How to Remove Potting Compound
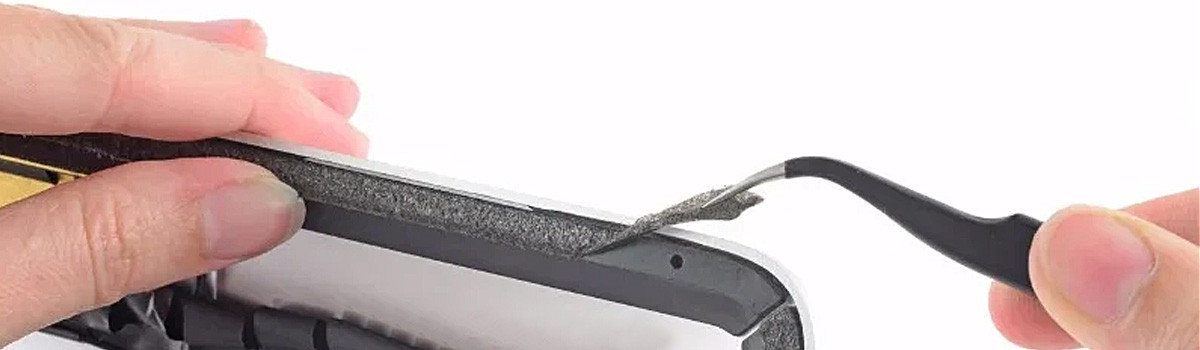
Potting compounds are commonly used in electronics and electrical applications to protect components from moisture, dust, and other environmental hazards. However, there may come a time when you need to remove the potting compound, either for repairs, upgrades, or recycling purposes. Knowing the proper techniques for removing potting compounds can save time and prevent damage to sensitive components. This guide will explore various methods and tips for safely and effectively eliminating potting compounds from electronics and electrical assemblies.
Table of Contents
ToggleCritical information you should understand:
What is a potting compound, and why might you need to remove it?
A potting compound is commonly used in electronics and electrical engineering to encapsulate and protect sensitive components. It is a type of thermosetting polymer resin that, when cured, forms a hard, protective shell around the components it encases. This compound serves several purposes, including insulation from environmental factors such as moisture, dust, chemicals, and mechanical shocks. It also provides structural support, prevents vibration-induced damage, and enhances the thermal conductivity of components by dissipating heat effectively.
However, there are situations where it becomes necessary to remove the potting compound:
- Repair and Maintenance: When a component inside the encapsulated assembly fails or requires maintenance, the potting compound must be removed to access and replace the faulty part. This could be a damaged capacitor, resistor, or other component needing servicing.
- Upgrades and Modifications: In some cases, upgrades or modifications to the electronics may be necessary. Removing the potting compound allows engineers to change the circuitry or replace outdated components with newer ones.
- Quality Control and Testing: During manufacturing, it’s essential to conduct quality control tests on individual components. Removing potting compounds enables technicians to inspect components for defects or irregularities that may affect performance.
- Environmental Concerns: Some potting compounds contain hazardous materials that can pose environmental risks if improperly handled. Removing and disposing of old or damaged potting compounds responsibly helps mitigate these risks.
- End-of-Life Recycling: When electronic devices end their lifespan, recycling becomes crucial for recovering valuable materials and minimizing electronic waste. Removing potting compounds allows for the separation and recycling of components and materials.
- Reverse Engineering: In situations where reverse engineering is necessary, such as understanding the design of a competitor’s product or analyzing a legacy system, removing the potting compound may be required to access and study the internal components and circuitry.
While potting compounds provide valuable protection and stability to electronic components, there are various scenarios where their removal is necessary for repair, maintenance, testing, environmental considerations, or reverse engineering purposes.
What safety precautions should be taken before attempting to remove the potting compound?
Before attempting to remove the potting compound, it’s crucial to ensure safety precautions are in place to minimize risks associated with the process. Potting compounds, often used in electronic components to provide insulation and protection, can be hazardous due to their chemical composition and potential for releasing harmful fumes or particles during removal. Here are some essential safety precautions to consider:
- Personal Protective Equipment (PPE):Wear appropriate PPE such as safety goggles, gloves, a respirator mask, and protective clothing to prevent direct contact with the potting compound and to minimize inhalation of fumes or dust.
- Ventilation:Work in a well-ventilated area to reduce exposure to potentially harmful fumes or airborne particles. Use exhaust fans or open windows to improve air circulation during removal.
- Chemical Compatibility:Identify the type of potting compound used (e.g., epoxy, silicone) and research its chemical properties to ensure compatibility with the removal method and any solvents or chemicals being used.
- Read Material Safety Data Sheets (MSDS):Review MSDS or safety data sheets provided by the manufacturer for information on potential hazards, recommended protective measures, and first aid procedures in case of exposure.
- Isolation:If possible, isolate the work area from other sensitive equipment or areas to prevent contamination or damage from debris generated during the removal process.
- Tools and Equipment:Use appropriate tools and equipment to remove the potting compound safely. This may include heat guns, chemical solvents, scrapers, or specialized debonding agents designed for the specific type of potting material.
- Fire Safety:Be aware of the potential fire hazards associated with particular removal methods, especially those involving heat sources. Keep fire extinguishing equipment readily available and follow proper fire safety protocols.
- Training and Supervision:Ensure that personnel involved in the removal process are adequately trained in handling hazardous materials and follow established safety procedures. Supervision by experienced individuals can help minimize risks and ensure safe practices are followed throughout the process.
- Emergency Preparedness:Have emergency response procedures in place in case of accidents or exposure to hazardous materials. This includes knowing the location of emergency exits, eyewash stations, and first aid kits and how to respond to chemical spills or injuries.
Implementing these safety precautions can help mitigate the risks associated with removing potting compounds and ensure the safety of the personnel involved. Always prioritize safety and follow recommended guidelines to prevent accidents or injuries.
What tools and materials are commonly used for removing potting compounds?
