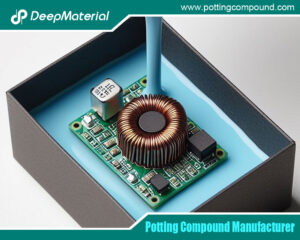
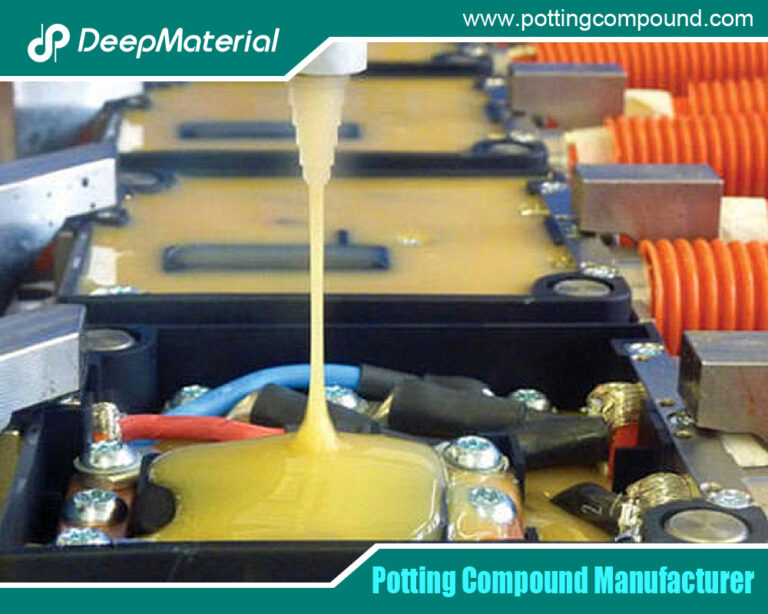
Electronic Potting Compound: A Comprehensive Guide
- Electronic Potting Material Manufacturer
- August 22, 2024
- Automotive potting material manufacturers, Benefits of Potting Electronics, circuit board potting, circuit board potting compound, Connector Potting Compound, custom automated electronics potting, customize china electronic potting silicone factories, customize china electronic potting silicone manufacturer, customize china electronic potting silicone supplier, deepmaterial PCB Potting, deepmaterial potting compound, electrical potting compound, Electronic Encapsulant Potting Compound, electronic encapsulant potting compounds, Electronic Epoxy Encapsulant Potting Compound, electronic epoxy encapsulant potting compounds, Electronic Epoxy Potting Compound, electronic potting compound, Electronic Potting Compounds Manufacturer, electronic potting silicone manufacturer, Encapsulant Potting Compound, Encapsulants and Potting Compounds Suppliers, Epoxy Encapsulant Potting Compound, epoxy potting compound, epoxy potting compound manufacturers, Flexible Potting Compound, potting
Electronic Potting Compound: A Comprehensive Guide
In the rapidly evolving world of electronics, the need for reliable protection of sensitive components has become increasingly important. Electronic potting compounds are one of the most effective methods to safeguard electronic devices from environmental factors, mechanical damage, and electrical insulation. These compounds are materials used to encapsulate electronic components, providing them with a protective layer that enhances their durability and performance. This article will explore the various aspects of electronic potting compounds, including their types, benefits, applications, and selection criteria.
What is an Electronic Potting Compound?
Electronic potting compounds are specialized materials used to encase or encapsulate electronic assemblies, components, and circuits. Their primary function is to protect the electronic parts from environmental factors such as moisture, dust, chemicals, and temperature fluctuations. Potting compounds also offer mechanical protection against shocks, vibrations, and physical damage, ensuring the longevity and reliability of electronic devices.
Potting compounds are typically made from materials like epoxy, polyurethane, silicone, and acrylics. Each type offers distinct properties that make it suitable for specific applications. The compound is applied in a liquid form and then cured to form a solid, protective layer around the electronic components.
Types of Electronic Potting Compounds
- Epoxy Potting Compounds
Epoxy is one of the most widely used materials for potting electronic components. Epoxy potting compounds are known for their excellent mechanical strength, adhesion, and chemical resistance. They provide robust protection against environmental factors and are suitable for various applications. Epoxy compounds can be formulated to be thermally conductive, making them ideal for applications where heat dissipation is crucial.
However, epoxy compounds have limitations, such as limited flexibility and potential for yellowing when exposed to UV light. They are also more challenging to remove if rework or repair is needed.
