What Material is Used for Conformal Coating
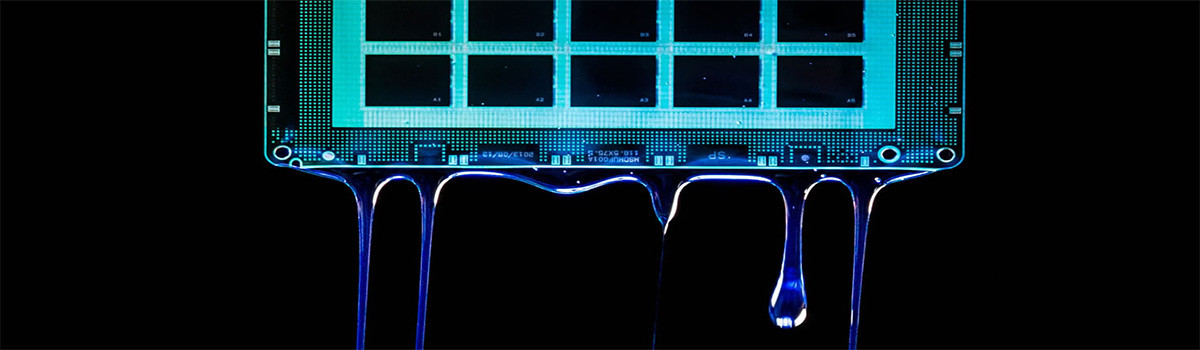
Conformal coating plays a crucial role in protecting electronic components from environmental factors such as moisture, dust, chemicals, and temperature variations. Choosing the right material for conformal coating is essential to ensure the longevity and reliability of electronic devices. Various materials are available, each offering unique properties suited to different applications and environmental conditions.
Table of Contents
ToggleFundamental concepts you must comprehend:
What is conformal coating?
Conformal coating is a protective material applied to electronic circuitry to safeguard it from various environmental factors such as moisture, dust, chemicals, and temperature extremes. The coating conforms to the contours of the circuit board, hence the term “conformal.” Its primary purpose is to enhance the reliability and longevity of electronic assemblies, especially those deployed in harsh conditions like automotive, aerospace, marine, and industrial environments.
These coatings are typically thin films, ranging from a few micrometers to several hundred micrometers in thickness, and can be applied through various methods including spraying, dipping, brushing, and selective coating. The choice of coating method depends on factors such as the type of circuit board, the complexity of components, and production volume.
There are several types of conformal coatings available, each with its own unique properties and applications:
- Acrylic: Acrylic coatings offer good moisture resistance, flexibility, and ease of application. They are commonly used for general-purpose protection where moderate environmental protection is required.
- Silicone: Silicone coatings provide excellent protection against extreme temperatures, chemicals, and moisture. They are highly flexible and can withstand thermal cycling, making them suitable for demanding applications such as automotive electronics and outdoor equipment.
- Urethane: Urethane coatings offer superior abrasion resistance and chemical resistance compared to acrylics. They provide a durable protective layer suitable for assemblies exposed to harsh environments or mechanical stress.
- Epoxy: Epoxy coatings provide excellent adhesion and chemical resistance, making them ideal for applications where superior protection against moisture and chemicals is required.
- Parylene: Parylene is a unique conformal coating material deposited as a vapor, resulting in a pinhole-free, ultra-thin film. It offers exceptional protection against moisture, chemicals, and electrical insulation, making it suitable for delicate components and medical devices.
Conformal coatings play a crucial role in ensuring the reliability and performance of electronic assemblies in challenging environments, extending their lifespan and reducing the risk of premature failure. Proper selection and application of conformal coatings are essential to meet the specific requirements of each application and ensure optimal protection of electronic devices.
Why is conformal coating essential for electronic components?
Conformal coating protects electronic components from various environmental hazards, ensuring their reliability, longevity, and functionality. Here’s why it’s essential:
- Environmental Protection: Electronic components are often exposed to harsh environments such as moisture, dust, chemicals, and temperature variations. Conformal coatings form a protective barrier around these components, shielding them from these external elements. Moisture, for instance, can cause corrosion and short circuits in electronic circuits, leading to malfunctions or complete failure. Conformal coatings prevent moisture ingress, safeguarding the components.
- Chemical Resistance: Electronic devices may encounter chemical substances during operation or maintenance, which can degrade the performance or damage the components. Conformal coatings offer chemical resistance, protecting against corrosive substances and extending the lifespan of the electronics.
- Mechanical Protection: Components on electronic circuit boards are susceptible to mechanical damage from vibration, shock, or physical impact. Conformal coatings provide a layer of insulation that absorbs shock and vibration, reducing the risk of mechanical failures and enhancing the durability of the components.
- Dielectric Insulation: Conformal coatings act as dielectric insulators, preventing electrical shorts between closely spaced components or conductive traces on the circuit board. This insulation is crucial for maintaining the integrity of the electronic circuitry and preventing electrical leakage or arcing.
- Enhanced Reliability: By safeguarding electronic components against environmental, chemical, and mechanical stresses, conformal coatings significantly improve the reliability of electronic devices. They minimize the risk of premature failures, reducing maintenance costs and enhancing overall product performance.
- Conformal Application: Unlike traditional potting methods that encapsulate entire assemblies, conformal coatings can be applied precisely and controlled, covering only the necessary areas while leaving connectors and other sensitive parts accessible for servicing or replacement.
Conformal coating is indispensable for electronic components as it offers comprehensive protection against environmental hazards, enhances reliability, and prolongs the lifespan of electronic devices, ensuring their optimal performance in diverse operating conditions.
What are the common environmental factors that conformal coating protects against?
Conformal coating is a protective layer applied to electronic components and circuit boards to safeguard them against various environmental factors. These coatings serve as a barrier, shielding sensitive electronics from potentially harmful elements. Conformal coating protects against common ecological factors, including moisture, dust, chemicals, temperature fluctuations, and physical impact.
