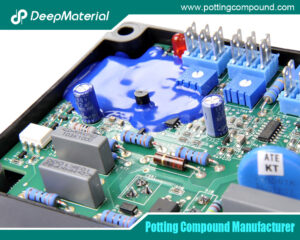
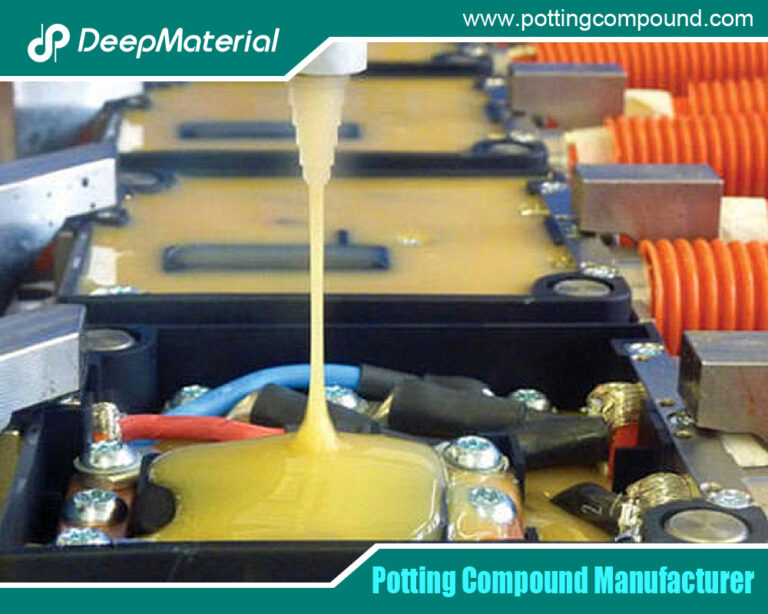
Mastering The Art Of Electronic Potting Process: Ensuring Longevity And Reliability
- Electronic Potting Material Manufacturer
- June 19, 2024
- Benefits of Potting Electronics, china electronic potting silicone manufacturer, china electronic potting silicone supplier, custom automated electronics potting, customize china electronic potting silicone factories, customize china electronic potting silicone supplier, Electrical Component Encapsulation, Electronic Encapsulation Methods, Electronic Potting and Encapsulation, electronic potting compound, Electronic Potting Compounds Manufacturer, electronic potting material, Electronic Potting Process, electronic potting silicone china fabrication, electronic potting silicone china manufacturing, electronic potting silicone manufacturers china, electronic potting silicone products china companies, epoxy potting compound manufacturers, Potting and Encapsulation in the Electronics Industry, potting material for electronic compounds, potting material for electronics, potting process for electronics, Potting Solutions for Electronics Manufacturing
Mastering The Art Of Electronic Potting Process: Ensuring Longevity And Reliability
In the realm of electronic manufacturing, ensuring longevity and reliability is paramount. One crucial process that aids in achieving these goals is electronic potting. Whether you’re a seasoned professional or a newcomer to the field, understanding the nuances of this process can elevate the quality of your electronic products. In this comprehensive guide, we delve into the intricacies of electronic potting, exploring its significance, methods, materials, and best practices.
