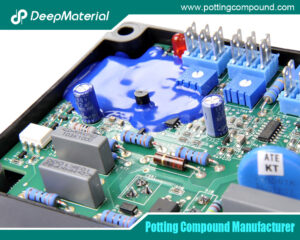
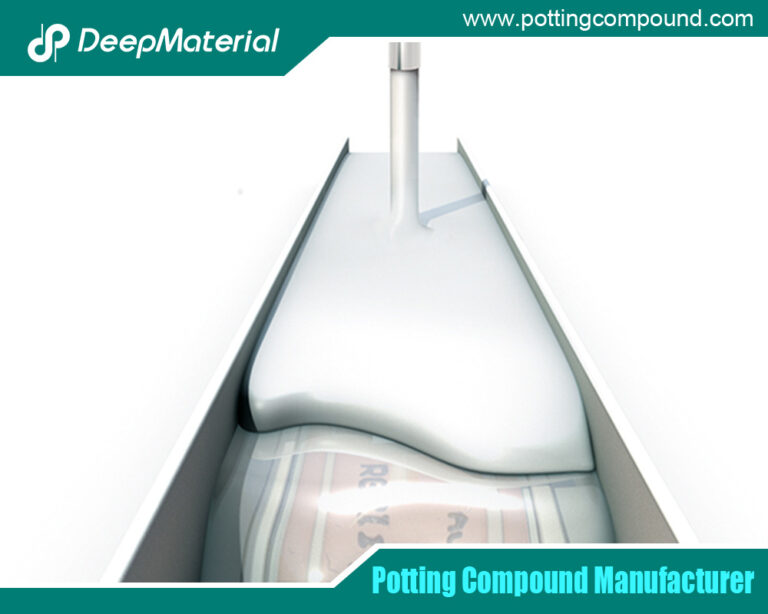
The Connector Potting Process: Ensuring Durability and Reliability in Electronics
- Electronic Potting Material Manufacturer
- November 22, 2024
- Connector Potting Compound, Connector Potting Process, Electronic Conformal Coating, electronic potting compound, epoxy conformal coating, epoxy potting compound, epoxy resin for potting electronic, Epoxy Resin for Potting Electronic China Hotsale, Epoxy Resin for Potting Electronic China OEM, Epoxy Resin for Potting Electronic China Wholesale, Epoxy Resin for Potting Electronic Factory Hotsale, Epoxy Resin for Potting Electronic Factory OEM, Epoxy Resin for Potting Electronic Factory Wholesale, Epoxy Resin for Potting Electronic Manufacturer, Epoxy Resin for Potting Electronic Supplier, Flexible Potting Compound, Industrial Conformal Coating, LED Potting Compound, pcb conformal coating, PCB Potting Compound, polyurethane potting compound, Potting Process, Silicone Potting Compound, Urethane Conformal Coating, UV Cure Conformal Coating, UV Cure Potting Compound, Waterproof Conformal Coating, waterproof potting compound
The Connector Potting Process: Ensuring Durability and Reliability in Electronics
In electronics, connectors serve as crucial links between various components, enabling communication and power transfer. As devices become increasingly compact and exposed to harsh environmental conditions, ensuring the durability and reliability of these connectors is paramount. One effective method for enhancing the performance of connectors is the potting process. This blog post will provide a detailed overview of the connector potting process, covering its significance, materials used, application techniques, benefits, challenges, and future trends.
Understanding the Potting Process
Potting encapsulates electronic components in a protective compound to enhance their performance and longevity. This process is essential for connectors, often exposed to moisture, dust, temperature fluctuations, and mechanical stress. By using potting compounds, manufacturers can protect connectors from environmental hazards and improve their reliability.
Critical Components of the Potting Process
- Potting Compound: A resin-based material encapsulates connectors, providing insulation and protection.
- Connector Type: The connector’s design and configuration influence the potting process, as different connectors may require specific techniques or compounds.
- Curing Method: This method hardens the potting compound, which can significantly affect the performance of the encapsulated connectors.
Why Potting Connectors Are Essential
Potting connectors offer several advantages that contribute to the reliability and performance of electronic devices. Some key reasons include:
Environmental Protection
Potting helps shield connectors from various environmental factors:
- Moisture: Prevents corrosion and electrical failures due to water ingress.
- Dust and Debris: Keeps internal components clean and operational.
- Temperature Extremes: Protects against thermal cycling and sudden temperature changes.
Mechanical Protection
Potting compounds provide a protective barrier around connectors, which enhances their mechanical strength. This is particularly important for:
- Vibration Resistance: Reduces the risk of connector damage in high-vibration environments, such as automotive and aerospace applications.
- Impact Protection: Safeguards against physical shocks and impacts that can occur during use.
Electrical Insulation
The potting process improves the electrical performance of connectors by providing excellent dielectric properties. This helps in:
- Preventing Short Circuits: Reduces the risk of electrical failures due to moisture or dust.
- Improving Signal Integrity: Maintains consistent performance of connectors in sensitive electronic systems.
Longevity and Reliability
Encapsulating connectors with potting compounds can significantly extend their lifespan and reliability, leading to the following:
- Reduced Failures: Minimizes the need for repairs and replacements.
- Cost-Effectiveness: Saves on maintenance costs in the long run.
The Potting Process: Step-by-Step
The potting process involves several key steps, each crucial for achieving optimal results. Here’s a detailed breakdown:
Step 1: Preparation
Proper preparation is essential for a successful potting process. This includes:
- Cleaning the Connectors: Remove any dirt, dust, or grease from the connectors to ensure proper adhesion of the potting compound.
