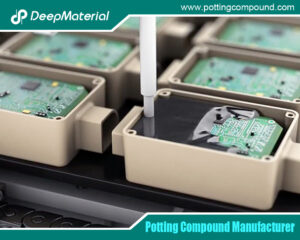
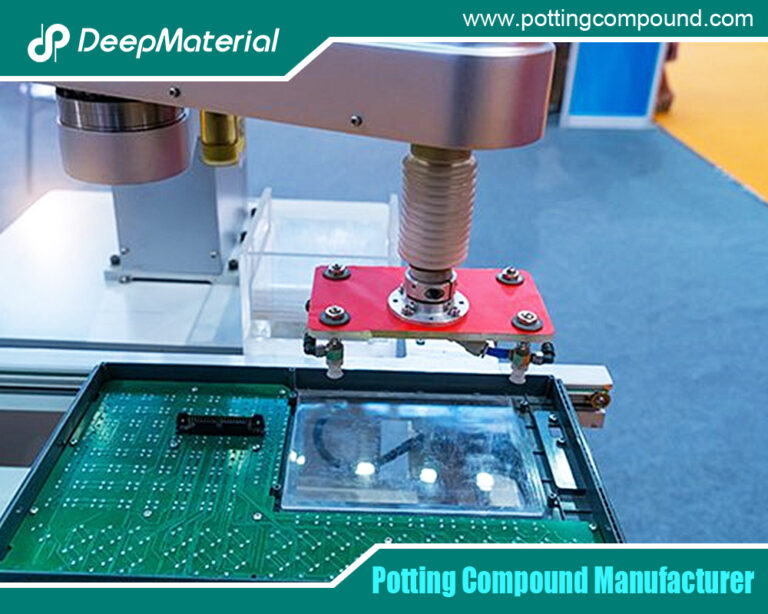
The Potting Manufacturing Process: A Comprehensive Guide to Protecting and Enhancing Component Durability
- Electronic Potting Material Manufacturer
- November 13, 2024
- conformal coating for electronics, conformal coating for pcb, conformal coating for pcb standards, conformal coating material, conformal coating pcb, conformal coating process, conformal coating silicone, conformal coating spray, conformal coating waterproof, electrical potting compound, epoxy potting compound, polyurethane potting compound, potting compound for electronics, potting compound for pcb, potting compound vs epoxy, Potting Manufacturing Process, Potting Manufacturing Process China Hotsale, Potting Manufacturing Process China OEM, Potting Manufacturing Process China Wholesale, Potting Manufacturing Process Factory Hotsale, Potting Manufacturing Process Factory OEM, Potting Manufacturing Process Factory Wholesale, Potting Manufacturing Process Manufacturer, Potting Manufacturing Process Supplier, silicone potting compound for electronics, thermal potting compound, UV curing potting compound, waterproof potting compound
The Potting Manufacturing Process: A Comprehensive Guide to Protecting and Enhancing Component Durability
Reliability and durability are paramount in various industries—electronics, automotive, aerospace, and medical devices. The potting manufacturing process offers an effective solution to protect sensitive components from environmental factors like moisture, vibrations, and temperature extremes. Potting involves encasing components with specialized compounds, often in a shell or mold, providing a protective shield that enhances durability and performance. This article provides an in-depth overview of each stage of the potting process, explores different potting compounds, discusses their benefits, and highlights best practices to achieve optimal results.
Understanding the Potting Manufacturing Process
Potting is a method of protecting and insulating components by encapsulating them with a specific material, known as a potting compound. This process creates a barrier that serves multiple functions:
- Environmental Protection: Shields components from moisture, dust, and other harmful elements.
- Shock and Vibration Resistance: Provides stability, reducing the risk of damage from physical shocks or vibrations.
- Thermal Management: Helps disperse heat, allowing components to withstand high temperatures.
- Electrical Insulation: Reduces the risk of electrical interference and short circuits.
The potting process is standard in electronics but extends to any industry where safeguarding component integrity is crucial.
Types of Potting Compounds
The choice of potting material is critical as each type has unique properties suited to specific applications. Here are some commonly used potting compounds:
- Epoxy Resin:Known for its strong adhesive properties, high resistance to temperature, and durability. Epoxy is ideal for industrial settings but lacks flexibility, making it more prone to cracking under mechanical stress.
- Polyurethane Resin: A flexible compound offering good moisture resistance and suitable for low-power electronics or applications where some movement is expected. Polyurethane performs well in environments with moderate temperature fluctuations.
- Silicone Resin: Offers excellent heat resistance and flexibility, making it a preferred choice for applications exposed to extreme temperatures. Silicone is commonly used in the automotive and aerospace industries.
- Acrylic Resin: Known for fast curing times and UV resistance, acrylic is ideal for outdoor or UV-exposed applications. However, it has moderate durability and thermal resistance compared to other materials.
Step-by-Step Guide to the Potting Manufacturing Process
Each step in the potting process requires careful attention to detail to ensure that the protective material provides comprehensive coverage and adheres effectively. Here’s a step-by-step breakdown:
Step 1: Preparation of Materials
- Selecting the Potting Compound: Choose a potting material based on the component’s requirements and the environmental conditions it will face.
- Mixing the Compound: Many compounds come as two-part formulas that require precise mixing to achieve a uniform consistency. Proper mixing ensures that the compound cures evenly and provides consistent protection.
Step 2: Component Preparation
- Cleaning the Components: Dust, grease, or other contaminants can interfere with adhesion, so components should be thoroughly cleaned.