Moisture is one of the most significant threats to electronic components, as it can cause corrosion, short circuits, and electrical leakage. Conformal coatings create a moisture-resistant barrier, preventing water or humidity from infiltrating and damaging the components. This is particularly important in applications exposed to high humidity or outdoor environments.
Dust and particulate matter pose another risk to electronic devices, potentially causing overheating, clogging cooling systems, and interfering with electrical connections. Conformal coatings help mitigate this risk by sealing off components from dust ingress, maintaining optimal performance and reliability.
Chemical exposure is a concern in industrial environments where electronic devices may come into contact with solvents, oils, or other corrosive substances. Conformal coatings provide chemical resistance, protecting against degradation and ensuring the longevity of the components.
Temperature fluctuations can impact the performance and lifespan of electronic devices, especially in applications subject to extreme temperatures. Conformal coatings offer thermal insulation, helping stabilize the enclosed components’ temperature and reducing the risk of thermal stress-related failures.
Physical impact and mechanical shock can also threaten electronic components, leading to damage or dislodgement of sensitive parts. Conformal coatings provide a protective barrier against mechanical stress, enhancing the durability and ruggedness of the electronic assembly.
Conformal coating safeguards electronic components and circuit boards against various environmental factors, including moisture, dust, chemicals, temperature fluctuations, and physical impact. By providing a protective barrier, conformal coatings help ensure electronic devices’ reliability, performance, and longevity in various applications and operating conditions.
What are the primary materials used for conformal coating?
Conformal coating is a protective layer applied to electronic circuitry to protect it from environmental factors such as moisture, dust, chemicals, and temperature extremes. The choice of materials for conformal coating depends on the application’s specific requirements, including the operating environment, desired performance characteristics, and manufacturing constraints. Several primary materials are commonly used for conformal coating:
- Acrylics: Acrylic conformal coatings are popular due to their excellent moisture, abrasion resistance, and good electrical properties. They offer relatively easy application and removal, making them suitable for various electronic assemblies. Acrylic coatings provide a durable protective layer that maintains flexibility over a broad temperature range.
- Silicones: Silicone conformal coatings are known for their high-temperature resistance, flexibility, and excellent protection against moisture and chemicals. They are often preferred for applications exposed to extreme temperatures or harsh environmental conditions. Silicone coatings provide good dielectric properties and can withstand thermal cycling without cracking or delamination.
- Urethanes: Urethane conformal coatings offer superior chemical resistance and mechanical strength compared to other materials. They protect against solvents, fuels, and corrosive substances, making them suitable for demanding applications such as automotive electronics or aerospace systems. Urethane coatings can withstand high-stress levels and offer good adhesion to various substrates.
- Epoxies: Epoxy conformal coatings are renowned for their high dielectric strength and chemical resistance. They form a formidable, durable barrier that protects electronic assemblies from moisture, solvents, and mechanical damage. Epoxies are often used in applications where superior performance under harsh conditions is required, such as marine electronics or industrial controls.
- Parylene: Parylene conformal coatings are unique because they are deposited as a vapor and conformally coat all assembly surfaces, including crevices and complex geometries. Parylene coatings offer exceptional chemical resistance, biocompatibility, and uniform coverage without impacting the electrical properties of the components. They are commonly used in medical devices, aerospace electronics, and other high-reliability applications.
Each conformal coating material type has advantages and limitations, and the selection should consider factors such as application requirements, environmental conditions, regulatory compliance, and manufacturing processes. Additionally, proper surface preparation and application techniques are essential to ensure the effectiveness and reliability of the conformal coating.
How does silicone conformal coating differ from acrylic conformal coating?
Silicone conformal coating and acrylic conformal coating are widely used in electronics manufacturing to protect printed circuit boards (PCBs) and electronic components from environmental factors such as moisture, dust, chemicals, and temperature variations. Although they serve the same general purpose, they differ in their chemical composition, properties, and applications.
Silicone conformal coatings are derived from silicone polymers, which offer exceptional flexibility and resistance to extreme temperatures ranging from very low to very high. This makes silicone coatings ideal for applications where thermal cycling is every day, such as automotive electronics or outdoor equipment. Silicone coatings also provide excellent moisture resistance and are highly resistant to chemicals, making them suitable for harsh environments.
On the other hand, acrylic conformal coatings are based on acrylic resins, which offer good electrical insulation properties and adhesion to various substrates. Acrylic coatings dry quickly and form a hard, durable film that protects against moisture, fungus, and corrosion. They are often preferred for their transparency and ability to maintain clarity over time, making them suitable for applications where component inspection is necessary.
In terms of application, silicone conformal coatings are typically applied in thicker layers than acrylic coatings. This is because silicone coatings have higher viscosity and tend to flow less during application, resulting in a denser, more protective layer. On the other hand, acrylic coatings are applied in thinner layers and can be easily reworked or removed if necessary.
One key difference between the two types of coatings is their flexibility. Silicone conformal coatings offer superior flexibility and are less prone to cracking or delamination when subjected to mechanical stress or thermal cycling. Acrylic coatings, while durable, may become brittle over time, especially when exposed to extreme temperatures or UV radiation.
Silicone conformal coatings are preferred for their flexibility, wide temperature range, and chemical resistance, making them suitable for demanding environments. On the other hand, acrylic conformal coatings offer good adhesion, clarity, and ease of application, making them ideal for a wide range of electronics applications where cost-effectiveness and ease of use are prioritized.
What are the advantages of using acrylic conformal coating?
Acrylic conformal coating offers a range of advantages, making it a popular choice for protecting electronic assemblies and components in various industries. Here are some key advantages:
- Excellent Protection: Acrylic conformal coatings provide a durable protective barrier against environmental contaminants, including moisture, dust, chemicals, and solvents. This protection helps prevent corrosion, dendritic growth, and other forms of damage that can compromise the performance and reliability of electronic devices.
