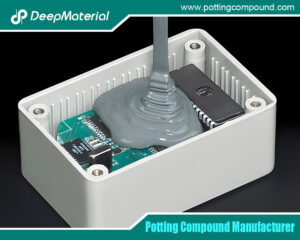
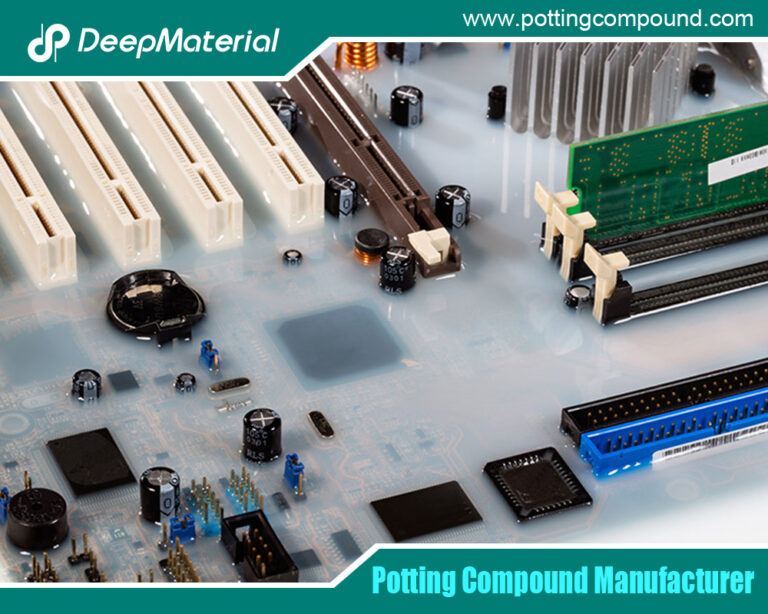
A Comprehensive Analysis of the Performance Differences of Epoxy Resin, Silicone Rubber and Polyurethane Encapsulation Materials
- Electronic Potting Material Manufacturer
- April 8, 2025
- conformal coating material, conformal coating process, conformal coating waterproof, electrical potting compound, electronic board level underfill and encapsulation material market, electronic epoxy encapsulant potting compounds, encapsulation material, encapsulation material manufacturer, epoxy potting compound, pcb potting, polyurethane potting compound, polyurethane potting compound for electronics, potting and encapsulation material, potting and encapsulation material china, potting and encapsulation material china hotsale, potting and encapsulation material factory OEM, potting and encapsulation material hotsale, potting and encapsulation material manufacturer, potting and encapsulation material supplier wholesale, potting and encapsulation material wholesale, potting compound for electronics, potting compound for pcb, potting compound vs epoxy, potting material for electronic components, potting material for electronics, potting pcb, silicone potting compound for electronics, UV curing potting compound, UV Curing Potting Compounds, waterproof potting compound, what is pcb potting
A Comprehensive Analysis of the Performance Differences of Epoxy Resin, Silicone Rubber and Polyurethane Encapsulation Materials
In the manufacturing process of electronic devices, the selection of encapsulation materials is of utmost importance as it directly affects the performance, reliability and service life of the devices. Epoxy resin, silicone rubber and polyurethane are three common encapsulation materials, which have obvious differences in electrical properties, mechanical properties and aging resistance properties. A thorough understanding of these differences is of great significance for the correct selection of encapsulation materials and the improvement of the quality and performance of electronic devices.