- Surface Pre-treatment (if required): Certain materials, like metals, may need pre-treatment or a primer to enhance bonding with the potting compound.
- Fixture or Mold Preparation:If the component needs to be held in a specific orientation during potting, prepare a fixture or mold to keep it in place.
Step 3: Application of the Potting Compound
- Pouring the Compound: Slowly pour or inject the potting compound around and over the component. Ensuring even distribution and controlling the flow helps prevent air bubbles or gaps.
- Controlling the Flow and Filling Depth:Ensure the potting compound covers all critical areas without overflowing or exposing parts of the component.
- Anti-Bubble Techniques: Employ methods like vacuum potting or slow pouring to reduce air bubbles that could compromise the potting material’s effectiveness.
Step 4: Curing Process
- Determining the Right Curing Environment:Most potting compounds cure at room temperature, but some may require elevated temperatures. Epoxy, for example, often cures faster under controlled heat.
- Monitoring Curing Time and Temperature: Too much heat or prolonged curing time may cause cracking or shrinkage in the potting compound.
- Post-Curing Inspection: After curing, examine the component for defects, such as cracks, voids, or incomplete coverage.
Step 5: Quality Control and Finishing
- Inspection for Defects: Ensure the potting material has cured properly without cracks, air pockets, or uneven coverage.
- Trimming Excess Material: Any excess material can be cut for a clean finish, especially in high-precision applications.
- Packaging and Final Assembly: After finishing, components can proceed to packaging or assembly for final product integration.
Benefits of Potting in Component Manufacturing
Potting offers several advantages that enhance the performance and longevity of components, especially in demanding environments. Key benefits include:
- Durability Enhancement: Potting compounds’ encapsulation significantly improves component resistance to external factors, reducing the risk of environmental damage.
- Performance Reliability: Potting ensures stable and reliable performance by isolating components from electrical interference and managing thermal conditions.
- Extended Component Lifespan: Potting reduces stress and wear from moisture, mechanical shock, and temperature fluctuations, leading to longer-lasting components.
- Safety and Compliance Assurance:Potting compounds help prevent electrical malfunctions, contributing to safer operation and compliance with industry standards.
- Cost Efficiency in Maintenance:Potting reduces the need for frequent repairs or replacements, ultimately lowering maintenance costs.
Critical Factors for Successful Potting
Achieving optimal results in potting requires adherence to best practices and consideration of several critical factors:
- Material Compatibility:Ensure that the potting compound chosen aligns with the component’s specific needs, such as heat resistance or flexibility.
- Thorough Cleaning:Contaminants can interfere with bonding, so components should be cleaned before potting.
- Curing Conditions:Preach precise curing times and temperatures to prevent shrinkage or cracking.
- Anti-Bubble Techniques:Employ degassing or vacuum potting to avoid air bubbles in the material.
- Application Technique: Control the flow and fill depth to ensure even and complete component coverage.
Common Challenges in the Potting Manufacturing Process
Despite its many benefits, potting can present challenges, particularly in high-volume or complex applications. Some common issues include:
- Air Bubbles and Voids:Improper mixing or pouring can introduce air pockets, compromising protection. Degassing or vacuum potting can mitigate this.
- Inconsistent Curing: Variations in temperature or humidity can lead to uneven curing, resulting in cracks or insufficient bonding.
- Overfilling or Underfilling: Incorrect amounts of potting material may expose parts of the Difficulty in Rework or Repairs: Once cured, potting compounds can be challenging to remove, complicating rework or repairs on encapsulated components.
Best Practices for Optimal Potting Results
To enhance the effectiveness of the potting process, consider implementing these best practices:
- Prioritize Material Selection: Match the compound properties with the application’s requirements to ensure durability and effectiveness.
- Clean Components Thoroughly:Clean components reduce the chances of adhesion issues, contributing to a robust final product.
- Use Controlled Curing: To avoid common issues, stick to each potting compound’s recommended curing times and methods.
- Implement Anti-Bubble Techniques:Pour slowly or consider vacuum potting to minimize air bubbles.
- Conduct Rigorous Quality Checks:Inspect each batch of potting for defects to maintain high-quality standards across all components.
Conclusion
Potting manufacturing is indispensable for industries requiring durable, reliable components to withstand environmental challenges. From selecting suitable materials to ensuring precision in application and curing, each phase of the potting process plays a crucial role in the final product’s quality. When applied correctly, potting provides enhanced durability, performance, and longevity, ultimately leading to safer and more reliable end products. By following best practices and understanding potential challenges, manufacturers can achieve consistent results, protecting valuable components and improving overall product performance.
For more about choosing the potting manufacturing process: a comprehensive guide to protecting and enhancing component durability, you can pay a visit to DeepMaterial at https://www.pottingcompound.com/ for more info.
Recent Posts
- What is PCB Potting
- The Evolution of Smart Watch Assembly Adhesive: A Key Component in Modern Wearable Technology
- Laptop Tablet Assembly Adhesive: The Key to Durable and Reliable Device Construction
- Power Bank Assembly Adhesive: The Essential Component for Building Durable Power Banks
- Smartphone Assembly Adhesive: Enhancing Durability and Precision in Modern Devices
- TV Backplane Support and Reflective Film Bonding: A Comprehensive Guide
- Innovative Use of Compounded Materials in Electronic Device Housings: A Comprehensive Guide
- Enhancing Battery Pack Performance: A Deep Dive into Potting Materials, Benefits, and Applications
- A Comprehensive Guide to Industrial Conformal Coatings: Applications, Types, and Future Trends
- Understanding Epoxy Potting Compound Manufacturers: What You Need to Know