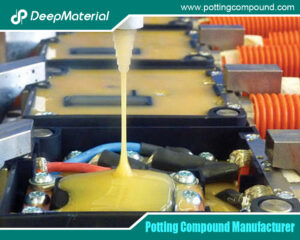
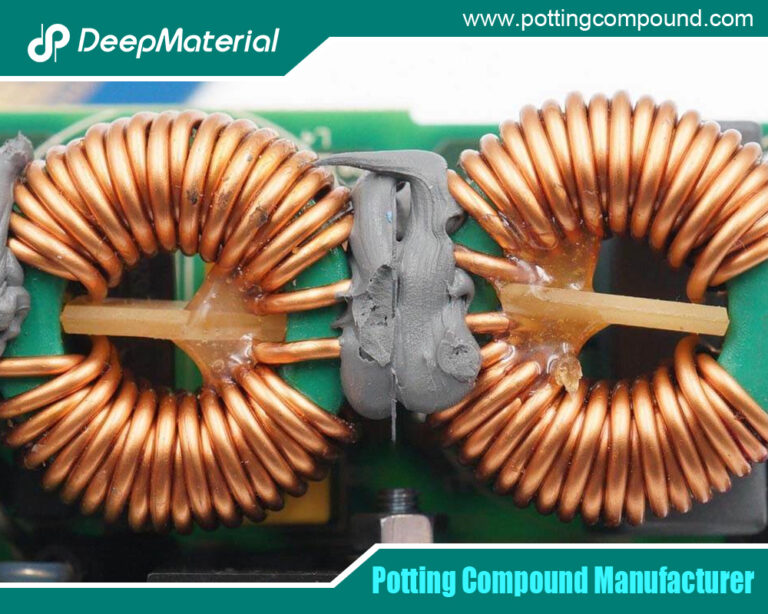
Electronics Encapsulation Epoxy Adhesive
- Electronic Potting Material Manufacturer
- August 8, 2024
- circuit board potting, conformal coating for electronics, conformal coating pcb, conformal coating silicone, conformal coating waterproof, electronic epoxy encapsulant potting compounds, electronics encapsulation epoxy adhesive, electronics encapsulation epoxy adhesive glue, epoxy encapsulation, epoxy encapsulation electronic components, epoxy encapsulation for photovolatics and oleds, epoxy encapsulation led, epoxy encapsulation meaning, epoxy encapsulation molding compound, epoxy potting compound, epoxy resin encapsulation, epoxy resin encapsulation solar panels, ossila encapsulation epoxy, pcb encapsulation epoxy, pcb encapsulation epoxy adhesive glue, pcb potting, polyurethane potting compound for electronics, potting compound for electronics, potting compound vs epoxy, potting material for electronic components, potting material for electronics, silicone potting compound for electronics
Electronics Encapsulation Epoxy Adhesive
Electronic encapsulation epoxy adhesive is a critical component in the manufacturing and protecting electronic devices. This material protects sensitive electronic components from environmental factors such as moisture, dust, chemicals, and physical damage. By providing a robust protective layer, encapsulation epoxy adhesives help ensure electronic device longevity, reliability, and performance.
Properties of Electronics Encapsulation Epoxy Adhesive
Thermal Stability
One of the essential properties of encapsulation epoxy adhesives is their thermal stability. Electronic devices often generate heat during operation, and the adhesive must withstand these high temperatures without degrading. Epoxy adhesives typically have high thermal resistance, allowing them to maintain their integrity and protective qualities even under extreme conditions.
Electrical Insulation
Encapsulation epoxy adhesives provide excellent electrical insulation. This property is crucial for preventing short circuits and ensuring the safe operation of electronic components. The adhesive forms a non-conductive barrier that helps isolate individual components, protecting them from unintended electrical interference.
Chemical Resistance
Electronic devices can be exposed to various chemicals during their lifetime, including solvents, oils, and cleaning agents. Encapsulation epoxy adhesives are formulated to resist chemical degradation, ensuring that the protective barrier remains intact and provides reliable protection.
Mechanical Strength
The mechanical strength of encapsulation epoxy adhesives is vital for protecting electronic components from physical damage. These adhesives can absorb and distribute mechanical stresses, reducing the risk of fractures, disconnections, or other physical damage to the components they protect.
Applications of Electronics Encapsulation Epoxy Adhesive
Consumer Electronics
Encapsulation epoxy adhesives are widely used in consumer electronics to protect components in devices such as smartphones, tablets, and laptops. These adhesives help safeguard sensitive circuits and chips from the everyday hazards of moisture, dust, and physical impact.
