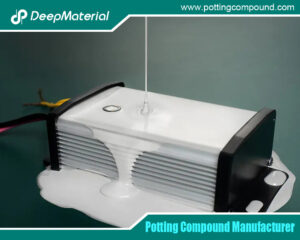
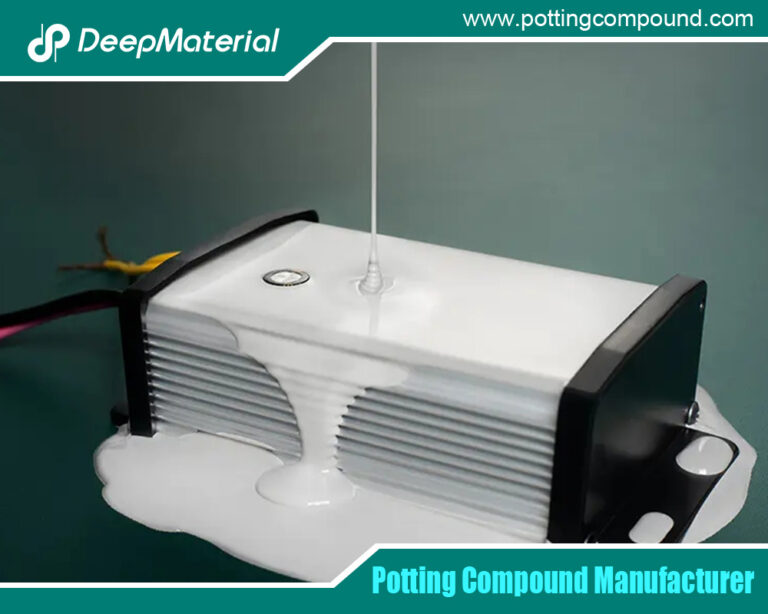
A Comprehensive Analysis of Curing Problems of Encapsulating Materials and Their Solutions
- Electronic Potting Material Manufacturer
- April 29, 2025
- Acrylic Conformal Coating, acrylic vs silicone conformal coating, conformal coating, conformal coating electronics, conformal coating for electronics, conformal coating for pcb, conformal coating for pcb standards, conformal coating in electronics market, conformal coating material, conformal coating pcb, conformal coating process, conformal coating silicone, conformal coating spray, conformal coating types, conformal coating waterproof, electrical potting compound, encapsulating materials, encapsulating materials factory, encapsulating materials manufacturer, encapsulating materials supplier, epoxy encapsulation electronic components, epoxy encapsulation led, epoxy potting compound, led uv glue adhesive, polyurethane potting compound, potting compound for electronics, potting compound for pcb, potting compound vs epoxy, silicone potting compound for electronics, uv adhesives for touch screen, UV curing potting compound, waterproof potting compound
A Comprehensive Analysis of Curing Problems of Encapsulating Materials and Their Solutions
In numerous industrial fields such as electronics and machinery, encapsulating materials are widely applied. They play a crucial role in providing functions like waterproofing, moisture-proofing, insulation, and protection for electronic components and mechanical parts. However, during the curing process of encapsulating materials, various problems often arise. These problems not only affect the performance and quality of products but, in severe cases, may also lead to product failure and increase production costs. Therefore, it is of great importance for industrial production to have an in-depth understanding of the potential problems during the curing process of encapsulating materials and to master effective solutions.
Incomplete Curing
Phenomenon and Influence
Incomplete curing is a common issue in the curing process of encapsulating materials. It is manifested as the partially or wholly soft state of the encapsulated materials, which fails to reach the expected hardness and degree of curing. This phenomenon can severely impact the performance of the encapsulating materials, making them unable to effectively fulfill functions such as waterproofing, moisture-proofing, and insulation. For example, in electronic devices, the incompletely cured encapsulating materials cannot provide reliable protection for electronic components, which may lead to the damage of components due to moisture and reduce the stability and service life of the devices.
Cause Analysis
- Inaccurate Proportioning: The mixing ratio of the main agent and the curing agent is a key factor in the curing of encapsulating materials. During the preparation process, if the ratio of the main agent and the curing agent deviates from the required range specified by the product due to operator errors, malfunction of the measuring equipment, or other reasons, it will affect the progress of the curing reaction. When the amount of the curing agent is too small, it cannot react with enough main agent, resulting in an insufficient curing reaction. On the other hand, if the amount of the curing agent is excessive, it may trigger excessive reactions and produce adverse side reactions, also leading to incomplete curing.