- Flexibility: Acrylic coatings offer excellent flexibility, allowing them to expand and contract with temperature fluctuations and mechanical stresses without cracking or delaminating. This flexibility is particularly beneficial in applications where thermal cycling or vibration is present, as it helps maintain the integrity of the coating over time.
- Optical Clarity: Acrylic coatings typically have good optical clarity, allowing for easy visual inspection of underlying components and circuitry. This transparency can be crucial for troubleshooting, maintenance, and quality control purposes, as it enables technicians to identify issues such as solder bridges, component misalignment, or foreign debris without removing the coating.
- Ease of Application: Acrylic conformal coatings are relatively easy to apply using various methods, including spraying, brushing, dipping, or selective coating techniques. Their low viscosity and good wetting properties facilitate uniform coverage and penetration into tight spaces, ensuring comprehensive protection for complex assemblies and densely populated circuit boards.
- Fast Cure Times: Acrylic coatings typically cure quickly at ambient or slightly elevated temperatures, allowing for rapid processing and shorter production cycles. This feature can help improve manufacturing efficiency and reduce turnaround times, particularly in high-volume production environments where throughput is critical.
- Compatibility: Acrylic conformal coatings are compatible with many substrates, including metals, plastics, ceramics, and composites, making them versatile for various applications. They also exhibit good adhesion to different surface finishes, such as solder masks, gold, and tin, ensuring reliable performance across diverse electronic assemblies.
- Cost-Effectiveness: Acrylic coatings are generally more cost-effective than alternative conformal coating materials, such as silicone or urethane. Their relatively low material cost and efficient application and curing processes make them an attractive option for manufacturers seeking reliable protection without breaking the budget.
Overall, acrylic conformal coatings offer a compelling combination of protection, flexibility, transparency, ease of application, compatibility, and cost-effectiveness, making them a preferred choice for safeguarding electronic assemblies in demanding environments.
What are the disadvantages of using silicone conformal coating?
Silicone conformal coatings offer numerous advantages in protecting electronic components from environmental hazards such as moisture, dust, chemicals, and temperature variations. However, they also come with some disadvantages that need to be considered:
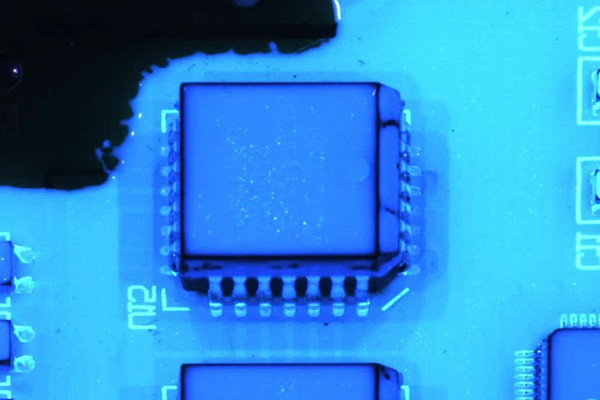
- Poor Solvent Resistance: Silicone coatings may not withstand certain solvents or cleaning agents. This can lead to degradation or partial removal of the coating, compromising its protection. Compatibility testing with cleaning agents is necessary to ensure the coating’s longevity.
- Limited Temperature Range: While silicone conformal coatings generally have good resistance to high temperatures, they may not perform well under extreme temperature conditions. Silicone coatings can degrade or become brittle at very high temperatures, potentially exposing the coated components to damage.
- High Cost: Silicone conformal coatings are more expensive than other types, such as acrylics or urethanes. This can significantly increase the overall manufacturing cost, especially for large-scale production or coating extensive areas.
- Thermal Insulation: Silicone coatings can act as thermal insulators, which might lead to heat buildup in electronic components. This thermal insulation property could be a disadvantage in applications where efficient heat dissipation is crucial, such as in power electronics.
- Complex Repair and Rework: Silicone conformal coatings typically have strong adhesion properties, making them challenging to remove for repair or rework. Specialized solvents or mechanical methods may be required, which can increase labor and time costs.
- Potential for Silicone Migration: Over time, silicone conformal coatings may experience silicone migration, where silicone compounds migrate from the coating into adjacent materials. This can contaminate sensitive electronic components or cause compatibility issues with other materials in the device.
- UV Degradation: Some silicone conformal coatings may be prone to degradation when exposed to ultraviolet (UV) light. This can result in yellowing or embrittlement of the coating over time, reducing its effectiveness in protecting the underlying electronics.
Despite these disadvantages, silicone conformal coatings remain a popular choice for many applications due to their excellent protective properties, flexibility, and wide range of applications. Careful consideration of the specific requirements and potential drawbacks is essential when selecting a conformal coating material.
Are there any environmental concerns associated with conformal coating materials?
Conformal coatings are protective materials applied to electronic components to safeguard them from environmental stresses such as moisture, dust, chemicals, and temperature variations. While they play a crucial role in enhancing the reliability and longevity of electronic devices, environmental concerns are associated with some of the materials used in conformal coatings.
One primary concern is the potential toxicity of certain coating materials. Many traditional conformal coatings contain hazardous substances such as volatile organic compounds (VOCs), including solvents like toluene and xylene, and heavy metals like lead and cadmium. These substances can pose risks to human health and the environment during the manufacturing, application, and disposal stages if not handled properly.
Furthermore, the production and disposal of conformal coating materials can contribute to environmental pollution. The manufacturing process often involves the release of pollutants and greenhouse gases, contributing to air and water pollution. Improper disposal methods, such as landfilling or incineration, can release harmful chemicals into the environment, impacting soil and water quality.
Another concern is the potential for bioaccumulation and ecological harm. Some components of conformal coatings, such as specific polymers or additives, may persist in the environment for long periods and bioaccumulate in organisms, potentially causing harm to wildlife and ecosystems.
