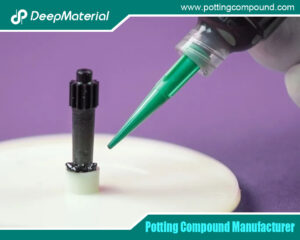
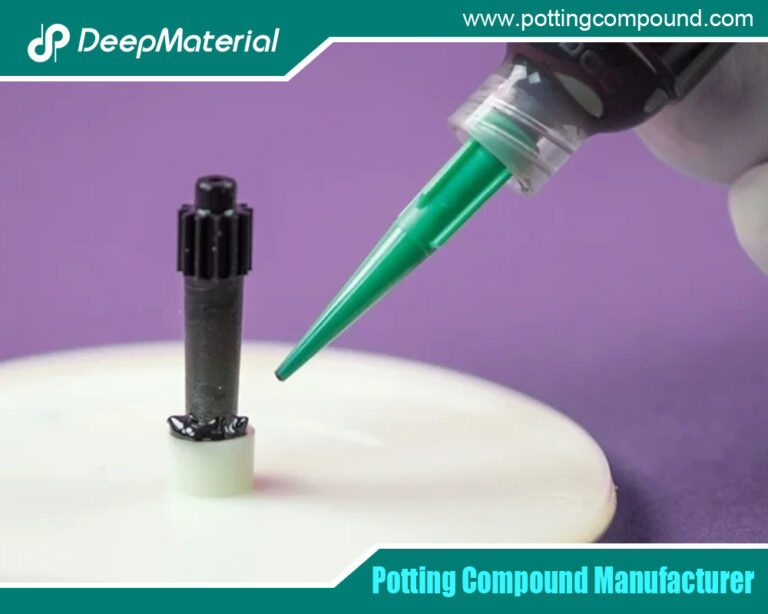
How to Determine the Appropriate Encapsulation Thickness
- Electronic Potting Material Manufacturer
- April 24, 2025
- Ceramic Potting Compound, Ceramic Potting Compound Manufacturer, circuit board encapsulation, circuit board potting compound, Connector Potting Compound, deepmaterial potting compound, Electrical Component Encapsulation, electrical encapsulation, electronic board level underfill and encapsulation material market, electronic encapsulation, electronic encapsulation china hotsale, Electronic Encapsulation in Potting Material Manufacturing, electronic encapsulation manufacturer, Electronic Encapsulation Manufacturing, Electronic Encapsulation Methods, Electronic encapsulation process, electronic encapsulation supplier, electronic epoxy encapsulant potting compounds, encapsulation thickness, epoxy encapsulation, epoxy encapsulation electronic components, epoxy encapsulation for photovolatics, epoxy encapsulation for photovolatics and oleds, epoxy encapsulation led, epoxy encapsulation meaning, epoxy encapsulation molding compound, epoxy potting compound, pcb encapsulation epoxy, pcb potting, polyurethane potting compound for electronics, potting compound, potting material for electronic components, potting material for electronics, uv potting compound
How to Determine the Appropriate Encapsulation Thickness
In numerous fields such as electronic packaging, mechanical manufacturing, and building waterproofing, the encapsulation technology plays a crucial role. It can provide various functions for the encapsulated objects, including waterproofing, moisture resistance, insulation, and protection. The encapsulation thickness, as an important parameter in the encapsulation process, has a vital impact on the encapsulation effect. Determining the appropriate encapsulation thickness not only ensures the stable performance of products but also effectively controls costs and improves production efficiency. This article will deeply explore the methods and key points of determining the appropriate encapsulation thickness.
