Electronic Conformal Coating
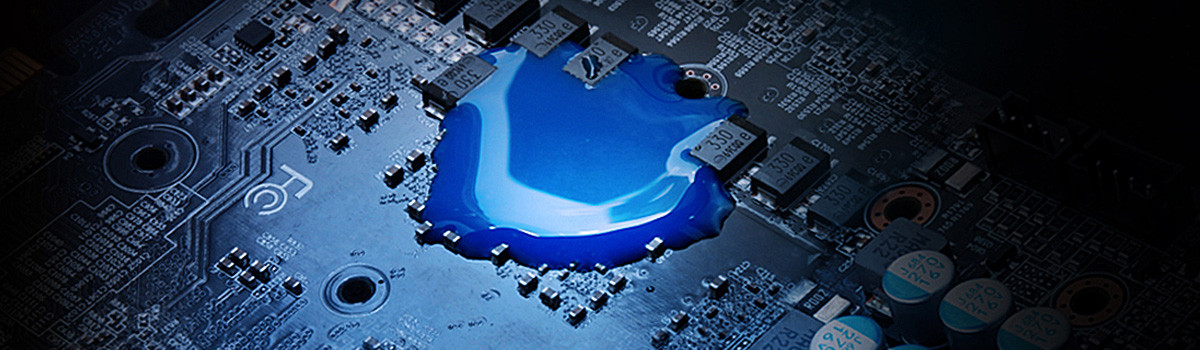
Electronic conformal coating is a crucial process in electronics manufacturing. It involves applying a protective layer over electronic components and circuitry. This coating safeguards against environmental factors such as moisture, dust, chemicals, and temperature fluctuations, thereby enhancing the reliability and longevity of electronic devices. Various coating materials and techniques are employed, each offering unique advantages tailored to specific applications. Understanding the fundamentals of electronic conformal coating is essential for ensuring optimal performance and durability of electronic assemblies.
Table of Contents
ToggleWhat is the electronic conformal coating?
Electronic conformal coating is a protective layer applied to electronic components and circuitry to safeguard them from environmental factors such as moisture, dust, chemicals, and temperature variations. This coating conforms to the contours of the components, ensuring complete coverage and protection. It’s typically made of insulating materials such as acrylics, silicones, urethanes, or epoxy resins.
The primary purpose of electronic conformal coating is to enhance the reliability and longevity of electronic devices by preventing corrosion, short circuits, and other damage caused by environmental exposure. Here’s a breakdown of its key features and benefits:
- Protection from Environmental Hazards: Conformal coatings act as a barrier against moisture, preventing corrosion of sensitive electronic components. They also shield against dust, dirt, chemicals, and other contaminants that can compromise performance or cause electrical shorts.
- Insulation: By providing electrical insulation, conformal coatings reduce the risk of electrical arcing or short circuits, especially in high-voltage applications. This insulation helps maintain signal integrity and prevents unintended current leakage.
- Thermal Management: Some conformal coatings offer thermal conductivity properties, aiding in heat dissipation from electronic components. Effective thermal management helps prevent overheating, which can degrade performance and reduce the lifespan of electronic devices.
- Mechanical Protection: The conformal coating adds a layer of mechanical protection, safeguarding components from physical damage such as scratches, abrasion, or vibration during handling or operation.
- UV Resistance: Certain conformal coatings are formulated to withstand exposure to ultraviolet (UV) light, which can cause degradation over time. UV-resistant coatings maintain their protective properties even in outdoor or high-exposure environments.
- Ease of Application: Conformal coatings can be applied using various methods, including spraying, brushing, dipping, or automated dispensing systems, making them suitable for small-scale and large-scale manufacturing processes.
- Transparent and Dielectric: Most conformal coatings are transparent, allowing visual inspection of components after application. They are also dielectric, meaning they do not conduct electricity, ensuring they do not interfere with the operation of electronic circuits.
Overall, electronic conformal coating plays a crucial role in enhancing electronic devices’ reliability, durability, and performance, making them suitable for a wide range of applications across industries such as automotive, aerospace, medical, and consumer electronics.
Why is conformal coating necessary for electronic components?
Conformal coating is necessary for electronic components primarily to protect them from environmental factors that could compromise their functionality and lifespan. Here are several reasons why conformal coating is essential:
- Moisture Protection: Electronic components are highly susceptible to damage from moisture and humidity, which can cause corrosion, short circuits, and electrical leakage. Conformal coating creates a barrier that prevents moisture from reaching sensitive circuitry areas, safeguarding against these issues.
- Chemical Resistance: Many electronic devices are exposed to chemicals in their operating environments, whether from cleaning agents, industrial processes, or atmospheric pollutants. Conformal coatings resist these chemicals, preventing corrosion and degradation of the components.
- Dust and Particle Shielding: Dust, dirt, and other airborne particles can settle on electronic components and cause overheating, electrical shorts, or signal interference. Conformal coating seals the components, keeping them from contamination and maintaining optimal performance.
- Temperature and Thermal Management: Temperature fluctuations can affect electronic components’ performance and reliability. Conformal coatings offer thermal insulation and conductivity properties, dissipating heat away from critical areas and helping to maintain consistent operating temperatures.
- Mechanical Protection: Electronic components can be subject to mechanical stress, such as vibrations, shocks, or abrasion, during transportation, installation, or operation. Conformal coatings add a layer of protection, reducing the risk of physical damage and prolonging the lifespan of the components.
- Electrical Insulation: Conformal coatings provide insulation, preventing electrical arcing, short circuits, and unintended current leakage. This insulation is particularly crucial in high-voltage applications where maintaining signal integrity and preventing safety hazards are paramount.
- UV Resistance: Exposure to ultraviolet (UV) light can degrade unprotected electronic components over time. Conformal coatings with UV-resistant properties maintain their protective integrity even in outdoor or high-exposure environments, extending the lifespan of the electronics.
Overall, conformal coating is indispensable for ensuring electronic components’ reliability, durability, and performance in a wide range of applications and operating conditions. It helps mitigate various risks posed by environmental factors, ensuring the longevity and functionality of electronic devices.
What are the primary environmental threats that conformal coating protects against?
