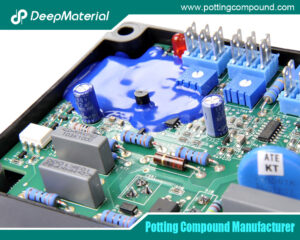

Conformal Coatings for Electronics Applications
- Electronic Potting Material Manufacturer
- September 14, 2024
- Acrylic Conformal Coating, acrylic vs silicone conformal coating, conformal coating, conformal coating electronics, conformal coating for electronics, conformal coating for pcb, conformal coating for pcb standards, Conformal Coating in Electronic, conformal coating in electronics market, conformal coating manufacturers, conformal coating material, conformal coating material types, conformal coating overspray, conformal coating pcb, conformal coating process, conformal coating silicone, conformal coating spray, conformal coating suppliers, conformal coating types, conformal coating waterproof, Conformal Coatings for Electronic, conformal coatings for electronics applications, Industrial Conformal Coating, pcb conformal coating, Silicone Conformal Coating, Urethane Conformal Coating, UV Cure Conformal Coating, Waterproof Conformal Coating
Conformal Coatings for Electronics Applications
In the world of electronics, ensuring durability and reliability is paramount. One critical method for achieving this is through the application of conformal coatings. These protective layers are essential in safeguarding electronic components from environmental factors such as moisture, dust, chemicals, and temperature extremes. This article explores conformal coatings, covering their types, applications, benefits, and future trends.
1. What Are Conformal Coatings?
Conformal coatings are protective layers applied to electronic circuits and components to shield them from environmental conditions that could cause damage or failure. Unlike traditional coatings, conformal coatings are designed to conform to the contours of the substrate, providing a uniform layer of protection even in complex geometries.
1.1. Purpose and Importance
Conformal coatings’ primary purpose is to enhance the reliability and lifespan of electronic devices. They prevent moisture and contaminants from causing short circuits or corrosion, which can be detrimental to electronic assemblies’ performance. In high-reliability applications, such as aerospace, medical devices, and military electronics, conformal coatings are crucial for maintaining functionality under harsh conditions.
1.2. Types of Conformal Coatings
There are several types of conformal coatings, each with distinct properties and applications:
- Acrylic Coatings:These are popular for their ease of application and removal. Acrylic coatings provide good moisture resistance and are typically used in consumer electronics and general-purpose applications.
- Silicone Coatings:Known for their high-temperature resistance and flexibility, silicone coatings are ideal for applications exposed to extreme temperatures and vibrations. They are commonly used in the automotive and aerospace industries.
- Polyurethane Coatings:These coatings offer excellent chemical resistance and are suitable for environments where chemical exposure is a concern. They are used in industrial electronics and outdoor applications.
- Epoxy Coatings:Epoxy coatings provide robust protection against moisture and chemicals but are more rigid and difficult to remove than other types. They are often used in high-reliability and harsh environment applications.
- Parylene Coatings:Parylene coatings are applied via vapor deposition, creating a thin, uniform layer with excellent barrier properties. They are used in medical devices, electronics, and aerospace applications.
2. Application Methods
Various methods can be used to apply conformal coatings, each suited to different types of coatings and production requirements.
2.1. Spray Application
Spray application is a versatile method for acrylic, polyurethane, and silicone coatings. It involves spraying the coating onto the surface using a spray gun or aerosol can. This method is suitable for both manual and automated processes, making it ideal for prototyping and low—to medium-volume production.
2.2. Dip Coating
Dip coating involves immersing the entire assembly into a coating bath, allowing the coating to cover all surfaces. This method is commonly used for acrylic and polyurethane coatings and is suitable for high-volume production. Dip coating ensures a uniform layer but may not be ideal for assemblies with delicate components.
2.3. Brush Application
Brush application is a manual method for coating with a brush or applicator. This method is helpful for touch-ups or small-scale production but is labor-intensive and may result in uneven coating thickness.
2.4. Selective Coating
Selective coating involves applying the coating only to specific areas of the assembly, typically using automated equipment. This method is ideal for protecting sensitive components while leaving other regions uncoated. It is commonly used with acrylic and silicone coatings in medium to high-volume production.
2.5. Parylene Deposition
Parylene coatings are applied using a vapor deposition process in a vacuum chamber. The coating material is vaporized and then deposited onto the substrate, creating a thin, uniform layer. This method suits applications requiring high precision and consistent coverage, such as medical devices and high-tech electronics.
3. Benefits of Conformal Coatings
Conformal coatings offer several benefits that enhance the performance and longevity of electronic devices.
