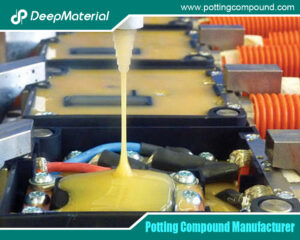
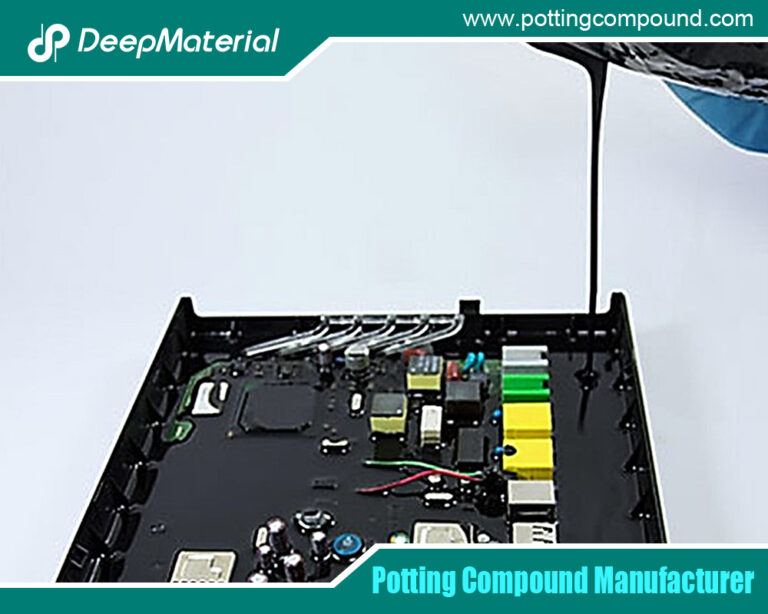
Electronic Coating Material Manufacturers: Innovating for the Future
- Electronic Potting Material Manufacturer
- July 26, 2024
- Acrylic Conformal Coating, acrylic vs silicone conformal coating, conformal coating electronics, conformal coating for electronics, conformal coating for pcb, conformal coating for pcb standards, Conformal Coating in Electronic, conformal coating in electronics market, conformal coating manufacturers, conformal coating material, conformal coating material types, conformal coating overspray, conformal coating pcb, conformal coating process, conformal coating silicone, conformal coating spray, conformal coating suppliers, conformal coating types, conformal coating waterproof, conformal coatings for electronics, contact electronic coatings technologies, Electronic Coating Material Manufacturers, electronic coating technologies, electronic coating technologies services
Electronic Coating Material Manufacturers: Innovating for the Future
In the fast-paced world of electronics, the role of electronic coating materials cannot be overstated. These materials protect electronic components from environmental damage, enhance performance, and ensure longevity. As the demand for smaller, more efficient, and more reliable electronic devices continues to rise, manufacturers of electronic coating materials are at the forefront of innovation. This article delves into the world of electronic coating material manufacturers, exploring their significance, the types of coatings they produce, technological advancements, and their impact on various industries.
The Significance of Electronic Coating Materials
Electronic coating materials, or conformal coatings, safeguard electronic components from environmental factors such as moisture, dust, chemicals, and temperature variations. These coatings provide a protective barrier that enhances the durability and performance of electronic devices. The significance of electronic coating materials can be summarised in the following points:
- Protection: Coatings shield electronic components from environmental contaminants, preventing corrosion and extending the lifespan of devices.
- Insulation: They provide electrical insulation, avoiding short circuits and ensuring the reliable operation of electronic circuits.
- Thermal Management: Certain coatings offer thermal management properties, such as dissipating heat and avoiding overheating components.
- Chemical Resistance: Coatings protect against chemical exposure, crucial in industries where devices are exposed to harsh environments.
- Enhanced Performance: By reducing the risk of failure and improving reliability, coatings contribute to the overall performance of electronic devices.