- Polyurethane Potting Compounds
Polyurethane potting compounds are known for their flexibility and elasticity, making them ideal for applications where components may be subject to movement or vibration. They provide reasonable protection against moisture, chemicals, and abrasion. Polyurethane compounds can also be formulated as flame retardants, making them suitable for safety-critical applications.
One key advantage of polyurethane compounds is their ability to maintain flexibility over a wide range of temperatures. However, they may have lower mechanical strength than epoxy compounds, and their curing time can be longer.
- Silicone Potting Compounds
Silicone potting compounds offer excellent thermal stability and flexibility, making them suitable for extreme temperature resistance applications. They are also highly resistant to moisture, UV light, and chemicals, providing long-term protection for electronic components.
Silicone compounds, such as in automotive and aerospace industries, are often used in applications where thermal cycling is a concern. They have low shrinkage during curing, reducing the stress risk on the encapsulated components. However, silicone compounds are generally more expensive than epoxy and polyurethane compounds.
- Acrylic Potting Compounds
Acrylic potting compounds are known for their quick curing times and ease of use. They offer good protection against moisture and environmental contaminants and are often used in applications requiring rapid production. Acrylic compounds can be formulated to be UV resistant, making them suitable for outdoor applications.
While acrylic compounds offer many advantages, they may provide a different level of mechanical protection than epoxy or silicone compounds. They are also more prone to yellowing when exposed to UV light over time.
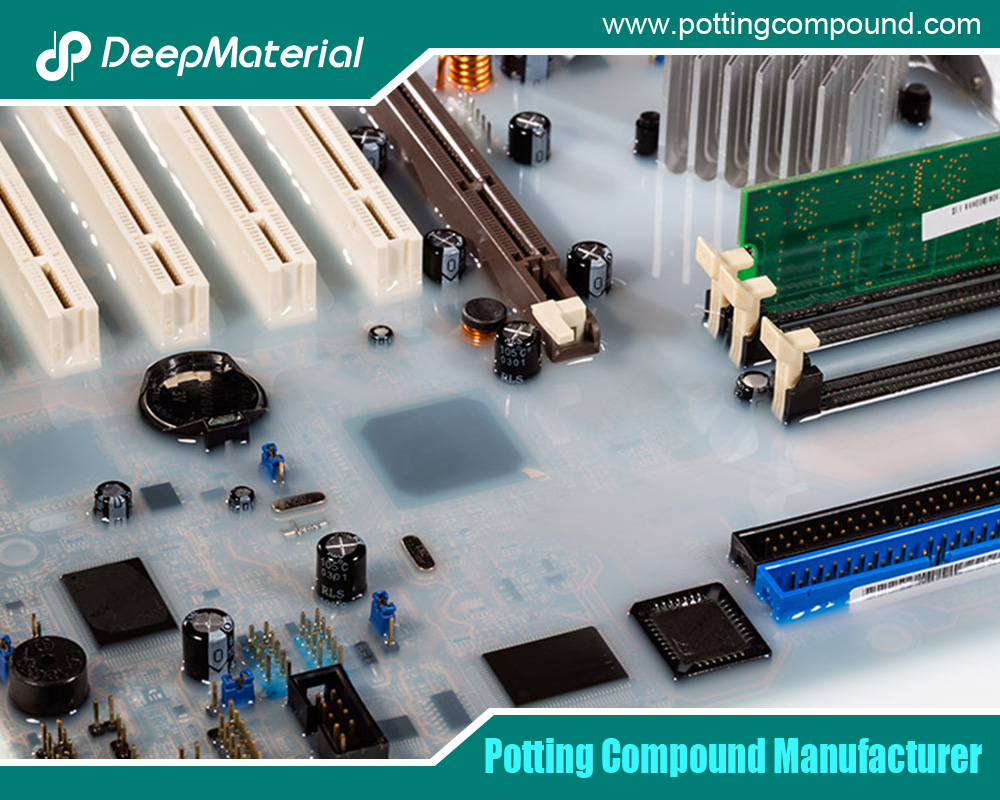
Benefits of Using Electronic Potting Compounds
- Environmental Protection
One of the primary benefits of using electronic potting compounds is their protection against environmental factors. Potting compounds create a barrier that prevents moisture, dust, chemicals, and other contaminants from reaching the sensitive electronic components. This protection is essential for ensuring the longevity and reliability of electronic devices, especially in harsh environments.
