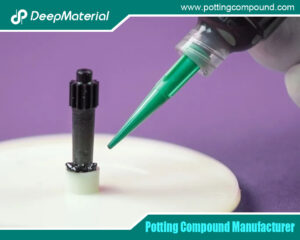
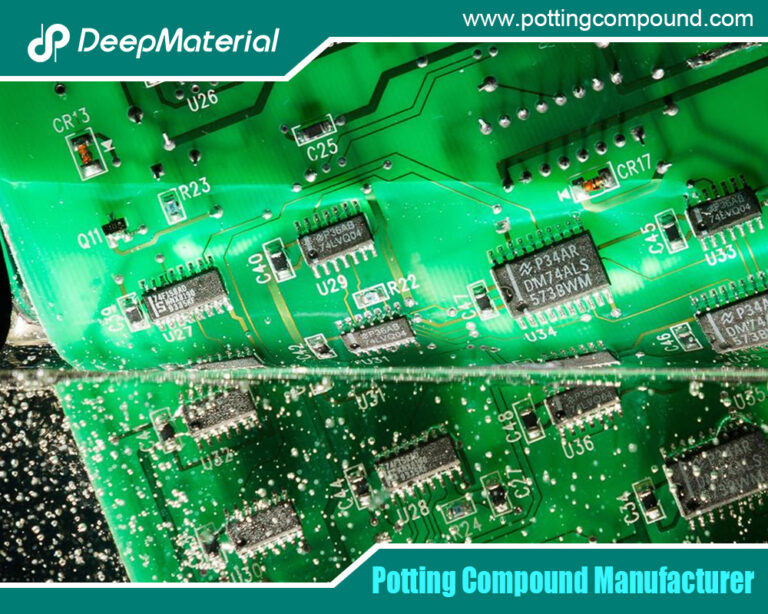
Encapsulation Considerations
If the potting material contains air inclusions or ‘voids’, then it may not be such an effective method of protection. Voids can reduce the insulation effectiveness by allowing internal arc-over or surface tracking and, of course, will reduce the thermal conductivity. Also, an inclusion could create mechanical stresses such as cracking due to very high or low air pressures or expansion/contraction of air in the void with temperature.
There are several techniques that can be used to eliminate significant air inclusions in the potting compound, the most effective being vacuum mixing and dispensing. The potting compound is prepared and mixed under a vacuum which causes any air bubbles to rise to the surface. It is then pumped into dispensing syringes via a pressurized system that does not allow air to re-enter into the compound. Some products, we use the potting as part of their approved safety isolation barrier and safety agencies require that the penetration of potting compound and void-free performance must be controlled in production. This is guaranteed by the vacuum impregnation process along with periodic monitoring by ‘sectioning’ or X-ray.
However, the majority of our products are not potted under a vacuum as this speeds up the production capacity greatly, important when you are manufacturing more than one million products each month. DeepMaterial can still avoid air bubbles in the potting compound by using other techniques, which in combination, can eliminate almost all included voids. The first of these is the correct potting process; firstly, the case is partly filled with the potting compound, then the pre-tested and assembled PCB is inserted into the case and the case filled almost to the top. The partly-completed converter is then placed in a resting oven which is warm, but held below the curing temperature of the compound. The potting compound becomes very liquid at the warm temperature and any trapped air bubbles rise to the surface and, if necessary, the case can be placed on a shaker table to encourage the bubbles to rise. Finally, the converter case is filled completely and transferred to a curing oven at a higher temperature.
Two-component epoxy potting material is hydroscopic – it will absorb moisture from the air leading to a mottled surface appearance called “amine bloom”, so it is important to use fresh chemical compounds that have been stored in a low-humidity, temperature-controlled environment. Also, the PCB itself should be clean and free from residue. As DeepMaterial has its own SMD production lines, we can control the cleanliness, humidity and temperature in our production area closely. A clean, bare-board converter will allow the potting compound to adhere well to the components and PCB to reduce air inclusions.
Finally, we can use X-ray inspection to check the converters for voids. For new designs, some air bubbles can be unexpectedly trapped under components or under the PCB and be difficult to remove. In this case, we can use the results of the X-ray inspection to either reposition the components or to add strategic holes in the PCB to allow trapped air to escape during the potting process.
Factors affecting the choice of potting compound
All potting compounds shrink when they transition from the liquid to the solid state. The amount of shrinkage is small for most of the common compounds used for potting electronics, but any shrinkage places mechanical stress on the components or can open up microscopic cracks or gaps that allow the ingress of liquids or gasses. The solution is to use potting compounds that are not too hard, but retain some softness once fully cured. The mechanical stress caused by the shrinkage is then dissipated by the elastomeric (“rubbery-ness”) property of the potting compound, and the seals to the case, pins and components remain tight. Further, the potting compound should also have a low CTE (Coefficient of Thermal Expansion) so that the effects of thermal cycling do not cause mechanical stress on the components or PCB, which may have a different CTE. A certain softness in the cured potting material also mitigates against such thermally-induced mechanical stresses.
Recent Posts
- How to Determine the Appropriate Encapsulation Thickness
- Influence of Encapsulation Thickness on the Heat Dissipation Performance and Electrical Insulation Performance of PCB
- Causes and Avoidance Methods of Bubble Generation in the Potting Process
- Technical Details on Controlling Parameters such as Temperature, Pressure, and Speed in the Potting Process to Ensure Potting Quality
- A Comprehensive Analysis of PCB Pretreatment Before Potting Process: A Crucial Link to Ensure the Performance and Reliability of Electronic Devices
- A Comprehensive Analysis of the Performance Differences of Epoxy Resin, Silicone Rubber and Polyurethane Encapsulation Materials
- How to Select Suitable Potting Materials for PCB According to the Working Environment
- What is PCB Potting
- The Evolution of Smart Watch Assembly Adhesive: A Key Component in Modern Wearable Technology
- Laptop Tablet Assembly Adhesive: The Key to Durable and Reliable Device Construction