Potting compound removal typically involves a combination of tools and materials tailored to the specific properties of the compound and the surface it’s adhered to. Potting compounds are commonly used in electronics and other industries to encapsulate and protect sensitive components from environmental factors like moisture, vibration, and heat. However, there are situations where the potting compound needs to be removed for repairs, upgrades, or recycling purposes. Here are some commonly used tools and materials for eliminating potting compounds:
- Heat Guns: Heat guns are often used to soften the potting compound, making removing it easier. By applying heat evenly to the surface, the compound softens and becomes more pliable, allowing for easier extraction.
- Chemical Solvents: Solvents dissolve or weaken the bond between the potting compound and the substrate. Typical solvents include acetone, methyl ethyl ketone (MEK), isopropyl alcohol, and various proprietary solvent blends formulated explicitly for potting compound removal.
- Mechanical Tools: Mechanical tools such as chisels, scrapers, screwdrivers, and dental picks physically break apart and remove the softened potting compound. Care must be taken to avoid damaging the underlying components or substrate.
- Ultrasonic Cleaners: Ultrasonic cleaners use high-frequency sound waves to agitate a solvent, enhancing its cleaning power. This method is particularly effective for removing potting compounds from small or intricate components where mechanical tools may not be suitable.
- Abrasive Materials: Abrasive materials like sandpaper or abrasive wheels can rub away the potting compound once heat or solvent softens it. This method requires caution to avoid damaging delicate components or substrates.
- Protective Gear: Safety equipment such as gloves, safety glasses, and respirators may be necessary when working with heat guns, solvents, and abrasive materials to protect against burns, chemical exposure, and inhalation of fumes.
- Cleanup Supplies: Rags, sponges, brushes, and containers for solvent disposal are essential for cleaning the work area and removing any residual potting compound or solvent.
Removing the potting compound involves a combination of heat, solvents, mechanical tools, and protective gear to soften, dissolve, or physically remove the compound while minimizing damage to the underlying components or substrate. The specific tools and materials used will depend on the type of potting compound, the substrate material, and the desired outcome of the removal process.
How can heat be used to soften potting compounds for removal?
Heat can be a highly effective method for softening potting compounds to facilitate their removal. Potting compounds are commonly used in electronics to encapsulate and protect components from moisture, vibration, and other environmental factors. However, when repair or component replacement is necessary, removing these compounds without damaging the components they protect becomes essential. Here’s how heat can be employed for this purpose:
- Thermal Expansion: Potting compounds, typically epoxy resins, soften and expand when exposed to heat. This expansion creates stress within the compound, causing it to lose its adhesive properties and become more pliable. As the material softens, it releases its grip on the components, making them easier to remove.
- Temperature Control: Controlling the temperature is crucial to prevent damage to sensitive electronic components while softening the potting compound. Heating elements such as heat guns, hot plates, or ovens can apply controlled heat to the encapsulated area. Thermocouples or infrared thermometers can monitor the temperature to ensure it remains within a safe range.
- Gradual Heating: Gradually increasing the temperature allows the potting compound to soften uniformly without causing thermal shock to the components. Rapid temperature changes can lead to cracking or delamination of the encapsulated materials, which may compromise the integrity of the electronics.
- Localized Heating: Focused heat application to specific areas can help soften targeted sections of the potting compound without affecting surrounding components. This can be achieved using heat shields or heat-resistant materials to protect adjacent parts.
- Mechanical Assistance: While heating softens the potting compound, mechanical tools such as dental picks, chisels, or tweezers can remove it. Care must be taken to avoid damaging the components or the circuit board during this process.
- Safety Considerations: Proper ventilation is essential when using heat to soften potting compounds, as some compounds may release toxic fumes when heated. Personal protective equipment such as heat-resistant gloves and safety glasses should also be worn to prevent injury.
Heat can effectively soften potting compounds for removal by inducing thermal expansion, controlling temperature, and applying gradual, localized heating. Heat offers a reliable method for extracting encapsulated components from electronic devices when combined with appropriate mechanical techniques and safety precautions.
What are the steps for using solvents to dissolve potting compounds?
Solvents to dissolve potting compounds involve several steps to ensure effective and safe compound removal. Potting compounds are typically used to encapsulate electronic components for protection and insulation. When removal is necessary, solvents can be employed to dissolve the compound. Here’s a general guide:
- Identify the Potting Compound: Determine the type of potting compound used. Common types include epoxy, silicone, polyurethane, and acrylic. Different compounds may require different solvents for dissolution.
- Select Suitable Solvent: Choose a solvent compatible with the potting compound. Solvent compatibility charts or consulting material safety data sheets (MSDS) can help select the appropriate solvent. Typical solvents include acetone, methyl ethyl ketone (MEK), toluene, xylene, and isopropyl alcohol.
- Prepare Safety Equipment: Wear appropriate personal protective equipment (PPE) such as gloves, goggles, and respirators if working in a poorly ventilated area. Ensure the workspace is well-ventilated to prevent inhalation of solvent vapors.
- Apply Solvent: Apply the selected solvent to the potting compound. This can be done by brushing, spraying, or immersion, depending on the size and accessibility of the component. Allow the solvent to penetrate and soften the potting compound.
- Monitor Progress: Monitor the dissolution process closely. The time required for dissolution can vary depending on factors such as the type of solvent, the thickness of the potting compound, and the ambient temperature.
- Remove Dissolved Compound: Once the potting compound has softened and dissolved, remove it from the electronic component using tools such as brushes, scrapers, or compressed air. Repeat solvent application if necessary to ensure complete removal.
- Clean Residual Solvent: After removing the dissolved potting compound, clean the electronic component to remove any residual solvent. This can be done using a clean cloth or rinsing with a solvent-compatible cleaner.
- Dispose of Waste Properly: Dispose of solvent-soaked materials and waste according to local regulations. Solvent waste should be handled and disposed of properly to prevent environmental contamination.
- Safety Precautions: Throughout the process, observe safety precautions to minimize exposure to solvents and ensure safe handling and disposal practices.