However, ongoing research and development is focused on addressing these environmental concerns. Manufacturers are shifting towards more environmentally friendly alternatives, such as low-VOC or VOC-free coatings, water-based formulations, and halogen-free materials. These alternatives aim to reduce the environmental impact throughout the lifecycle of conformal coatings, from production to disposal.
Additionally, proper handling, storage, and disposal practices are essential to minimize the environmental footprint of conformal coatings. This includes reducing emissions during manufacturing, ensuring adequate ventilation during application, and employing safe disposal methods such as recycling or incineration in controlled environments.
While conformal coatings are vital for protecting electronic components, environmental concerns are associated with certain materials used in their production and application. However, ongoing efforts to develop and adopt more environmentally friendly alternatives and responsible handling and disposal practices can help mitigate these concerns and promote sustainable use of conformal coatings.
Can conformal coating materials withstand high temperatures?
Conformal coating materials protect electronic components from environmental stresses such as moisture, dust, chemicals, and temperature extremes. While many conformal coatings offer excellent protection against these factors, their ability to withstand high temperatures depends on the specific material composition.
Several types of conformal coating materials are available, each with its temperature resistance properties:
- Silicone-based coatings: Silicone conformal coatings are known for their excellent thermal resistance. They can typically withstand temperatures ranging from -55°C to 200°C or higher, making them suitable for applications where high heat is a concern. Silicone coatings provide flexibility and good adhesion to many substrates, making them popular in automotive, aerospace, and industrial electronics.
- Acrylic-based coatings: Acrylic conformal coatings offer good protection against moisture and chemicals but may have lower thermal resistance than silicones. They can typically withstand temperatures up to 125°C to 150°C, making them suitable for many electronic applications but less ideal for extreme heat environments.
- Polyurethane-based coatings: Polyurethane conformal coatings provide excellent chemical and mechanical protection but may have limited thermal resistance compared to silicone coatings. Depending on the specific formulation, they can generally withstand temperatures up to 130°C to 150°C.
- Parylene coatings: Parylene is a unique conformal coating material deposited as a vapor-phase polymer, offering excellent protection in harsh environments. It exhibits high thermal stability and can withstand temperatures exceeding 200°C, making it ideal for applications requiring extreme temperature resistance.
When selecting a conformal coating material for high-temperature environments, it’s crucial to consider the application’s operating temperature range and choose a coating that can withstand those conditions. Factors such as adhesion to the substrate, flexibility, and ease of application should also be considered to ensure optimal performance and protection of electronic components. Conducting thorough testing and consulting with coating manufacturers can help determine the most suitable material for specific high-temperature applications.
Which conformal coating material is best suited for harsh chemical environments?
In harsh chemical environments, the choice of conformal coating material is critical to ensure the protection and longevity of electronic components. Several factors need consideration, including chemical resistance, temperature stability, adhesion properties, and ease of application. Among the various options available, polyurethane and perylene coatings are often preferred for their excellent performance in harsh chemical environments.
Polyurethane coatings protect against various chemicals, including solvents, acids, and bases. They form a durable barrier that can withstand exposure to harsh environments without degrading. Polyurethane coatings also provide flexibility, making them suitable for applications where thermal cycling or mechanical stress may occur. They are relatively easy to apply and can be reworked, providing versatility in manufacturing processes.
Parylene coatings, on the other hand, offer unique advantages in harsh chemical environments due to their exceptional chemical resistance and inertness. Parylene is a vapor-deposited polymer that forms a conformal and pinhole-free coating, providing uniform protection even on complex geometries. This coating exhibits superior resistance to various chemicals, including strong acids, bases, solvents, and corrosive gasses. Parylene coatings also offer excellent thermal stability and electrical insulation properties, enhancing their suitability for demanding applications.
While both polyurethane and parylene coatings offer excellent protection in harsh chemical environments, the choice between them depends on specific application requirements. Polyurethane coatings may be preferred for their ease of application and flexibility, especially when mechanical stress is a concern. On the other hand, parylene coatings are ideal for applications requiring ultra-thin and highly conformal protection with superior chemical resistance.
Both polyurethane and perylene coatings are well-suited for harsh chemical environments, offering robust protection against a wide range of chemicals. The selection between them should be based on application requirements, substrate compatibility, and desired performance characteristics.
What factors should be considered when selecting a conformal coating material?
Selecting a conformal coating protects electronic components from environmental factors such as moisture, dust, chemicals, and temperature extremes. Several factors should be considered in the selection process:
- Environmental Conditions: Understand the operating environment where the coated electronics will be deployed. Consider temperature variations, humidity levels, chemical exposure, and potential mechanical stresses. The coating material should offer protection against these specific conditions.
- Compatibility: Ensure compatibility between the electronic components’ conformal coating material and the substrate material. Different substrates (e.g., PCBs, silicon, glass) may require different coating chemistries to ensure proper adhesion and performance.
- Application Method: Consider the method of application for the conformal coating. Standard methods include spraying, dipping, brushing, or selective coating. Choose a material that can be applied effectively using the chosen method without compromising performance or coverage.
- Thickness and Coverage: Determine the desired thickness and coverage of the coating. Thicker coatings may offer more excellent protection but could affect heat dissipation and component tolerances. Balance the need for protection with other requirements of the application.
- Electrical Properties: Evaluate the electrical properties of the coating material, especially if the electronics are sensitive to insulation resistance, dielectric strength, or capacitance. Ensure that the coating material does not interfere with the electrical functionality of the components.
- Chemical Resistance: Consider the resistance of the coating material to various chemicals, including solvents, acids, bases, and oils. Choose a coating material that can withstand exposure to substances commonly encountered in the application environment.
- Curing Process: Understand the curing process of the coating material, including the required temperature, time, and curing mechanism (e.g., thermal, UV, moisture). Ensure that the curing process is compatible with the electronic components and does not cause any damage during or after application.
- Serviceability and Repairability: Evaluate the ease of rework or repair in case of component replacement or repair. Some coating materials may be more difficult to remove or reapply than others, affecting maintenance and servicing operations.
