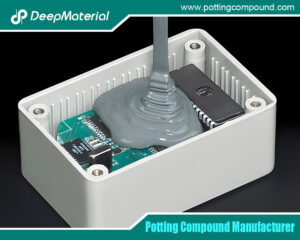
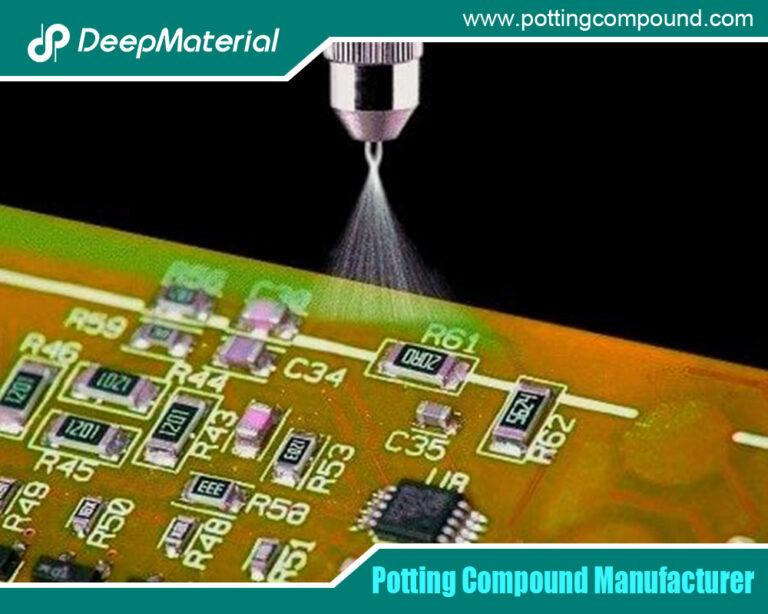
Understanding Potting and Encapsulation: A Guide for Manufacturers
- Electronic Potting Material Manufacturer
- December 3, 2024
- Acrylic Conformal Coating, Ceramic Potting Compound, circuit board potting compound, Connector Potting Compound, deepmaterial potting compound, electric motor potting compound, Electronic Conformal Coating, Electronic Potting and Encapsulation, Electronic Potting and Encapsulation Resins, electronic potting compound, Flexible Potting Compound, Industrial Conformal Coating, LED Potting Compound, pcb conformal coating, PCB Potting Compound, potting and encapsulation, Potting and Encapsulation in the Electronics Industry, potting and encapsulation machine, potting and encapsulation material, potting and encapsulation material china hotsale, potting and encapsulation material china OEM, potting and encapsulation material factory OEM, potting and encapsulation material hotsale, potting and encapsulation material manufacturer, potting and encapsulation material supplier wholesale, potting and encapsulation material wholesale, potting and encapsulation process, potting and encapsulation services, potting and encapsulation supplier, potting compound, Urethane Conformal Coating, UV Cure Conformal Coating, UV Cure Potting Compound, waterproof potting compound
Understanding Potting and Encapsulation: A Guide for Manufacturers
In the ever-evolving landscape of technology and manufacturing, potting and encapsulation have emerged as essential processes for protecting electronic components. As a potting and encapsulation manufacturer, understanding these techniques can enhance product reliability and extend the lifespan of sensitive components. This article delves into the intricacies of potting and encapsulation, their importance, materials used, and best practices for manufacturers aiming to implement these processes effectively.
What is Potting and Encapsulation?
Definitions
- Potting:This involves enclosing electronic components in a solid or gelatinous compound to protect against moisture, dust, chemicals, and mechanical shock.
- Encapsulation:Similar to potting, encapsulation involves surrounding a component with a protective layer, but it often refers to using a resin or polymer that forms a barrier.
Key Differences
- Application Method: Potting typically involves filling a cavity, while encapsulation may include a coating or layering process.
- Material Thickness: Potting usually results in a thicker layer of protection than encapsulation.
Importance of Potting and Encapsulation
- Protection:Both processes provide robust protection against environmental factors, ensuring the longevity of electronic components.
- Electrical Insulation:They help insulate components from electrical interference, enhancing performance.
- Mechanical Support:Potting and encapsulation can provide additional structural integrity to fragile components.
- Thermal Management:Certain materials help dissipate heat, preventing overheating and damage.
Materials Used in Potting and Encapsulation
Common Potting Compounds
- Epoxy Resins: Known for their excellent adhesion and chemical resistance.
- Polyurethane:Offers flexibility and good moisture resistance.
- Silicones:Provide thermal stability and flexibility, ideal for extreme conditions.
Encapsulation Materials
- Acrylics:Lightweight and suitable for various applications but less durable than other options.
- Polyester Resins:Cost-effective and versatile but may not offer the same level of protection as epoxies.
- Thermoplastic Polyurethanes (TPUs):Flexible and rigid, making them ideal for applications requiring movement.
Best Practices for Potting and Encapsulation Manufacturers
Material Selection
- Understand Application Needs:Choose materials based on environmental factors like temperature, humidity, and chemical exposure.
- Conduct Compatibility Tests: Ensure the chosen material is compatible with the electronic components.
Process Optimization
- Temperature Control: Maintain optimal temperatures during curing to avoid defects.
- Vacuum Degassing: Use vacuum processes to eliminate air bubbles that can compromise the protective layer.
- Mixing Techniques: Ensure thorough mixing of potting compounds to achieve uniformity and performance.
