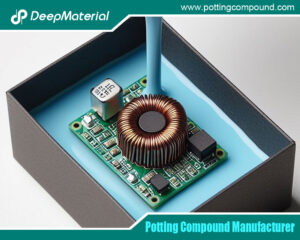
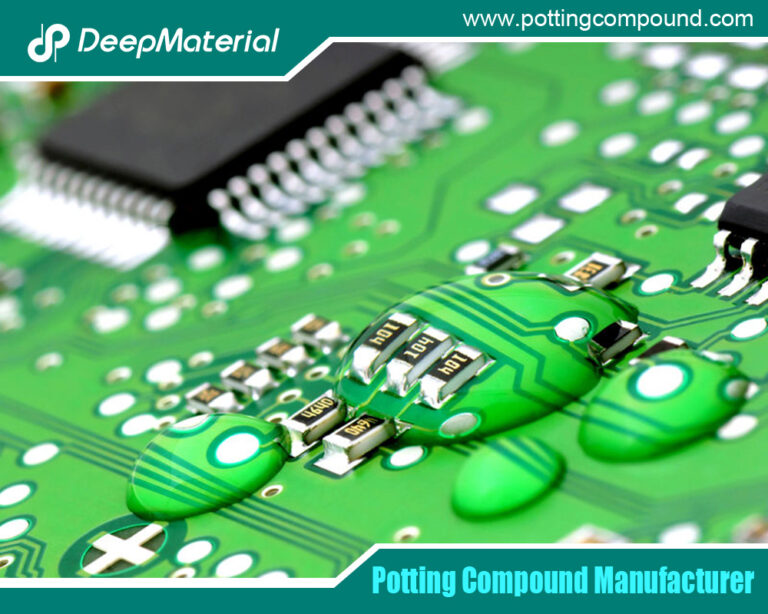
A Brief Overview on Epoxies in Electronics: Properties, Applications, and Modifications
- Electronic Potting Material Manufacturer
- September 30, 2024
- Acrylic Conformal Coating, Electronic Conformal Coating, Electronic Epoxy Potting Compound, Epoxies in Electronics, epoxy conformal coating, epoxy potting compound, epoxy potting compound manufacturer, epoxy potting compound manufacturers, Epoxy potting material manufacturers, epoxy resin manufacturers, epoy electronic adhesive, Industrial Conformal Coating, LED Potting Compound, Non Conductive Adhesive Glue, Non Conductive Epoxy, Non-conductive epoxy resin, Non-conductive epoxy resin manufacturers, pcb conformal coating, PCB Potting Compound, polyurethane potting compound, Silicone Conformal Coating, Silicone Potting Compound, Urethane Conformal Coating, UV Cure Conformal Coating, uv epoxy electronic adhesive glue, Waterproof Conformal Coating, waterproof potting compound
A Brief Overview on Epoxies in Electronics: Properties, Applications, and Modifications
In electronics, choosing materials is crucial to ensuring device reliability and performance. One such material that has gained prominence is epoxy resin, particularly non-conductive epoxy resin. This resin type is essential for protecting electronic components and ensuring their longevity. This article will delve into the properties, applications, and modifications of non-conductive epoxy resin, shedding light on its role in the electronics industry. We will explore how non-conductive epoxy resin manufacturers contribute to the field, the various types of epoxy resins, and their specific uses in electronic devices.
What is Non-Conductive Epoxy Resin?
When searching for a non-conductive epoxy resin manufacturer, it’s crucial to understand the key characteristics and benefits of non-conductive epoxy resin. This specialized synthetic polymer is designed to provide robust electrical insulation, making it a preferred choice for various electronic applications where protection from electrical currents is paramount. Unlike conductive epoxies, non-conductive resins do not permit electrical flow, ensuring that sensitive electronic components are shielded from potential short circuits.
Here’s a closer look at the essential properties of non-conductive epoxy resin:
- Insulation: These resins are renowned for their excellent electrical insulation capabilities. They effectively prevent the passage of electrical current, critical for safeguarding electronic circuits and components.
- Thermal Stability: Non-conductive epoxy resins maintain stability and performance even under fluctuating temperature conditions. This thermal resilience ensures that the epoxy protects electronic components effectively, regardless of the environment.
- Mechanical Strength: One of the standout features of non-conductive epoxy resins is their high mechanical strength. This property enhances the durability of electronic components by providing robust structural support and resistance to physical stress.
- Chemical Resistance:These resins are also known for their resistance to various chemicals and solvents. This chemical resistance protects electronic components from environmental damage and ensures long-term reliability.
Applications of Non-Conductive Epoxy Resin in Electronics
Non-conductive epoxy resin is a critical material in electronics. It plays several crucial roles in ensuring the reliability and longevity of electronic devices. As a versatile substance, it finds extensive application across different facets of electronics, providing both protection and performance enhancement.
Circuit Board Protection
- Encapsulation:Non-conductive epoxy resin is frequently used to encapsulate circuit boards. This process shields the boards from environmental threats such as moisture, dust, and mechanical damage, enhancing their durability and operational reliability.