Following these steps carefully, you can effectively use solvents to dissolve and remove the potting compound from electronic components. Always prioritize safety and follow proper disposal procedures to prevent environmental harm and ensure a successful outcome.
Are there any environmentally friendly solvents suitable for removing potting compounds?
Yes, there are environmentally friendly solvents suitable for removing potting compounds, particularly in electronics manufacturing or repair, where potting compounds are commonly used. Potting compounds are typically resins or polymers used to encapsulate electronic components to protect against environmental factors like moisture, vibration, and shock.
One environmentally friendly solvent option is citrus-based solvents. These solvents are derived from natural citrus extracts and are effective at dissolving many organic compounds without harsh chemicals. They are biodegradable and have low toxicity, making them safer for workers and the environment. Citrus-based solvents can be used to soften and remove potting compounds without damaging the underlying electronic components.
Another option is soy-based solvents. These solvents are made from soybean oil and are non-toxic, biodegradable, and renewable. They offer similar effectiveness to traditional solvents but with significantly lower environmental impact. Soy-based solvents can penetrate and break down potting compounds, allowing easy removal without leaving harmful residues behind.
Additionally, terpene-based solvents derived from pine or other plant sources can be effective and environmentally friendly options for removing potting compounds. Terpenes are natural hydrocarbons found in many plants and have solvent properties that make them suitable for various applications, including potting compound removal. Like citrus and soy-based solvents, terpene-based solvents are biodegradable and have low toxicity.
It’s important to note that the effectiveness of environmentally friendly solvents may vary depending on the specific type of potting compound being removed and the application method. In some cases, a combination of solvents or mechanical methods may be needed for complete removal.
Overall, using environmentally friendly solvents for removing potting compounds aligns with efforts to reduce the environmental impact of manufacturing processes while maintaining effective and safe solutions for electronic component maintenance and repair.
Can mechanical methods such as scraping or grinding remove potting compounds?
Yes, mechanical methods such as scraping or grinding can remove potting compounds. However, their effectiveness may depend on various factors, such as the type of potting compound, the potted materials, and the desired outcome.
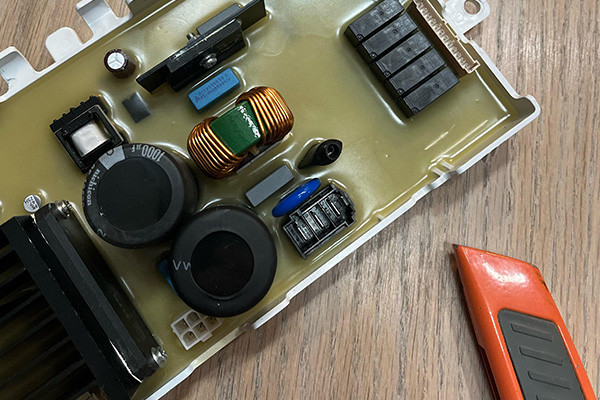
Scraping is a standard method for removing potting compounds, especially when dealing with softer compounds or when precision is required. This method involves using tools such as chisels, scrapers, or knives to carefully chip away at the potting material and remove it layer by layer. It’s crucial to exercise caution when scraping to avoid damaging the underlying components or surfaces.
Grinding is another mechanical method that effectively removes potting compounds, particularly for more complex or resilient compounds. Grinding involves using abrasive tools such as sandpaper, grinding wheels, or rotary tools to wear away the potting material until it is entirely removed. This method is often faster than scraping but may generate more heat and debris, so proper ventilation and safety measures are essential.
When using mechanical methods to remove potting compounds, it’s essential to consider the potential impact on the surrounding components and surfaces. Careful planning and execution are necessary to avoid damaging sensitive components or creating unintended consequences. Additionally, proper protective equipment such as goggles, gloves, and masks should be worn to ensure safety during the process.
In some cases, a combination of mechanical methods may be used, depending on the specific requirements of the task. For example, scraping may be employed initially to remove the bulk of the potting compound, followed by grinding to clean up any remaining residue or uneven surfaces.
Overall, while mechanical methods such as scraping or grinding can be effective for removing potting compounds, they require careful attention to detail and safety considerations to achieve the desired results without damaging the surrounding materials.
What are the risks associated with aggressive mechanical removal of potting compounds?
Aggressive mechanical removal of potting compound, a process commonly employed in electronics repair or component salvage, poses several significant risks that can affect both the integrity of the components and the safety of personnel performing the removal. Here are some critical risks associated with this process:
- Component Damage: Aggressive mechanical removal techniques, such as scraping or grinding, can inadvertently damage delicate electronic components. Components like integrated circuits, resistors, capacitors, and wires are vulnerable to physical stress or deformation caused by excessive force or friction.
- Electrical Damage: Mechanical removal methods increase the likelihood of short circuits or damage to electrical connections within the device. Scratches, gouges, or accidental severing of conductive traces can compromise the device’s functionality or render it completely inoperable.
- Release of Hazardous Materials: Some potting compounds contain hazardous materials such as lead, cadmium, or toxic chemicals. Aggressive mechanical removal can generate dust, debris, or airborne particles containing these substances, posing health risks to individuals involved in the removal process if proper protective measures are not taken.
- Contamination of Surrounding Components: Mechanical removal can result in the dispersion of potting compound particles onto surrounding components or circuitry. These particles may cause electrical shorts, corrosion, or damage to adjacent components, leading to further complications or failures.
- Physical Injury: Using tools or machinery for aggressive removal increases the risk of physical injury to personnel. Accidental slips, tool malfunctions, or flying debris can cause cuts, abrasions, or more severe injuries if proper safety precautions, such as wearing protective gear, are not observed.
- Voiding of Warranty: Aggressive mechanical removal methods often void warranties manufacturers provide. Attempting to repair or salvage components using such techniques may result in losing warranty coverage, leaving individuals liable for any subsequent damages or replacement costs.
