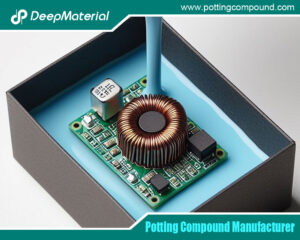
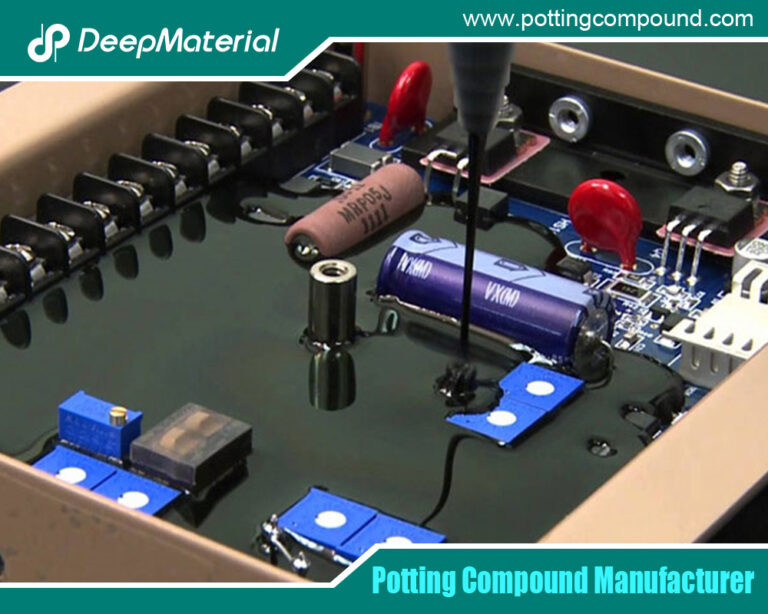
Solutions for Electrical Insulation with Epoxy Resins
- Electronic Potting Material Manufacturer
- July 9, 2024
- adhesive glue manufacturer, conformal coating for electronics, conformal coating for pcb standards, conformal coating pcb, conformal coating waterproof, deepmaterial adhesive glue, Electrical Insulation, electrical insulation coating, Electrical Insulation with Epoxy Resins, electrical potting compound, epoxy coating for electrical insulation, epoxy encapsulation electronic components, epoxy potting compound, epoxy powder coating for electrical insulation, high temperature electrical insulation coating, industrial adhesive suppliers, polyurethane potting compound, potting compound for electronics, potting compound for pcb, potting material for electronic components, silicone potting compound for electronics, UV curing potting compound, waterproof potting compound
Solutions for Electrical Insulation with Epoxy Resins
Electrical insulation is crucial in modern electrical and electronic systems, ensuring equipment’s safety, performance, and longevity. Epoxy resins have emerged as a preferred material for electrical insulation due to their exceptional mechanical, thermal, and electrical properties. This article delves into the role of epoxy resins in electrical insulation, exploring their advantages, applications, and the latest advancements in this field.
What Are Epoxy Resins?
Epoxy resins are a class of thermosetting polymers known for their excellent adhesion, chemical resistance, and durability. They are formed by an epoxide (a three-membered cyclic ether) reaction with a polyamine, resulting in a highly cross-linked polymer. This chemical structure gives epoxy resins unique properties, making them suitable for various applications, including electrical insulation.
Advantages of Epoxy Resins for Electrical Insulation
- High Dielectric Strength: Epoxy resins exhibit high dielectric strength, meaning they can withstand high voltages without breaking down. This makes them ideal for insulating components in high-voltage applications.
- Thermal Stability: They maintain their properties over a wide temperature range, ensuring reliable performance in high- and low– temperature environments.
- Chemical Resistance: Epoxy resins resist chemicals, moisture, and solvents, which help protect electrical components from corrosion and environmental damage.
- Mechanical Strength: The high mechanical strength of epoxy resins provides structural support and protection against mechanical stress and vibrations.
- Low Shrinkage: During curing, epoxy resins exhibit minimal shrinkage, reducing the risk of cracks and voids that can compromise insulation.
- Customization: Epoxy resins can be formulated to meet specific requirements, such as flexibility, thermal conductivity, or flame retardancy, allowing for tailored solutions for different applications.
Applications of Epoxy Resins in Electrical Insulation
- Transformers: Epoxy resins are used in the insulation of transformers to protect windings and other internal components from electrical, thermal, and mechanical stresses. Cast resin transformers, for instance, utilize epoxy resin to encapsulate windings, providing robust insulation and reducing the risk of short circuits.
- Motors and Generators: Epoxy resins insulate windings, stators, and rotors. This ensures efficient performance, reduces energy loss, and enhances the lifespan of the equipment.
- Printed Circuit Boards (PCBs): Epoxy resins are widely used as coatings for PCBs, providing electrical insulation, moisture resistance, and protection from mechanical damage. They also help in maintaining the integrity of solder joints and connections.
- Insulating Bushings: Epoxy resins are used to produce insulating bushings, which are critical components in high-voltage equipment. These bushings provide insulation and mechanical support, ensuring safe and reliable operation.
- Cable Joints and Terminations: Epoxy resins are employed in insulating cable joints and terminations, preventing electrical failures and enhancing the durability of power transmission systems.
- Potting and Encapsulation: In various electronic devices and components, epoxy resins are used for potting and encapsulation. This process involves embedding components in epoxy resin to provide electrical insulation, protection from environmental factors, and mechanical stability.
