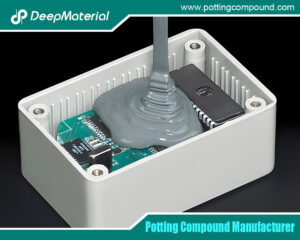
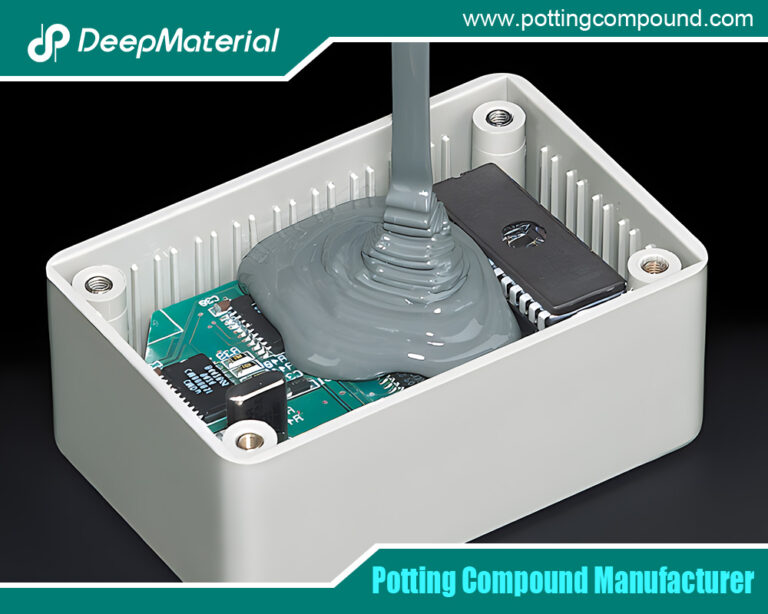
Causes and Avoidance Methods of Bubble Generation in the Potting Process
- Electronic Potting Material Manufacturer
- April 17, 2025
- Benefits of Potting Electronics, Ceramic Potting Compound, china electronic potting silicone manufacturer, china electronic potting silicone supplier, circuit board potting compound, circuit board potting compounds, Connector Potting Compound, custom automated electronics potting, electronic epoxy encapsulant potting compounds, Electronic Potting Process, epoxy potting compound, Epoxy Potting Process, Epoxy Potting Process Manufacturer, glass fiber adhesive glue, polyurethane potting compound, polyurethane potting compound for electronics, potting compound for electronics, potting material for electronic components, potting material for electronics, potting pcb, Potting Process, potting process manufacturer, potting process supplier, silicone potting compound for electronics, UV Curable Conformal Coating, UV Cured Epoxy Potting, UV Curing Potting Compounds, waterproof potting compound
Causes and Avoidance Methods of Bubble Generation in the Potting Process
In many fields such as electronic manufacturing, the potting process is an important link for protecting electronic components, enhancing product stability and reliability. If bubbles are generated during the potting process, it will not only affect the appearance of the product, but also may lead to serious problems such as a decrease in electrical performance, a reduction in mechanical strength, and the failure of sealing performance. This article will deeply explore the causes of bubble generation during the potting process and elaborate in detail on the effective methods to avoid bubble generation.
Causes of Bubble Generation
Air Introduction During the Mixing Process
- High-speed Mixing: During the mixing process of the potting adhesive, if the mixing speed is too fast, air will be entrained into the adhesive liquid, forming a large number of tiny bubbles. For example, when using an electric mixer to mix a two-component potting adhesive at a high rotation speed, the centrifugal force generated by the rapid rotation of the mixing paddle will cause the surrounding air to be sucked into the adhesive liquid. Especially for potting adhesives with low viscosity, high-speed mixing is more likely to lead to the generation of bubbles because the low-viscosity adhesive liquid has good fluidity, and air is more likely to form bubbles in it and be encapsulated.
- Improper Mixing Method: If the adhesive is not mixed at a constant speed in one direction during mixing, but is mixed back and forth or irregularly, air will also be mixed into the adhesive liquid to generate bubbles. For example, frequently changing the mixing direction during the mixing process will cause turbulence inside the adhesive liquid, increasing the chance of air entrainment. In addition, the selection of the mixing tool is also very important. If an inappropriate mixing tool is used, such as a mixing rod with a rough surface or grooves, it is easy to entrain air during the mixing process, thus introducing bubbles.
