Home > Potting Compound > Electronic Potting Compound
Electronic Potting Compound
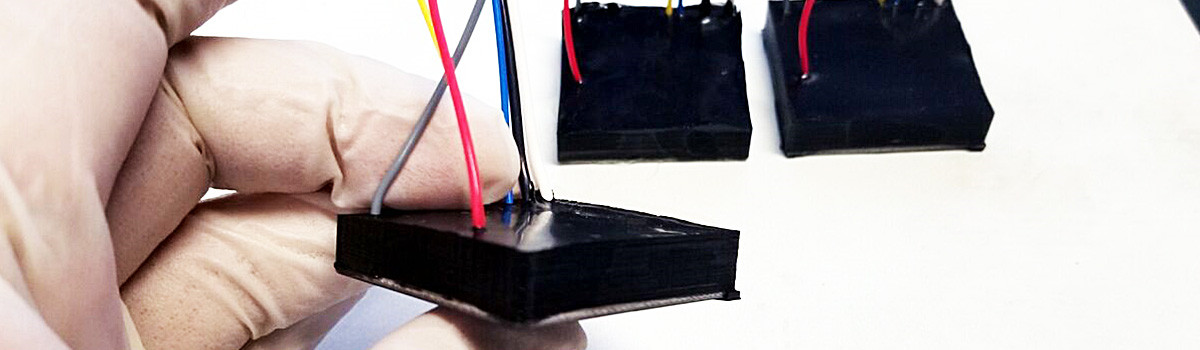
Electronic potting compound is a crucial material used in various industries, particularly in electronics manufacturing, to protect sensitive electronic components from environmental factors such as moisture, dust, and vibrations. This page aims to provide comprehensive insights into electronic potting compounds, covering its composition, applications, benefits, and more.
Table of Contents
ToggleWhat is Electronic Potting Compound?
Electronic potting compound is a specialized material utilized in the electronics industry to protect and encapsulate electronic components. It is a thermosetting polymer resin poured or injected into enclosures or around electronic assemblies to create a shield against external elements like moisture dust, chemicals, and vibration. The primary aim of potting compounds is to shield sensitive electronic components from these external elements, enhancing their reliability, durability, and longevity.
Potting compounds are available in various formulations tailored to specific application requirements and environmental conditions. Common types include epoxy, silicone, and polyurethane resins, offering distinct properties such as temperature resistance, flexibility, adhesion, and chemical resistance. These materials are adaptable to fit the requirements of different electronic assemblies, ensuring optimal performance in diverse operating environments.
The potting process involves carefully encapsulating electronic components or assemblies within a protective shell of the potting compound. Techniques such as casting, molding, or potting under vacuum are typically employed to ensure complete coverage and proper adhesion to the components. Once cured, the potting compound forms a solid, insulating barrier around the electronics, effectively sealing them from external threats.
Electronic potting compound plays a crucial role in safeguarding electronic components from environmental hazards and mechanical stresses, thereby ensuring the reliability and longevity of electronic devices across various industries.
How does Electronic Potting Compound Work?
Electronic potting compounds encapsulate electronic components within a protective material to shield them from environmental stressors. Here’s a breakdown of how they function:
- Encapsulation:Electronic potting compounds typically consist of polymers such as epoxy, silicone, or urethane, which are poured or dispensed around electronic assemblies.
- Filling Voids:The compound fills voids and crevices around the components, providing a seamless protective barrier.
- Preventing Moisture Damage:One primary role is to stop the ingress of moisture, which can cause corrosion and short circuits. The compound forms a waterproof seal, safeguarding sensitive electronics from humidity and water exposure.
- Enhancing Mechanical Stability:By surrounding components with a solid material, electronic potting compounds improve mechanical stability, reducing the risk of damage from vibration, shock, or impact.
- Thermal Management:Some compounds are formulated to have excellent thermal conductivity, helping to dissipate heat generated by electronic devices, thus improving overall performance and reliability.
- Electrical Insulation:Electronic potting compounds also serve as insulators, preventing contact between conductive components and reducing the risk of electrical short circuits.
- Chemical Resistance:They resist various chemicals, protecting electronic assemblies from corrosive substances in their operating environments.
Overall, electronic potting compounds act as a shield, providing a protective cocoon around electronic assemblies, ensuring their longevity and reliability in demanding applications.
What are the Components of Electronic Potting Compounds?
Understanding the composition of electronic potting compounds is crucial for selecting the suitable material to protect electronic components effectively. These compounds are formulated using a combination of specific components tailored to provide the desired properties such as adhesion, flexibility, thermal conductivity, and resistance to environmental factors. Let’s delve into the key elements that make up electronic potting compounds:
Resin Systems:
- Epoxy:Commonly used for its excellent adhesion, mechanical strength, and chemical resistance.
- Silicone:Offers flexibility, high-temperature resistance, and good electrical insulation properties, making it a versatile choice for electronic potting applications.
- Polyurethane:Provides flexibility, impact resistance, and thermal stability.
Fillers and Additives:
- Fillers such as silica, alumina, or glass microspheres are added to improve mechanical properties and reduce shrinkage during curing.
- Thickeners may be included to adjust viscosity for a more straightforward application.
- Flame retardants enhance fire resistance, which is crucial for applications with stringent safety requirements.
- Conductive fillers like silver or graphite can improve thermal conductivity for better heat dissipation.
Curing Agents:
- Hardeners or curing agents initiate the cross-linking reaction in the resin system, transforming the liquid mixture into a solid.
- Various curing agents are used depending on the specific resin system, including amines, anhydrides, or catalysts.
Modifiers:
- Plasticizers may be added to adjust the cured compound’s flexibility or durometer (hardness).
- Adhesion promoters improve bonding to substrates, ensuring reliable encapsulation.
- UV stabilizers and antioxidants help prevent degradation from exposure to UV radiation and oxidation.
Solvents and Diluents:
- Solvents adjust viscosity or aid in processing, evaporating during curing.
- Diluents may be added to reduce viscosity without affecting the final properties of the cured compound.
Colorants and Pigments:
- Colorants are added for aesthetic purposes or to differentiate between different formulations.
- Pigments can also provide UV protection or improve the opacity of the compound.
Understanding the role of each component in electronic potting compounds allows engineers and manufacturers to tailor formulations to meet specific performance requirements for various applications, ensuring optimal protection and reliability for electronic assemblies.
What are the Different Types of Electronic Potting Compounds?
