conformal coating for a specific application?
Selecting the appropriate light-curable conformal coating for a specific application requires careful consideration of various factors to ensure optimal performance and reliability:
- Substrate Compatibility: Ensure compatibility with the substrate material to prevent adhesion issues or damage. Consider the substrate’s composition, surface energy, and potential reactions with the coating material.
- Environmental Conditions: Evaluate the operating environment, including temperature fluctuations, humidity, chemical exposure, and mechanical stress. Choose a coating that offers robust protection against these conditions to maintain performance and longevity.
- Curing Requirements: Assess the curing method and conditions compatible with the application’s production process. Light-curable coatings offer rapid curing through UV or visible light exposure, minimizing production time compared to thermal or chemical curing methods.
- Coating Thickness: Determine the required coating thickness to protect against environmental factors and mechanical stress. Optimize thickness to balance protection with potential impacts on weight and space constraints.
- Optical Clarity: For applications requiring optical clarity, such as displays or sensors, select coatings with minimal yellowing or haze after curing to maintain optical performance.
- Chemical Resistance: Consider exposure to various chemicals or solvents in the application environment. Choose a coating with excellent chemical resistance to prevent degradation and ensure long-term protection.
- Electrical Properties: Evaluate the impact of the coating on electrical properties, such as insulation resistance and dielectric strength. Ensure the coating maintains electrical integrity and prevents conductivity issues or short circuits.
- Conformal Coating Method: Consider the application method, whether spray, dip, or selective coating, and ensure compatibility with the chosen coating material to achieve uniform coverage and consistent results.
- Regulatory Compliance: Ensure compliance with relevant industry standards, such as IPC or MIL specifications, and regulatory requirements for specific applications, such as medical devices or automotive electronics.
- Reliability and Testing: Validate the performance of the selected coating through reliability testing, including accelerated aging, thermal cycling, and environmental exposure, to ensure it meets the application’s durability and reliability requirements.
By carefully considering these factors, manufacturers can select the most suitable light-curable conformal coating for their specific application, ensuring optimal protection, performance, and reliability.
Are there any environmental or safety concerns associated with these coatings?
While light-curable conformal coatings offer numerous benefits, such as rapid curing and enhanced performance, there are also environmental and safety considerations associated with their use:
- Hazardous Ingredients: Some formulations of light-curable conformal coatings may contain dangerous chemicals such as monomers, oligomers, photoinitiators, and additives. These substances can pose risks to human health and the environment during manufacturing, application, and disposal if not appropriately handled.
- Volatile Organic Compounds (VOCs): Certain coatings may contain volatile organic compounds, contributing to air pollution and adversely affecting air quality and human health. VOC emissions can occur during application and curing processes, requiring proper ventilation and control measures to minimize exposure.
- Skin and Respiratory Hazards: Contact with uncured coating materials can cause skin irritation or sensitization, while inhalation of volatile components or aerosols may irritate the respiratory system. To prevent exposure, workers should use appropriate personal protective equipment (PPE), including gloves, safety glasses, and respiratory protection.
- Potential for Combustion: Light-curable coatings may pose a fire hazard due to their explosive properties, particularly in the presence of heat, sparks, or open flames. Proper storage, handling, and disposal procedures should be followed to minimize the risk of fire accidents.
- Waste Disposal: Disposal of unused or cured coating materials and cleaning solvents and waste generated during the application process requires careful consideration to prevent environmental contamination. Compliance with local regulations and best practices for waste management is essential to minimize ecological impact.
- Regulatory Compliance: Manufacturers must ensure compliance with relevant environmental and safety regulations, such as REACH (Registration, Evaluation, Authorization, and Restriction of Chemicals) and OSHA (Occupational Safety and Health Administration) standards, to protect both workers and the environment.