- Mechanical Protection
Potting compounds provide mechanical protection by encapsulating the electronic components in a solid, durable layer. This layer helps absorb shocks and vibrations, reducing the risk of physical damage to the components. Mechanical protection is critical in applications where electronic devices are subject to frequent movement or impact.
- Electrical Insulation
Electronic potting compounds also serve as electrical insulators, preventing short circuits and protecting components from electrical interference. Their insulating properties help maintain the integrity of electronic circuits, ensuring that they function correctly and safely.
- Thermal Management
Thermally conductive potting compounds can be used in applications where heat dissipation is crucial. These compounds help dissipate heat away from the electronic components, preventing overheating and ensuring optimal performance. Effective thermal management is essential for maintaining the reliability and efficiency of electronic devices.
- Enhanced Durability
Potting compounds enhance the durability of devices by providing a protective layer around the electronic components. This increased durability is paramount in automotive, aerospace, and industrial equipment industries, where electronic components are exposed to harsh conditions.
- Improved Aesthetics
Potting compounds can also improve the aesthetics of electronic devices by covering unsightly wires and components. The smooth, solid finish the potting compound provides can give the device a clean and professional appearance.
Applications of Electronic Potting Compounds
- Automotive Industry
The automotive industry is one of the largest users of electronic potting compounds. Modern vehicles have various electronic components, including sensors, control units, and lighting systems. These components must be protected from harsh environmental conditions, such as temperature fluctuations, moisture, and vibrations. Potting compounds encapsulate and protect these critical components, ensuring their reliable performance over the vehicle’s life.
- Aerospace Industry
Electronic components in the aerospace industry are exposed to extreme temperatures, high altitudes, and intense vibrations. Potting compounds protect avionics, sensors, and control systems from these harsh conditions. Silicone potting compounds’ lightweight and flexible properties make them particularly suitable for aerospace applications.
- Consumer Electronics
Potting compounds are widely used in consumer electronics to protect sensitive components from moisture, dust, and mechanical damage. Products such as smartphones, tablets, and wearable devices often use potting compounds to enhance their durability and reliability. Potting compounds also help improve devices’ water resistance, making them more suitable for everyday use.
- Industrial Equipment
Industrial equipment often operates in challenging environments where exposure to chemicals, moisture, and extreme temperatures is expected. Potting compounds protect electronic control systems, sensors, and power supplies in industrial equipment. The protection provided by potting compounds helps extend the life of the equipment and reduces the risk of failure.
- Medical Devices
Medical devices often require high reliability and protection, especially in critical applications. Potting compounds are used to encapsulate electronic components in medical devices such as pacemakers, imaging equipment, and diagnostic tools. This ensures these devices can operate safely and effectively, even in demanding conditions.
- Renewable Energy Systems
Renewable energy systems like solar panels and wind turbines use electronic components to convert and manage energy. These components are often exposed to harsh environmental conditions, including UV light, moisture, and temperature fluctuations. Potting compounds protect these components, ensuring renewable energy systems’ long-term performance and reliability.
Selection Criteria for Electronic Potting Compounds
Choosing the suitable electronic potting compound for a specific application requires careful consideration of several factors:
- Environmental Conditions
The environmental conditions in which the electronic components will operate play a crucial role in selecting the appropriate potting compound. Factors such as temperature range, exposure to moisture, chemicals, and UV light should be considered when choosing a potting compound.
- Thermal Conductivity
Selecting a potting compound with high thermal conductivity is essential for applications where heat dissipation is critical. Thermally conductive potting compounds help prevent overheating and ensure the efficient operation of electronic components.
- Mechanical Strength
The potting compound’s mechanical strength is essential for applications where the components may be subject to shocks, vibrations, or physical impact. Epoxy and polyurethane compounds are known for their excellent mechanical properties, making them suitable for demanding applications.
- Flexibility
Flexibility is essential, especially in applications where the electronic components may experience movement or thermal expansion. Silicone and polyurethane compounds offer excellent flexibility, making them ideal for applications with dynamic conditions.
- Curing Time
The curing time of the potting compound can impact the production process. Acrylic compounds offer quick curing times, making them suitable for applications where rapid production is required. However, other compounds like epoxy may need longer curing times, which should be considered in manufacturing.
- Reworkability
In some applications, removing or reworking the potting compound is essential. While epoxy compounds offer excellent protection, they are challenging to remove once cured. Depending on the specific formulation, silicone and acrylic compounds offer better reworkability.
