Low-Density Potting Compound
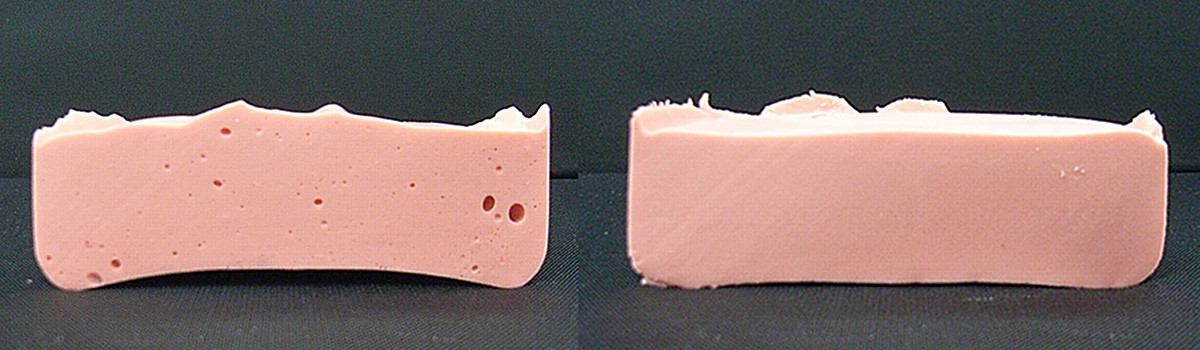
Low density potting compounds play a crucial role in various industries where lightweight, high-performance materials are required for encapsulating and protecting sensitive electronic components. These compounds are formulated to provide excellent thermal conductivity, electrical insulation, and mechanical protection while minimizing weight. As demand for lightweight yet durable materials continues to rise, understanding the features, applications, and benefits of low density potting compounds becomes essential. In this category, we delve into the fundamentals of low density potting compounds through a series of questions and answers.
Table of Contents
ToggleWhat are low density potting compounds?
Low-density potting compounds are materials used in electronics and electrical applications to encapsulate or protect delicate components such as circuit boards, wires, and sensors. These compounds are formulated to have a relatively low density compared to traditional potting materials while still providing effective insulation and protection against environmental factors like moisture, heat, and mechanical stress.
The low density of these compounds offers several advantages in various applications. Firstly, it helps reduce the overall weight of the encapsulated components, making them suitable for applications where weight is a critical factor, such as aerospace and automotive industries. Additionally, low-density potting compounds often have excellent thermal properties, helping to dissipate heat generated by electronic components and preventing overheating, which can degrade performance and reliability.
These compounds typically consist of a resin matrix, such as epoxy or silicone, filled with lightweight materials like hollow glass microspheres or syntactic foam. The incorporation of these lightweight fillers helps reduce the density of the compound while maintaining its structural integrity and insulating properties. Additionally, low-density potting compounds may contain additives such as flame retardants or UV stabilizers to enhance their performance and durability in specific environments.
One significant application of low-density potting compounds is in the manufacture of buoyancy modules for underwater equipment and offshore structures. By encapsulating components with these lightweight materials, manufacturers can ensure that the equipment remains buoyant while providing protection against corrosion and other environmental hazards encountered in marine environments.
low-density potting compounds offer a lightweight, yet durable solution for encapsulating and protecting electronic components in various applications. Their unique combination of low density, thermal insulation, and environmental resistance makes them ideal for use in industries where weight savings and reliability are paramount concerns.
How are low-density potting compounds different from conventional potting compounds?
Low-density and conventional potting compounds serve the same fundamental purpose: encapsulating electronic components to protect them from environmental factors such as moisture, vibration, and thermal shock. However, they differ significantly in their composition, properties, and applications.
Low-density potting compounds are formulated with a lower specific gravity than conventional potting compounds. This characteristic makes them lighter and more suitable for applications where weight is a concern, such as aerospace and automotive electronics. Using lightweight fillers and additives, these compounds achieve reduced density without compromising their protective properties.
Conventional potting compounds, on the other hand, typically have a higher density and are often filled with heavier materials like silica or mineral fillers. While they offer excellent protection and structural support for electronic assemblies, their higher density may be better for weight-sensitive applications.
In terms of composition, low-density potting compounds often utilize advanced resin systems such as epoxies or silicones combined with lightweight fillers like microspheres or hollow glass beads. These fillers help to decrease the overall density while maintaining the necessary mechanical and thermal properties. Additionally, low-density compounds may incorporate additives for specific functionalities such as flame retardancy or thermal conductivity.
Conventional potting compounds, meanwhile, may contain a broader range of fillers and additives tailored to meet various performance requirements, including higher thermal conductivity or more excellent resistance to harsh chemicals.
Regarding application methods, both types of potting compounds can be applied using techniques such as encapsulation, potting, or molding. However, the choice between low-density and conventional potting compounds depends on the specific needs of the electronic assembly. For instance, aerospace applications prioritize weight reduction, making low-density compounds the preferred choice, while industrial applications prioritize durability and mechanical strength, favoring conventional potting compounds.
Low-density potting compounds differ from conventional potting compounds primarily in their lower density, achieved through lightweight fillers and advanced resin systems. While both types provide adequate protection for electronic components, their distinct properties make them suitable for different applications within the electronics industry.
What are the critical properties of low-density potting compounds?
Low-density potting compounds are specialized materials used in electronic and electrical applications to encapsulate and protect sensitive components. These compounds offer several fundamental properties essential for their intended purposes:
- Lightweight: One of the primary characteristics of low-density potting compounds is their lightweight nature. They have a low mass per unit volume, making them suitable for applications where weight is a concern, such as aerospace or automotive electronics.
- Thermal Insulation: Low-density potting compounds possess excellent thermal insulation properties. They can effectively dissipate heat generated by electronic components, preventing overheating and ensuring the reliability and longevity of the device.
- Chemical Resistance: These compounds are often formulated to resist various chemicals, including solvents, oils, and corrosive substances. This resistance helps protect the encapsulated components from environmental factors and chemical exposure, enhancing their durability and reliability.
- Low Dielectric Constant: Low-density potting compounds typically exhibit a low dielectric constant, which is crucial for electrical insulation. This property prevents electrical leakage and ensures the integrity of the encapsulated components, especially in high-voltage applications.
- Shock Absorption: Another essential property of these compounds is their ability to absorb mechanical shocks and vibrations. This feature is particularly beneficial in rugged environments or applications subjected to mechanical stress, as it helps prevent damage to delicate electronic components.
