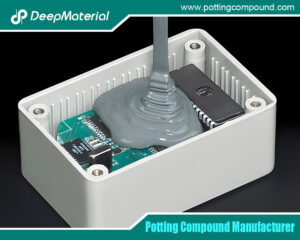
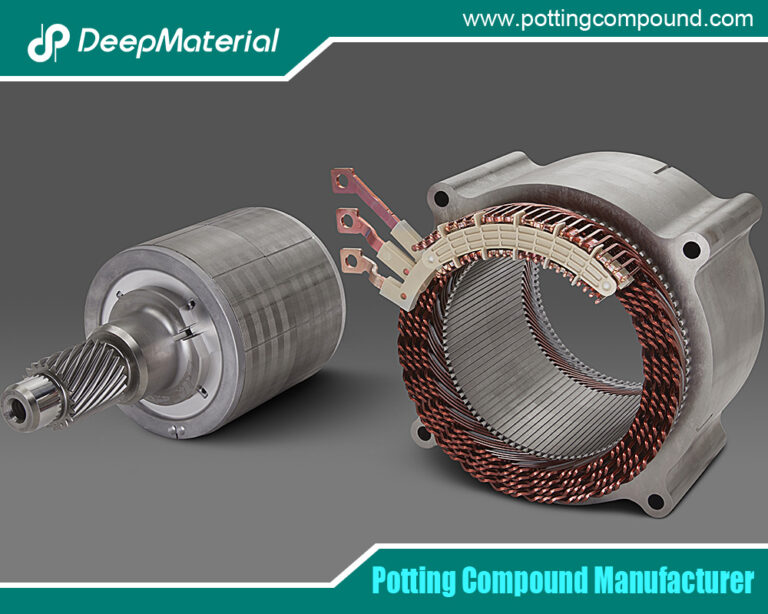
Understanding the Vacuum Potting Process: A Comprehensive Overview
- Electronic Potting Material Manufacturer
- November 26, 2024
- Ceramic Potting Compound, Ceramic Potting Compound Manufacturer, circuit board potting compound, Connector Potting Compound, deepmaterial potting compound, electrical potting compound, Electronic Encapsulant Potting Compound, Electronic Epoxy Potting Compound, Electronic Potting Compound Market, Encapsulant Potting Compound, Encapsulants and Potting Compounds Suppliers, epoxy conformal coating, Epoxy Encapsulant Potting Compound, Industrial Conformal Coating, pcb conformal coating, potting compound china hotsale, potting compound china OEM, potting compound factory hotsale, potting compound factory OEM, potting compound factory wholesale, Silicone Conformal Coating, Urethane Conformal Coating, UV Cure Conformal Coating, vacuum potting process, Waterproof Conformal Coating
Understanding the Vacuum Potting Process: A Comprehensive Overview
In the ever-evolving world of electronics, ensuring the reliability and longevity of components is paramount. One critical method that has gained prominence is the vacuum potting process. This technique primarily encapsulates sensitive electronic parts in protective materials, shielding them from environmental factors like moisture, dust, and extreme temperatures. By creating a vacuum, manufacturers can eliminate air pockets and voids that may compromise the integrity of the encapsulated components. This blog post aims to provide an in-depth understanding of the vacuum potting process, exploring its benefits, applications, challenges, and step-by-step procedures.
What is Vacuum Potting?
Vacuum potting is a manufacturing technique that involves encapsulating electronic components with a polymer resin under vacuum conditions. This process serves several purposes, including:
- Protection:It provides a barrier against moisture, dust, and chemical exposure.
- Thermal Management: Enhances heat dissipation, crucial for maintaining performance and extending lifespan.
- Mechanical Strength: Increases the structural integrity of components, making them more resistant to physical stress.
Key Features of Vacuum Potting
Encapsulation
- Definition:Encapsulation involves surrounding electronic components with a protective material.
- Purpose: To prevent environmental damage and improve durability.
Thermal Management
- Importance: Efficient heat management is essential for electronic components, which generate heat during operation.
- Effectiveness:The suitable potting material can significantly enhance thermal conductivity.
Mechanical Protection
- Shock Absorption:Potting materials can absorb shocks and vibrations, protecting sensitive components from mechanical stress.
- Structural Integrity: Provides a rigid structure that helps maintain alignment and connectivity.
Enhanced Reliability
- Failure Reduction:By sealing connections, vacuum potting minimizes the risk of failure due to environmental factors.
- Consistency: Ensures that electronic components perform reliably over their expected lifespan.
Benefits of Vacuum Potting
The vacuum potting process offers numerous advantages for manufacturers and end-users alike:
- Improved Durability: Protects components from moisture, contaminants, and mechanical stress, significantly extending their lifespan.
- Increased Reliability: Eliminating air pockets and voids reduces the risk of failure due to thermal expansion or contraction.
- Enhanced Performance:Improves electronic devices’ thermal and electrical performance, making them more efficient and reliable.
- Versatility: Applicable across various industries, including automotive, aerospace, telecommunications, and consumer electronics.
- Cost-Effectiveness: While the initial equipment investment may be high, the long-term benefits and savings from reduced failures often outweigh these costs.
Applications of Vacuum Potting
Vacuum potting is utilized across a broad spectrum of industries. Some notable applications include:
- Automotive Electronics: Protects critical components in harsh environments, such as sensors and control units.
- Aerospace Components: Ensures the reliability of parts exposed to extreme conditions and vibrations.
- Telecommunications:Encapsulates circuit boards and connectors to prevent damage from moisture and dust.
