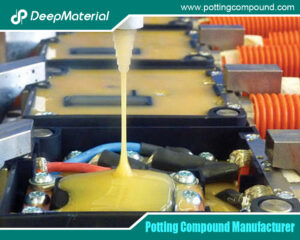
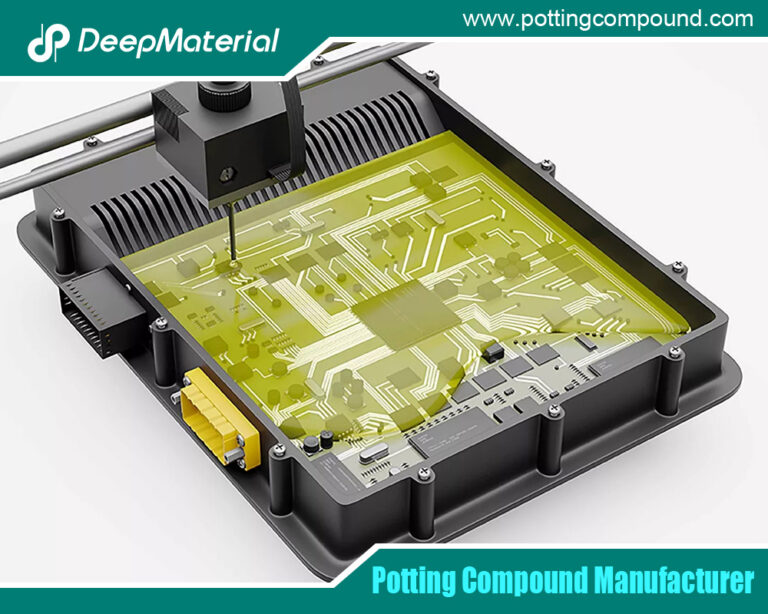
Comprehensive Guide to Conformal Coatings for Electronics Applications: Enhancing Durability and Performance
- Electronic Potting Material Manufacturer
- November 8, 2024
- Acrylic Conformal Coating, conformal coatings for electronics, Electronic Conformal Coating, epoxy conformal coating, Epoxy Conformal Coating china OEM, epoxy potting compound, Industrial Conformal Coating, pcb conformal coating, PCB Potting Compound, polyurethane potting compound, Remove term: conformal coatings for electronics conformal coatings for electronic china OEM, Remove term: conformal coatings for electronics conformal coatings for electronic factory hotsale, Remove term: conformal coatings for electronics conformal coatings for electronic factory OEM, Remove term: conformal coatings for electronics conformal coatings for electronic manufacturer wholesale, Remove term: conformal coatings for electronics conformal coatings for electronic supplier hotsale, Remove term: conformal coatings for electronics conformal coatings for electronic wholesale, Silicone Conformal Coating, Silicone Potting Compound, Urethane Conformal Coating, UV Cure Conformal Coating, Waterproof Conformal Coating, waterproof potting compound
Comprehensive Guide to Conformal Coatings for Electronics Applications: Enhancing Durability and Performance
The demand for durable, reliable, high-performance devices continues growing in the rapidly evolving electronics landscape. With the proliferation of smaller, more complex components, ensuring the longevity and functionality of these devices is paramount. One of the most effective ways to protect sensitive electronic components from environmental hazards is by applying conformal coatings.
Conformal coatings are protective layers that conform to the surface of circuit boards and components, shielding them from moisture, dust, chemicals, and temperature fluctuations. This blog post will explore the various types of conformal coatings, their benefits, application methods, selection criteria, and industry applications, providing a comprehensive overview for manufacturers and engineers looking to enhance their electronics.
What are Conformal Coatings?
Conformal coatings are thin protective films applied to printed circuit boards (PCBs) and electronic components to safeguard against environmental factors. These coatings are designed to conform to the contours of the substrate, providing a barrier that does not interfere with the device’s electronic performance.
Benefits of Conformal Coatings
Conformal coatings offer numerous advantages for electronic applications:
- Environmental Protection:They guard against moisture, dust, chemicals, and extreme temperatures, preventing corrosion and electrical failures.
- Increased Reliability:By enhancing the durability of components, conformal coatings reduce the likelihood of device malfunctions and extend operational life.
- Thermal Management:Some coatings offer thermal insulation, helping to dissipate heat and maintain optimal operating conditions for sensitive components.
- Mechanical Protection:They reduce the impact of vibrations and shocks, protecting delicate electronic parts from physical damage.
- Cost Efficiency:Investing in conformal coatings can prevent costly repairs or replacements by prolonging the lifespan of electronic devices.
Types of Conformal Coatings
Acrylic Coatings
- Characteristics:Fast-drying, easy to apply, and removable.
- Applications:Common in consumer electronics and automotive components.
- Advantages:Good moisture resistance and excellent clarity.
Polyurethane Coatings
- Characteristics:Durable, chemical-resistant, and provides good abrasion resistance.
- Applications:Ideal for industrial equipment and outdoor devices.
- Advantages:Exceptional moisture and chemical resistance, suitable for harsh environments.
Silicone Coatings
- Characteristics:Flexible and capable of withstanding extreme temperatures.
- Applications:Used in aerospace, automotive, and high-temperature electronics.
- Advantages:Great thermal stability and excellent electrical insulation properties.
Epoxy Coatings
- Characteristics:Hard and rigid finish, offering excellent mechanical protection.
- Applications:Heavy-duty industrial applications and high-stress environments.
- Advantages:Strong adhesion and exceptional chemical resistance.
Parylene Coatings
- Characteristics:Vacuum-deposited, providing uniform coverage.
- Applications:Medical devices and sensitive electronics.