To mitigate these risks, technicians should consider alternative removal methods, such as solvent-based or thermal techniques, which offer gentler approaches to potting compound removal. Additionally, adherence to proper safety protocols, including personal protective equipment and adequate ventilation, is essential to minimize the health and safety hazards associated with aggressive mechanical removal.
How can ultrasonic cleaning be employed to remove potting compounds?
Ultrasonic cleaning is a highly effective method employed in various industries to remove contaminants, residues, and coatings from surfaces. Ultrasonic cleaning can offer significant advantages when it comes to eliminating potting compounds commonly used to encapsulate electronic components for protection.
Potting compounds are often resilient and can adhere firmly to surfaces, making their removal challenging. However, ultrasonic cleaning utilizes the principle of cavitation to dislodge and dissolve contaminants from substrates. Cavitation occurs when high-frequency sound waves are passed through a liquid, creating microscopic bubbles. These bubbles implode near the cleaned surface, generating intense localized pressure and temperatures, effectively loosening and removing contaminants.
To employ ultrasonic cleaning for potting compound removal, the following steps are typically involved:
- Selection of Cleaning Solution: Choosing the appropriate cleaning solution is crucial. The solution should be compatible with the potting compound and the substrate material. Solvents or detergents formulated explicitly for breaking down potting compounds may be used.
- Setup: The electronic component or assembly containing the potting compound is immersed in the chosen cleaning solution within an ultrasonic cleaning tank.
- Ultrasonic Cleaning Process: The ultrasonic cleaner generates high-frequency sound waves propagating through the cleaning solution. As the sound waves pass through the solution, they create cavitation bubbles.
- Cavitation Action: The cavitation bubbles collapse near the component’s surface, creating localized agitation and pressure. This action effectively dislodges the potting compound from the substrate.
- Rinse and Dry: The component is typically rinsed thoroughly to remove any remaining cleaning solution and loosened debris after the cleaning cycle. Subsequently, it is dried to prevent water spots or corrosion.
- Inspection: Once dried, the component is inspected to ensure complete removal of the potting compound. If necessary, additional cleaning cycles may be performed.
Ultrasonic cleaning offers several advantages for removing potting compounds, including its ability to clean intricate geometries, its non-destructive nature to delicate components, and its efficiency in eliminating stubborn contaminants. However, optimizing cleaning parameters such as frequency, temperature, and duration is essential to achieve the best results without damaging the components. Additionally, proper disposal of cleaning solutions and adhering to safety precautions are crucial considerations in the ultrasonic cleaning process.
Are there any specific considerations for removing potting compounds from delicate electronic components?
Removing potting compounds from delicate electronic components requires careful attention to prevent damage to the components. Potting compounds are often used to protect electronic devices from moisture, shock, and vibration, but they can become problematic when repair or component extraction is necessary. Here are some specific considerations for safely removing potting compound:
- Assessment of Component Sensitivity: Before attempting to remove the potting compound, assess the sensitivity of the electronic components. Mechanical stress or temperature fluctuations may easily damage delicate components such as integrated circuits (ICs), resistors, and capacitors.
- Selection of Removal Method: Choose the appropriate method for removing the potting compound based on the type of compound used and the components involved. Standard methods include mechanical removal using dental picks or screwdrivers, thermal methods like heating or freezing, and chemical solvent dissolution.
- Temperature Control: If using a thermal method, exercise caution when controlling the temperature carefully. Rapid temperature changes can cause thermal shock, leading to component damage. Gradual heating or cooling is preferable, and the temperature should be kept within safe limits for the components.
- Mechanical Stress Management: When employing mechanical methods, apply gentle pressure and precision tools to minimize the risk of damaging delicate components. Work slowly and patiently to avoid accidental slips or excessive force that could cause component breakage.
- Chemical Compatibility: If using chemical solvents for dissolution, ensure compatibility with the potting compound and the electronic components. Some solvents may cause corrosion or damage specific materials, so research and testing are essential before application.
- Safety Precautions: Wear appropriate personal protective equipment (PPE), gloves, and goggles when handling chemical solvents. Work in a well-ventilated area to avoid inhaling fumes, and follow safety guidelines provided by the solvent manufacturer.
- Post-Removal Inspection: After removing the potting compound, carefully inspect the electronic components for any signs of damage or contamination. Clean components thoroughly, if necessary, using appropriate methods and materials.
- Documentation and Testing: Document the removal process and any observations made during the inspection. Test the components to ensure they function correctly before reassembly or further use.
By following these considerations, technicians can safely remove potting compounds from delicate electronic components without causing damage, facilitating repair or replacement.
Can freezing techniques aid in the removal of potting compounds?
Freezing techniques can help remove potting compounds, especially when dealing with electronic components or devices encapsulated within the compound. Potting compounds often protect electronic assemblies from environmental factors such as moisture, dust, and vibration. However, removing the potting compound without damaging the components can be challenging when repairs or modifications are necessary.
One method involves utilizing the thermal expansion and contraction properties of materials. Potting compounds typically have a higher coefficient of thermal expansion than the materials they encapsulate, such as circuit boards and components. When the assembly is subjected to freezing temperatures, the potting compound contracts more than the components, creating stress and potentially weakening the bond between the compound and the parts it encases.
Liquid nitrogen is commonly used for freezing applications due to its extremely low temperature of around -196°C (-321°F). The assembly can be submerged in liquid nitrogen or exposed to a stream of vapors to cool it down rapidly. As the potting compound contracts, it may become more brittle, making it easier to break or chip away.
Freezing can also alter the physical properties of the potting compound, making it less adhesive or more prone to cracking. This allows for mechanical methods such as scraping, chiseling, or even thermal cycling (alternating between freezing and heating) to weaken the bond further and facilitate removal.
However, it’s essential to exercise caution when employing freezing techniques. Rapid temperature changes can induce thermal stress in sensitive components, potentially causing damage. Therefore, controlled and gradual cooling methods may be preferable, especially when dealing with delicate electronic parts.
Also, freezing may not be suitable for all potting compounds or components. Some compounds may not contract significantly when subjected to low temperatures, or the elements may be sensitive to cold environments.
