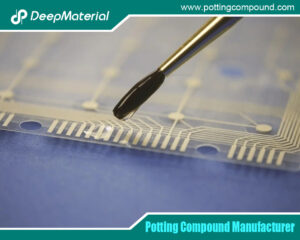
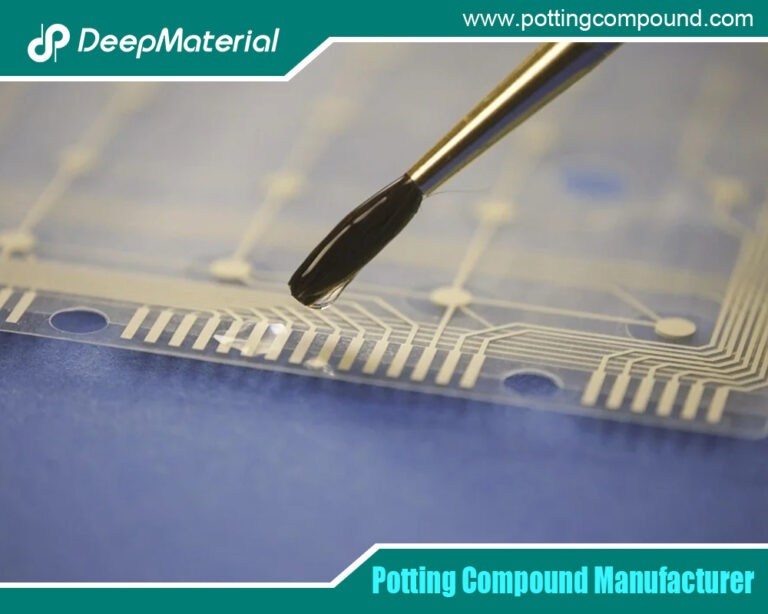
Determination of Curing Parameters of Encapsulating Materials: From Theory to Practice
- Electronic Potting Material Manufacturer
- April 27, 2025
- circuit board potting compounds, conformal coating for electronics, conformal coating for pcb, conformal coating material, conformal coating pcb, conformal coating process, conformal coating silicone, conformal coating spray, conformal coating waterproof, Connector Potting Compound, deepmaterial potting compound, electric motor potting compound, electrical potting compound, electronic epoxy encapsulant potting compounds, encapsulating materials, encapsulating materials factory, encapsulating materials manufacturer, encapsulating materials supplier, epoxy potting compound, pcb encapsulation epoxy, polyurethane potting compound, potting compound for electronics, potting compound for pcb, potting compound vs epoxy, potting material for electronic components, silicone potting compound for electronics, UV curing potting compound, waterproof potting compound
Determination of Curing Parameters of Encapsulating Materials: From Theory to Practice
In numerous fields such as electronics manufacturing, aerospace, and automotive, encapsulating materials are widely used to protect electronic components, enhance structural stability, and achieve functions like waterproofing, moisture resistance, and insulation. The curing time and curing conditions of encapsulating materials, such as temperature and humidity, play a decisive role in their final performance. Correctly determining these parameters can not only ensure the quality and reliability of products but also improve production efficiency and reduce costs. This article will delve into how to scientifically determine the curing time and curing conditions of encapsulating materials.
Curing Principle of Encapsulating Materials
Different types of encapsulating materials have different curing principles. Take the common epoxy resin encapsulating material as an example. It usually consists of epoxy resin and a curing agent. During the curing process, the epoxy groups in the epoxy resin molecules react chemically with the active groups in the curing agent to form a three-dimensional network structure, thus transforming the material from a liquid state to a solid state. This process involves complex chemical kinetics, and the reaction rate is affected by various factors, such as temperature and the concentration of the curing agent.
Silicone encapsulating materials mostly cure through condensation reactions or addition reactions. Condensation-type silicone releases small molecular by-products, such as ethanol, during the curing process; addition-type silicone undergoes a hydrosilylation reaction to achieve curing under the action of a catalyst, and no small molecules are generated during the reaction. Understanding these curing principles is the basis for understanding the influencing factors of curing time and conditions.