To mitigate these environmental and safety concerns, manufacturers should prioritize using environmentally friendly and safer alternatives, implement proper handling procedures, provide adequate training and PPE for workers, and adhere to regulatory requirements throughout the product life cycle. Additionally, ongoing research and development efforts focus on developing safer and more sustainable formulations for conformal coatings to address these concerns effectively.
How do light-curable conformal coatings contribute to the longevity of electronic devices?
Light-curable conformal coatings play a vital role in enhancing the longevity of electronic devices by providing a protective barrier against various environmental factors and mechanical stresses. These coatings are typically applied to the electronic components of devices to safeguard them from moisture, dust, chemicals, and other contaminants that could compromise their functionality over time.
One key way these coatings contribute to longevity is through their ability to form a conformal and uniform layer over intricate electronic assemblies. This ensures that all exposed surfaces, including small gaps and crevices, are adequately protected. By creating a barrier against moisture ingress, light-curable coatings help prevent corrosion and oxidation of sensitive electronic components, such as printed circuit boards (PCBs) and solder joints. This protection is particularly crucial in harsh environments where electronic devices may be exposed to high humidity levels or extreme temperatures.
Moreover, light-curable coatings offer rapid curing times, enabling efficient and cost-effective manufacturing processes. Once applied, the coatings can be quickly cured using ultraviolet (UV) or visible light sources, reducing production cycle times and improving throughput. This swift curing process also minimizes the risk of contamination during assembly, ensuring the reliability of the coated components.
Furthermore, these coatings exhibit excellent adhesion properties, bonding firmly to various substrate materials commonly used in electronic devices. This strong adhesion helps prevent the coating from delamination or peeling over time, even under mechanical stresses such as vibrations or thermal cycling.
Additionally, light-curable conformal coatings can be formulated to provide specific performance characteristics tailored to the requirements of different electronic applications. For instance, they can offer enhanced chemical resistance, UV stability, or flexibility, depending on the device’s operating conditions and environmental factors.
In summary, light-curable conformal coatings contribute to the longevity of electronic devices by forming a protective barrier against environmental hazards, facilitating rapid and reliable manufacturing processes, and ensuring durable adhesion to substrate materials. By safeguarding electronic components from degradation and damage, these coatings help extend the operational lifespan of devices, thereby enhancing their reliability and performance.
What testing methods are used to evaluate the performance of light-curable conformal coatings?
Several testing methods are employed to evaluate the performance and effectiveness of light-curable conformal coatings in protecting electronic devices from environmental factors and ensuring their long-term reliability:
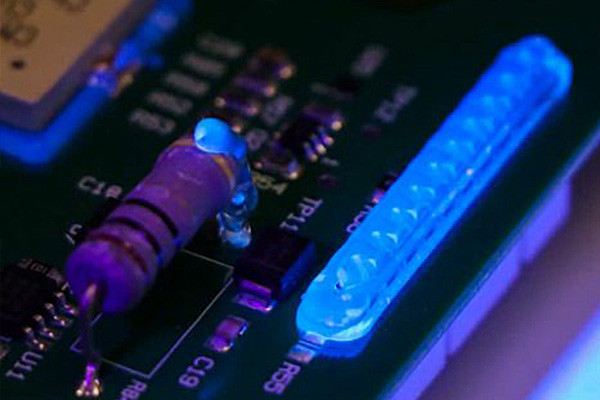
- Adhesion Testing: Adhesion testing assesses the strength of the bond between the conformal coating and the substrate material, such as printed circuit boards (PCBs). Methods like tape or cross-cut adhesion testing are commonly used to evaluate the coating’s ability to adhere firmly to the substrate without delamination or peeling.
- Chemical Resistance Testing: Chemical resistance testing determines the coating’s resilience against exposure to various chemicals commonly encountered in industrial or operating environments. Immersion or spot tests with different chemical solutions simulate real-world conditions to assess the coating’s resistance to degradation or dissolution.
- Moisture Resistance Testing: Moisture resistance testing evaluates the coating’s ability to prevent moisture ingress and protect electronic components from corrosion and oxidation. Methods such as humidity, salt fog, or water immersion testing subject the coated samples to high humidity or corrosive environments to assess their performance over time.