Electronic potting compounds come in various types, each tailored to specific applications and performance requirements. Selecting the right one requires understanding the multiple varieties of most suitable materials to ensure adequate protection and longevity of electronic components. Let’s explore the main categories of electronic potting compounds:
Epoxy Resin Compounds:
- Epoxy resin compounds are one of the most widely used types of electronic potting materials due to their excellent adhesion, mechanical strength, and chemical resistance.
- They offer good electrical insulation properties and are appropriate for uses where high temperature and chemical resistance are required.
- Epoxy potting compounds come in various formulations, including flexible, rigid, and flame-retardant options for different application needs.
Silicone Resin Compounds:
- Silicone resin compounds are known for their flexibility, high-temperature resistance, and excellent electrical insulation properties.
- They are suitable for applications where flexibility and thermal stability are crucial, such as in harsh environmental conditions or high-vibration environments.
- Silicone potting compounds also exhibit good resistance to moisture, making them ideal for outdoor or marine applications.
Polyurethane Resin Compounds:
- Polyurethane resin compounds offer flexibility, impact resistance, and thermal stability.
- They are commonly used when vibration damping and shock absorption are critical, such as in automotive electronics or aerospace applications.
- Polyurethane potting compounds provide excellent adhesion to various substrates and can be formulated to meet specific performance requirements.
UV-Curable Compounds:
- UV-curable potting compounds offer rapid curing times and can be cured using UV light, eliminating the need for heat curing.
- They are ideal for applications requiring fast production cycles or heat-sensitive components to be encapsulated.
- UV-curable compounds provide excellent adhesion and can be formulated with various properties such as flexibility, thermal conductivity, and chemical resistance.
Thermally Conductive Compounds:
- Thermally conductive potting compounds are formulated to improve heat dissipation from electronic components, thereby enhancing overall device reliability.
- They contain alumina, boron nitride, or silver fillers to improve thermal conductivity while maintaining electrical insulation properties.
- Thermally conductive compounds are commonly used in power electronics, LED lighting, and automotive applications where heat management is critical.
By understanding the different types of electronic potting compounds and their unique properties, engineers and manufacturers can decide to select the finest appropriate material for their particular application needs, guaranteeing peak efficiency and reliability of electronic assemblies.
What are the Key Properties of Electronic Potting Compounds?
Electronic potting compounds possess several fundamental properties that make them indispensable for protecting electronic components in various applications. Here are some of the essential properties:
- Electrical Insulation:Electronic potting compounds offer high electrical insulation, preventing current leakage and short circuits, crucial for maintaining the integrity of electronic circuits.
- Thermal Conductivity:Some potting compounds are formulated with high thermal conductivity, facilitating efficient heat dissipation from electronic components, thereby enhancing device reliability and longevity.
- Chemical Resistance:Potting compounds resist various chemicals, including solvents, acids, and bases, protecting electronic assemblies in hostile settings where coming into contact with acidic materials is prevalent.
- Mechanical Strength:Electronic potting compounds provide robust mechanical strength, protecting electronic components from physical damage due to vibration, shock, or impact, thereby increasing the durability and reliability of the encapsulated devices.
- Flexibility:Certain potting compounds offer flexibility, allowing them to conform to the shape of the encapsulated components, reducing stress and preventing cracking or delamination, particularly in applications subject to mechanical stress or thermal cycling.
- Water and Moisture Resistance:Potting compounds form a waterproof seal around electronic components, preventing moisture ingress and protecting sensitive electronics from corrosion and malfunction. The moisture protection provided by electronic potting compounds is crucial for applications exposed to humid or wet environments.
- Adhesion:Effective adhesion to various substrates ensures that the potting compound forms a strong bond with the encapsulated components, preventing moisture ingress and ensuring long-term reliability.
- Flame Retardancy:Some potting compounds are formulated to meet flame retardancy standards, reducing the risk of fire propagation and enhancing safety in applications where fire resistance is critical, such as in automotive, aerospace, and consumer electronics.
- UV Resistance:UV-resistant potting compounds prevent degradation from prolonged exposure to ultraviolet radiation, ensuring encapsulated electronic devices’ long-term performance and reliability, particularly in outdoor or high-exposure applications.
These fundamental properties collectively contribute to the effectiveness of electronic potting compounds in safeguarding electronic components from various external circumstances, guaranteeing their reliable operation and longevity in diverse applications. By considering these properties, engineers and manufacturers can select the most suitable potting compound to meet the specific requirements of their electronic assemblies, thereby enhancing overall performance and reliability.
What are the Applications of Electronic Potting Compounds?
Electronic potting compounds are versatile materials extensively used in various industries to protect electronic components from outside elements like dust, moisture, vibration, and temperature fluctuations. These compounds offer excellent protection and insulation, ensuring electronic devices’ and assemblies’ longevity and reliability. Understanding the applications of electronic potting compounds sheds light on their significance across industries.
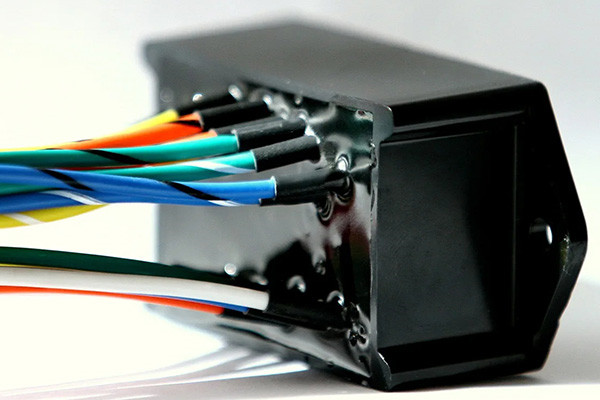
Electronics Industry:
In the electronics sector, electronic potting compounds are widely used to encapsulate and protect sensitive components such as circuit boards, sensors, and connectors. Specific measures are implemented to ensure functionality in challenging environments, such as automotive electronics subjected to high temperatures and vibrations or outdoor electronics exposed to moisture and UV radiation.
2. Automotive Sector:
In automotive applications, electronic potting compounds safeguard electronic control units (ECUs), sensors, and ignition systems from harsh operating conditions in vehicle engines, undercarriages, and interiors. Potting compounds enhance component durability, reliability, and chemical resistance, ensuring optimal performance and longevity in automotive environments.
3. Aerospace and Defense:
The aerospace and defense industries rely on electronic potting compounds to protect critical electronic systems and components in aircraft, spacecraft, and military equipment. These compounds provide superior insulation against electromagnetic interference (EMI), shock, and vibration, ensuring the integrity and functionality of electronic devices in demanding aerospace and defense applications.