Freezing techniques can be valuable tools for removing potting compounds from electronic assemblies, leveraging materials’ differential thermal expansion properties. However, careful consideration of the specific materials involved and the potential risks to the components is essential to ensure successful and safe removal.
What are some common challenges encountered when attempting to remove potting compounds?
Removing a potting compound, a material used to encapsulate electronic components can pose several challenges due to its adhesive and insulating properties. Some common challenges encountered when attempting to remove potting compound include:
- Adhesion Strength: Potting compounds are designed to adhere firmly to the components they encapsulate and to the surrounding substrate. This strong adhesion can make it difficult to remove the compound without damaging the components or substrate.
- Hardness: Potting compounds can harden over time, becoming rigid and challenging to remove. Their hardness can make mechanical removal methods such as scraping or chiseling ineffective or risky, as they may cause damage to the components or substrate.
- Insulating Properties: Potting compounds are often formulated to provide insulation and protection to electronic components. While this property benefits the components during operation, it can hinder efforts to remove the compound, as traditional solvents or chemical methods may not effectively penetrate or dissolve the material.
- Compatibility: The choice of solvent or chemical agent for removing the potting compound must be compatible with both the compound itself and the materials of the components and substrate. Using incompatible solvents can lead to damage or corrosion of the components or substrate.
- Environmental Concerns: Some potting compounds contain hazardous or toxic substances, posing environmental and safety concerns during removal. Proper disposal of the removed compound and associated chemicals is essential to prevent ecological and human health harm.
- Time and Labor Intensive: Removing potting compounds can be time-consuming and labor-intensive, especially if multiple components need to be extracted or the compound is particularly stubborn. This can increase downtime and production costs for electronic devices or systems undergoing repair or refurbishment.
- Precision and Care: Careful handling and precision are required when attempting to remove the potting compound to avoid damaging delicate electronic components or causing harm to the substrate. This necessitates skilled personnel and specialized tools or equipment.
Overall, the challenges of removing potting compounds underscore the importance of careful planning, proper equipment, and expertise to ensure successful extraction while minimizing damage to components and substrates.
How can one determine the type of potting compound used and the appropriate removal method?
Determining the type of potting compound used and choosing the appropriate removal method requires a systematic approach, considering both the compound’s properties and the potted component. Here’s a guide to help:
Identification of Potting Compound Type:
- Visual Inspection: Examine the potting material’s color, texture, and transparency. Is it hard or soft? Does it have any distinct odor?
- Material Safety Data Sheets (MSDS): If available, consult the MSDS provided by the manufacturer. This document typically includes information about the composition and properties of the potting compound.
- Thermal Analysis: Some potting compounds respond differently to temperature changes. Conducting thermal analysis, such as differential scanning calorimetry (DSC), can help identify thermally reactive compounds.
- Chemical Tests: Perform simple chemical tests to identify specific compounds, such as the presence of epoxy, silicone, or polyurethane.
Consideration of Component Compatibility:
- Compatibility Testing: Test the selected removal method on a small, inconspicuous component area to ensure it doesn’t damage the material.
- Thermal Sensitivity: Determine if the component is sensitive to heat, as some removal methods involve heating.
- Mechanical Sensitivity: Assess whether the component can withstand mechanical stress, as mechanical removal methods may be abrasive.
Selection of Removal Method:
- Chemical Solvents: Depending on the potting compound type, certain solvents like acetone, isopropyl alcohol, or specialized solvent blends may effectively soften or dissolve the potting material.
- Thermal Methods: Heat can soften or melt some potting compounds, facilitating removal. Techniques include using hot air guns, ovens, or heat plates.
- Mechanical Methods: Mechanical removal involves physical scraping, chiseling, or grinding. It’s suitable for complex potting compounds but requires caution to avoid damaging the component.
- Combination Approach: In some cases, a combination of methods might be necessary for effective removal, such as softening the compound with a solvent before mechanical extraction.
Safety Precautions:
- Ventilation: Ensure adequate ventilation when working with chemical solvents or heat to avoid inhalation of fumes.
- Personal Protective Equipment (PPE): Wear appropriate PPE, gloves, goggles, and respiratory protection, as needed.
- Environmental Considerations: Dispose of removed potting material and cleaning agents according to local regulations.
Following these steps, one can accurately determine the potting compound type and select the most suitable removal method while prioritizing safety and minimizing damage to the potted component.
Is it possible to reuse or recycle potting compound after removal?
Potting compounds, commonly used in electronics and manufacturing industries, encapsulate and protect delicate components from environmental factors such as moisture, dust, and vibration. Once applied, removing potting compounds can be challenging, often involving chemical solvents or mechanical methods. However, despite its resilience, recycling or reusing potting compound after removal presents several challenges.
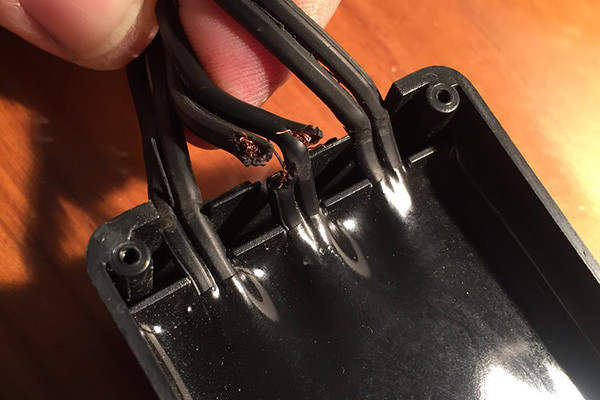
One of the primary obstacles to recycling potting compounds is their altered chemical composition and physical properties after use. Potting compounds undergo curing processes that change their molecular structure, making it difficult to revert to their original form. Additionally, during removal, contaminants such as dust, debris, or other chemicals may mix with the compound, further complicating recycling efforts.
