Industrial Conformal Coating
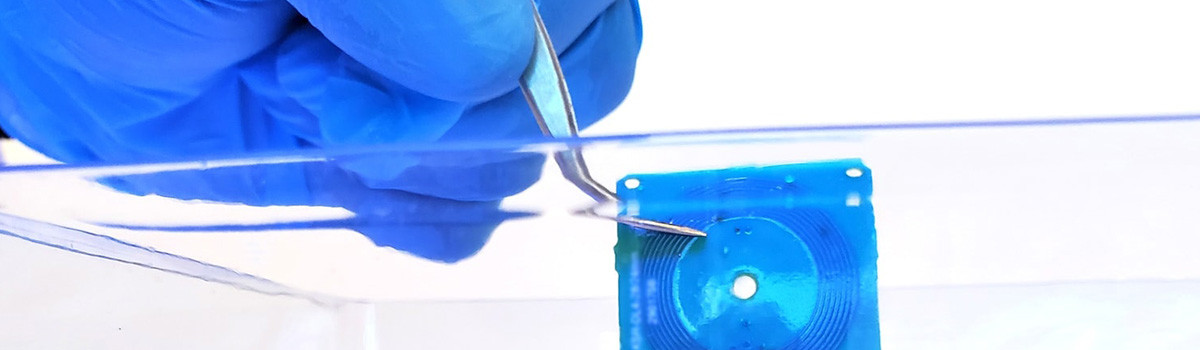
Industrial conformal coatings protect electronic components from environmental factors such as moisture, dust, chemicals, and temperature extremes. These coatings ensure the reliability and longevity of electronics in various industries, including aerospace, automotive, medical devices, and consumer electronics. They provide a protective barrier shielding sensitive circuitry from potential damage, enhancing product performance and lifespan. Understanding the diverse range of conformal coatings available and their applications is essential for industries reliant on electronic systems.
Table of Contents
ToggleFundamental Concepts You Ought to Understand:
What are industrial conformal coatings?
Industrial conformal coatings are specialized protective coatings applied to electronic circuit boards and components to safeguard them against environmental factors such as moisture, dust, chemicals, and temperature extremes. These coatings conform to the contours of the components, providing a uniform protective layer that helps prevent corrosion, electrical short circuits, and other forms of damage.
Typically, these coatings are applied through various methods, including spraying, dipping, brushing, or selective coating, depending on the specific application requirements and the type of coating being used. Standard conformal coatings include acrylics, silicones, urethanes, and epoxies, each offering unique properties such as flexibility, chemical resistance, and temperature stability.
One of the primary purposes of conformal coatings is to enhance the reliability and longevity of electronic devices, particularly in harsh operating environments such as automotive, aerospace, marine, and industrial settings. By protecting the circuitry from moisture and contaminants, conformal coatings help to reduce the risk of electrical failures and ensure consistent performance over time.
Moreover, conformal coatings can also provide insulation properties, helping to prevent electrical leakage and shorts that can occur due to moisture or conductive contaminants. This is especially crucial in applications where reliability is paramount, such as medical devices, military equipment, and telecommunications infrastructure.
In addition to their protective functions, conformal coatings can offer other benefits, such as improved thermal management, vibration dampening, and enhanced resistance to mechanical stress. This makes them invaluable for applications where electronic components are subjected to demanding operating conditions.
Overall, industrial conformal coatings are vital in extending the lifespan and reliability of electronic devices and circuitry, allowing them to perform effectively even in challenging environments. As technology advances and electronic devices become increasingly pervasive, the demand for high-performance conformal coatings is expected to grow, driving further innovation in this field.
How do conformal coatings protect electronic components?
Conformal coatings are a crucial protective layer for electronic components, safeguarding them against various environmental hazards and ensuring their reliability and longevity. These coatings are typically thin films of material applied directly onto the surface of electronic assemblies, conforming to the contours of the components. Here’s how they provide protection:
- Environmental Protection: Conformal coatings shield electronic components from environmental stresses, including moisture, dust, dirt, chemicals, and temperature fluctuations. Creating a barrier between the sensitive electronic circuitry and the external environment prevents corrosion, short circuits, and other damage that could occur due to exposure.
- Insulation: Many conformal coatings have excellent insulating properties, which help avoid electrical leakage and short circuits caused by the buildup of moisture or contaminants. This insulation is essential in harsh or humid environments with a higher risk of electrical arcing.
- Mechanical Protection: Besides environmental factors, electronic components can also be susceptible to physical damage from vibration, shock, or mechanical stress. Conformal coatings provide a protective layer that absorbs some of this mechanical energy, reducing the risk of damage to delicate components.
- Chemical Resistance: Certain conformal coatings are formulated to resist chemical exposure, making them ideal for applications where electronic assemblies may come into contact with solvents, oils, or other corrosive substances. This resistance helps maintain the integrity of the components and prevents degradation over time.
- UV Protection: Some conformal coatings offer UV-resistant properties that are significant for outdoor or high-exposure applications. These coatings prevent the degradation of sensitive materials due to prolonged exposure to ultraviolet radiation from the sun.
- Ease of Application: Conformal coatings are typically applied using methods such as spraying, dipping, or brushing, allowing for uniform coverage even on complex or irregularly shaped components. This ease of application ensures that all areas requiring protection are adequately covered.
Conformal coatings play a vital role in protecting electronic components by providing insulation, environmental resistance, mechanical protection, chemical resistance, UV protection, and ease of application. By effectively sealing and safeguarding electronic assemblies, these coatings contribute to electronic devices’ reliability, durability, and performance across various industries.
What are the common types of conformal coatings?
Conformal coatings are essential protective layers applied to electronic components to safeguard them against environmental factors such as moisture, dust, chemicals, and temperature extremes. There are several common types of conformal coatings, each with distinct properties and suitable applications:
- Acrylic Conformal Coatings: Acrylic coatings are popular due to their easy application, fast curing times, and excellent moisture resistance. They provide good electrical insulation and withstand a wide range of temperatures. Acrylic coatings are commonly used in consumer electronics, automotive, and industrial applications.
