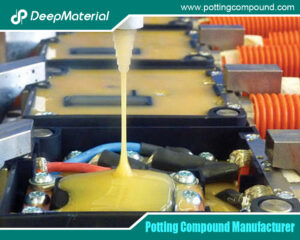
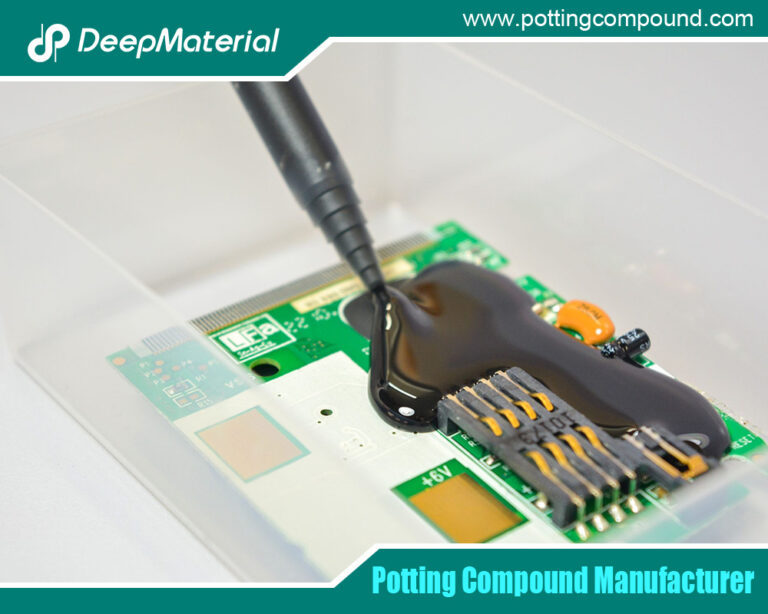
Enhancing Electrical Safety and Performance: A Deep Dive into Epoxy Powder Coating for Electrical Insulation
- Electronic Potting Material Manufacturer
- August 21, 2024
- Acrylic Conformal Coating, acrylic vs silicone conformal coating, conformal coating, conformal coating electronics, conformal coating for electronics, conformal coating for pcb, conformal coating for pcb standards, Conformal Coating in Electronic, conformal coating in electronics market, conformal coating manufacturers, conformal coating material, conformal coating material types, conformal coating pcb, conformal coating process, conformal coating silicone, conformal coating spray, conformal coating suppliers, conformal coating types, conformal coating waterproof, Epoxy Coating, epoxy coating for electrical insulation, Epoxy Powder Coating, Epoxy Powder Coating for Electrical, epoxy powder coating for electrical insulation, Epoxy Powder for Electrical Insulation, Industrial Conformal Coating, insulating epoxy coating, pcb conformal coating, Silicone Conformal Coating, Urethane Conformal Coating, UV Cure Conformal Coating, Waterproof Conformal Coating
Enhancing Electrical Safety and Performance: A Deep Dive into Epoxy Powder Coating for Electrical Insulation
Electrical insulation is crucial in ensuring the safety and efficiency of electrical components and systems. Epoxy powder coating stands out among various insulation materials for its unique properties and applications. This article explores the fundamentals, applications, advantages, manufacturing processes, testing standards, comparisons with other insulation methods, and future trends of epoxy powder coating in electrical insulation.
Section 1: Basics of Epoxy Powder Coating
Epoxy powder coating is a thermosetting polymer that consists of epoxy resin and a curing agent. It is applied as a dry powder and cured into a tough, protective layer through heat. This coating adheres to metal substrates, forming a seamless barrier that protects against electrical conductivity and environmental factors. The powder coating process involves electrostatic spraying, applied to a grounded substrate, ensuring even coverage before curing.
Section 2: Applications of Epoxy Powder Coating in Electrical Insulation
Due to their excellent insulation properties, epoxy powder coatings are widely used in electrical equipment and components. They are applied in:
- Transformers:Coating on transformer cores and windings provides insulation against high voltages and ensures operational reliability.
- Electric Motors:Insulating motor windings and components prevents electrical shorts and enhances lifespan.
- Switchgear and Circuit Breakers:Coating on contacts and internal components to prevent arcing and to improve reliability in electrical distribution systems.
- Capacitors:Insulating capacitor banks and components to maintain dielectric strength and to avoid leakage currents.
Section 3: Advantages of Epoxy Powder Coating
Epoxy powder coatings offer several advantages over traditional insulation methods:
- Thermal Stability:Withstand high temperatures without degradation, making them suitable for applications where heat dissipation is critical.
