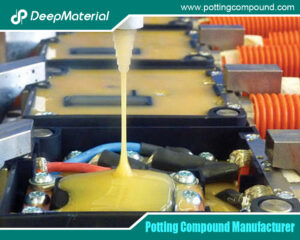
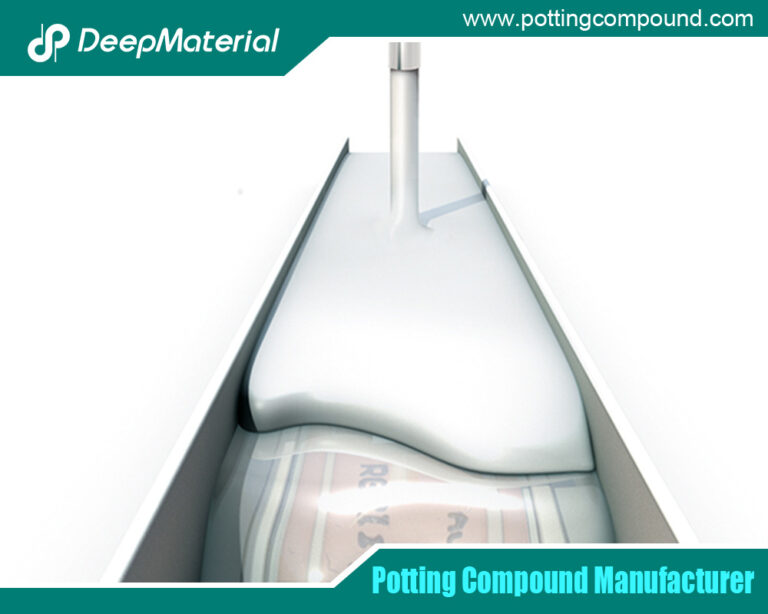
Electronic Epoxy Encapsulant Potting Compounds: A Comprehensive Guide
- Electronic Potting Material Manufacturer
- September 18, 2024
- conformal coating manufacturers, conformal coating pcb, conformal coating silicone, conformal coating waterproof, Connector Potting Compound, Electronic Epoxy Encapsulant Potting Compound, Electronic Epoxy Potting Compound, Electronic Potting and Encapsulation, electronic potting compound, electronic potting material, electronic potting silicone manufacturer, Encapsulant Potting Compound, Epoxy Encapsulant Potting Compound, epoxy potting compound, Flexible Potting Compound, LED Potting Compound, pcb conformal coating, PCB Potting Compound, polyurethane potting compound, potting compound, Silicone Potting Compound, silicone potting compound for electronics, uv potting compound, Waterproof Conformal Coating, waterproof potting compound
Electronic Epoxy Encapsulant Potting Compounds: A Comprehensive Guide
In the ever-evolving world of electronics, ensuring the reliability and durability of components is paramount. One essential method to achieve this is using electronic epoxy encapsulant potting compounds. These compounds protect sensitive electronic components from environmental factors such as moisture, chemicals, and physical damage. This article delves into the intricacies of electronic epoxy encapsulant potting compounds, exploring their types, applications, benefits, and critical considerations.
1. Understanding Electronic Epoxy Encapsulant Potting Compounds
Electronic epoxy encapsulant potting compounds are a protective material used to encase and secure electronic components within a device. Potting involves filling an electronic assembly or component with a solid or gelatinous compound, which then hardens to form a robust protective layer. The primary purpose of this process is to safeguard the electronics from environmental hazards, enhance mechanical stability, and improve the device’s overall performance.
Epoxy-based potting compounds are among the most widely used materials for this purpose. Epoxy resins are favored due to their excellent adhesive properties, chemical resistance, and ability to form a strong bond with a wide range of substrates. Once cured, epoxy potting compounds offer a rigid and durable encapsulation that shields electronics from external factors.
1.1 Types of Epoxy Potting Compounds
Electronic epoxy encapsulant potting compounds come in various formulations, each tailored to specific applications and requirements. The most common types include:
- One-Part Epoxy Compounds:These compounds are pre-mixed and ready to use, requiring no additional mixing before application. They typically cure at room temperature or with heat. One-part epoxies are convenient and easy to use, making them suitable for applications requiring quick processing.
- Two-Part Epoxy Compounds:These compounds, which consist of two components—resin and hardener—require mixing before application. The chemical reaction between the resin and hardener initiates the curing process. Two-part epoxies offer greater flexibility in formulation and are often used in applications requiring specific curing times and properties.