- Silicone Conformal Coatings: Silicone coatings offer outstanding flexibility, durability, and high-temperature resistance. They maintain their properties over a wide temperature range and protect against moisture, chemicals, and UV radiation. Silicone coatings are suitable for harsh environments such as aerospace, automotive, and marine applications.
- Urethane Conformal Coatings: Urethane coatings provide superior chemical resistance and mechanical protection. They offer good moisture resistance and withstand abrasion and environmental stresses. Urethane coatings, such as military and aerospace electronics, are often chosen for enhanced durability applications.
- Epoxy Conformal Coatings: Epoxy coatings offer excellent adhesion to various substrates and provide exceptional protection against moisture and chemicals. They have high dielectric strength and offer good resistance to temperature extremes. Epoxy coatings are commonly used in industrial, automotive, and marine applications.
- Parylene Conformal Coatings: Parylene coatings are vaporized and offer uniform, pinhole-free coverage. They protect against moisture, chemicals, and temperature extremes while maintaining optical clarity and flexibility. Parylene coatings find applications in medical devices, aerospace electronics, and telecommunications.
- Polyurethane Conformal Coatings: Polyurethane coatings combine the properties of urethane and acrylic coatings, offering good moisture resistance, flexibility, and chemical resistance. They provide reliable protection for electronics in demanding environments such as automotive, marine, and outdoor applications.
Choosing the suitable conformal coating depends on specific application requirements, environmental conditions, desired performance characteristics, and manufacturing processes. Manufacturers often conduct testing to ensure compatibility and effectiveness before selecting a conformal coating for their electronic components.
What are the primary functions of conformal coatings?
Conformal coatings protect electronic components and assemblies from various environmental stressors, ensuring reliability and longevity. These coatings are typically thin films applied onto the surface of printed circuit boards (PCBs) and other electronic devices. Their primary functions can be summarized as follows:
- Environmental Protection: Conformal coatings create a barrier between sensitive electronic components and potentially harmful environmental elements such as moisture, dust, chemicals, and contaminants. By sealing off the surface, they prevent corrosion, oxidation, and other forms of damage that can compromise the functionality of the electronics.
- Insulation: They provide electrical insulation, safeguarding against short circuits and other electrical failures caused by moisture ingress or the presence of conductive debris. This insulation is essential in high-humidity or harsh operating environments where moisture can lead to conductivity and electrical leakage.
- Mechanical Protection: Conformal coatings offer mechanical protection against physical damage, including abrasion, vibration, and shock. Forming a durable yet flexible layer over the electronic components, they help mitigate the risks of mechanical stresses encountered during handling, transportation, and operation.
- Enhanced Dielectric Strength: Many conformal coatings possess high dielectric strength, improving electronic assemblies’ overall reliability and performance by reducing the risk of electrical breakdown or arcing between closely spaced conductors.
- Thermal Management: Some coatings are formulated to dissipate heat effectively, enhancing thermal management within electronic devices. By promoting heat transfer away from critical components, they prevent overheating and subsequent performance degradation or failure.
- UV Protection: Certain conformal coatings offer UV protection, shielding sensitive components from the damaging effects of ultraviolet radiation. This is particularly beneficial for outdoor or exposed applications where prolonged exposure to sunlight can lead to material degradation and performance issues.
- Chemical Resistance: They resist a wide range of chemicals, including solvents, oils, and fuels, thereby extending the operational lifespan of electronic devices used in environments where exposure to such substances is daily.
Conformal coatings serve as a vital protective layer for electronic components and assemblies. They offer a combination of environmental, electrical, mechanical, thermal, and chemical protection to ensure the reliable operation of electronic devices in diverse applications and operating conditions.
How do conformal coatings improve the reliability of electronic devices?
Conformal coatings play a critical role in enhancing the reliability of electronic devices by protecting various environmental factors and mechanical stressors. These coatings are typically thin films of polymeric materials applied directly onto the electronic components, forming a conformal layer that closely follows the contours of the substrate. Here’s how conformal coatings contribute to improved reliability:
- Protection Against Environmental Factors: Conformal coatings act as barriers against moisture, dust, chemicals, and other contaminants that could compromise the functionality of electronic devices. For instance, moisture can lead to metal contact corrosion, short circuits, and electrical leakage. Conformal coatings prevent moisture ingress by encapsulating the components, thereby extending the device’s lifespan.
- Insulation: In electronic devices, components are often densely packed, increasing the risk of short circuits due to accidental contact between conductive elements. Conformal coatings provide electrical insulation, preventing unintended connections and reducing the likelihood of electrical failures.
- Thermal Management: Many conformal coatings offer excellent thermal conductivity of insulation properties. Proper thermal management is crucial for electronic devices to maintain optimal operating temperatures and prevent overheating, which can degrade performance and reduce lifespan. Conformal coatings with tailored thermal properties can help dissipate heat effectively or insulate sensitive components from excessive thermal stress.
- Mechanical Protection: Electronic devices may experience mechanical stresses during handling, assembly, or operation. Conformal coatings provide a protective layer that absorbs mechanical shocks, vibrations, and impacts, reducing the risk of physical damage to delicate components such as solder joints, traces, and microchips. This mechanical resilience enhances the robustness and durability of the device, especially in harsh operating environments.
- Corrosion Resistance: Conformal coatings can offer corrosion-resistant properties, shielding electronic components from oxidation and other forms of chemical degradation. This is particularly beneficial in applications where devices are exposed to corrosive agents such as salt spray, sulfur compounds, or industrial pollutants.
Conformal coatings are multifunctional protective layers that safeguard electronic devices against environmental, electrical, thermal, and mechanical threats. By enhancing reliability and durability, these coatings contribute to the longevity and performance of electronic systems in multiple applications.
What factors should be considered when selecting a conformal coating?