4. Renewable Energy:
Electronic potting compounds protect sensitive electronics in systems that use renewable energy, like solar inverters, wind turbines, and battery storage units, from environmental factors encountered in outdoor installations. By encapsulating components like power converters and controllers, potting compounds enhance the reliability and lifespan of renewable energy infrastructure, contributing to sustainable energy generation.
5. Consumer Electronics:
Consumer electronics, including smartphones, tablets, and wearable devices, benefit from using electronic potting compounds to protect internal circuitry from moisture, dust, and physical damage. These compounds contribute to the durability and longevity of consumer electronic products, ensuring consistent performance and reliability throughout their lifespan.
Electronic potting compounds have applications across diverse industries, from electronics and automotive to aerospace, defense, renewable energy, and consumer electronics. By providing robust protection and insulation for electronic components, these compounds play a vital role in enhancing the reliability, durability, and performance of various electronic devices and systems in demanding operating environments.
How is Electronic Potting Compound Applied?
The electronic potting compound is a crucial material used in the electronics industry to protect delicate elements from the environment, including dust, dampness, and vibration. Applying electronic potting compounds requires precision and understanding of the process to ensure optimal performance of electronic devices. Here’s an overview of how electronic potting compound is applied:
- Surface Preparation:Before applying the potting compound, surfaces must be well-cleaned and let air dry. Contaminants that could interfere with adhesion should be carefully identified and removed before attempting any bonding process.
- Mixing:Electronic potting compounds typically have two parts: resin and hardener. These components must be mixed in precise ratios to activate the curing process effectively.
- Application Technique:The compound is applied using various techniques such as pouring, injection molding, or dispensing, depending on the nature of the components and the desired outcome.
- Curing:Once applied, the potting compound undergoes a curing process, which can be accelerated using heat or other curing agents. Taking this step is essential to obtaining the intended mechanical and electrical properties.
- Quality Control:Throughout the application process, quality control measures are implemented to ensure uniformity of coverage and the absence of air bubbles or voids that could compromise the protection of the electronic components.
- Post-Application Handling:Excess material is trimmed after curing, and the encapsulated components undergo further testing to verify functionality and durability.
Electronic potting compound application demands meticulous attention to detail and adherence to proper procedures to safeguard electronic devices against environmental stresses and ensure their reliability and longevity.
What Factors Should be Considered When Selecting Electronic Potting Compounds?
Selecting the appropriate electronic potting compound ensures electronic devices and components’ reliability, durability, and performance. Electronic potting compounds, or encapsulants, protect sensitive electronics from environmental factors such as moisture, vibration, thermal cycling, and chemical exposure. However, choosing the suitable potting compound involves considering various factors to meet specific application requirements effectively.
1. Material Properties:
The first consideration when selecting electronic potting compounds is understanding the material properties. Hardness, flexibility, thermal conductivity, chemical resistance, and dielectric strength are essential for determining the compound’s appropriateness for the planned use. For instance, applications requiring high thermal conductivity may necessitate potting compounds with excellent heat dissipation properties.
2. Environmental Conditions:
Assessing the environmental conditions to which the electronic device will be exposed is crucial. Whether the device operates indoors, outdoors, or in harsh industrial environments impacts the choice of potting compound. Extreme temperatures, moisture exposure, and other factors such as UV radiation, chemicals, and mechanical stress influence selection.
3. Application Method:
Consideration should also be given to the method of application. Potting compounds are available in various forms, including liquid, paste, and pre-mixed formulations. Understanding the application process, such as manual or automated dispensing, casting, or molding, helps in choosing the compound’s appropriate viscosity, curing time, and pot life.
4. Compatibility:
Ensuring compatibility between the potting compound and the materials it will come into contact with is essential to prevent compatibility issues that could lead to the degradation or failure of the electronic device. Compatibility considerations extend to substrates, components, connectors, and other assembly materials.
5. Regulatory Compliance:
When selecting electronic potting compounds, respect industry norms and guidelines, including RoHS (Restriction of Hazardous Substances) and REACH (Registration, Evaluation, Authorization, and Restriction of Chemicals). Complying with these regulations ensures environmental sustainability and product safety.
6. Cost and Manufacturing Considerations:
Balancing performance requirements with cost considerations is essential. While high-performance potting compounds may offer superior protection, they can also be more expensive. Manufacturers must weigh the trade-offs between performance, cost, and ease of manufacturing to achieve the desired balance.
Selecting the suitable electronic potting compound requires a comprehensive evaluation of material properties, environmental conditions, application methods, compatibility, regulatory compliance, and cost considerations. By carefully assessing these factors, manufacturers can ensure the durability and dependability of electrical equipment and parts in various applications.
What are the Advantages of Using Electronic Potting Compounds?
Electronic potting compounds are materials widely used in electronic manufacturing to encapsulate and protect delicate electronic components from environmental stresses. These compounds offer numerous advantages over traditional protection techniques, making them a popular option across various businesses. Understanding the benefits of using electronic potting compounds can help optimize electronic designs for enhanced performance and durability.
Advantages of Using Electronic Potting Compounds:
Protection from Environmental Factors:
- Electronic potting compounds create a robust barrier against chemicals, dust, moisture, and other environmental elements that can compromise electronic components’ integrity.
- This protection extends the lifespan of electronics, particularly those used in harsh environments such as automotive, aerospace, and marine applications.
Improved Mechanical Strength:
- Potting compounds enhance the mechanical strength of electronic assemblies by providing structural support and reinforcement.
- They prevent the movement of components due to vibrations or shocks, reducing the risk of damage during operation or transportation.
Thermal Management:
- These compounds offer excellent thermal conductivity, dissipating heat efficiently from electronic components.
- By maintaining optimal operating temperatures, potting compounds help prolong the lifespan and dependability of electrical devices, especially in high-power applications.
Electrical Insulation:
- Electronic potting compounds are effective electrical insulators, preventing short circuits and electrical interference.
- They offer insulation against high voltages and enhance the safety of electronic systems, which is critical in applications where electrical hazards are a concern.
Chemical Resistance:
- Many electronic potting compounds resist various chemicals, oils, and solvents, ensuring the integrity of electronic assemblies in challenging environments.
- This chemical resistance reduces the risk of corrosion and degradation, particularly in industrial settings where exposure to harsh substances is common.
Ease of Application:
- Potting compounds are available in different formulations, including liquid, paste, and gel forms, offering flexibility in application methods.
- Their ease of use allows for efficient encapsulation of complex shapes and configurations, streamlining the manufacturing process and reducing production time.
