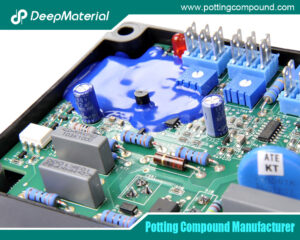
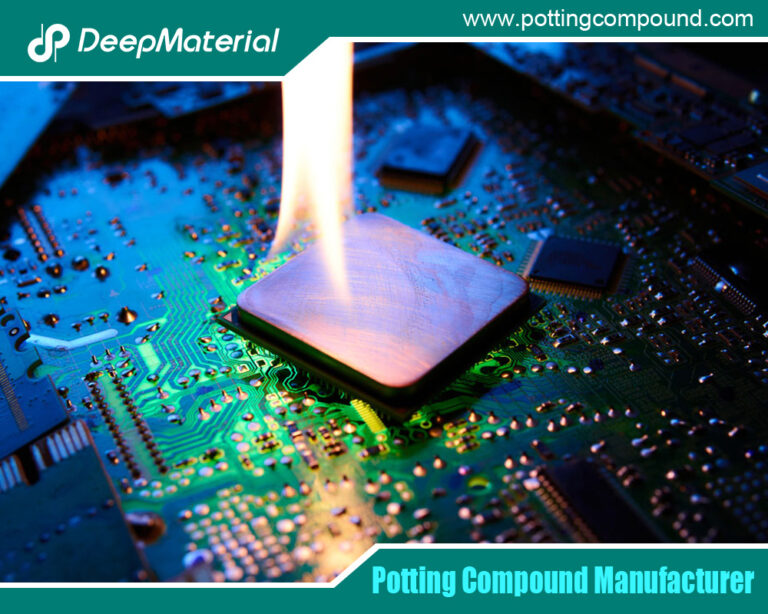
A Comprehensive Guide to Industrial Conformal Coatings: Applications, Types, and Future Trends
- Electronic Potting Material Manufacturer
- December 18, 2024
- Acrylic Conformal Coating, acrylic vs silicone conformal coating, Ceramic Potting Compound, circuit board potting compound, conformal coating electronics, conformal coating for electronics, conformal coating for pcb, conformal coating for pcb standards, Conformal Coating in Electronic, conformal coating in electronics market, conformal coating manufacturers, conformal coating market, conformal coating material, conformal coating material types, conformal coating overspray, conformal coating pcb, conformal coating process, conformal coating silicone, conformal coating spray, conformal coating suppliers, conformal coating types, Connector Potting Compound, deepmaterial potting compound, electric motor potting compound, Industrial Conformal Coating, Industrial Conformal Coating China Hotsale, Industrial Conformal Coating Factory, Industrial Conformal Coating Factory OEM, Industrial Conformal Coating Wholesale
A Comprehensive Guide to Industrial Conformal Coatings: Applications, Types, and Future Trends
The demand for reliable, long-lasting, and resilient electronic components has surged in today’s fast-paced industrial landscape. One key solution to enhancing the longevity and durability of these components is industrial conformal coatings. These coatings serve as protective layers, shielding electronics from environmental stressors like moisture, dust, and chemical exposure, which can significantly affect performance. This article delves into the essentials of industrial conformal coatings, exploring their applications, types, unique properties, and future industry trends.
Understanding Industrial Conformal Coatings
Industrial conformal coatings are thin layers applied to electronic components and circuitry to protect them from harsh environmental conditions. They are designed to conform to the element’s shape, ensuring a seamless protective barrier without affecting the device’s functionality. Here, we break down the fundamentals of these coatings, including their benefits, applications, and how they improve product reliability.
What Are Industrial Conformal Coatings?
- Thin Protective Layer: Conformal coatings are thin, flexible materials that protect electronic assemblies.
- Seamless Conformity: The coating conforms to the shape of the electronic component, providing comprehensive protection.
- Broad Application Range:Used widely across industries, especially aerospace, automotive, and consumer electronics.
