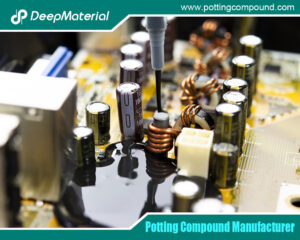
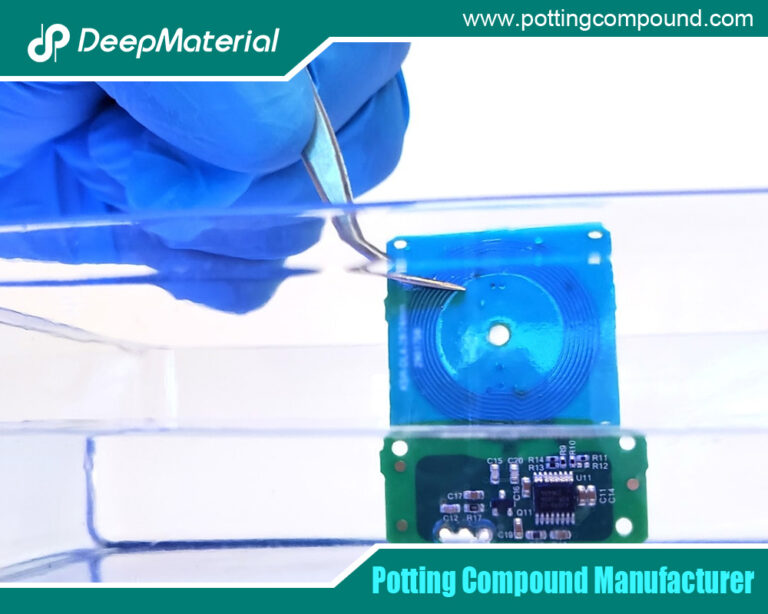
Innovating The Future: Exploring Electronic Coating Material Manufacturing In Electronics Industry
- Electronic Potting Material Manufacturer
- June 19, 2024
- coating for electronic implants, conformal coating electronics, conformal coating manufacturers, conformal coating material, conformal coating material types, conformal coating suppliers, contact electronic coatings technologies, electric coating technologies, electrical insulating coating for metal, electrical insulation coating, electronic coating technologies, electronic coating technologies services, electronics conformal coating, high temperature electrical insulation coating, high voltage conformal coating, high-temperature insulation coatings for transformers, insulated coating supplier for electrical, modified conformal coating manufacture, pcb conformal coating, sharp edge coverage conformal coatings, silicone vs acrylic conformal coating, waterproof coating for electronics, waterproof electronics coating, waterproof nano coating for electronics
Innovating The Future: Exploring Electronic Coating Material Manufacturing In Electronics Industry
Electronic coating materials play a pivotal yet often overlooked role in the dynamic world of electronics, where innovation is the currency of progress. These materials are the unsung heroes, providing protection, insulation, and functionality to electronic components, ensuring their longevity and reliability in harsh environmental conditions. In this blog post, we delve into the world of electronic coating material manufacturing, exploring its significance, advancements, challenges, and the promising future it holds.