By carefully considering these factors, manufacturers can select the most appropriate conformal coating material to ensure their electronic assemblies’ long-term reliability and performance in diverse operating environments.
Are there specific standards or certifications for conformal coating materials?
There are specific standards and certifications for conformal coating materials, primarily to ensure their effectiveness in protecting electronic assemblies from environmental stresses such as moisture, dust, chemicals, and temperature variations. Some of the most notable standards and certifications include:
- IPC Standards: The IPC (Association Connecting Electronics Industries) provides several standards related to conformal coating materials, application processes, and inspection criteria. IPC-A-610, IPC-CC-830, and IPC-HDBK-830 are critical standards that provide guidelines for conformal coating materials and their application.
- MIL-STD-810: This standard issued by the United States Department of Defense outlines environmental test methods and engineering guidelines for military equipment. While it covers a broad range of environmental factors, it also includes criteria for conformal coating materials to ensure suitability for military applications.
- UL Certification: Underwriters Laboratories (UL) offers certification services for conformal coating materials to ensure safety and performance standards compliance. UL certification assures that the conformal coatings meet specific requirements for electrical insulation, flammability, and environmental resistance.
- IEC Standards: The International Electrotechnical Commission (IEC) also publishes standards related to conformal coating materials, such as IEC 61086, which specifies requirements for conformal coatings used in electronic assemblies.
- ISO Standards: The International Organization for Standardization (ISO) has developed standards such as ISO 9001 and ISO 14001, which provide quality management and environmental management system requirements, respectively. While these standards don’t specifically focus on conformal coating materials, they are relevant for companies manufacturing or using them to ensure consistent quality and environmental responsibility.
- RoHS Compliance: Restriction of Hazardous Substances (RoHS) directives restrict the use of certain hazardous materials in electrical and electronic equipment. Conformal coating materials must comply with RoHS regulations to ensure they do not contain restricted substances such as lead, mercury, cadmium, and certain flame retardants.
Compliance with these standards and certifications ensures that conformal coating materials meet recognized criteria for performance, safety, and environmental sustainability, thereby enhancing the reliability and longevity of electronic assemblies.
Can conformal coating materials be removed or reworked?
Conformal coating materials, commonly used in electronics manufacturing to protect circuitry from environmental factors such as moisture, dust, and chemicals, can be removed or reworked under certain circumstances. Here’s an overview of the processes involved:
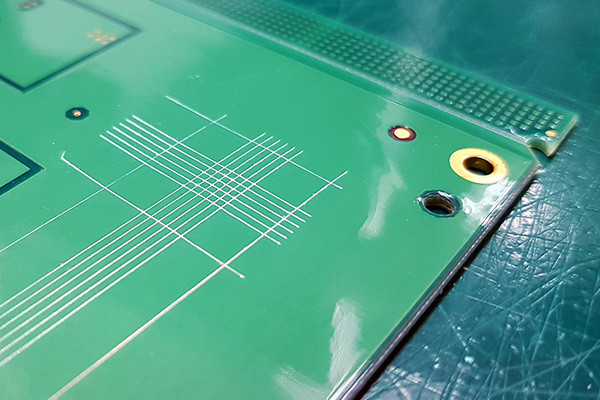
Removal of Conformal Coating:
- Chemical Stripping: Chemical solvents often dissolve and remove conformal coatings. The choice of solvent depends on the type of coating material used. For example, acrylic coatings may be removed using solvents like xylene or toluene, while silicone coatings might require different solvents.
- Mechanical Methods: Mechanical abrasion or scraping can also remove conformal coatings. However, this method is more aggressive and may risk damaging the underlying components or circuitry if not performed carefully.
- Thermal Methods: Some conformal coatings can be thermally stripped using localized heating or infrared radiation techniques. This method involves heating the coating to a temperature where it becomes soft and can be peeled or scraped away.
Reworking Conformal Coating:
- Localized Application: In cases where only specific circuitry areas require rework, the conformal coating can be selectively applied or reapplied to those areas using techniques such as brushing, spraying, or dipping.
- Masking: Before rework, regions that do not require coating can be masked off using tapes or other masking materials to prevent the application of coating where it’s not needed.
- Reapplication: If the existing coating needs to be removed entirely due to rework requirements, the process of removal (as described above) followed by reapplication can be carried out to achieve the desired protection.
Considerations:
- Compatibility: Ensure the removal and reapplication methods are compatible with the substrate materials and components to prevent damage.
- Environmental Concerns: Environmental regulations should ensure the disposal of removed coating materials and solvents.
- Quality Control: Careful inspection of the reworked areas is essential to ensure that the coating is applied correctly and provides adequate protection without defects.
Conformal coating materials can be removed or reworked using various methods depending on the application’s specific requirements, the type of coating used, and the extent of rework needed. It’s crucial to choose appropriate techniques and exercise caution to avoid damaging the underlying components or compromising the coating’s effectiveness.
Are there any considerations for application methods based on the material used?
Yes, the choice of application method for materials is crucial and depends on various factors, including the properties of the material, the desired outcome, efficiency, safety, and cost-effectiveness. Here are some considerations for different application methods based on the material used:
Liquid Materials (e.g., Paints, Adhesives, Coatings):
- Spraying: Ideal for large surface areas, providing even coverage and smooth finishes. It requires proper ventilation and protective gear.
- Brushing/Rolling: Suitable for smaller areas or intricate surfaces, offering precise control over application. It’s slower but allows for thicker coats.
- Dipping: Used for coating objects entirely, ensuring uniform coverage. It’s efficient but may require post-application drying or curing.
Solid Materials (e.g., Powders, Granules):
- Sprinkling/Scattering: Effective for evenly spreading granular or powdered substances over surfaces. It requires careful control to avoid wastage.
- Compression Molding: Utilized to shape powdered or granular materials under high pressure and temperature. It’s common in manufacturing processes for plastics and ceramics.
