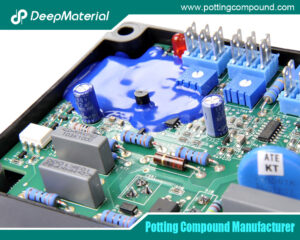
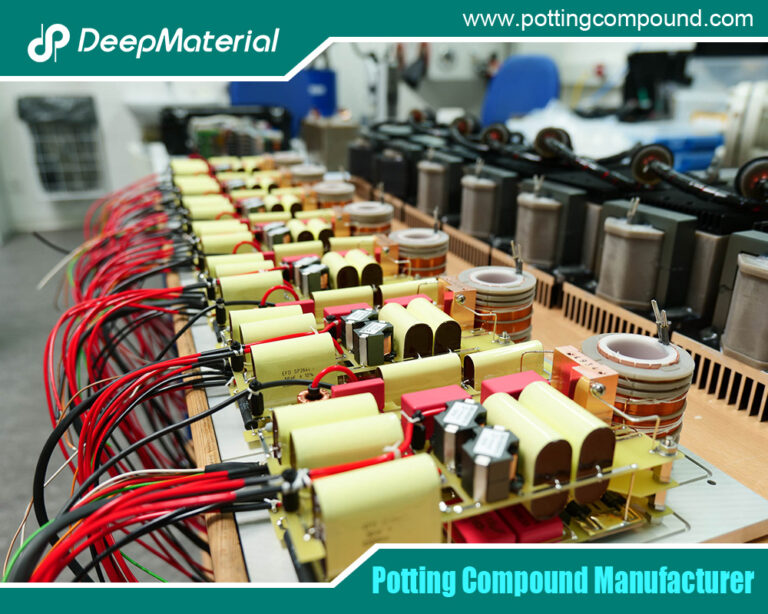
Exploring Potting Material Manufacturers: Innovations, Applications, and Industry Insights
- Electronic Potting Material Manufacturer
- July 22, 2024
- adhesive glue manufacturer, Automotive potting material manufacturers, circuit board potting, circuit board potting compound, Connector Potting Compound, custom automated electronics potting, customize china electronic potting silicone factories, customize china electronic potting silicone manufacturer, customize china electronic potting silicone supplier, deepmaterial PCB Potting, electrical potting compound, electronic potting material, epoxy potting compound, Epoxy potting material manufacturers, industrial adhesive suppliers, polyurethane potting compound, potting compound for electronics, potting compound for pcb, potting compound vs epoxy, potting material, potting material for electronic, potting material manufacturers, Potting material manufacturers in usa, silicone potting compound for electronics, thermal potting compound, UV curing potting compound, waterproof potting compound
Exploring Potting Material Manufacturers: Innovations, Applications, and Industry Insights
Potting materials play a crucial role in modern industries by providing protection and stability to sensitive electronic components, machinery, and renewable energy systems. This comprehensive guide delves into the world of potting material manufacturers, exploring their products, applications, manufacturing processes, market trends, and the factors to consider when choosing the proper manufacturer.
Section 1: Understanding Potting Materials
Potting materials are specially formulated compounds designed to encapsulate and protect electronic components, machinery, and structural elements from environmental factors such as moisture, vibration, and thermal stress. These materials are crucial in maintaining various devices’ operational integrity and longevity across industries. There are several types of potting materials commonly used:
- Epoxy Resins: Known for their excellent electrical insulation properties and resistance to chemicals and moisture.
- Silicone Compounds: Flexible and durable, ideal for thermal stability applications and environmental sealing.
- Polyurethanes: Versatile materials offering good physical properties and ease of processing.
- Acrylics: Fast-curing materials suitable for applications requiring rapid production turnaround.
Each type of potting material offers distinct advantages depending on the application’s specific requirements, such as temperature resistance, flexibility, and adhesion to substrates.
Section 2: Applications of Potting Materials
Potting materials find extensive use across various industries due to their ability to enhance the reliability and performance of critical components:
- Electronics Industry: Potting materials encapsulate sensitive electronic components such as circuit boards, sensors, and connectors. They protect these components from moisture, dust, and mechanical shock, ensuring reliable operation in diverse environments.
- Automotive Sector: Potting materials are employed in control units, ignition systems, and sensors in automotive applications. They safeguard electronics from vibration and thermal cycling, enhancing the durability and performance of automotive components.
- Aerospace and Defense: The aerospace industry relies on potting materials to protect electronic assemblies and sensors in aircraft and spacecraft. These materials must meet stringent standards for reliability, durability, and resistance to extreme temperatures and conditions.
- Renewable Energy: Potting materials are crucial in renewable energy systems such as solar panels, wind turbines, and energy storage devices. They provide insulation and protection to electronics and power components, ensuring optimal performance and longevity in outdoor and challenging environments.
Each application area demands specific performance characteristics from potting materials, driving continuous innovation in material formulations and manufacturing techniques.
Section 3: Manufacturing Process of Potting Materials
The manufacturing of potting materials involves several key stages to ensure quality and consistency:
- Raw Material Selection: Manufacturers carefully select raw materials based on the desired properties of the final product, such as electrical insulation, thermal conductivity, and mechanical strength.
- Formulation and Mixing: The selected raw materials are blended in precise ratios to achieve the desired material properties. Additives such as fillers, flame retardants, and adhesion promoters may be incorporated to enhance specific characteristics.
