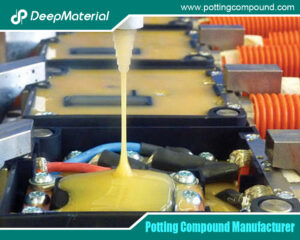
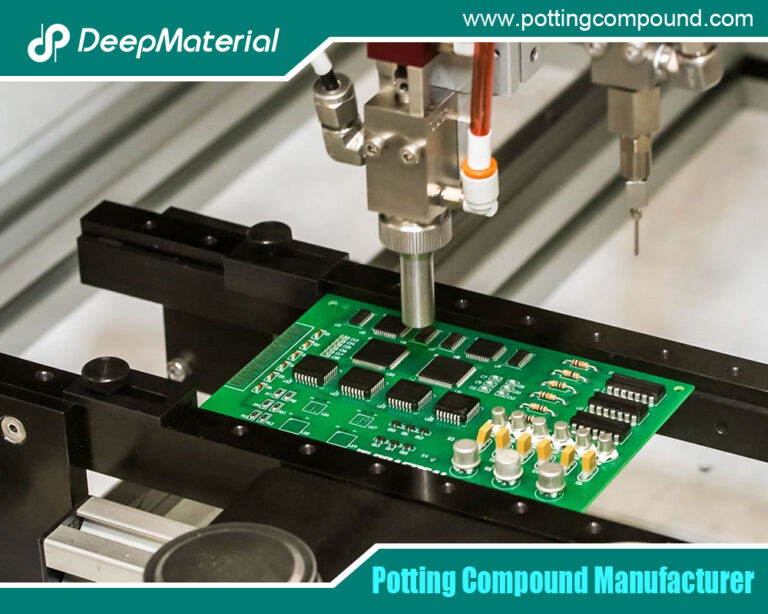
Potting Materials for the Electronics Market: A Comprehensive Overview
- Electronic Potting Material Manufacturer
- October 11, 2024
- Automotive potting material manufacturers, Benefits of Potting Electronics, china electronic potting silicone manufacturer, china electronic potting silicone supplier, circuit board potting, circuit board potting compound, Connector Potting Compound, custom automated electronics potting, customize china electronic potting silicone factories, customize china electronic potting silicone manufacturer, customize china electronic potting silicone supplier, deepmaterial PCB Potting, deepmaterial potting compound, electrical potting compound, Electronic Encapsulant Potting Compound, Electronic Epoxy Encapsulant Potting Compound, Electronic Epoxy Potting Compound, electronic potting material, electronic potting material manufacturer, Epoxy potting material manufacturers, potting material, potting material for components, potting material for electronic, potting material for electronic components, potting material for electronic compounds, potting material for electronics, potting material manufacturer, Potting Materials for Electronics, Potting Materials for the Electronic, Potting Materials for the Electronics Market
Potting Materials for the Electronics Market: A Comprehensive Overview
The rapid advancement of technology has led to the proliferation of electronic devices across multiple sectors, including automotive, aerospace, telecommunications, and consumer electronics. As these devices become more complex and compact, adequate protection solutions have become increasingly important. Potting materials protect sensitive electronic components from moisture, dust, vibrations, and thermal fluctuations. By understanding the different types of potting materials available in the market, manufacturers can make informed decisions that enhance the reliability and performance of their products.
Understanding Potting
Potting is a process used to encase electronic components in a protective material. This method provides several benefits, including:
- Environmental Protection: Shields components from moisture, dust, and contaminants.
- Mechanical Stability:Provides structural support, reducing the risk of damage from vibrations and impacts.
- Thermal Management:Aids in heat dissipation, preventing overheating.
- Electrical Insulation: Prevents short circuits and enhances safety.
The choice of potting material is essential in achieving these benefits, as different materials offer varying properties suited to specific applications.
Types of Potting Materials
Potting materials can be broadly categorized into several types based on their chemical composition and properties. The most commonly used potting materials in the electronics market include:
Epoxy Resins
Epoxy resins are among the most widely used potting materials due to their excellent mechanical properties and chemical resistance.
Key Characteristics:
- Durability:High strength and toughness.