- Ease of Application: Low-density potting compounds are designed for easy application, typically in liquid form that can be poured or injected into the desired area. They cure quickly to form a solid, protective enclosure around the components, simplifying manufacturing.
- Environmental Friendliness: Many formulations of low-density potting compounds are engineered to be environmentally friendly, with low levels of volatile organic compounds (VOCs) and other hazardous substances. This ensures compliance with regulations and minimizes the environmental impact of electronic waste.
Low-density potting compounds offer a combination of lightweight, thermal insulation, chemical resistance, electrical insulation, shock absorption, ease of application, and environmental friendliness, making them ideal for protecting electronic components in various applications.
What are the typical applications of low-density potting compounds?
Low-density potting compounds find application across various industries due to their unique properties and versatility. Here are some typical applications:
- Electronics Encapsulation: Low-density potting compounds encapsulate electronic components such as integrated circuits (ICs), sensors, and circuit boards. These compounds protect delicate electronics from environmental factors like moisture, dust, and vibrations while providing electrical insulation.
- LED Lighting: LED lighting assemblies often use low-density potting compounds to protect LED modules and drivers from heat, moisture, and mechanical stresses. The potting material helps to enhance thermal management, extending the lifespan and reliability of LED lighting systems.
- Solar Panels: Low-density potting compounds are employed in solar panel manufacturing to encapsulate photovoltaic cells and junction boxes. This encapsulation protects the cells from weathering effects, thermal cycling, and mechanical shock, thus maintaining the efficiency and longevity of solar panels.
- Automotive Electronics: Automotive electronics, including control units, sensors, and ignition systems, benefit from low-density potting compounds. These compounds shield sensitive electronic components from extreme temperatures, automotive fluids, and mechanical vibrations, ensuring reliable performance in harsh automotive environments.
- Aerospace Applications: In the aerospace industry, low-density potting compounds are used for encapsulating avionics, navigation systems, and communication equipment. These compounds offer lightweight protection against thermal cycling, altitude changes, and exposure to harsh chemicals encountered in aerospace operations.
- Renewable Energy Systems: Beyond solar panels, low-density potting compounds play a role in other renewable energy systems such as wind turbines and hydroelectric generators. They help protect control electronics and sensors from moisture, temperature fluctuations, and mechanical stresses, ensuring reliable operation in challenging outdoor environments.
- Medical Devices: Certain medical devices utilize low-density potting compounds to protect sensitive electronic components from bodily fluids and sterilization processes. These compounds comply with regulatory standards for biocompatibility and ensure the longevity and reliability of medical equipment.
- Underwater Equipment: Equipment designed for underwater use, such as marine sensors, underwater communication devices, and submersible robotics, often rely on low-density potting compounds for waterproofing and corrosion protection in marine environments.
Low-density potting compounds offer various applications across industries where electronic components’ protection, insulation, and reliability are crucial, making them indispensable in modern technological advancements.
How do low density potting compounds contribute to weight reduction in electronic assemblies?
Low-density potting compounds play a pivotal role in the quest for weight reduction in electronic assemblies, especially in applications where weight is a critical factor such as aerospace, automotive, and portable electronics. These compounds are engineered materials designed to encapsulate and protect electronic components while being lightweight.
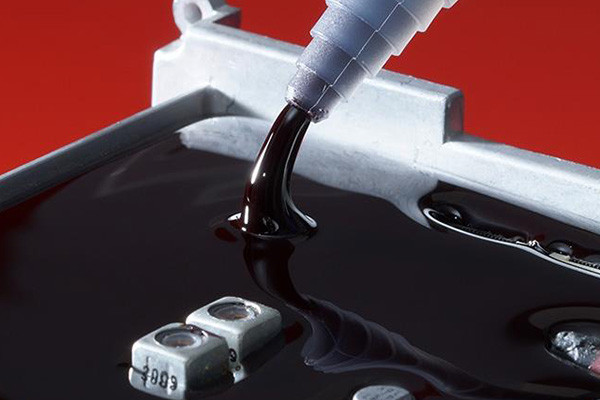
One of the primary mechanisms through which low-density potting compounds contribute to weight reduction is their composition. These compounds are formulated with lightweight materials such as epoxies, silicones, or urethanes, often incorporating hollow microspheres or other additives to decrease density without compromising mechanical or protective properties. By using lighter materials, the overall weight of the potting material itself is reduced compared to traditional encapsulants like metals or high-density plastics.
Moreover, the low-density nature of these compounds allows for a more efficient use of materials. They can be applied in thinner layers while still providing adequate protection to electronic components, thereby further reducing the total weight of the assembly. This thin layer approach is particularly advantageous in weight-sensitive applications where every gram saved contributes to overall performance and efficiency.
Furthermore, the lightweight nature of low-density potting compounds enables the design of sleeker and more compact electronic assemblies. With smaller and lighter potting materials, designers have more flexibility in optimizing the layout and configuration of electronic components, leading to more streamlined and space-efficient designs. This not only reduces weight but also potentially decreases the overall size of the electronic device, making it more portable and easier to integrate into various systems.
Additionally, the use of low-density potting compounds can indirectly contribute to weight reduction by enhancing the reliability and longevity of electronic assemblies. By effectively encapsulating and protecting sensitive components from environmental factors such as moisture, dust, vibration, and thermal fluctuations, these compounds can minimize the need for bulky secondary protective measures or reinforcements, further trimming down the overall weight of the assembly.
In essence, low-density potting compounds offer a multifaceted approach to weight reduction in electronic assemblies by leveraging lightweight materials, enabling thinner applications, facilitating compact designs, and enhancing overall reliability, thereby addressing the demand for lighter, more efficient, and more agile electronic devices in a variety of industries.
What factors should be considered when selecting a low-density potting compound?
Selecting a low-density potting compound involves considering several critical factors to ensure optimal performance and compatibility with the intended application:
- Density: The primary consideration is the density of the potting compound. Low-density compounds are typically lighter, making them suitable for applications where weight is a concern. This factor impacts transportation costs, ease of handling, and overall system weight.
- Thermal Properties: Evaluate the compound’s thermal conductivity and coefficient of thermal expansion (CTE). Low-density potting compounds with good thermal insulation properties help protect electronic components from heat damage while minimizing stress on the encapsulated parts due to thermal cycling.