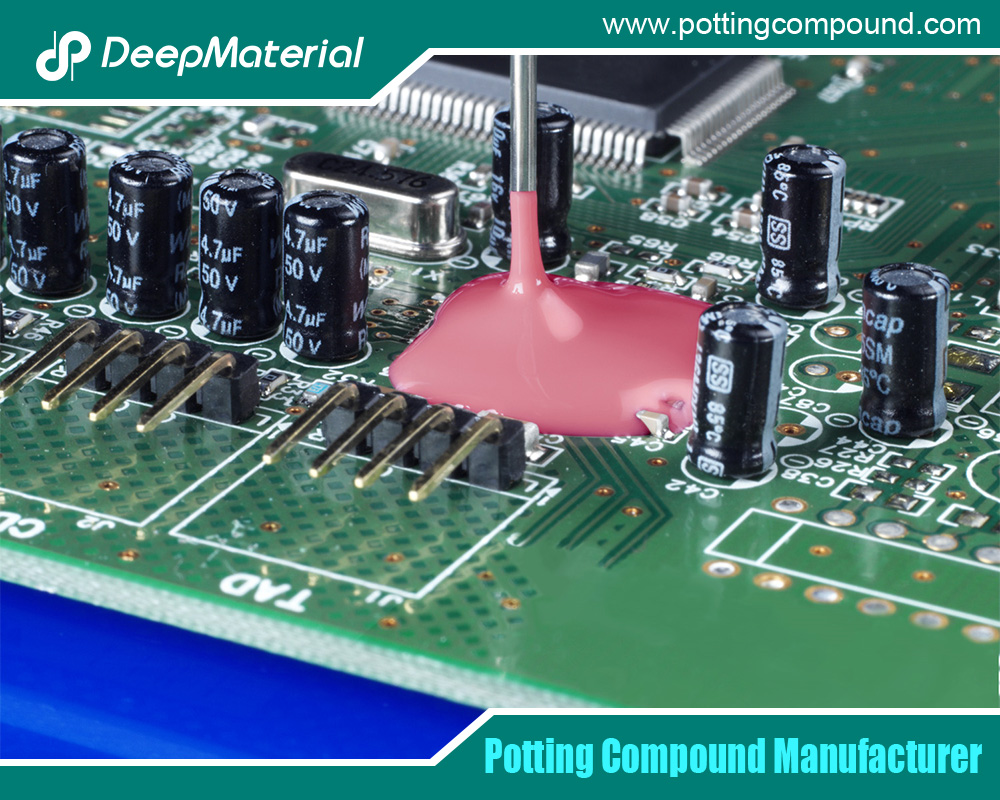
Understanding Electronic Potting
Understanding electronic potting is essential for anyone involved in electronic manufacturing. This process consists of encapsulating electronic components in a protective material to shield them from environmental factors such as moisture, dust, and vibration. The primary goal of electronic potting is to enhance the longevity, reliability, and performance of electronic devices by providing electrical insulation, thermal conductivity, and mechanical support. It plays a crucial role in safeguarding delicate components from damage and ensuring the integrity of electronic assemblies, making it a fundamental aspect of modern electronics manufacturing.
Importance of Electronic Potting
The electronic potting process is a critical step in the manufacturing of electronic devices, providing essential protection and encapsulation for delicate components. This paragraph explores the importance of the electronic potting process in ensuring the reliability, durability, and longevity of electronic devices, highlighting its role in safeguarding against environmental factors and mechanical stress.
Protection from Environmental Factors:
The electronic potting process involves encapsulating electronic components in a protective material, such as epoxy resin or silicone, to shield them from environmental factors like moisture, dust, chemicals, and temperature fluctuations. This protective barrier prevents corrosion, electrical short circuits, and performance degradation caused by exposure to harsh conditions, ensuring the reliability and functionality of electronic devices in diverse operating environments.
Mechanical Stability and Shock Absorption:
In addition to environmental protection, electronic potting materials provide mechanical stability and shock absorption, safeguarding electronic components against mechanical stress and vibration. By encapsulating components in a resilient material, the potting process helps prevent damage from physical impact and mechanical shock, ensuring the integrity and longevity of electronic devices in applications prone to mechanical stress, such as automotive and industrial environments.
Enhanced Thermal Management:
Electronic potting materials can also enhance thermal management by dissipating heat generated by electronic components during operation. Thermally conductive potting materials help transfer heat away from sensitive components, preventing overheating and thermal damage and ensuring the reliable performance of electronic devices, especially in applications with high power densities or elevated operating temperatures.
Types of Potting Materials
The electronic potting process is crucial in encapsulating electronic components in protective materials to ensure their longevity and reliability. Understanding the various potting materials available is essential for manufacturers seeking optimal protection against environmental factors and mechanical stress.
- Epoxy Resins: Epoxy resins are widely used in electronic potting due to their excellent adhesion, chemical resistance, and mechanical strength. They offer protection against moisture, vibration, and thermal cycling, making them suitable for various applications.
- Silicone Rubbers: Silicone rubbers are prized for their flexibility, thermal stability, and resistance to extreme temperatures. They provide reliable protection against moisture ingress, thermal shock, and electrical insulation, making them ideal for applications in harsh environments.