Conformal coating is a protective layer applied to electronic circuitry to safeguard against environmental threats. Its primary function is insulation and protection against moisture, dust, chemicals, temperature fluctuations, and mechanical damage. These threats can severely compromise the performance and lifespan of electronic devices if left unprotected.
- Moisture and Humidity: One of the most significant threats to electronic components is moisture ingress. Moisture can lead to corrosion, short circuits, and electrical leakage, causing malfunctions or complete failure. Conformal coatings create a barrier that prevents moisture from reaching sensitive components, thereby preserving their functionality and reliability, particularly in humid environments or outdoor applications.
- Dust and Contaminants: Dust, dirt, and airborne contaminants can accumulate on circuit boards, leading to overheating, arcing, or electrical leakage. Conformal coatings act as a barrier against these particles, preventing their ingress and maintaining the integrity of the electronics. This is particularly important in industrial settings or areas with high airborne pollutants.
- Chemical Exposure: Electronic devices may come into contact with various chemicals during their lifespan, either during manufacturing processes or in their operational environment. Conformal coatings offer protection against chemical exposure, including acids, solvents, oils, and cleaning agents, which could otherwise degrade or corrode sensitive components.
- Temperature Extremes: Temperature fluctuations can cause the expansion and contraction of materials, leading to stress on electronic components and potential failure. Conformal coatings provide thermal insulation, helping to mitigate the effects of temperature extremes and ensuring stable performance over a wide range of operating conditions.
- Mechanical Shock and Vibration: Conformal coatings also offer mechanical protection against shock and vibration, which can occur during the handling, transportation, or operation of electronic devices. AdheringAdheres firmly to the circuit board helps dampen vibrations and prevent damage to solder joints or delicate components.
Conformal coating plays a crucial role in safeguarding electronic circuitry against moisture, dust, chemicals, temperature fluctuations, and mechanical damage, thereby enhancing electronic devices’ reliability, longevity, and performance in diverse environmental conditions.
How does conformal coating enhance the reliability of electronic devices?
Conformal coating is a critical component in enhancing the reliability of electronic devices by providing protection against a wide array of environmental hazards and operational stresses. Its application offers several key benefits that contribute to the overall robustness and longevity of electronic assemblies.
- Environmental Protection: Conformal coatings create a barrier that shields sensitive electronic components from moisture, dust, chemicals, and other contaminants. By preventing these environmental factors from reaching the circuitry, the coatings mitigate the risk of corrosion, short circuits, and electrical leakage, which can compromise device performance and reliability, particularly in harsh operating environments.
- Insulation and Dielectric Properties: Many conformal coatings possess excellent insulating properties, effectively isolating conductive traces and components from each other and external sources. This insulation helps prevent electrical shorts, arcing, and other issues that can arise from unintended contact between conductive elements, thus enhancing the reliability of the electronic assembly.
- Protection Against Mechanical Stress: Electronic devices are often subjected to mechanical stresses such as vibration, shock, and physical impact during handling, transportation, or operation. Conformal coatings provide a protective layer that helps dampen vibrations, absorb shocks, and distribute mechanical forces, reducing the risk of damage to solder joints, components, and traces. This mechanical protection contributes significantly to the device’s reliability, especially in applications where ruggedness is essential.
- Thermal Management: Some conformal coatings offer thermal management properties, dissipating heat generated during device operation. By facilitating heat transfer away from critical components, these coatings help prevent overheating, thermal stress, and premature failure, thereby improving the overall reliability of the electronic system.
- Long-Term Stability and Performance: By maintaining a stable environment around electronic components, conformal coatings help ensure consistent performance over time. They reduce the likelihood of degradation or drift in electrical properties, prolonging the operational lifespan of the device and minimizing the need for maintenance or replacement.
Conformal coating plays a vital role in enhancing the reliability of electronic devices by providing robust environmental protection, insulation, mechanical stability, thermal management, and long-term performance stability. Its application helps mitigate risks associated with environmental hazards and operational stresses, thereby increasing the overall dependability and durability of electronic assemblies in a wide range of applications.
What types of materials are commonly used for conformal coating?
Conformal coating is a protective material applied to electronic circuitry to protect it from environmental stresses such as moisture, chemicals, dust, and temperature extremes. The choice of coating material depends on factors such as the application requirements, environmental conditions, and desired properties. Several types of materials are commonly used for conformal coating:
- Acrylic Resins: Acrylic conformal coatings are popular due to their excellent moisture and abrasion resistance. They provide reasonable protection against humidity, salt spray, and chemicals. Acrylic coatings are known for their ease of application and relatively low cost, making them suitable for a wide range of applications.
- Polyurethane Resins: Polyurethane coatings offer superior chemical and solvent resistance compared to acrylics. They also provide excellent protection against moisture and humidity. Polyurethane coatings are known for their toughness and durability, making them suitable for harsh environments such as automotive and aerospace applications.
- Silicone Resins: Silicone conformal coatings are highly flexible and offer excellent resistance to extreme temperatures, ranging from very low to very high. They also provide reasonable protection against moisture, chemicals, and UV radiation. Silicone coatings, such as automotive electronics and outdoor LED lighting, are often used in applications where thermal cycling and flexibility are critical.
- Epoxy Resins: Epoxy coatings provide superior adhesion and mechanical strength. They offer excellent protection against moisture, chemicals, and abrasion. Epoxy coatings are known for their high dielectric strength, making them suitable for applications requiring electrical insulation, such as PCBs in harsh industrial environments.
- Parylene: Parylene coatings are deposited via vapor deposition, resulting in a thin, pinhole-free film. Parylene coatings offer excellent barrier properties against moisture, chemicals, and gases while maintaining the integrity of delicate electronic components. They are often used in medical devices, aerospace, and military applications where reliability and biocompatibility are critical.
Each type of conformal coating material has advantages and limitations, and the selection should be based on the application’s specific requirements to ensure optimal performance and reliability of the coated electronic devices.
How does the selection of conformal coating material impact performance?