Types of Electronic Coating Materials
Electronic coating materials come in various types, each designed to meet specific requirements and applications. The most common types include:
- Acrylic Coatings: Acrylic coatings are widely used for their ease of application, excellent adhesion, and flexibility. They provide reasonable protection against moisture and humidity and are relatively easy to remove for rework.
- Epoxy Coatings: Epoxy coatings are known for their robust mechanical properties and excellent chemical resistance. They offer superior adhesion to various substrates and are often used in harsh environments.
- Silicone Coatings: Silicone coatings are highly flexible and provide excellent thermal stability. They are ideal for applications with extreme temperature variations and offer good moisture and chemical resistance.
- Polyurethane Coatings: Polyurethane coatings combine the advantages of acrylic and epoxy coatings, offering good flexibility, chemical resistance, and mechanical strength. They are often used in automotive and aerospace applications.
- Parylene Coatings: Parylene coatings are unique in that they are applied using a vapor deposition process. They provide a uniform, pinhole-free coating with exceptional moisture and chemical resistance. Parylene coatings are used in medical devices and critical electronic components.
Advancements in Electronic Coating Materials
The electronic coating material industry continuously evolves, driven by the need for more advanced and efficient solutions. Recent advancements have focused on improving these materials’ performance, application processes, and environmental impact. Some notable advancements include:
- Nanocoatings: Nanotechnology has revolutionised the electronic coating industry. Nanocoatings are ultra-thin layers that provide superior protection without adding bulk to the components. They offer enhanced moisture resistance, improved thermal management, and increased durability.
- UV-Curable Coatings: UV-curable coatings have gained popularity due to their rapid curing times and energy efficiency. These coatings can be applied and cured within seconds using UV light, reducing production time and costs.
- Environmentally Friendly Coatings: Manufacturers are developing coatings with reduced environmental impact as sustainability becomes a priority. Water-based coatings, for example, are being used as alternatives to solvent-based coatings, reducing volatile organic compound (VOC) emissions.
- Innovative Coatings: Smart coatings are designed to respond to environmental stimuli. For example, self-healing coatings can repair minor scratches and damages, while conductive coatings can change their properties in response to electrical signals.
- Enhanced Adhesion and Flexibility: Researchers are improving the adhesion and flexibility of coatings to meet the demands of flexible and wearable electronics. These advancements ensure that coatings can withstand bending and stretching without compromising performance.
Impact on Various Industries
Electronic coating materials play a pivotal role in numerous industries, ensuring the reliability and performance of electronic devices. Some of the critical industries benefiting from these materials include:
- Consumer Electronics: The consumer electronics industry relies heavily on coatings to protect smartphones, tablets, laptops, and other devices from environmental damage. Coatings enhance the durability and performance of these devices, ensuring they can withstand daily wear and tear.
- Automotive: In the automotive industry, electronic coatings protect critical components such as sensors, control units, and infotainment systems. Coatings ensure these components function reliably in harsh conditions, including temperature extremes, moisture, and chemical exposure.
- Aerospace: The aerospace industry demands high-performance coatings to protect avionics, communication systems, and other electronic components. These coatings must withstand extreme temperatures, pressure changes, and chemical exposure.
- Medical Devices: In the medical field, electronic coatings protect devices such as pacemakers, hearing aids, and diagnostic equipment. Coatings ensure these devices function reliably and are safe for use in the human body.
- Industrial Applications: Machinery and equipment rely on electronic coatings to protect control systems, sensors, and automation components. Coatings prevent corrosion and damage, ensuring the longevity and performance of industrial electronics.
- Telecommunications: The telecommunications industry uses coatings to protect infrastructure components such as antennas, switches, and routers. Coatings ensure these components function reliably in various environmental conditions.
Leading Manufacturers in the Industry
Several leading manufacturers populate the electronic coating material industry, each contributing to technological advancements and meeting the demands of various sectors. Some of the prominent manufacturers include:
- Henkel AG & Co. KGaA: Henkel is a global leader in adhesive technologies and electronic coatings. The company offers various conformal coatings, including acrylics, polyurethanes, and silicones, for multiple applications.
