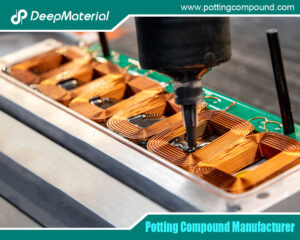
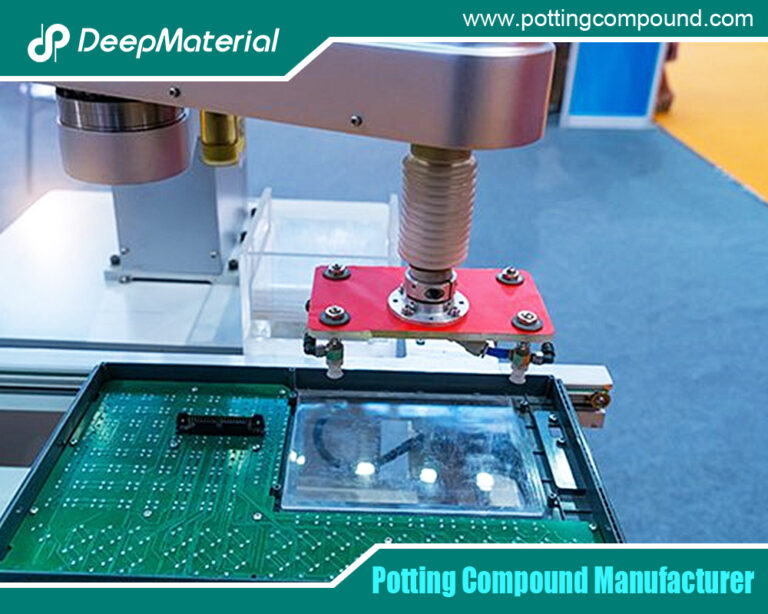
Potting Material for Electronic Components
- Electronic Potting Material Manufacturer
- July 10, 2024
- Automotive potting material manufacturers, circuit board potting, circuit board potting compound, conformal coating for electronics, conformal coating for pcb, conformal coating for pcb standards, conformal coating material, conformal coating pcb, conformal coating process, conformal coating silicone, conformal coating spray, conformal coating types, conformal coating waterproof, Connector Potting Compound, custom automated electronics potting, customize china electronic potting silicone factories, electrical potting compound, electronic epoxy encapsulant potting compounds, Electronic Potting and Encapsulation, electronic potting compound, electronic potting material, electronic potting silicone, epoxy encapsulation electronic components, pcb potting, polyurethane potting compound for electronics, potting material, potting material for electronic, potting material for electronic components, potting material for electronic compounds, potting material for electronics, what is pcb potting
Potting Material for Electronic Components
In the intricate world of electronic manufacturing, potting materials play a pivotal role in ensuring electronic components’ longevity, performance, and reliability. This article delves into the various types of potting materials, their applications, benefits, and the evolving technological landscape surrounding their use in electronics.
Introduction to Potting Materials
Potting materials encapsulate electronic components to protect them from environmental hazards such as moisture, chemicals, mechanical shocks, and vibrations. The process, known as potting, involves filling an electronic assembly with a liquid compound that hardens to form a protective shell. This technique is critical in enhancing the durability and performance of electronic devices in various industries, from consumer electronics to aerospace and automotive sectors.
Types of Potting Materials
The choice of potting material depends on the application’s specific requirements, including thermal management, electrical insulation, and environmental protection. The primary types of potting materials include:
- Epoxy Resins
- Polyurethane Resins
- Silicone Resins
- Acrylics
- Epoxy Resins
Epoxy resins are widely used due to their excellent electrical insulation properties, high mechanical strength, and good adhesion to various substrates. They are ideal for applications requiring robust protection against environmental stressors. Epoxy resins offer superior resistance to chemicals and heat, making them suitable for high-temperature applications. However, they can be brittle, which may limit their use in applications involving significant thermal cycling or mechanical stress.