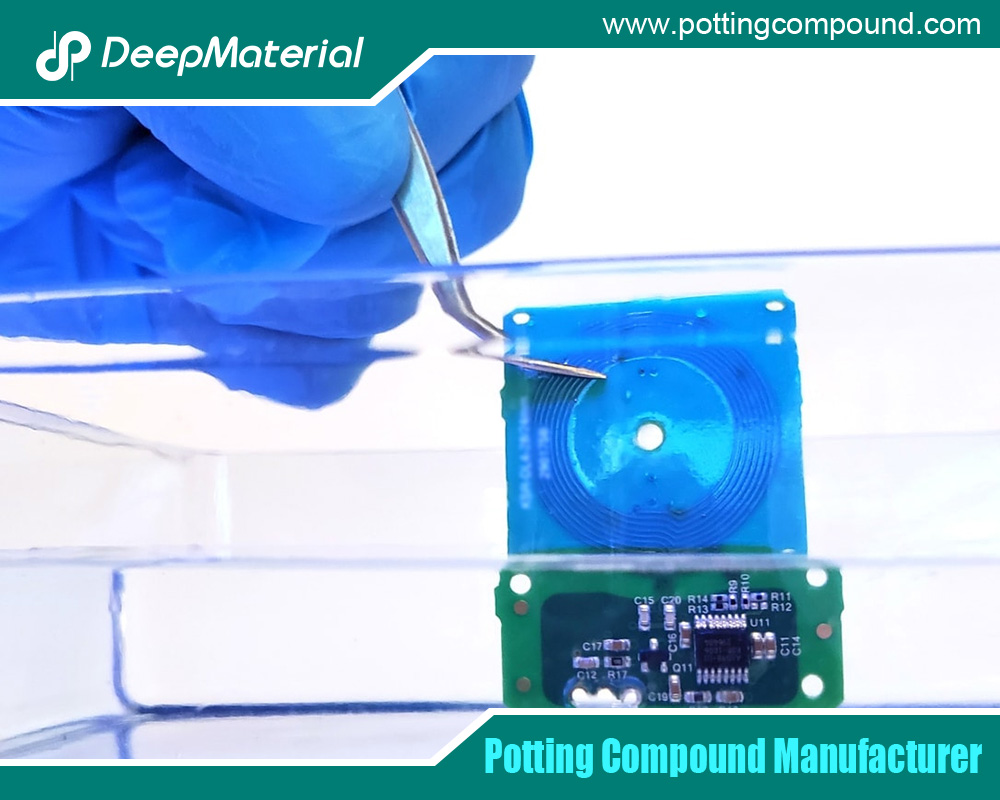
Comparison of Electrical Properties
I. Insulation Resistance
- Epoxy Resin: It has a relatively high insulation resistance, generally ranging from 10^13 to 10^15 Ω·cm. This enables it to effectively prevent current leakage and ensure the electrical isolation between electronic components, making it suitable for applications with high requirements for insulation performance, such as high-voltage electrical equipment and circuit boards.
- Silicone Rubber: The insulation resistance is also quite considerable, usually within the range of 10^14 to 10^16 Ω·cm. The molecular structure of silicone rubber contains silicon-oxygen bonds, and the stability of these chemical bonds endows silicone rubber with good insulation performance. Moreover, in harsh environments such as high temperature and humidity, the change in its insulation performance is relatively small.
- Polyurethane: The insulation resistance is generally around 10^12 to 10^14 Ω·cm. Although its insulation performance is slightly inferior to that of epoxy resin and silicone rubber, in most common electronic device applications, it can still meet the basic insulation requirements. However, the insulation performance of polyurethane is relatively sensitive to humidity. In a high-humidity environment, its insulation resistance may decrease.
II. Dielectric Constant and Dissipation Factor
- Epoxy Resin: The dielectric constant is generally between 3 and 5 (at 1 MHz), and the dissipation factor is between 0.005 and 0.02 (at 1 MHz). The low dielectric constant and dissipation factor mean that under a high-frequency electric field, the energy loss generated by epoxy resin is relatively small, and the stability of signal transmission is high, making it suitable for the encapsulation of high-frequency electronic circuits.
- Silicone Rubber: The dielectric constant is relatively low, usually between 2.5 and 3.5 (at 1 MHz), and the dissipation factor is also very small, generally between 0.001 and 0.005 (at 1 MHz). This gives silicone rubber excellent electrical performance in high-frequency applications, which can effectively reduce signal attenuation and distortion, and is often used in electronic devices with strict requirements for high-frequency performance, such as microwave devices and radio frequency modules.
- Polyurethane: The dielectric constant is between 4 and 6 (at 1 MHz), and the dissipation factor is relatively large, between 0.01 and 0.05 (at 1 MHz). Due to its relatively high dielectric constant and dissipation factor, the performance of polyurethane in high-frequency applications is not as good as that of epoxy resin and silicone rubber, and it is more suitable for the encapsulation of low-frequency or electronic devices with low requirements for high-frequency performance.
III. Dielectric Strength
- Epoxy Resin: It has a relatively high dielectric strength, generally reaching 20 to 30 kV/mm. This enables epoxy resin to withstand a relatively high electric field strength without breakdown, providing reliable electrical insulation protection for electronic devices, and is often used in the field of high-voltage insulation, such as the encapsulation of transformers and insulators.