Selecting the appropriate conformal coating for electronic devices involves considering several critical factors to ensure optimal performance, reliability, and compatibility with specific application requirements. Here are key considerations:
- Environmental Conditions: Evaluate the operating environment where the electronic device will be deployed. Factors such as temperature extremes, humidity levels, exposure to chemicals, and potential abrasion or mechanical stressors should influence the choice of conformal coating. For example, outdoor devices may require coatings with enhanced UV resistance, while those deployed in harsh industrial environments might need superior chemical resistance.
- Electrical Properties: Consider the electrical characteristics of the conformal coating, such as dielectric strength, insulation resistance, and surface resistivity. These properties are crucial for preventing electrical leakage, short circuits, and signal interference within the device. Ensure the coating material maintains the desired electrical performance across the operating temperature range.
- Application Method: Different conformal coatings may require specific application methods such as spraying, dipping, brushing, or selective coating. When selecting the application method, consider the complexity of the device’s geometry, production volume, and desired coating thickness. Additionally, compatibility with existing manufacturing processes and equipment should be assessed to streamline production.
- Material Compatibility: Assess compatibility between the conformal coating material and the substrate materials used in the electronic device, including printed circuit boards (PCBs), components, solder joints, and encapsulants. Incompatibility can lead to adhesion issues, delamination, or chemical reactions compromising reliability. Conduct compatibility testing to verify the suitability of the coating for all materials involved.
- Conformal Coating Properties: Evaluate specific properties of the conformal coating, such as flexibility, hardness, adhesion strength, and thermal conductivity. The coating should withstand thermal cycling, mechanical stress, and vibrations without cracking or delaminating. Additionally, ensure that the coating material meets relevant industry standards and regulatory requirements for safety, reliability, and environmental compliance.
- Serviceability and Reworkability: Consider whether the conformal coating allows for easy rework or repair in case of component replacement or troubleshooting. Some coatings may require specialized removal techniques, while others can be easily reworked using common solvents or mechanical methods.
By carefully considering these factors, engineers can select the most suitable conformal coating that meets the unique requirements of their electronic devices, ensuring long-term reliability and performance in diverse applications.
What are the application methods for industrial conformal coatings?
Industrial conformal coatings are applied to electronic components and assemblies to protect them from environmental factors such as moisture, dust, chemicals, and temperature extremes. These coatings enhance the reliability and lifespan of electronic devices in harsh operating conditions. Several application methods are employed in industrial settings to ensure efficient and effective coating deposition:
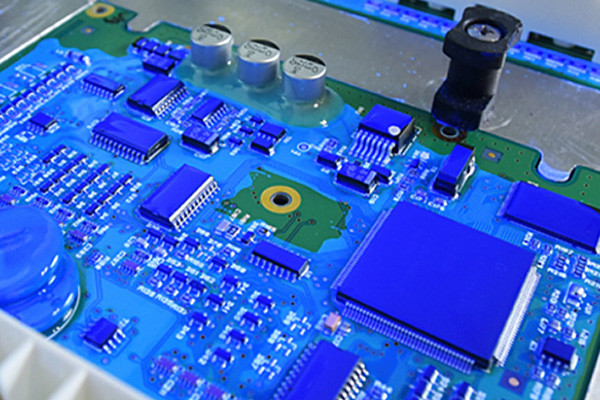
- Dipping: In this method, electronic assemblies are immersed in a bath of liquid conformal coating material. The components are withdrawn at a controlled rate to ensure uniform coverage. Dipping is suitable for high-volume production and provides complete coverage even in complex geometries.
- Spraying: Conformal coatings can be applied using automated spray equipment. This method atomizes the coating material into fine droplets, which are then directed onto the surfaces of the components. Spraying offers versatility in coating thickness and coverage and is suitable for batch and continuous processing.
- Brushing: Manual or automated brushing involves applying conformal coating material onto the surfaces using brushes or applicators. This method is ideal for selective coating specific areas or touch-up applications requiring precision and control.
- Selective Coating: Selective coating systems use precision dispensing equipment to apply conformal coatings only to predetermined regions of the electronic assembly. This method offers high accuracy and is often used for masking delicate components or connectors that should remain uncoated.
- Vapor Deposition: In vapor deposition methods such as chemical vapor deposition (CVD) or physical vapor deposition (PVD), conformal coating materials are vaporized and deposited onto the surfaces of electronic components under controlled vacuum conditions. Vapor deposition techniques ensure uniform coverage and precise control over coating thickness.
- Film Lamination: Some conformal coatings are available as pre-cut films or sheets. These films are applied to the surfaces of electronic assemblies using heat and pressure to bond them securely. Film lamination offers quick and clean application without liquid coatings or solvents.
Each of these application methods has advantages and is selected based on factors such as production volume, complexity of the components, coating material properties, and desired coating thickness. By employing the appropriate application method, industrial manufacturers can ensure consistent and reliable protection for their electronic devices.
How do environmental factors affect the choice of conformal coatings?
Environmental factors play a crucial role in determining the suitability of conformal coatings for electronic components. Conformal coatings protect electronic assemblies from ecological stresses like moisture, dust, chemicals, and temperature fluctuations. The choice of conformal coating depends on the specific environmental conditions the electronics will encounter during their lifecycle.
Moisture is one of the most common environmental factors that can lead to corrosion and electrical failures in electronic components. In humid environments or applications where exposure to water is likely, it’s essential to select conformal coatings with high moisture resistance properties, such as silicone or acrylic coatings. These coatings form a barrier that prevents moisture ingress and protects sensitive electronic circuitry.
Temperature extremes can also impact the performance of conformal coatings. In high-temperature environments, coatings must withstand elevated temperatures without degrading or losing their protective properties. Silicone-based coatings are known for their excellent heat resistance, making them suitable for applications exposed to high temperatures, such as automotive under-the-hood electronics or aerospace components. Conversely, coatings must remain flexible and durable in cryogenic applications where temperatures drop significantly to prevent cracking or delamination. Polyurethane coatings are often chosen for their ability to maintain flexibility at low temperatures.