Cost-Effectiveness:
- Despite their advanced properties, electronic potting compounds are often cost-effective compared to alternative protection methods.
- The long-term benefits of extended component lifespan and reduced maintenance outweigh the initial investment, making potting compounds a financially prudent choice.
Electronic potting compounds offer many advantages that contribute to electronic devices and systems’ reliability, performance, and longevity. From environmental protection to thermal management and electrical insulation, these compounds play a crucial role in ensuring the integrity of electronic assemblies across various industries. Understanding and leveraging these advantages can lead to more robust and durable electronic designs, meeting the demands of modern technological applications.
Can Electronic Potting Compounds Withstand Harsh Environments?
Electronic potting compounds are vital materials in safeguarding electronic components from environmental stresses, ensuring their reliable operation across various applications. One crucial question often posed is whether these compounds can effectively withstand harsh environments. Examining their properties and performance under adverse conditions provides valuable insights into their suitability for demanding applications.

Properties of Electronic Potting Compounds:
Chemical Composition:
Electronic potting compounds are typically formulated using epoxy resins, polyurethanes, silicones, and other specialized polymers.
Depending on the intended application, these compounds are engineered to exhibit specific properties, such as chemical resistance, thermal conductivity, and mechanical strength.
Environmental Resistance:
Potting compounds resist moisture, dust, chemicals, and other environmental factors that could compromise electronic components.
Their ability to withstand harsh environments is critical for automotive, aerospace, marine, and industrial applications.
Temperature Tolerance:
Many electronic potting compounds offer exceptional thermal stability, capable of withstanding wide temperature fluctuations without degradation.
This property is essential for electronics deployed in extreme climates or subjected to high operating temperatures.
Performance in Harsh Environments:
Moisture and Humidity Resistance:
Electronic potting compounds create a protective barrier that prevents moisture ingress, safeguarding sensitive electronic components from corrosion and malfunction.
Even in humid situations, they maintain their integrity, ensuring long-term reliability in outdoor or submerged applications.
Chemical Resistance:
Potting compounds resist various chemicals, oils, solvents, and other corrosive substances commonly encountered in industrial environments.
This resistance helps preserve the functionality and longevity of electronic assemblies deployed in chemical processing plants, oil rigs, and similar harsh settings.
Mechanical Durability:
The mechanical strength provided by potting compounds protects electronic components from physical damage due to vibration, shock, or impact.
They maintain structural integrity, even in rugged environments such as automotive engine compartments or heavy machinery.
Due to their tailored properties and robust formulations, electronic potting compounds demonstrate remarkable resilience in withstanding harsh environments. From resisting moisture and chemicals to maintaining mechanical durability and temperature tolerance, these compounds are essential to preserving the dependability and durability of electronic assemblies across diverse industries. Understanding their performance characteristics is necessary for selecting the most suitable potting compound for specific application requirements, ultimately enhancing the resilience of electronic systems in challenging environments.
Are Electronic Potting Compounds Resistant to Chemicals?
Electronic potting compounds offer chemical resistance and guarantee the durability and dependability of electronic equipment in various electronic devices in diverse operational environments. They are critical in safeguarding sensitive electronic components from environmental stresses such as moisture, dust, and mechanical impact. However, their ability to withstand exposure to various chemicals is equally crucial, given the potential for chemical ingress to compromise performance or cause failure.
The resistance of electronic potting compounds to chemicals hinges on multiple factors, including the specific formulation of the compound and the types of chemicals it may encounter during its intended use. Manufacturers typically engineer potting compounds to resist common chemicals like oils, fuels, solvents, and cleaning agents in industrial settings. Moreover, tailored formulations may be developed to withstand more aggressive chemicals in specialized environments such as laboratories or chemical processing facilities.
Rigorous testing procedures are employed to assess the chemical resistance of potting compounds, ensuring the reliability of electronic devices. These tests simulate real-world conditions to evaluate the compound’s performance when exposed to various chemicals. Such assessments enable manufacturers to validate the effectiveness of their formulations and ensure compliance with industry standards and regulatory requirements.
Despite the resilience of electronic potting compounds, users must conduct thorough compatibility assessments before deployment. It involves identifying the specific chemicals in the device’s operating environment and evaluating their potential interaction with the potting compound. Manufacturers and users can mitigate the risk of chemical-induced degradation or failure by selecting appropriate potting compounds and adhering to recommended handling procedures.
It needs routine upkeep and observation to spot any chemical attack symptoms and ensure the continued protection of electronic components. Timely intervention can prevent potential damage and extend the service life of electronic devices, thereby minimizing downtime and maintenance costs.
Electronic potting compounds safeguard electronic devices from environmental and chemical stresses. By selecting chemically resistant formulations and implementing proper handling and maintenance practices, manufacturers and users can lengthen and improve the dependability of electrical gadgets across a wide range of applications.
How Does Electronic Potting Improve Thermal Conductivity?
Electronic potting, a common technique in electronics manufacturing, involves encapsulating sensitive electronic components within a protective material to shield them from environmental factors and ensure their longevity. One significant benefit of electronic potting is its capacity to enhance thermal conductivity within electronic devices. By effectively dissipating heat generated during operation, electronic potting helps maintain optimal temperatures, safeguarding the components from overheating and potential damage. Understanding how electronic potting improves thermal conductivity is essential for maximizing the efficiency and reliability of electronic systems. Here’s an exploration of the mechanisms behind this enhancement:
- Heat Transfer Pathways:Electronic potting compounds, often formulated containing fillers that carry heat, like ceramics or metallic particles, create efficient pathways for heat transfer within the device. These fillers facilitate the movement of heat away from sensitive components towards areas with lower temperatures, promoting thermal equilibrium.
- Reduced Thermal Resistance:Electronic potting encapsulation eliminates air gaps and irregularities that impede heat transfer. Potting compounds reduce thermal resistance by forming a uniform layer around the components, allowing heat to flow more freely throughout the system.
- Improved Contact and Interface:Electronic potting enhances the contact between heat-generating components and heat sinks or other dissipative elements. This improved interface minimizes thermal impedance, enabling more effective heat dissipation from the components to the surrounding environment.
- Enhanced Cooling Efficiency:Electronic potting can be tailored to specific applications, allowing manufacturers to optimize thermal conductivity based on the device’s requirements. By selecting potting materials with high thermal conductivity and tailoring the encapsulation process, engineers can significantly improve the cooling efficiency of electronic systems.