- Mechanical Strength: Despite the low density, the potting compound should provide adequate mechanical strength to support and protect encapsulated components from mechanical shock, vibration, and environmental stresses. Conduct thorough testing to ensure the compound meets the required mechanical specifications.
- Chemical Compatibility: Consider the compatibility of the potting compound with the materials it will come into contact with, including substrates, components, and any environmental factors such as moisture, chemicals, or solvents. Compatibility ensures long-term reliability and prevents degradation or corrosion of encapsulated parts.
- Electrical Insulation Properties: Ensure the potting compound provides sufficient electrical insulation to protect sensitive electronic components from short circuits and electrical interference. Low-density compounds should maintain dielectric strength and resistivity to prevent electrical leakage.
- Curing Process: Evaluate the curing process of the potting compound, including curing time, temperature requirements, and any special equipment needed. Opt for compounds with a curing process that aligns with manufacturing timelines and capabilities.
- Environmental Considerations: Assess ecological factors such as operating temperature range, humidity, and exposure to UV radiation or harsh outdoor conditions. Choose a potting compound that can withstand the intended ecological conditions without degradation or loss of performance.
- Regulatory Compliance: Ensure the selected potting compound complies with relevant industry standards, regulations, and certifications, such as RoHS (Restriction of Hazardous Substances) and REACH (Registration, Evaluation, Authorization, and Restriction of Chemicals), to guarantee safety and environmental responsibility.
By considering these factors comprehensively, manufacturers can select a suitable low-density potting compound that meets the specific requirements of their application while ensuring reliability, performance, and longevity.
Can low-density potting compounds provide adequate protection against environmental factors?
Low-density potting compounds offer adequate protection against environmental factors in specific applications. Potting compounds, or encapsulants, are materials used to encapsulate electronic components, protecting them from environmental stresses such as moisture, dust, chemicals, and physical shock. While traditional potting compounds tend to be denser, low-density alternatives have gained popularity due to their unique properties and advantages.
One primary advantage of low-density potting compounds is their ability to protect without adding excessive weight or bulk to the electronic assembly. This characteristic is particularly beneficial in aerospace, automotive, and other weight-sensitive applications where every gram matters. By using low-density materials, manufacturers can achieve the desired level of protection without compromising the system’s overall weight and performance.
Additionally, low-density potting compounds often exhibit excellent thermal conductivity properties. This feature is crucial for dissipating heat generated by electronic components, thereby preventing overheating and ensuring optimal performance and reliability. Effective thermal management helps prolong the lifespan of electronic devices and reduces the risk of premature failure, especially in demanding operating conditions.
Furthermore, low-density potting compounds can resist environmental factors such as moisture, humidity, and chemical exposure. Many formulations are specifically engineered to provide robust protection against corrosive substances and harsh environments, making them suitable for various applications, including outdoor and industrial settings.
Despite these advantages, it’s essential to select the appropriate low-density potting compound based on the application’s specific requirements. Factors such as curing time, flexibility, adhesion properties, and compatibility with other materials must be carefully considered to ensure optimal performance and reliability. Additionally, proper application techniques and thorough quality control measures are essential to maximize the effectiveness of the potting process and achieve consistent results.
Low-density potting compounds can offer adequate protection against environmental factors in various applications thanks to their lightweight nature, excellent thermal conductivity, and resistance to moisture and chemicals. By choosing suitable materials and employing proper application techniques, manufacturers can ensure the reliability and longevity of electronic assemblies in challenging operating environments.
How do low density potting compounds enhance thermal management in electronic devices?
Low-density potting compounds play a crucial role in enhancing thermal management in electronic devices by effectively dissipating heat and maintaining the optimal operating temperatures of components. These compounds, typically composed of polymers or resins, are engineered with specific properties to facilitate heat transfer while providing protection and stability to electronic assemblies.
One key advantage of low-density potting compounds is their ability to efficiently conduct heat away from sensitive electronic components. Unlike traditional high-density potting materials, which can act as insulators and trap heat within the device, low-density compounds have a higher porosity and lower thermal resistance. This allows heat to dissipate more readily through the material, preventing hot spots and thermal buildup that can degrade performance and reliability.
Additionally, the lightweight nature of these compounds reduces the overall weight of the electronic device, which is especially important in applications where weight constraints are a concern, such as aerospace or automotive electronics. By minimizing weight, low-density potting compounds contribute to improved portability and energy efficiency of electronic systems.
Moreover, low-density potting compounds often exhibit excellent adhesion properties, ensuring reliable encapsulation and protection of electronic components from environmental factors such as moisture, dust, and mechanical stress. This encapsulation not only safeguards the components but also enhances heat transfer by eliminating air gaps that can impede thermal conductivity.
Furthermore, these compounds can be formulated with additives such as thermally conductive fillers or phase change materials to further enhance their thermal management capabilities. Thermally conductive fillers, such as ceramic particles or metallic flakes, help improve the overall thermal conductivity of the compound, while phase change materials absorb and release heat during phase transitions, effectively regulating temperatures within the device.
low-density potting compounds offer a multifaceted approach to thermal management in electronic devices by promoting efficient heat dissipation, reducing weight, providing robust protection, and incorporating specialized additives to optimize thermal performance. Their use is essential in modern electronic design to ensure reliability, longevity, and optimal functionality of electronic systems in diverse applications.
Can low-density potting compounds provide adequate protection against environmental factors?
Low-density potting compounds offer adequate protection against environmental factors in specific applications. Potting compounds, or encapsulants, are materials used to encapsulate electronic components, protecting them from environmental stresses such as moisture, dust, chemicals, and physical shock. While traditional potting compounds tend to be denser, low-density alternatives have gained popularity due to their unique properties and advantages.
One primary advantage of low-density potting compounds is their ability to protect without adding excessive weight or bulk to the electronic assembly. This characteristic is particularly beneficial in aerospace, automotive, and other weight-sensitive applications where every gram matters. By using low-density materials, manufacturers can achieve the desired level of protection without compromising the system’s overall weight and performance.
Additionally, low-density potting compounds often exhibit excellent thermal conductivity properties. This feature is crucial for dissipating heat generated by electronic components, thereby preventing overheating and ensuring optimal performance and reliability. Effective thermal management helps prolong the lifespan of electronic devices and reduces the risk of premature failure, especially in demanding operating conditions.