- Extrusion: Suitable for shaping materials with a high viscosity into specific forms, such as plastics, metals, and food products.
Gaseous Materials (e.g., Gases, Vapors):
- Injection/Atomization: Injecting gases or vaporized substances into specific environments or materials. It’s crucial in processes like fuel injection or perfume manufacturing.
- Diffusion: Employed to disperse gases or vapors evenly within a given space or material. It’s vital in processes like gas-phase reactions and semiconductor manufacturing.
Composite Materials (e.g., Fiberglass, Carbon Fiber):
- Lamination: Involves layering composite materials and bonding them under pressure and heat. It’s common in aerospace and automotive industries for producing lightweight yet strong components.
- Vacuum Bagging: Utilized to consolidate composite materials under vacuum to remove air bubbles and ensure proper adhesion. It’s critical for achieving high-quality composite parts.
The selection of application methods for materials depends on their physical state, properties, and intended use. Each method has advantages and limitations, and choosing the appropriate one is essential for achieving desired results efficiently and effectively.
How does the cost vary among different conformal coating materials?
Conformal coatings protect electronic components from environmental factors such as moisture, dust, chemicals, and temperature variations. The cost of these coatings can vary significantly based on several factors, including material composition, application method, coverage area, and performance characteristics. Here are some key considerations influencing the cost variability among different conformal coating materials:
- Material Composition: Conformal coatings can be made from various materials such as acrylics, silicones, polyurethanes, epoxies, and perylene. The cost of raw materials varies depending on factors like availability, complexity of synthesis, and desired properties. For instance, parylene coatings, known for their superior moisture barrier properties and biocompatibility, are more expensive due to the intricate deposition process and high purity requirements.
- Performance Characteristics: Different applications may require specific performance attributes such as chemical resistance, thermal conductivity, flexibility, or UV stability. Specialty coatings with enhanced properties typically command a higher price than standard formulations. For example, coatings designed for aerospace or automotive industries often undergo rigorous testing and certification, contributing to higher costs.
- Application Method: Conformal coatings can be applied using various techniques, including spraying, dipping, brushing, or selective coating. The choice of application method affects labor costs, equipment investment, material wastage, and efficiency. Automated application processes may require initial capital investment but can offer cost savings in the long run through improved consistency and reduced labor expenses.
- Coverage Area: The cost per unit area of coating application depends on the thickness required for adequate protection. Due to lower material consumption, thin-film coatings may be more economical for large-scale production. In contrast, thicker coatings may incur higher material costs but provide enhanced protection in demanding environments.
- Regulatory Compliance: Compliance with industry standards and environmental regulations can influence material sourcing, manufacturing processes, and quality control measures, impacting overall production costs. Coatings formulated with environmentally friendly or low-VOC (volatile organic compound) materials may incur additional expenses but can offer sustainability and regulatory compliance advantages.
The cost of conformal coatings varies based on material composition, performance characteristics, application method, coverage area, and regulatory compliance. Selecting the most suitable coating involves balancing cost considerations with the desired level of protection and application requirements.
Can conformal coating materials affect the electrical properties of components?
Conformal coating materials components’ electrical properties, albeit to varying extents, depending on the specific material used and its application method. Conformal coatings are applied to electronic circuit boards to protect them from environmental factors such as moisture, dust, chemicals, and temperature fluctuations. However, specific properties of the coating materials can inadvertently influence the electrical characteristics of the components they cover.
One significant aspect is the coating material’s dielectric constant. The dielectric constant measures a material’s ability to store electrical energy in an electric field. Coating materials with high dielectric constants can alter the capacitance of components or traces on the circuit board. This alteration can lead to changes in impedance, signal propagation delays, and signal integrity issues, particularly in high-frequency circuits.
Additionally, the thickness of the conformal coating layer can impact electrical properties. Excessive thickness may introduce capacitance between adjacent traces or components, affecting impedance and signal integrity. Furthermore, variations in coating thickness across the board can cause uneven insulation, potentially leading to shorts or increased parasitic capacitance.
The thermal conductivity of the coating material is another crucial factor. While conformal coatings are often applied to improve thermal management by protecting against overheating, some coatings may have poor thermal conductivity, leading to heat buildup and affecting the performance and reliability of sensitive components.
Moreover, the application method and curing process can influence electrical properties. Improper application techniques or incomplete curing may result in the formation of voids, bubbles, or uneven coatings, which can introduce unwanted electrical characteristics such as leakage currents or partial discharges.
While conformal coatings primarily protect electronic components from environmental stresses, they can inadvertently affect electrical properties. Engineers must carefully consider the dielectric constant, thickness, thermal conductivity, application method, and curing process of the coating material to minimize adverse effects on the performance and reliability of electronic devices.
What role does the thickness of the conformal coating play in its effectiveness?
The thickness of the conformal coating is a critical factor in determining its effectiveness in protecting electronic components. Conformal coatings are applied to circuit boards to protect them from environmental factors such as moisture, dust, chemicals, and mechanical stress. The thickness of the coating influences several critical aspects of its performance.
Firstly, the thickness of the coating directly affects its ability to provide insulation. A thicker coating creates a more substantial barrier between the conductive traces on the circuit board and the surrounding environment. This insulation helps prevent short circuits and electrical leakage caused by contaminants or moisture ingress. Thus, a thicker coating is generally more effective at maintaining the integrity and reliability of the electronic assembly.
Secondly, the thickness of the conformal coating impacts its ability to provide mechanical protection. Thin coatings may offer limited resistance to physical damage such as abrasion, impact, or vibration. In contrast, thicker coatings can absorb more mechanical stress and provide better protection against these hazards. This is particularly important in applications where electronic components are subjected to harsh operating conditions or frequent handling.
Furthermore, the thickness of the coating influences its ability to withstand temperature fluctuations. Thicker coatings typically have higher thermal conductivity, which helps dissipate heat generated by electronic components more effectively. This property is crucial for ensuring the longevity and performance of the coated assembly, especially in applications where temperature variations are significant.