- Polyurethane Resins: Polyurethane resins offer exceptional toughness, abrasion, and chemical resistance. They are commonly used in potting applications requiring superior mechanical protection and durability, such as automotive electronics and outdoor applications.
- Acrylic Resins: Acrylic resins provide good adhesion, moisture resistance, and thermal stability. Due to their versatility and cost-effectiveness, they are often chosen for potting applications in consumer electronics, PCBs, and industrial control systems.
- Potting Compounds with Fillers: Potting compounds can be formulated with various fillers such as glass fibers, silica, or ceramic particles to enhance specific properties such as thermal conductivity, flame resistance, or electrical insulation, catering to the requirements of specialized applications.
- Parylene Coatings: Parylene coatings offer ultra-thin, pinhole-free protection with excellent chemical resistance and dielectric properties. They are applied through a vapor deposition, providing uniform coverage and superior protection for delicate electronic components and assemblies.
By understanding the unique properties and applications of different potting materials, manufacturers can select the most suitable material to ensure the optimal protection and performance of their electronic assemblies in diverse operating conditions.
Electronic Potting Methods
The electronic potting process is critical in protecting sensitive electronic components from environmental factors such as moisture, dust, and vibration. This encapsulation method involves surrounding electronic assemblies with a protective material, ensuring longevity and reliability. Understanding the various potting methods available is essential for manufacturers seeking to optimize the protection of their electronic devices.
- Encapsulation: Encapsulation involves completely immersing electronic components or assemblies in a potting compound, ensuring uniform coverage and protection from external elements. This method is ideal for applications requiring maximum protection and durability, such as automotive electronics and outdoor equipment.
- Selective Potting: Selective potting involves applying the potting material only to specific electronic assembly areas and exposing other regions. This method allows for targeted protection of sensitive components while minimizing material usage and reducing weight, making it suitable for applications where space and weight constraints are critical.
- Conformal Coating: Conformal coating is a thin protective film applied directly onto the surface of electronic assemblies using methods such as spraying, dipping, or brushing. While not technically a potting method, the conformal coating offers protection against moisture, dust, and corrosion, allowing for visual inspection and repairability of components.
- Molding: Molding involves encapsulating electronic components or assemblies in a pre-formed mold using materials such as silicone or epoxy. This method provides precise shaping and protection while allowing for ease of assembly and integration into larger systems.
- Injection Molding: Injection molding is a high-volume manufacturing process in which molten potting material is injected into a mold cavity containing electronic components. This method offers fast production cycles and precise control over material distribution, making it suitable for mass-producing electronic devices.
By understanding the strengths and limitations of each potting method, manufacturers can choose the most appropriate technique to ensure the reliability and performance of their electronic products in various operating environments.
Best Practices for Electronic Potting
The electronic potting process protects sensitive electronic components from environmental factors and mechanical stress. This paragraph explores best practices for electronic potting, ensuring optimal performance and reliability of electronic devices.
Material Selection:
Choosing a suitable potting material is essential for adequate protection. Chemical resistance, thermal conductivity, and flexibility should be considered to ensure compatibility with the application’s requirements and operating environment.
Proper Preparation:
Thorough preparation of components and molds is critical to a successful potting process. Components should be clean and dry to ensure proper adhesion, while molds should be coated with a release agent to facilitate easy removal of the encapsulated assembly.
Precise Mixing and Dispensing:
Accurate mixing and dispensing of potting material are critical for uniform coverage and optimal performance. Automated dispensing systems can ensure consistency and precision, reducing the risk of voids or uneven encapsulation.
Controlled Curing:
Controlled curing conditions, including temperature and humidity, are essential for achieving desired material properties and performance. Proper curing ensures thorough cross-linking and adhesion, maximizing the effectiveness of the potting material in protecting electronic components.
Quality Assurance:
Regular testing and inspection throughout the potting process help identify issues early on and ensure compliance with quality standards. Various quality control measures are employed to ensure the integrity and reliability of the encapsulated assembly. These include visual inspections, material testing, and performance validation.