- Prevention of Hotspots:Hotspots, localized areas of excessive heat buildup, pose a risk to the reliability and performance of electronic devices. Electronic potting helps distribute heat evenly across the device, mitigating the formation of hotspots and reducing the likelihood of thermal-induced failures.
- Long-Term Stability:Effective thermal management through electronic potting contributes to electronic devices’ long-term stability and reliability. By maintaining consistent operating temperatures and preventing thermal stress, potting compounds extend the lifespan of components and minimize the risk of premature failure.
Electronic potting plays a vital role in improving thermal conductivity within electronic devices by facilitating heat transfer, reducing thermal resistance, enhancing contact interfaces, optimizing cooling efficiency, preventing hotspots, and ensuring long-term stability. This enhancement in thermal management is crucial for maintaining the reliability and performance of electronic systems across various applications.
What Are the Differences Between Conformal Coating and Potting?
In electronic manufacturing, conformal coating and potting are protective measures for electronic assemblies. However, they fulfill different functions and provide unique advantages. Understanding the differences between conformal coating and potting is crucial for selecting the most suitable protection method based on an application’s specific requirements.
Purpose and Application:
Conformal Coating:
- A thin layer of protection called conformal coating is placed directly onto the surface of electronic components and PCBs.
- It protects against moisture, dust, chemicals, and other environmental contaminants without adding significant bulk or weight to the assembly.
- They are commonly used in applications where flexibility, reworkability, and visibility of components are essential, such as consumer electronics, PCBs, and LED lighting.
Potting:
- Potting involves encapsulating electronic components or entire assemblies within a protective compound, forming a solid barrier around them.
- It provides comprehensive protection against moisture, vibration, shock, and thermal stress, enhancing the mechanical and environmental durability of electronic systems.
- They are typically employed in applications where robust protection is paramount, such as automotive electronics, aerospace systems, and industrial machinery.
Material and Application Process:
Conformal Coating:
- Conformal coatings are available in various formulations, including acrylics, silicones, urethanes, and epoxies. Each offers different properties, such as flexibility, chemical resistance, and dielectric strength.
- They are applied using methods like spraying, dipping, brushing, or selective coating, allowing for precise coverage and control over the thickness of the coating layer.
Potting:
- Potting compounds consist of materials such as epoxy resins, polyurethanes, or silicones, formulated to provide robust protection and structural support to enclosed components.
- The potting process involves immersing electronic assemblies in the liquid compound, which then cures to form a solid encapsulation around the components.
- Potting can be performed using various techniques, including vacuum potting, pressure potting, or manual potting, depending on the specific application requirements.
Advantages and Considerations:
Conformal Coating:
- It offers flexibility and reworkability, allowing for easier repair and component replacement.
- It provides good protection against environmental contaminants while allowing for the visibility of components.
- It may require reapplication or touch-up in case of damage or wear over time.
Potting:
- The electronic potting compound protects against various environmental stresses, including moisture, vibration, and thermal cycling.
- Enhances mechanical strength and structural integrity of electronic assemblies, reducing the risk of damage or failure.
- Offers superior protection in harsh and demanding environments but may limit accessibility for repairs or modifications.
While conformal coating and potting both serve to protect electronic assemblies, they differ in their application methods, materials, and the level of protection they offer. Conformal coating provides a thin, flexible layer of security suitable for applications where visibility and reworkability are essential. In contrast, potting offers comprehensive encapsulation and structural reinforcement for electronics deployed in harsh environments. Understanding the distinctions between conformal coating and potting is crucial in selecting the most appropriate protection method to ensure the reliability and longevity of electronic systems.
Can Electronic Potting Compounds Enhance Electrical Insulation?
Electronic potting compounds safeguard electronic components and devices from environmental stressors such as moisture, heat, and mechanical shocks. One aspect often overlooked is their potential to enhance electrical insulation. Understanding how electronic potting compounds can contribute to improved electrical insulation is essential for engineers and manufacturers aiming to optimize the performance and reliability of their electronic systems.
1. Dielectric Strength:
Dielectric strength is a crucial property in determining the effectiveness of electronic potting compounds in enhancing electrical insulation. Compounds with high dielectric strength can withstand higher electric field intensities without breakdown, thus providing better insulation against voltage leakage and short circuits.
2. Surface Coating and Sealing:
Electronic potting compounds form a protective coating around electronic components, sealing them from the surrounding environment. This barrier protects against moisture and contaminants and helps prevent electrical leakage and corona discharge by insulating the components’ surfaces.
3. Filling Voids and Gaps:
Potting compounds can effectively fill voids, gaps, and irregularities between electronic components and circuit elements. By eliminating air pockets and providing a uniform insulation layer, these compounds reduce the risk of partial discharges and improve the system’s overall insulation integrity.
4. Thermal Conductivity:
While not directly related to electrical insulation, the thermal conductivity of potting compounds is a critical factor. Efficient heat dissipation helps maintain stable operating temperatures of electronic components, prevent thermal breakdown of insulation materials, and ensure long-term electrical insulation performance.
5. Material Compatibility:
The compatibility of potting compounds with the materials they encapsulate is essential for maintaining electrical insulation over time. Compounds chemically compatible with the substrate materials minimize the risk of degradation, delamination, or loss of insulation properties due to material interactions.
6. Regulatory Compliance and Reliability Testing:
Adherence to industry standards and reliability testing procedures is vital to ensure the effectiveness of electronic potting compounds in enhancing electrical insulation. Manufacturers should verify that the chosen compounds meet relevant standards for dielectric properties, insulation resistance, and long-term reliability under expected operating conditions.
Are There Environmental Considerations with Electronic Potting Compounds?
Electronic potting compounds are essential materials that shield electrical parts from the elements, including moisture, dust, and mechanical stress. While these compounds offer significant benefits regarding device reliability and longevity, it’s crucial to consider their environmental impact and sustainability. Understanding the ecological considerations associated with electronic potting compounds is necessary to make knowledgeable decisions on their use in electronics manufacturing. Here’s an exploration of the environmental aspects related to electronic potting compounds:
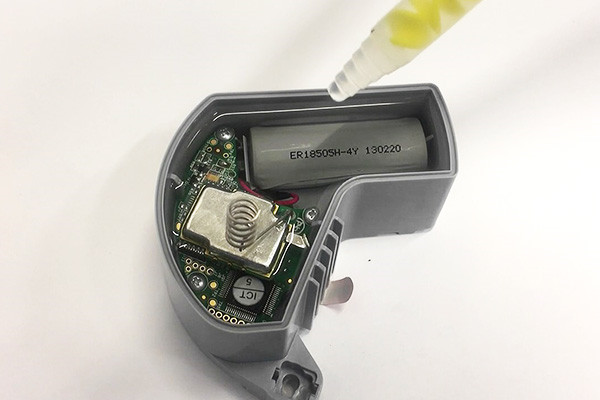
- Material Selection:The choice of materials used in electronic potting compounds greatly influences their environmental impact. Choosing sustainable and environmentally beneficial materials, such as biodegradable resins or those derived from renewable sources, can reduce the overall ecological footprint of potting compounds.