- Advantages:High dielectric strength, conformability, and moisture resistance.
Application Methods for Conformal Coatings
The method chosen for applying conformal coatings can significantly affect their performance and effectiveness. Here are the primary application methods:
Spraying
- Process:Coating material is atomized and sprayed onto the substrate.
- Suitability:Ideal for large surfaces and complex geometries.
- Advantages:Allows for controlled thickness and even coverage.
Dipping
- Process:Components are immersed in a tank of liquid coating material.
- Suitability:Suitable for small batches and simple geometries.
- Advantages:Ensures uniform coverage but may require excess coating removal.
Brushing
- Process:Coating is applied using a brush or roller.
- Suitability:Useful for touch-ups or small components.
- Advantages:Provides precise control over application but can result in uneven thickness.
Selective Coating
- Process:Automated systems only apply coating to specific circuit board areas.
- Suitability:Ideal for complex PCBs where only specific components require protection.
- Advantages:Minimizes material usage and reduces risk to unprotected areas.
Vacuum Deposition (for Parylene)
- Process:Parylene is deposited in a vacuum chamber, creating a thin, uniform layer.
- Suitability:Best for sensitive applications requiring thorough coverage.
- Advantages:Provides the most uniform coating with excellent barrier properties.
Key Considerations When Selecting a Conformal Coating
When choosing a conformal coating for your electronics application, consider the following factors:
Environmental Conditions
- Assess the operating environment: humidity, temperature extremes, chemical exposure, and potential for physical shock.
Component Sensitivity
- Evaluate the sensitivity of the components being coated. Some coatings are more suitable for high-density applications, while others are better for rugged use.
Adhesion and Compatibility
- Ensure the conformal coating has good adhesion to the substrate material and is compatible with other materials used in the assembly.
Thickness and Coverage
- Determine the required coating thickness. Some applications may need thicker coatings for added protection, while others require thinner layers to avoid affecting functionality.
Regulatory Compliance
- Ensure the coating complies with industry standards and regulations, particularly in sectors like automotive, aerospace, and medical devices.
Industry Applications of Conformal Coatings
Conformal coatings are used across various industries, each with unique requirements and challenges:
Consumer Electronics
- Applications:Smartphones, laptops, and wearables.
- Requirements:Moisture and dust protection, durability, and lightweight materials.
Automotive
- Applications:Control units, sensors, and power electronics.
- Requirements:Chemical resistance, temperature stability, and mechanical protection.
Aerospace and Defense
- Applications:Avionics, radar systems, and satellite components.
- Requirements:High reliability, thermal stability, and resistance to harsh environmental conditions.
Medical Devices
- Applications:Implantable devices, diagnostic equipment, and surgical instruments.
- Requirements:Biocompatibility, moisture resistance, and protection against contaminants.
Industrial Electronics
- Applications:Automation equipment, robotics, and heavy machinery.
- Requirements:Chemical and mechanical resistance, durability, and performance under extreme conditions.
Challenges in Using Conformal Coatings
While conformal coatings offer numerous benefits, some challenges may arise during their application and use:
Application Complexity
- Specific methods, such as spraying or selective coating, may require specialized equipment and expertise, increasing the complexity of the application process.
Curing Time
- Depending on the coating type, curing times can vary significantly. Extended curing periods may delay production schedules.
Thickness Control
- Achieving a consistent desired thickness can be challenging, particularly in complex geometries where some areas may receive more coating than others.
Surface Preparation
- Proper surface preparation is critical for ensuring adhesion. Any contaminants on the surface can lead to coating failures.
Cost Considerations
- The initial investment in conformal coating materials and application equipment can be significant. Manufacturers must weigh these costs against the long-term benefits.
Future Trends in Conformal Coatings
The field of conformal coatings is evolving rapidly, with several trends emerging that may shape the future of this technology:
Advancements in Materials
- Developing new coating formulations, such as bio-based materials and nano coatings, may enhance performance while reducing environmental impact.
Increased Automation
- Automation in the application process can improve consistency, reduce labor costs, and minimize human error, leading to more reliable coatings.
Smart Coatings
- Integrating intelligent coatings that can change properties in response to environmental conditions (e.g., moisture levels) is an exciting area of research and development.
Sustainability Initiatives
- As manufacturers prioritize sustainability, there will be a push towards eco-friendly coating materials and processes that reduce waste and energy consumption.
Conclusion
Conformal coatings enhance the durability and performance of electronic devices in various applications. By protecting against environmental hazards, these coatings contribute to the reliability and longevity of sensitive electronic components. Understanding the different types of conformal coatings, their benefits, application methods, and critical considerations is crucial for manufacturers and engineers looking to optimize their products.
For more about comprehensive guide to conformal coatings for electronics applications: enhancing durability and performance, you can pay a visit to DeepMaterial at https://www.pottingcompound.com/ for more info.
Recent Posts
- How to Select Suitable Potting Materials for PCB According to the Working Environment
- What is PCB Potting
- The Evolution of Smart Watch Assembly Adhesive: A Key Component in Modern Wearable Technology
- Laptop Tablet Assembly Adhesive: The Key to Durable and Reliable Device Construction
- Power Bank Assembly Adhesive: The Essential Component for Building Durable Power Banks
- Smartphone Assembly Adhesive: Enhancing Durability and Precision in Modern Devices
- TV Backplane Support and Reflective Film Bonding: A Comprehensive Guide
- Innovative Use of Compounded Materials in Electronic Device Housings: A Comprehensive Guide
- Enhancing Battery Pack Performance: A Deep Dive into Potting Materials, Benefits, and Applications
- A Comprehensive Guide to Industrial Conformal Coatings: Applications, Types, and Future Trends