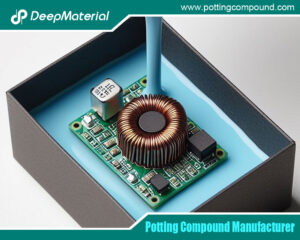
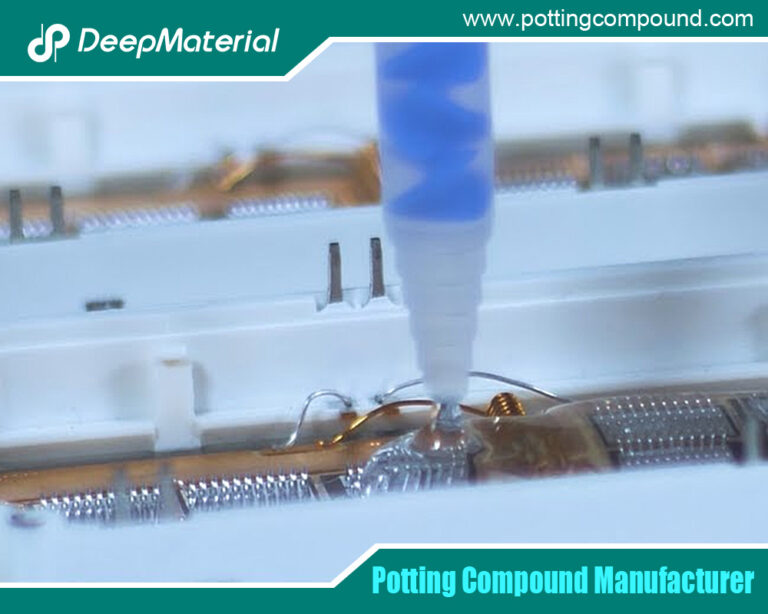
Conformal Coating in the Electronics Market: A Comprehensive Overview
- Electronic Potting Material Manufacturer
- August 26, 2024
- Acrylic Conformal Coating, acrylic vs silicone conformal coating, conformal coating, conformal coating electronics, conformal coating for electronics, conformal coating for pcb, conformal coating for pcb standards, Conformal Coating in Electronic, conformal coating in electronics market, conformal coating manufacturers, conformal coating material, conformal coating material types, conformal coating overspray, conformal coating pcb, conformal coating process, conformal coating silicone, conformal coating spray, conformal coating suppliers, conformal coating types, conformal coating waterproof, Electronic Conformal Coating, epoxy conformal coating, Industrial Conformal Coating, pcb conformal coating, Silicone Conformal Coating, Urethane Conformal Coating, UV Cure Conformal Coating, Waterproof Conformal Coating
Conformal Coating in the Electronics Market: A Comprehensive Overview
Conformal coating is an essential aspect of electronics manufacturing and assembly. As technology advances, the demand for reliable and durable electronic devices increases, making conformal coating a critical component in the electronics market. This article delves into the various aspects of conformal coating, its types, applications, and significance in the electronics industry.
What is Conformal Coating?
Conformal coating is a protective layer applied to electronic circuit boards and components to shield them from environmental factors such as moisture, dust, chemicals, and extreme temperatures. The coating conforms to the contours of the substrate, providing a protective barrier that ensures the longevity and reliability of electronic devices. This layer is essential for enhancing the performance and durability of electronic products, particularly in harsh or demanding environments.
Types of Conformal Coatings
Acrylic Coatings
Acrylic conformal coatings are popular due to their ease of application and removal. They offer good protection against moisture and are suitable for applications requiring flexibility and easy reworkability. Acrylic coatings are also known for their fast drying times and low toxicity.
Silicone Coatings
Silicone conformal coatings are renowned for their exceptional thermal stability and flexibility. They can withstand extreme temperatures and are highly resistant to moisture and chemicals, making them ideal for applications in automotive, aerospace, and other high-temperature environments.
Epoxy Coatings
Epoxy conformal coatings protect against moisture, chemicals, and mechanical wear. They are known for their durability and strength, making them suitable for applications requiring high resistance to environmental stress. However, epoxy coatings can be challenging to remove, which may limit their reworkability.
Polyurethane Coatings
Polyurethane conformal coatings balance flexibility, chemical resistance, and durability. They provide reasonable protection against moisture and abrasion while maintaining flexibility. Polyurethane coatings are often used in applications where security and flexibility are needed.
Parylene Coatings
Parylene is a unique conformal coating material applied through a chemical vapor deposition (CVD) process. It provides a skinny, uniform coating that protects against moisture, chemicals, and physical damage. Parylene coatings are used in specialized applications where precise coating is critical.
Applications of Conformal Coating
Consumer Electronics
Conformal coatings are used in consumer electronics, such as smartphones, tablets, and wearables, to protect sensitive components from moisture, dust, and other contaminants. The coating ensures the longevity and reliability of these devices, even in challenging environments.
Automotive Industry
The automotive industry relies heavily on conformal coatings to protect electronic components in vehicles. These coatings safeguard against extreme temperatures, vibrations, and exposure to chemicals, ensuring the performance and reliability of automotive electronics.