Factors Affecting Curing Time and Conditions
- Temperature: Temperature has the most significant influence on the curing of encapsulating materials. According to the Arrhenius equation, the chemical reaction rate has an exponential relationship with temperature. For the curing reaction of encapsulating materials, as the temperature increases, the molecular activity increases, the reaction rate accelerates, and the curing time is shortened. For example, a certain epoxy resin encapsulating adhesive may take 24 hours to basically cure at room temperature (25°C), while under the heating condition of 60°C, it may only take 1 – 2 hours. However, too high a temperature may also bring negative impacts, such as causing stress concentration inside the material, generating bubbles, and deteriorating performance. When some encapsulating materials are cured at too high a temperature, the material will become brittle, reducing its mechanical properties and impact resistance.
- Humidity: The influence of humidity on the curing of encapsulating materials varies depending on the material type. For some moisture-sensitive encapsulating materials, such as some epoxy resin and polyurethane encapsulating materials, a high-humidity environment may interfere with the curing reaction. Moisture may react with the curing agent in a side reaction, consuming the curing agent and resulting in incomplete curing. In a high-humidity environment, the epoxy resin encapsulating adhesive may have problems such as insufficient hardness after curing and a sticky surface. Moisture may also form bubbles during the curing process of the encapsulating material, affecting the compactness and performance of the material. But for some silicone encapsulating materials, appropriate humidity can promote their curing reaction because their curing mechanism may involve a reaction with moisture.
- Type and Dosage of Curing Agent: Different types of curing agents have different activities and reaction mechanisms, which directly affect the curing speed and final performance of the encapsulating material. For example, aliphatic amine curing agents have a fast reaction speed and can make the encapsulating material cure quickly, but the cured product is relatively brittle; while anhydride curing agents have a relatively slow reaction speed, but the cured product has good heat resistance and electrical properties. The dosage of the curing agent is also crucial. Insufficient dosage will lead to incomplete curing, and the material performance cannot meet the expectations; excessive dosage may make the material brittle and also increase the cost. Generally, the product instruction manual of the encapsulating material will give the recommended dosage ratio of the curing agent, but in practical applications, fine-tuning is still required according to specific situations.
- Formulation of Encapsulating Material: The basic formulation of the encapsulating material, including the types and proportions of the resin, filler, additives, etc., has an important impact on the curing time and conditions. The addition of fillers can improve the physical properties of the encapsulating material, such as increasing hardness and reducing the shrinkage rate, but it may also affect the curing reaction rate. Some special additives, such as accelerators, can speed up the curing reaction, while inhibitors will delay the curing. Due to the slight differences in the formulations, the curing characteristics of the same type of encapsulating materials produced by different manufacturers may also vary.
Methods for Determining Curing Time and Conditions
- Experimental Testing Method
- Observing the Curing Process: This is the most intuitive method. Apply or encapsulate the encapsulating material on the test piece, and under different temperature and humidity conditions, regularly observe the state changes of the material, such as fluidity, surface dryness, and hardness changes. A hardness tester can be used to regularly measure the hardness of the material, and a curve of hardness changing with time can be drawn to determine the curing time under different conditions. For example, for a certain silicone encapsulating adhesive, in an environment of 25°C and a relative humidity of 50%, by measuring the hardness once every hour, it is found that its hardness begins to increase significantly after 3 hours and basically reaches a stable hardness after 12 hours. The curing time under this condition can be preliminarily determined.
- Using Testing Equipment: Professional equipment can be used to more accurately measure the curing time and reaction process. Differential scanning calorimetry (DSC) determines the starting, peak, and ending temperatures of the curing reaction, as well as the heat effect of the curing reaction, by measuring the heat change during the curing process, so as to calculate the curing time. Dynamic mechanical analysis (DMA) can measure the modulus change of the material during the curing process, reflecting the transformation process of the material from a liquid state to a solid state. For example, through DSC testing of a certain epoxy resin encapsulating material, it is found that when it is cured at 80°C, the starting temperature of the reaction is 60°C, the peak temperature is 75°C, the ending temperature of the reaction is 90°C, and the whole curing process takes about 2 hours.
- Referencing Product Instruction Manuals and Empirical Data: Manufacturers of encapsulating materials usually provide recommended ranges of curing time and conditions in the product instruction manuals. These data are obtained based on a large number of experiments and practical application experiences of the manufacturers and have important reference value. When using a new encapsulating material, preliminary experiments should first be carried out according to the suggestions in the instruction manual. Different industries and application scenarios have also accumulated rich empirical data. For example, in the electronics industry, for the common encapsulation of LED lights, the process of heating and curing at 60°C for 2 – 3 hours is usually adopted; while in the encapsulation of automotive electronic modules, different curing conditions may be selected according to the working environment and reliability requirements of the modules.