Air Entrainment During the Potting Process
- Improper Pouring Method: When pouring the potting adhesive into the circuit board or other containers, if the height is too high or the speed is too fast, the adhesive liquid will impact the bottom of the container or the existing adhesive layer, thus generating bubbles. For example, when directly pouring the adhesive liquid from a relatively high position into a relatively deep container, the impact force of the adhesive liquid will cause air to be entrained and form bubbles. In addition, during the pouring process, if the flow rate of the adhesive liquid is unstable, changing from large to small, it is also easy to entrain air.
- Poor Adhesive Liquid Flow: If the potted space has a complex structure, the potting adhesive may be blocked during the flowing process, resulting in local eddies or turbulence, thus introducing bubbles. For example, on a circuit board with many dense electronic components and narrow gaps, the adhesive liquid may flow poorly when filling these areas, forming bubbles. In addition, the viscosity of the potting adhesive will also affect the generation of bubbles. If the viscosity is relatively high, the fluidity of the adhesive liquid is poor, and it is more likely to generate bubbles during the potting process.
Bubble Generation During the Curing Process
- Gas Generation Due to Chemical Reactions: Some potting adhesives will undergo chemical reactions during the curing process, which may generate gas, thus forming bubbles. For example, when a two-component epoxy resin potting adhesive is cured, the chemical reaction between the two components may release a small amount of gas. If this gas cannot be discharged in time, it will form bubbles in the adhesive liquid. Under different potting adhesive formulations and curing conditions, the possibility and amount of gas generation will also vary.
- Temperature Changes: During the curing process of the potting adhesive, if the temperature changes greatly, the volume of the adhesive liquid will expand or contract, which may lead to the generation of bubbles. For example, during the heating and curing process, if the heating rate is too fast, the internal temperature of the adhesive liquid is uneven, which will cause local expansion and thus generate bubbles. Similarly, during the cooling process, if the cooling rate is too fast, it may also cause a negative pressure inside the adhesive liquid, thus sucking in air and forming bubbles.
Methods to Avoid Bubble Generation
Raw Materials and Preparation Stage
- Select Appropriate Potting Adhesive: According to the specific application scenarios and requirements, select potting adhesive products with reliable quality and a low tendency to generate bubbles. Different types of potting adhesives, such as epoxy resin potting adhesives, silicone resin potting adhesives, and polyurethane potting adhesives, have different performance and bubble generation characteristics. For example, some low-viscosity, self-leveling potting adhesives are more likely to discharge bubbles during the potting process.
- Inspect the Quality of Raw Materials: Ensure that the potting adhesive, curing agent and other raw materials are not expired and have no signs of deterioration. Improper storage may cause water or other impurities to be mixed into the potting adhesive, which may cause bubble generation during the curing process. For example, if the potting adhesive is exposed to a high humidity environment for a long time and absorbs water, the water will vaporize during the curing process and form bubbles.
- Preheat the Potted Object: Preheating the potted components or products is helpful for the escape of air and reduces the possibility of bubble generation. For example, before potting an electronic circuit board, preheating the circuit board at a certain temperature (such as 50 – 60°C) for a period of time can make the air on the surface and inside of the circuit board expand and escape due to heat, avoiding being encapsulated in the adhesive liquid to form bubbles during the potting process.
Mixing and Blending Stage
- Control the Mixing Speed and Method: Adopt low-speed mixing, generally it is recommended that the rotation speed is 300 – 500rpm, and the mixing time is determined according to the amount of adhesive liquid and the actual mixing effect, usually 2 – 5 minutes, to ensure sufficient mixing while avoiding entraining too much air. When mixing, it is necessary to maintain uniform mixing in the same direction, such as in a clockwise direction, and avoid mixing back and forth or quickly. For example, when mixing a two-component potting adhesive, slowly and uniformly mixing can make the two components fully blend without generating too many bubbles.
- Select Appropriate Mixing Tools: Use mixing rods or mixing paddles with a smooth surface and no grooves to reduce air entrainment. For example, a smooth metal mixing paddle is less likely to entrain air into the adhesive liquid during the mixing process compared to a rough plastic mixing rod.
Potting Operation Stage
- Optimize the Pouring Method: Reduce the pouring height of the potting adhesive, control the pouring speed, and make the adhesive liquid flow into the potted container slowly and steadily. Methods such as drip potting and injection with a syringe can be adopted, especially for the potting of small or precision components. For example, when potting a small electronic module, slowly injecting the potting adhesive with a syringe can effectively reduce the generation of bubbles.