- Thermally Conductive Epoxy Compounds:These specialized epoxy formulations are designed to dissipate heat generated by electronic components. Thermally conductive epoxies contain fillers, such as aluminum oxide or boron nitride, which enhance their ability to transfer heat away from sensitive components.
- UV-Curable Epoxy Compounds:These compounds cure upon exposure to ultraviolet (UV) light, allowing for rapid processing. UV-curable epoxies are ideal for applications where speed and precision are critical, such as in manufacturing small electronic devices.
2. Applications of Epoxy Encapsulant Potting Compounds
Electronic epoxy encapsulant potting compounds find widespread use across various industries due to their versatility and protective properties. Some of the critical applications include:
2.1 Automotive Electronics
In the automotive industry, electronic components are exposed to harsh conditions, including extreme temperatures, vibration, and exposure to chemicals. Epoxy potting compounds protect engine control units (ECUs), sensors, and other electronic modules from these adverse conditions. The encapsulation ensures that the components remain operational and reliable, even in challenging environments.
2.2 Aerospace and Defense
Aerospace and defense applications demand the highest levels of reliability and durability. Epoxy potting compounds protect avionics, communication systems, and other critical electronics in aircraft and defense equipment. These compounds resist temperature fluctuations, moisture, and mechanical stress, ensuring the continued functionality of the components in mission-critical situations.
2.3 Consumer Electronics
Miniaturization and reliability are vital considerations in consumer electronics. Epoxy encapsulants protect delicate components in smartphones, laptops, wearable devices, and other consumer gadgets. The encapsulation prevents moisture ingress, which can lead to corrosion and electrical failure, extending the devices’ lifespan.
2.4 Industrial Equipment
Industrial equipment often operates in environments where dust, chemicals, and mechanical stress are exposed dailyy. Epoxy potting compounds protect machinery and control systems’ sensors, controllers, and other electronic components. The encapsulation ensures that the electronics remain functional and resistant to environmental factors, reducing the likelihood of downtime and maintenance costs.
2.5 Renewable Energy Systems
Electronic components in renewable energy systems, such as solar panels and wind turbines, are subjected to varying weather conditions and environmental stressors. Epoxy potting compounds protect these systems’ inverters, controllers, and critical electronics. The encapsulation ensures the longevity and efficiency of the components, contributing to the overall reliability of the renewable energy infrastructure.
3. Benefits of Using Epoxy Encapsulant Potting Compounds
The use of electronic epoxy encapsulant potting compounds offers several benefits, making them a preferred choice for protecting electronic components:
3.1 Environmental Protection
One of the primary benefits of epoxy potting compounds is their ability to protect electronics from environmental factors, such as moisture, dust, chemicals, and temperature fluctuations. The encapsulation creates a barrier that prevents the ingress of contaminants, reducing the risk of corrosion and electrical failures.
3.2 Enhanced Mechanical Stability
Epoxy potting compounds provide mechanical support to electronic components, reducing the likelihood of damage due to vibration, shock, or mechanical stress. This is particularly important in applications where the electronics are subjected to constant movement or impact.
3.3 Improved Electrical Insulation
Epoxy resins offer excellent electrical insulation properties, preventing short circuits and electrical interference between components. This is especially critical in densely packed electronic assemblies, where the risk of electrical interference is higher.
3.4 Thermal Management
Thermally conductive epoxy potting compounds help dissipate heat generated by electronic components, preventing overheating and ensuring the longevity of the devices. Effective thermal management is crucial in applications involving high power densities, such as power electronics and LED lighting.
3.5 Customizable Properties
Epoxy potting compounds can be formulated to meet specific requirements, such as varying curing times, flexibility, and thermal conductivity. This flexibility in formulation allows manufacturers to tailor the encapsulant to the application’s particular needs, ensuring optimal performance.
4. Key Considerations When Selecting Epoxy Encapsulant Potting Compounds
Choosing the suitable epoxy encapsulant potting compound for a specific application requires careful consideration of several factors. These include:
4.1 Application Requirements
The first step in selecting an epoxy potting compound is to assess the application’s specific requirements. Consider factors such as the operating environment, temperature range, chemical exposure, and mechanical stress. Understanding these requirements will help narrow the options and select a compound that meets the necessary criteria.
4.2 Thermal Management Needs
Selecting a thermally conductive epoxy compound is essential for applications where heat dissipation is critical. Consider the compound’s thermal conductivity and whether it can effectively transfer heat away from the components. The operating temperature range must also be evaluated to ensure the compound remains stable under the expected conditions.
