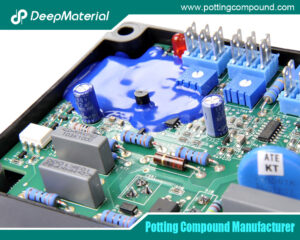
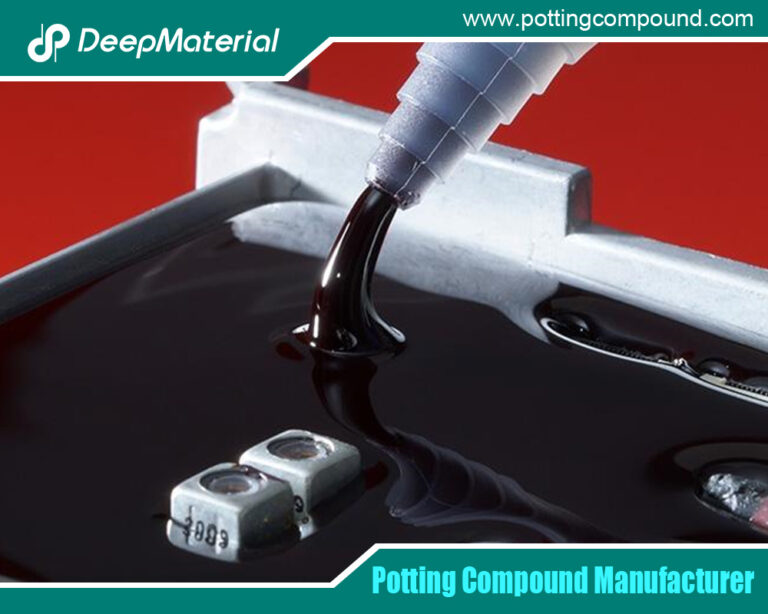
Enhancing Electronics Durability: A Deep Dive into Electronic Potting Compounds
- Electronic Potting Material Manufacturer
- December 16, 2024
- conformal coating for electronics, conformal coating for pcb, conformal coating for pcb standards, conformal coating material, conformal coating pcb, conformal coating process, conformal coating silicone, conformal coating spray, conformal coating types, conformal coating waterproof, Connector Potting Compound, electrical potting compound, electronic potting compound, Electronic Potting Compound Market, electronic potting compounds, Electronic Potting Compounds Manufacturer, epoxy potting compound, Flexible Potting Compound, LED Potting Compound, PCB Potting Compound, polyurethane potting compound, potting compound for electronics, potting compound for pcb, potting compound vs epoxy, Silicone Potting Compound, silicone potting compound for electronics, thermal potting compound, UV Cure Potting Compound, UV curing potting compound, waterproof potting compound
Enhancing Electronics Durability: A Deep Dive into Electronic Potting Compounds
Electronic potting compounds have become essential in modern electronics manufacturing, protecting sensitive components against environmental threats like moisture, dust, heat, and vibration. By creating a protective seal around circuit boards and other delicate elements, electronic potting compounds significantly enhance electronic devices’ lifespan, reliability, and safety. From industrial machinery to consumer gadgets, the application of these compounds helps manufacturers ensure device integrity even in challenging conditions. This article will explore electronic potting compounds’ types, benefits, and considerations, offering a comprehensive overview of their role in today’s electronics landscape.
Understanding the Basics of Electronic Potting Compounds
Potting compounds are specialty materials used to encapsulate electronic circuits for protection. They’re often applied to fill the enclosure around electronic assemblies, sealing the components entirely. Here’s a breakdown of their primary roles and types:
- Primary Function: Protect against external elements such as moisture, dust, shock, and vibrations.
- Types of Compounds: This category includes epoxy, polyurethane, and silicone-based potting compounds, each tailored to different protective needs.
- Fundamental Properties: Thermal stability, chemical resistance, and electrical insulation are among the top attributes that make these compounds indispensable in electronics.
Selecting the Right Potting Compound for Your Electronics
Choosing the correct potting compound is crucial for maximizing the durability and performance of an electronic device. Here are some key considerations when selecting a potting compound:
- Thermal Conductivity:A compound with good thermal conductivity is critical for high-power devices to prevent overheating.
- Dielectric Strength: Ensures the electrical insulation between components, essential for devices operating in high-voltage environments.
- Hardness and Flexibility: Harder compounds provide robust protection but may not suit components that experience regular vibration or movement; flexible compounds, such as silicone, can be more adaptable.
- Environmental Compatibility: Choose a compound based on exposure risks such as UV radiation, extreme temperatures, and chemical contact.
The Role of Potting Compounds in Different Industries
Electronic potting compounds are utilized in various fields, each with unique demands. Below are some industries where potting compounds play a pivotal role:
- Automotive: Protects electronic modules, sensors, and connectors in vehicles that must endure temperature fluctuations and vibrations.
- Consumer Electronics:Shields small gadgets and devices from moisture and wear, extending product lifespan.
- Medical Devices:Offers high levels of insulation and sterilization resistance for devices exposed to frequent cleaning.
- Aerospace:Provides critical stability for components exposed to high altitudes, severe temperatures, and pressure changes.
Potting vs. Conformal Coating: Key Differences
While both potting compounds and conformal coatings offer protection for electronic assemblies, they serve distinct purposes and provide different levels of security.
- Coverage:Potting involves encasing the entire assembly in a compound, while conformal coatings are thin layers applied over the surface.
- Protection Level: Potting protects against extreme environments, including high moisture and vibration.