- Improve the Fluidity of the Adhesive Liquid: For potted spaces with complex structures, the viscosity of the potting adhesive can be adjusted (add a diluent within the allowable range, but pay attention to the impact on the curing performance) or auxiliary means such as tilting the potted object and gently vibrating can be adopted to help the adhesive liquid fill and discharge bubbles. For example, when potting an electronic component with a complex heat sink structure, gently vibrating the component can make the adhesive liquid fill the gaps better and discharge the bubbles.
- Adopt Layered Potting: For deep cavities or large-volume potted objects, the method of layered potting can be adopted. First pot a part, and after it is initially cured (but still has a certain fluidity), then carry out subsequent potting, which can reduce the generation of internal bubbles. For example, when potting a large transformer, pot it in 2 – 3 times, and wait for several hours for each potting to let it initially cure, which can effectively avoid a large number of bubbles gathering inside.
Degassing Treatment Stage
- Vacuum Degassing: Put the mixed potting adhesive into a vacuum environment for degassing treatment. Generally, evacuate to – 0.08MPa to – 0.1MPa and maintain it for 5 – 15 minutes, and the specific time and vacuum degree are determined according to the characteristics of the adhesive liquid and the bubble situation. In a vacuum environment, the bubbles in the adhesive liquid will expand and escape. For example, for the potting of precision electronic devices that are sensitive to bubbles, vacuum degassing is an essential step.
- Centrifugal Degassing: Use a centrifuge to carry out centrifugal degassing on the potting adhesive, and make the bubbles gather on the surface of the adhesive liquid and be discharged through centrifugal force. It is suitable for some potting adhesives with high viscosity that are difficult to be completely degassed by vacuum. For example, for some high-viscosity polyurethane potting adhesives, combining centrifugal degassing with vacuum degassing can achieve a better degassing effect.
Curing Stage
- Control the Curing Temperature and Speed: Adopt a slow heating and curing method to avoid rapid temperature changes. For example, for potting adhesives that need to be cured by heating, a stepped heating method can be adopted, such as first curing at 40 – 50°C for 1 – 2 hours, and then raising the temperature to 70 – 80°C for 2 – 3 hours. This can allow the gas in the adhesive liquid enough time to escape and reduce the generation of bubbles caused by rapid temperature changes.
- Adjust the Dosage and Proportion of the Curing Agent: Strictly prepare the mixture according to the dosage and proportion of the curing agent provided by the potting adhesive supplier to ensure the normal progress of the curing reaction. Too much or too little dosage of the curing agent may lead to abnormal curing speed, uneven heat release during the reaction and other problems, thus causing bubble generation. For example, when using an epoxy resin potting adhesive, accurately weighing the dosage of the epoxy resin and the curing agent, and controlling the error within a very small range can ensure the stability of the curing process.
Environmental Control Stage
- Temperature and Humidity Control: Keep the temperature and humidity of the potting operation environment stable. Generally, the temperature is controlled at 20 – 25°C, and the humidity is controlled at 40% – 60%, which is more appropriate. Too high humidity may cause the potting adhesive to absorb water, and generate bubbles during the curing process; too high or too low temperature may affect the viscosity and curing speed of the potting adhesive, indirectly leading to bubble generation. For example, in the rainy season with high humidity, using a dehumidifier to control the environmental humidity can effectively reduce the bubbles generated due to humidity problems.
- Reduce Environmental Airflow Interference: Avoid carrying out potting operations in an environment with strong airflows, as strong airflows may entrain air into the adhesive liquid to form bubbles. For example, setting up an isolation barrier in the potting area to reduce the impact of external airflows on the potting process.
For more about the causes and avoidance methods of bubble generation in the potting process, you can pay a visit to DeepMaterial at https://www.pottingcompound.com/ for more info.
Recent Posts
- Causes and Avoidance Methods of Bubble Generation in the Potting Process
- Technical Details on Controlling Parameters such as Temperature, Pressure, and Speed in the Potting Process to Ensure Potting Quality
- A Comprehensive Analysis of PCB Pretreatment Before Potting Process: A Crucial Link to Ensure the Performance and Reliability of Electronic Devices
- A Comprehensive Analysis of the Performance Differences of Epoxy Resin, Silicone Rubber and Polyurethane Encapsulation Materials
- How to Select Suitable Potting Materials for PCB According to the Working Environment
- What is PCB Potting
- The Evolution of Smart Watch Assembly Adhesive: A Key Component in Modern Wearable Technology
- Laptop Tablet Assembly Adhesive: The Key to Durable and Reliable Device Construction
- Power Bank Assembly Adhesive: The Essential Component for Building Durable Power Banks
- Smartphone Assembly Adhesive: Enhancing Durability and Precision in Modern Devices