Critical Benefits of Industrial Conformal Coatings
- Enhanced Reliability: Reduces the risk of circuit failure due to environmental exposure.
- Extended Lifespan:Improves the durability of electronic devices and machinery.
- Cost-Effectiveness:Reduces maintenance and replacement costs by preventing early degradation.
Types of Industrial Conformal Coatings and Their Applications
Different types of conformal coatings are chosen based on specific application needs, environmental conditions, and industry standards. Below, we explore various industrial conformal coatings and their unique benefits.
1. Acrylic-Based Conformal Coatings
Acrylic-based conformal coatings are famous for their ease of application and reworkability.
- Key Characteristics: Provide excellent moisture resistance and flexibility.
- Applications:Ideal for low-moisture environments and consumer electronics.
- Pros: Cost-effective, easy to apply, and remove.
2. Silicone-Based Conformal Coatings
Silicone coatings are known for their superior temperature and chemical resistance.
- Key Characteristics: High elasticity, suitable for high-temperature and outdoor applications.
- Applications: Widely used in automotive and aerospace industries.
- Pros: Durable and resistant to both high temperatures and UV radiation.
3. Urethane-Based Conformal Coatings
Urethane coatings are valued for their resistance to abrasion and chemical exposure.
- Key Characteristics: Strong and highly resistant to solvents, chemicals, and mechanical stress.
- Applications: Common in military and aerospace equipment.
- Pros: Highly durable with excellent chemical and mechanical resistance.
4. Epoxy-Based Conformal Coatings
Epoxy coatings offer robust protection but can be challenging to remove.
- Key Characteristics: Rigid and highly resistant to moisture and physical damage.
- Applications: Used in critical industrial and military equipment.
- Pros:Exceptional mechanical strength and moisture resistance.
5. Parylene Conformal Coatings
Parylene is a high-performance coating applied through vapor deposition, offering uniform coverage.
- Key Characteristics: Transparent, thin, and highly effective against moisture and chemical damage.
- Applications: Utilized in medical, aerospace, and precision instruments.
- Pros: Biocompatible, highly resistant, and provides excellent dielectric properties.
Application Techniques for Industrial Conformal Coatings
The application of conformal coatings requires precision to ensure optimal protection. Various techniques achieve uniform, controlled coating layers on electronic components.
Brushing
One of the simplest methods, brushing, is often used for smaller-scale applications and repairs.
- Advantages: Cost-effective, minimal equipment needed, and suitable for touch-ups.
- Drawbacks: Inconsistent thickness; not ideal for large-scale projects.
Spraying
Spraying is a popular method for precision coating large volumes.
- Advantages: It provides a uniform layer and adjustable coverage and is efficient for more significant components.
- Drawbacks: Controlled conditions and proper ventilation are required to avoid overspray.
Dipping
This method submerges components in the coating material, providing an even layer.
- Advantages:Ideal for complex shapes and ensures thorough coverage.
- Drawbacks:High material use; requires drying or curing time.
Selective Coating
This automated method is used for precision application, targeting specific areas.
- Advantages:High precision, minimal waste, and suitable for high-volume production.
- Drawbacks:Initial equipment costs can be high, and setup requires expertise.
Fundamental Performance Properties of Industrial Conformal Coatings
Each type of conformal coating is designed to meet specific performance requirements. Let’s explore the essential properties that make these coatings a valuable choice for various industrial applications.
Dielectric Strength
Conformal coatings provide insulation, preventing current leakage and protecting against short circuits.
- Importance: Essential for high-voltage applications where insulation is critical.
- Example Use: Protects sensitive electronic circuits in automotive systems.
Moisture Resistance
Many industrial environments have high humidity levels or may expose electronics to water.
- Importance: Reduces corrosion and degradation caused by moisture.
- Example Use: Essential in outdoor applications, like traffic control systems.
Thermal Stability
Industrial conformal coatings can withstand a wide range of temperatures.
- Importance: Critical for industries such as aerospace and automotive, where electronics are exposed to extreme temperatures.
- Example Use:Ensures circuit reliability in high-temperature zones.