Advantages of Epoxy Resins:
- High mechanical strength
- Excellent adhesion
- Superior chemical resistance
- Good electrical insulation
Disadvantages of Epoxy Resins:
- Brittle nature
- Limited flexibility
- Extended curing times for some formulations
Polyurethane Resins
Polyurethane resins are known for their flexibility, which makes them ideal for applications requiring impact resistance and thermal cycling. They provide good electrical insulation and can be formulated to offer varying degrees of hardness, from soft and rubbery to stiff and rigid. Polyurethanes are also resistant to moisture and chemicals, making them suitable for outdoor and automotive applications.
Advantages of Polyurethane Resins:
- Flexible and impact-resistant
- Good electrical insulation
- Moisture and chemical resistance
- Versatile hardness options
Disadvantages of Polyurethane Resins:
- Potential for hydrolytic degradation
- Sensitivity to moisture during curing
- Limited high-temperature resistance compared to epoxies
Silicone Resins
Silicone resins are valued for their outstanding thermal stability and flexibility. They remain stable over a wide temperature range, from as low as -55°C to as high as 200°C or more, making them suitable for harsh environmental conditions. Silicones also offer excellent moisture resistance and electrical insulation. Their inherent flexibility helps absorb mechanical stresses, reducing the risk of component damage.
Advantages of Silicone Resins:
- Excellent thermal stability
- High flexibility
- Superior moisture resistance
- Good electrical insulation
Disadvantages of Silicone Resins:
- Higher cost compared to other resins
- Longer curing times for some formulations
- Potential for outgassing
Acrylics
Acrylics are less commonly used but offer unique advantages, such as UV resistance and fast curing times. They are typically used in applications where rapid processing is essential. Acrylic potting compounds provide good electrical insulation and moderate mechanical strength. However, their thermal stability is generally lower than epoxies and silicones.
Advantages of Acrylics:
- Fast curing
- UV resistance
- Good electrical insulation
Disadvantages of Acrylics:
- Lower thermal stability
- Limited mechanical strength compared to epoxies and polyurethanes
Applications of Potting Materials
Potting materials are used in a myriad of applications across various industries. Here are some prominent examples:
Consumer Electronics
In consumer electronics, potting materials protect delicate components such as sensors, microchips, and circuit boards from environmental factors like dust, moisture, and mechanical shocks. Smartphones, tablets, and wearable devices often rely on potting compounds to enhance durability and reliability.
Automotive Electronics
The automotive industry heavily relies on electronic systems for engine control units (ECUs), sensors, and infotainment systems. Potting materials ensure these components withstand the harsh conditions of automotive environments, including temperature extremes, vibrations, and exposure to chemicals like fuel and oil.
Aerospace and Defense
Aerospace and defense applications demand the highest reliability and performance from electronic components. Potting materials in these industries must endure extreme temperatures, high altitudes, and intense mechanical stresses. They protect avionics, navigation systems, and communication devices from these challenging conditions.
Industrial Equipment
Electronic components are often exposed to harsh environments in industrial settings, including high temperatures, moisture, chemicals, and mechanical shocks. Potting compounds protect sensors, control units, and power supplies, ensuring consistent performance and longevity.
Renewable Energy
Renewable energy systems like solar panels and wind turbines rely on electronics for power conversion, monitoring, and control. Potting materials shield these components from environmental factors like UV radiation, moisture, and temperature fluctuations, enhancing the reliability and efficiency of renewable energy installations.
Selection Criteria for Potting Materials
Choosing the suitable potting material involves evaluating several vital factors to ensure optimal protection and performance of electronic components. Some critical selection criteria include:
Thermal Conductivity
Thermal conductivity is crucial for applications where heat dissipation is a concern. Potting materials with high thermal conductivity help manage heat generated by electronic components, preventing overheating and ensuring reliable operation.
Electrical Insulation
Electrical insulation properties are vital for preventing short circuits and ensuring the safe operation of electronic devices. Potting compounds must offer excellent dielectric strength to protect sensitive components.
Mechanical Strength
Mechanical strength is essential for withstanding mechanical shocks, vibrations, and impacts. Potting materials must provide adequate mechanical support to prevent damage to electronic components.
Chemical Resistance
Chemical resistance is necessary for applications exposed to corrosive substances, such as automotive and industrial environments. Potting compounds must resist degradation from chemicals like fuels, oils, and solvents.