The selection of conformal coating material plays a crucial role in determining the performance and longevity of electronic components and assemblies. Conformal coatings protect circuitry from environmental factors such as moisture, dust, chemicals, and temperature variations. The choice of coating material directly influences several critical aspects of performance:
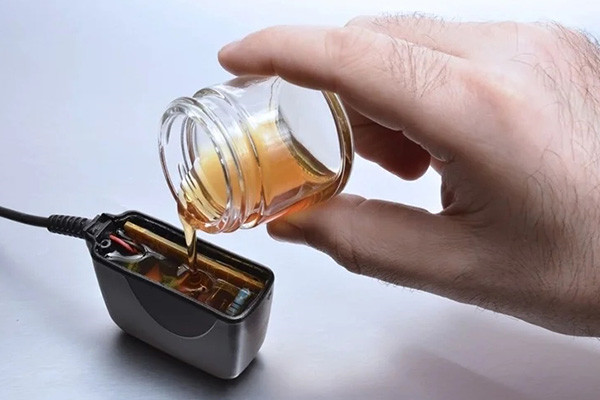
- Environmental Protection: Different materials offer varying degrees of protection against environmental hazards. Silicone-based coatings are known for their excellent resistance to moisture and high temperatures, making them suitable for harsh environments. Acrylic coatings offer good moisture resistance but may not withstand extreme temperatures or chemicals as well as silicone. Polyurethane coatings provide robust protection against chemicals but may be less flexible than silicone or acrylic.
- Electrical Insulation: Conformal coatings must insulate circuitry to prevent short circuits and electrical malfunctions. The dielectric properties of the coating material determine its effectiveness as an insulator. Silicone coatings typically exhibit high dielectric strength, making them ideal for critical electrical insulation applications.
- Adhesion: Proper adhesion of the coating to the substrate is essential for long-term performance. Some materials adhere better to certain types of surfaces than others. For instance, acrylic coatings often provide strong adhesion to many substrates, including metals and plastics, while silicone coatings may require surface treatments for optimal adhesion.
- Flexibility: Components subjected to mechanical stress or vibration require flexible coatings to prevent cracking or delamination. Silicone coatings are renowned for their flexibility, allowing them to withstand movement without compromising protection. Polyurethane coatings offer moderate flexibility but may become brittle over time, especially in cold environments.
- Chemical Resistance: Applications exposed to chemicals or solvents demand coatings that resist degradation. Polyurethane coatings are preferred for their exceptional chemical resistance, making them suitable for harsh industrial environments. Silicone coatings also exhibit good resistance to many chemicals but may degrade in the presence of certain solvents.
The selection of conformal coating material significantly impacts performance by influencing environmental protection, electrical insulation, adhesion, flexibility, and chemical resistance. Engineers must carefully evaluate the specific requirements of their application to choose the most suitable coating material for optimal performance and reliability.
What are the different methods of applying conformal coating?
Conformal coating is a protective layer applied to electronic circuitry to protect it from environmental factors such as moisture, dust, chemicals, and temperature extremes. Several methods are used for applying conformal coatings, each with its own advantages and suitability for different applications.
- Brush Application: This is one of the simplest methods for manually applying the conformal coating material using a brush. It’s suitable for small-scale production or repair work, offering flexibility and ease of application. However, it may result in uneven coating thickness and require skilled labor.
- Dipping: Components or entire circuit boards are submerged into a bath of conformal coating material. After dipping, the excess coating is drained off, and the board is dried. This method provides uniform coverage and is suitable for high-volume production. However, it may require masking specific areas and careful control of viscosity and drying parameters.
- Spraying: Conformal coating can be applied using automated spray equipment, similar to spray painting. This method offers reasonable control over coating thickness and can be used for manual and automated production lines. However, it requires proper ventilation and may result in overspray if not carefully controlled.
- Selective Coating: This method involves applying conformal coating only to specific circuit board areas, typically using a robotic dispenser. It offers precise control over coating placement and avoids masking or post-application trimming. Selective coating is suitable for complex PCB designs with components requiring protection but not coated.
- Conformal Coating Parylene Deposition: Parylene is a unique conformal coating material applied through vapor deposition. It forms a thin, uniform coating that penetrates crevices and around components, offering excellent protection without affecting circuit performance. However, this method requires specialized equipment and is typically used for high-reliability applications.
- Film Lamination: This method applies a pre-formed conformal coating film to the circuit board using heat and pressure. The film adheres to the surface, providing uniform coverage without liquid coatings. It offers good protection and is suitable for applications requiring high throughput and minimal waste.
Each method of applying conformal coating has advantages and limitations, and the choice depends on factors such as production volume, complexity of the circuit design, required level of protection, and available equipment and expertise.
What are the advantages and disadvantages of dip coating?
Dip coating is a versatile and widely used method for applying thin films onto substrates in various industries. Its advantages and disadvantages can vary depending on the application and materials involved.
Advantages:
- Simple Process: Dip coating is relatively simple, requiring minimal equipment and expertise compared to other coating methods. This simplicity often translates to lower costs and more straightforward implementation.
- Uniform Coating: Dip coating can produce uniform coatings with consistent thicknesses, especially on simple geometries. This uniformity is crucial for many applications, such as electronics or optics, where precise coating thickness is required for optimal performance.
- Broad Material Compatibility: Dip coating is compatible with various materials, including polymers, ceramics, metals, and composites. This versatility allows for the deposition of multiple coatings tailored to specific requirements, such as protection, insulation, or aesthetics.
- Controlled Thickness: By controlling parameters such as withdrawal speed and solution viscosity, dip coating offers precise control over coating thickness. This control enables the customization of coatings for different purposes, ensuring optimal performance and cost-effectiveness.
- High Throughput: Dip coating can be easily scaled up for high-throughput production, making it suitable for mass manufacturing applications. With automation, multiple parts can be coated simultaneously, improving efficiency and reducing production time.
Disadvantages:
- Limited to Simple Geometries: Dip coating is most suitable for substrates with simple geometries, such as flat surfaces or cylindrical shapes. Complex shapes or internal surfaces may be challenging to coat uniformly using this method, leading to uneven coating thickness or incomplete coverage.
- Waste Generation: Dip coating often generates excess coating solution, leading to material wastage and potential environmental concerns. Proper management of waste solutions is necessary to minimize environmental impact and maintain cost-effectiveness.
- Slow Processing Speed: While dip coating is capable of high throughput with automation, the process can be relatively slow compared to other coating methods. Slower processing speeds may limit its suitability for applications requiring rapid production cycles.