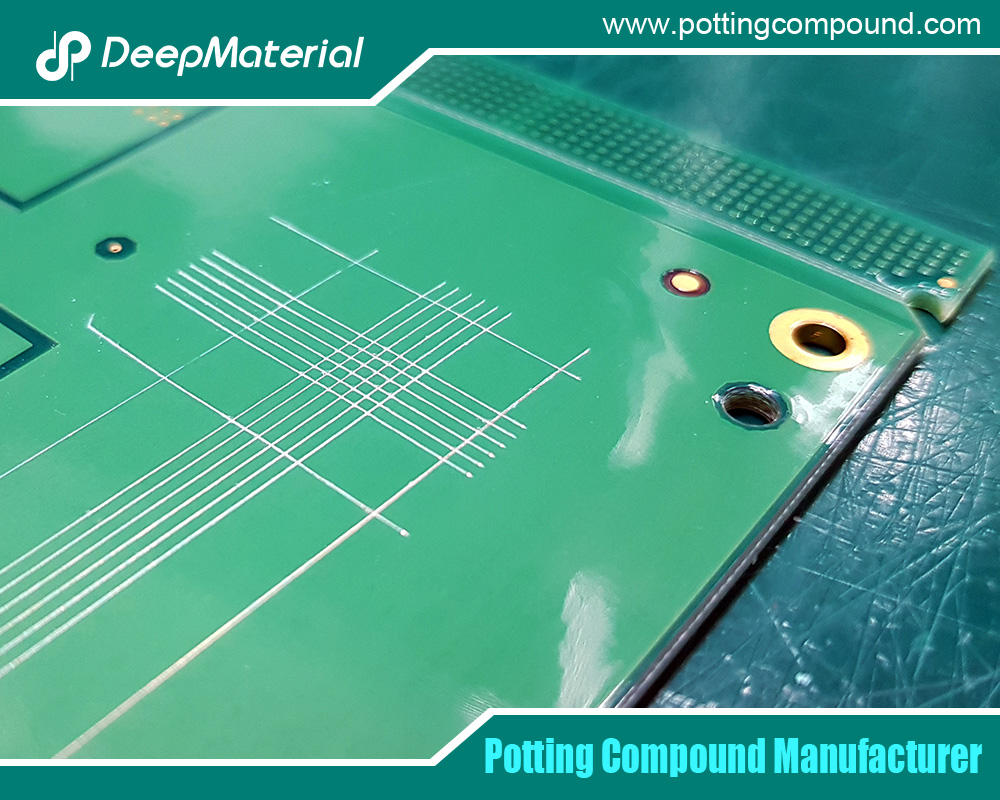
Conclusion
Mastering the art of electronic potting is a journey marked by precision, innovation, and adaptability. As electronic devices evolve in complexity and functionality, potting and ensuring their longevity and reliability becomes increasingly critical. By staying abreast of emerging materials, techniques, and industry trends, manufacturers can elevate their potting processes to new heights, setting a standard for excellence in electronic encapsulation. Embracing this holistic approach safeguards the integrity of electronic products and fosters trust and confidence among consumers in an ever-expanding digital landscape.
For more about mastering the art of electronic potting process: ensuring longevity and reliability,you can pay a visit to DeepMaterial at https://www.pottingcompound.com/electronic-potting-compound/ for more info.
Recent Posts
- Influence of Encapsulation Thickness on the Heat Dissipation Performance and Electrical Insulation Performance of PCB
- Causes and Avoidance Methods of Bubble Generation in the Potting Process
- Technical Details on Controlling Parameters such as Temperature, Pressure, and Speed in the Potting Process to Ensure Potting Quality
- A Comprehensive Analysis of PCB Pretreatment Before Potting Process: A Crucial Link to Ensure the Performance and Reliability of Electronic Devices
- A Comprehensive Analysis of the Performance Differences of Epoxy Resin, Silicone Rubber and Polyurethane Encapsulation Materials
- How to Select Suitable Potting Materials for PCB According to the Working Environment
- What is PCB Potting
- The Evolution of Smart Watch Assembly Adhesive: A Key Component in Modern Wearable Technology
- Laptop Tablet Assembly Adhesive: The Key to Durable and Reliable Device Construction
- Power Bank Assembly Adhesive: The Essential Component for Building Durable Power Banks