- Simulation Method: With the development of computer technology, it has become possible to use simulation software to predict the curing process of encapsulating materials. By establishing a mathematical model of the curing of the encapsulating material and inputting physical and chemical parameters of the material, environmental conditions, and other information, the software can simulate the temperature distribution, stress change, curing degree, etc. during the curing process. This is helpful for optimizing the curing process before actual production, reducing the number of experiments and costs. For example, when designing the encapsulation process of a large electronic device, the software can analyze the stress distribution inside the material under different curing conditions in advance through simulation to avoid damage to components or cracking of the encapsulation layer caused by curing stress.
Optimization and Adjustment in Practical Applications
- Considering Product Performance Requirements: When determining the curing time and conditions, the final performance requirements of the product must be taken as the guiding principle. If the product needs to work in a high-temperature environment for a long time, the curing conditions of the encapsulating material should ensure that it has good stability and performance at high temperatures. For the encapsulation of electronic components requiring high insulation performance, factors affecting the insulation performance should not be introduced during the curing process. For example, for the encapsulation of electronic equipment in the aerospace field, due to its complex working environment and extremely high requirements for the performance of the encapsulating material, such as resistance to high and low temperatures and radiation, great care is needed in the selection of the curing process, and it may be necessary to determine the optimal curing conditions through multiple experiments and optimizations.
- Balancing Production Efficiency and Cost: In industrial production, production efficiency and cost are also important considerations. Although increasing the curing temperature can shorten the curing time, it may require more investment in energy costs and also higher requirements for production equipment. Therefore, it is necessary to find a balance between curing time and cost on the premise of ensuring product quality. For example, in the mass production of electronic products, the curing process can be optimized by adopting a segmented curing method. First, pre-cure at a lower temperature to make the encapsulating material initially take shape, and then quickly cure at a higher temperature. This can not only ensure the curing quality but also improve production efficiency and reduce costs.
- Quality Control and Monitoring: In the actual production process, it is very necessary to establish a perfect quality control system and conduct real-time monitoring of the curing process of the encapsulating material. Online monitoring equipment, such as infrared sensors to monitor the temperature change during the curing process and pressure sensors to monitor the stress change during the curing process, can be used. Regularly conduct performance tests on the cured products, such as hardness tests, electrical performance tests, and mechanical performance tests, to ensure that the product quality meets the standards. Once an abnormality in the curing process is found or the product performance does not meet the requirements, the cause should be analyzed in a timely manner, and the curing time and conditions should be adjusted.
Determining the curing time and curing conditions of encapsulating materials is a comprehensive task. It is necessary to have an in-depth understanding of the curing principle of the encapsulating material, fully consider various influencing factors, and conduct experimental testing, reference empirical data, and simulation through scientific methods. In practical applications, optimization and adjustment should also be carried out according to product performance requirements, production efficiency, and cost, and at the same time, strengthen quality control and monitoring to ensure that the encapsulating material can play its best performance and meet the application requirements in different fields. With the continuous development of materials science and technology, the curing process of encapsulating materials in the future will be more accurate, efficient, and intelligent.
For more about choosing the top determination of curing parameters of encapsulating materials: from theory to practice, you can pay a visit to DeepMaterial at https://www.pottingcompound.com/ for more info.
Recent Posts
- Determination of Curing Parameters of Encapsulating Materials: From Theory to Practice
- How to Determine the Appropriate Encapsulation Thickness
- Influence of Encapsulation Thickness on the Heat Dissipation Performance and Electrical Insulation Performance of PCB
- Causes and Avoidance Methods of Bubble Generation in the Potting Process
- Technical Details on Controlling Parameters such as Temperature, Pressure, and Speed in the Potting Process to Ensure Potting Quality
- A Comprehensive Analysis of PCB Pretreatment Before Potting Process: A Crucial Link to Ensure the Performance and Reliability of Electronic Devices
- A Comprehensive Analysis of the Performance Differences of Epoxy Resin, Silicone Rubber and Polyurethane Encapsulation Materials
- How to Select Suitable Potting Materials for PCB According to the Working Environment
- What is PCB Potting
- The Evolution of Smart Watch Assembly Adhesive: A Key Component in Modern Wearable Technology