Quality Control
- Regular Testing:Implement routine testing for mechanical strength, thermal resistance, and moisture barrier performance.
- Documenting Processes:Maintain detailed records of material batches and process parameters for traceability.
Challenges Faced by Potting and Encapsulation Manufacturers
Material Limitations
- Curing Time: Some materials require extended curing times, slowing production.
- Cost Considerations: High-performance materials may increase manufacturing costs.
Environmental Concerns
- Waste Management:Proper disposal of unused materials and waste products is crucial for sustainability.
- Regulatory Compliance:Manufacturers must adhere to environmental regulations regarding chemical use and emissions.
Technological Advancements
- Keeping Up with Innovation:Staying updated with new materials and technologies is essential for competitive advantage.
Applications of Potting and Encapsulation
Electronics
- Circuit Boards:Protecting circuit boards from moisture and contaminants.
- Sensors: Encapsulating sensors to ensure reliability in various environments.
Automotive Industry
- Electrical Components:Ensuring the durability of components exposed to harsh conditions.
Aerospace
- Critical Systems:Potting and encapsulation of avionics to withstand extreme temperatures and vibrations.
Medical Devices
- Safety and Reliability: Protecting sensitive electronics in medical devices from environmental factors.
Future Trends in Potting and Encapsulation
Emerging Materials
- Biodegradable Resins:The push for sustainable materials leads to the development of eco-friendly potting and encapsulation compounds.
Advanced Technologies
- Brilliant Encapsulation:Innovations in materials that can respond to environmental changes (e.g., temperature fluctuations) are rising.
Automation and Robotics
- Improved Efficiency: Implementing automated processes can enhance consistency and reduce labor costs.
Critical Considerations for Choosing a Potting and Encapsulation Manufacturer
When selecting a potting and encapsulation manufacturer, several factors come into play to ensure you partner with a reliable and effective provider. Here are some critical considerations to keep in mind:
Experience and Expertise
- Industry Knowledge:Look for manufacturers with a proven track record in your specific industry, such as electronics, automotive, or medical devices.
- Technical Skills: Assess the technical expertise of their team, including knowledge of materials and application processes.
Quality Assurance
- Certifications:Ensure the manufacturer has relevant quality certifications, such as ISO 9001, to guarantee adherence to international standards.
- Testing Protocols: Inquire about their quality control measures and testing protocols to validate the performance of potting and encapsulation materials.
Material Selection
- Range of Materials:Evaluate whether the manufacturer offers diverse potting and encapsulation materials for various applications.
- Customization Options:Check if they can provide custom formulations tailored to your needs.
Production Capabilities
- Scalability:Ensure the manufacturer can scale production to meet your volume requirements for small batches or large-scale manufacturing.
- Lead Times: Discuss lead times and delivery schedules to ensure they align with your project timelines.
Environmental Practices
- Sustainability Initiatives:Look for manufacturers committed to sustainable practices, including using eco-friendly materials and responsible waste management.
- Regulatory Compliance:Confirm their compliance with environmental chemical use and emissions regulations.
Customer Support
- Technical Support: Choose a manufacturer that provides comprehensive technical support, from material selection to application advice.
- Communication:Evaluate their responsiveness and communication style to ensure a smooth collaboration throughout the project.
Cost Considerations
- Competitive Pricing:While cost should not be the only factor, obtaining quotes from multiple manufacturers is essential to ensure competitive pricing.
- Value for Money:Assess the overall value, including quality, service, and support, rather than just focusing on the lowest price.
References and Reviews
- Client Testimonials: Request references from previous clients to gauge their satisfaction and the manufacturer’s reliability.
- Industry Reputation:Research online reviews and industry reputation to make an informed decision.
By carefully evaluating these considerations, you can choose a potting and encapsulation manufacturer that aligns with your business goals and technical requirements, ultimately contributing to the success of your projects.
Conclusion
As the demand for reliable electronic components continues to grow, the role of potting and encapsulation manufacturers has never been more critical. By understanding the nuances of these processes, selecting appropriate materials, and implementing best practices, manufacturers can significantly enhance the durability and performance of their products. As the industry moves toward innovative materials and automated processes, staying informed and adaptable will ensure success in this dynamic field. Embracing these changes will meet the demands of modern applications and pave the way for sustainable practices in the manufacturing sector.
For more about understanding potting and encapsulation: a guide for manufacturers, you can pay a visit to DeepMaterial at https://www.pottingcompound.com/ for more info.
Recent Posts
- Causes and Avoidance Methods of Bubble Generation in the Potting Process
- Technical Details on Controlling Parameters such as Temperature, Pressure, and Speed in the Potting Process to Ensure Potting Quality
- A Comprehensive Analysis of PCB Pretreatment Before Potting Process: A Crucial Link to Ensure the Performance and Reliability of Electronic Devices
- A Comprehensive Analysis of the Performance Differences of Epoxy Resin, Silicone Rubber and Polyurethane Encapsulation Materials
- How to Select Suitable Potting Materials for PCB According to the Working Environment
- What is PCB Potting
- The Evolution of Smart Watch Assembly Adhesive: A Key Component in Modern Wearable Technology
- Laptop Tablet Assembly Adhesive: The Key to Durable and Reliable Device Construction
- Power Bank Assembly Adhesive: The Essential Component for Building Durable Power Banks
- Smartphone Assembly Adhesive: Enhancing Durability and Precision in Modern Devices