- Thermal Cycling Testing: Thermal cycling testing evaluates the coating’s ability to withstand fluctuations in temperature without cracking, delamination, or degradation. Samples undergo exposure cycles to extreme temperature variations, simulating the thermal stresses experienced during device operation.
- Electrical Insulation Testing: Electrical insulation testing measures the coating’s ability to maintain electrical insulation properties and prevent leakage currents or short circuits. Dielectric strength and insulation resistance testing assess the coating’s electrical performance under specified voltage conditions.
- UV Stability Testing: UV stability testing evaluates the coating’s resistance to ultraviolet (UV) radiation, which can cause degradation or discoloration over time. Exposure to UV light sources simulates prolonged outdoor or high-intensity light exposure to assess the coating’s stability and color retention.
- Mechanical Testing: Mechanical testing assesses the coating’s resistance to physical stresses such as abrasion, impact, or flexing. Methods like pencil hardness testing, abrasion resistance testing, or mandrel bend testing evaluate the coating’s durability and flexibility under mechanical loads.
By subjecting light-curable conformal coatings to these comprehensive testing methods, manufacturers can ensure that the coatings meet the desired performance standards and provide reliable protection to electronic devices in diverse operating conditions.
Are there any emerging trends or advancements in light-curable conformal coatings?
Light-curable conformal coatings, also known as UV-curable conformal coatings, have gained momentum due to their efficiency, eco-friendliness, and effectiveness in protecting electronic components. Several emerging trends and advancements are shaping the field:
- Nanostructured Coatings: Researchers are exploring the integration of nanostructures into light-curable conformal coatings. These nanostructures can enhance scratch resistance, moisture protection, and even antimicrobial properties, expanding the range of applications for these coatings.
- Multifunctional Coatings: The demand for coatings that offer multiple functionalities beyond mere protection is rising. Manufacturers are developing coatings that protect against environmental factors and provide features such as thermal management, electrical insulation, and even self-healing capabilities.
- Improved Adhesion: Adhesion to various substrates has been challenging in conformal coating applications. Advancements in surface treatment techniques and formulation chemistry lead to coatings with superior adhesion properties, ensuring long-term reliability even in harsh operating conditions.
- Low-VOC Formulations: Environmental concerns and regulatory pressures drive the development of low-VOC (volatile organic compound) formulations for conformal coatings. Manufacturers formulate coatings with minimal environmental impact while maintaining high performance and reliability.
- Inline Process Integration: Integrating light-curable conformal coating processes into existing production lines is becoming seamless. Automation technologies and inline curing systems are being developed to streamline the coating process, reducing cycle times and improving overall efficiency.
- Innovative Coatings: There is growing interest in coatings that can provide real-time monitoring of the health and performance of electronic components. Innovative coatings embedded with sensors or indicators can affect changes in temperature, humidity, or other environmental factors, providing early warnings of potential issues and enabling predictive maintenance strategies.
- Customization and Tailoring: Manufacturers increasingly offer customizable formulations to meet specific application requirements. Tailoring coating properties such as flexibility, hardness, and chemical resistance allows for optimized protection tailored to different electronic devices and environments’ unique needs.
These emerging trends and advancements drive innovation in light-curable conformal coatings, paving the way for enhanced performance, sustainability, and versatility in electronic component protection.
What industries commonly utilize light-curable conformal coatings?
Light-curable conformal coatings are widely utilized across various industries due to their unique properties and benefits. These coatings are applied to electronic components to protect them from environmental factors such as moisture, dust, chemicals, and temperature extremes. Here are some industries where light-curable conformal coatings are commonly used:
- Electronics: The electronics industry is one of the primary users of light-curable conformal coatings. Printed circuit boards (PCBs), integrated circuits (ICs), and other electronic components are coated to enhance their durability and reliability. These coatings help prevent corrosion, leakage currents, and short circuits, extending the lifespan of electronic devices.