- Uneven Mixing: Mixing is an important step to ensure the full mixing of the main agent and the curing agent. If the mixing method is inappropriate, the mixing time is insufficient, or the mixing tool is unsuitable, it may result in uneven mixing of the two components. In this case, the main agent and the curing agent in some areas of the encapsulating materials fail to fully contact and react, leading to the phenomenon of local incomplete curing. For example, when mixing by hand, if the bottom and edges of the container are not fully mixed, these parts are prone to curing problems.
- Inappropriate Curing Conditions: The curing temperature and time play a decisive role in the curing process of encapsulating materials. Each type of encapsulating material has its specific curing temperature range and time requirements. When the curing temperature is too low, the molecular activity decreases, the curing reaction speed slows down or even stops, resulting in incomplete curing. If the curing time is too short, the reaction cannot proceed fully, and the encapsulating materials cannot be completely cured. In addition, environmental factors such as humidity may also affect the curing process. For example, some humidity-sensitive encapsulating materials may undergo hydrolysis and other reactions during curing in a high-humidity environment, hindering the curing process.
Solutions
- Precise Proportioning: Use high-precision measuring equipment such as electronic scales and metering pumps to strictly weigh the main agent and the curing agent according to the proportions specified in the product manual of the encapsulating materials. During the operation, the operators should receive professional training to improve the accuracy and standardization of their operations. At the same time, a strict quality inspection system should be established to review each proportioning to ensure that the proportion is accurate.
- Adequate Mixing: Select appropriate mixing tools and methods. For small-batch production, a mixing rod can be used for manual mixing, but it should be noted that the mixing time should be no less than 10 – 15 minutes, and the edges and bottom of the container should be fully scraped to ensure that all areas of the materials in the container are uniformly mixed. For large-batch production, it is recommended to use mechanical mixing equipment such as electric mixers and mixing paddles. According to the characteristics of the materials and the batch size, reasonably adjust the mixing speed and time to ensure the full integration of the main agent and the curing agent. In addition, the mixed encapsulating materials can be poured into another container and mixed again to further improve the mixing uniformity.
- Optimizing Curing Conditions: Set appropriate curing temperature and time according to the characteristics of the encapsulating materials. Experimental tests can be carried out to determine the optimal curing time at different temperatures and formulate a detailed curing process parameter table. In actual production, use constant temperature equipment such as ovens and curing furnaces to strictly control the temperature during the curing process to ensure that the temperature fluctuation is within the allowable range. At the same time, pay attention to the influence of environmental factors on curing. For humidity-sensitive encapsulating materials, the curing operation should be carried out in a dry environment, and a dehumidifying device can be used to control the environmental humidity if necessary.
Shrinkage and Deformation
Phenomenon and Influence
Shrinkage and deformation refer to the change in the shape and size of the encapsulated parts due to volume shrinkage during the curing process of the encapsulating materials. This deformation may be manifested as the appearance of shrink holes and depressions on the surface of the encapsulated parts, or the overall size becoming smaller and the shape being distorted. Shrinkage and deformation not only affect the appearance quality of the encapsulated parts but may also cause internal components to be subjected to stress, affecting their performance and reliability. In electronic devices, shrinkage and deformation may loosen the connections between electronic components, causing electrical performance problems. In the encapsulation of mechanical parts, deformation may lead to a decrease in the assembly accuracy of the parts, affecting the normal operation of the equipment.
Cause Analysis
- Chemical Shrinkage: During the curing process of the encapsulating materials, a chemical reaction occurs, and the materials change from a liquid state to a solid state. In this process, the distance between molecules decreases, and the chemical bonds are rearranged, resulting in volume shrinkage. Different types of encapsulating materials have different chemical shrinkage rates. For example, during the curing of epoxy resin encapsulating materials, due to the cross-linking reaction between molecules, a certain degree of chemical shrinkage will occur.
- Physical Shrinkage: In addition to chemical shrinkage, the encapsulating materials will also undergo physical shrinkage due to thermal expansion and contraction during the cooling process after curing. When the encapsulated parts cool from the curing temperature to room temperature, the volume of the materials will decrease with the decrease in temperature. If the thermal expansion coefficients of the encapsulating materials and the objects being encapsulated are significantly different, during the cooling process, the shrinkage degrees of the two are inconsistent, which will generate internal stress and lead to the shrinkage and deformation of the encapsulated parts.
- Improper Curing Process: Process parameters such as the heating rate, curing temperature, and curing time during the curing process also have an important impact on shrinkage and deformation. If the heating rate is too fast, the curing speeds inside and outside the encapsulating materials are inconsistent, and internal stress is likely to be generated, leading to shrinkage and deformation. One-time high-temperature curing may make the chemical shrinkage and physical shrinkage during the curing process too concentrated, resulting in excessive shrinkage stress. If the curing time is insufficient, the encapsulating materials cannot be fully cured, and they may continue to shrink during subsequent use, also causing deformation.