4.3 Cure Time and Processing
The curing time of the epoxy potting compound can significantly impact the manufacturing process. Some applications may require fast-curing compounds for quick turnaround times, while others may benefit from slower curing times to allow for adjustments during assembly. Consider the processing requirements and select a compound that aligns with the production timeline.
4.4 Mechanical Properties
Evaluate the epoxy compound’s mechanical properties, such as hardness, flexibility, and adhesion. The compound should protect against mechanical stress and vibration while maintaining a solid bond with the substrate. Additionally, consider whether the compound needs to remain flexible or if a rigid encapsulation is preferred.
4.5 Chemical Resistance
In applications where chemical exposure is a concern, selecting an epoxy compound with high chemical resistance is crucial. The compound should withstand contact with solvents, oils, and other chemicals without degrading or losing its protective properties.
4.6 Electrical Insulation
Electrical insulation is a key consideration for electronic applications. Ensure the epoxy compound offers sufficient dielectric strength to prevent electrical breakdown and short circuits. Additionally, evaluate the compound’s ability to resist moisture, which can compromise insulation properties.
4.7 Environmental Impact
Consider the epoxy potting compound’s environmental impact, especially its long-term stability and potential for outgassing. Some applications may require low-VOC (volatile organic compound) formulations to minimize environmental and health risks.
5. Challenges and Future Trends in Epoxy Potting Compounds
While epoxy encapsulant potting compounds offer numerous benefits, they also present specific challenges. These challenges include:
5.1 Shrinkage During Curing
Epoxy compounds can undergo shrinkage during curing, which may lead to internal stresses and potential damage to the encapsulated components. To mitigate this, manufacturers must carefully control the curing process and select formulations with minimal shrinkage.
5.2 Moisture Sensitivity
Some epoxy compounds may be sensitive to moisture during the curing process, leading to incomplete curing or reduced performance. Manufacturers must ensure proper storage and handling of the compounds to minimize moisture exposure.
5.3 Compatibility with Substrates
The adhesion of epoxy potting compounds to various substrates can vary depending on the formulation and surface preparation. Ensuring the epoxy and substrate compatibility is critical for achieving a solid and durable bond.
5.4 Future Trends
The field of epoxy potting compounds is continuously evolving, with ongoing research and development focused on enhancing their properties and expanding their applications. Some of the emerging trends in this field include:
- Nano-Enhanced Epoxy Compounds:Incorporating nanoparticles into epoxy formulations can improve their mechanical, thermal, and electrical properties. Nano-enhanced epoxies are being explored for use in advanced electronics and high-performance applications.
- Biodegradable and Eco-Friendly Formulations:With increasing environmental concerns, there is a growing demand for biodegradable epoxy potting compounds that have reduced environmental impact. Research is being conducted to develop eco-friendly formulations that offer the same level of protection as traditional epoxies.
- Innovative Epoxy Compounds:Smart materials that can respond to environmental changes, such as temperature or stress, are integrated into epoxy formulations. These smart epoxies have the potential to provide real-time monitoring and self-healing capabilities in electronic devices.
Conclusion
Electronic epoxy encapsulant potting compounds are essential in ensuring electronic components’ reliability, durability, and performance across various industries. Their ability to protect against environmental factors, enhance mechanical stability, and provide electrical insulation makes them a critical component in the manufacturing of electronic devices. As technology advances, the development of innovative epoxy formulations will further expand their applications, meeting the evolving demands of modern electronics. By understanding the types, applications, benefits, and considerations associated with epoxy potting compounds, manufacturers can make informed decisions to optimize the protection and longevity of their electronic products.
For more about choosing the Top Electronic Epoxy Encapsulant Potting Compounds: A Comprehensive Guide, you can pay a visit to DeepMaterial at https://www.pottingcompound.com/ for more info.
Recent Posts
- How to Select Suitable Potting Materials for PCB According to the Working Environment
- What is PCB Potting
- The Evolution of Smart Watch Assembly Adhesive: A Key Component in Modern Wearable Technology
- Laptop Tablet Assembly Adhesive: The Key to Durable and Reliable Device Construction
- Power Bank Assembly Adhesive: The Essential Component for Building Durable Power Banks
- Smartphone Assembly Adhesive: Enhancing Durability and Precision in Modern Devices
- TV Backplane Support and Reflective Film Bonding: A Comprehensive Guide
- Innovative Use of Compounded Materials in Electronic Device Housings: A Comprehensive Guide
- Enhancing Battery Pack Performance: A Deep Dive into Potting Materials, Benefits, and Applications
- A Comprehensive Guide to Industrial Conformal Coatings: Applications, Types, and Future Trends