Aerospace and Defense
In aerospace and defense applications, conformal coatings protect electronic systems from harsh environmental conditions, such as high altitudes, temperature extremes, and chemical exposure. The coatings help maintain the functionality and safety of critical systems in these demanding sectors.
Medical Devices
Conformal coatings are essential in the medical device industry. They protect electronic components from moisture and biological contaminants, ensuring the reliability and safety of medical devices often used in sensitive and high-risk environments.
Industrial Equipment
Industrial equipment, such as machinery and control systems, benefits from conformal coatings that protect against dust, moisture, and chemicals. The coatings help maintain the operational efficiency and longevity of these critical systems.
Advantages of Conformal Coating
Enhanced Durability
Conformal coatings provide a protective barrier that enhances the durability of electronic components. By shielding against environmental factors, the coatings extend the lifespan of devices and reduce the risk of component failure.
Improved Reliability
Applying conformal coatings improves electronic systems’ reliability by preventing damage from moisture, dust, and other contaminants. This increased reliability is crucial for maintaining the performance and functionality of electronic devices in various applications.
Resistance to Environmental Factors
Conformal coatings resist various environmental factors, including moisture, chemicals, temperature extremes, and mechanical stress. This protection ensures that electronic components can operate effectively in demanding environments.
Reduced Maintenance Costs
Conformal coatings help reduce maintenance and repair costs by protecting electronic components from damage. The coatings minimize the need for frequent servicing and extend the operational life of devices, resulting in cost savings for manufacturers and users.
Flexibility and Reworkability
Some types of conformal coatings, such as acrylic coatings, offer flexibility and ease of rework. This feature allows repairs and modifications to be made without significant difficulty, making the coating process more manageable for manufacturers.
Challenges and Considerations
Application Process
Applying conformal coatings requires careful consideration of coating thickness, curing conditions, and substrate compatibility. Proper application is essential to ensure the coating’s effectiveness and avoid such problems as incomplete coverage or inadequate adhesion.
Cost
While conformal coatings provide valuable protection, the cost of materials and application can be a consideration for manufacturers. Choosing the correct type of coating for a specific application involves balancing performance requirements with cost-effectiveness.
Environmental Impact
The environmental impact of conformal coatings, particularly those containing hazardous materials, is an important consideration. Manufacturers are increasingly seeking eco-friendly coating options and adopting practices to minimize the coating process’s environmental footprint.
Regulatory Compliance
Conformal coatings must comply with industry regulations and standards, depending on the application and region. Manufacturers must ensure their coating materials and processes meet relevant regulatory requirements to avoid potential compliance issues.
Future Trends in Conformal Coating
Advancements in Coating Materials
Ongoing research and development in conformal coating materials are expected to lead to the introduction of new and improved coating options. These advancements may include coatings with enhanced performance characteristics, such as increased resistance to emerging environmental challenges.
Integration with Smart Technologies
An emerging trend is the integration of conformal coatings with smart technologies, such as sensors and IoT devices. These advanced coatings can provide additional functionalities, such as self-healing properties or embedded sensors for monitoring and diagnostics.
Focus on Sustainability
Sustainability is becoming a key consideration in the electronics industry, and conformal coatings are no exception. Manufacturers are exploring eco-friendly coating materials and processes to reduce the environmental impact of conformal coating applications.
Customization and Precision
As electronic devices become more complex, the need for customized and precise conformal coatings is increasing. Advances in coating application techniques, such as selective coating and precision deposition, are expected to meet the evolving needs of the electronics market.
Conclusion
Conformal coating plays a vital role in the electronics market by providing essential protection for electronic components and devices. With various coatings available, manufacturers can choose the most suitable option based on their requirements and application environments. As technology advances, conformal coatings will remain a critical component in ensuring electronic products’ durability, reliability, and performance. The future of conformal coating holds exciting possibilities, with advancements in materials, innovative technologies, and sustainability driving innovation in this essential field.
For more about choosing the Top Conformal Coating in the Electronics Market: A Comprehensive Overview, you can pay a visit to DeepMaterial at https://www.pottingcompound.com/ for more info.
Recent Posts
- Potting Compound vs. Epoxy: A Comprehensive Comparison
- Potting Compound for PCB
- In – depth Analysis of the Curing Characteristics of Electronic Potting Compounds
- A Comprehensive Analysis of the Environmental Performance of Encapsulating Materials: From Regulations to Practices
- A Comprehensive Analysis of PCB Encapsulation Quality Inspection: Innovative Application of Non-Destructive Testing Technologies
- Analysis of the Improvement of the Seismic and Impact Resistance Performance of PCB by Encapsulation
- A Comprehensive Guide to Evaluating the Reliability of Encapsulation Materials for Encapsulated PCBs
- In-depth Analysis of the Reparability of Encapsulation Materials
- A Comprehensive Analysis of Post-Potting PCB Issues and the Repair and Rework of Potting Materials
- A Comprehensive Analysis of the Compatibility between Encapsulation Materials and PCBs: Exploration of Chemical Reactions and Their Impact on Performance