Advancements in Epoxy Resins for Electrical Insulation
- Nanotechnology: The incorporation of nanomaterials into epoxy resins has led to significant improvements in their properties. Nanoparticles such as silica, alumina, and carbon nanotubes enhance epoxy resins’ mechanical strength, thermal conductivity, and dielectric properties. These advanced nanocomposites offer better performance and reliability in demanding applications.
- High Thermal Conductivity Epoxies: New formulations of epoxy resins with enhanced thermal conductivity have been developed to address heat dissipation challenges in electrical and electronic systems. These materials help manage thermal loads, prevent overheating, and improve insulated components’ efficiency. Epoxies: UV-curable epoxy resins offer rapid curing times and reduced energy consumption compared to traditional thermal curing methods. These resins are particularly useful in applications requiring quick turnaround and lower processing temperatures.
- Bio-based Epoxies: With growing environmental concerns, research has focused on developing bio-based epoxy resins derived from renewable resources. These sustainable alternatives perform comparable to conventional epoxies while reducing the ecological footprint.
- Flexible Epoxy Systems: Advances in epoxy formulations have led to development of flexible epoxy systems that combine high flexibility with excellent electrical insulation properties. These materials are ideal for applications where mechanical flexibility is crucial, such as wearable electronics and flexible circuits.
- Enhanced Flame Retardancy: The development of epoxy resins with enhanced flame retardancy has been a significant advancement, particularly for applications requiring high safety and fire resistance levels. These materials help prevent the spread of flames and ensure the safety of electrical systems.
Challenges and Future Directions
Despite the numerous advantages and advancements, there are still challenges associated with using epoxy resins for electrical insulation. One of the primary challenges is the brittleness of epoxy resins, which can lead to cracks and failures under mechanical stress. Efforts are ongoing to develop formulations that balance mechanical strength and flexibility.
Another challenge is the environmental impact of epoxy resins, particularly those derived from petrochemical sources. Developing bio-based and recyclable epoxy resins is a step in the right direction, but further research is needed to improve their performance and scalability.
The future of epoxy resins in electrical insulation lies in the continuous development of advanced formulations and composites. Innovations in nanotechnology, material science, and sustainable chemistry will play a crucial role in addressing current challenges and expanding the applications of epoxy resins in electrical insulation.
Case Studies and Real-world Applications
- High-Voltage Transformer Insulation: A leading electrical equipment manufacturer implemented epoxy resin insulation in their high-voltage transformers. The result was a significant reduction in electrical losses and enhanced operational reliability. Using epoxy resin also minimized the risk of oil leaks and environmental contamination, a common issue with traditional oil-filled transformers.
- Electric Vehicle (EV) Batteries: With the rise of electric vehicles, the demand for reliable and efficient battery insulation has increased. Epoxy resins have been utilized to insulate and protect battery modules, ensuring safety and performance. The thermal stability and chemical resistance of epoxy resins help manage the thermal and electrical stresses within EV batteries.
- Renewable Energy Systems: In wind turbines and solar power systems, epoxy resins insulate and protect electrical components exposed to harsh environmental conditions. For instance, in wind turbines, epoxy resin-based composites are used to insulate and encapsulate the generators, improving durability and reducing maintenance costs.
- Consumer Electronics: Leading electronics companies use epoxy resins to spot and encapsulate sensitive components in smartphones, laptops, and other devices. This not only provides electrical insulation but also protects against moisture, dust, and mechanical shocks, ensuring the longevity and reliability of the devices.
Conclusion
Epoxy resins have become indispensable in electrical insulation. They offer a combination of high dielectric strength, thermal stability, chemical resistance, and mechanical robustness. Their versatility and ability to be tailored for specific applications make them suitable for various electrical and electronic systems.
Advancements in nanotechnology, high thermal conductivity formulations, UV-curable systems, bio-based alternatives, and flexible epoxies are driving the evolution of epoxy resins, addressing existing challenges, and expanding their applications. As research and development continue, epoxy resins are poised to play an even more critical role in the future of electrical insulation, contributing to safer, more efficient, and sustainable electrical and electronic systems.
Through continuous innovation and adaptation, epoxy resins will remain at the forefront of materials used for electrical insulation, meeting the growing demands of modern technology and industry.
For more about the solutions for electrical insulation with epoxy resins, you can pay a visit to DeepMaterial at https://www.pottingcompound.com/ for more info.
Recent Posts
- Potting Compound vs. Epoxy: A Comprehensive Comparison
- Potting Compound for PCB
- In – depth Analysis of the Curing Characteristics of Electronic Potting Compounds
- A Comprehensive Analysis of the Environmental Performance of Encapsulating Materials: From Regulations to Practices
- A Comprehensive Analysis of PCB Encapsulation Quality Inspection: Innovative Application of Non-Destructive Testing Technologies
- Analysis of the Improvement of the Seismic and Impact Resistance Performance of PCB by Encapsulation
- A Comprehensive Guide to Evaluating the Reliability of Encapsulation Materials for Encapsulated PCBs
- In-depth Analysis of the Reparability of Encapsulation Materials
- A Comprehensive Analysis of Post-Potting PCB Issues and the Repair and Rework of Potting Materials
- A Comprehensive Analysis of the Compatibility between Encapsulation Materials and PCBs: Exploration of Chemical Reactions and Their Impact on Performance