- Curing Methods: Potting materials are cured through various methods, including:
- Heat Curing: Utilising ovens or autoclaves to initiate chemical reactions and cross-linking polymers.
- Room Temperature Curing: Materials that cure at ambient temperatures, offering convenience and energy savings.
- UV Curing: Fast-curing formulations activated by ultraviolet light are suitable for rapid production cycles.
- Quality Control: Stringent quality control measures are implemented throughout manufacturing to ensure consistency and reliability. Testing procedures may include viscosity measurement, hardness testing, thermal cycling, and electrical insulation testing.
The choice of curing method and quality control practices significantly influence the performance and reliability of potting materials in real-world applications.
Section 4: Market Trends and Innovations
The potting material industry is characterised by continuous innovation and technological advancements to meet evolving market demands:
- Growth Drivers: The increasing adoption of electronics in the automotive, aerospace, and renewable energy sectors drives the demand for advanced potting materials. The emphasis on miniaturisation and lightweighting of components further boosts market growth.
- Technological Advancements: Manufacturers leverage nanotechnology to enhance material properties such as thermal conductivity and mechanical strength. Nanocomposites offer improved performance while reducing material usage.
- Environmental Sustainability: There is a growing focus on developing eco-friendly potting materials that minimise environmental impact without compromising performance. Biodegradable and recyclable formulations are gaining traction among environmentally conscious industries.
- Market Segmentation: The market for potting materials is segmented by region, end-user industry, and application type. Due to technological advancements and stringent regulatory standards, North America and Europe dominate the market.
- Regulatory Impact: Compliance with international standards and regulations, such as UL (Underwriters Laboratories) certification, is crucial for manufacturers to ensure product safety and market acceptance.
Section 5: Choosing the Right Potting Material Manufacturer
Selecting the proper potting material manufacturer is critical to achieving optimal performance and reliability in applications:
- Industry Experience and Expertise: Evaluate the manufacturer’s experience developing potting materials for specific industries and applications. Established manufacturers with a proven track record often offer reliable solutions tailored to customer requirements.
- Quality Certifications: Look for manufacturers with certifications such as ISO 9001 (Quality Management Systems) and UL recognition for electrical insulation. Compliance with regulatory standards demonstrates a commitment to product quality and safety.
- Customization Capabilities: Assess the manufacturer’s ability to customise potting materials to meet unique application requirements, such as material colour, viscosity, and curing profile.
- Supply Chain Reliability: Consider the manufacturer’s supply chain capabilities, including raw material sourcing, production scalability, and logistics management. A robust supply chain ensures consistent product availability and on-time delivery.
- Case Studies and References: Review case studies and customer testimonials to gauge the manufacturer’s success in delivering reliable potting solutions. References from industry peers can provide valuable insights into the manufacturer’s reputation and customer satisfaction.
Section 6: Case Studies of Leading Potting Material Manufacturers
The potting material industry is poised for continued growth and innovation driven by technological advancements and market demands. However, several challenges and opportunities lie ahead:
- Emerging Technologies: Advances in nanotechnology and materials science will continue to expand the performance capabilities of potting materials, enhancing electrical conductivity, thermal management, and mechanical strength.
- Environmental Regulations: Manufacturers will face increasing pressure to develop sustainable potting materials that comply with stringent environmental regulations and support green manufacturing practices.
- Global Market Expansion: The demand for potting materials is expected to grow across emerging markets in Asia-Pacific and Latin America, driven by industrialization, urbanisation, and infrastructure development.
- Industry Collaboration: Collaborative efforts between manufacturers, research institutions, and end-users will drive innovation and address industry-specific challenges, such as miniaturisation and reliability in harsh environments.
- Supply Chain Resilience: Ensuring resilience in the supply chain, including raw material sourcing and logistics management, will be crucial to meet growing demand and mitigate risks associated with global economic uncertainties.
Conclusion
Potting materials safeguard electronic components and critical systems across diverse industries. As technological advancements and market demands continue to evolve, potting material manufacturers are at the forefront of innovation, developing advanced formulations that enhance performance, reliability, and environmental sustainability. By understanding the key considerations in choosing a potting material manufacturer and staying informed about industry trends, stakeholders can effectively navigate the dynamic landscape of potting materials and drive innovation in their respective fields.
For more about exploring potting material manufacturers: innovations, applications, and industry insights, you can pay a visit to DeepMaterial at https://www.pottingcompound.com/ for more info.
Recent Posts
- Influence of Encapsulation Thickness on the Heat Dissipation Performance and Electrical Insulation Performance of PCB
- Causes and Avoidance Methods of Bubble Generation in the Potting Process
- Technical Details on Controlling Parameters such as Temperature, Pressure, and Speed in the Potting Process to Ensure Potting Quality
- A Comprehensive Analysis of PCB Pretreatment Before Potting Process: A Crucial Link to Ensure the Performance and Reliability of Electronic Devices
- A Comprehensive Analysis of the Performance Differences of Epoxy Resin, Silicone Rubber and Polyurethane Encapsulation Materials
- How to Select Suitable Potting Materials for PCB According to the Working Environment
- What is PCB Potting
- The Evolution of Smart Watch Assembly Adhesive: A Key Component in Modern Wearable Technology
- Laptop Tablet Assembly Adhesive: The Key to Durable and Reliable Device Construction
- Power Bank Assembly Adhesive: The Essential Component for Building Durable Power Banks