Chemical Resistance
In some industries, electronic components come into contact with oils, solvents, or other chemicals.
- Importance: Protects against chemical degradation, prolonging component life.
- Example Use: Common in chemical processing plants.
Flexibility and Mechanical Strength
Conformal coatings need to be flexible yet durable to withstand mechanical stresses.
- Importance: Ideal for electronics that may undergo vibration, impact, or movement.
- Example Use: Used in wearable technology and flexible circuit boards.
Emerging Trends in Industrial Conformal Coatings
With advancements in materials science and manufacturing techniques, new trends are shaping the future of industrial conformal coatings. Here are some noteworthy developments to watch.
Eco-Friendly Coatings
As environmental concerns grow, the demand for eco-friendly, low-VOC (volatile organic compound) coatings increases.
- Characteristics:Compliance with environmental regulations, safer use, and reduced harmful emissions.
- Industry Impact: Preferred in consumer electronics and medical devices.
Nanocoatings
Nanotechnology has led to the development of ultra-thin, highly protective coatings.
- Characteristics: Exceptional barrier properties in a microscopic layer.
- Industry Impact: Revolutionizing precision electronics, medical devices, and nanoelectronics protection.
Smart Coatings
Innovative coatings change properties in response to environmental changes, like temperature or humidity.
- Characteristics: Adaptive, responsive, and often self-healing.
- Industry Impact: Opens new possibilities in the aerospace, automotive, and wearable technology sectors.
Advanced Application Methods
Innovations in robotics and automation enhance the precision and efficiency of conformal coating applications.
- Characteristics: Allows faster production, more consistent application, and reduced labor costs.
- Industry Impact: Key to scaling up automotive and consumer electronics production.
Best Practices for Choosing and Applying Industrial Conformal Coatings
Selecting the appropriate conformal coating and application technique is crucial for optimal protection. Consider these best practices to ensure successful application and maximum durability.
Assess Environmental Factors
Understand the environment in which the electronic component will operate, considering temperature, moisture, and exposure to chemicals.
- Guideline: Select a coating that can withstand the specific conditions of your industry.
Prioritize Material Compatibility
Ensure the coating material is compatible with the electronics and other materials.
- Guideline: Avoid coatings that may react adversely with component materials.
Test for Coating Integrity
Perform testing to verify coating thickness, adhesion, and other essential properties.
- Guideline:Conduct tests to identify any potential weaknesses or areas needing touch-ups.
Conclusion
Industrial conformal coatings are critical in safeguarding electronic components across diverse industries, enhancing their resilience to environmental and mechanical stress. With advancements in materials and application technologies, these coatings continue to evolve, offering even better protection, durability, and eco-friendly options. By understanding the types of conformal coatings, their specific benefits, and best application practices, manufacturers can ensure the longevity and reliability of their products, setting a foundation for sustained innovation and operational efficiency.
For more about choosing A Comprehensive Guide to Industrial Conformal Coatings: Applications, Types, and Future Trends, you can pay a visit to DeepMaterial at https://www.pottingcompound.com/ for more info.
Recent Posts
- Influence of Encapsulation Thickness on the Heat Dissipation Performance and Electrical Insulation Performance of PCB
- Causes and Avoidance Methods of Bubble Generation in the Potting Process
- Technical Details on Controlling Parameters such as Temperature, Pressure, and Speed in the Potting Process to Ensure Potting Quality
- A Comprehensive Analysis of PCB Pretreatment Before Potting Process: A Crucial Link to Ensure the Performance and Reliability of Electronic Devices
- A Comprehensive Analysis of the Performance Differences of Epoxy Resin, Silicone Rubber and Polyurethane Encapsulation Materials
- How to Select Suitable Potting Materials for PCB According to the Working Environment
- What is PCB Potting
- The Evolution of Smart Watch Assembly Adhesive: A Key Component in Modern Wearable Technology
- Laptop Tablet Assembly Adhesive: The Key to Durable and Reliable Device Construction
- Power Bank Assembly Adhesive: The Essential Component for Building Durable Power Banks