- Chemical Resistance:Resist oils, solvents, and other chemicals, ensuring longevity in harsh operating environments.
- Mechanical Durability:Provide a rugged, impact-resistant coating that protects against abrasion and mechanical stress.
- Dielectric Properties:Maintain high dielectric strength and insulation resistance, which are crucial for preventing electrical breakdown.
- Environmental Benefits:Low VOC emissions during application and curing, contributing to ecological sustainability.
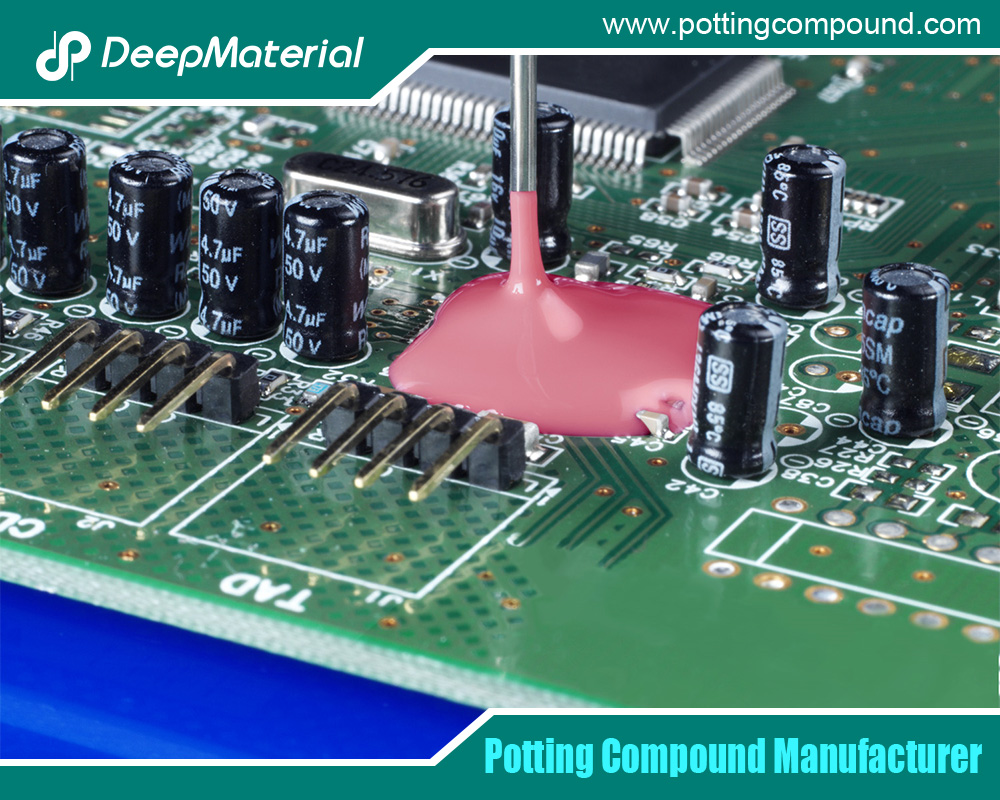
Section 4: Manufacturing Process of Epoxy Powder Coating
The manufacturing process of epoxy powder coating involves several stages:
- Formulation:Mixing epoxy resin, curing agents, pigments, and additives to achieve desired properties.
- Extrusion and Cooling:Extruding the mixture into long strands, cooling, and chipping into smaller particles.
- Milling and Classification:Milling the chips into fine powders of controlled particle size for uniform application.
- Application:Electrostatic spraying onto preheated metal substrates, followed by curing in ovens to cross-link the polymer chains and form a durable coating.
- Quality Control:Testing for thickness, adhesion, hardness, and other critical parameters to ensure compliance with specifications.
Section 5: Testing and Standards for Epoxy Powder Coating
Epoxy powder coatings undergo rigorous testing to ensure performance and reliability:
- Adhesion Testing:Determines the strength of the bond between the coating and the substrate.
- Thickness Measurement:Ensures uniform coating thickness to meet insulation requirements.
- Dielectric Strength:Measures the ability of the coating to withstand electrical stress without breakdown.
- Salt Spray Resistance:Evaluates corrosion resistance in marine and harsh environments.
- Impact and Flexibility:Tests for resistance to mechanical stress and deformation.
- Compliance with Standards:Conform to international standards such as ASTM, NEMA, and IEC for quality assurance and regulatory compliance.