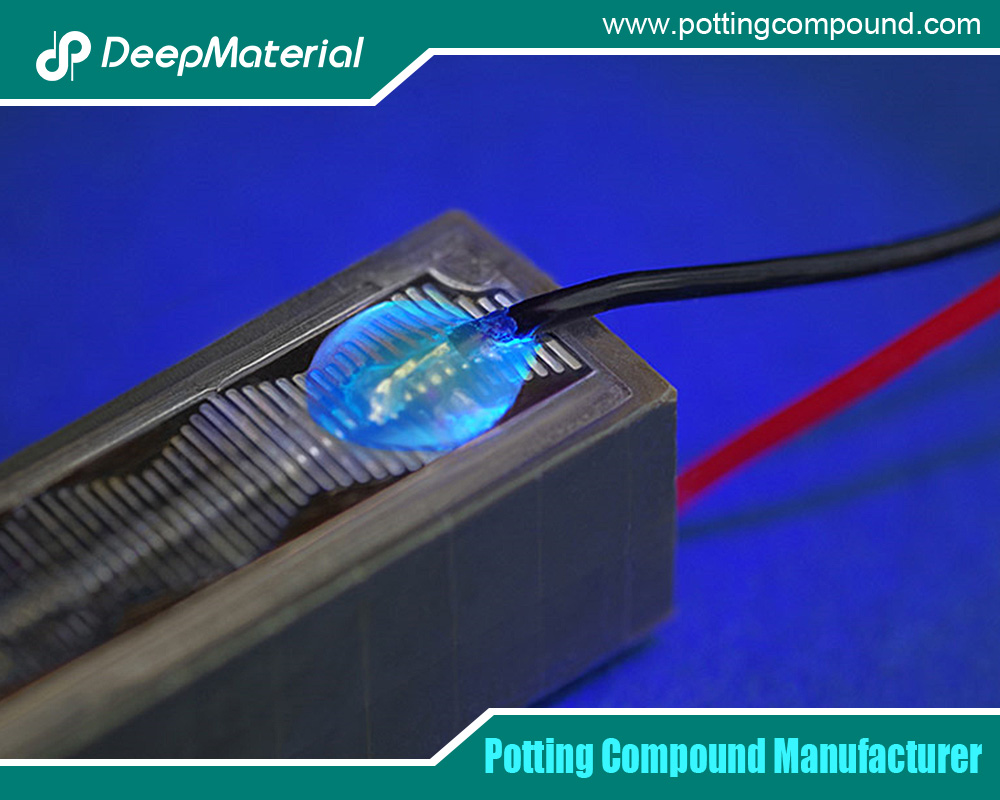
The Importance of Electronic Coating Materials
Electronic coating materials protect components from various environmental factors, ensuring their reliability and longevity. This paragraph explores the importance of electronic coating materials in the electronics industry, highlighting their role in safeguarding against moisture, corrosion, dust, and other contaminants.
Environmental Protection:
Electronic coating materials create a protective barrier around electronic components, shielding them from moisture, humidity, dust, and chemical contaminants. This barrier prevents corrosion, electrical short circuits, and performance degradation caused by exposure to harsh environmental conditions, ensuring the reliability and functionality of electronic devices in various operating environments.
Thermal Management:
In addition to environmental protection, electronic coating materials contribute to thermal management by dissipating heat generated by electronic components during operation. Thermally conductive coating materials help transfer heat away from sensitive components, preventing overheating and thermal damage. Effective thermal management ensures the reliable performance of electronic devices, particularly in applications with high power densities or elevated operating temperatures.
Mechanical Stability:
Electronic coating materials provide mechanical stability and shock absorption, protecting electronic components against mechanical stress and vibration. By encapsulating components in a resilient material, electronic coating materials help prevent damage from physical impact and mechanical shock, ensuring the integrity and longevity of electronic devices in applications prone to mechanical stress, such as automotive and industrial environments.
Advanced Materials and Manufacturing Processes
As electronic devices become increasingly sophisticated and diverse in their applications, the demand for high-performance coating materials continues to rise. Electronic coating material manufacturers play a pivotal role in developing and supplying advanced materials tailored to the specific needs of various industries. Their expertise in formulating innovative coatings and employing cutting-edge manufacturing processes is essential for ensuring electronic products’ reliability, durability, and functionality in challenging environments.
- Nano-coatings: Electronic coating material manufacturers leverage nanotechnology to develop nano-coatings with unique properties such as superhydrophobicity, self-healing capabilities, and enhanced electrical conductivity. These coatings offer superior protection against moisture, corrosion, and wear, making them ideal for automotive, aerospace, and consumer electronics applications.
- Conductive Polymers: Conductive polymers are gaining traction as coating materials for electronic devices due to their lightweight, flexible, and electrically conductive properties. Manufacturers are exploring novel synthesis techniques and additive formulations to improve the performance and durability of conductive polymer coatings for applications such as printed electronics and wearable devices.
- Flame-retardant Coatings: With an increasing focus on safety and regulatory compliance, electronic coating material manufacturers are developing flame-retardant coatings that meet stringent industry standards. These coatings provide vital protection against fire hazards while maintaining the integrity and functionality of electronic components in critical applications such as electrical panels, power supplies, and industrial control systems.