- Limited Thickness Control: While dip coating offers control over coating thickness, achieving extremely thin or thick coatings may be challenging. Thin films may suffer from inconsistencies or defects, while thick coatings may require multiple dips or alternative deposition methods.
- Surface Tension Effects: Surface tension effects can influence the uniformity of the coating, especially on substrates with irregular surfaces. Managing surface tension through additives or modifying coating parameters may be necessary to achieve the desired results.
Dip coating offers simplicity, uniformity, and material compatibility, making it a valuable technique for various applications. However, its limitations in coating complex geometries and challenges in precise thickness control should be considered when selecting a coating method for specific purposes.
How does spray coating compare to other application methods?
Spray coating is a versatile application method that offers several advantages compared to traditional methods like brushing, dipping, or rolling. Here’s a comparison of spray coating with other application methods:
- Efficiency: Spray coating is highly efficient as it allows for uniform coverage over large surfaces in a shorter time frame than brushing or rolling. This efficiency is particularly beneficial in industrial settings where speed and precision are essential for productivity.
- Uniformity: Spray coating ensures uniform application of the coating material, resulting in consistent thickness and coverage across the entire surface. This uniformity is challenging to achieve consistently with brushing or rolling methods, where variations in pressure and technique can lead to uneven coating.
- Accessibility: Spray coating can reach areas that are difficult to access with other methods, such as intricate crevices, complex geometries, or irregular surfaces. This accessibility makes spray coating ideal for objects with intricate designs or uneven surfaces, which may be challenging to coat effectively using brushing or rolling techniques.
- Thickness Control: Spray coating provides better control over the thickness of the coating layer. By adjusting parameters such as spray pressure, nozzle size, and distance from the surface, operators can achieve the desired thickness more precisely compared to brushing or rolling, where thickness control may be more variable.
- Waste Reduction: Spray coating minimizes material waste compared to other methods. Excess coating material can accumulate on tools or drip off the surface with brushing or rolling, leading to higher material consumption and cleanup efforts. In contrast, spray coating directs the material precisely onto the surface, reducing waste and minimizing cleanup requirements.
- Speed: Spray coating offers faster application compared to brushing or rolling methods. This speed is particularly advantageous for large-scale projects or production lines where time is of the essence. Additionally, the quick drying time of spray-applied coatings further enhances efficiency by reducing downtime between coats or handling.
While spray coating offers numerous advantages, it also has limitations, such as overspray issues, environmental concerns related to airborne particles, and initial setup costs for equipment and ventilation systems. Overall, spray coating remains a preferred choice for many applications due to its efficiency, uniformity, and versatility.
What factors should be considered when choosing a conformal coating method?
When selecting a conformal coating method, several factors must be carefully considered to ensure electronic components’ optimal performance and protection. These factors include:
- Environmental Conditions: The operating environment of the electronic assembly plays a crucial role in determining the type of conformal coating method to use. Factors such as temperature extremes, humidity levels, chemical exposure, and potential mechanical stressors must be considered. For example, a more robust and moisture-resistant coating method like perylene or silicone may be preferred if the electronic device operates in a harsh environment with high humidity or exposure to corrosive substances.
- Substrate Compatibility: The compatibility of the conformal coating material with the substrate material is essential to ensure proper adhesion and performance. Different substrates, such as printed circuit boards (PCBs), flexible circuits, or sensitive components, may require specific coating formulations to prevent damage or interference with functionality.
- Application Method: Various application methods are available for applying conformal coatings, including spray coating, dip coating, brush coating, and selective coating. The choice of application method depends on factors such as production volume, component complexity, coating thickness requirements, and accessibility of the components. For instance, spray coating may be suitable for high-volume production lines, while selective coating may be preferred for assemblies with complex geometries or sensitive areas that require masking.
- Coating Thickness: The desired thickness of the conformal coating layer is a critical consideration, as it influences the level of protection provided to the electronic components. Different coating methods offer varying degrees of control over the coating thickness. For example, dip coating typically results in a uniform but thicker layer, while selective coating allows precise control over the thickness in specific areas.
- Regulatory Compliance: Compliance with industry standards and regulations, such as IPC standards or RoHS directives, may influence the choice of conformal coating method and material. It’s essential to select coatings that meet relevant regulatory requirements for environmental safety, performance, and reliability.
By carefully evaluating these factors, manufacturers can choose the most appropriate conformal coating method to ensure electronic assemblies’ long-term reliability and functionality in their intended application environments.
Can the conformal coating be applied manually?
Yes, the conformal coating can be applied manually, although it’s typically done with specialized tools and techniques to ensure proper coverage and consistency. Conformal coating is a protective material used in electronic circuitry to protect it from moisture, dust, chemicals, and temperature extremes. While automated application methods are standard in industrial settings for their precision and efficiency, manual application remains a viable option, especially for small-scale operations or when dealing with irregularly shaped components.
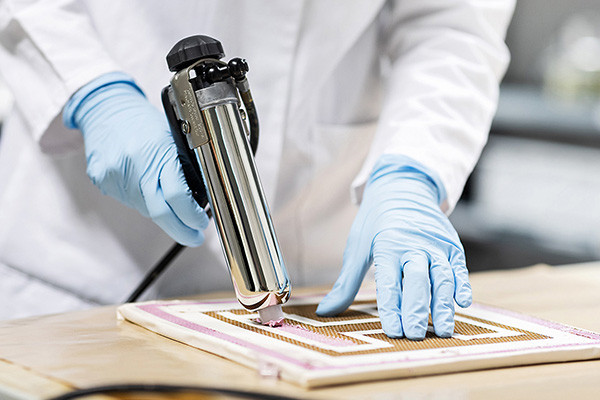
The manual application of conformal coating involves several key steps:
- Preparation: Before applying the coating, the surface of the circuit board must be thoroughly cleaned and prepared to ensure adhesion and uniform coverage. This may involve cleaning with solvents and removing any contaminants or residues.
- Selection of Coating Material: Depending on the specific requirements of the application, different types of conformal coatings may be chosen, such as acrylics, silicones, urethanes, or epoxy-based coatings. The choice depends on factors like desired protection level, operating environment, and ease of application.
- Application: Manual application methods include brushing, spraying, dipping, or even selective coating using a syringe. Each method has its advantages and is chosen based on factors like the board’s complexity, the coating material’s viscosity, and the desired coating thickness.