Automotive Electronics
The automotive industry relies heavily on encapsulation epoxy adhesives to protect electronic systems in vehicles. From engine control units (ECUs) to infotainment systems, these adhesives ensure that automotive electronics can withstand the harsh conditions of temperature fluctuations, vibrations, and exposure to chemicals like fuel and oil.
Industrial Electronics
Industrial environments can be particularly harsh on electronic components. Encapsulation epoxy adhesives are used in industrial electronics to protect sensors, control systems, and other critical components from dust, moisture, chemicals, and mechanical stress exposure.
Medical Devices
In the medical field, encapsulation epoxy adhesives are crucial in protecting electronic components in devices such as pacemakers, hearing aids, and diagnostic equipment. These adhesives ensure that medical devices remain reliable and safe for use in various conditions, including exposure to bodily fluids and sterilisation processes.
Benefits of Using Electronics Encapsulation Epoxy Adhesive
Enhanced Durability and Longevity
By providing a protective barrier against environmental factors, encapsulation epoxy adhesives significantly enhance the durability and longevity of electronic components. This protection translates to longer device lifespans and reduced maintenance costs.
Improved Performance and Reliability
Encapsulation epoxy adhesives help maintain the performance and reliability of electronic devices by preventing damage from moisture, dust, and chemicals. This reliability is critical in applications where device failure, such as automotive or medical electronics, can have serious consequences.
Cost-Effective Protection
Investing in encapsulation epoxy adhesives can be a cost-effective strategy for protecting electronic components. By reducing the likelihood of component failure and extending device lifespans, these adhesives can help lower the overall cost of ownership for electronic devices.
Challenges and Considerations in Using Electronics Encapsulation Epoxy Adhesive
Curing Time and Conditions
The curing time and conditions for encapsulating epoxy adhesives can vary widely depending on the formulation. Some adhesives may require elevated temperatures or extended curing times to achieve their complete protective properties. Manufacturers must carefully consider these factors when selecting an adhesive for their application.
Compatibility with Electronic Components
It is essential to ensure that the encapsulation epoxy adhesive is compatible with the electronic components and materials used in the device. Incompatible materials can lead to poor adhesion, chemical reactions, or component damage.
Application Process
The application process for encapsulation of epoxy adhesives can be complex and may require specialised equipment or techniques. Manufacturers must develop robust application processes to ensure the adhesive is applied consistently and effectively, providing the intended protection for the electronic components.
Advances in Electronics Encapsulation Epoxy Adhesive Technology
Low-Temperature Cure Formulations
Recent advances in encapsulation epoxy adhesive technology have led to developing low-temperature cure formulations. These adhesives can achieve complete cures at lower temperatures, reducing the risk of heat damage to sensitive electronic components during the curing process.
Enhanced Thermal Conductivity
Some encapsulation epoxy adhesives are now formulated with enhanced thermal conductivity properties. These adhesives can help dissipate heat generated by electronic components, improving thermal management and reducing the risk of overheating.
Eco-Friendly Formulations
There is a growing demand for eco-friendly encapsulation epoxy adhesives that minimize environmental impact. Manufacturers are developing adhesives with reduced volatile organic compounds (VOCs) and other environmentally harmful substances, making them safer for the environment and the people handling them.
Case Studies of Electronics Encapsulation Epoxy Adhesive
Smartphone Manufacturing
Encapsulation epoxy adhesives are extensively used in the smartphone industry to protect internal components such as the motherboard, chips, and battery connections. A leading smartphone manufacturer implemented a high-performance encapsulation epoxy adhesive to enhance its latest model’s water and dust resistance. The result was significantly reduced device failures due to moisture ingress, leading to improved customer satisfaction and reduced warranty claims.
Automotive Electronic Control Units (ECUs)
Automotive ECUs are critical for engine performance, transmission, and other vehicle functions. A prominent automotive electronics supplier faced challenges with ECU reliability due to exposure to harsh under-the-hood environments. The supplier improved ECU durability and reliability by adopting a specialised encapsulation epoxy adhesive with superior thermal and chemical resistance, resulting in fewer failures and enhanced vehicle performance.
Industrial Sensor Protection
An industrial equipment manufacturer utilised encapsulation epoxy adhesives to protect sensors used in heavy machinery. These sensors were prone to damage from dust, moisture, and vibrations. Introducing a robust encapsulation solution significantly reduced sensor failures, ensuring continuous and reliable operation of the machinery in demanding environments.
Medical Device Reliability
A medical device company producing implantable devices, such as pacemakers, faced strict regulatory requirements for device reliability and longevity. Using biocompatible encapsulation epoxy adhesives, the company ensured that the electronic components within their devices were protected from bodily fluids and sterilisation processes. This extended the devices’ lifespan and ensured patient safety and compliance with medical standards.
