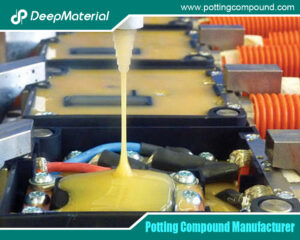
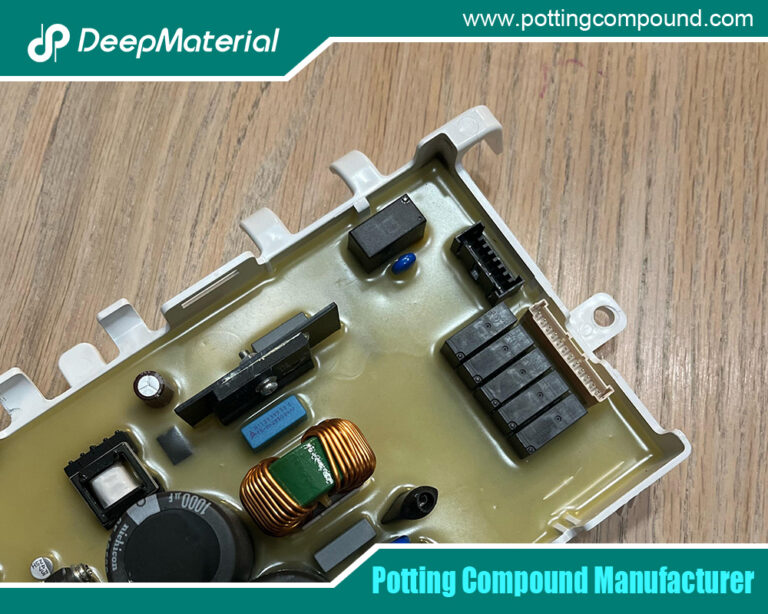
Non-Conductive Coatings for Electronics: Ensuring Safety and Longevity
- Electronic Potting Material Manufacturer
- July 4, 2024
- Acrylic Conformal Coating, adhesive glue manufacturer, conformal coating for electronics, conformal coating for pcb, conformal coating for pcb standards, conformal coating material, conformal coating process, conformal coating silicone, conformal coating spray, conformal coating waterproof, Connector Potting Compound, deepmaterial adhesive glue, Electronic Conformal Coating, electronic potting compound, epoxy adhesive, epoxy conformal coating, epoxy potting compound, Flexible Potting Compound, industrial adhesive suppliers, Industrial Conformal Coating, LED Potting Compound, non-conductive coatings for electronics, One Part Epoxy Adhesive, pcb conformal coating, PCB Potting Compound, potting compound for electronics, potting compound for pcb, silicnoe epoxy adhesive glue, Silicone Conformal Coating, silicone epoxy adhesive glue, Urethane Conformal Coating, UV Cure Conformal Coating, UV Cure Potting Compound, Waterproof Conformal Coating, waterproof potting compound
Non-Conductive Coatings for Electronics: Ensuring Safety and Longevity
The rapid advancement of electronics has revolutionized modern life, embedding complex circuitry into almost every aspect of our daily activities. As electronic devices become more sophisticated and ubiquitous, protecting these sensitive components from environmental hazards has become paramount. Non-conductive coatings are crucial in safeguarding electronic devices, ensuring their longevity, reliability, and performance. This article delves into the significance, types, applications, and prospects of non-conductive coatings for electronics.
Importance of Non-Conductive Coatings
Electrical Insulation
Non-conductive coatings are essential for providing electrical insulation, preventing short circuits leading to device failure, or even hazardous situations such as fires. By coating components with materials that do not conduct electricity, manufacturers can ensure that adjacent conductive parts do not unintentionally connect, thereby maintaining the integrity of the circuit.
Environmental Protection
Electronic devices are often exposed to environmental stressors such as moisture, dust, chemicals, and temperature fluctuations. Non-conductive coatings serve as a barrier, protecting sensitive components from corrosion, oxidation, and other forms of degradation. This protection is crucial in harsh environments, such as industrial settings or outdoor applications.
Enhanced Durability
The application of non-conductive coatings significantly enhances the durability of electronic devices. These coatings can prevent wear and tear, reduce the impact of mechanical stresses, and increase the overall lifespan of the devices. This not only improves the reliability of the electronics but also reduces maintenance costs and the frequency of replacements.
Types of Non-Conductive Coatings
Conformal Coatings
Conformal coatings are thin layers of non-conductive material applied to the surface of electronic components. They conform to the contours of the board and components, providing a uniform protective layer. Common materials used for conformal coatings include:
- Acrylicsare easy to apply and remove, offering good moisture resistance and dielectric properties.
- Polyurethanes: Known for their excellent chemical resistance and mechanical properties.
- Silicones: Provide superior flexibility and thermal stability, making them ideal for high-temperature applications.
- Epoxies: Offer strong adhesion and excellent protection against moisture and chemicals but can be harder to remove for rework.
Encapsulation (Potting) Compounds
Encapsulation involves surrounding an electronic component or assembly with a non-conductive compound, completely embedding it within a protective layer. This method protects against mechanical stresses, vibration, and environmental factors. Common encapsulation materials include:
- Epoxy Resins: Known for their strong mechanical properties and excellent moisture resistance.