- Curing: After application, the coating must be cured to achieve its protective properties fully. Curing methods vary depending on the coating material used and may involve air drying, thermal curing, or exposure to UV light.
- Inspection and Quality Control: Once the coating is applied and cured, it undergoes inspection to ensure uniform coverage without any defects or areas of incomplete coverage. This step is crucial to guarantee the reliability and longevity of the coated electronics.
While manual application of conformal coating requires more labor and attention to detail than automated methods, it offers flexibility. It can be cost-effective for smaller production runs or prototypes. However, it’s essential to maintain consistency and precision in the application process to ensure the reliability of the coated electronics.
What are the challenges associated with the manual application of conformal coating?
Manual application of conformal coating, while common in specific industries, poses several challenges that can affect the quality and consistency of the coating as well as the efficiency of the process:
- Consistency: Achieving consistent thickness and coverage across the entire board can be difficult with manual application. Variations in operator technique, speed, and concentration can lead to uneven coating distribution, potentially leaving areas unprotected or causing over-coating.
- Quality Control: Manual application increases the risk of defects like bubbles, drips, and uneven edges. These defects can compromise the integrity of the coating and may lead to reliability issues or failure of the electronic components over time.
- Operator Skill and Training: Manual application requires skilled operators trained to apply the coating accurately and efficiently. Inexperienced operators may need help to achieve the desired results, leading to increased scrap and rework.
- Health and Safety Concerns: Many conformal coatings contain volatile organic compounds (VOCs) and other hazardous chemicals. Manual application increases the risk of operators’ exposure to these chemicals, requiring appropriate safety measures and ventilation systems to be in place.
- Time and Labor Intensive: Manual application is generally slower and more labor-intensive than automated methods. This can increase production times and higher labor costs, especially for large-scale manufacturing operations.
- Limited Accessibility: Some electronic assemblies may have complex geometries or components with tight spaces, making it challenging for operators to reach all areas with manual application methods. This can result in inadequate coverage and reduced protection for critical components.
- Environmental Conditions: Manual application is sensitive to environmental factors such as temperature, humidity, and airflow. Fluctuations in these conditions can impact the drying and curing process of the coating, affecting its performance and longevity.
- Traceability and Documentation: Manual applications may need more traceability and documentation provided by automated systems. This can make tracking the application process more difficult and ensure compliance with quality standards and regulatory requirements.
Addressing these challenges often involves a combination of operator training, process optimization, and potentially transitioning to automated application methods where feasible to improve consistency, efficiency, and overall quality of the conformal coating process.
What role does curing play in the conformal coating process?
Curing is a critical step in the conformal coating process. It involves applying a protective material layer onto electronic circuitry to safeguard it from environmental factors such as moisture, dust, chemicals, and temperature extremes. Curing refers to drying and hardening the conformal coating material after applying it to the substrate. This step is essential for achieving the desired protective properties and ensuring the coating adheres firmly to the surface.
The curing process serves several crucial roles in conformal coating:
- Chemical Crosslinking: Many conformal coating materials, such as acrylics, silicones, and urethanes, undergo chemical reactions during curing that result in crosslinking. Crosslinking creates a network of chemical bonds within the coating, enhancing its strength, durability, and resistance to environmental stressors. This chemical transformation also improves the coating’s adhesion to the substrate, preventing it from delaminating or peeling off over time.
- Evaporation of Solvents: Some conformal coating formulations contain volatile solvents that facilitate application but must be removed to achieve optimal performance. During curing, these solvents evaporate from the coating, leaving a solid protective layer behind. Proper solvent evaporation is crucial for preventing defects like bubbles, blisters, or uneven coating thickness, which can compromise the effectiveness of the protective barrier.
- Physical Hardening: Besides chemical changes, curing involves the physical hardening of the coating material. As the solvent evaporates and chemical reactions occur, the coating transforms from a liquid or gel-like state to a solid, continuous film. This solidification process enhances the coating’s mechanical properties, making it more resistant to abrasion, scratching, and mechanical stress.
- Temperature and Time Control: Curing conditions, including temperature and duration, must be carefully controlled to ensure uniformity and consistency across the coated surface. Variations in curing parameters can affect the final properties of the coating, including its thickness, adhesion, flexibility, and electrical insulation characteristics. Optimizing curing conditions helps achieve the desired balance between rapid production throughput and high-quality coating performance.
Curing plays a crucial role in the conformal coating process by chemically transforming the coating material, evaporating solvents, physically hardening the coating, and controlling key parameters to ensure consistent and reliable protection for electronic circuitry in various environmental conditions. Proper curing is essential for maximizing the performance and longevity of conformal coatings in demanding applications.
How does curing affect the properties of the coating?
Curing is a critical process in coating applications that profoundly influences the properties and performance of the final product. Whether it’s paint, varnish, epoxy, or any other coating, curing involves the chemical or physical transformation of the coating material from a liquid or semi-liquid state to a solid state. This transformation brings about several critical changes in the properties of the coating:
- Hardness: Curing typically leads to an increase in hardness. As the coating material solidifies, it forms a more rigid and durable surface. This hardness protects against physical damage, wear, and abrasion.
- Adhesion: Proper curing enhances the adhesion of the coating to the substrate. During the curing process, the coating material forms molecular solid bonds with the substrate surface, ensuring better adhesion and minimizing the risk of delamination or peeling.
- Chemical Resistance: Cured coatings often exhibit improved resistance to chemicals, solvents, acids, and other environmental factors. This resistance is essential for protecting the substrate from corrosion, degradation, and staining.
- Durability: Curing enhances the overall durability and longevity of the coating. An adequately cured coating is less prone to cracking, chipping, or fading over time, extending the coated surface’s lifespan.
- Appearance: Curing can influence the aesthetic qualities of the coating, such as gloss level, texture, and color retention. Proper curing ensures uniformity in the coating’s appearance and minimizes defects like orange peel or solvent popping.
- Mechanical Properties: Curing affects various mechanical properties of the coating, including flexibility, tensile strength, and impact resistance. These properties determine how well the coating can withstand bending, stretching, or sudden impacts without cracking or rupturing.