- Dow: Dow is known for its innovative solutions in the electronic coating industry. The company provides high-performance silicone coatings and other advanced materials to protect and enhance electronic devices.
- HumiSeal: HumiSeal specialises in the development and production of conformal coatings. The company offers a comprehensive range of coatings, including acrylics, polyurethanes, epoxies, and UV-curable coatings, known for their reliability and performance.
- Electrolube: Electrolube is a leading manufacturer of conformal coatings and other electronic protection solutions. The company’s products are widely used in automotive, aerospace, and industrial applications, offering excellent protection and reliability.
- MG Chemicals: MG Chemicals provides various conformal coatings, including acrylics, polyurethanes, silicones, and epoxies. The company focuses on delivering high-quality coatings that meet the stringent requirements of multiple industries.
- Chase Corporation: Chase Corporation offers a range of protective coatings and materials for the electronics industry. The company’s solutions are designed to enhance the reliability and performance of electronic components in demanding environments.
The Future of Electronic Coating Materials
The future of electronic coating materials is marked by continuous innovation and advancements. As technology evolves, manufacturers will likely focus on developing coatings that offer more excellent protection, enhanced performance, and reduced environmental impact. Some key trends shaping the future of the industry include:
- Increased Focus on Sustainability: With manufacturers developing eco-friendly coatings that reduce VOC emissions, sustainability will remain a key driver. Water-based coatings and recyclable materials will gain prominence.
- Integration with Emerging Technologies: Integrating electronic coatings with emerging technologies such as 5G, the Internet of Things (IoT), and artificial intelligence (AI) will create new opportunities and challenges. Coatings will need to meet the specific requirements of these technologies, such as high-frequency performance and data integrity.
- Customization and Flexibility: Manufacturers will focus on developing coatings that can be customised for particular applications and offer greater flexibility. This will be crucial for the growing demand for wearable electronics and flexible displays.
- Enhanced Performance Metrics: Coatings with improved thermal management, higher electrical insulation, and more excellent chemical resistance will be in demand. Advanced materials and nanotechnology will play a significant role in achieving these performance metrics.
- Regulatory Compliance: As regulations become more stringent, manufacturers must ensure their coatings comply with global standards for safety, environmental impact, and performance.
Conclusion
Electronic coating material manufacturers play a vital role in the electronics industry, providing essential protection and enhancing the performance of electronic devices. As technology advances, these manufacturers are at the forefront of innovation, developing coatings that meet the evolving needs of various industries. From consumer electronics to aerospace and medical devices, electronic coatings are indispensable in ensuring the reliability and longevity of modern electronic components. With a focus on sustainability, performance, and customization, the future of electronic coating materials looks promising, promising a new era of advancements and opportunities in the world of electronics.
For more about choosing the Top Electronic Coating Material Manufacturers: Innovating for the Future, you can pay a visit to DeepMaterial at https://www.pottingcompound.com/ for more info.
Recent Posts
- How to Select Suitable Potting Materials for PCB According to the Working Environment
- What is PCB Potting
- The Evolution of Smart Watch Assembly Adhesive: A Key Component in Modern Wearable Technology
- Laptop Tablet Assembly Adhesive: The Key to Durable and Reliable Device Construction
- Power Bank Assembly Adhesive: The Essential Component for Building Durable Power Banks
- Smartphone Assembly Adhesive: Enhancing Durability and Precision in Modern Devices
- TV Backplane Support and Reflective Film Bonding: A Comprehensive Guide
- Innovative Use of Compounded Materials in Electronic Device Housings: A Comprehensive Guide
- Enhancing Battery Pack Performance: A Deep Dive into Potting Materials, Benefits, and Applications
- A Comprehensive Guide to Industrial Conformal Coatings: Applications, Types, and Future Trends