However, some companies and researchers are exploring innovative methods to repurpose or recycle potting compounds. One approach involves separating and purifying the compound through chemical processes, aiming to isolate its core components for reuse. This method requires extensive research and development to identify suitable techniques for effectively recovering usable material from the removed compound.
Another potential avenue for recycling potting compounds involves incorporating them into other materials or products. For example, ground-up potting compounds could be mixed with polymers or resins to create composite materials with desirable properties. However, this approach requires thorough testing to ensure compatibility and performance in the final product.
Despite these efforts, challenges must be solved to establish efficient and cost-effective recycling processes for potting compounds. Limited demand for recycled potting compounds and the high costs associated with collection, processing, and purification hinder the widespread adoption of recycling initiatives.
While reusing or recycling potting compounds after removal is technically feasible, it poses significant challenges. Research into innovative recycling methods and collaboration between industry stakeholders is essential to overcome these hurdles and establish sustainable practices for managing potting compound waste. Additionally, advancements in material science and recycling technology may offer promising solutions in the future, driving toward a more circular approach to potting compound usage and disposal.
What are the potential consequences of improper potting compound removal?
Improper removal of potting compound, a substance used to encapsulate electronic components, can lead to several consequences ranging from functional impairment to physical damage. Here are some potential repercussions:
- Component Damage: Potting compounds protect environmental factors like moisture, dust, and vibrations. Improper removal can expose sensitive electronic components to these elements, leading to corrosion, short circuits, or other forms of damage.
- Electrical Malfunctions: If potting compound removal damages wires, circuits, or connections, it can cause electrical malfunctions. This may include intermittent connections, increased resistance, or complete failure of the device.
- Safety Hazards: In some applications, potting compounds insulate high-voltage components. Improper removal can compromise this insulation, posing risks of electric shock or fire hazards.
- Voiding Warranties: Many electronic devices have warranties that become void if the device is tampered with or damaged due to improper handling. Improper removal of potting compound may result in warranty voidance, leaving the user responsible for repair or replacement costs.
- Performance Degradation: Potting compounds may be specifically chosen to enhance thermal conductivity, protect against thermal cycling, or provide other performance-enhancing properties. Improper removal can compromise these characteristics, leading to reduced efficiency or lifespan of the device.
- Costly Repairs: Repairing damage caused by improper potting compound removal can be expensive. It may involve replacing damaged components, rewiring circuits, or even replacing the entire device, depending on the extent of the damage.
- Time and Effort: Removing potting compounds improperly can be time-consuming and labor-intensive. Identifying and rectifying any resulting issues, troubleshooting, and diagnostic work may be required.
- Environmental Impact: Improperly removed potting compounds may contain hazardous materials that can have ecological implications if not disposed of properly. This includes potential soil, water, or air contamination if the compounds are not handled according to regulations.
Improper removal of potting compounds can result in various consequences, including damage to electronic components, safety hazards, warranty voidance, performance degradation, costly repairs, and environmental impact. Following proper procedures and guidelines when dealing with potting compounds is crucial to mitigate these risks.
Are there any specialized services or professionals that offer potting compound removal?
Potting compound removal is a specialized service often sought in electronics manufacturing, repair, and recycling industries. Potting compounds, such as epoxy resins, silicones, and urethanes, encapsulate electronic components to protect against environmental factors like moisture, shock, and vibration. However, there are instances where the removal of these compounds becomes necessary, such as during repair, component replacement, or recycling processes.
Several specialized professionals and services cater to the need for potting compound removal:
- Electronics Repair Technicians: Skilled technicians with experience in electronics repair may offer potting compound removal services. They use various techniques and tools to safely extract components from the encapsulating material without damaging them.
- Engineering Services: Some engineering firms specialize in reverse engineering and component salvage. They have expertise in safely removing potting compounds to access and salvage valuable components for reuse or refurbishment.
- Materials Science and Chemical Engineering Consultants: Materials science and chemical engineering professionals offer consultancy services for potting compound removal. They develop custom solutions and processes tailored to specific materials and applications, ensuring safe and efficient compound removal.
- Environmental and Recycling Companies: Companies specializing in electronic waste recycling often offer potting compound removal as part of their services. They employ environmentally friendly techniques to extract components from electronic devices for recycling while minimizing waste generation.
- Specialized Equipment Manufacturers: Some companies manufacture equipment specifically for potting compound removal. These may include thermal heating systems, mechanical extraction tools, or chemical dissolution processes tailored to different potting compounds.
- Research Institutions: Universities and research institutions with expertise in materials science and engineering may offer potting compound removal services for research purposes or as part of collaborative projects with industries.
When seeking potting compound removal services, factors such as the type of potting compound used, the sensitivity of the components involved, environmental concerns, and the desired outcome (e.g., component salvage, recycling, or repair) must be considered. Working with experienced professionals ensures the safe and effective removal of potting compounds while preserving the integrity of the encapsulated components.
How can one minimize damage to surrounding components during potting compound removal?
Minimizing damage to surrounding components during potting compound removal is crucial to preserve the integrity and functionality of electronic devices. Potting compounds, often used to encapsulate and protect sensitive components, can become difficult to remove without causing harm to adjacent parts. Here are some methods to minimize damage:
- Heat Application: Applying controlled heat to the potting compound can soften it, making removal easier. However, it’s essential to use precise temperature control to prevent overheating nearby components, which could lead to damage or malfunction.
- Chemical Softeners: Certain chemicals can weaken the bond of the potting compound without affecting surrounding components. It’s crucial to select chemicals compatible with the materials used in the device and follow proper safety protocols when handling chemicals.
- Mechanical Methods: Chisels, knives, or drills can help break apart the potting compound. However, extreme care must be taken to avoid accidentally damaging adjacent components. Precision and a steady hand are essential when using mechanical methods.
- Ultrasonic Treatment: Ultrasonic waves can effectively break down potting compounds without causing damage to nearby components. This method benefits delicate electronic assemblies where mechanical force could cause harm.
