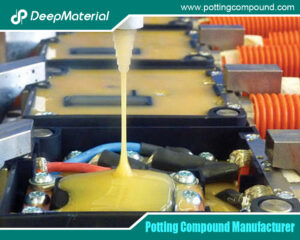
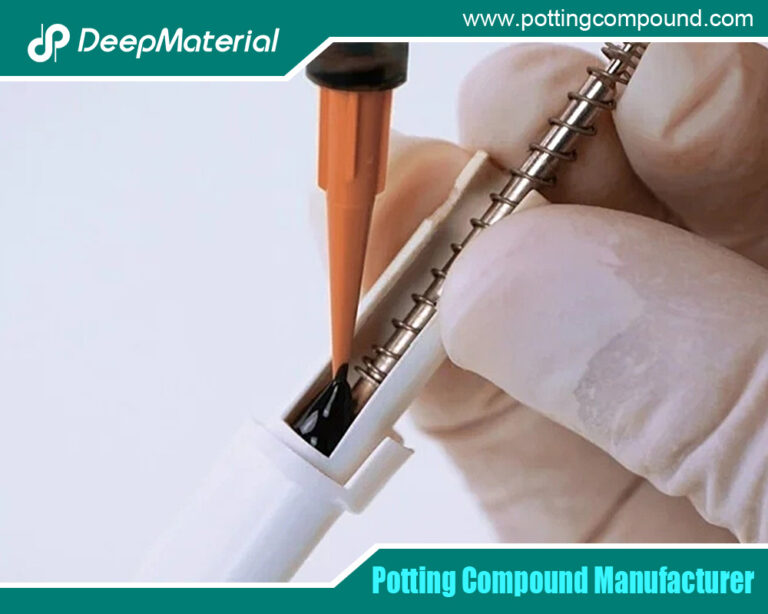
The Comprehensive Guide to Electronics Encapsulation Epoxy Adhesive
- Electronic Potting Material Manufacturer
- November 4, 2024
- Acrylic Conformal Coating, adhesive glue manufacturer, Connector Potting Compound, deepmaterial conformal coating, deepmaterial epoxy adhesive glue, deepmaterial PCB Potting, deepmaterial potting compound, Electronic Conformal Coating, electronic potting compound, electronics encapsulation epoxy adhesive, electronics encapsulation epoxy adhesive China hotsale, electronics encapsulation epoxy adhesive factory OEM, electronics encapsulation epoxy adhesive glue, electronics encapsulation epoxy adhesive glue hotsale, electronics encapsulation epoxy adhesive manufacturer hotsale, electronics encapsulation epoxy adhesive supplier wholesale, Flexible Potting Compound, industrial adhesive suppliers, Industrial Conformal Coating, LED Potting Compound, pcb conformal coating, PCB Potting Compound, polyurethane potting compound, Silicone Potting Compound, Urethane Conformal Coating, UV Cure Conformal Coating, UV Cure Potting Compound, Waterproof Conformal Coating, waterproof potting compound
The Comprehensive Guide to Electronics Encapsulation Epoxy Adhesive
In today’s fast-paced technological world, the reliability and durability of electronic components are more critical than ever. As devices become smaller and more complex, the need for adequate protection against environmental factors and mechanical stress has surged. One of the most effective solutions for this challenge is electronics encapsulation epoxy adhesive. This specialized adhesive bonds components together and provides a robust protective barrier against moisture, dust, chemicals, and mechanical damage. This comprehensive guide will explore what electronics encapsulation epoxy adhesives are, their composition, advantages, applications, and critical considerations for selection and use.
What is Electronics Encapsulation Epoxy Adhesive?
Electronics encapsulation epoxy adhesive is a resin-based adhesive specifically formulated to provide strong bonding and protection for electronic components. Unlike traditional adhesives, encapsulation epoxy adhesives create a robust encapsulating layer around electronic parts, safeguarding them from external environmental threats.
Critical Characteristics of Encapsulation Epoxy
- Resin Matrix:The resin matrix serves as the foundation of the adhesive, providing bonding properties and structural integrity.