- Automotive: In the automotive sector, light-curable conformal coatings are applied to various electronic components, including engine control units (ECUs), sensors, and wiring harnesses. These coatings protect sensitive electronics from exposure to moisture, heat, and automotive fluids, ensuring optimal performance and reliability in harsh operating conditions.
- Aerospace: Aerospace applications often involve extreme environmental conditions, including high altitudes, temperature variations, and radiation exposure. Light-curable conformal coatings protect critical electronic systems onboard aircraft and spacecraft, safeguarding against moisture ingress, vibration, and thermal cycling.
- Medical Devices: Medical devices, such as implantable electronics, diagnostic equipment, and monitoring devices, require reliable protection against bodily fluids, sterilization processes, and other environmental challenges. Light-curable conformal coatings offer biocompatible and sterilizable coatings that ensure the longevity and functionality of medical electronics.
- Telecommunications: Telecommunication equipment, including antennas, routers, and base stations, often operates in outdoor environments exposed to weather elements. Light-curable conformal coatings provide a barrier against moisture, salt spray, and UV radiation, preserving the performance and reliability of communication systems.
- Consumer Electronics: Products like smartphones, tablets, and wearable devices incorporate light-curable conformal coatings to enhance their resistance to water damage, dust intrusion, and mechanical stress. These coatings contribute to the overall durability and longevity of consumer electronics.
Overall, the versatility, rapid curing, and protective properties of light-curable conformal coatings make them indispensable in various industries where electronic components require reliable protection against environmental hazards.
How do light-curable conformal coatings protect against environmental factors such as moisture, dust, and chemicals?
Light-curable conformal coatings offer robust protection against environmental factors like moisture, dust, and chemicals through unique properties and application methods.
These coatings are formulated with specially designed chemical compositions that provide excellent barrier properties. When applied to electronic components or substrates, they form a thin, uniform protective layer as a physical barrier against moisture and dust ingress. This barrier prevents the penetration of water molecules and airborne contaminants, safeguarding sensitive electronic circuits from corrosion, short circuits, and other damage caused by environmental exposure.
Moreover, the curing process of light-curable conformal coatings significantly enhances their protective capabilities. These coatings are typically cured using ultraviolet (UV) or visible light sources. Upon exposure to the appropriate wavelength of light, the coating undergoes a rapid polymerization reaction, transforming from a liquid or gel state into a solid, durable film. This curing mechanism results in a coating with high crosslinking density and excellent adhesion to the substrate, ensuring long-term protection against moisture, dust, and chemicals.
Additionally, light-curable conformal coatings often exhibit superior chemical resistance to traditional solvent-based coatings. Their chemical composition can be tailored to resist various corrosive substances, including acids, bases, solvents, and fuels. This resistance helps prevent chemical attacks and degradation of the coated surfaces, prolonging the lifespan of electronic devices and equipment operating in harsh environments.
Furthermore, the application process of light-curable conformal coatings offers several advantages in terms of efficiency and reliability. These coatings can be applied using automated dispensing systems or selective coating equipment, ensuring precise coverage and uniform thickness across complex geometries. The ability to cure the coating instantly with light allows for rapid production throughput and reduced cycle times, making them highly suitable for high-volume manufacturing environments.
Light-curable conformal coatings effectively protect against moisture, dust, and chemicals by forming a durable barrier, undergoing rapid curing, exhibiting superior chemical resistance, and offering efficient application methods. These properties make them indispensable for safeguarding electronic assemblies and devices from environmental hazards in various industries.
Can light-curable conformal coatings be removed or reworked if necessary?
Light-curable conformal coatings are widely used in various industries, offering rapid curing times and excellent protection for electronic components. While they provide robust protection against environmental factors such as moisture, chemicals, and mechanical stresses, there are methods for removing or reworking them if necessary.