- Potting: Another critical application is potting, where the resin fills cavities around electronic components. It protects these components from thermal and mechanical stresses and extends their lifespan.
Component Adhesive
- Mounting:In the assembly of electronic devices, non-conductive epoxy resin serves as an effective adhesive for mounting electronic components onto circuit boards. Its strong bonding properties ensure that components remain securely attached.
- Bonding: The resin is also used to bond various parts of electronic assemblies. This creates a stable and reliable connection between different components, which is essential for the device’s proper functioning.
Insulation Coating
- Coating: Non-conductive epoxy resin provides an excellent coating for wires and other electronic components. This coating prevents electrical shorts and reduces interference, which is crucial for maintaining the performance and safety of electronic circuits.
- Layering: Additionally, the resin is used to apply additional insulation layers in multi-layered electronic devices. This extra layer of protection enhances the overall insulation and helps avoid potential electrical issues.
Modifications and Enhancements
As a leading non-conductive epoxy resin manufacturer, our commitment extends beyond essential production to encompass a range of modifications and enhancements that elevate the performance and versatility of our products. Here’s how we advance our epoxy resin formulations:
- Improving Thermal Conductivity: We integrate thermal conductive fillers such as aluminum oxide or silicon carbide into our epoxy resin to boost heat dissipation while maintaining electrical insulation. This careful balance ensures enhanced thermal management without sacrificing non-conductivity.
- Enhancing Mechanical Properties: Our epoxy resins are fortified with reinforcements like glass or carbon fibers, which significantly bolsters their mechanical strength and flexibility. These reinforcements create a resin that can withstand more significant stress and strain, making it ideal for demanding applications.
- Customizing Curing Conditions: We offer tailored curing processes to meet specific needs. By adjusting curing temperatures, we fine-tune the mechanical and thermal properties of the resin. Additionally, the inclusion of curing accelerators helps to shorten curing times, which in turn boosts production efficiency and output rates.
- Environmental Resistance: Our formulations are designed with longevity in mind. We incorporate UV stabilizers to protect the resin from degradation caused by ultraviolet exposure and enhance water resistance to guard against moisture damage. It ensures that our epoxy resins maintain their integrity and performance in diverse environmental conditions.
The Role of Non-Conductive Epoxy Resin Manufacturers
Non-conductive epoxy resin manufacturers play a crucial role in the electronics industry by ensuring the reliability and effectiveness of their products. These manufacturers are responsible for several vital functions that enhance the performance and applicability of epoxy resins in various electronic applications.
Quality Assurance:
- Standards Compliance: Manufacturers adhere to strict industry standards to guarantee that their epoxy resins meet high-quality benchmarks and perform reliably in their intended applications.
- Testing and Certification: Rigorous testing processes are employed to certify that the resins are suitable for diverse electronic uses and meet all necessary performance criteria.
Innovation and Development:
- Research and Development: Continuous R&D efforts are dedicated to creating new resin formulations and refining existing ones, aiming to push the boundaries of performance and application.
- Customization: Manufacturers often offer customized solutions tailored to various electronic applications’ specific needs, allowing for enhanced adaptability and functionality.
Supply Chain Management:
- Distribution: Efficient supply chain management is crucial for timely delivery, ensuring that high-quality resins reach manufacturers and end-users without delays.
- Support: Technical support is provided to clients, assisting with applications and handling challenges, enhancing the overall user experience and satisfaction.
Conclusion
Non-conductive epoxy resins play a pivotal role in the electronics industry, offering critical protection and enhancing the performance of electronic components. These resins are indispensable in modern electronics, from safeguarding circuit boards to improving mechanical properties and environmental resistance. Non-conductive epoxy resin manufacturers contribute significantly by ensuring high quality, driving innovation, and supporting the industry’s needs. As electronics continue to evolve, the advancements in epoxy resin technology will undoubtedly keep pace, further solidifying the importance of this material in the realm of electronics.
For more about choosing a brief overview on epoxies in electronics: properties, applications, and modifications, you can pay a visit to DeepMaterial at https://www.pottingcompound.com/ for more info.
Recent Posts
- Potting Compound vs. Epoxy: A Comprehensive Comparison
- Potting Compound for PCB
- In – depth Analysis of the Curing Characteristics of Electronic Potting Compounds
- A Comprehensive Analysis of the Environmental Performance of Encapsulating Materials: From Regulations to Practices
- A Comprehensive Analysis of PCB Encapsulation Quality Inspection: Innovative Application of Non-Destructive Testing Technologies
- Analysis of the Improvement of the Seismic and Impact Resistance Performance of PCB by Encapsulation
- A Comprehensive Guide to Evaluating the Reliability of Encapsulation Materials for Encapsulated PCBs
- In-depth Analysis of the Reparability of Encapsulation Materials
- A Comprehensive Analysis of Post-Potting PCB Issues and the Repair and Rework of Potting Materials
- A Comprehensive Analysis of the Compatibility between Encapsulation Materials and PCBs: Exploration of Chemical Reactions and Their Impact on Performance