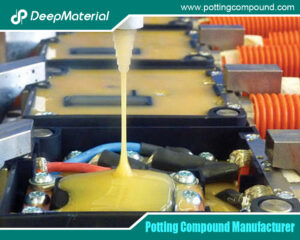
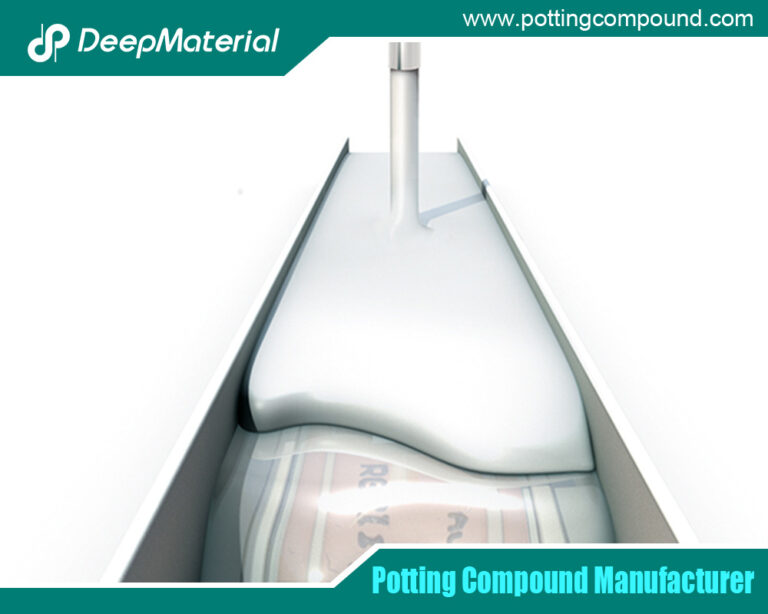
Epoxy Powder Coating for Electrical Insulation: Enhancing Performance and Protection
- Electronic Potting Material Manufacturer
- July 18, 2024
- Acrylic Conformal Coating, acrylic vs silicone conformal coating, circuit board potting, conformal coating electronics, conformal coating for electronics, conformal coating for pcb, conformal coating for pcb standards, conformal coating material, conformal coating pcb, conformal coating process, conformal coating silicone, conformal coating spray, conformal coating types, conformal coating waterproof, electrical potting compound, electronic epoxy encapsulant potting compounds, epoxy encapsulation electronic components, epoxy encapsulation meaning, epoxy encapsulation molding compound, epoxy potting compound, Epoxy Powder Coating for Electrical, Industrial Conformal Coating, polyurethane potting compound, potting compound for electronics, potting compound for pcb, potting compound vs epoxy, potting material for electronic components, potting material for electronics, silicone potting compound for electronics, thermal potting compound, Urethane Conformal Coating, UV curing potting compound, Waterproof Conformal Coating
Epoxy Powder Coating for Electrical Insulation: Enhancing Performance and Protection
In the modern world, where electrical systems and components are integral to daily life and industry, ensuring their longevity and reliability is paramount. One critical method to protect these components is using epoxy powder coatings. Epoxy powder coating for electrical insulation has emerged as a vital technology, providing superior insulation, enhanced durability, and improved performance. This article explores the intricacies of epoxy powder coatings, their application in electrical insulation, and their numerous benefits.
Understanding Epoxy Powder Coating
Epoxy powder coating is a dry finishing process that has become extremely popular since its introduction in North America in the 1960s. Pier coatings on various products represent over 15% of the total industrial finishing market. More and more companies specify powder coatings for a high-quality, durable finish, allowing for maximized production, improved efficiencies, and simplified environmental compliance. Here are critical aspects of epoxy powder coating, particularly for electrical insulation:
- Durable Finish: Epoxy powder coatings provide a robust, long-lasting finish that protects against corrosion, wear, and impact.
- Electrical Insulation: This coating type is widely used for its excellent electrical insulation properties, making it ideal for electronic and electrical components.
- High-Quality:It offers a superior finish that enhances the appearance and performance of coated products.
- Efficiency: The application process, with minimal waste and high transfer efficiency, contributes to cost savings.
- Environmental Compliance: Epoxy powder coatings are solvent-free and emit negligible volatile organic compounds (VOCs), making them an environmentally friendly choice.
- Versatility: Suitable for various substrates, including metals and heat-sensitive materials, due to its low curing temperatures.
Critical Characteristics of Epoxy Powder Coatings
- Durability: Epoxy coatings are renowned for their hardness and resistance to abrasion and impact, making them ideal for protecting electrical components subjected to mechanical stresses.
- Adhesion: These coatings exhibit excellent adhesion properties, ensuring they stay intact and provide consistent insulation over time.
- Chemical Resistance:Epoxy powder coatings resist chemicals and solvents, preventing corrosion and degradation in harsh environments.
- Thermal Stability: They maintain their properties over a wide temperature range, which is crucial for electrical components that generate significant heat.
The Role of Epoxy Powder Coating in Electrical Insulation
Electrical insulation is critical to the safe and efficient operation of electrical systems. Insulation materials prevent unwanted current flow, protect against electrical shock, and ensure electrical components operate within their specified parameters.