- Selective Dissolution: Employing solvent-based solutions that selectively dissolve the potting compound while leaving other components unaffected can be a practical approach. However, thorough testing is necessary to ensure the solvent does not react with or damage nearby materials.
- Protective Shielding: Before applying any removal method, surrounding components can be shielded with materials such as tape, silicone barriers, or protective coatings to minimize the risk of damage. This creates a physical barrier between the removal process and the sensitive components.
- Expertise and Experience: Entrusting the task to professionals in electronic repair and component removal can significantly reduce the likelihood of damage. Experienced technicians understand the intricacies of various removal methods and can apply them skillfully to minimize collateral damage.
By employing these methods carefully and judiciously, it is possible to remove potting compounds while mitigating the risk of damage to surrounding components, ensuring electronic devices’ continued functionality and reliability.
Are there any alternative methods for encapsulating electronics besides potting compounds?
Yes, there are several alternative methods for encapsulating electronics besides potting compound, each with its own advantages and specific applications:
- Conformal Coating: This method involves applying a thin protective coating over the electronic components, PCBs, and connections. Conformal coatings can be silicone, acrylic, urethane, or epoxy. They protect against moisture, dust, chemicals, and electrical shock while maintaining flexibility and allowing for easy repair or rework.
- Enclosure Encapsulation: Enclosing electronics within a sealed enclosure or casing is a standard protection method. Depending on the application requirements, enclosures can be made from various materials, such as plastic, metal, or glass. This method provides physical protection against environmental factors and mechanical stress.
- Gel Encapsulation: Gel encapsulation involves filling the enclosure or housing with a soft gel-like material, such as silicone or polyurethane gel. This method offers excellent protection against vibration, shock, and thermal cycling while maintaining flexibility and allowing easy access to components when needed.
- Vacuum Sealing: Vacuum sealing involves removing air and moisture from the enclosure or packaging before sealing it completely. This method prevents oxidation, corrosion, and moisture ingress, making it suitable for sensitive electronic components and devices operating in harsh environments.
- Potting with Encapsulating Films: Instead of using traditional potting compounds, some applications may benefit from encapsulating films, which are thin, flexible films applied directly onto the electronic components. These films protect against moisture, dust, and mechanical stress, offering easy application and reworkability.
- Encapsulating with Resin Injection Molding: Resin injection molding is a method where liquid resin is injected into a mold containing the electronic components. Once cured, the resin forms a solid, protective layer around the components, providing excellent mechanical and environmental protection.
Each alternative method offers unique advantages and suitability for different applications, ranging from consumer electronics to industrial and automotive applications. The choice of encapsulation method depends on factors such as environmental conditions, mechanical stress requirements, reworkability, and cost considerations.
What are some DIY tips for safely and effectively removing potting compounds?
Potting compounds, commonly used in electronics and other applications to protect components from moisture and mechanical damage, can be challenging to remove once cured. Here are some DIY tips for safely and effectively eliminating potting compounds:
- Heat Method: Apply heat to soften the potting compound. Use a heat gun or hairdryer on a low setting to gently warm the compound. Be cautious not to overheat, as this could damage surrounding components or materials.
- Chemical Solvents: Certain solvents can dissolve potting compounds. Standard options include acetone, isopropyl alcohol, or specialized adhesive removers. Apply the solvent with a brush or cloth, allowing it to penetrate the compound. Always work in a well-ventilated area and wear appropriate safety gloves and goggles.
- Mechanical Methods: Mechanical methods like scraping or peeling can be effective for softer potting compounds. Use non-abrasive tools such as plastic or wooden scrapers to avoid damaging surfaces underneath.
- Ultrasonic Cleaning: If feasible, consider using an ultrasonic cleaner. Submerging the components in a solvent while subjecting them to ultrasonic vibrations can help dislodge and dissolve the potting compound.
- Freezing Method: In some cases, freezing the potting compound can make it more brittle and more accessible to remove. Place the component in a freezer for several hours, then carefully chip away at the compound using a non-metallic tool.
- Combinations: A combination of methods may be necessary for stubborn potting compounds. For example, you might soften the compound with heat and then use a solvent to dissolve it further before mechanically removing the residue.
- Safety Precautions: Regardless of the method used, prioritize safety. Wear appropriate personal protective equipment (PPE) such as gloves, goggles, and a respirator if working with chemicals or generating airborne particles.
- Test on a Small Area: Before applying any method to the entire component, test it on a small, inconspicuous area to ensure compatibility and effectiveness.
- Patience: Removing the potting compounds can be time-consuming, particularly for large or intricate components. Exercise patience and work methodically to avoid causing damage.
You can safely and effectively remove potting compounds from electronic components or other surfaces using these DIY tips. However, always exercise caution and prioritize safety throughout the process.
Can potting compound removal be automated or scaled up for industrial applications?
Potting compound removal, typically used to encapsulate electronic components to protect against environmental factors, can be automated and scaled up for industrial applications. Automation and scaling are essential for efficiency, consistency, and cost-effectiveness in industrial settings.
Automation of potting compound removal can be achieved through various methods:
- Robotic Systems: Robotic arms equipped with specialized end-effectors can be programmed to remove potting compounds from electronic components precisely. These robots can execute tasks with high repeatability and accuracy, reducing the risk of damage to delicate components.
- Chemical Solutions: Automated systems can utilize chemical solutions tailored for potting compound removal. These solutions can be applied in a controlled manner using pumps, sprayers, or immersion baths. Automation ensures uniform application and minimizes waste.
- Mechanical Processes: Automated machinery can employ mechanical methods such as milling, grinding, or ultrasonic vibration to break down and remove potting compounds. These processes can be optimized for efficiency and adapted to various component shapes and sizes.
Scaling up potting compound removal for industrial applications involves increasing throughput and capacity while maintaining quality standards. This can be achieved through:
- Parallel Processing: Implementing multiple automated systems in parallel can significantly increase throughput. By running several removal processes simultaneously, production capacity can be scaled up to meet demand.