- Thin-film Deposition Techniques: Advanced thin-film deposition techniques such as atomic layer deposition (ALD) and chemical vapor deposition (CVD) enable manufacturers to precisely control the thickness, composition, and properties of coatings at the nuclear level. These techniques allow for the deposition of ultra-thin protective layers with exceptional uniformity and adhesion, paving the way for developing next-generation electronic devices with enhanced performance and reliability.
- Environmentally Friendly Formulations: Electronic coating material manufacturers increasingly focus on developing environmentally friendly formulations that minimize hazardous chemicals and reduce carbon footprint. By adopting sustainable raw materials and manufacturing processes, these manufacturers are addressing the growing demand for eco-friendly coating solutions while ensuring compliance with regulatory requirements and corporate sustainability goals.
Through continuous innovation and collaboration with research institutions and industry partners, electronic coating material manufacturers are driving advancements in materials science and manufacturing technology to meet the evolving needs of electronic manufacturers and end-users worldwide.
Applications Across Industries
Electronic coating material manufacturers play an indispensable role in electronics, providing essential solutions for protecting sensitive electronic components from environmental factors and mechanical stress. These manufacturers develop and supply a wide range of coating materials tailored to the diverse needs of the automotive, aerospace, and consumer electronics industries. Understanding the applications of electronic coating materials across various sectors is crucial for appreciating their significance in enhancing the reliability and performance of electronic devices.
- Automotive Industry: Electronic coating materials are extensively used in automotive electronics to protect control units, sensors, and wiring harnesses from moisture, corrosion, and thermal cycling. These coatings help ensure the reliability and longevity of critical electronic components in vehicles, enhancing safety and performance.
- Aerospace and Defense: Electronic coating materials protect avionics systems, communication devices, and radar equipment from harsh operating environments, including extreme temperatures, humidity, and vibration. These coatings are essential for maintaining the integrity and functionality of electronic systems in mission-critical applications.
- Consumer Electronics: Electronic coating materials enhance the durability and reliability of consumer electronics such as smartphones, tablets, and wearables. These coatings protect against moisture ingress, dust, scratches, and accidental damage, prolonging the lifespan of electronic gadgets and improving user experience.
- Industrial Applications: Electronic coating materials find diverse applications in industrial settings, including automation, robotics, and process control systems. These coatings protect electronic components from exposure to chemicals, solvents, and abrasive materials commonly encountered in industrial environments, ensuring uninterrupted operation and minimizing downtime.
- Medical Devices: In the healthcare industry, electronic coating materials protect medical devices and equipment from contamination, sterilization processes, and bodily fluids. These coatings provide biocompatibility, chemical resistance, and moisture protection, making them suitable for various medical applications, including implantable devices, diagnostic equipment, and wearable health monitors.
By providing tailored coating solutions for specific industry requirements, electronic coating material manufacturers play a vital role in enabling the widespread adoption of electronic technology across diverse applications, ensuring reliability, performance, and safety in critical systems and devices.
Challenges and Solutions
Electronic coating material manufacturers face various challenges in meeting the electronics industry’s demands while ensuring the reliability and performance of their products. This paragraph explores these challenges and the innovative solutions they employ to address them.
Compatibility and Performance:
One of the primary challenges electronic coating material manufacturers face is ensuring compatibility and performance across a wide range of electronic components and applications. To overcome this challenge, manufacturers invest in research and development to develop versatile coating formulations that offer optimal protection and performance in diverse operating environments.
Environmental Regulations:
Compliance with environmental regulations, such as RoHS (Restriction of Hazardous Substances) and REACH (Registration, Evaluation, Authorization, and Restriction of Chemicals), presents another challenge for electronic coating material manufacturers. To ensure compliance, manufacturers may need to reformulate their coatings to eliminate or reduce the use of hazardous substances while maintaining performance standards.
Process Optimization:
Electronic coating material manufacturers must optimize the coating process for efficiency and consistency. Ensuring uniform coating coverage, precise coating thickness control, and efficient curing processes are essential aspects of electronic coating material manufacturing. Manufacturers may implement automated dispensing systems and quality control measures to streamline the coating process and minimize defects.
Future Trends and Innovations
As electronic devices continue to advance in complexity and functionality, the role of electronic coating material manufacturers becomes increasingly vital in ensuring their reliability and performance. Anticipating future trends and innovations in electronic coatings is essential for manufacturers to stay ahead in the rapidly evolving landscape of electronic manufacturing.