- Silicone Rubber: The dielectric strength is also quite good, usually between 25 and 35 kV/mm. The good dielectric strength of silicone rubber makes it perform excellently in electrical insulation. At the same time, its soft characteristics can effectively buffer the electric field stress and reduce the possibility of partial discharge, improving the operation stability of electronic devices.
- Polyurethane: The dielectric strength is generally around 15 to 25 kV/mm. Although its dielectric strength is slightly lower than that of epoxy resin and silicone rubber, in many medium and low voltage electronic devices, it can still meet the normal use requirements. However, in an environment with high voltage and strong electric field, the use of polyurethane encapsulation materials needs to be carefully evaluated.
Comparison of Mechanical Properties
I. Hardness
- Epoxy Resin: After curing, it has a relatively high hardness, and the Shore hardness is generally between 80 and 90 D. The high hardness enables epoxy resin to provide good support and protection for electronic components, preventing the components from being squeezed and collided by external forces. However, the high hardness also means that the flexibility of epoxy resin is poor. When subjected to large impacts or vibrations, it is prone to cracking.
- Silicone Rubber: The hardness is relatively low, and the Shore hardness is usually between 20 and 60 A. The soft characteristics of silicone rubber enable it to effectively absorb and buffer external forces, providing good shock absorption protection for electronic components. Moreover, silicone rubber has good flexibility and elasticity, and can adapt to electronic components of different shapes and sizes, and has obvious advantages in some occasions with high requirements for flexibility, such as the encapsulation of flexible circuit boards.
- Polyurethane: The hardness range is relatively wide, and the Shore hardness can be adjusted between 30 and 90 A. By adjusting the formula and curing process, polyurethane can obtain different hardnesses to meet the requirements of different application scenarios. For example, in occasions where a certain degree of flexibility and wear resistance are required, a polyurethane with lower hardness can be selected; while in situations where higher support strength is required, a polyurethane with higher hardness can be chosen.
II. Tensile Strength and Elongation at Break
- Epoxy Resin: It has a relatively high tensile strength, generally between 30 and 80 MPa, but the elongation at break is relatively low, usually between 1% and 5%. This indicates that when subjected to tensile force, epoxy resin can maintain a relatively high strength, but its deformation ability is poor. Once the limit is exceeded, it is prone to brittle fracture.
- Silicone Rubber: The tensile strength is relatively low, generally between 2 and 10 MPa, but the elongation at break is very high, reaching 200% to 1000%. The good elongation at break of silicone rubber enables it to maintain the integrity of the structure within a large deformation range and is not easy to break. This is a very important performance for electronic devices that need to adapt to environmental factors such as temperature changes and mechanical vibrations.
- Polyurethane: The tensile strength is between 10 and 50 MPa, and the elongation at break is between 100% and 500%. Polyurethane has both a certain strength and good flexibility, and its tensile strength and elongation at break are between those of epoxy resin and silicone rubber, which can play a good role in some occasions with comprehensive requirements for mechanical properties.
III. Shear Strength
- Epoxy Resin: It has a relatively high shear strength for most materials and can achieve good adhesion with a variety of substrates such as metals, ceramics and plastics, generally between 10 and 30 MPa. This enables epoxy resin to firmly fix the electronic components in the encapsulation body during the encapsulation process, ensuring the stability of the electronic device under various working conditions.
- Silicone Rubber: The shear strength is relatively low, generally between 1 and 5 MPa. The molecular structure of silicone rubber is relatively flexible, and the intermolecular force is weak, resulting in its adhesion strength with the substrate being inferior to that of epoxy resin. However, in some occasions where the requirements for adhesion strength are not high, but the flexibility and temperature resistance are more important, the low shear strength of silicone rubber does not affect its application.
- Polyurethane: The shear strength is between 5 and 20 MPa, and the adhesion performance is between that of epoxy resin and silicone rubber. Polyurethane can form good adhesion with a variety of materials, and while maintaining a certain adhesion strength, it can also provide a certain degree of flexibility, making it have advantages in some applications that require both adhesion and flexibility.