The Influence of Encapsulation Thickness on Performance
1. Electrical Performance
For electronic encapsulation, the encapsulation thickness directly affects the insulation performance. In high-voltage electrical equipment, if the encapsulation thickness is insufficient, it may not be able to withstand high voltages, leading to problems such as leakage and breakdown, which seriously threaten the safe operation of the equipment. Generally speaking, to ensure good insulation effects, in high-voltage environments, the encapsulation thickness needs to be increased accordingly. For example, in 10kV electrical equipment, the thickness of the encapsulation adhesive may need to reach a certain value (such as 10 – 15mm according to relevant standards or empirical values) to meet the insulation withstand voltage requirements. However, the encapsulation thickness is not the thicker the better. An overly thick encapsulation layer may, due to problems such as internal stress concentration, generate defects like cracks during long-term operation, instead reducing the insulation performance.
2. Mechanical Performance
The encapsulation material can provide a certain degree of mechanical protection for the encapsulated objects, resisting external impacts, vibrations, etc. An appropriate encapsulation thickness can effectively enhance this protective effect. Taking electronic components as an example, when subjected to mechanical vibrations, a thicker encapsulation layer can better buffer the vibration energy, reduce the stress on the components, and lower the risk of component damage. In automotive electronics, since vehicles will generate various vibrations and impacts during driving, the encapsulation thickness for automotive electronic modules needs to be reasonably determined according to the actual vibration environment and the bearing capacity of the components. Generally, it may be around 5 – 10mm to ensure the stable operation of the electronic modules in complex mechanical environments. However, if the encapsulation thickness is too large, when the temperature changes, the stress generated due to the difference in the coefficient of thermal expansion between the encapsulation material and the encapsulated object will also increase, which may cause the encapsulation layer to crack or debond from the encapsulated object, weakening the mechanical protection effect.
3. Thermal Performance
In electronic devices, the dissipation of heat is of great importance. The encapsulation thickness will affect the heat transfer efficiency. An overly thin encapsulation layer is not conducive to the transfer of heat from the heating element to the outside, resulting in an increase in the element temperature and affecting its performance and lifespan. For example, in high-power LED lighting fixtures, in order to ensure that the heat generated by the LED chips can be dissipated in a timely manner, the encapsulation adhesive needs to have an appropriate thickness (such as 3 – 5mm) to ensure a good heat conduction path. However, if the encapsulation thickness is too thick, the thermal resistance will increase, which is also not conducive to the transfer of heat, making the temperature inside the device too high. Therefore, it is necessary to find a balance between heat conduction and thermal resistance to determine the optimal encapsulation thickness to ensure the normal heat dissipation of the device.
4. Chemical Performance
In some chemically corrosive environments, the encapsulation layer needs to play a protective role. Sufficient encapsulation thickness can extend the time for chemical substances to penetrate into the protected object and provide better corrosion resistance. For example, in the electronic control system of chemical equipment, if it is in an environment with corrosive gases, the encapsulation thickness may need to be thicker than in ordinary environments (such as 8 – 12mm) to ensure that the internal electronic components are not corroded. However, if the encapsulation material is not properly selected, even if the thickness is sufficient, it may not be able to effectively resist chemical corrosion. Therefore, when determining the encapsulation thickness, it is necessary to comprehensively consider it in combination with the chemical resistance of the encapsulation material.
Consideration Factors for Determining the Encapsulation Thickness
1. Application Scenarios and Environments
Different application scenarios have different requirements for the encapsulation thickness. In outdoor electronic devices, since they need to withstand harsh environments such as wind, rain, and temperature changes, the encapsulation thickness is usually larger than that of indoor devices. For example, for the encapsulation of outdoor LED displays, in order to be waterproof, dustproof, and weather-resistant, the encapsulation thickness may be around 5 – 8mm. In the aerospace field, due to the extremely high requirements for the weight and reliability of the equipment, the encapsulation thickness needs to be as thin as possible on the premise of ensuring performance. At the same time, high-performance encapsulation materials need to be used to meet the stringent environmental requirements. In addition, for occasions with explosion-proof requirements, the encapsulation thickness also needs to meet the corresponding explosion-proof standards to prevent sparks and other internal factors from triggering external dangers.