- Application Process: Potting requires molding or casting around components, whereas conformal coatings can be sprayed or brushed on.
- Cost Considerations:Potting compounds are generally more expensive due to material and labor requirements, but they offer heightened protection for critical applications.
Common Challenges and Solutions in Potting Compound Application
Applying electronic potting compounds can present challenges, especially for intricate or sensitive electronic assemblies. Some of these common issues include:
- Bubbles and Voids Can affect insulation properties.
- Solution: Vacuum potting or degassing helps remove air bubbles during application.
- Excessive Heat Generation: Some potting processes may produce heat that can damage components.
- Solution: Use low-exothermic compounds and apply them in layers.
- Adhesion Issues: Poor adhesion can reduce the potting compound’s effectiveness.
- Solution:Ensure proper surface preparation, cleaning, and possibly using primers.
- Curing Time: Extended curing times can delay manufacturing.
- Solution: Select compounds with shorter curing times or opt for UV-curable options where feasible.
Key Advantages of Using Electronic Potting Compounds
Potting compounds bring a range of benefits that can improve device longevity and performance:
- Enhanced Durability: Increases the lifespan of electronics by shielding them from environmental stresses.
- Improved Thermal Management: Thermal potting compounds help dissipate heat, which is essential for high-performance electronics.
- Superior Moisture Resistance: This material acts as a barrier against moisture, which is crucial for devices used in humid or damp conditions.
- Electromagnetic Shielding: Some potting compounds protect against electromagnetic interference (EMI), a critical feature for electronics in high-density environments.
Sustainability and Potting Compounds: The Eco-Friendly Evolution
With increasing attention to sustainable practices, the potting compound industry is adapting to environmentally friendly materials and processes. Here’s how:
- Bio-based Compounds:Some manufacturers now offer potting compounds derived from renewable resources.
- Reduced Toxicity: New formulations lessen the use of hazardous materials, enhancing workplace safety and minimizing environmental impact.
- Recycling Options: While potting compounds traditionally make recycling difficult, newer materials are designed for easier separation, enabling partial recycling of electronic assemblies.
- Energy-Efficient Curing: UV-curable compounds offer a sustainable alternative with faster curing times and reduced energy consumption.
Future Trends in Electronic Potting Compounds
As electronics evolve, so will the materials used to protect them. Emerging trends in electronic potting compounds include:
- Nanotechnology:Integrating nanoparticles in potting compounds to improve thermal and mechanical properties.
- Innovative Materials: Development of compounds that adjust properties like flexibility and hardness in response to environmental changes.
- Automation in Application: Automated potting processes are becoming more common, ensuring consistency and efficiency in compound applications.
- High-Temperature Resistance: With the advent of advanced electronic devices, compounds with increased thermal tolerance are gaining traction.
Protecting Electronics from Environmental Hazards with Potting Compounds
Electronic potting compounds are a robust defense against various environmental hazards that can compromise the performance and longevity of devices. With advances in potting materials, manufacturers can now offer specialized protection for electronics used in challenging environments.
- Moisture and Humidity Resistance: Creates a waterproof seal around electronic components, preventing corrosion and short-circuiting in damp or humid conditions.
- Chemical Resistance: Shields sensitive electronics from corrosive chemicals and solvents, ideal for industrial and laboratory settings.
- Vibration and Shock Absorption:Potting compounds with flexible properties cushion components against mechanical stresses, enhancing durability in automotive and aerospace applications.
- Dust and Particulate Protection: This product prevents dust, dirt, and other particles from infiltrating and interfering with electronics, ensuring reliable performance in dusty or outdoor environments.
- UV and Thermal Stability:High-performance potting compounds resist UV degradation and can withstand extreme temperature changes, making them suitable for outdoor and high-heat applications.
Potting compounds address these environmental hazards, which is crucial for maintaining the stability, safety, and functionality of electronic devices in a wide range of demanding settings.
Conclusion
Electronic potting compounds are integral to modern electronics’ longevity, reliability, and performance. By shielding sensitive components from environmental and operational stresses, these compounds play a crucial role across various industries, from consumer electronics to aerospace. As technology advances and sustainability becomes a priority, potting compounds adapt to meet performance and environmental standards. By selecting a suitable potting material and understanding its application, manufacturers can significantly enhance the durability and functionality of their electronic products, supporting a future where technology withstands even the harshest conditions.
For more about choosing the top enhancing electronics durability: a deep dive into electronic potting compounds, you can pay a visit to DeepMaterial at https://www.pottingcompound.com/ for more info.
Recent Posts
- Influence of Encapsulation Thickness on the Heat Dissipation Performance and Electrical Insulation Performance of PCB
- Causes and Avoidance Methods of Bubble Generation in the Potting Process
- Technical Details on Controlling Parameters such as Temperature, Pressure, and Speed in the Potting Process to Ensure Potting Quality
- A Comprehensive Analysis of PCB Pretreatment Before Potting Process: A Crucial Link to Ensure the Performance and Reliability of Electronic Devices
- A Comprehensive Analysis of the Performance Differences of Epoxy Resin, Silicone Rubber and Polyurethane Encapsulation Materials
- How to Select Suitable Potting Materials for PCB According to the Working Environment
- What is PCB Potting
- The Evolution of Smart Watch Assembly Adhesive: A Key Component in Modern Wearable Technology
- Laptop Tablet Assembly Adhesive: The Key to Durable and Reliable Device Construction
- Power Bank Assembly Adhesive: The Essential Component for Building Durable Power Banks