Furthermore, low-density potting compounds can resist environmental factors such as moisture, humidity, and chemical exposure. Many formulations are specifically engineered to provide robust protection against corrosive substances and harsh environments, making them suitable for various applications, including outdoor and industrial settings.
Despite these advantages, it’s essential to select the appropriate low-density potting compound based on the application’s specific requirements. Factors such as curing time, flexibility, adhesion properties, and compatibility with other materials must be carefully considered to ensure optimal performance and reliability. Additionally, proper application techniques and thorough quality control measures are essential to maximize the effectiveness of the potting process and achieve consistent results.
Low-density potting compounds can offer adequate protection against environmental factors in various applications thanks to their lightweight nature, excellent thermal conductivity, and resistance to moisture and chemicals. By choosing suitable materials and employing proper application techniques, manufacturers can ensure the reliability and longevity of electronic assemblies in challenging operating environments.
Are low density potting compounds compatible with different types of electronic components?
Low-density potting compounds are often used in electronic applications where weight and thermal management are crucial considerations. These compounds typically have a lower density compared to traditional potting materials like epoxy resins, silicone, or polyurethanes. The lower density offers advantages such as reduced weight and improved thermal conductivity, making them compatible with various electronic components.
One key factor in compatibility is the ability of the potting compound to provide adequate protection while not causing any harm to the electronic components. Low-density potting compounds are formulated to be non-corrosive and non-conductive, ensuring they do not damage sensitive electronic parts. Additionally, these compounds often have excellent adhesion properties, ensuring they form a secure bond with different types of components and substrates.
Compatibility extends beyond just physical properties to encompass thermal management. Many electronic components generate heat during operation, and effective thermal dissipation is essential for their performance and longevity. Low-density potting compounds can offer superior thermal conductivity compared to traditional potting materials, helping to dissipate heat more efficiently and keeping electronic components within safe operating temperatures.
Furthermore, low-density potting compounds are often engineered to be chemically inert, meaning they are resistant to a wide range of chemicals and environmental factors. This resistance ensures the long-term stability and reliability of the encapsulated electronic assembly, even in harsh operating conditions.
Another aspect of compatibility is ease of application. Low-density potting compounds are typically formulated to be pourable or injectable, allowing for easy application and encapsulation of various types of electronic components, including intricate assemblies with delicate parts.
In summary, low-density potting compounds offer compatibility with different types of electronic components by providing adequate protection, thermal management, chemical resistance, and ease of application. Their versatility makes them suitable for a wide range of electronic applications, from consumer electronics to industrial equipment and automotive electronics.
Can low-density potting compounds provide adequate protection against environmental factors?
Low-density potting compounds offer adequate protection against environmental factors in specific applications. Potting compounds, or encapsulants, are materials used to encapsulate electronic components, protecting them from environmental stresses such as moisture, dust, chemicals, and physical shock. While traditional potting compounds tend to be denser, low-density alternatives have gained popularity due to their unique properties and advantages.
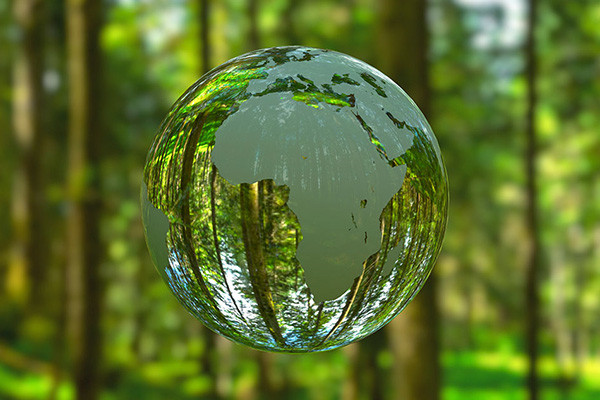
One primary advantage of low-density potting compounds is their ability to protect without adding excessive weight or bulk to the electronic assembly. This characteristic is particularly beneficial in aerospace, automotive, and other weight-sensitive applications where every gram matters. By using low-density materials, manufacturers can achieve the desired level of protection without compromising the system’s overall weight and performance.
Additionally, low-density potting compounds often exhibit excellent thermal conductivity properties. This feature is crucial for dissipating heat generated by electronic components, thereby preventing overheating and ensuring optimal performance and reliability. Effective thermal management helps prolong the lifespan of electronic devices and reduces the risk of premature failure, especially in demanding operating conditions.
Furthermore, low-density potting compounds can resist environmental factors such as moisture, humidity, and chemical exposure. Many formulations are specifically engineered to provide robust protection against corrosive substances and harsh environments, making them suitable for various applications, including outdoor and industrial settings.
Despite these advantages, it’s essential to select the appropriate low-density potting compound based on the application’s specific requirements. Factors such as curing time, flexibility, adhesion properties, and compatibility with other materials must be carefully considered to ensure optimal performance and reliability. Additionally, proper application techniques and thorough quality control measures are essential to maximize the effectiveness of the potting process and achieve consistent results.
Low-density potting compounds can offer adequate protection against environmental factors in various applications thanks to their lightweight nature, excellent thermal conductivity, and resistance to moisture and chemicals. By choosing suitable materials and employing proper application techniques, manufacturers can ensure the reliability and longevity of electronic assemblies in challenging operating environments.
What are the curing mechanisms for low-density potting compounds?
Low-density potting compounds are commonly used in electronic applications where weight and thermal conductivity are significant concerns. These compounds encapsulate and protect delicate electronic components from environmental factors such as moisture, dust, and vibration. Several curing mechanisms can be employed in low-density potting compounds to ensure proper solidification and performance:
- Thermal Curing: Thermal curing is one of the most widely used mechanisms for low-density potting compounds. In this process, the compound undergoes polymerization when subjected to elevated temperatures. Typically, a catalyst or initiator is added to the compound to accelerate the reaction. As the temperature increases, chemical bonds form between the polymer chains, leading to cross-linking and forming a solid structure.
- UV Curing: UV curing involves using ultraviolet (UV) light to initiate polymerization. The potting compound contains photoinitiators that undergo a photochemical reaction upon UV light exposure, leading to forming radicals or other reactive species. These species then initiate the polymerization process, resulting in the solidification of the compound. UV curing offers rapid curing times and precise control over the curing process.
- Moisture Curing: Moisture curing relies on atmospheric moisture to initiate the curing process. The potting compound contains moisture-sensitive functional groups, such as silanes or urethanes, which react with water vapor in the air. This reaction triggers the cross-linking of polymer chains and ultimately leads to the solidification of the compound. Moisture curing is advantageous for applications where heat or UV light may not be readily available.