2. Structure and Size of the Encapsulated Object
The complexity of the structure and the size of the encapsulated object are important bases for determining the encapsulation thickness. For components with a simple structure and small size, the encapsulation thickness can be relatively thin. For example, the encapsulation of small integrated circuit chips may only require a thickness of 1 – 3mm to meet the protection requirements. However, for objects with a complex structure and internal cavities or gaps, a sufficient encapsulation thickness is required to ensure complete filling and effective protection. For example, in some large power modules, there are multiple electronic components and complex wiring inside, and the encapsulation thickness may need to reach 10 – 15mm or even thicker to ensure that the encapsulation material can fill all corners and provide comprehensive protection.
3. Characteristics of the Encapsulation Material
Different encapsulation materials have different physical and chemical characteristics, and these characteristics will affect the selection of the encapsulation thickness. For example, epoxy resin encapsulation adhesive has high strength and good insulation performance, but it has a relatively large shrinkage rate during the curing process. In order to reduce the impact of the stress generated by shrinkage on the encapsulated object, it may be necessary to appropriately increase the encapsulation thickness. Silicone encapsulation adhesive has good flexibility and excellent high and low-temperature resistance performance, but its hardness is relatively low. In occasions with high requirements for mechanical strength, a thicker encapsulation layer may be required to make up for its insufficient hardness. In addition, the fluidity of the encapsulation material will also affect the encapsulation thickness. Materials with good fluidity can achieve good filling at a relatively thin thickness, while materials with poor fluidity may require a thicker thickness to ensure the filling effect.
4. Cost Factors
The encapsulation thickness is directly related to the amount of encapsulation material used, thus affecting the cost. On the premise of meeting the performance requirements, a relatively thin encapsulation thickness should be selected as much as possible to reduce costs. For products in large-scale production, cost control is particularly important. For example, in the production of consumer electronics products, by optimizing the encapsulation process and determining the appropriate encapsulation thickness, the production cost can be significantly reduced while ensuring the product quality. However, it is not advisable to excessively reduce the encapsulation thickness just to reduce costs, which may lead to a decline in product performance. It is necessary to find the best balance between cost and performance.
Methods and Processes for Determining the Encapsulation Thickness
1. Refer to Industry Standards and Specifications
In many industries, there are standards and specifications regarding the encapsulation thickness. For example, in the electronics industry, organizations such as the International Electrotechnical Commission (IEC) and the Institute of Electrical and Electronics Engineers (IEEE) have formulated a series of standards related to electronic encapsulation, specifying the requirements for the encapsulation thickness in different application scenarios. When designing the encapsulation process, the relevant industry standards should be consulted and followed first to ensure that the encapsulation thickness meets the basic safety and performance requirements. For example, in the insulation encapsulation of electrical equipment, standards such as IEC 60664 regarding the insulation distance and encapsulation thickness can be referred to to ensure the electrical safety performance of the equipment.
2. Conduct Simulation Analysis
Using computer-aided engineering (CAE) software for simulation analysis is an effective method for determining the encapsulation thickness. By establishing a three-dimensional model of the encapsulated object and the encapsulation material, inputting the physical parameters of the encapsulation material, environmental conditions, and the structure of the encapsulated object, etc., the software can simulate the flow, curing of the material during the encapsulation process, and its performance under different working conditions. For example, through simulation, the influence of the encapsulation thickness on the electrical insulation performance, heat transfer performance, and mechanical stress distribution can be analyzed, so as to predict the performance of the product under different encapsulation thicknesses and provide a basis for determining the appropriate encapsulation thickness. In the development of automotive electronics, CAE software is often used to simulate the encapsulation process and optimize the encapsulation thickness to improve the reliability of products in complex environments.