- Curing Agent (Hardener): This crucial component initiates the chemical reaction that hardens the epoxy.
- Fillers and Additives: These enhance specific properties such as thermal conductivity, flame retardance, and electrical insulation.
- Colorants:Colorants improve visibility or enhance the product’s aesthetic appeal.
Types of Encapsulation Epoxy Adhesives
- Thermal Conductive Epoxies: Designed for applications requiring heat dissipation.
- Low-Viscosity Epoxies:Ideal for intricate designs and complex geometries where flowability is crucial.
- Flame Retardant Epoxies: Provides enhanced safety in applications exposed to high heat or fire hazards.
Advantages of Electronics Encapsulation Epoxy Adhesive
Electronics encapsulation epoxy adhesives offer a wide range of benefits that make them an ideal choice for protecting electronic components:
Exceptional Durability
- High Resistance:These adhesives resist temperature fluctuations, humidity, and chemicals, ensuring long-term reliability.
- Mechanical Strength:It provides structural integrity to assemblies, enhancing their resistance to vibration, shock, and other mechanical stresses.
Electrical Insulation
- Prevents Short Circuits: The adhesive creates an insulating barrier that protects sensitive components from electrical interference and shorts.
- High Dielectric Strength: Suitable for high-voltage applications due to their ability to withstand electrical stress.
Thermal Stability
- Wide Temperature Range:Maintains performance in extreme temperatures, making them suitable for diverse environments.
- Thermal Conductivity:Certain formulations enhance heat dissipation, protecting sensitive components from overheating.
Moisture and Chemical Resistance
- Waterproofing:This creates a moisture barrier that protects against corrosion and deterioration.
- Chemical Resistance:Effective in environments exposed to solvents, oils, and other harsh substances.
Applications of Electronics Encapsulation Epoxy Adhesive
Electronics encapsulation epoxy adhesives are utilized across various industries with specific needs and requirements. Here are some typical applications:
PCB Encapsulation
- Protection from Contaminants:Encapsulating printed circuit boards (PCBs) to shield them from moisture, dust, and other environmental threats.
- Thermal Management: Using thermal conductive epoxies to improve heat dissipation in high-performance applications.
Potting of Components
- Encapsulating Sensitive Components:Protecting components like sensors, transistors, and integrated circuits from external stresses.
- Improving Reliability: Enhancing the performance and lifespan of electronic devices in harsh environments.
Sealing and Bonding
- Assembly of Electronic Devices:The assembly of electronic devices involves using adhesives to bond and seal components in smartphones, tablets, and other consumer electronics.
- Creating Robust Connections:Ensures mechanical stability and electrical insulation in electronic assemblies.
Automotive Electronics
- Protection of Modules:Module protection involves encapsulating sensitive electronic components in vehicles to shield them from extreme temperatures and vibrations.
- Enhancing Safety:Ensures reliable operation of critical safety systems like airbag sensors and stability control modules.
Aerospace Applications
- Reliability in Avionics:Protecting electronic systems subjected to rigorous environmental stresses, including temperature extremes and radiation.
- Weight Reduction:Utilizing lightweight epoxy formulations that contribute to overall weight savings in aerospace designs.
Key Features to Consider When Selecting Electronics Encapsulation Epoxy Adhesive
Choosing the suitable electronics encapsulation epoxy adhesive requires careful consideration of various features that align with your specific application requirements:
Cure Time
- Fast-Curing Options:Suitable for high-throughput production environments.
- Longer Working Times:Ideal for complex assemblies requiring more aliment and adjustment time.
Viscosity
- Low Viscosity: Facilitates more accessible application in intricate designs and tight spaces.
- High Viscosity:Better for applications requiring thicker adhesive layers for structural integrity.
Thermal Conductivity
- Heat Dissipation:Essential for applications where managing heat is critical for component performance.
- Thermal Resistance:Consider how the adhesive performs at high temperatures and whether it meets your operational requirements.