- Chemical Curing: Chemical curing involves using reactive chemical agents, such as amines or peroxides, to initiate polymerization. These agents react with functional groups present in the potting compound, forming cross-links and a solid network structure. Chemical curing can be tailored to specific application requirements by adjusting the type and concentration of curing agents.
These curing mechanisms offer distinct advantages and may be selected based on factors such as curing time, environmental conditions, and performance requirements. By understanding the properties of each mechanism, manufacturers can optimize the curing process to achieve desired outcomes in low-density potting compound applications.
How do manufacturers achieve low density without sacrificing performance?
Manufacturers achieve low density without sacrificing performance through material selection, design optimization, and advanced manufacturing techniques.
Firstly, they carefully select materials with properties that allow for lightweight construction without compromising strength or performance. Advanced composite materials, such as carbon fiber reinforced polymers (CFRP) or advanced alloys like aluminum-lithium, offer high strength-to-weight ratios, making them ideal for reducing density while maintaining structural integrity.
Secondly, manufacturers employ design optimization techniques to minimize material usage while meeting performance requirements. This involves sophisticated computer-aided design (CAD) software and finite element analysis (FEA) tools to refine the design iteratively for maximum efficiency. Manufacturers can reduce weight by strategically placing materials and optimizing structural shapes without sacrificing performance.
Additionally, advanced manufacturing techniques enable the production of complex lightweight structures with precision and consistency. Processes such as additive manufacturing (3D printing) allow for creating intricate geometries that would be impossible or prohibitively expensive to produce using traditional methods. This reduces weight and enables customization and optimization of components for specific applications.
Furthermore, manufacturers may incorporate innovative technologies such as sandwich structures, honeycomb cores, or lattice structures to reduce weight further while maintaining strength. These structures distribute loads efficiently, improving overall performance without adding unnecessary mass.
Moreover, rigorous testing and validation procedures ensure that lightweight components meet stringent performance standards and safety requirements. These procedures include structural testing, fatigue testing, and simulation-based analysis to verify performance under various operating conditions.
Achieving low density without sacrificing performance requires a holistic approach integrating material science, design optimization, advanced manufacturing techniques, and rigorous testing. By leveraging these strategies, manufacturers can develop lightweight solutions that offer exceptional performance across various applications.
Can low-density potting compounds be customized for specific applications?
Low-density potting compounds can be customized for specific applications, offering a versatile solution across various industries. Potting compounds are typically used to encapsulate electronic components to protect them from environmental factors such as moisture, vibration, and thermal cycling. Low-density potting compounds offer the added benefit of reduced weight while still providing excellent protection and insulation. Here’s how these compounds can be tailored to meet specific application requirements:
- Material Composition: Low-density potting compounds can be formulated using base materials such as epoxy, silicone, polyurethane, or acrylic resins. The choice of material depends on factors like desired flexibility, temperature resistance, chemical resistance, and adhesion properties. For example, silicone-based compounds offer excellent flexibility and high-temperature resistance, making them suitable for applications subjected to extreme conditions.
- Fillers and Additives: Fillers and additives can be incorporated into the potting compound formulation to enhance specific properties. For instance, adding glass or ceramic microspheres can reduce density without compromising mechanical strength. Other additives like flame retardants, UV stabilizers, or conductive fillers can be included based on the application’s requirements.
- Curing Profiles: The curing profile of the potting compound can be adjusted to suit the manufacturing process and application needs. This includes variations in curing time, temperature, and curing method (heat cure, room temperature cure, or UV cure). Customizing the curing profile ensures optimal performance and compatibility with different substrates and components.
- Physical Properties: The physical properties of low-density potting compounds, such as hardness, elongation, and tensile strength, can be tailored to meet specific application requirements. This customization ensures the encapsulated components are adequately protected while maintaining desired mechanical properties.
- Environmental Compatibility: Depending on the application environment, potting compounds can be customized to withstand exposure to harsh chemicals, extreme temperatures, or outdoor conditions. Specialized formulations can be developed for aerospace, automotive, marine, or electronics applications, ensuring long-term reliability and performance.
The customization of low-density potting compounds allows for precise tailoring to meet the unique demands of various applications, providing adequate protection and insulation for sensitive electronic components while minimizing weight and maximizing performance.
What are the challenges associated with using low-density potting compounds?
Low-density potting compounds offer several advantages, such as weight reduction, improved thermal conductivity, and cost-effectiveness. However, they also pose specific challenges that must be considered:
- Mechanical Strength: Low-density potting compounds often lack the mechanical strength to withstand harsh environmental conditions, such as vibration, shock, or high-pressure scenarios. This weakness can lead to physical damage or premature failure of the encapsulated component.
- Chemical Resistance: Some low-density materials may have limited resistance to chemicals or solvents present in the operating environment. Exposure to these substances can degrade the potting compound, compromising its integrity and potentially affecting the encapsulated components.
- Moisture Ingress: The reduced density of potting compounds may also increase susceptibility to moisture ingress. Moisture infiltration can lead to corrosion, electrical shorts, and other reliability issues, particularly in outdoor or high-humidity environments.
- Thermal Management: Low-density materials often exhibit improved thermal conductivity compared to traditional potting compounds; they may still face challenges in efficiently dissipating heat, especially in high-power applications. Inadequate thermal management can lead to overheating, performance degradation, or even catastrophic failure of the encapsulated electronics.
- Adhesion and Encapsulation: Achieving proper adhesion and complete encapsulation with low-density materials can be challenging. Poor adhesion may result in delamination or voids within the potting layer, compromising its protective function and leaving the components vulnerable to environmental factors.
- Processing and Handling: Low-density potting compounds may have different processing requirements than higher-density alternatives. Specialized equipment or techniques may be necessary for mixing, dispensing, and curing these materials effectively, adding complexity to manufacturing processes.
- Cost Considerations: Low-density potting compounds offer benefits such as reduced material usage and transportation costs, but they may also be more expensive on a per-unit basis than conventional options. Balancing the performance advantages with the associated costs is essential when selecting a potting compound for a particular application.
Addressing these challenges often requires careful material selection, process optimization, and thorough testing to ensure the reliability and performance of encapsulated electronic devices in real-world conditions.
How do low-density potting compounds contribute to overall system reliability?