3.1. Protection Against Environmental Factors
Conformal coatings provide a barrier against moisture, dust, chemicals, and temperature extremes. This protection prevents corrosion, short circuits, and degradation of electronic components, ensuring reliable performance in harsh environments.
3.2. Increased Reliability
Conformal coatings contribute to the overall reliability of electronic assemblies by protecting them from environmental stressors. This is particularly important in critical applications such as aerospace, automotive, and medical devices, where failure can have severe consequences.
3.3. Enhanced Durability
Coated electronic assemblies are more resistant to mechanical stress, vibration, and thermal cycling. This increased durability extends the device’s lifespan and reduces the need for frequent repairs or replacements.
3.4. Improved Performance
Conformal coatings can help maintain electronic components’ performance by preventing contaminants from interfering with their operation. This is especially important for high-frequency and high-precision applications, where even minor interference can impact performance.
3.5. Cost-Effectiveness
While the initial cost of applying conformal coatings may be higher, the long-term benefits outweigh the expense. The increased reliability and durability reduce the need for maintenance and replacements, ultimately resulting in cost savings over the device’s lifespan.
4. Challenges and Considerations
Despite their advantages, conformal coatings present several challenges and considerations that must be addressed.
4.1. Selection of Coating Type
Choosing the appropriate coating type for a specific application requires careful consideration of environmental conditions, component materials, and performance requirements. Each coating has its properties and limitations, making it essential to match the coating to the application’s needs.
4.2. Application Process
The application process for conformal coatings can be complex and may require specialized equipment and expertise. Ensuring uniform coverage, avoiding defects, and controlling coating thickness are critical factors in achieving optimal performance.
4.3. Compatibility with Components
Some conformal coatings may react with certain materials or components, potentially causing damage or affecting performance. To avoid issues, it is essential to test the coating’s compatibility with all components before application.
4.4. Removal and Repair
Removing conformal coatings can be challenging in cases where repairs or modifications are needed. Different coatings require different removal methods; some may be more difficult to remove than others. The coating selection process should consider repairability and ease of coating removal.
5. Future Trends in Conformal Coatings
The field of conformal coatings is continuously evolving, with ongoing research and development leading to new advancements and trends.
5.1. Advanced Materials
Researchers are exploring new materials and formulations for conformal coatings to enhance their properties and performance. Advances in nanotechnology and polymers are leading to the development of coatings with improved barrier properties, flexibility, and environmental resistance.
5.2. Smart Coatings
Innovative coatings are an emerging trend involving incorporating sensors or functional elements into the coating. These coatings can provide real-time monitoring of environmental conditions or changes in the coating’s integrity, offering additional layers of protection and diagnostic capabilities.
5.3. Eco-Friendly Coatings
There is a growing emphasis on developing eco-friendly conformal coatings that minimize environmental impact. Water-based and low-VOC (volatile organic compound) coatings are becoming more common, aligning with sustainability goals and regulatory requirements.
5.4. Integration with Automation
Integrating conformal coating processes with automation and Industry 4.0 technologies enhances production efficiency and consistency. Automated coating systems equipped with advanced control and monitoring capabilities are improving the accuracy and quality of coating applications.
Conclusion
Conformal coatings protect electronic components and ensure their reliability and longevity. With various coating types and application methods available, manufacturers can choose the best solution. While there are challenges to consider, the benefits of conformal coatings make them a valuable investment in high-performance electronics. As technology advances, the field of conformal coatings will continue to evolve, offering new solutions and innovations to meet the demands of an ever-changing electronic landscape.
For more about choosing the best Conformal Coatings for Electronics Applications, you can pay a visit to DeepMaterial at https://www.pottingcompound.com/ for more info.
Recent Posts
- Influence of Encapsulation Thickness on the Heat Dissipation Performance and Electrical Insulation Performance of PCB
- Causes and Avoidance Methods of Bubble Generation in the Potting Process
- Technical Details on Controlling Parameters such as Temperature, Pressure, and Speed in the Potting Process to Ensure Potting Quality
- A Comprehensive Analysis of PCB Pretreatment Before Potting Process: A Crucial Link to Ensure the Performance and Reliability of Electronic Devices
- A Comprehensive Analysis of the Performance Differences of Epoxy Resin, Silicone Rubber and Polyurethane Encapsulation Materials
- How to Select Suitable Potting Materials for PCB According to the Working Environment
- What is PCB Potting
- The Evolution of Smart Watch Assembly Adhesive: A Key Component in Modern Wearable Technology
- Laptop Tablet Assembly Adhesive: The Key to Durable and Reliable Device Construction
- Power Bank Assembly Adhesive: The Essential Component for Building Durable Power Banks