Benefits of Epoxy Powder Coating for Electrical Insulation:
- Enhanced Electrical Insulation: Epoxy powder coatings provide superior dielectric properties, ensuring effective insulation and reducing the risk of electrical faults.
- Heat Resistance: They can withstand high temperatures without losing their insulating properties, making them suitable for components under thermal stress.
- Moisture and Chemical Resistance: These coatings protect against moisture ingress and chemical exposure, which can otherwise compromise the insulating properties of electrical components.
- Environmental Protection: Epoxy coatings safeguard components from environmental factors such as humidity, dust, and corrosive agents, extending their lifespan and reliability.
Application Techniques
Applying epoxy powder coating involves several steps, each crucial to achieving a high-quality, durable finish. The process can be divided into the following stages:
- Surface Preparation: To ensure proper adhesion, the substrate must be cleaned and prepared. It often involves cleaning, degreasing, and sometimes sandblasting to create a suitable surface profile.
- Powder Application:The epoxy powder is electrostatically charged and sprayed onto the grounded component. It ensures even coverage and adherence of the powder to the surface.
- Curing: The coated component is then heated in a curing oven, where the powder melts and flows into a smooth, continuous film. The heat also initiates a chemical reaction that hardens the epoxy, creating a robust coating.
Advantages Over Traditional Insulation Methods
While traditional insulation methods, such as varnishes and tapes, are still in use, epoxy powder coatings offer several advantages:
- Uniform Coverage:Powder coating ensures even and uniform coverage, eliminating weak spots that can occur with liquid coatings or tapes.
- Enhanced Durability:Epoxy powder coatings are more resistant to mechanical damage and environmental factors, offering longer-lasting protection.
- Efficiency: The powder coating process is highly efficient, with minimal waste and the ability to coat complex shapes and geometries.
- Safety and Environmental Impact: Powder coatings are free of solvents and volatile organic compounds (VOCs), making them safer for workers and reducing environmental impact.
Applications in Various Industries
Epoxy powder coatings are used in a wide range of industries, each benefiting from this technology’s enhanced protection and performance.
Industrial Applications:
- Electrical Motors and Generators:These components benefit from the superior insulating properties and thermal stability of epoxy coatings, ensuring reliable operation under high loads and temperatures.
- Transformers:Epoxy powder coatings protect transformer windings and cores from moisture, chemicals, and mechanical damage, improving efficiency and lifespan.
- Switchgear and Control Panels: These critical components are protected from environmental factors and mechanical wear, ensuring consistent performance and safety.
Consumer Electronics:
- Circuit Boards: Epoxy coatings provide a protective layer that insulates and shields delicate electronic circuits from moisture, dust, and physical damage.
- Connectors and Terminals: The coatings prevent corrosion and ensure reliable electrical connections in various devices and appliances.
Automotive Industry:
- Battery Components: Epoxy coatings protect battery terminals and connectors from corrosion and ensure efficient power transmission.
- Electric Vehicle Motors: These motors benefit from the enhanced insulation and durability provided by epoxy powder coatings, contributing to electric vehicles’ overall reliability and performance.
Future Trends and Developments
The demand for epoxy powder coatings in electrical insulation is expected to grow, driven by technological advancements and increasing awareness of their benefits. Future trends may include:
- Nanotechnology: Incorporating nanomaterials into epoxy coatings to enhance their properties, such as increased thermal conductivity and mechanical strength.
- Eco-Friendly Formulations:Developing more environmentally friendly epoxy coatings with reduced environmental impact and improved safety profiles.
- Innovative Coatings: Innovating with coatings that can change properties in response to environmental conditions, providing adaptive protection for electrical components.
Conclusion
Epoxy powder coating for electrical insulation represents a significant advancement in the protection and performance of electrical components. By providing superior dielectric properties, thermal stability, and resistance to environmental factors, these coatings enhance the reliability and longevity of a wide range of products and systems. As technology continues to evolve, epoxy powder coatings will likely play an increasingly important role in ensuring electrical systems safe and efficient operation across various industries. The future holds exciting possibilities for this versatile and essential technology, promising continued improvements and innovations that will benefit industry and consumers alike.
For more about choosing the Top Epoxy Powder Coating for Electrical Insulation: Enhancing Performance and Protection, you can pay a visit to DeepMaterial at https://www.pottingcompound.com/ for more info.
Recent Posts
- How to Select Suitable Potting Materials for PCB According to the Working Environment
- What is PCB Potting
- The Evolution of Smart Watch Assembly Adhesive: A Key Component in Modern Wearable Technology
- Laptop Tablet Assembly Adhesive: The Key to Durable and Reliable Device Construction
- Power Bank Assembly Adhesive: The Essential Component for Building Durable Power Banks
- Smartphone Assembly Adhesive: Enhancing Durability and Precision in Modern Devices
- TV Backplane Support and Reflective Film Bonding: A Comprehensive Guide
- Innovative Use of Compounded Materials in Electronic Device Housings: A Comprehensive Guide
- Enhancing Battery Pack Performance: A Deep Dive into Potting Materials, Benefits, and Applications
- A Comprehensive Guide to Industrial Conformal Coatings: Applications, Types, and Future Trends