Low-density potting compounds enhance overall system reliability through several vital mechanisms. Potting compounds are materials used to encapsulate electronic components within a protective casing. Low-density variants of these compounds offer specific advantages that contribute significantly to the reliability of electronic systems.
Firstly, low-density potting compounds provide excellent protection against environmental factors such as moisture, dust, and chemicals. By encapsulating delicate electronic components, they create a barrier that shields them from potential damage, thereby prolonging their lifespan and ensuring consistent performance even in harsh operating conditions. This protection is vital in applications where electronics are exposed to extreme temperatures, humidity, or corrosive substances.
Secondly, the lightweight nature of low-density potting compounds minimizes the overall weight of electronic assemblies. This is especially beneficial in aerospace, automotive, and other weight-sensitive applications where reducing mass is critical for efficiency and performance. By utilizing low-density materials, manufacturers can achieve weight savings without compromising the protective properties of the potting compound, thus improving the system’s reliability without sacrificing functionality.
Moreover, low-density potting compounds offer excellent thermal conductivity, dissipating heat generated by electronic components more efficiently. Effective heat dissipation is essential for preventing overheating, which can lead to premature component failure and degraded performance. By maintaining optimal operating temperatures, low-density potting compounds contribute to the reliability and longevity of electronic systems, ensuring consistent performance over extended periods.
Additionally, the flexibility and resilience of low-density potting compounds provide mechanical shock and vibration resistance, safeguarding delicate electronic components against damage caused by external impacts or movement. This is particularly crucial in applications subject to rough handling or dynamic environments, where robust protection is necessary to maintain system reliability.
Low-density potting compounds enhance overall system reliability by providing superior protection against environmental factors, reducing weight without compromising performance, improving thermal management, and offering mechanical resilience. By effectively safeguarding electronic components, these materials contribute to the longevity and consistent operation of electronic systems in various applications.
Are there any regulatory considerations when using low-density potting compounds?
Several regulatory considerations must be considered to ensure compliance with safety, environmental, and industry standards when utilizing low-density potting compounds. Here are some key points to consider:
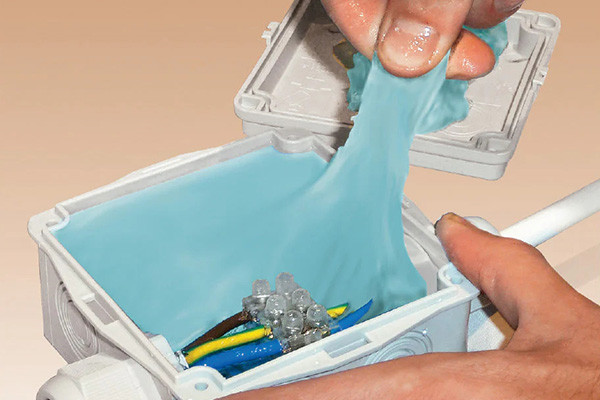
- Material Safety Data Sheets (MSDS): Before using any potting compound, the manufacturer must review the MSDS provided. This document outlines potential hazards associated with the compound, safety precautions for handling, and proper disposal methods.
- Regulatory Compliance: Low-density potting compounds may be subject to various regulations depending on their composition and intended use. These regulations can include environmental regulations such as REACH (Registration, Evaluation, Authorization and Restriction of Chemicals) in the European Union or Toxic Substances Control Act (TSCA) in the United States, as well as industry-specific standards like IPC (Association Connecting Electronics Industries) standards for electronic assemblies.
- Volatile Organic Compounds (VOCs): Some potting compounds may contain VOCs, adversely affecting human health and the environment. Regulatory bodies may limit VOC emissions, requiring manufacturers to comply with specific VOC content regulations or implement measures to reduce emissions during application and curing.
- Hazardous Substances: Certain chemicals used in potting compounds may be classified as dangerous substances or pollutants. Regulatory authorities such as the Environmental Protection Agency (EPA) in the U.S. or the European Chemicals Agency (ECHA) in the EU may regulate these substances’ use, handling, and disposal to minimize environmental and health risks.
- Waste Disposal: Proper disposal of unused potting compounds and any waste generated during application or manufacturing processes is crucial to prevent environmental contamination. Compliance with regulations governing hazardous waste disposal, recycling, or treatment methods is essential to avoid legal penalties and mitigate ecological impact.
- Labeling and Documentation: Manufacturers and users of potting compounds must ensure proper labeling of containers, providing clear information about the product’s composition, hazards, handling instructions, and safety precautions. Accurate record-keeping of usage, storage, and disposal activities is also necessary for regulatory compliance and accountability.
When using low-density potting compounds, adherence to regulatory requirements regarding safety, environmental protection, and product stewardship is paramount. By staying informed about applicable regulations, implementing appropriate safety measures, and following best practices for handling and disposal, businesses can mitigate risks and ensure compliance throughout the product life cycle.
What are the environmental impacts of low-density potting compounds?
Low-density potting compounds, often used in electronics and other industries to encapsulate and protect components, can have both positive and negative environmental impacts.
On the positive side, low-density potting compounds typically require less encapsulation material than higher-density alternatives. This means less raw material is consumed during production, reducing natural resource extraction and lowering energy consumption during manufacturing processes. Additionally, lighter-weight compounds may contribute to reduced transportation emissions since less fuel is required for shipping.
However, there are also negative environmental impacts associated with low-density potting compounds. One significant concern is the composition of these materials. Many potting compounds contain synthetic polymers like epoxy resins, polyurethanes, and silicones. Producing these polymers often involves the use of fossil fuels and the release of greenhouse gases. Additionally, some compounds may contain additives or fillers that can harm the environment, such as heavy metals or persistent organic pollutants.
Another issue is disposing of potting compounds at the end of their lifecycle. While these materials are designed to provide long-term protection for electronic components, they may eventually need to be removed or replaced as equipment becomes obsolete or undergo maintenance. Disposal methods for potting compounds vary, but landfilling is expected, which can release potentially harmful chemicals into the environment over time as the compounds degrade.
Furthermore, potting compounds are not correctly managed during manufacturing processes. In that case, there is a risk of emissions of volatile organic compounds (VOCs) or other hazardous substances into the air or water, contributing to air and water pollution.
While low-density potting compounds offer some environmental benefits compared to higher-density alternatives, such as reduced material usage and transportation emissions, they also pose ecological challenges due to their composition and potential impacts during production, use, and disposal. Efforts to minimize the environmental materials’ ecological footprint, improving recycling and disposal methods, and exploring alternative materials with lower environmental impact.