- Drying: Ensure the connectors are completely dry to prevent moisture from interfering with the potting process.
Step 2: Selecting the Potting Compound
Choosing a suitable potting compound is vital for achieving the desired performance characteristics. Considerations include:
- Material Properties: Select compounds with the necessary viscosity, curing time, and thermal stability for the application.
- Compatibility: To avoid adverse reactions, ensure that the potting compound is compatible with the materials used in the connectors.
Step 3: Application of the Potting Compound
The application method for the potting compound can vary depending on the specific requirements of the connectors:
- Manual Application: This method is suitable for small batches or specialized connectors. It may involve pouring or dispensing the potting compound by hand.
- Automated Dispensing: This method is ideal for large-scale production where precise potting compound dispensing is required. Automated systems can use various methods, such as syringe dispensing or pressure pots.
Step 4: Curing the Potting Compound
Curing hardens the potting compound to form a solid encapsulation around the connectors. This can be achieved through various methods:
- Room Temperature Curing: Some potting compounds cure at ambient temperatures, making this method convenient and energy-efficient.
- Heat Curing: Applying heat can accelerate the curing process and enhance the properties of the potting compound, resulting in a stronger bond.
- UV Curing: Certain compounds can be cured using ultraviolet light, providing quick curing times and high-performance properties.
Step 5: Quality Control
After the potting process is complete, it is crucial to perform quality control checks to ensure that the connectors meet the required specifications. This may include:
- Visual Inspection: Checking for any defects or irregularities in the potting.
- Electrical Testing: Verifying the electrical performance of the encapsulated connectors to ensure they function as intended.
Benefits of the Potting Process for Connectors
The potting process offers numerous benefits, including:
- Enhanced Durability: Protects connectors from environmental hazards, ensuring long-lasting performance.
- Improved Reliability: Reduces the likelihood of connector failures, leading to more excellent system reliability.
- Cost Savings: Lowers maintenance and repair costs by minimizing the need for replacements.
- Versatility: Suitable for various applications across multiple industries, including automotive, aerospace, medical devices, and consumer electronics.
Challenges in the Potting Process
While the potting process offers significant benefits, there are challenges that manufacturers must consider:
Material Selection
Choosing the appropriate potting compound is critical, as different materials exhibit varying properties. Factors to consider include:
- Curing Time: Longer curing times can slow production, while quick-curing materials may compromise performance.
- Thermal Stability: Selecting a compound that can withstand the operating temperatures of the application is essential.
Application Techniques
Applying potting compounds can be challenging, particularly for complex connector designs. Issues may arise from:
- Air Entrapment: Care must be taken to avoid trapping air bubbles during the application, which can compromise the protective barrier.
- Inconsistent Coating: Ensuring a uniform application is essential for adequate protection.
Curing Conditions
Achieving the right curing conditions is crucial for optimal performance. Factors include:
- Temperature and Humidity: Fluctuations in these conditions can affect curing, leading to inconsistent results.
- Time Constraints: Balancing the need for quick production with the required curing times can be challenging.
Innovations and Future Trends in Connector Potting
As technology advances, so does the potting process for connectors. Some emerging trends include:
Eco-Friendly Materials
With growing environmental concerns, there is a shift towards using eco-friendly potting compounds. Manufacturers are increasingly seeking:
- Biodegradable Resins: To minimize environmental impact without sacrificing performance.
- Low-VOC Formulations: To improve workplace safety and reduce harmful emissions.
Smart Potting Solutions
Innovative materials that can respond to environmental changes are being developed. These innovative potting solutions may include:
- Self-healing potting compounds: They are capable of repairing minor damage automatically.
- Temperature-Sensitive Materials: They can adapt to temperature fluctuations, providing better protection.
Automation and Robotics
The use of automation and robotics in the potting process is becoming more prevalent, offering several advantages:
- Increased Precision: Automated systems ensure consistent application and reduce the risk of human error.
- Higher Throughput: Automation allows for faster production rates, improving overall efficiency.
Conclusion
The connector potting process is vital for ensuring the durability and reliability of electronic devices in a wide range of applications. Manufacturers can safeguard against environmental hazards, mechanical stress, and electrical failures by encapsulating connectors with protective potting compounds.
For more about choosing the connector potting process: ensuring durability and reliability in electronics, you can pay a visit to DeepMaterial at https://www.pottingcompound.com/ for more info.
Recent Posts
- Influence of Encapsulation Thickness on the Heat Dissipation Performance and Electrical Insulation Performance of PCB
- Causes and Avoidance Methods of Bubble Generation in the Potting Process
- Technical Details on Controlling Parameters such as Temperature, Pressure, and Speed in the Potting Process to Ensure Potting Quality
- A Comprehensive Analysis of PCB Pretreatment Before Potting Process: A Crucial Link to Ensure the Performance and Reliability of Electronic Devices
- A Comprehensive Analysis of the Performance Differences of Epoxy Resin, Silicone Rubber and Polyurethane Encapsulation Materials
- How to Select Suitable Potting Materials for PCB According to the Working Environment
- What is PCB Potting
- The Evolution of Smart Watch Assembly Adhesive: A Key Component in Modern Wearable Technology
- Laptop Tablet Assembly Adhesive: The Key to Durable and Reliable Device Construction
- Power Bank Assembly Adhesive: The Essential Component for Building Durable Power Banks