However, it’s essential to strike a balance when considering the thickness of the conformal coating. While thicker coatings offer enhanced protection, excessive thickness can lead to uneven coverage, air entrapment, and difficulty in rework or repair. Additionally, thicker coatings may increase the overall size and weight of the electronic device, which can be undesirable in some applications.
The thickness of the conformal coating plays a crucial role in determining its effectiveness in protecting electronic components. It impacts insulation, mechanical protection, thermal management, and overall reliability. Engineers must carefully consider the application’s specific requirements to determine the optimal coating thickness for maximum performance and longevity.
Are there any health and safety considerations when working with conformal coating materials?
When working with conformal coating materials, several health and safety considerations must be considered to ensure the well-being of personnel and the environment. Conformal coatings are commonly used in electronics manufacturing to protect printed circuit boards (PCBs) from environmental stresses, such as moisture, dust, chemicals, and temperature variations. Here are some important health and safety measures to consider:
- Ventilation: Adequate ventilation is crucial when working with conformal coating materials to prevent the inhalation of harmful vapors. Ensure work areas are adequately ventilated with exhaust systems or fans to remove fumes generated during application and curing processes.
- Personal Protective Equipment (PPE): Workers should wear appropriate PPE, including gloves, goggles, and protective clothing, to minimize skin contact and prevent eye irritation or chemical exposure. Nitrile gloves are commonly recommended for handling conformal coatings as they provide chemical resistance.
- Handling and Storage: Conformal coating materials should be stored and handled according to manufacturer guidelines. Ensure containers are tightly sealed when not in use to prevent evaporation and contamination. Store materials in a well-ventilated area away from heat sources and incompatible chemicals.
- Training: Employees should receive thorough training on the proper handling, application, and disposal procedures for conformal coating materials. This includes understanding the potential hazards associated with each type of coating and knowing how to respond in case of spills or accidents.
- Emergency Procedures: Establish clear procedures for accidental exposure or spills. This may include providing access to safety showers, eyewash stations, spill kits, and emergency contact information for medical assistance.
- Disposal: Conformal coating materials may contain hazardous substances, so proper disposal is essential to prevent environmental contamination. Follow local regulations and guidelines for disposal, which may involve recycling or hazardous waste disposal facilities.
- Health Monitoring: Implement regular health monitoring programs to assess potential exposure risks and detect any adverse health effects among workers. This may include medical surveillance, such as periodic health assessments and monitoring for respiratory or skin conditions.
By adhering to these health and safety considerations, companies can minimize the risks associated with working with conformal coating materials, create a safer working environment for employees, and ensure product quality and reliability. Regular review and updates of safety protocols in line with industry standards are also recommended.
Can conformal coating materials be customized for specific applications?
Conformal coating materials can be customized for specific applications to meet various requirements and environmental conditions. Conformal coatings are applied to electronic circuitry to protect against moisture, dust, chemicals, and temperature extremes, enhancing reliability and longevity. Customization allows manufacturers to tailor the coating properties to the specific needs of their application. Here’s how customization can be achieved:
- Material Composition: Conformal coatings are available in various chemical compositions, including acrylics, silicones, polyurethanes, and epoxies. Each material offers different properties, such as flexibility, hardness, chemical resistance, and thermal stability. Manufacturers can select or even develop formulations that best suit the requirements of their application.
- Thickness and Coverage: The thickness of the coating layer can be adjusted to provide adequate protection without compromising electrical performance or adding excessive weight. Customizing the coverage area ensures that only the necessary components are coated, reducing material waste and cost.
- Specialized Properties: Some applications may require specialized properties such as UV resistance, flame retardance, or thermal conductivity. Custom formulations can incorporate additives or modifiers to impart these properties to the coating.
- Application Method: Depending on the specific requirements of the application, conformal coatings can be applied using various methods such as spraying, dipping, brushing, or selective coating. Customization involves selecting the most suitable application method to ensure uniform coverage and minimal waste.
- Curing Process: The curing process of conformal coatings can be customized based on factors such as time, temperature, and humidity. Manufacturers can optimize the curing conditions to achieve the desired level of adhesion, hardness, and chemical resistance.
- Testing and Validation: Customized conformal coatings undergo rigorous testing and validation to ensure compliance with industry standards and performance requirements. This may include accelerated aging tests, environmental exposure tests, and electrical insulation tests.
Customization of conformal coating materials enables manufacturers to tailor the protective layer to the specific demands of their application, ensuring optimal performance, reliability, and durability in diverse operating environments.
What advancements are being made in conformal coating materials?
Advancements in conformal coating materials are driven by the ever-evolving demands of modern electronics manufacturing, which require improved protection, performance, and sustainability. Several notable advancements are shaping the landscape of conformal coatings:
- Nanotechnology Integration: Nanotechnology offers opportunities to enhance conformal coatings by incorporating nanoparticles for improved barrier properties, mechanical strength, and thermal conductivity. Nanocoatings provide finer coverage and better adhesion while maintaining flexibility, thus offering superior protection against moisture, dust, and corrosion.
- Self-Healing Coatings: Researchers are exploring self-healing polymers for conformal coatings, which can autonomously repair microcracks and damage incurred during operation or handling. These coatings utilize microcapsules or reversible chemical reactions to restore the integrity of the protective layer, thereby extending the lifespan of electronic devices.
- Environmentally Friendly Formulations: There’s a growing emphasis on developing eco-friendly conformal coating materials that minimize environmental impact without compromising performance. This includes using solvent-free or low-VOC (volatile organic compound) formulations and bio-based materials derived from renewable sources, contributing to sustainability efforts in electronics manufacturing.
- Functional Coatings: Conformal coatings are evolving beyond mere protection to offer additional functionalities tailored to specific applications. For instance, coatings with enhanced thermal conductivity facilitate heat dissipation in high-power electronics, while hydrophobic coatings repel water to prevent electrical short circuits in humid environments.
