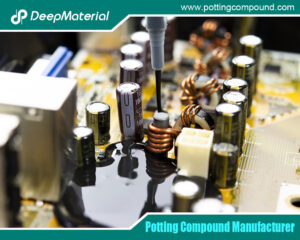
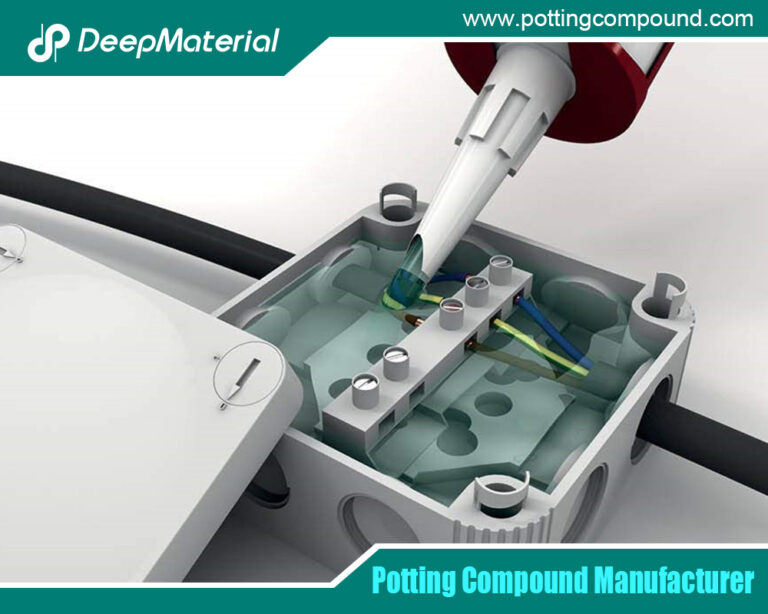
Potting Material for Electronic Components: An In-Depth Guide
- Electronic Potting Material Manufacturer
- August 13, 2024
- Automotive potting material manufacturers, Benefits of Potting Electronics, china electronic potting silicone manufacturer, china electronic potting silicone supplier, circuit board potting, circuit board potting compound, Connector Potting Compound, custom automated electronics potting, customize china electronic potting silicone manufacturer, deepmaterial PCB Potting, deepmaterial potting compound, electrical potting compound, electronic encapsulant potting compounds, electronic epoxy encapsulant potting compounds, Electronic Potting and Encapsulation, electronic potting compound, electronic potting material, Epoxy potting material manufacturers, potting material, potting material for electronic, potting material for electronic components, potting material for electronic compounds, potting material for electronics, potting material manufacturers, Potting Materials for Electronics
Potting Material for Electronic Components: An In-Depth Guide
Electronic components, crucial in virtually every modern device, need protection from environmental factors like moisture, dust, and mechanical shock. One of the most effective ways to safeguard these components is through potting. Potting involves encapsulating electronic assemblies with a protective material that enhances durability and reliability. This article delves into the types of potting materials, their applications, benefits, and considerations for selecting suitable potting materials for electronic components.
Types of Potting Materials
The choice of potting material depends on the specific requirements of the electronic assembly and its operating environment. Here are the primary types of potting materials used in the industry:
- Epoxy Resins:
- Properties: Epoxy resins are known for their excellent adhesion, mechanical strength, and chemical resistance. They cure to form a hard, durable finish.
- Applications: Used extensively in automotive, aerospace, and industrial electronics where durability and thermal stability are crucial.
- Advantages: High thermal conductivity, excellent electrical insulation, and resistance to environmental factors like moisture and chemicals.
- Disadvantages: Once cured, epoxy resins are hard to remove, making rework or repair challenging. They can also be brittle and may not be suitable for components subject to thermal cycling.
- Polyurethane (PU) Resins:
- Properties: PU resins are versatile and can be formulated to be flexible or rigid. They offer good impact resistance and are relatively easy to work with.
- Applications: Commonly used in consumer electronics, automotive, and telecommunications where flexibility and vibration resistance are required.
- Advantages: Flexibility, good adhesion, and moisture resistance. They also cure at lower temperatures compared to epoxies.
- Disadvantages: Generally, they have lower thermal stability and chemical resistance than epoxies.
- Silicone Resins:
- Properties: Silicone resins are highly flexible and have excellent thermal and chemical resistance. They can operate over a wide temperature range.
- Applications: Ideal for high-temperature applications, such as automotive and aerospace industries and components requiring frequent thermal cycling.
- Advantages: Flexibility, excellent thermal stability, and good electrical insulation properties. They are also easy to remove if rework is needed.
- Disadvantages: Generally, it is more expensive than other potting materials and may have longer curing times.
- Acrylic Resins:
- Properties: Acrylics are UV-resistant and can be cured quickly using UV light. They offer good adhesion and flexibility.
- Applications: Used in applications where quick curing is essential, such as LED potting and specific medical devices.
- Advantages: Fast curing, UV stability, and good adhesion. They are also easier to remove compared to epoxies.
- Disadvantages: Lower thermal and chemical resistance compared to epoxies and silicones.
- Polyester Resins:
- Properties: Polyester resins are cost-effective and provide good mechanical properties. However, they are less commonly used in high-performance applications.
- Applications: Often used in less demanding applications where cost is a significant factor.
- Advantages: Cost-effective and good mechanical properties.