- Hazardous Components:Some electronic potting compounds contain dangerous materials like heavy metals, volatile chemical compounds (VOCs), or toxic additives. Proper handling, disposal, and recycling procedures are necessary to reduce the amount of harmful compounds that are released into the environment and mitigate potential harm to human health and ecosystems.
- Recycling and Disposal:Disposing of electronic potting compounds at the end of a product’s life cycle presents challenges due to their non-biodegradable nature and potential toxicity. Developing efficient recycling processes or exploring alternative disposal methods, such as incineration with energy recovery, can help mitigate the environmental impact of discarded potting compounds.
- Energy Consumption:The manufacturing process of electronic potting compounds typically involves significant energy consumption, especially during curing or polymerization stages. Implementing energy-efficient production methods and utilizing renewable energy sources can reduce the carbon footprint associated with potting compound manufacturing.
- Emissions and Air Quality:Certain potting compounds may emit volatile compounds or harmful fumes during curing or application, contributing to air pollution and indoor air quality concerns. Employing low-VOC formulations and implementing proper ventilation measures in manufacturing facilities can help minimize these emissions and ensure a healthier working environment.
- Regulatory Compliance:Adherence to environmental laws and guidelines, including RoHS (Restriction of Hazardous Substances) directives, is essential for ensuring the ecological sustainability of electronic potting compounds. Manufacturers must adhere to stringent guidelines regarding the use of hazardous substances to minimize environmental pollution and promote product safety.
While electronic potting compounds offer invaluable protection for electronic components, it’s crucial to consider their environmental implications. By prioritizing sustainable material selection, implementing recycling and disposal strategies, reducing energy consumption, minimizing emissions, and ensuring regulatory compliance, the electronics industry can mitigate the environmental impact of electronic potting compounds and move towards more environmentally responsible manufacturing practices.
What are the Challenges Associated with Electronic Potting Compounds?
Electronic potting compounds protect electronic components from environmental hazards, ensuring their reliability and longevity. However, despite their many benefits, several challenges are associated with these materials’ selection, application, and performance. Understanding these challenges is crucial for engineers and manufacturers striving to maximize the effectiveness of potting compounds in electronic assemblies.
1. Material Selection Complexity:
Choosing the suitable potting compound involves navigating a complex landscape of material properties, including hardness, flexibility, thermal conductivity, and chemical resistance. The wide range of available formulations adds to the complexity, requiring careful consideration of application requirements, environmental conditions, and compatibility with other materials.
2. Adhesion and Compatibility Issues:
Strong adhesion between the potting compound and substrate materials ensures proper encapsulation and protection. However, compatibility issues may arise, leading to poor adhesion, delamination, or material degradation. Ensuring compatibility between the potting compound and substrates and any components or connectors within the assembly is paramount.
3. Curing and Processing Challenges:
The curing process of potting compounds can pose challenges, particularly in large-scale production environments. Factors such as pot life, curing time, and curing temperature must be carefully controlled to avoid under-curing or over-curing, which can compromise the integrity of the encapsulation and lead to performance issues.
4. Thermal Management Considerations:
While potting compounds offer thermal insulation properties, they can also impede heat dissipation from electronic components. Managing thermal issues becomes crucial, especially in high-power applications where excessive heat buildup can degrade the performance and reliability of electronic devices. Balancing insulation and thermal conductivity properties is essential to prevent overheating.
5. Impact on Repairability and Maintenance:
Once electronic components are potted, accessing and repairing them becomes challenging. Potting compounds create a barrier that hinders repairability and maintenance, potentially increasing downtime and cost in the event of component failure or troubleshooting needs. Finding ways to balance the need for protection with accessibility for repairs is a significant challenge.
6. Regulatory Compliance and Environmental Impact:
Adherence to regulatory standards such as RoHS and REACH adds another layer of complexity to selecting and using electronic potting compounds. Manufacturers must ensure that chosen compounds comply with environmental regulations while meeting performance and reliability requirements.
How Can I Ensure Proper Curing of Electronic Potting Compounds?
Ensuring proper curing of electronic potting compounds is necessary to optimise the functionality and dependability of encapsulated electronic assemblies. Proper curing guarantees the formation of a durable, resilient barrier around sensitive components, protecting them from environmental stresses and mechanical damage. Understanding the methods and factors influencing the curing procedure is essential to getting the best outcomes in electronic manufacturing.
Factors Affecting the Curing Process:
Temperature:
- Temperature during curing is essential for the curing process of potting compounds.
- Most potting compounds have specified temperature ranges for curing, and adherence to these ranges is vital for achieving proper cross-linking and polymerization.
Humidity and Moisture:
- High humidity levels can hinder the curing process by interfering with the chemical reactions involved.
- Controlling humidity during curing, especially in environments with elevated moisture levels, is necessary to ensure uniform curing and prevent defects like bubbles or delamination.
Mixing Ratio and Homogeneity:
- Proper mixing of potting compound components is essential to ensure uniform curing and properties throughout the encapsulated assembly.
- Deviating from the recommended mixing ratios or inadequate mixing can lead to incomplete curing or uneven distribution of curing agents, compromising the integrity of the encapsulation.
Methods for Ensuring Proper Curing:
Temperature Control:
- Utilize temperature-controlled curing ovens or chambers to maintain consistent curing temperatures within the specified range.
- Monitor and record temperature profiles during the curing process to ensure compliance with manufacturer recommendations.
Moisture Management:
- Control humidity levels in the curing environment using desiccants, dehumidifiers, or climate-controlled chambers.
- Ensure proper sealing of curing enclosures to prevent moisture ingress during the curing period.
Optimized Mixing Procedures:
- Follow manufacturer guidelines for mixing ratios and procedures to attain the appropriate qualities and curing traits.
- Utilize equipment such as vacuum degassing chambers or mechanical mixers to ensure thorough mixing and elimination of air bubbles.
Curing Time and Dwell Period:
- Adhere to the recommended curing time specified by the potting compound manufacturer.