Chemical exposure is another critical consideration in specific environments, such as industrial settings or areas with high pollution levels. Conformal coatings may come into contact with solvents, oils, fuels, or cleaning agents, which can degrade certain coatings. In such cases, selecting chemically resistant coatings like epoxy or perylene can effectively protect against chemical attack.
Furthermore, UV exposure from sunlight can degrade conformal coatings over time, leading to loss of protection and discoloration of electronic components. Typically based on acrylic or urethane chemistries, UV-resistant coatings are recommended for outdoor or applications exposed to direct sunlight.
The choice of conformal coating is heavily influenced by the specific environmental conditions the electronic components will encounter. Understanding the impact of moisture, temperature, chemicals, and UV exposure is essential for selecting the most suitable coating to ensure electronic assemblies’ long-term reliability and performance.
What are the critical differences between acrylic and silicone conformal coatings?
Acrylic and silicone conformal coatings are widely used in electronics manufacturing to protect boards (PCBs) from environmental factors such as moisture, dust, chemicals, and temperature fluctuations. However, they have distinct properties that make them suitable for different applications.
- Chemical Composition: Acrylic conformal coatings are typically made from acrylic resins, which offer good electrical insulation and protection against humidity. On the other hand, silicone conformal coatings are based on silicone polymers, which provide superior resistance to extreme temperatures, chemicals, and UV radiation.
- Physical Properties: Acrylic coatings tend to have a more complex, rigid film once cured, offering excellent abrasion resistance and mechanical protection. Silicone coatings, in contrast, are softer and more flexible, making them ideal for applications where thermal expansion and contraction are significant concerns.
- Temperature Resistance: Silicone conformal coatings excel in high-temperature environments, maintaining their properties and integrity even at temperatures exceeding 200°C. Acrylic coatings have lower thermal resistance, typically withstanding temperatures around 125-150°C before degradation occurs.
- Chemical Resistance: Silicone coatings offer superior resistance to various chemicals, including solvents, acids, and bases, making them suitable for harsh industrial environments. Acrylic coatings provide good resistance to moisture and some chemicals but may not perform as well in highly corrosive or chemically aggressive environments.
- Adhesion: Acrylic conformal coatings generally exhibit better adhesion to various substrates, including metals, plastics, and ceramics. Silicone coatings may require primers or surface treatments to ensure adequate adhesion, particularly on difficult-to-bond substrates.
- Dielectric Properties: Both acrylic and silicone conformal coatings offer excellent electrical insulation properties. However, acrylic coatings typically have higher dielectric strength and lower dielectric constant than silicone coatings.
The choice between acrylic and silicone conformal coatings depends on the application’s specific requirements. Acrylic coatings are preferred for their hardness, adhesion, and cost-effectiveness in less demanding environments. In contrast, in harsh conditions, silicone coatings are favored for their flexibility, temperature resistance, and chemical resilience.
How do UV-curable conformal coatings differ from traditional coatings?
UV-curable conformal coatings differ significantly from traditional coatings in several vital aspects, offering unique advantages in various applications. Traditional conformal coatings, typically solvent-based, rely on chemical reactions or physical evaporation to cure and form a protective layer over electronic components. In contrast, UV-curable coatings undergo rapid polymerization upon exposure to ultraviolet (UV) light, providing distinct benefits:
- Curing Time: UV-curable coatings offer speedy curing times compared to traditional coatings. While traditional coatings may require hours or even days to cure fully, UV-curable coatings cure almost instantly upon exposure to UV light, reducing production time and increasing throughput.
- Energy Efficiency: UV-curable coatings require less energy for curing since the curing process is initiated by UV light rather than heat. This energy-efficient curing process leads to lower energy consumption and reduced operating costs, making UV-curable coatings environmentally friendly and cost-effective.
- Controlled Application: UV-curable coatings provide precise control over the curing process. As the curing reaction occurs rapidly upon exposure to UV light, manufacturers can achieve consistent coating thickness and uniform coverage, ensuring reliable protection for electronic components.
- Chemical Resistance: UV-curable coatings often exhibit superior chemical resistance compared to traditional coatings. The rapid polymerization process creates a densely cross-linked network, making coatings more resistant to chemicals, solvents, and environmental stresses.
- Environmental Impact: UV-curable coatings contain fewer volatile organic compounds (VOCs) than solvent-based traditional coatings, reducing harmful emissions and minimizing environmental impact. Additionally, UV-curable coatings eliminate the need for solvent recovery systems, further reducing waste and pollution.
- Versatility: UV-curable coatings offer versatility in application and are suitable for various substrates, including plastics, metals, and ceramics. Their rapid curing properties make them ideal for high-speed production processes, such as electronics manufacturing, where quick turnaround times are crucial.
UV-curable conformal coatings provide numerous advantages over traditional coatings, including faster curing times, energy efficiency, controlled application, enhanced chemical resistance, reduced environmental impact, and versatility. These advantages make them a preferred choice for many electronic and industrial applications.
What role do conformal coatings play in preventing corrosion?
Conformal coatings are critical in preventing corrosion, particularly in electronic components and assemblies where exposure to moisture, chemicals, and environmental contaminants can lead to degradation over time. These coatings act as protective barriers, shielding sensitive circuitry and components from the harmful effects of corrosion.
One primary role of conformal coatings is to create a barrier against moisture ingress. Moisture is one of the leading causes of corrosion, especially in electronic devices, which cause short circuits, oxidation of metal contacts, and degradation of insulation materials. Conformal coatings, typically made from acrylics, silicones, or polyurethanes, form a thin, uniform layer over the electronic assembly, sealing it from moisture and preventing its penetration into vulnerable areas.
Moreover, conformal coatings provide insulation against other environmental contaminants such as dust, dirt, salt spray, and chemicals. These contaminants can accelerate corrosion by promoting oxidation or causing chemical reactions with the metal surfaces. Covering the components with a conformal coating minimizes exposure to these corrosive agents, thus extending the lifespan of the electronic device.