One standard method for removing light-curable conformal coatings is using chemical strippers formulated explicitly for this purpose. These strippers typically contain solvents or chemical agents that break down the polymer matrix of the coating, allowing it to be lifted or washed away from the substrate. Care must be taken to select a stripper that effectively removes the coating without damaging the underlying components or substrate material.
Another approach involves mechanical methods such as abrasive blasting or scraping. Abrasive blasting utilizes fine particles propelled at high velocity to remove the coating from the substrate’s surface. Scraping involves physically scraping the coating off the substrate using specialized tools. While effective, these methods are more labor-intensive and damage delicate components if not executed carefully.
In some cases, localized rework of light-curable conformal coatings may be feasible. This involves selectively reapplying the coating to specific areas where removal is necessary. Techniques such as masking or precision dispensing can be employed to ensure precise application and minimal disruption to surrounding areas.
It’s essential to consider the potential impact of removal or rework on the coated assembly’s overall integrity and performance. Careful evaluation of the substrate material, component sensitivity, and environmental requirements should guide the selection of appropriate removal or rework methods. Adherence to safety protocols and environmental regulations is also crucial when handling chemical strippers or abrasive materials.
While light-curable conformal coatings offer excellent protection and durability, they can be removed or reworked using chemical, mechanical, or localized rework methods. Proper planning, selection of appropriate techniques, and adherence to safety guidelines are essential to ensure successful removal or rework while maintaining the integrity of the coated assembly.
What are the prospects for developing and adopting light-curable conformal coatings?
The future prospects for the development and adoption of light-curable conformal coatings appear promising, driven by several factors:
- Rising Demand for Advanced Protection: With the increasing complexity and miniaturization of electronic devices, a growing need for protective coatings that offer superior performance in harsh environments is needed. Light-curable conformal coatings provide an effective barrier against moisture, chemicals, dust, and other contaminants, ensuring the longevity and reliability of electronic components.
- Advancements in Material Science: Ongoing research in material science leads to developing novel formulations with enhanced properties such as improved adhesion, flexibility, and thermal stability. These advancements are crucial for meeting the evolving requirements of various industries, including automotive, aerospace, medical devices, and consumer electronics.
- Efficiency and Cost-Effectiveness: Light-curable coatings offer significant advantages over traditional solvent-based coatings regarding curing time and energy consumption. The ability to rapidly cure coatings using UV or LED light sources reduces processing time and increases productivity. Additionally, eliminating solvent evaporation lowers production costs and environmental impact, making light-curable coatings an attractive option for manufacturers seeking efficiency and sustainability.
- Customization and Versatility: Manufacturers increasingly seek customizable coating solutions to address specific application needs. Light-curable formulations can be tailored to achieve desired properties such as optical clarity, electrical insulation, or color matching. Moreover, these coatings can be applied to various substrates, including plastics, metals, and ceramics, further enhancing their versatility and market appeal.
- Regulatory Compliance and Sustainability: Stringent regulations regarding volatile organic compounds (VOCs) and hazardous air pollutants (HAPs) are driving the adoption of eco-friendly coating technologies. Light-curable formulations typically have lower VOC emissions and comply with environmental standards, making them a preferred choice for companies committed to sustainability and regulatory compliance.
The development and adoption of light-curable conformal coatings are poised for growth due to their superior performance, efficiency, customization options, and environmental benefits. As industries prioritize reliability, efficiency, and sustainability, these coatings will likely become increasingly prevalent across various applications, driving innovation and market expansion in the coming years.
Conclusion:
Light-curable conformal coatings represent a cutting-edge solution for protecting electronic components and assemblies in various industries. Their ability to rapidly cure under UV light, conform to complex shapes, and provide reliable insulation make them indispensable. Despite challenges such as substrate adhesion and environmental considerations, ongoing research and advancements continue to improve the performance and versatility of these coatings. As industries evolve, the demand for efficient and effective protection of electronic devices will further drive innovation in light-curable conformal coatings.