Solutions
- Selecting Appropriate Encapsulating Materials: When selecting encapsulating materials, comprehensively consider their chemical shrinkage rate and physical properties. Try to select encapsulating materials with a low shrinkage rate and a thermal expansion coefficient that matches the object being encapsulated. For example, for the encapsulation of some electronic components with high requirements for dimensional stability, encapsulating materials added with special fillers can be selected. These fillers can effectively reduce the shrinkage rate of the materials and improve dimensional stability.
- Optimizing the Curing Process: Adopt a step-by-step curing process. First, carry out pre-curing at a lower temperature to initially cross-link the encapsulating materials and release part of the shrinkage stress. Then, gradually increase the temperature for post-curing to fully cure the materials. This can avoid the excessive concentration of shrinkage stress during the curing process. At the same time, reasonably control the heating rate, generally at 1 – 3℃/min, to ensure uniform curing inside and outside the encapsulating materials. After curing is completed, let the encapsulated parts cool slowly with the heating equipment to reduce the internal stress caused by thermal expansion and contraction.
- Adding Additives: Adding an appropriate amount of additives such as toughening agents and stress release agents to the encapsulating materials can improve the performance of the materials and reduce shrinkage and deformation. Toughening agents can improve the flexibility of the encapsulating materials, enabling them to better adapt to the changes in internal stress during the shrinkage process and reducing the risk of cracking and deformation. Stress release agents can reduce the internal stress of the encapsulating materials, thereby reducing the degree of shrinkage and deformation.
Bubble Problem
Phenomenon and Influence
The bubble problem is manifested as the presence of bubbles inside the cured encapsulating materials. These bubbles may be single or multiple and clustered together. The presence of bubbles will reduce the density and strength of the encapsulating materials, affecting their insulation performance and waterproof performance. In high-voltage electrical equipment, bubbles may become the source of partial discharge, accelerating the aging and damage of the materials and seriously threatening the safe operation of the equipment.
Cause Analysis
- Air Entrainment During Mixing: During the mixing process of the encapsulating materials, if the mixing speed is too fast or the mixing method is inappropriate, a large amount of air will be introduced into the materials. These air bubbles are formed in the materials, and if they are not fully discharged before curing, they will remain in the cured encapsulated parts. For example, when using a high-speed mixer, it is easy to generate vortices, causing air to be drawn into the interior of the materials.
- Gas Evolution During Curing: Some components in the encapsulating materials may undergo chemical reactions during the curing process, generating gas. Or the gas originally dissolved in the materials may be released due to a decrease in solubility during curing. For example, in some encapsulating materials containing volatile solvents, the solvents will volatilize during the curing process, forming bubbles.
- Encapsulation Process Problems: Process factors such as the environmental pressure, temperature, and encapsulation speed during the encapsulation process also affect the generation and discharge of bubbles. When encapsulating under normal pressure, it is difficult to discharge the bubbles. If the encapsulation temperature is too high, the viscosity of the materials will decrease, making it easier for bubbles to form and difficult to discharge. If the encapsulation speed is too fast, air may not have time to escape and be wrapped in the materials.
Solutions
- Improving the Mixing Method: Reduce the mixing speed, adopt low-speed mixing or use equipment such as dispersers for mixing to reduce the entrainment of air. At the same time, it is possible to pause appropriately during the mixing process to allow the bubbles to rise to the surface and escape. In addition, preheating the raw materials before mixing to reduce their viscosity is also helpful for the discharge of bubbles.
- Vacuum Degassing Treatment: Before encapsulation, put the mixed encapsulating materials into a vacuum environment for degassing treatment. By reducing the environmental pressure, the bubbles in the materials will expand and escape. The vacuum degree is generally controlled between -0.08MPa and -0.1MPa, and the degassing time depends on the amount of materials and the bubble situation, generally 5 – 15 minutes.
- Optimizing the Encapsulation Process: Select appropriate encapsulation temperature and speed. Generally, the encapsulation temperature should be controlled within the recommended operating temperature range of the materials, and the encapsulation speed should not be too fast. Methods such as drip encapsulation and casting can be used for encapsulation to make the materials fill slowly and uniformly, which is conducive to the discharge of bubbles. In addition, during the encapsulation process, the encapsulated parts can be appropriately vibrated to help the bubbles float up and be discharged, but pay attention that the vibration amplitude should not be too large to avoid generating new bubbles.