- Consumer Electronics:Used in devices like smartphones, laptops, and wearable technology to enhance durability and performance.
- Medical Devices: Safeguards sensitive electronic components in diagnostic and therapeutic equipment.
The Vacuum Potting Process: A Step-by-Step Guide
Understanding the vacuum potting process requires familiarity with its various stages. Below is a detailed breakdown of the steps involved:
Preparation
- Component Cleaning: Ensure all components are clean and free of contaminants. This step is crucial, as any debris can affect adhesion and performance.
- Mold Design: Create a mold to hold the components in place during potting. The mold should be designed to accommodate the shape and size of the components while allowing for proper resin flow.
Mixing the Resin
- Resin Selection: Choose the appropriate resin based on the application. Standard options include epoxy, silicone, and polyurethane. Each type of resin has unique properties suited for different environments.
- Mixing: Follow manufacturer instructions to thoroughly mix the resin and hardener, ensuring an even consistency. Pay close attention to the mixing ratio, as improper proportions can lead to suboptimal performance.
Vacuum Chamber Setup
- Chamber Loading: Place the components and mixed resin into the vacuum chamber. Ensure the components are correctly positioned to avoid misalignment during the curing process.
- Sealing:Seal the chamber to ensure no air escapes during the vacuum process. Proper sealing is essential to maintaining the required vacuum level.
Creating a Vacuum
- Vacuum Application: Activate the vacuum pump to remove air from the chamber. Monitor the pressure to ensure it reaches the desired level.
- Time Duration: Maintain the vacuum for the specified duration. This allows the resin to flow into all cavities and eliminates trapped air.
Pouring the Resin
- Resin Injection:Carefully inject or pour the resin into the mold once the vacuum is achieved. For precision, this step can also be done using a dispensing system. Ensure that the resin fills all voids without creating air bubbles.
Curing
- Curing Conditions:The resin can be cured under specified temperature and pressure conditions. The curing process can vary depending on the type of resin used. Monitor the conditions closely to ensure proper curing.
- Post-Curing: To achieve optimal properties, some resins may require additional curing at elevated temperatures. This step helps improve the final product’s mechanical strength and thermal stability.
Demolding
- Removing the Mold: Carefully remove the mold from the encapsulated components once the resin has cured. Take care not to damage the encapsulated parts during this process.
- Trimming and Finishing: Trim any excess material and perform finishing touches to ensure a smooth surface. This step is essential for aesthetic purposes and prevents sharp edges that could cause injury or damage.
Common Challenges in Vacuum Potting
While vacuum potting offers numerous benefits, it can present particular challenges that manufacturers must navigate:
- Air Entrapment: If not properly executed, air can become trapped within the resin, leading to potential failures. Adequate vacuum levels and careful pouring techniques are essential to mitigate this risk.
- Material Compatibility:Selecting the wrong resin can affect adhesion and performance. It is crucial to choose materials that are compatible with the components being encapsulated.
- Curing Issues: Improper curing can lead to weak spots or inconsistent properties. Close attention to curing conditions and times is necessary to ensure optimal results.
- Cost of Equipment: Initial investments in vacuum chamber systems and mixing equipment can be significant. However, the long-term benefits often justify these costs.
- Environmental Considerations: Disposing of resin materials and waste products must comply with environmental regulations, necessitating proper waste management practices.
Best Practices for Successful Vacuum Potting
To achieve the best results from the vacuum potting process, consider the following best practices:
- Thorough Component Cleaning: Ensure all components are meticulously cleaned to remove any contaminants affecting adhesion.
- Accurate Resin Mixing: Follow the manufacturer’s guidelines for mixing ratios and procedures to ensure optimal resin performance.
- Careful Monitoring of Vacuum Levels: Maintain proper vacuum levels throughout the process to prevent air entrapment.
- Detailed Curing Procedures: Adhere to the recommended curing times and temperatures for the specific resin used.
- Regular Equipment Maintenance: Keep vacuum chambers and mixing equipment well-maintained to ensure consistent performance.
Conclusion
The vacuum potting process is vital in modern manufacturing, providing enhanced durability and reliability for electronic components. As industries continue to innovate and demand higher-quality products, the importance of this process will only continue to grow. By understanding the benefits, applications, and step-by-step procedures involved in vacuum potting, manufacturers can leverage this technique to improve product performance and reduce failures.
For more about understanding the vacuum potting process: a comprehensive overview, you can pay a visit to DeepMaterial at https://www.pottingcompound.com/ for more info.
Recent Posts
- Causes and Avoidance Methods of Bubble Generation in the Potting Process
- Technical Details on Controlling Parameters such as Temperature, Pressure, and Speed in the Potting Process to Ensure Potting Quality
- A Comprehensive Analysis of PCB Pretreatment Before Potting Process: A Crucial Link to Ensure the Performance and Reliability of Electronic Devices
- A Comprehensive Analysis of the Performance Differences of Epoxy Resin, Silicone Rubber and Polyurethane Encapsulation Materials
- How to Select Suitable Potting Materials for PCB According to the Working Environment
- What is PCB Potting
- The Evolution of Smart Watch Assembly Adhesive: A Key Component in Modern Wearable Technology
- Laptop Tablet Assembly Adhesive: The Key to Durable and Reliable Device Construction
- Power Bank Assembly Adhesive: The Essential Component for Building Durable Power Banks
- Smartphone Assembly Adhesive: Enhancing Durability and Precision in Modern Devices