- Adhesion:Strong adhesion to a variety of substrates.
- Chemical Resistance:Resistant to many solvents, acids, and bases.
Applications:
- Used for potting circuit boards, connectors, and sensors.
- Ideal for applications requiring high-temperature resistance and mechanical stability.
Polyurethane
Polyurethane potting materials offer flexibility and resilience, making them suitable for various applications.
Key Characteristics:
- Flexibility:Provides a degree of flexibility, which is beneficial in applications subject to mechanical stress.
- Moisture Resistance:Excellent barrier against moisture and environmental factors.
- Thermal Stability:Good thermal performance across a range of temperatures.
Applications:
- It is commonly used in automotive electronics, lighting applications, and consumer electronics.
- Suitable for potting sensitive components exposed to vibrations.
Silicone
Silicone potting materials are known for their outstanding temperature resistance and flexibility.
Key Characteristics:
- High-Temperature Resistance:Effective in extreme temperatures ranging from -60°C to +200°C.
- Electrical Insulation:Excellent electrical insulation properties.
- UV Resistance:Resistant to ultraviolet (UV) light and weathering.
Applications:
- Frequently used in outdoor electronics, automotive components, and medical devices.
- It is ideal for applications requiring thermal cycling resistance.
Thermoplastic Elastomers (TPE)
Thermoplastic elastomers combine the properties of rubber and plastic, making them versatile potting materials.
Key Characteristics:
- Reworkability:Can be melted and reshaped, allowing for easy rework of components.
- Elasticity:Offers excellent elasticity and flexibility.
- Impact Resistance: Good resistance to mechanical impacts.
Applications:
- Used in consumer electronics, automotive applications, and industrial devices.
- Suitable for potting components that may require repairs or modifications.
Polyimides
Polyimide materials provide excellent thermal stability and chemical resistance.
Key Characteristics:
- High Thermal Resistance:Capable of withstanding high temperatures without degradation.
- Chemical Resistance:Resistant to various chemicals and solvents.
- Dimensional Stability:Maintains its properties under extreme conditions.
Applications:
- Often used in aerospace, automotive, and high-performance electronics.
- Suitable for potting applications requiring high thermal stability.
Selection Criteria for Potting Materials
Choosing the suitable potting material for electronic components involves considering several factors, including:
Environmental Conditions
- Temperature:Assess the operating temperature range of the application.
- Moisture:Consider exposure to humidity and water.
Mechanical Stress
- Vibration and Shock:Determine if the components will be subjected to vibrations or impacts.
- Flexibility Requirements:Consider whether flexibility is needed to accommodate movement.
Electrical Properties
- Dielectric Strength:Ensure the potting material provides adequate electrical insulation.
- Thermal Conductivity:Evaluate the material’s ability to dissipate heat.
Chemical Resistance
- Exposure to Chemicals:Identify any chemicals or solvents the potting material may encounter.
Curing Time and Process
- Cure Method:Consider whether the material requires heat or is self-curing.
- Processing Time:Evaluate the curing time required for production schedules.
Cost Considerations
- Budget Constraints:Balance performance requirements with budget constraints when selecting potting materials.
Advantages of Potting Materials in Electronics
Potting materials offer numerous benefits that contribute to the reliability and longevity of electronic components:
Enhanced Durability
- Potting materials provide robust protection against environmental factors, increasing the lifespan of electronic components.
Improved Reliability
- Potting materials enhance the reliability of electronic devices by preventing moisture ingress and mechanical damage.
Better Thermal Management
- Effective heat dissipation through potting materials helps prevent overheating, which can lead to component failure.
Increased Safety
- Electrical insulation properties reduce the risk of short circuits and other safety hazards, ensuring user safety.
Versatility
- Potting materials can be tailored to meet specific application needs, making them suitable for various industries.
Challenges in Potting Materials
While potting materials offer significant advantages, there are also challenges that manufacturers may encounter:
Adhesion Issues
- Poor adhesion between the potting material and the substrate can lead to delamination and failure. Proper surface preparation is essential to achieve optimal adhesion.