Poor Surface of the Cured Product or Local Incomplete Curing
Phenomenon and Influence
The poor surface of the cured product is manifested as a rough surface, stickiness, cracks, etc., and local incomplete curing refers to the partial areas of the encapsulated parts that are not completely cured. These problems will affect the appearance quality and protective performance of the encapsulated parts, reducing the grade and reliability of the products. The encapsulated parts with a poor surface are likely to adsorb dust and moisture, accelerating the aging of the materials. The locally incompletely cured areas cannot provide effective protection, which may lead to the damage of internal components.
Cause Analysis
- Malfunction of the Measuring or Mixing Device: If the measuring equipment malfunctions, such as an inaccurate electronic scale or a blocked metering pump, it will lead to incorrect measurement of the main agent and the curing agent, causing an imbalance in their proportion and affecting the curing effect. If the mixing device malfunctions, such as a damaged mixing paddle or a loose mixing shaft, it will result in uneven mixing of the materials, causing local curing abnormalities.
- Raw Material Problems: After long-term storage, the main agent or the curing agent may experience phenomena such as precipitation and stratification. If they are not fully stirred evenly before use, it will lead to inconsistent actual material compositions, affecting the curing reaction. In addition, if the curing agent is exposed to the air for too long, it may absorb moisture and become ineffective, unable to participate in the curing reaction normally.
- Environmental Factors: A high-humidity environment will cause the encapsulating materials to absorb moisture. Especially for some moisture-sensitive materials, the intrusion of moisture will interfere with the curing reaction, leading to problems such as a sticky surface and local incomplete curing. In addition, too low an environmental temperature will also slow down the curing reaction speed, or even prevent it from proceeding normally.
Solutions
- Regular Equipment Maintenance: Regularly inspect and maintain the measuring and mixing devices to ensure the accuracy and normal operation of the equipment. Regularly calibrate the measuring equipment, check whether the mixing components of the mixing device are in good condition, and replace the damaged components in a timely manner. Before each use, conduct a trial run of the equipment to confirm that the equipment is normal before production.
- Proper Storage and Use of Raw Materials: Store the main agent and the curing agent in a dry, cool, and well-ventilated environment according to the storage requirements of the raw materials, and avoid direct sunlight and high temperatures. Before use, fully stir the main agent to ensure that the precipitation is evenly dispersed. For the curing agent, store it in a sealed manner and use it as soon as possible after opening to avoid moisture absorption. At the same time, pay attention to the shelf life of the raw materials, and it is strictly prohibited to use expired raw materials.
- Controlling Environmental Conditions: Control the humidity and temperature of the environment during the encapsulation and curing processes. For humidity-sensitive encapsulating materials, in seasons or environments with high humidity, a dehumidifying device can be used to control the environmental humidity within an appropriate range, generally, the humidity is controlled at 40% – 60%. At the same time, maintain the environmental temperature within the specified range according to the curing requirements of the materials. If the temperature requirements cannot be met, a heating device or a constant temperature box can be used for heating or temperature maintenance.
The problems of incomplete curing, shrinkage and deformation, bubble problems, and poor surface of the cured product or local incomplete curing that occur during the curing process of encapsulating materials seriously affect the quality and performance of products. By deeply analyzing the causes of these problems and taking corresponding solutions such as precise proportioning, adequate mixing, optimizing the curing process, selecting appropriate materials, adding additives, improving the mixing method, vacuum degassing, equipment maintenance, and environmental condition control, these problems can be effectively reduced and avoided. This can improve the curing quality of the encapsulating materials, ensure the reliability and stability of products, and provide strong support for the smooth progress of industrial production. In the actual production process, it is also necessary to continuously summarize experience, continuously improve processes and methods to deal with various possible problems, and enhance the competitiveness of products.
For more about choosing a comprehensive analysis of curing problems of encapsulating materials and their solutions, you can pay a visit to DeepMaterial at https://www.pottingcompound.com/ for more info.
Recent Posts
- A Comprehensive Analysis of Curing Problems of Encapsulating Materials and Their Solutions
- Determination of Curing Parameters of Encapsulating Materials: From Theory to Practice
- How to Determine the Appropriate Encapsulation Thickness
- Influence of Encapsulation Thickness on the Heat Dissipation Performance and Electrical Insulation Performance of PCB
- Causes and Avoidance Methods of Bubble Generation in the Potting Process
- Technical Details on Controlling Parameters such as Temperature, Pressure, and Speed in the Potting Process to Ensure Potting Quality
- A Comprehensive Analysis of PCB Pretreatment Before Potting Process: A Crucial Link to Ensure the Performance and Reliability of Electronic Devices
- A Comprehensive Analysis of the Performance Differences of Epoxy Resin, Silicone Rubber and Polyurethane Encapsulation Materials
- How to Select Suitable Potting Materials for PCB According to the Working Environment
- What is PCB Potting