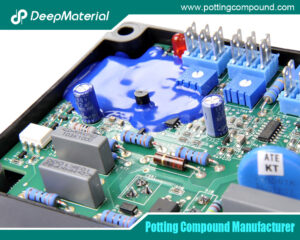
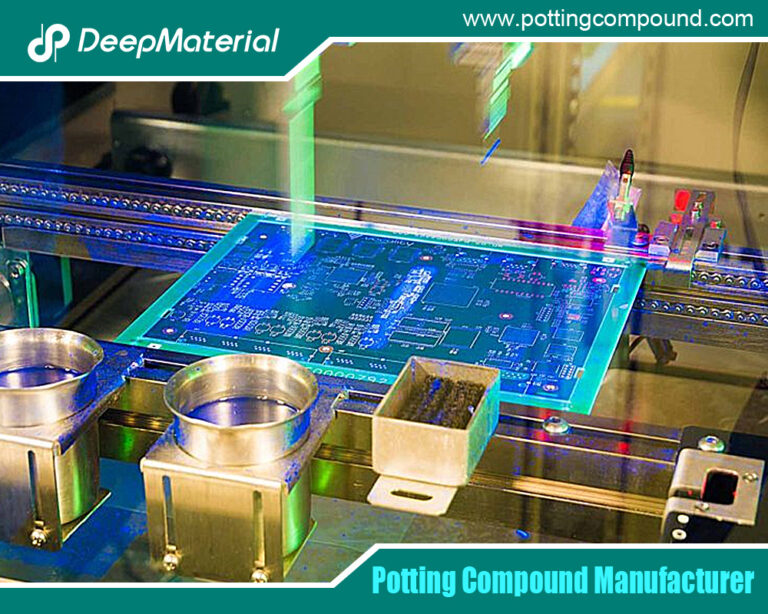
Polyurethane Potting Compound for Electronics: A Comprehensive Guide
- Electronic Potting Material Manufacturer
- November 20, 2024
- electronic potting compound, epoxy potting compound, Flexible Potting Compound, Industrial Conformal Coating, LED Potting Compound, pcb conformal coating, PCB Potting Compound, polyurethane potting compound, Polyurethane Potting Compound for Electronic, Polyurethane Potting Compound for Electronic China Hotsale, Polyurethane Potting Compound for Electronic China OEM, Polyurethane Potting Compound for Electronic China Wholesale, Polyurethane Potting Compound for Electronic Factory Hotsale, Polyurethane Potting Compound for Electronic Factory OEM, Polyurethane Potting Compound for Electronic Factory Wholesale, Polyurethane Potting Compound for Electronic Manufacturer, Polyurethane Potting Compound for Electronic Supplier, Polyurethane Potting Compound for Electronic Supplier Hotsale, Polyurethane Potting Compound for Electronic Supplier Wholesale, Silicone Potting Compound, Urethane Conformal Coating, UV Cure Conformal Coating, UV Cure Potting Compound, waterproof potting compound
Polyurethane Potting Compound for Electronics: A Comprehensive Guide
In today’s fast-paced electronics industry, ensuring the reliability and longevity of electronic components is more critical than ever. As devices become smaller and more complex, protecting sensitive electronics from environmental factors is paramount. One of the most effective methods to achieve this protection is through the use of potting compounds, mainly polyurethane potting compounds. This blog post aims to thoroughly understand polyurethane potting compounds, their properties, applications, advantages, and important considerations for their use in electronics.
What is a Polyurethane Potting Compound?
Polyurethane potting compounds are versatile materials used to encapsulate and protect electronic components. They are typically composed of a polyol and an isocyanate that react to form a solid polymer matrix. The resulting potting material can be tailored to meet specific requirements such as flexibility, hardness, and thermal stability.
Critical Characteristics of Polyurethane Potting Compounds
- Chemical Resistance: Polyurethane potting compounds resist various chemicals, including oils, solvents, and moisture.
- Thermal Stability: These compounds can maintain performance over a broad temperature range, making them suitable for diverse environmental conditions.
- Mechanical Strength: Polyurethane provides outstanding mechanical protection, safeguarding components against physical damage such as shock, vibration, and impact.
- Electrical Insulation: These compounds offer superior electrical insulation properties, preventing short circuits and enhancing overall device safety.
- Adhesion: Polyurethane potting compounds can bond well with different substrates, ensuring a secure components encapsulation.
Applications of Polyurethane Potting Compound in Electronics
Polyurethane potting compounds are widely utilized across various sectors of the electronics industry. Here are some notable applications:
Consumer Electronics
- Smartphones: Encapsulates circuit boards to protect against moisture, dust, and physical damage.
- Laptops: Provides insulation and protection for internal components, extending device life.
- Wearable Devices: Protects sensitive electronics in fitness trackers and smartwatches from environmental stressors.
Automotive Electronics
- Sensors: Safeguards sensitive vehicle electronic parts from harsh conditions, including extreme temperatures and vibrations.
- Control Units: Protects electronic control units (ECUs) from moisture and physical impact, ensuring reliable performance.
Industrial Equipment
- Motors: Insulates and protects electrical components from dirt, humidity, and mechanical stress.
- Control Panels: Enhances the durability of control panels in industrial environments by providing a protective barrier.
Medical Devices
- Sensors and Monitors: Ensures reliability in critical applications by protecting sensitive electronics from moisture and contaminants.
- Implantable Devices: Provides biocompatibility and safeguards electronic components from bodily fluids and environmental conditions.
Aerospace and Defense
- Avionics: Encapsulates sensitive avionics equipment to withstand extreme environmental conditions.
- Military Electronics: Protects electronic components in military applications from shock, vibration, and moisture.