- Allow sufficient dwell time after the curing process to ensure complete polymerization and curing of the compound.
Quality Control and Testing:
Visual Inspection:
- Conduct visual inspections of cured potting compounds for uniformity, absence of bubbles, and adhesion to substrate surfaces.
- Address any irregularities or defects promptly to prevent compromised performance or reliability.
Mechanical and Electrical Testing:
- Mechanical tests such as hardness, adhesion, and flexibility testing are performed to assess the quality of the cured potting compound.
- Conduct electrical tests, including insulation resistance and dielectric strength measurements, to verify the electrical integrity of encapsulated assemblies.
What Are Some Common Mistakes to Avoid When Using Electronic Potting Compounds?
Electronic potting compounds protect electronic components from environmental stresses, ensuring their reliability and longevity. However, improper usage or application of these compounds can result in expensive errors and jeopardize the performance of electronic devices. Understanding common pitfalls to avoid when using electronic potting compounds is essential for achieving optimal results in electronics manufacturing. Here are some critical mistakes to steer clear of:
- Inadequate Surface Preparation:Neglecting to properly clean and prepare the surfaces of electronic components before potting can result in poor adhesion and compromised protection of the components. Surface contaminants such as dust, grease, or moisture must be thoroughly removed to ensure proper bonding of the potting compound.
- Incorrect Mixing Ratios:Electronic potting compounds typically have two or more components that must be combined in exact proportions to start the curing process. Failure to adhere to the specified mixing ratios can lead to complete curing, soft spots, or reduced mechanical strength of the encapsulant.
- Improper Application Technique:The method of applying electronic potting compounds, whether pouring, injection molding, or dispensing, should be chosen based on the particular specifications of the components and the desired outcome of the application. Using the wrong application technique or applying the compound un-evenly can result in air bubbles, voids, or incomplete coverage, compromising the effectiveness of the encapsulation.
- Insufficient Curing Time:Rushing the curing process of electronic potting compounds or subjecting them to inadequate curing conditions can lead to under-cured or poorly bonded encapsulants. It’s essential to allow sufficient curing time and provide optimal conditions, such as temperature and humidity, to develop mechanical and electrical properties properly.
- Overfilling or Underfilling:Incorrectly estimating the volume of potting compound needed to encapsulate electronic components can result in overfilling, leading to wastage and potential damage to adjacent parts or underfilling, leaving components vulnerable to environmental hazards. Careful planning and accurate volume calculations are essential to achieve optimal encapsulation.
- Ignoring Compatibility Issues:Certain electronic potting compounds may not be compatible with specific substrates or components, leading to adhesion failure, chemical reactions, or performance degradation over time. It’s crucial to select potting materials compatible with the materials used in the electronic assembly and consider factors such as thermal expansion coefficients and chemical resistance.
- Lack of Testing and Quality Control:Skipping or inadequately performing testing and quality control measures can result in undetected defects or inconsistencies in the encapsulation process, compromising the reliability of electronic devices. Regular testing for mechanical strength, electrical insulation, and environmental resistance is essential to ensure the effectiveness of electronic potting compounds.
Can Electronic Potting Compounds Be Removed or Reversed?
Electronic potting compounds protect electronic components from environmental stresses and mechanical damage. However, there are instances where the need arises to remove or reverse the potting process, whether for repair, rework, or component replacement. Understanding the feasibility and methods for eliminating or reversing electronic potting compounds is essential for maintaining flexibility and efficiency in electronic manufacturing and repair processes.
Feasibility of Removal:
Material Considerations:
The feasibility of removing electronic potting compounds depends mainly on the material properties of the compound used.
Some potting compounds may be designed with properties that make them easier to remove or rework, while others may form a more permanent bond.
Curing Process:
Fully cured potting compounds may pose more significant challenges for removal due to their hardened and cross-linked structure.
Compounds that cure via heat, chemical reaction, or UV radiation may have varying degrees of reversibility depending on the curing mechanism.
Methods for Removal:
Mechanical Methods:
Mechanical methods involve physically breaking or cutting away the potting material to access the encapsulated components.
Techniques such as drilling, milling, or chiseling may be employed, but these methods can be time-consuming and may risk damaging the components.
Chemical Solvents:
Chemical solvents can soften or dissolve certain potting compounds, facilitating their removal.
Solvents such as acetone, isopropyl alcohol, or specialized potting compound removers may be used, but compatibility with the potting material and encapsulated components must be considered.
Thermal Techniques:
Thermal methods involve heating the potting material to soften or melt it for easier removal.
Care must be taken to avoid damaging sensitive components or substrates during heating, and temperature control is crucial to prevent thermal damage.
Considerations and Challenges:
Component Integrity:
The removal process must be performed carefully to avoid damaging the encapsulated components or underlying substrate.
Delicate components such as integrated circuits or sensors may be particularly vulnerable to mechanical or thermal stress during removal.
Environmental Impact:
Chemical solvents used for potting compound removal may pose environmental and safety concerns, requiring proper handling and disposal procedures.
Sustainable and eco-friendly removal methods are increasingly sought after to minimize environmental impact.
While electronic potting compounds are designed to provide durable protection for electronic components, methods are available for removal or reversal when necessary. Mechanical, chemical, or thermal methods can remove potting compounds depending on material properties, curing process, and application requirements. However, careful consideration of component integrity, environmental impact, and the feasibility of removal is essential to ensure successful outcomes and minimize risks during the potting compound removal process.
What is the Future of Electronic Potting Compounds in Industry?
Electronic potting compounds have long been integral to the electronics industry, providing essential protection and insulation for electronic components in diverse applications. As technology advances and the demands on electronic systems evolve, the future of electronic potting compounds holds both opportunities and challenges. Understanding the trajectory of these materials in the industry is vital for manufacturers, engineers, and researchers shaping the next generation of electronic devices.
1. Advanced Materials Development:
The future of electronic potting compounds lies in the continued development of advanced materials with enhanced properties. Innovations in material science are expected to yield compounds with improved thermal conductivity, dielectric strength, flexibility, and chemical resistance, enabling more excellent performance and reliability in demanding applications.
2. Integration with Emerging Technologies:
As emerging technologies such as 5G, the Internet of Things (IoT), and electric vehicles increase, electronic potting compounds will play a crucial role in protecting and enabling the seamless operation of these systems. Customized formulations tailored to the specific requirements of these technologies, such as high-frequency operation or extreme environmental conditions, will drive innovation in the industry.