Another essential function of conformal coatings is to provide mechanical protection to the components. They act as shock absorbers, reducing the impact of physical stresses and vibrations on delicate electronic parts. This mechanical protection not only prevents physical damage but also helps maintain the integrity of the coating itself, ensuring continued corrosion resistance over time.
Furthermore, conformal coatings can enhance thermal conductivity or insulation, depending on the specific requirements of the electronic assembly. By optimizing heat dissipation or insulation, these coatings contribute to the overall reliability and performance of the device while still providing corrosion protection.
Conformal coatings prevent corrosion by forming protective barriers against moisture, chemicals, and environmental contaminants. They provide insulation and mechanical protection and can improve thermal properties, ultimately ensuring the reliability and longevity of electronic components and assemblies in challenging operating environments.
Can conformal coatings withstand high temperatures?
Conformal coatings are specially formulated materials that protect electronic circuits and components from environmental factors such as moisture, dust, chemicals, and temperature extremes. While many conformal coatings offer excellent protection against various environmental conditions, their ability to withstand high temperatures depends on the specific formulation and intended application.
Several types of conformal coatings are designed to withstand high temperatures:
- Silicone-based coatings: Silicone conformal coatings are known for their wide temperature range, typically from -50°C to 200°C or even higher, depending on the formulation. They offer excellent flexibility and resistance to high temperatures, making them suitable for applications where thermal cycling or exposure to elevated temperatures is expected.
- Polyurethane coatings: Some conformal coatings can withstand temperatures up to 150°C or more. They provide good chemical resistance and mechanical protection while maintaining electrical insulation properties.
- Fluoropolymer coatings: Fluoropolymer-based conformal coatings, such as PTFE (polytetrafluoroethylene), offer exceptional thermal stability and withstand temperatures ranging from -200°C to 260°C. These coatings provide excellent chemical resistance, low friction properties, and high-temperature tolerance.
- Epoxy coatings: Epoxy conformal coatings typically have a lower maximum temperature resistance than silicone or fluoropolymer coatings, usually up to around 130°C. However, some specially formulated epoxy coatings can withstand temperatures up to 200°C with proper curing.
It’s important to note that while conformal coatings may withstand high temperatures, their performance can be influenced by factors such as the duration of exposure, temperature cycling, substrate material, and other environmental stresses. Additionally, the application method and thickness of the coating can also affect its thermal resistance.
While many conformal coatings offer good resistance to high temperatures, it’s crucial to select the appropriate type based on the application’s specific temperature requirements and to consider other factors that may impact performance over time.
Are there eco-friendly options available in conformal coatings?
Conformal coatings protect electronic components from environmental factors such as moisture, dust, chemicals, and temperature variations. As environmental consciousness grows, there is an increasing demand for eco-friendly options in conformal coatings. Several eco-friendly alternatives have emerged in response to this demand, offering adequate protection while minimizing environmental impact.
One eco-friendly option is water-based conformal coatings. Traditional solvent-based coatings use water as the primary solvent instead of volatile organic compounds (VOCs). By replacing VOCs with water, these coatings significantly reduce harmful emissions during application and curing processes, lowering environmental impact and improving workplace safety.
Another eco-friendly alternative is UV-curable conformal coatings. These coatings utilize ultraviolet (UV) light instead of heat for curing, eliminating the need for energy-intensive curing processes. UV-curable coatings contain fewer volatile organic compounds than solvent-based coatings, further reducing environmental harm. Additionally, UV curing enables faster processing times, reducing overall energy consumption and enhancing production efficiency.
Bio-based conformal coatings represent another environmentally friendly option. These coatings utilize renewable resources such as plant-based oils or biodegradable polymers as primary ingredients. By reducing reliance on fossil fuels and non-renewable resources, bio-based coatings contribute to sustainability efforts and help minimize carbon footprint.
Furthermore, some manufacturers are exploring innovative approaches, such as recyclable conformal coatings. These coatings are designed to be easily removed and recycled, reducing waste generation and promoting circular economy principles. Companies can minimize environmental impact by implementing closed-loop systems for coating application and removal while optimizing resource utilization.
Eco-friendly options in conformal coatings offer adequate protection for electronic components while minimizing environmental harm. Water-based, UV-curable, bio-based, and recyclable coatings are among the sustainable alternatives gaining traction in the industry. Embracing these eco-friendly solutions enhances ecological stewardship and aligns with the growing sustainability initiatives across various sectors.
How do you ensure proper adhesion of conformal coatings?
Proper adhesion of conformal coatings is crucial for ensuring adequate protection of electronic components against environmental factors. Several factors contribute to achieving adequate adhesion, and implementing proper techniques is essential for optimizing coating performance and reliability.
Surface preparation is paramount in ensuring proper adhesion of conformal coatings. Before application, the substrate must be thoroughly cleaned to remove contaminants such as dust, grease, oils, and residues from previous processes. Methods such as solvent cleaning, plasma treatment, or mechanical abrasion may achieve a clean and properly prepared surface. Surface roughening techniques, such as sandblasting or chemical etching, can also enhance adhesion by promoting mechanical interlocking between the coating and the substrate.
Additionally, promoting surface wettability is crucial for enhancing adhesion. Proper surface activation techniques, such as plasma treatment or corona discharge, can improve the substrate’s surface energy, allowing the coating to spread evenly and form strong bonds. Proper control of application parameters, including temperature, humidity, and coating thickness, is also essential for optimizing adhesion. Manufacturers should adhere to recommended curing conditions specified by the coating manufacturer to ensure proper cross-linking and adhesion.
Furthermore, selecting the appropriate conformal coating material is critical for achieving good adhesion. Compatibility between the coating and substrate materials is essential to prevent delamination or adhesion failure. Conducting compatibility tests and trials with different coating formulations and substrate materials can help identify the most suitable option for specific applications.
Regular quality control measures, such as cross-hatch or tape testing, should be implemented to assess coating adhesion throughout production. These tests help ensure that coatings adhere correctly to the substrate and meet required standards for reliability and performance.