Benefits of Using Polyurethane Potting Compounds
Choosing polyurethane potting compounds for electronic applications offers several advantages:
Enhanced Protection
- Moisture Barrier: Prevents corrosion and damage from water ingress, which can compromise electronic functionality.
- Shock Absorption: Provides cushioning against mechanical impacts, reducing the risk of component failure.
Longevity
- Extended Lifespan: Protects components from environmental factors that could lead to premature failure, increasing product longevity.
Versatility
- Custom Formulations: Polyurethane potting compounds can be tailored to meet specific performance requirements, such as flexibility or rigidity.
- Various Hardness Levels: Available in multiple hardness options to suit different applications, ensuring optimal performance.
Ease of Use
- Simple Application: This can be easily mixed and applied to components, facilitating efficient production processes.
- Fast Curing Times: Many polyurethane compounds cure quickly, reducing production time and increasing efficiency.
Cost-Effectiveness
- Reduced Maintenance Costs: Polyurethane potting compounds can reduce maintenance and replacement costs by protecting components from damage.
- Improved Reliability: Enhanced protection translates to increased reliability, reducing warranty claims and enhancing customer satisfaction.
Considerations When Using Polyurethane Potting Compounds
While polyurethane potting compounds provide numerous benefits, there are several considerations to keep in mind:
Curing Conditions
- Temperature and Humidity: Ensure the compound is cured under recommended conditions for optimal performance. Deviations can lead to incomplete curing and compromised properties.
Environmental Impact
- Volatile Organic Compounds (VOCs): Assess the environmental impact of the materials used, particularly any VOCs released during curing. Look for low-VOC formulations when possible to minimize environmental impact.
Compatibility
- Material Compatibility: Verify the compatibility of the potting compound with the electronic components being encapsulated to avoid any degradation or adverse reactions.
Cost Considerations
- Cost-Effectiveness: Evaluate the cost of the potting compound relative to its performance benefits and the specific application. Sometimes, investing in a higher-quality compound can save money in the long run by reducing failures.
Application Techniques
- Mixing and Application: Ensure proper mixing of components to avoid issues like uneven curing or insufficient adhesion. Consider using automated dispensing systems for consistent application.
Health and Safety
- Handling Precautions: Follow safety guidelines for handling chemicals, including wearing appropriate protective gear and ensuring adequate ventilation during application.
Comparison with Other Potting Compounds
When selecting a potting compound, it’s essential to compare polyurethane with other materials, such as epoxy and silicone.
Polyurethane vs. Epoxy
- Flexibility: Polyurethane is more flexible than epoxy, making it suitable for applications requiring some movement or shock absorption.
- Cure Time: Polyurethane typically cures faster than epoxy, which can be advantageous in high-volume production environments.
- Moisture Resistance: Both offer excellent moisture resistance, but polyurethane can be more forgiving in varying conditions.
Polyurethane vs. Silicone
- Temperature Range: Silicone generally has a broader temperature range, making it suitable for extreme thermal environments.
- Adhesion: Polyurethane often provides better adhesion to various substrates than silicone, enhancing its effectiveness in many applications.
- Elasticity: Silicone is typically more elastic, which may be preferable in applications where flexibility is paramount.
Best Practices for Using Polyurethane Potting Compounds
To maximize the effectiveness of polyurethane potting compounds, consider the following best practices:
Surface Preparation
- Cleaning: Thoroughly clean surfaces to remove dust, grease, and other contaminants that may hinder adhesion.
- Roughening: For improved adhesion, consider roughening the surface of components before applying the potting compound.
Accurate Mixing
- Follow Manufacturer Instructions: Adhere to the manufacturer’s recommended mixing ratios and instructions to ensure optimal performance.
- Use Proper Equipment: Consider using a mechanical mixer for consistent mixing, especially in large-scale applications.
Controlled Application
- Temperature and Humidity Control: Maintain consistent temperature and humidity levels during application and curing to avoid variations in performance.
- Automated Dispensing: Automated dispensing systems are used for precise and consistent application, reducing the risk of operator error.
Quality Control
- Testing: Conduct regular quality control tests on the potting compound to ensure it meets performance specifications.
- Inspection: Inspect finished products for any defects or inconsistencies in the potting process.
Conclusion
Polyurethane potting compounds play a vital role in the protection and longevity of electronic devices. Their unique combination of chemical resistance, thermal stability, and mechanical strength makes them suitable for various applications, from consumer electronics to aerospace and defense. The demand for reliable and effective potting solutions like polyurethane compounds will only grow as technology advances.
For more about choosing the Top Polyurethane Potting Compound for Electronics: A Comprehensive Guide, you can pay a visit to DeepMaterial at https://www.pottingcompound.com/ for more info.
Recent Posts
- Influence of Encapsulation Thickness on the Heat Dissipation Performance and Electrical Insulation Performance of PCB
- Causes and Avoidance Methods of Bubble Generation in the Potting Process
- Technical Details on Controlling Parameters such as Temperature, Pressure, and Speed in the Potting Process to Ensure Potting Quality
- A Comprehensive Analysis of PCB Pretreatment Before Potting Process: A Crucial Link to Ensure the Performance and Reliability of Electronic Devices
- A Comprehensive Analysis of the Performance Differences of Epoxy Resin, Silicone Rubber and Polyurethane Encapsulation Materials
- How to Select Suitable Potting Materials for PCB According to the Working Environment
- What is PCB Potting
- The Evolution of Smart Watch Assembly Adhesive: A Key Component in Modern Wearable Technology
- Laptop Tablet Assembly Adhesive: The Key to Durable and Reliable Device Construction
- Power Bank Assembly Adhesive: The Essential Component for Building Durable Power Banks