Section 6: Comparison with Other Insulation Methods
Compared to traditional insulation methods like varnishes and resins, epoxy powder coating offers distinct advantages:
- Performance:Superior thermal and mechanical properties ensure longer service life and reliability.
- Application Efficiency:Faster curing times and reduced environmental impact during application.
- Cost-effectiveness:Lower maintenance costs and downtime due to extended service intervals and enhanced durability.
Section 7: Future Trends and Innovations
Future advancements in epoxy powder coating technology are focused on:
- Enhanced Performance:Development of coatings with higher dielectric strength and improved thermal dissipation capabilities.
- Environmental Sustainability:Formulations with reduced VOC emissions and energy-efficient curing processes.
- Innovative Coatings:Integration of sensors for real-time monitoring of insulation integrity and performance.
- Customization:Tailoring coatings for specific applications, such as high-frequency transformers and renewable energy systems.
Section 8: Adoption and Industry Insights
Adoption in Various Industries
Epoxy powder coatings have found extensive adoption across diverse industries due to their versatile properties and reliability:
- Energy and Utilities:Used in power generation, transmission, and distribution equipment to ensure safe and efficient operation.
- Automotive and Transportation:Applied in electric vehicle components, battery systems, and railway infrastructure for electrical insulation and corrosion protection.
- Industrial Manufacturing:Utilised machinery, control panels, and automation systems to safeguard against electrical hazards and environmental factors.
- Renewable Energy:Integral to wind turbines, solar inverters, and energy storage systems for insulation and reliability in renewable power generation.
Insights from Industry Experts
Industry experts emphasise the critical role of epoxy powder coatings in enhancing electrical system reliability and longevity:
- Amanda Lee, Electrical Engineer:“Epoxy powder coatings provide a robust barrier against electrical faults and environmental degradation, crucial for maintaining uptime and minimising maintenance costs in industrial applications.”
- John Martinez, Renewable Energy Specialist:“In renewable energy projects, such as solar farms and wind turbines, epoxy powder coatings ensure the durability and efficiency of electrical components exposed to varying weather conditions and operational demands.”
Section 9: Case Studies and Real-World Applications
Case Study 1: Transformer Insulation
Epoxy powder coatings are extensively used in transformer manufacturing to insulate windings and cores:
- Application:Coating applied to transformer windings ensures dielectric strength and thermal stability.
- Benefits:Enhances transformer efficiency, reduces electrical losses, and extends service life compared to traditional insulation methods.
Case Study 2: Electric Motor Protection
In electric motors, epoxy powder coatings protect against electrical shorts and mechanical stress:
- Application:Coating on motor windings and components prevents corrosion and insulation breakdown.
- Advantages:Improves motor efficiency, reliability, and operational safety in industrial and automotive applications.
Section 10: Environmental Considerations and Sustainability
Epoxy powder coatings contribute to sustainability initiatives through:
- Low VOC Emissions:Minimal volatile organic compound emissions during application and curing, reducing environmental impact.
- Longevity and Durability:Extended service life reduces material consumption and waste generation, promoting resource efficiency.
- Energy Efficiency:Energy-efficient curing processes and reduced maintenance requirements lower energy consumption and operational costs.
Section 11: Challenges and Mitigation Strategies
Despite its advantages, epoxy powder coating faces challenges such as:
- Complex Application:Requires specialised equipment and trained personnel for proper application and curing.
- Cost Considerations:Initial investment in equipment and materials may be higher than traditional insulation methods.
- Compatibility Issues:Compatibility with substrates and operational environments requires careful consideration and testing.
Mitigation Strategies
- Training and Education:Continuous training programs for operators and technicians to ensure proper handling and application techniques.
- Cost-Benefit Analysis:Conduct thorough cost-benefit analyses to justify investment in epoxy powder coatings based on long-term performance and lifecycle cost savings.
- Collaboration with Suppliers:Working closely with suppliers to customise formulations and address specific application challenges.
Section 12: Future Outlook and Emerging Trends
Innovations in Formulations and Applications
Future developments in epoxy powder coatings focus on the following:
- Advanced Formulations:Development of coatings with enhanced thermal conductivity, flame retardancy, and self-healing properties.
- Innovative Coatings:Integration of sensors and IoT technologies for real-time insulation integrity and performance monitoring.
- Biodegradable Options:Research into bio-based and recyclable epoxy formulations to further reduce environmental footprint.