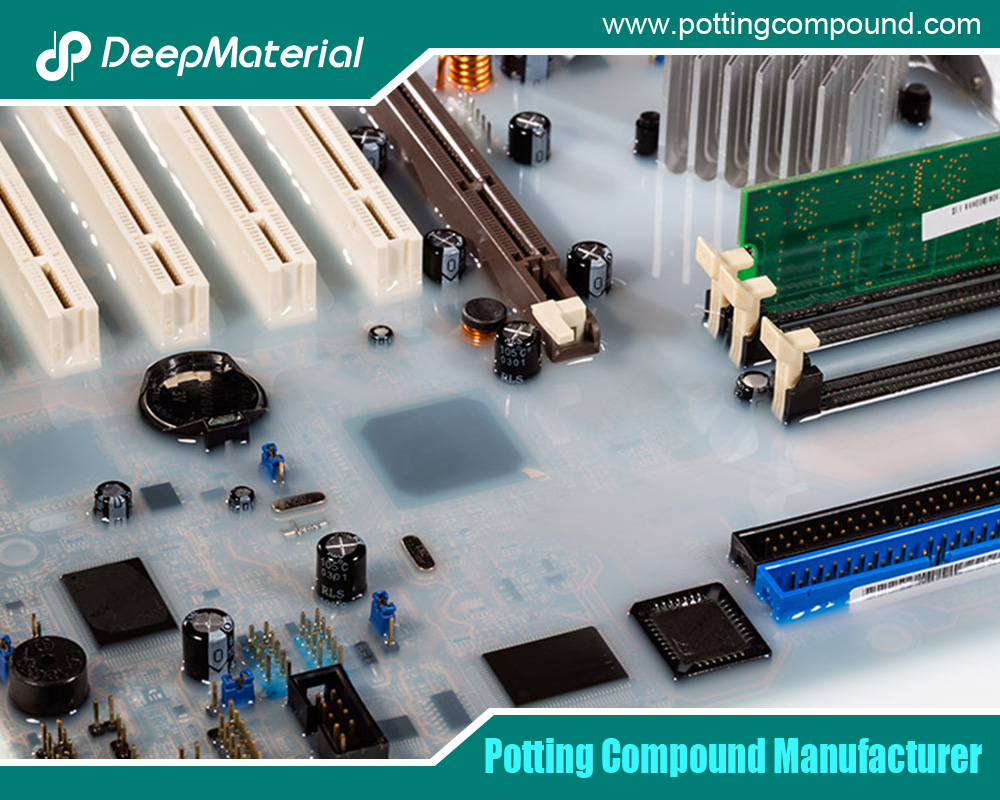
Conclusion
As technology evolves rapidly, the importance of electronic coating materials will only grow. From protecting delicate circuitry to enabling cutting-edge innovations, these materials are the unsung heroes of the electronics industry. With advancements in materials science, manufacturing processes, and collaborative efforts across sectors, the future of electronic coating material manufacturing is brimming with possibilities. As we look ahead, let us embrace the challenges and opportunities driving us toward a future where electronic devices are more intelligent, robust, resilient, and reliable than ever.
For more about innovating the future: exploring electronic coating material manufacturing in electronics industry,you can pay a visit to DeepMaterial at https://www.pottingcompound.com/electronic-conformal-coating/ for more info.
Recent Posts
- Potting Compound for PCB
- In – depth Analysis of the Curing Characteristics of Electronic Potting Compounds
- A Comprehensive Analysis of the Environmental Performance of Encapsulating Materials: From Regulations to Practices
- A Comprehensive Analysis of PCB Encapsulation Quality Inspection: Innovative Application of Non-Destructive Testing Technologies
- Analysis of the Improvement of the Seismic and Impact Resistance Performance of PCB by Encapsulation
- A Comprehensive Guide to Evaluating the Reliability of Encapsulation Materials for Encapsulated PCBs
- In-depth Analysis of the Reparability of Encapsulation Materials
- A Comprehensive Analysis of Post-Potting PCB Issues and the Repair and Rework of Potting Materials
- A Comprehensive Analysis of the Compatibility between Encapsulation Materials and PCBs: Exploration of Chemical Reactions and Their Impact on Performance
- How to Ensure the Compatibility between Encapsulation Materials and Various Components on PCBs