How do low-density potting compounds compare in terms of cost-effectiveness?
Low-density potting compounds offer several advantages in terms of cost-effectiveness compared to higher-density alternatives. These compounds are typically formulated with lightweight fillers such as glass bubbles or hollow microspheres, reducing weight per volume while providing adequate insulation and protection for electronic components.
One significant advantage is the reduction in material usage. Due to their lower density, these compounds require less material to fill a given volume, resulting in lower material costs per unit. This can be particularly beneficial in large-scale manufacturing, where even slight reductions in material usage can translate to substantial cost savings over time.
Additionally, the lightweight nature of low-density potting compounds can lead to savings in transportation and handling costs. Lighter materials require less transportation energy and are often cheaper to ship, especially when considering international logistics. Furthermore, handling lighter materials is generally more straightforward and may require less specialized equipment, reducing associated labor costs.
Moreover, low-density potting compounds can offer cost savings through improved efficiency in manufacturing processes. Their lower viscosity compared to higher-density compounds allows for more effortless pouring and dispensing, reducing the time and labor required for application. This can result in higher throughput and lower production costs.
Furthermore, the reduced weight of electronic assemblies potted with low-density compounds can save downstream costs. Lighter products may require less robust packaging materials, leading to savings in packaging costs and potentially reduced shipping expenses for customers.
However, it’s essential to consider the specific application requirements when evaluating the cost-effectiveness of low-density potting compounds. While they offer advantages in material usage, transportation, handling, and manufacturing efficiency, their suitability for a particular application depends on factors such as thermal conductivity, mechanical strength, and environmental resistance. Balancing these factors ensures that the chosen potting compound protects electronic components while optimizing cost-effectiveness.
Can low-density potting compounds be used in high-voltage applications?
While low-density potting compounds offer advantages such as reduced weight and improved thermal conductivity, they may only sometimes be suitable for high-voltage applications. High-voltage environments present unique challenges that must be carefully considered when selecting potting materials.
One primary concern with low-density potting compounds in high-voltage applications is their ability to provide adequate insulation. In high-voltage scenarios, the risk of electrical breakdown is heightened, necessitating robust insulation properties to prevent arcing or short circuits. Low-density compounds may have lower dielectric strength than denser alternatives, potentially compromising their ability to withstand high voltages without breakdown.
Additionally, the mechanical strength of potting compounds becomes critical in high-voltage environments. Low-density materials may offer less structural integrity, increasing the risk of cracking or damage under the mechanical stresses associated with high-voltage equipment. This could lead to insulation failure or compromised safety.
Furthermore, the thermal properties of potting compounds are crucial in high-voltage applications where temperature fluctuations can occur. While low-density compounds often boast enhanced thermal conductivity, they may also have lower thermal stability compared to denser materials. Maintaining stable operating temperatures in high-voltage equipment is essential to prevent thermal runaway and ensure reliable performance.
However, with proper consideration and design precautions, low-density potting compounds can be used in high-voltage applications. For instance, low-density materials may offer viable solutions in applications where weight reduction is critical or where moderate voltages are involved. Additionally, incorporating additives or reinforcements into low-density formulations can enhance their electrical and mechanical properties, making them more suitable for high-voltage environments.
While low-density potting compounds offer certain benefits, their use in high-voltage applications requires careful assessment of their insulation, mechanical strength, and thermal properties. Engineers must weigh these factors against the application’s specific requirements and operating conditions to determine the suitability of low-density materials or opt for denser alternatives better suited to high-voltage environments.
Are there any advancements or innovations in the field of low-density potting compounds?
In recent years, advancements in low-density potting compounds have primarily focused on enhancing performance, sustainability, and ease of use. One notable innovation involves the development of novel formulations that maintain structural integrity while offering reduced density. These compounds typically leverage advanced polymer chemistries and additives to achieve the desired properties.
One significant advancement is the introduction of lightweight fillers, such as hollow microspheres or syntactic foams, into potting compound formulations. These fillers effectively displace traditional heavier materials, resulting in a lower overall density without compromising mechanical strength or thermal stability. Manufacturers have optimized the distribution and concentration of these fillers to ensure uniformity and consistent performance across varied applications.
Furthermore, researchers are exploring bio-based and sustainable alternatives to conventional potting compounds derived from petrochemicals. These eco-friendly formulations utilize renewable resources such as plant-derived resins or biodegradable polymers. These innovations align with the growing demand for sustainable materials in various industries by reducing reliance on fossil fuels and minimizing environmental impact.
Advancements in processing techniques have also facilitated the use of low-density potting compounds in complex applications. Improved viscosity control and curing profiles enable precise dispensing and rapid curing, enhancing production efficiency and reducing manufacturing costs. Additionally, compatibility testing and predictive modeling developments assist engineers in selecting the most suitable potting compounds for specific applications, optimizing performance and reliability.
Recent innovations in low-density potting compounds have focused on enhancing performance, sustainability, and processability. By incorporating lightweight fillers, exploring bio-based alternatives, and improving processing techniques, researchers and manufacturers continue to push the boundaries of what is achievable in this critical area of materials science. These advancements address current challenges and pave the way for future developments in electronics, automotive, aerospace, and other industries.
How can companies integrate low-density potting compounds into their manufacturing processes effectively?
Integrating low-density potting compounds into manufacturing processes effectively requires careful planning, consideration of material properties, and adherence to best practices. Here’s a brief guide:
- Material Selection: Select a low-density potting compound suitable for your application. Consider thermal conductivity, electrical insulation properties, and environmental resistance. Ensure compatibility with the materials being potted and any regulatory requirements.
- Process Optimization: Evaluate your existing manufacturing processes to identify potential integration points for the potting compound. This may involve modifying existing equipment or developing new procedures to accommodate the unique characteristics of low-density materials.
- Dispensing Equipment: Invest in dispensing equipment capable of accurately metering and mixing the potting compound. Choose equipment suitable for low-density materials to prevent air entrapment or uneven distribution.
- Surface Preparation: Proper surface preparation ensures adhesion and prevents contamination. Clean and dry surfaces thoroughly before applying the potting compound to promote optimal bonding.
- Curing Conditions: Follow manufacturer recommendations for curing conditions such as temperature and humidity to achieve the desired physical properties. Ensure adequate ventilation to prevent the buildup of harmful fumes during curing.