- Optimized Workflow: Analyzing and optimizing the workflow, including material handling, processing, and quality control steps, can improve efficiency and minimize downtime. Streamlining the process ensures smooth operation at scale.
- Customization and Flexibility: Industrial-scale systems should be adaptable to different types of potting compounds and electronic components. Customizable parameters and interchangeable tooling allow for versatility in handling diverse products.
- Continuous Monitoring and Maintenance: Implementing sensors and monitoring systems ensures consistent quality and identifies potential real-time issues. Scheduled maintenance protocols keep equipment running smoothly and minimize unexpected downtime.
Potting compound removal can be automated and scaled up for industrial applications by integrating robotic systems, chemical solutions, mechanical processes, and optimized workflows. By leveraging automation and scalability, manufacturers can enhance efficiency, reduce costs, and meet the demands of modern electronics production.
Conclusion:
Removing potting compounds from electronics and electrical assemblies requires careful consideration of techniques, safety measures, and potential risks. Whether using heat, solvents, mechanical methods, or a combination thereof, it’s essential to approach the process cautiously to avoid damaging sensitive components. By following appropriate guidelines and best practices, individuals and professionals can safely and effectively remove potting compounds as needed.
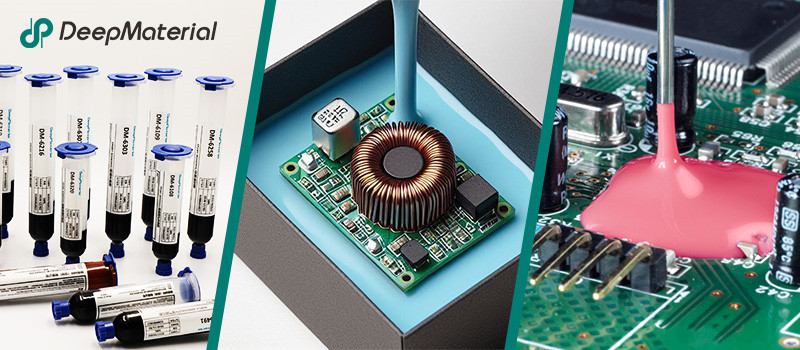
About DeepMaterial
DeepMaterial is a trusted supplier of encapsulant materials that are used in electronics manufacturing worldwide. From chip on board encapsulants such as glob top material to conformal coatings, underfills, low pressure molding, and potting solutions, DeepMaterial offers a full range of circuit board protection materials that effectively protect circuit boards while help reduce costs. More…Deepmaterial is a the manufacturer of epoxy adhesives including hardeners, metalbond, and metal filled resins. Structural, toughened medium viscosity, and non-sag adhesives are also offered. Some adhesives are resistant to thermal shock, chemical, vibration dampening, and impact. Suitable for metals, plastics, wood, and ceramics. Serves electronics, aerospace, automotive, tooling, marine, and construction industries. REACH and RoHS compliant. FDA approved. UL listed. Meets military specifications. We are the one of best adhesive manufacturers in China.
Blogs & News
Potting compounds are at the frontline of electronics assembly, delivering effective protection in challenging environmental conditions while improving mechanical strength and offering high electric insulation. Used within a variety of industries, electrical potting compounds are found within a broad range of consumer electronics, as well as used in applications across the automotive, aerospace, and other industries where electronic assemblies are prevalent.
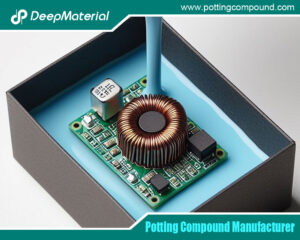
Potting Compound vs. Epoxy: A Comprehensive Comparison
Potting Compound vs. Epoxy: A Comprehensive Comparison In the world of electronics, manufacturing, and material encapsulation, two terms frequently come up: potting compounds and epoxy.
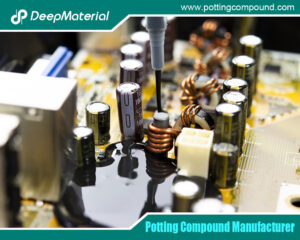
Potting Compound for PCB
Potting Compound for PCB A potting compound is a liquid or semi-liquid material that is poured or injected over a PCB or electronic assembly, then
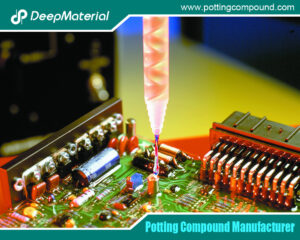
In – depth Analysis of the Curing Characteristics of Electronic Potting Compounds
In – depth Analysis of the Curing Characteristics of Electronic Potting Compounds Electronic potting compounds play a vital role in the electronics industry. They can
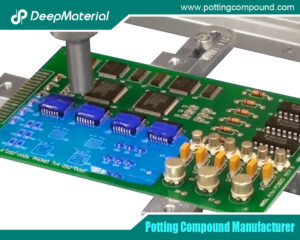
A Comprehensive Analysis of the Environmental Performance of Encapsulating Materials: From Regulations to Practices
A Comprehensive Analysis of the Environmental Performance of Encapsulating Materials: From Regulations to Practices In modern industrial manufacturing, encapsulating materials are widely used in numerous

A Comprehensive Analysis of PCB Encapsulation Quality Inspection: Innovative Application of Non-Destructive Testing Technologies
A Comprehensive Analysis of PCB Encapsulation Quality Inspection: Innovative Application of Non-Destructive Testing Technologies In the field of electronic manufacturing, the encapsulation process of printed
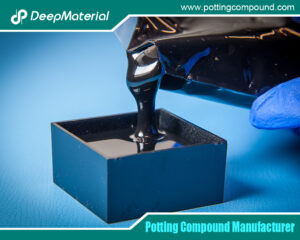
Analysis of the Improvement of the Seismic and Impact Resistance Performance of PCB by Encapsulation
Analysis of the Improvement of the Seismic and Impact Resistance Performance of PCB by Encapsulation During the operation of electronic devices, the PCB (Printed Circuit