- Polyurethane Resins: Provide flexibility and good resistance to thermal cycling.
- Silicone GelsOffer excellent flexibility and are ideal for applications requiring thermal and mechanical shock resistance.
Parylene Coatings
Parylene is a unique type of non-conductive coating applied through a vapor deposition process. It forms a pinhole-free, uniform film with excellent moisture, chemical, and dielectric protection. Parylene coatings are highly valued in applications requiring ultra-thin, highly conformal layers, such as medical devices and aerospace electronics.
Ceramic Coatings
Ceramic coatings are used for their exceptional thermal stability and insulating properties. These coatings can withstand extreme temperatures and protect against wear and corrosion. They are commonly used in high-power electronics and applications exposed to harsh thermal environments.
Applications of Non-Conductive Coatings
Consumer Electronics
In consumer electronics, non-conductive coatings are used extensively to protect devices like smartphones, tablets, laptops, and wearable technology. These coatings ensure that the devices remain operational despite moisture, dust, and mechanical stress exposure, enhancing their durability and performance.
Automotive Electronics
The automotive industry relies heavily on electronic systems such as engine control, safety systems, infotainment, etc. Non-conductive coatings protect these critical systems from harsh operating conditions, including temperature extremes, humidity, and vibrations, ensuring vehicle reliability and safety.
Medical Devices
Medical devices require the highest reliability and protection, as their failure can have severe consequences. Non-conductive coatings protect devices such as pacemakers, diagnostic equipment, and patient monitoring systems from bodily fluids, sterilization processes, and other environmental factors.
Industrial Electronics
Electronic components are exposed to rigorous conditions in industrial settings, including chemicals, moisture, and mechanical wear. Non-conductive coatings protect control systems, sensors, and other electronic components, ensuring long-term functionality and safety.
Aerospace and Defense
Aerospace and defense applications demand the highest standards of reliability and durability. Non-conductive coatings protect avionics, communication systems, and navigation equipment from extreme temperatures, radiation, moisture, and other environmental hazards during flight and in space.
Future Trends in Non-Conductive Coatings
Nanotechnology
Advancements in nanotechnology are shaping the future of non-conductive coatings. Nanocoatings offer superior protective properties due to their tiny particle size, which allows for the formation of highly uniform and dense protective layers. These coatings can enhance protection against moisture, chemicals, and mechanical stresses while maintaining excellent electrical insulation properties.
Smart Coatings
Innovative coatings are an emerging trend in the field of non-conductive coatings. These coatings can alter their properties to respond to environmental changes, such as temperature or humidity. For example, an intelligent coating might change its thermal conductivity in response to temperature changes, providing dynamic protection for electronic components. This adaptability can significantly enhance the performance and reliability of electronic devices in varying conditions.
Eco-Friendly Coatings
With growing environmental concerns, developing eco-friendly, non-conductive coatings is gaining traction. Researchers are exploring biodegradable and sustainable materials for coatings that minimize environmental impact without compromising performance. These advancements align with global efforts to reduce the carbon footprint and promote sustainability in the electronics industry.
Advanced Application Techniques
Innovations in application techniques are also shaping the future of non-conductive coatings. Methods such as plasma-enhanced chemical vapor deposition (PECVD) and atomic layer deposition (ALD) are being refined to provide more precise and controlled coating processes. These techniques allow for the deposition of ultra-thin, highly uniform coatings that offer superior protection and performance.
Integration with IoT and Wearable Technology
The rise of the Internet of Things (IoT) and wearable technology drives the need for advanced non-conductive coatings that protect miniaturized electronic components while maintaining flexibility and lightweight properties. Coatings that provide robust protection without adding significant bulk are crucial for developing next-generation wearable devices and IoT sensors.
Conclusion
Non-conductive coatings are indispensable in electronics, providing essential protection that ensures devices’ safety, reliability, and longevity across various industries. These coatings shield sensitive components from environmental hazards, electrical failures, and mechanical stresses from consumer electronics to aerospace. As technology continues to evolve, the development of advanced non-conductive coatings will play a pivotal role in meeting the growing demands for durable, high-performance electronic devices. The future holds exciting possibilities, with innovations in nanotechnology, intelligent coatings, and eco-friendly materials poised to revolutionize the field and pave the way for safer, more resilient electronics.
For more about non-conductive coatings for electronics: ensuring safety and longevity, you can pay a visit to DeepMaterial at https://www.pottingcompound.com/ for more info.
Recent Posts
- How to Select Suitable Potting Materials for PCB According to the Working Environment
- What is PCB Potting
- The Evolution of Smart Watch Assembly Adhesive: A Key Component in Modern Wearable Technology
- Laptop Tablet Assembly Adhesive: The Key to Durable and Reliable Device Construction
- Power Bank Assembly Adhesive: The Essential Component for Building Durable Power Banks
- Smartphone Assembly Adhesive: Enhancing Durability and Precision in Modern Devices
- TV Backplane Support and Reflective Film Bonding: A Comprehensive Guide
- Innovative Use of Compounded Materials in Electronic Device Housings: A Comprehensive Guide
- Enhancing Battery Pack Performance: A Deep Dive into Potting Materials, Benefits, and Applications
- A Comprehensive Guide to Industrial Conformal Coatings: Applications, Types, and Future Trends