- Quality Control: Implement rigorous quality control measures throughout manufacturing to identify and address defects or inconsistencies. This may include visual inspections, dimensional checks, and performance testing.
- Worker Training: Provide comprehensive training to employees handling and applying the potting compound. Emphasize safety protocols, proper handling techniques, and troubleshooting procedures to minimize errors and ensure product quality.
- Documentation and Traceability: Maintain detailed documentation of materials, processes, and equipment settings to facilitate traceability and troubleshooting. This information can also aid in process optimization and continuous improvement efforts.
- Environmental Considerations: Consider the environmental impact of the potting compound throughout its lifecycle, from manufacturing to disposal. Choose materials with minimal environmental footprint and explore opportunities for recycling or reuse.
- Feedback and Iteration: Solicit stakeholder input and monitor performance metrics to identify areas for improvement. Continuously iterate on your processes to enhance efficiency, quality, and sustainability over time.
Following these guidelines, companies can effectively integrate low-density potting compounds into their manufacturing processes, producing high-quality products with optimized performance characteristics.
Conclusion:
In conclusion, low-density potting compounds offer a lightweight yet robust solution for encapsulating and protecting electronic components across various industries. With their unique properties and versatile applications, these compounds continue to drive innovation in electronics manufacturing. By understanding their characteristics, benefits, and challenges, businesses can make informed decisions regarding selecting and implementing low-density potting compounds in their products and processes. As technology evolves, so will the capabilities and offerings of low-density potting compounds, shaping the future of electronics manufacturing towards lighter, more efficient solutions.
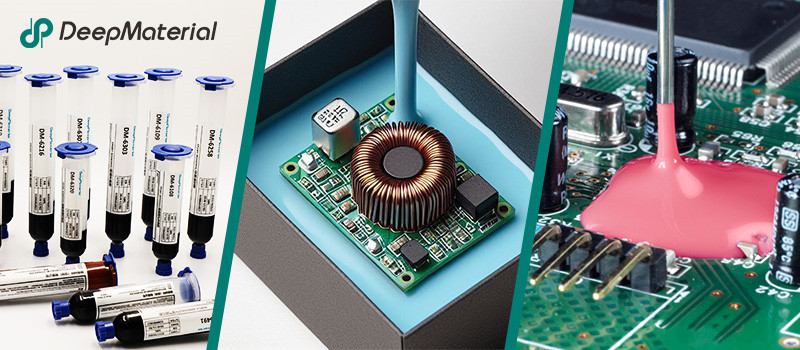
About DeepMaterial
DeepMaterial is a trusted supplier of encapsulant materials that are used in electronics manufacturing worldwide. From chip on board encapsulants such as glob top material to conformal coatings, underfills, low pressure molding, and potting solutions, DeepMaterial offers a full range of circuit board protection materials that effectively protect circuit boards while help reduce costs. More…Deepmaterial is a the manufacturer of epoxy adhesives including hardeners, metalbond, and metal filled resins. Structural, toughened medium viscosity, and non-sag adhesives are also offered. Some adhesives are resistant to thermal shock, chemical, vibration dampening, and impact. Suitable for metals, plastics, wood, and ceramics. Serves electronics, aerospace, automotive, tooling, marine, and construction industries. REACH and RoHS compliant. FDA approved. UL listed. Meets military specifications. We are the one of best adhesive manufacturers in China.
Blogs & News
Potting compounds are at the frontline of electronics assembly, delivering effective protection in challenging environmental conditions while improving mechanical strength and offering high electric insulation. Used within a variety of industries, electrical potting compounds are found within a broad range of consumer electronics, as well as used in applications across the automotive, aerospace, and other industries where electronic assemblies are prevalent.
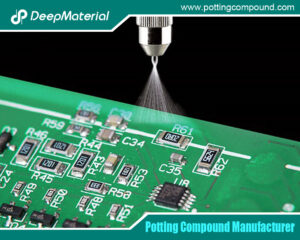
The Ultimate Guide to Electrical Potting Compound and Market Application
The Ultimate Guide to Electrical Potting Compound and Market Application In the modern world of electronics, where devices are increasingly compact and exposed to harsh
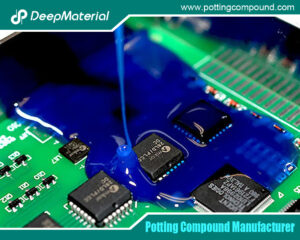
The Top Polyurethane Potting Compound
The Top Polyurethane Potting Compound In the fast-evolving world of electronics and industrial manufacturing, protecting sensitive components from environmental hazards is critical to ensuring reliability
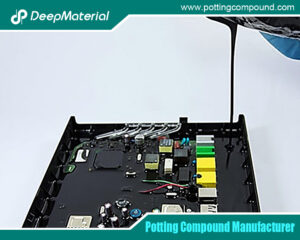
Advanced Epoxy Potting Compound for Superior Electronic Protection
Advanced Epoxy Potting Compound for Superior Electronic Protection In the realm of electronics and industrial manufacturing, protecting sensitive components from environmental hazards is critical to
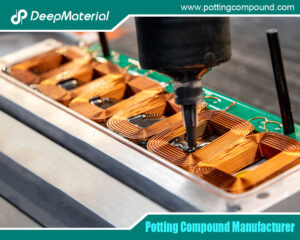
Waterproof Potting Compound: A Comprehensive Guide
Waterproof Potting Compound: A Comprehensive Guide In today’s technology-driven world, protecting sensitive electronic components from environmental hazards is paramount. One of the most effective solutions
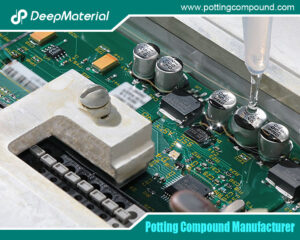
Silicone Potting Compound for Electronics
Silicone Potting Compound for Electronics In the rapidly evolving world of electronics, ensuring the reliability, durability, and performance of electronic components is paramount. One critical
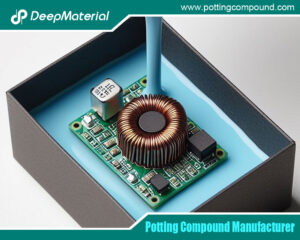
Potting Compound vs. Epoxy: A Comprehensive Comparison
Potting Compound vs. Epoxy: A Comprehensive Comparison In the world of electronics, manufacturing, and material encapsulation, two terms frequently come up: potting compounds and epoxy.