Environmental Conditions
The environmental conditions in which the electronic components will operate play a significant role in material selection. Factors such as temperature extremes, humidity, and exposure to UV radiation must be considered.
Curing Time
Curing time impacts the production process and overall efficiency. Fast-curing potting materials are advantageous for high-volume manufacturing, while slower-curing materials may suit applications requiring precise encapsulation.
Advances in Potting Material Technology
The field of potting materials continues to evolve, driven by advancements in material science and the increasing demands of modern electronic applications. Some notable trends and innovations include:
Nanocomposites
Nanocomposites are emerging as a promising class of potting materials. By incorporating nanoparticles into traditional resins, these materials offer enhanced thermal conductivity, mechanical strength, and electrical insulation. Nanocomposites can provide superior protection for high-performance electronic components.
Environmentally Friendly Formulations
As sustainability becomes a priority, there is a growing demand for environmentally friendly potting materials. Researchers are developing bio-based resins and formulations with reduced environmental impact. These green potting materials offer similar performance characteristics while minimizing ecological footprint.
UV-Curable Potting Compounds
UV-curable potting compounds provide rapid curing times, making them ideal for high-speed manufacturing processes. These materials harden upon exposure to ultraviolet light, significantly reducing production cycle times and increasing throughput.
Advanced Thermal Management Solutions
With electronic devices’ increasing power density, advanced thermal management solutions are crucial. Potting materials with high thermal conductivity and phase-change properties help dissipate heat effectively, ensuring reliable performance in high-power applications.
Smart Potting Materials
Innovative potting materials are being developed to offer additional functionalities such as self-healing and sensing capabilities. These materials can detect and repair minor damages, enhancing the longevity of electronic components and reducing maintenance costs.
Challenges and Future Outlook
While potting materials offer numerous benefits, they also present specific challenges that must be addressed to meet the evolving demands of the electronics industry.
Compatibility Issues
Ensuring compatibility between potting materials and electronic components is critical. Incompatibility can lead to poor adhesion, delamination, and reduced performance. Ongoing research focuses on developing materials that are compatible with a wide range of substrates and component materials.
Process Optimization
Optimizing the potting process is essential for achieving consistent results and minimizing defects. Factors such as viscosity, curing time, and application methods must be carefully controlled to ensure uniform encapsulation and reliable protection.
Cost Considerations
The cost of potting materials can be a significant factor, especially for high-volume manufacturing. Balancing performance and cost-effectiveness is crucial for selecting the suitable material for a given application. Advances in material formulations and manufacturing techniques aim to reduce costs without compromising quality.
Regulatory Compliance
Meeting regulatory requirements and industry standards is essential for the widespread adoption of potting materials. Ensuring compliance with safety, environmental, and performance standards is crucial for manufacturers and end-users.
Conclusion
Potting materials are indispensable in the electronics industry, providing essential protection and enhancing the reliability of electronic components. The diverse potting materials, including epoxy, polyurethane, silicone, and acrylic resins, offer solutions for various applications and environmental conditions. As technology advances, innovative potting materials such as nanocomposites, environmentally friendly formulations, and intelligent materials are poised to address emerging challenges and drive the future of electronic manufacturing. With ongoing research and development, the role of potting materials in ensuring the performance and longevity of electronic devices will remain critical, supporting the ever-evolving landscape of modern electronics.
For more about potting material for electronic components, you can pay a visit to DeepMaterial at https://www.pottingcompound.com/ for more info.
Recent Posts
- Waterproof Potting Compound: A Comprehensive Guide
- Silicone Potting Compound for Electronics
- Potting Compound vs. Epoxy: A Comprehensive Comparison
- Potting Compound for PCB
- In – depth Analysis of the Curing Characteristics of Electronic Potting Compounds
- A Comprehensive Analysis of the Environmental Performance of Encapsulating Materials: From Regulations to Practices
- A Comprehensive Analysis of PCB Encapsulation Quality Inspection: Innovative Application of Non-Destructive Testing Technologies
- Analysis of the Improvement of the Seismic and Impact Resistance Performance of PCB by Encapsulation
- A Comprehensive Guide to Evaluating the Reliability of Encapsulation Materials for Encapsulated PCBs
- In-depth Analysis of the Reparability of Encapsulation Materials