- Film Formation: Curing facilitates the formation of a continuous, uniform film across the substrate surface. This film acts as a barrier, protecting against moisture, UV radiation, and other environmental factors.
Curing is a crucial step in coating application that significantly impacts the coating’s hardness, adhesion, chemical resistance, durability, appearance, mechanical properties, and film formation. Proper curing ensures the coating delivers optimal performance and protection over its lifespan.
Are there specialized coatings for specific electronic applications?
Specialized coatings are crucial in various electronic applications, offering protection, enhancing performance, and enabling advanced functionalities. Here are some examples:
- Conformal Coatings: These coatings are applied to printed circuit boards (PCBs) to protect them from moisture, dust, chemicals, and other environmental factors. Common materials include acrylics, silicones, urethanes, and epoxies. Conformal coatings provide insulation and prevent corrosion, extending the lifespan of electronic components.
- Anti-Reflective (AR) Coatings: AR coatings are essential for optical components such as lenses, displays, and sensors. They minimize surface reflections, improving contrast and image quality. In electronic devices like cameras, AR coatings enhance performance in various lighting conditions, reducing glare and ghosting.
- Thermal Management Coatings: These coatings facilitate heat dissipation in electronic devices, preventing overheating and maintaining optimal operating temperatures. Thermal interface compounds (TICs) and phase-change materials (PCMs) are applied between heat-generating components and heat sinks to enhance thermal conductivity.
- Hydrophobic/Oleophobic Coatings: These coatings repel water and oils, minimizing the risk of damage from spills and fingerprints on electronic screens, lenses, and touch surfaces. They improve visibility and maintain device functionality in wet or oily environments.
- EMI Shielding Coatings: Electromagnetic interference (EMI) can disrupt electronic signals and affect device performance. EMI shielding coatings contain conductive materials like metals or carbon to block or redirect electromagnetic radiation, ensuring signal integrity and compliance with regulatory standards.
- Anti-Static Coatings: Electrostatic discharge (ESD) can damage sensitive electronic components during handling and operation. Anti-static coatings provide a controlled path for static electricity dissipating, protecting devices from ESD-related failures and malfunctions.
- UV-Curable Coatings: UV-curable coatings offer rapid curing times and excellent adhesion properties, making them suitable for high-speed manufacturing. They are used in applications such as PCB protection, encapsulation of components, and enhancing surface durability.
Specialized coatings in electronic applications continue to evolve, driven by advances in materials science and the demand for improved performance, reliability, and miniaturization in electronic devices. As technology advances, developing novel coatings tailored to specific electronic functions and requirements will continue to play a crucial role in enabling innovation in various industries.
What considerations are essential when selecting a conformal coating for aerospace electronics?
Selecting a conformal coating for aerospace electronics involves carefully considering several factors to ensure optimal performance, reliability, and compliance with industry standards. Here are key considerations:
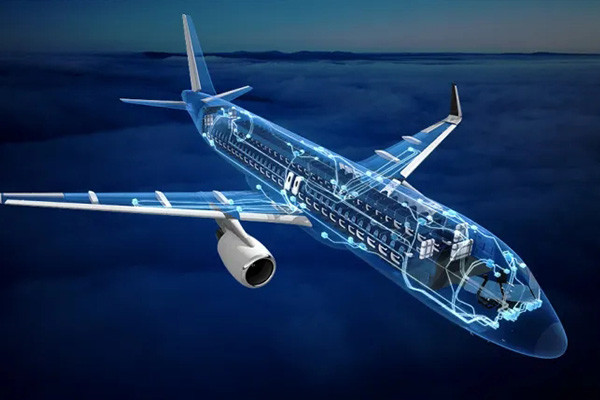
- Environmental Durability: Aerospace electronics operate in harsh environments with extreme temperatures, high humidity, vibration, and chemical exposure. The conformal coating must protect against these conditions to prevent corrosion, moisture ingress, and electrical failures.
- Chemical Resistance: Aerospace applications may involve exposure to fuels, hydraulic fluids, solvents, and other chemicals. The coating should resist these substances to maintain its integrity and protective properties over time.
- Temperature Stability: Aerospace electronics experience wide temperature fluctuations during flight, from cold at high altitudes to high temperatures near engines or avionics systems. The conformal coating must maintain its performance and adhesion across this temperature range without cracking, delaminating, or degrading.
- Electrical Properties: The coating should not interfere with the electrical functionality of the components it protects. It must provide sufficient insulation resistance and dielectric strength to prevent leakage currents and shorts, especially in high-voltage applications.
- Adhesion: Proper adhesion to the substrate is critical for the conformal coating’s long-term effectiveness. It should bond well with materials commonly used in aerospace electronics, including PCB substrates, solder joints, and component leads.
- Thickness Control: Aerospace electronics often have tight space constraints and delicate components. The conformal coating should be applied and controlled to achieve the desired thickness without bridging, pooling, or causing interference with mechanical or thermal interfaces.
- Conformance to Standards: Compliance with industry standards such as MIL-I-46058, IPC-CC-830, and relevant aerospace specifications is essential. The chosen conformal coating should meet or exceed these standards for performance, reliability, and safety in aerospace applications.
- Repairability and Workability: In the event of maintenance or repairs, the conformal coating should be easy to remove and reapply without damaging the underlying electronics or compromising the integrity of the coating system.
By considering these factors, aerospace engineers can select a conformal coating that provides robust protection and reliability for electronics in demanding aerospace environments.
How does conformal coating contribute to the protection of automotive electronics?
Conformal coating is vital in safeguarding automotive electronics by providing a protective barrier against various environmental and operational hazards. This thin, protective layer, typically made of materials like acrylic, silicone, or urethane, adheres to the surface of electronic components, forming a conformal and insulating film. Here’s how conformal coating contributes to the protection of automotive electronics:
- Moisture and Chemical Resistance: Automotive environments are subjected to moisture, chemicals, oils, and other fluids that can infiltrate electronic circuits, leading to corrosion and short circuits. Conformal coatings are a barrier, preventing these substances from reaching sensitive electronic components and causing damage.
- Dust and Debris Protection: Dust, dirt, and debris are omnipresent in automotive environments, mainly off-road or industrial settings. Conformal coatings encapsulate electronic assemblies, shielding them from particulate matter that could compromise functionality or cause abrasion-related failures.