Comparison of Aging Resistance Properties
I. Thermal Aging Performance
- Epoxy Resin: The temperature resistance of ordinary epoxy resin is average, and the long-term service temperature is usually between 80 and 150°C. In a high-temperature environment, epoxy resin will gradually undergo thermal oxidation degradation, resulting in a decrease in its performance, such as an increase in hardness, an increase in brittleness, and a deterioration of electrical properties. However, by adding special heat-resistant additives or using high-performance epoxy resin systems, its temperature resistance can be improved, enabling it to be used at higher temperatures.
- Silicone Rubber: It has excellent thermal stability and can maintain good performance within a wide temperature range of – 60 to 200°C. In the molecular structure of silicone rubber, the bond energy of the silicon-oxygen bond is relatively high, endowing it with excellent heat resistance and making it less likely to decompose and age at high temperatures. Even in a long-term high-temperature environment, the physical and chemical properties of silicone rubber change relatively little, which can provide reliable long-term protection for electronic devices.
- Polyurethane: The temperature resistance is relatively poor, and the general long-term service temperature does not exceed 100°C. At high temperatures, polyurethane is prone to thermal decomposition and oxidation reactions, resulting in a decrease in its hardness, loss of elasticity, and deterioration of adhesion performance. Therefore, the application of polyurethane encapsulation materials in high-temperature environments is limited to a certain extent, and it is more suitable for use in normal temperature or low-temperature environments.
II. UV Aging Resistance Performance
- Epoxy Resin: It is relatively sensitive to ultraviolet light. Under the irradiation of ultraviolet light, it is prone to photo-oxidative degradation, resulting in yellowing and embrittlement of the material surface and a decrease in performance. Therefore, when epoxy resin encapsulation materials are used in outdoor or environments with strong ultraviolet light irradiation, ultraviolet absorbers need to be added or other protective measures need to be taken to improve their UV aging resistance performance.
- Silicone Rubber: It has good UV aging resistance performance. The silicon-oxygen bonds in the molecular structure of silicone rubber have high stability to ultraviolet light and are not easily damaged by ultraviolet light. Moreover, the surface of silicone rubber is usually relatively smooth, and it is difficult for ultraviolet light to accumulate and accumulate energy on its surface, thereby reducing the damage of ultraviolet light to the internal structure of the material. Therefore, silicone rubber encapsulation materials have been widely used in outdoor electronic devices, solar cell modules and other fields.
- Polyurethane: The UV aging resistance performance is poor. Under the long-term irradiation of ultraviolet light, the molecular chain of polyurethane will break and crosslink, resulting in yellowing, hardening, cracking of the material and a serious decrease in performance. In order to improve the UV aging resistance performance of polyurethane, it is usually necessary to add light stabilizers, antioxidants and other additives. However, even so, its UV resistance performance is still not as good as that of silicone rubber.
III. Chemical Media Aging Resistance Performance
- Epoxy Resin: It has good resistance to most acids, alkalis, salts and other chemical media and can resist chemical corrosion to a certain extent. However, in extreme chemical environments such as strong oxidizing acids and strong alkalis, epoxy resin may undergo chemical reactions such as hydrolysis and oxidation, resulting in performance degradation. In addition, some organic solvents may also cause swelling or dissolution of epoxy resin, affecting its service performance.
- Silicone Rubber: It has good chemical stability and good resistance to a variety of chemical media. The silicon-oxygen bonds in the molecular structure of silicone rubber have strong resistance to chemical substances and are not easy to react with most chemical substances. Moreover, the non-polar characteristics of the surface of silicone rubber make it less likely to adsorb chemical substances, further improving its chemical media aging resistance performance. Therefore, silicone rubber encapsulation materials have advantages in corrosion-resistant applications in the chemical, electronic and other fields.
- Polyurethane: The chemical media aging resistance performance is average. In some environments with strong acids, alkalis and organic solvents, polyurethane may undergo phenomena such as swelling and degradation, resulting in a decrease in performance. The chemical stability of polyurethane is related to its molecular structure and formula. Through reasonable formula design and modification, its chemical media aging resistance performance can be improved to a certain extent, but overall, its chemical resistance is inferior to that of silicone rubber and epoxy resin.