Electrical Properties
- Dielectric Strength:Ensure the adhesive can withstand the electrical demands of your components.
- Insulating Properties:Insulating properties prevent electrical shorts and ensure long-term reliability.
Chemical Resistance
- Environmental Exposure:Assess whether the adhesive will be exposed to solvents, oils, or other harsh chemicals.
- Durability in Harsh Conditions:Consider the specific environment where the electronic assembly will operate.
How to Choose the Right Electronics Encapsulation Epoxy Adhesive
Selecting the suitable epoxy adhesive involves a systematic approach to assess various factors that affect performance:
Understand Your Application
- Environmental Conditions:Identify the environmental factors your electronics will face, such as temperature extremes, moisture, and chemical exposure.
- Performance Requirements:Define the specific performance metrics your application must meet, including Strength, flexibility, and curing Time.
Timeonsult Manufacturer Specifications
- Technical Data Sheets:Review the specifications and performance characteristics the manufacturer provides.
- Material Compatibility:Ensure compatibility between the adhesive and the materials you will be bonding.
Conduct Testing
- Prototype Testing:If feasible, conduct small-scale tests to evaluate the adhesive’s performance in your specific application.
- Comparative Analysis:Test multiple adhesives to determine which performs best under your conditions.
Seek Expert Advice
- Consult Adhesive Manufacturers:Contact manufacturers or application engineers for recommendations tailored to your project.
- Industry Standards: Stay informed about industry standards and certifications relevant to your application.
Tips for Effective Application of Electronics Encapsulation Epoxy Adhesive
To ensure optimal performance and adhesion, follow these tips during the application process:
Surface Preparation
- Clean Surfaces:Remove grease, dirt, and moisture from the surfaces to enhance adhesion.
- Roughen Surfaces:Consider lightly sanding or roughening smooth surfaces for better bonding.
Proper Mixing
- Follow Instructions:Adhere to the manufacturer’s guidelines for mixing the resin and hardener.
- Thoroughly Blend:Ensure a complete mix to prevent issues during curing.
Application Method
- Choose the Right Method:Depending on your assembly, select manual dispensing, syringe application, or automated systems.
- Control Dispensing:Use precision dispensing tools to apply the adhesive accurately.
Curing Conditions
- Monitor Environmental Conditions:Monitor temperature and humidity during curing to ensure complete and adequate bonding.
- Avoid Disturbances:Do not disturb the assembly until the adhesive has fully cured.
Post-Application Care
- Inspect for Voids:Check for any air bubbles or voids that could compromise the bond.
- Conduct Testing:Perform functional tests on the assembly to ensure reliability before full-scale production.
Conclusion
Electronics encapsulation epoxy adhesives are essential for ensuring the durability and reliability of electronic components in an increasingly complex and demanding technological landscape. Their unique properties and advantages make them invaluable for various consumer electronics, automotive, and aerospace applications. By understanding the characteristics, benefits, and considerations for selecting suitable adhesives, manufacturers, and engineers can enhance the performance and longevity of their electronic devices.
For more about choosing the top comprehensive guide to electronics encapsulation epoxy adhesive, you can pay a visit to DeepMaterial at https://www.pottingcompound.com/ for more info.
Recent Posts
- How to Select Suitable Potting Materials for PCB According to the Working Environment
- What is PCB Potting
- The Evolution of Smart Watch Assembly Adhesive: A Key Component in Modern Wearable Technology
- Laptop Tablet Assembly Adhesive: The Key to Durable and Reliable Device Construction
- Power Bank Assembly Adhesive: The Essential Component for Building Durable Power Banks
- Smartphone Assembly Adhesive: Enhancing Durability and Precision in Modern Devices
- TV Backplane Support and Reflective Film Bonding: A Comprehensive Guide
- Innovative Use of Compounded Materials in Electronic Device Housings: A Comprehensive Guide
- Enhancing Battery Pack Performance: A Deep Dive into Potting Materials, Benefits, and Applications
- A Comprehensive Guide to Industrial Conformal Coatings: Applications, Types, and Future Trends