- Vibration and Mechanical Shock Absorption: Vehicles encounter various vibration levels and mechanical shock during operation. Conformal coatings provide a degree of cushioning and shock absorption, reducing the risk of damage to delicate electronic components due to these mechanical stresses.
- Thermal Management: Automotive electronics generate heat during operation, and excessive heat can degrade performance and reliability. Some conformal coatings offer thermal management properties, dissipating heat away from sensitive components and ensuring optimal operating temperatures.
- Electrical Insulation: Conformal coatings serve as insulators, preventing electrical short circuits and leakage between adjacent conductive traces or components. This insulation capability is crucial for maintaining the integrity of electronic circuits in automotive applications.
- UV Protection: Exposure to sunlight’s ultraviolet (UV) radiation can degrade unprotected electronic components over time. Conformal coatings with UV-resistant properties shield automotive electronics from UV-induced damage, prolonging their lifespan and reliability.
- Environmental Sealing: Conformal coatings provide ecological sealing, safeguarding electronic assemblies from environmental factors such as humidity, salt spray, and temperature fluctuations commonly encountered in automotive settings.
Conformal coatings offer a comprehensive solution for protecting automotive electronics against a wide range of environmental, mechanical, and electrical hazards. By providing moisture resistance, dust protection, shock absorption, thermal management, electrical insulation, UV protection, and environmental sealing, they help enhance the reliability, longevity, and performance of electronic systems in vehicles.
Are there environmentally friendly options for conformal coating?
Conformal coating is a protective layer applied to electronic circuitry to guard against environmental factors such as moisture, dust, chemicals, and temperature extremes. While traditional conformal coatings have raised concerns due to their environmental impact, there are indeed environmentally friendly options available:
- Water-based coatings: These coatings use water as a solvent instead of harmful chemicals like solvents based on volatile organic compounds (VOCs). Water-based coatings significantly reduce VOC emissions, making them environmentally friendly. They are also easier to handle and dispose of compared to solvent-based coatings.
- UV-curable coatings: UV-curable coatings are cured using ultraviolet (UV) light instead of heat, reducing energy consumption and emissions associated with the curing process. These coatings often contain fewer hazardous substances than solvent-based ones, making them a greener alternative.
- Silicone-based coatings: Silicone-based coatings are known for their durability and resistance to extreme temperatures and harsh chemicals. They are also less harmful to the environment than solvent-based coatings because they have lower VOC emissions and are less toxic.
- Bio-based coatings: These are derived from renewable resources such as plant oils, natural resins, and other organic materials. These coatings offer a sustainable alternative to conventional coatings derived from fossil fuels. They can be formulated to provide adequate protection while minimizing environmental impact.
- Parylene coatings: Parylene coatings are applied using a vacuum deposition process, eliminating solvents and producing minimal waste. Parylene coatings are biocompatible, chemically inert, and offer excellent protection against moisture, making them suitable for environmentally sensitive applications.
- Recyclable coatings: Some manufacturers are developing conformal coatings that can be easily removed and recycled, reducing waste and environmental impact. These coatings are designed to provide adequate protection while allowing for easy rework or refurbishment of electronic components.
Overall, environmentally friendly conformal coating options are available. These options offer effective protection for electronic components while minimizing environmental impact through the use of water-based formulations, UV curing, silicone-based materials, bio-based resources, parylene coatings, and recyclable formulations. Adopting these greener alternatives can contribute to sustainable manufacturing practices in the electronics industry.
What quality control measures are employed during the conformal coating process?
Quality control measures are critical during the conformal coating process to ensure coated electronic components’ consistency, reliability, and performance. Several vital measures are employed throughout the process:
- Surface Preparation: Before applying conformal coating, thorough surface cleaning and preparation are essential. Quality control measures include visual inspection and cleanliness testing to ensure the substrate is free from contaminants such as oils, dust, and residues that could compromise coating adhesion and performance.
- Coating Thickness Control: Maintaining the correct coating thickness is crucial for achieving the desired level of protection without causing electrical interference or other issues. Quality control measures include using precision coating equipment with calibrated deposition rates and monitoring techniques like thickness measurement tools like profilometers or eddy current sensors.
- Uniformity Inspection: Ensuring uniform coverage of the conformal coating across the entire surface of the electronic component is vital for adequate protection. Quality control measures involve visual inspection, automated vision systems, or techniques like fluorescence inspection to detect any areas of uneven coating or missed spots.
- Adhesion Testing: Assessing the adhesion strength between the conformal coating and the substrate is essential to prevent delamination or peeling. Quality control measures include performing adhesion tests such as tape testing, cross-hatch adhesion tests, or pull-off tests according to industry standards to evaluate the integrity of the coating-substrate bond.
- Cure Validation: For coatings that require curing, verifying the completeness of the curing process is critical to ensure proper performance and durability. Quality control measures involve monitoring curing parameters such as time, temperature, and humidity and conducting post-cure inspections and testing to confirm adequate cross-linking and polymerization.
- Environmental Testing: Electronic components coated with conformal coatings are often subjected to harsh environmental conditions. Quality control measures include subjecting coated samples to environmental stress tests such as thermal cycling, humidity exposure, salt fog testing, or chemical resistance testing to evaluate the coating’s performance under real-world conditions.
By implementing these quality control measures throughout the conformal coating process, manufacturers can ensure coated electronic components’ reliability, durability, and effectiveness, ultimately improving product quality and customer satisfaction.
How does the thickness of conformal coating affect its performance?
Conformal coating, a protective material applied to electronic circuitry to guard against environmental factors, has its performance closely tied to its thickness. The thickness of the coating plays a critical role in determining its effectiveness in providing insulation, protection from moisture, dust, chemicals, and mechanical stress, and maintaining electrical properties.
Firstly, a thicker conformal coating provides better insulation. It creates a barrier between conductive elements on the circuit board, preventing short circuits and leakage currents. However, the excessive thickness can increase the capacitance between traces, potentially affecting signal integrity and circuit performance.
Secondly, the thickness affects protection from environmental factors. Thicker coatings offer enhanced resistance to moisture and humidity ingress, which is crucial for electronics operating in harsh conditions. They also provide better protection against dust, dirt, and chemical contaminants. However, the choice of coating material is equally important, as different formulations offer varying levels of resistance to specific environmental stressors.