Ensuring proper adhesion of conformal coatings involves meticulous surface preparation, promoting surface wettability, selecting compatible materials, and implementing appropriate application and curing techniques. By following these best practices, manufacturers can enhance the adhesion of conformal coatings, thereby improving the protection and reliability of electronic components in various applications.
What are the challenges associated with removing conformal coatings?
Conformal coatings protect electronic components from environmental factors like moisture, dust, chemicals, and temperature fluctuations. However, removing them can present several challenges, primarily due to their resilience and the need to ensure the integrity of delicate components. Here are the critical challenges associated with removing conformal coatings:
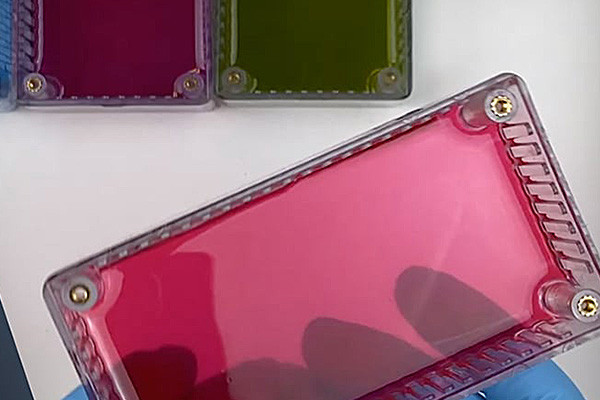
- Adhesion Strength: Conformal coatings are designed to adhere firmly to the surface they protect. This strong adhesion makes their removal difficult without damaging the underlying components. Traditional removal methods, such as scraping or abrasion, can risk harming sensitive electronics.
- Compatibility: Many conformal coatings are formulated to withstand harsh conditions, including exposure to various chemicals and solvents. A significant challenge is finding a solvent that effectively softens or dissolves the coating without damaging the substrate material or other components.
- Selectivity: Conformal coatings must be selectively removed without affecting adjacent components or materials. Achieving this selectivity requires precise control over the removal process, often demanding specialized equipment or techniques.
- Residue Management: Even after successful removal, residues from the coating or the removal agent may remain on the surface. These residues can interfere with subsequent processes or compromise the performance of the electronics. Proper cleaning and residue management are essential but can complicate the removal process.
- Environmental Considerations: Many conventional removal methods involve harsh chemicals or mechanical processes that pose environmental and health risks. Developing environmentally friendly removal techniques that meet regulatory standards without sacrificing effectiveness is an ongoing challenge.
- Time and Cost: Removing conformal coatings can be time-consuming and labor-intensive, particularly for complex electronic assemblies with intricate designs. Minimizing downtime and associated costs while ensuring thorough and safe removal adds another layer of difficulty.
Addressing these challenges often requires a combination of specialized equipment, expertise, and careful planning. Research and innovation in removal techniques, materials, and equipment continue to advance, aiming to streamline the process and minimize risks to electronic components and the environment.
Are there conformal coatings suitable for flexible substrates?
Yes, there are conformal coatings designed explicitly for flexible substrates. These coatings offer protection and insulation while accommodating the bending and flexing of the underlying material.
Flexible substrates, such as those found in wearable electronics, flexible displays, and flexible printed circuit boards (PCBs), require conformal coatings that adhere well to the surface without cracking or delamination during repeated bending cycles. Traditional conformal coatings, like acrylics, urethanes, and silicones, may not be suitable for flexible substrates due to their rigid nature.
However, specialized coatings have been developed to meet the unique requirements of flexible substrates. These coatings are typically formulated using elastomeric materials such as silicone elastomers or flexible epoxy resins.
Silicone elastomers offer excellent flexibility and conformability, making them well-suited for flexible substrates. They can withstand repeated bending without cracking or losing adhesion to the substrate. Silicone coatings also provide good resistance to moisture, chemicals, and temperature extremes, further enhancing the durability of flexible electronic devices.
Flexible epoxy resins, on the other hand, offer a balance between flexibility and adhesion strength. They can be tailored to match the specific mechanical and electrical properties required for the application. Flexible epoxy coatings provide robust protection against environmental factors while maintaining compatibility with the flexible substrate.
In addition to their mechanical properties, conformal coatings for flexible substrates must also consider factors such as thickness control, curing mechanisms, and compatibility with manufacturing processes like roll-to-roll coating or screen printing.
Conformal coatings suitable for flexible substrates play a crucial role in protecting electronic components from environmental hazards while maintaining the integrity of the flexible substrate. Their development continues to evolve as the demand for flexible electronics grows in various industries, including consumer electronics, healthcare, and automotive applications.
What considerations are essential for conformal coatings in aerospace applications?
Conformal coatings play a critical role in aerospace applications, protecting environmental factors like moisture, chemicals, temperature variations, and mechanical stress. Several considerations are essential for selecting and applying conformal coatings in aerospace:
- Environmental Durability: Aerospace components are subjected to extreme conditions, including high altitudes, temperature variations, and pressure changes. Conformal coatings must withstand these conditions without degrading or losing effectiveness.
- Chemical Resistance: Aerospace environments often expose components to various chemicals, such as fuels, hydraulic fluids, and cleaning agents. Conformal coatings should resist corrosion and chemical attack to maintain the integrity of the coated surfaces.
- Temperature Stability: Aerospace systems experience wide temperature ranges, from cold in high altitudes to extreme heat during re-entry. Conformal coatings must maintain their properties across these temperatures to provide consistent protection.
- Mechanical Protection: Components in aerospace applications are subject to vibration, shock, and mechanical stress during operation and transportation. Conformal coatings should provide a protective barrier to prevent damage from these mechanical forces.
- Adhesion: Proper adhesion is crucial to ensure the conformal coating remains securely bonded to the substrate. Poor adhesion can lead to delamination or peeling, compromising the effectiveness of the coating.
- Thickness Control: The thickness of the conformal coating is critical to its performance. Too thin a coating may not provide adequate protection, while excessive thickness can lead to issues such as cracking or interference with component tolerances.