Market Expansion and Adoption
As industries continue to prioritise efficiency, reliability, and sustainability in electrical systems, the demand for epoxy powder coatings is expected to grow:
- Renewable Energy Sector:Increasing deployment in wind and solar energy projects to enhance equipment reliability and operational efficiency.
- Electrification Trends:Adoption of electric vehicle batteries, charging infrastructure, and grid-scale energy storage systems to ensure safety and performance.
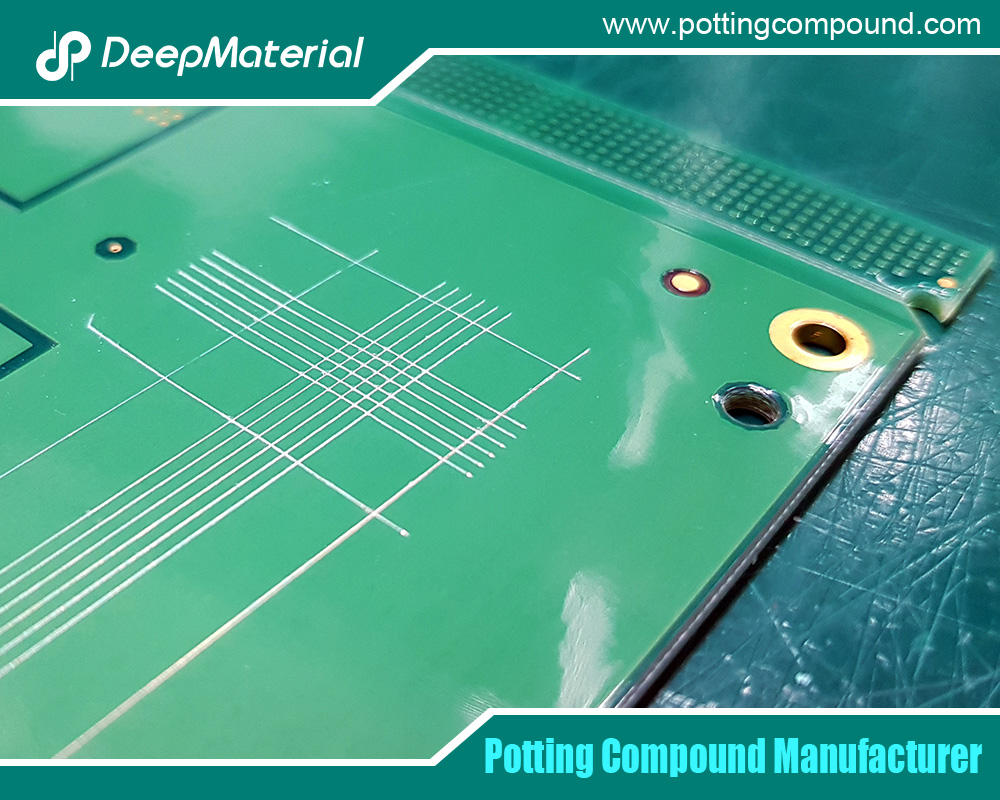
Conclusion
Epoxy powder coating represents a cornerstone in modern electrical insulation technology, offering unmatched durability, reliability, and environmental benefits. As industries continue to demand higher performance and sustainability from their electrical systems, epoxy powder coatings are poised to play a pivotal role in meeting these evolving requirements. By understanding their applications, advantages, manufacturing processes, testing standards, comparisons with other insulation methods, and future innovations, stakeholders can harness the full potential of epoxy powder coatings to enhance electrical safety and performance across various applications.
For more about enhancing electrical safety and performance: a deep dive into epoxy powder coating for electrical insulation, you can pay a visit to DeepMaterial at https://www.pottingcompound.com/ for more info.
Recent Posts
- How to Select Suitable Potting Materials for PCB According to the Working Environment
- What is PCB Potting
- The Evolution of Smart Watch Assembly Adhesive: A Key Component in Modern Wearable Technology
- Laptop Tablet Assembly Adhesive: The Key to Durable and Reliable Device Construction
- Power Bank Assembly Adhesive: The Essential Component for Building Durable Power Banks
- Smartphone Assembly Adhesive: Enhancing Durability and Precision in Modern Devices
- TV Backplane Support and Reflective Film Bonding: A Comprehensive Guide
- Innovative Use of Compounded Materials in Electronic Device Housings: A Comprehensive Guide
- Enhancing Battery Pack Performance: A Deep Dive into Potting Materials, Benefits, and Applications
- A Comprehensive Guide to Industrial Conformal Coatings: Applications, Types, and Future Trends