Furthermore, mechanical robustness is influenced by coating thickness. A thicker coating can absorb more mechanical shock and vibration, thus safeguarding delicate components from damage. This is particularly important in applications with rough handling or high vibration levels.
However, excessively thick coatings have drawbacks. Beyond a certain point, they can impede heat dissipation from components, leading to thermal issues and reduced reliability. Additionally, thicker coatings may be more prone to cracking or delamination due to thermal cycling or mechanical stress, compromising their protective function.
The thickness of a conformal coating significantly impacts its performance in terms of insulation, environmental protection, and mechanical robustness. While thicker coatings generally offer better protection, a balance must be struck to avoid negative effects such as increased capacitance or thermal problems. The optimal thickness depends on factors such as the specific application, environmental conditions, and the type of components being protected. Therefore, careful consideration and testing are essential when determining the appropriate coating thickness for a given electronics application.
Conclusion:
Electronic conformal coating is an indispensable aspect of electronics manufacturing, protecting against environmental stresses. With various materials and application methods available, selecting the appropriate conformal coating is crucial for ensuring the reliability and longevity of electronic assemblies. By understanding the fundamentals and addressing specific application requirements, manufacturers can optimize the performance and durability of electronic devices in diverse industries.
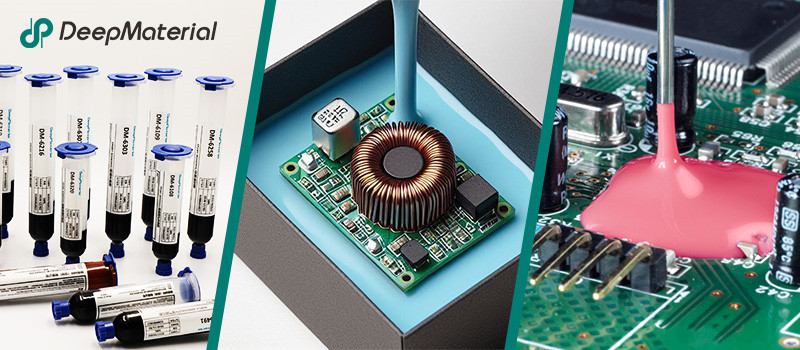
About DeepMaterial
DeepMaterial is a trusted supplier of encapsulant materials that are used in electronics manufacturing worldwide. From chip on board encapsulants such as glob top material to conformal coatings, underfills, low pressure molding, and potting solutions, DeepMaterial offers a full range of circuit board protection materials that effectively protect circuit boards while help reduce costs. More…Deepmaterial is a the manufacturer of epoxy adhesives including hardeners, metalbond, and metal filled resins. Structural, toughened medium viscosity, and non-sag adhesives are also offered. Some adhesives are resistant to thermal shock, chemical, vibration dampening, and impact. Suitable for metals, plastics, wood, and ceramics. Serves electronics, aerospace, automotive, tooling, marine, and construction industries. REACH and RoHS compliant. FDA approved. UL listed. Meets military specifications. We are the one of best adhesive manufacturers in China.
Blogs & News
Potting compounds are at the frontline of electronics assembly, delivering effective protection in challenging environmental conditions while improving mechanical strength and offering high electric insulation. Used within a variety of industries, electrical potting compounds are found within a broad range of consumer electronics, as well as used in applications across the automotive, aerospace, and other industries where electronic assemblies are prevalent.
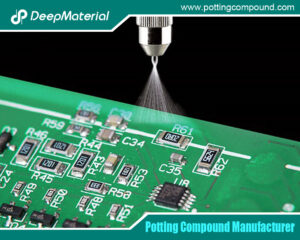
The Ultimate Guide to Electrical Potting Compound and Market Application
The Ultimate Guide to Electrical Potting Compound and Market Application In the modern world of electronics, where devices are increasingly compact and exposed to harsh
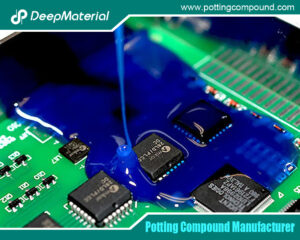
The Top Polyurethane Potting Compound
The Top Polyurethane Potting Compound In the fast-evolving world of electronics and industrial manufacturing, protecting sensitive components from environmental hazards is critical to ensuring reliability
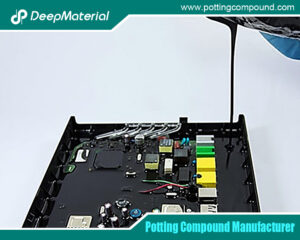
Advanced Epoxy Potting Compound for Superior Electronic Protection
Advanced Epoxy Potting Compound for Superior Electronic Protection In the realm of electronics and industrial manufacturing, protecting sensitive components from environmental hazards is critical to
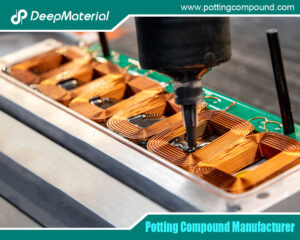
Waterproof Potting Compound: A Comprehensive Guide
Waterproof Potting Compound: A Comprehensive Guide In today’s technology-driven world, protecting sensitive electronic components from environmental hazards is paramount. One of the most effective solutions
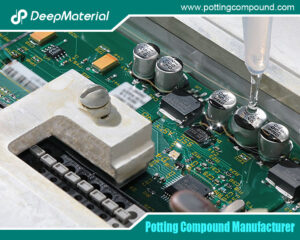
Silicone Potting Compound for Electronics
Silicone Potting Compound for Electronics In the rapidly evolving world of electronics, ensuring the reliability, durability, and performance of electronic components is paramount. One critical
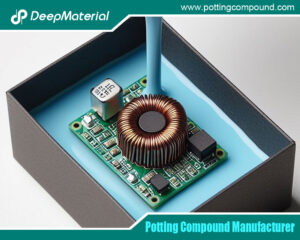
Potting Compound vs. Epoxy: A Comprehensive Comparison
Potting Compound vs. Epoxy: A Comprehensive Comparison In the world of electronics, manufacturing, and material encapsulation, two terms frequently come up: potting compounds and epoxy.