- Electrical Properties: Some aerospace components require electrical insulation or conductivity. Conformal coatings should be selected or formulated to meet specific electrical requirements without interfering with signal transmission or generating unwanted electrical effects.
- Regulatory Compliance: Aerospace coatings must comply with industry standards and regulations, such as those set by organizations like the Federal Aviation Administration (FAA) or the European Aviation Safety Agency (EASA).
- Application Method: The method of applying conformal coatings can impact their effectiveness and uniformity. Factors such as spray application, dip coating, or brush application should be considered based on the specific requirements of the aerospace component and the coating material.
- Maintenance and Repair: Conformal coatings should be designed for easy maintenance and repair, allowing for rework or recoating of components without compromising performance or safety.
By carefully considering these factors, aerospace engineers can select and apply conformal coatings that meet the stringent requirements of aerospace applications, ensuring the long-term reliability and performance of critical components and systems.
How do you assess the thickness of conformal coatings?
Assessing the thickness of conformal coatings is crucial in ensuring the integrity and effectiveness of the coating application, especially in industries like electronics, where conformal coatings protect circuitry from environmental factors. Several methods are employed for thickness assessment, each with advantages and limitations.
- Mil Thickness Gauge: This is a commonly used tool for measuring the thickness of conformal coatings. It employs a magnetic or eddy current principle to measure the distance between the probe and the substrate. However, it requires a flat surface and may not be suitable for complex geometries.
- Ultrasonic Measurement: Ultrasonic thickness gauges use sound waves to measure coating thickness. They are versatile and can measure coatings on irregular surfaces. However, accuracy can be affected by material properties and surface roughness.
- Cross-Sectional Analysis: This involves cutting a sample and examining it under a microscope. The thickness is measured directly from the cross-section. While highly accurate, this method is destructive and time-consuming.
- Optical Profilometry: Optical profilometers use light interference to measure coating thickness. They provide non-contact measurements and are suitable for transparent coatings. However, surface roughness can affect accuracy.
- X-ray Fluorescence (XRF): XRF can determine coating thickness by analyzing the intensity of X-rays reflected from different layers. It’s non-destructive and suitable for metallic coatings but may require calibration for accuracy.
- Eddy Current Measurement: Eddy current techniques measure changes in electrical conductivity induced by the coating’s presence. They are non-destructive and can be measured on non-conductive substrates, but coating composition may influence accuracy.
- Calibrated Weighing: This method involves weighing the substrate before and after the coating application. The difference in weight is used to calculate coating thickness. It’s simple but needs to be more accurate, particularly for thin coatings.
Selecting the appropriate method for assessing conformal coating thickness depends on substrate material, coating type, accuracy requirements, and budget constraints. A combination of techniques may often be employed to ensure comprehensive assessment and quality control.
What are the regulatory standards governing conformal coatings?
Conformal coatings protect electronic components from environmental factors such as moisture, dust, chemicals, and temperature extremes. Regulatory standards governing conformal coatings primarily focus on ensuring product safety, environmental sustainability, and performance reliability. These standards vary across regions, but several vital regulations are widely recognized:
- RoHS (Restriction of Hazardous Substances): RoHS directives restrict the use of certain hazardous materials in electrical and electronic products, including lead, mercury, cadmium, and various flame retardants. Conformal coatings must comply with RoHS to ensure they do not contain prohibited substances.
- REACH (Registration, Evaluation, Authorization, and Restriction of Chemicals): REACH regulations aim to protect human health and the environment from the risks associated with chemical substances. Conformal coatings must comply with REACH requirements by registering and ensuring the safe use of chemicals in their formulations.
- IPC (Association Connecting Electronics Industries): IPC standards provide guidelines for designing, manufacturing, and testing electronic assemblies. IPC-A-610 outlines acceptance criteria for electronic assemblies, including conformal coating requirements such as thickness, coverage, and insulation resistance.
- UL (Underwriters Laboratories): UL standards focus on product safety and performance. Conformal coatings must meet UL requirements for flammability, electrical insulation, and environmental resistance to obtain UL certification.
- ISO (International Organization for Standardization): ISO standards cover various aspects of quality management, including environmental management (ISO 14000 series) and quality management (ISO 9000 series). Conformal coating manufacturers may adhere to ISO standards to ensure consistent product quality and environmental responsibility.
- Mil-Spec (Military Specifications): Military specifications define requirements for materials, components, and systems used in military applications. To withstand harsh operating conditions, conformal coatings may need to meet specific Mil-Spec standards, such as MIL-I-46058 or MIL-STD-810.
Adherence to these regulatory standards ensures that conformal coatings are safe, environmentally friendly, and reliable for use in electronic applications. This contributes to electronic devices’ overall quality and longevity. Compliance fosters trust between manufacturers, suppliers, and end-users, promoting a sustainable and responsible electronics industry.
How do you troubleshoot issues with conformal coating applications?
Troubleshooting issues with conformal coating applications involves a systematic approach to identify and address various potential problems. Here’s a concise guide:
- Inspect Coating Quality: Begin by visually inspecting the coated surface for irregularities such as bubbles, voids, pinholes, or uneven coverage. These can indicate issues during the coating process.
- Review Process Parameters: Check the parameters of the coating process, including viscosity, temperature, humidity, and curing time. Ensure that these parameters are within the specified range for the conformal coating.
- Evaluate Substrate Preparation: Verify that the substrate was adequately cleaned and prepared before applying the conformal coating. Contaminants such as oils, dust, or residues can hinder adhesion and cause coating defects.
- Assess Application Method: Consider the method used for applying the conformal coating (e.g., spray, dip, brush, or selective coating). Each method has its own challenges and parameters that must be optimized for consistent results.
- Check Equipment Calibration: Ensure that the application equipment, such as spray nozzles, brushes, or dipping tanks, is calibrated correctly. Improper calibration can lead to uneven coating thickness or application issues.
- Verify Cure Process: If the conformal coating requires curing, confirm that the curing process is being carried out correctly. This includes verifying curing temperature, duration, and any necessary post-cure steps.