Future Trends in Electronics Encapsulation Epoxy Adhesive
Nanotechnology Integration
The integration of nanotechnology into encapsulation epoxy adhesives is an emerging trend. Nanomaterials can enhance adhesives’ thermal, electrical, and mechanical properties, providing excellent protection for electronic components. For example, incorporating graphene nanoparticles can improve thermal conductivity, aiding in better heat dissipation and enhancing the overall performance of the adhesive.
Smart Encapsulation Materials
Another exciting advancement is the development of smart encapsulation materials that can respond to environmental changes. These materials can adapt their properties based on external conditions, such as temperature or humidity, offering dynamic protection to electronic components. This adaptability can further enhance the reliability and longevity of devices in varying environments.
Sustainable and Bio-based Adhesives
As environmental concerns grow, the demand for sustainable and bio-based encapsulation epoxy adhesives increases. Research is underway to develop adhesives derived from renewable resources with minimal environmental impact. These eco-friendly adhesives aim to provide the same protection and performance as traditional epoxy adhesives while being more sustainable.
Enhanced Application Techniques
Advancements in application techniques, such as precision dispensing and automated application systems, are improving the efficiency and consistency of encapsulation processes. These technologies ensure that the adhesive is applied uniformly and accurately, reducing waste and improving the overall quality of the encapsulation.
Best Practices for Using Electronics Encapsulation Epoxy Adhesive
Surface Preparation
Proper surface preparation is crucial for achieving strong adhesion and optimal protection. Surfaces should be clean, dry, and free from contaminants such as oils, dust, or moisture. Mechanical or chemical surface treatments may be necessary to enhance adhesion, depending on the application.
Choosing the Right Adhesive
It is essential to select the appropriate encapsulation epoxy adhesive based on the application’s specific requirements. Consider thermal and electrical properties, chemical resistance, and curing conditions. Consulting with manufacturers or specialists can help identify the best adhesive for your needs.
Application Methodology
Consistent and controlled application of the adhesive is vital to ensure uniform protection. Techniques such as automated dispensing systems or manual applications with precision tools can be used. Follow manufacturer mixing, application, and curing guidelines to achieve the best results.
Curing Process
Adhering to the recommended curing process is critical for the adhesive to achieve its complete protective properties. Ensure that the curing environment, such as temperature and humidity, meets the adhesive manufacturer’s specifications. Some adhesives may require post-curing steps to enhance their performance further.
Electronics encapsulation epoxy adhesives are indispensable in modern electronic manufacturing, protecting sensitive components against various environmental hazards. Their properties, such as thermal stability, electrical insulation, chemical resistance, and mechanical strength, make them suitable for diverse applications in consumer electronics, automotive systems, industrial equipment, and medical devices.
Advancements in adhesive technology, including low-temperature cure formulations, enhanced thermal conductivity, and eco-friendly solutions, are expanding the capabilities and applications of encapsulation epoxy adhesives. As industries continue to demand higher performance and reliability from electronic devices, these adhesives will play a pivotal role in meeting those needs.
By understanding the properties, applications, benefits, and challenges of encapsulation epoxy adhesives, manufacturers can make informed decisions to enhance the protection and performance of their electronic products. Embracing best practices in surface preparation, adhesive selection, application, and curing will ensure optimal results and contribute to the longevity and reliability of electronic devices in an ever-evolving technological landscape.
Conclusion
Electronics encapsulation epoxy adhesives play a vital role in protecting and enhancing the performance of electronic devices across various industries. With their excellent thermal stability, electrical insulation, chemical resistance, and mechanical strength, these adhesives provide a reliable barrier against environmental hazards. As technology advances, new formulations and application techniques will further improve the effectiveness and versatility of encapsulation epoxy adhesives, ensuring that electronic devices remain durable, reliable, and high-performing in even the most challenging conditions.
For more about choosing the top electronics encapsulation epoxy adhesive, you can pay a visit to DeepMaterial at https://www.pottingcompound.com/ for more info.
Recent Posts
- How to Select Suitable Potting Materials for PCB According to the Working Environment
- What is PCB Potting
- The Evolution of Smart Watch Assembly Adhesive: A Key Component in Modern Wearable Technology
- Laptop Tablet Assembly Adhesive: The Key to Durable and Reliable Device Construction
- Power Bank Assembly Adhesive: The Essential Component for Building Durable Power Banks
- Smartphone Assembly Adhesive: Enhancing Durability and Precision in Modern Devices
- TV Backplane Support and Reflective Film Bonding: A Comprehensive Guide
- Innovative Use of Compounded Materials in Electronic Device Housings: A Comprehensive Guide
- Enhancing Battery Pack Performance: A Deep Dive into Potting Materials, Benefits, and Applications
- A Comprehensive Guide to Industrial Conformal Coatings: Applications, Types, and Future Trends