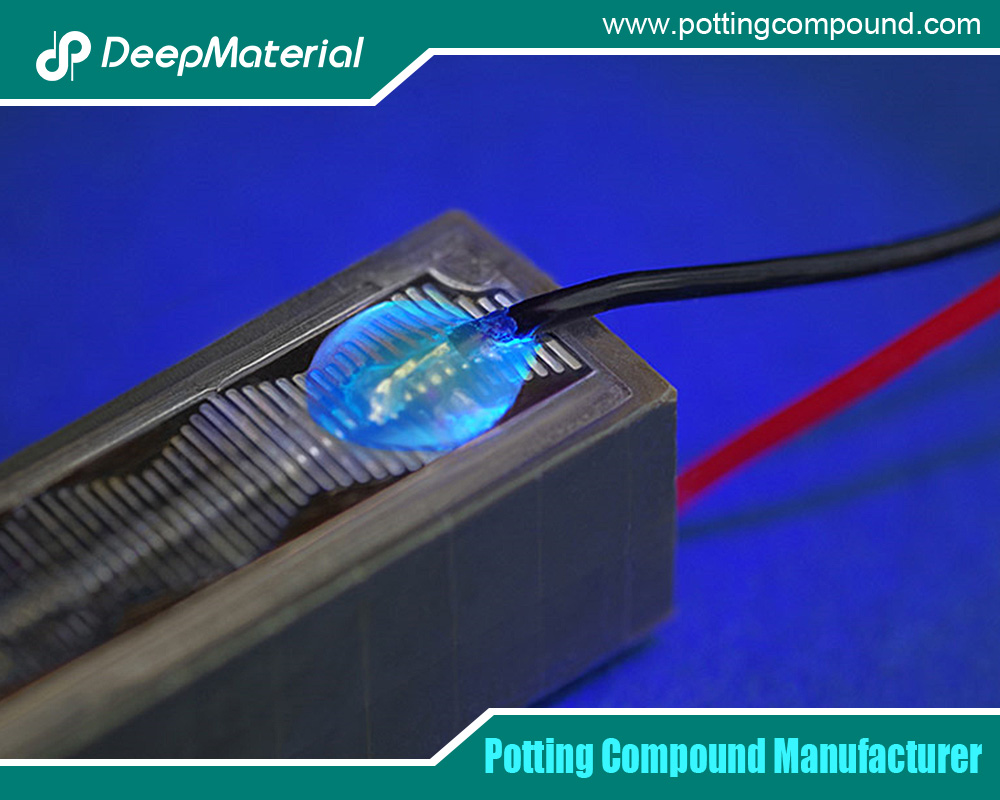
Conclusion
In conclusion, the three encapsulation materials, epoxy resin, silicone rubber and polyurethane, have their own characteristics in electrical properties, mechanical properties and aging resistance properties. Epoxy resin has high insulation resistance, dielectric strength and mechanical strength, and good adhesion to a variety of materials, but its flexibility and aging resistance performance are relatively weak; silicone rubber has excellent electrical properties, flexibility, high and low temperature resistance performance and aging resistance performance, but its adhesion strength is relatively low; the performance of polyurethane is between the two, with a certain strength and flexibility, and good low-temperature resistance performance, but its high-temperature resistance and aging resistance performance are relatively poor. In practical applications, the appropriate encapsulation material should be comprehensively selected according to the specific use environment, performance requirements and cost budget of electronic devices to ensure the reliability and service life of electronic devices.
For more about choosing a comprehensive analysis of the performance differences of epoxy resin, silicone rubber and polyurethane encapsulation materials, you can pay a visit to DeepMaterial at https://www.pottingcompound.com/ for more info.
Recent Posts
- Causes and Avoidance Methods of Bubble Generation in the Potting Process
- Technical Details on Controlling Parameters such as Temperature, Pressure, and Speed in the Potting Process to Ensure Potting Quality
- A Comprehensive Analysis of PCB Pretreatment Before Potting Process: A Crucial Link to Ensure the Performance and Reliability of Electronic Devices
- A Comprehensive Analysis of the Performance Differences of Epoxy Resin, Silicone Rubber and Polyurethane Encapsulation Materials
- How to Select Suitable Potting Materials for PCB According to the Working Environment
- What is PCB Potting
- The Evolution of Smart Watch Assembly Adhesive: A Key Component in Modern Wearable Technology
- Laptop Tablet Assembly Adhesive: The Key to Durable and Reliable Device Construction
- Power Bank Assembly Adhesive: The Essential Component for Building Durable Power Banks
- Smartphone Assembly Adhesive: Enhancing Durability and Precision in Modern Devices