- Investigate Environmental Factors: Environmental conditions such as temperature, humidity, and airflow can affect the conformal coating process. Ensure that the application environment is controlled and conducive to proper coating application.
- Consider Material Compatibility: Check the compatibility of the conformal coating material with the substrate material and any components it will contact. Incompatibility can lead to adhesion issues or coating failures.
- Troubleshoot Specific Defects: Address specific defects based on their characteristics. For example, if bubbles are present, it could indicate issues with solvent evaporation or air entrapment during application.
- Documentation and Record-Keeping: Maintain thorough documentation of the coating process parameters, equipment calibration records, and any troubleshooting steps taken. This information can help identify patterns and prevent future issues.
By systematically evaluating these factors and addressing any issues identified, you can troubleshoot problems with conformal coating applications and ensure consistent, high-quality results.
Conclusion:
Industrial conformal coatings serve as essential protective layers for electronic components, safeguarding them against various environmental stresses. Understanding their properties, application methods, and compatibility with different substrates is crucial with an array of coatings available. By selecting the appropriate conformal coating, industries can ensure their electronic devices’ reliability, durability, and performance, ultimately contributing to enhanced product quality and customer satisfaction.
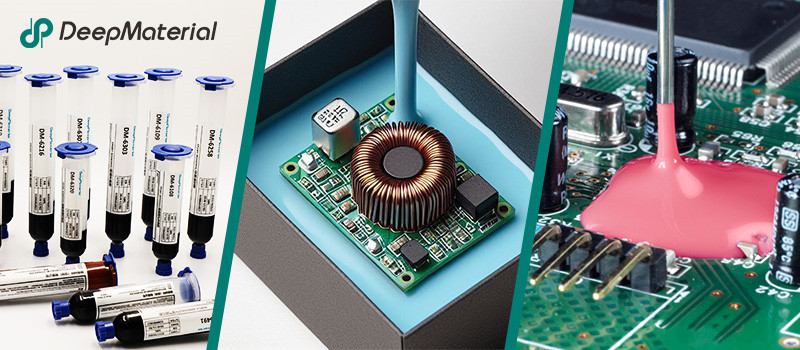
About DeepMaterial
DeepMaterial is a trusted supplier of encapsulant materials that are used in electronics manufacturing worldwide. From chip on board encapsulants such as glob top material to conformal coatings, underfills, low pressure molding, and potting solutions, DeepMaterial offers a full range of circuit board protection materials that effectively protect circuit boards while help reduce costs. More…Deepmaterial is a the manufacturer of epoxy adhesives including hardeners, metalbond, and metal filled resins. Structural, toughened medium viscosity, and non-sag adhesives are also offered. Some adhesives are resistant to thermal shock, chemical, vibration dampening, and impact. Suitable for metals, plastics, wood, and ceramics. Serves electronics, aerospace, automotive, tooling, marine, and construction industries. REACH and RoHS compliant. FDA approved. UL listed. Meets military specifications. We are the one of best adhesive manufacturers in China.
Blogs & News
Potting compounds are at the frontline of electronics assembly, delivering effective protection in challenging environmental conditions while improving mechanical strength and offering high electric insulation. Used within a variety of industries, electrical potting compounds are found within a broad range of consumer electronics, as well as used in applications across the automotive, aerospace, and other industries where electronic assemblies are prevalent.
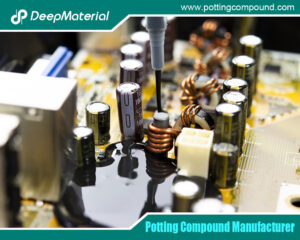
Potting Compound for PCB
Potting Compound for PCB A potting compound is a liquid or semi-liquid material that is poured or injected over a PCB or electronic assembly, then
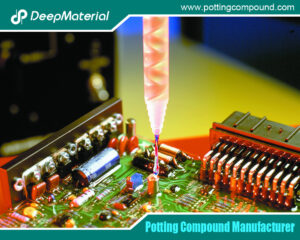
In – depth Analysis of the Curing Characteristics of Electronic Potting Compounds
In – depth Analysis of the Curing Characteristics of Electronic Potting Compounds Electronic potting compounds play a vital role in the electronics industry. They can
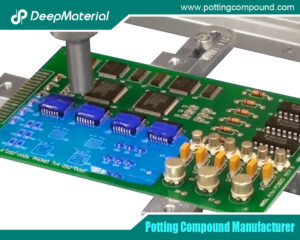
A Comprehensive Analysis of the Environmental Performance of Encapsulating Materials: From Regulations to Practices
A Comprehensive Analysis of the Environmental Performance of Encapsulating Materials: From Regulations to Practices In modern industrial manufacturing, encapsulating materials are widely used in numerous

A Comprehensive Analysis of PCB Encapsulation Quality Inspection: Innovative Application of Non-Destructive Testing Technologies
A Comprehensive Analysis of PCB Encapsulation Quality Inspection: Innovative Application of Non-Destructive Testing Technologies In the field of electronic manufacturing, the encapsulation process of printed
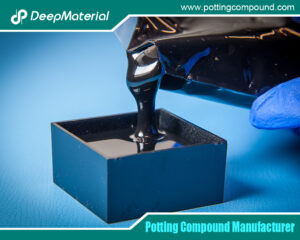
Analysis of the Improvement of the Seismic and Impact Resistance Performance of PCB by Encapsulation
Analysis of the Improvement of the Seismic and Impact Resistance Performance of PCB by Encapsulation During the operation of electronic devices, the PCB (Printed Circuit
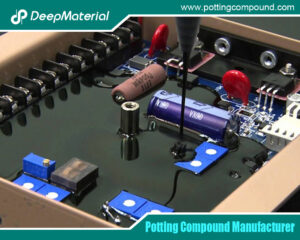
A Comprehensive Guide to Evaluating the Reliability of Encapsulation Materials for Encapsulated PCBs
A Comprehensive Guide to Evaluating the Reliability of Encapsulation Materials for Encapsulated PCBs In modern electronic devices, the printed circuit board (PCB) plays a central