3. Sustainable and Eco-Friendly Solutions:
The future of electronic potting compounds also involves a shift towards sustainable and eco-friendly solutions. Manufacturers are increasingly aware of environmental concerns, so manufacturers are under pressure to develop compounds that minimize environmental impact while delivering optimal performance. Biodegradable, recyclable, and non-toxic formulations will likely gain prominence in the industry.
4. Integration with Smart Manufacturing Processes:
Advancements in automation, robotics, and data analytics are transforming manufacturing processes in the electronics industry. Electronic potting compounds will be integrated into intelligent manufacturing systems, enabling precise dispensing, curing, and quality control measures to ensure consistent and reliable encapsulation of electronic components.
5. Customization and Application-Specific Solutions:
The future of electronic potting compounds will see a greater emphasis on customization and application-specific solutions. Manufacturers will collaborate closely with customers to develop tailored formulations that meet the unique requirements of their applications, whether it be aerospace, automotive, medical devices, or consumer electronics.
6. Regulatory Compliance and Standards:
Adherence to regulatory standards and industry certifications will remain a key consideration in the future of electronic potting compounds. Manufacturers must ensure compliance with evolving regulations such as RoHS, REACH, and UL standards while addressing emerging challenges related to material safety, toxicity, and environmental sustainability.
Conclusion
Electronic potting compounds play a vital role in safeguarding electronic components, ensuring their longevity and reliability in various operating conditions. Understanding their composition, properties, applications, and proper usage is essential for engineers and manufacturers aiming to achieve optimal performance and protection for their electronic devices. As technology advances, electronic potting compounds are likely to continue evolving to meet the ever-growing demands of the electronics industry.
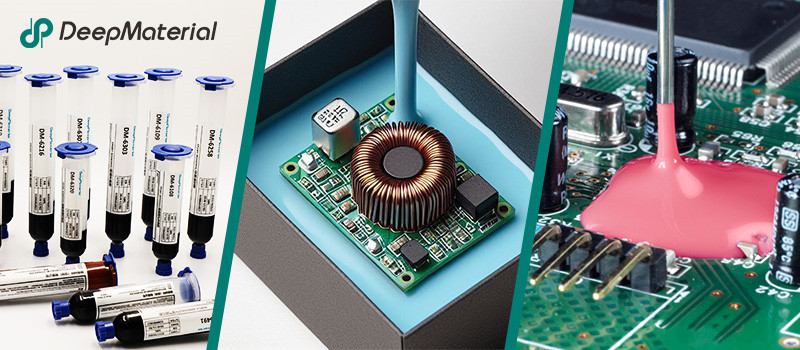
About DeepMaterial
DeepMaterial is a trusted supplier of encapsulant materials that are used in electronics manufacturing worldwide. From chip on board encapsulants such as glob top material to conformal coatings, underfills, low pressure molding, and potting solutions, DeepMaterial offers a full range of circuit board protection materials that effectively protect circuit boards while help reduce costs. More…Deepmaterial is a the manufacturer of epoxy adhesives including hardeners, metalbond, and metal filled resins. Structural, toughened medium viscosity, and non-sag adhesives are also offered. Some adhesives are resistant to thermal shock, chemical, vibration dampening, and impact. Suitable for metals, plastics, wood, and ceramics. Serves electronics, aerospace, automotive, tooling, marine, and construction industries. REACH and RoHS compliant. FDA approved. UL listed. Meets military specifications. We are the one of best adhesive manufacturers in China.
Blogs & News
Potting compounds are at the frontline of electronics assembly, delivering effective protection in challenging environmental conditions while improving mechanical strength and offering high electric insulation. Used within a variety of industries, electrical potting compounds are found within a broad range of consumer electronics, as well as used in applications across the automotive, aerospace, and other industries where electronic assemblies are prevalent.
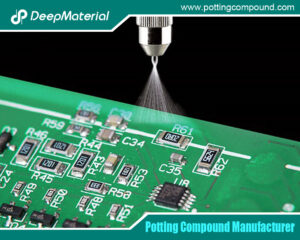
The Ultimate Guide to Electrical Potting Compound and Market Application
The Ultimate Guide to Electrical Potting Compound and Market Application In the modern world of electronics, where devices are increasingly compact and exposed to harsh
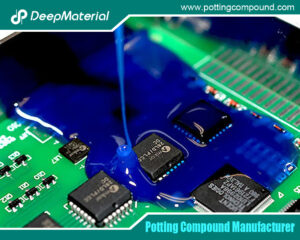
The Top Polyurethane Potting Compound
The Top Polyurethane Potting Compound In the fast-evolving world of electronics and industrial manufacturing, protecting sensitive components from environmental hazards is critical to ensuring reliability
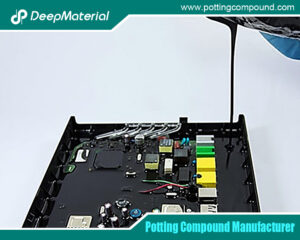
Advanced Epoxy Potting Compound for Superior Electronic Protection
Advanced Epoxy Potting Compound for Superior Electronic Protection In the realm of electronics and industrial manufacturing, protecting sensitive components from environmental hazards is critical to
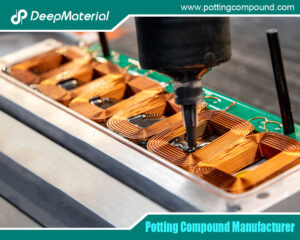
Waterproof Potting Compound: A Comprehensive Guide
Waterproof Potting Compound: A Comprehensive Guide In today’s technology-driven world, protecting sensitive electronic components from environmental hazards is paramount. One of the most effective solutions
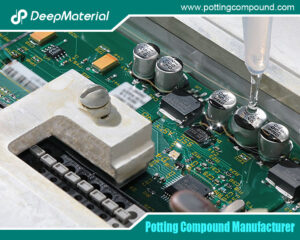
Silicone Potting Compound for Electronics
Silicone Potting Compound for Electronics In the rapidly evolving world of electronics, ensuring the reliability, durability, and performance of electronic components is paramount. One critical
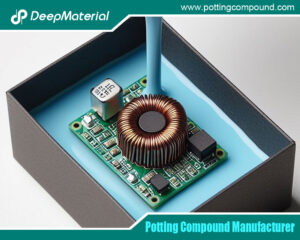
Potting Compound vs. Epoxy: A Comprehensive Comparison
Potting Compound vs. Epoxy: A Comprehensive Comparison In the world of electronics, manufacturing, and material encapsulation, two terms frequently come up: potting compounds and epoxy.