- Cost
The cost of the potting compound is an important consideration, especially in large-scale production. While silicone compounds may offer superior properties, they are generally more expensive than epoxy or polyurethane compounds. Balancing cost with performance is essential when selecting a potting compound.
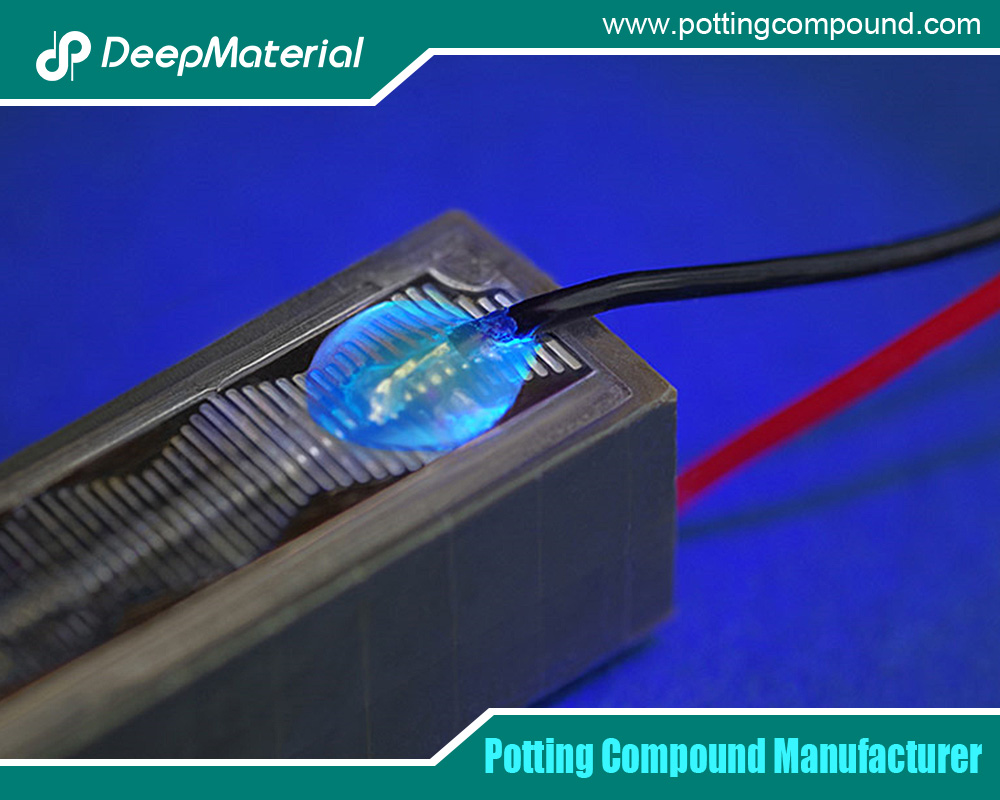
Conclusion
Electronic potting compounds play a vital role in protecting and enhancing the performance of electronic components in a wide range of applications. From the automotive and aerospace industries to consumer electronics and medical devices, potting compounds protect against environmental factors, mechanical damage, and electrical interference. By carefully selecting the appropriate potting compound based on factors such as environmental conditions, thermal conductivity, and mechanical strength, manufacturers can ensure their electronic products’ long-term reliability and durability.
For more about choosing the top electronic potting compound: a comprehensive guide, you can pay a visit to DeepMaterial at https://www.pottingcompound.com/ for more info.
Recent Posts
- Potting Compound vs. Epoxy: A Comprehensive Comparison
- Potting Compound for PCB
- In – depth Analysis of the Curing Characteristics of Electronic Potting Compounds
- A Comprehensive Analysis of the Environmental Performance of Encapsulating Materials: From Regulations to Practices
- A Comprehensive Analysis of PCB Encapsulation Quality Inspection: Innovative Application of Non-Destructive Testing Technologies
- Analysis of the Improvement of the Seismic and Impact Resistance Performance of PCB by Encapsulation
- A Comprehensive Guide to Evaluating the Reliability of Encapsulation Materials for Encapsulated PCBs
- In-depth Analysis of the Reparability of Encapsulation Materials
- A Comprehensive Analysis of Post-Potting PCB Issues and the Repair and Rework of Potting Materials
- A Comprehensive Analysis of the Compatibility between Encapsulation Materials and PCBs: Exploration of Chemical Reactions and Their Impact on Performance