- Disadvantages: Lower thermal and chemical resistance can shrink during curing, potentially causing stress on components.
Applications of Potting Materials
Potting materials are used in a variety of applications across different industries. Here are some key areas where they are commonly applied:
- Automotive Electronics:
- Components: Sensors, control units, and lighting systems.
- Requirements: High thermal stability, vibration resistance, and moisture protection.
- Preferred Materials: Epoxies and silicones.
- Aerospace and Defense:
- Components: Avionics, radar systems, and communication equipment.
- Requirements: Extreme temperature resistance, high reliability, and mechanical strength.
- Preferred Materials: Epoxies and silicones.
- Consumer Electronics:
- Components: Mobile phones, tablets, and wearable devices.
- Requirements: Compactness, flexibility, and quick curing times.
- Preferred Materials: Polyurethanes and acrylics.
- Industrial Electronics:
- Components: Power supplies, sensors, and control systems.
- Requirements: Chemical resistance, durability, and thermal management.
- Preferred Materials: Epoxies and polyurethanes.
- Telecommunications:
- Components: Antennas, transceivers, and signal processors.
- Requirements: Environmental protection, electrical insulation, and mechanical stability.
- Preferred Materials: Epoxies and silicones.
Benefits of Potting Electronic Components
Potting offers numerous advantages that enhance the performance and longevity of electronic assemblies:
- Environmental Protection:
- Moisture Resistance: Potting materials create a barrier that prevents moisture ingress, protecting sensitive components from corrosion and electrical shorts.
- Dust and Debris: Encapsulation shields components from dust and particulate matter that can cause malfunctions.
- Mechanical Protection:
- Shock and Vibration: Potting materials absorb and dissipate mechanical energy, protecting components from damage due to shock and vibration.
- Impact Resistance: Encapsulation provides a buffer against impacts, reducing the risk of physical damage.
- Thermal Management:
- Heat Dissipation: Certain potting materials, especially thermally conductive ones, help dissipate heat generated by electronic components, preventing overheating.
- Thermal Stability: Potting materials can withstand wide temperatures, ensuring reliable operation in harsh environments.
- Electrical Insulation:
- Preventing Short Circuits: Potting materials provide excellent electrical insulation, reducing the risk of short circuits and electrical faults.
- Dielectric Strength: The high dielectric strength of potting materials ensures reliable performance in high-voltage applications.
- Chemical Resistance:
- Corrosion Protection: Potting materials protect components from corrosive chemicals and gases, extending their operational life.
- Chemical Stability: They maintain their properties in the presence of various substances, ensuring long-term reliability.
Selecting the Right Potting Material
Choosing the appropriate potting material for electronic components involves considering several factors to meet the specific needs of the application:
- Operating Environment:
- Temperature Range: Select a material that can withstand the operating temperature range of the application.
- Exposure to Chemicals: Consider the presence of chemicals and solvents to which the potting material will be exposed.
- Mechanical Requirements:
- Flexibility vs. Rigidity: Determine if the application requires a flexible or rigid potting material.
- Shock and Vibration: Assess the level of mechanical stress the components will experience.
- Electrical Properties:
- Insulation Requirements: Ensure the material provides adequate electrical insulation for the application.
- Dielectric Strength: Consider the voltage levels to which the potting material will be exposed.
- Curing Process:
- Curing Time: Evaluate the required time and how it fits into manufacturing.
- Curing Conditions: Consider the temperature and humidity conditions needed for curing.
- Rework and Repair:
- Ease of Removal: Determine if the potting material needs removable for rework or repair.
- Repairability: Assess if the material can be easily repaired if damaged.
- Cost Considerations:
- Material Cost: Balance the cost of the potting material with the performance requirements.
- Processing Cost: Consider the cost associated with the potting process, including equipment and labour.
Conclusion
Potting materials protect electronic components from environmental and mechanical stresses, ensuring their reliability and longevity. The choice of potting material depends on the application’s requirements, including operating environment, mechanical and electrical properties, curing process, and cost considerations. By understanding the properties and applications of different potting materials, manufacturers can make informed decisions to enhance the performance and durability of their electronic assemblies. Whether it’s the high thermal stability of epoxies, the flexibility of silicones, or the quick curing of acrylics, selecting the suitable potting material is essential for the success of electronic components in diverse industries.
For more about choosing the Top Potting Material for Electronic Components: An In-Depth Guide, you can pay a visit to DeepMaterial at https://www.pottingcompound.com/ for more info.
Recent Posts
- Potting Compound for PCB
- In – depth Analysis of the Curing Characteristics of Electronic Potting Compounds
- A Comprehensive Analysis of the Environmental Performance of Encapsulating Materials: From Regulations to Practices
- A Comprehensive Analysis of PCB Encapsulation Quality Inspection: Innovative Application of Non-Destructive Testing Technologies
- Analysis of the Improvement of the Seismic and Impact Resistance Performance of PCB by Encapsulation
- A Comprehensive Guide to Evaluating the Reliability of Encapsulation Materials for Encapsulated PCBs
- In-depth Analysis of the Reparability of Encapsulation Materials
- A Comprehensive Analysis of Post-Potting PCB Issues and the Repair and Rework of Potting Materials
- A Comprehensive Analysis of the Compatibility between Encapsulation Materials and PCBs: Exploration of Chemical Reactions and Their Impact on Performance
- How to Ensure the Compatibility between Encapsulation Materials and Various Components on PCBs