Curing Conditions
- Some potting materials require specific curing conditions (e.g., temperature and humidity) to achieve desired properties. Inconsistent curing can affect performance.
VOC Emissions
- Many potting materials release volatile organic compounds (VOCs) during curing, raising environmental and health concerns. Selecting low-VOC options can mitigate this issue.
Cost Implications
- High-performance potting materials can be expensive, which may impact overall production costs. Manufacturers need to balance performance and cost-effectiveness.
Limited Reworkability
- Some potting materials, particularly rigid epoxies, may be complex to remove for rework. This limitation can pose challenges when repairs are needed.
Innovations in Potting Materials
The electronics market continually evolves, leading to innovations in potting materials that enhance performance and address existing challenges:
Low-Temperature Cure Epoxies
- New formulations allow for low-temperature curing, reducing energy costs and improving compatibility with heat-sensitive components.
Eco-Friendly Materials
- Increased focus on sustainability has led to developing eco-friendly potting materials with low VOC emissions and biodegradable properties.
Conductive Potting Materials
- Conductive potting materials are being developed for applications requiring electromagnetic interference (EMI) shielding, combining protection with signal integrity.
Smart Potting Materials
- Innovations in innovative materials enable monitoring environmental conditions, offering real-time feedback on component performance.
Potting vs. Encapsulation: Key Differences
While potting and encapsulation serve similar purposes, there are critical differences between the two processes:
Potting
- Definition:Enclosing components in a solid or gel-like material.
- Characteristics:Typically, a permanent seal provides excellent mechanical support and environmental protection.
- Applications are idealfor components that require complete moisture, dust, and mechanical stress protection.
Encapsulation
- Definition:Coating involves applying or surrounding components with a protective layer.
- Characteristics:This may allow for flexibility and reworkability, making it suitable for applications requiring access to accessible components.
- Applications:These materials are often used in sensitive medical devices, telecommunications, and consumer electronics components.
Best Practices for Potting in Electronics
To achieve optimal results in potting applications, consider the following best practices:
Surface Preparation
- Thoroughly clean and prepare surfaces to ensure good adhesion between the potting material and the component.
Material Testing
- Conduct compatibility tests on potting materials with substrates to ensure optimal performance.
Controlled Environment
- Carry out potting processes in a controlled environment to minimize the risk of contaminants affecting the final product.
Accurate Mixing
- Follow manufacturer guidelines for mixing potting compounds to achieve desired properties and performance.
Quality Assurance
- Regularly inspect finished products to ensure compliance with quality standards and identify potential defects early.
Conclusion
Potting materials enhance electronic components’ durability, reliability, and performance across various industries. With a diverse range of materials available, manufacturers can select the most suitable options based on their specific application requirements. Understanding different potting materials’ characteristics, advantages, and challenges is essential for making informed decisions in the electronics market. As technology advances and new materials emerge, the importance of potting in safeguarding electronic devices will continue to grow, ensuring that they remain reliable and effective in meeting the demands of an ever-evolving landscape. By adopting best practices and staying informed about innovations in potting materials, manufacturers can enhance their products’ longevity and performance, benefiting consumers and industries.
For more about choosing the Top Potting Materials for the Electronics Market: A Comprehensive Overview, you can pay a visit to DeepMaterial at https://www.pottingcompound.com/ for more info.
Recent Posts
- How to Select Suitable Potting Materials for PCB According to the Working Environment
- What is PCB Potting
- The Evolution of Smart Watch Assembly Adhesive: A Key Component in Modern Wearable Technology
- Laptop Tablet Assembly Adhesive: The Key to Durable and Reliable Device Construction
- Power Bank Assembly Adhesive: The Essential Component for Building Durable Power Banks
- Smartphone Assembly Adhesive: Enhancing Durability and Precision in Modern Devices
- TV Backplane Support and Reflective Film Bonding: A Comprehensive Guide
- Innovative Use of Compounded Materials in Electronic Device Housings: A Comprehensive Guide
- Enhancing Battery Pack Performance: A Deep Dive into Potting Materials, Benefits, and Applications
- A Comprehensive Guide to Industrial Conformal Coatings: Applications, Types, and Future Trends