3. Experimental Testing and Verification
Before actual production, experimental testing is an essential link. By making samples, encapsulating them with different encapsulation thicknesses, and conducting various performance tests on the samples, such as electrical performance tests, mechanical performance tests, and thermal performance tests. According to the test results, analyze the relationship between the encapsulation thickness and performance to determine the optimal encapsulation thickness. For example, when developing a new type of electronic sensor, make multiple samples with different encapsulation thicknesses, and conduct environmental tests such as high temperature, low temperature, vibration, and humidity, as well as electrical performance tests such as insulation resistance and withstand voltage. Through the analysis of the test data, determine the encapsulation thickness that can not only meet the performance requirements but also be the most economical and reasonable. During the experiment, the encapsulation process can also be optimized, such as adjusting parameters like the encapsulation speed and temperature to further improve the encapsulation quality.
Encapsulation Thickness Control and Quality Assurance
1. Encapsulation Process Control
During the encapsulation process, strictly controlling the process parameters is the key to ensuring the uniformity of the encapsulation thickness. The accuracy and stability of the encapsulation equipment have an important impact on the encapsulation thickness. For example, using a high-precision dispensing machine can accurately control the flow rate and velocity of the encapsulation material to ensure the consistency of the encapsulation thickness. At the same time, the temperature and humidity of the encapsulation environment need to be controlled, because changes in temperature and humidity will affect the fluidity and curing speed of the encapsulation material, and thus affect the encapsulation thickness. During the encapsulation process, attention also needs to be paid to the encapsulation method, such as whether it is a one-time encapsulation or a layered encapsulation. For a thicker encapsulation layer, layered encapsulation can reduce internal stress and improve the encapsulation quality, but attention needs to be paid to the control of the thickness of each layer and the bonding quality between layers.
2. Quality Inspection and Monitoring
Establish a complete quality inspection and monitoring system to conduct real-time monitoring and inspection of the encapsulation thickness. Non-contact measurement methods, such as laser ranging and ultrasonic measurement, can be used to conduct on-line monitoring of the encapsulation thickness during the encapsulation process, and promptly discover abnormal thickness situations and make adjustments. After the encapsulation is completed, through the method of sampling inspection, use tools such as calipers and micrometers to accurately measure the encapsulation thickness to ensure that the encapsulation thickness meets the design requirements. In addition, comprehensive evaluation of the encapsulation quality can also be carried out through means such as appearance inspection, electrical performance testing, and mechanical performance testing, and promptly discover quality problems caused by inappropriate encapsulation thickness or other reasons.
Determining the appropriate encapsulation thickness is a process of comprehensively considering various factors. It is necessary to conduct in-depth analysis and practice from multiple aspects, including the influence of the encapsulation thickness on performance, consideration factors for determining the encapsulation thickness, methods and processes for determination, as well as encapsulation thickness control and quality assurance. Only by scientifically and reasonably determining the encapsulation thickness and strictly controlling the quality during the encapsulation process can the encapsulated products operate stably and reliably in various application scenarios and meet the needs of different industries.
For more about how to determine the appropriate encapsulation thickness, you can pay a visit to DeepMaterial at https://www.pottingcompound.com/ for more info.
Recent Posts
- How to Determine the Appropriate Encapsulation Thickness
- Influence of Encapsulation Thickness on the Heat Dissipation Performance and Electrical Insulation Performance of PCB
- Causes and Avoidance Methods of Bubble Generation in the Potting Process
- Technical Details on Controlling Parameters such as Temperature, Pressure, and Speed in the Potting Process to Ensure Potting Quality
- A Comprehensive Analysis of PCB Pretreatment Before Potting Process: A Crucial Link to Ensure the Performance and Reliability of Electronic Devices
- A Comprehensive Analysis of the Performance Differences of Epoxy Resin, Silicone Rubber and Polyurethane Encapsulation Materials
- How to Select Suitable Potting Materials for PCB According to the Working Environment
- What is PCB Potting
- The Evolution of Smart Watch Assembly Adhesive: A Key Component in Modern Wearable Technology
- Laptop Tablet Assembly Adhesive: The Key to Durable and Reliable Device Construction