- Flexible and Stretchable Coatings: With the proliferation of flexible and wearable electronics, there’s a growing need for conformal coatings that can withstand bending, stretching, and deformation without compromising performance. Advances in elastomeric materials and manufacturing techniques enable the development of coatings that maintain adhesion and barrier properties even under extreme mechanical stress.
- Innovative Coatings: Integrating smart functionalities into conformal coatings is an emerging trend. These coatings can sense environmental changes such as temperature, humidity, or chemical exposure, triggering appropriate responses to adapt and optimize protection accordingly.
Ongoing advancements in conformal coating materials aim to address the evolving requirements of electronic devices, offering enhanced protection, functionality, sustainability, and adaptability to meet the demands of diverse applications and industries.
Conclusion:
Selecting the appropriate material for conformal coating is essential to ensure the reliability and performance of electronic devices in various environments. By understanding the properties, advantages, and limitations of different coating materials, manufacturers can make informed decisions to protect their products effectively. Stay updated on advancements in conformal coating materials to leverage the latest innovations for enhanced protection and longevity of electronic components.
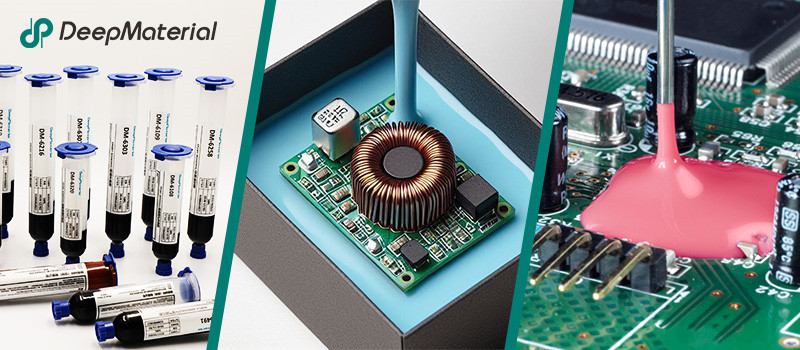
About DeepMaterial
DeepMaterial is a trusted supplier of encapsulant materials that are used in electronics manufacturing worldwide. From chip on board encapsulants such as glob top material to conformal coatings, underfills, low pressure molding, and potting solutions, DeepMaterial offers a full range of circuit board protection materials that effectively protect circuit boards while help reduce costs. More…Deepmaterial is a the manufacturer of epoxy adhesives including hardeners, metalbond, and metal filled resins. Structural, toughened medium viscosity, and non-sag adhesives are also offered. Some adhesives are resistant to thermal shock, chemical, vibration dampening, and impact. Suitable for metals, plastics, wood, and ceramics. Serves electronics, aerospace, automotive, tooling, marine, and construction industries. REACH and RoHS compliant. FDA approved. UL listed. Meets military specifications. We are the one of best adhesive manufacturers in China.
Blogs & News
Potting compounds are at the frontline of electronics assembly, delivering effective protection in challenging environmental conditions while improving mechanical strength and offering high electric insulation. Used within a variety of industries, electrical potting compounds are found within a broad range of consumer electronics, as well as used in applications across the automotive, aerospace, and other industries where electronic assemblies are prevalent.
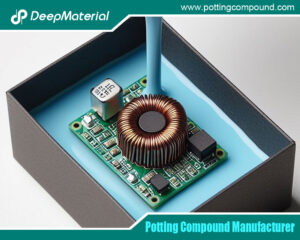
Potting Compound vs. Epoxy: A Comprehensive Comparison
Potting Compound vs. Epoxy: A Comprehensive Comparison In the world of electronics, manufacturing, and material encapsulation, two terms frequently come up: potting compounds and epoxy.
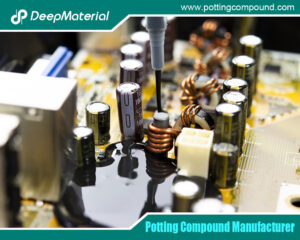
Potting Compound for PCB
Potting Compound for PCB A potting compound is a liquid or semi-liquid material that is poured or injected over a PCB or electronic assembly, then
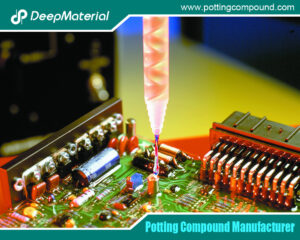
In – depth Analysis of the Curing Characteristics of Electronic Potting Compounds
In – depth Analysis of the Curing Characteristics of Electronic Potting Compounds Electronic potting compounds play a vital role in the electronics industry. They can
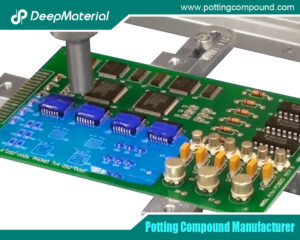
A Comprehensive Analysis of the Environmental Performance of Encapsulating Materials: From Regulations to Practices
A Comprehensive Analysis of the Environmental Performance of Encapsulating Materials: From Regulations to Practices In modern industrial manufacturing, encapsulating materials are widely used in numerous

A Comprehensive Analysis of PCB Encapsulation Quality Inspection: Innovative Application of Non-Destructive Testing Technologies
A Comprehensive Analysis of PCB Encapsulation Quality Inspection: Innovative Application of Non-Destructive Testing Technologies In the field of electronic manufacturing, the encapsulation process of printed
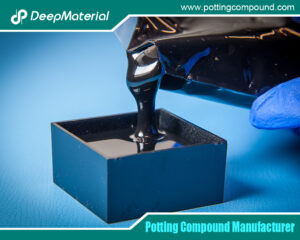
Analysis of the Improvement of the Seismic and Impact Resistance Performance of PCB by Encapsulation
Analysis of the Improvement of the Seismic and Impact Resistance Performance of PCB by Encapsulation During the operation of electronic devices, the PCB (Printed Circuit