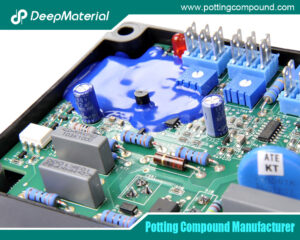
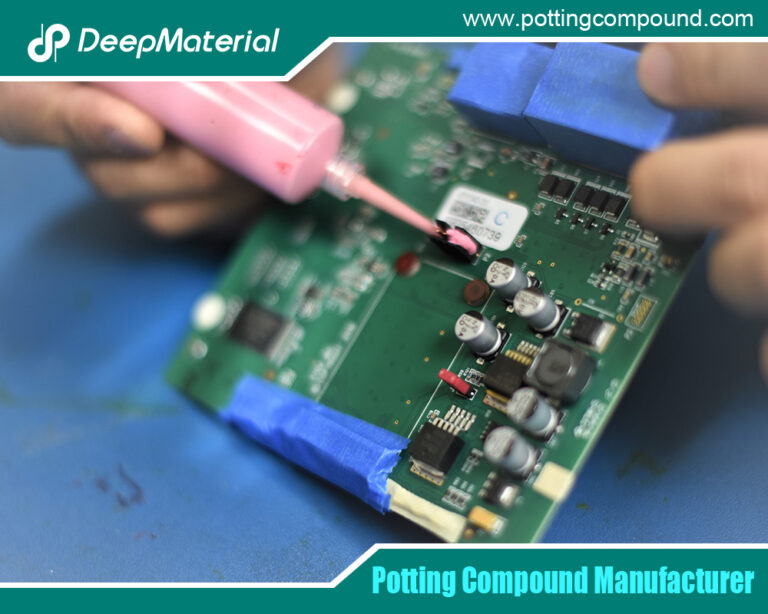
Potting Epoxy for Electronics: Ensuring Reliability and Longevity in Electronic Applications
- Electronic Potting Material Manufacturer
- November 19, 2024
- Connector Potting Compound, electronic potting compound, epoxy conformal coating, epoxy potting compound, Flexible Potting Compound, LED Potting Compound, PCB Potting Compound, polyurethane potting compound, Potting Epoxy for Electronic, Potting Epoxy for Electronic China Hotsale, Potting Epoxy for Electronic China OEM, Potting Epoxy for Electronic China Wholesale, Potting Epoxy for Electronic Factory Hotsale, Potting Epoxy for Electronic Factory OEM, Potting Epoxy for Electronic Factoty Wholesale, Potting Epoxy for Electronic Manufacturer, Potting Epoxy for Electronic Supplier, Potting Epoxy for Electronic Supplier Hotsale, Silicone Conformal Coating, Silicone Potting Compound, Urethane Conformal Coating, UV Cure Potting Compound, waterproof potting compound
Potting Epoxy for Electronics: Ensuring Reliability and Longevity in Electronic Applications
In the rapidly advancing world of electronics, the reliability and longevity of components are of utmost importance. Protecting sensitive electronic parts is crucial as devices become smaller, more complex, and often used in demanding environments. One effective method for safeguarding these components is the use of potting epoxy. This material is a robust barrier against environmental hazards such as moisture, dust, chemicals, and mechanical stress. This blog post will explore the properties, applications, benefits, and considerations of potting epoxy for electronics. By the end, you’ll have a comprehensive understanding of how potting epoxy can enhance the performance and durability of electronic devices.
What is Potting Epoxy?
Potting epoxy is a thermosetting resin commonly used to encapsulate and protect electronic components. Formulated from epoxy resins, hardeners, and various additives, potting epoxy provides a solid, protective layer that prevents moisture ingress, mechanical damage, and chemical exposure. It forms a durable, inert mass that insulates and physically supports the encapsulated components when cured.
Critical Properties of Potting Epoxy
Potting epoxies possess several essential properties that make them suitable for electronics:
- Durability: Once cured, potting epoxy forms a hard, impact-resistant material that protects components from physical stress.
- Chemical Resistance: Epoxy resins are known for resistance to various chemicals, ensuring long-term performance in harsh environments.
- Electrical Insulation: Potting epoxy offers excellent dielectric properties, preventing electrical shorts and ensuring the safe operation of electronic devices.
- Moisture Barrier: This creates a waterproof seal that protects sensitive electronics from humidity and water ingress.
- Thermal Stability:Capable of withstanding a wide temperature range without compromising integrity.
Applications of Potting Epoxy in Electronics
Potting epoxy is widely used in various sectors due to its protective qualities. Some typical applications include:
Consumer Electronics
- Smartphones and Tablets: These devices protect circuit boards and components from moisture and dust, enhancing their durability and longevity.
- Wearable Devices: Encapsulates electronics in fitness trackers and smartwatches, shielding them from sweat and environmental exposure.
Automotive Electronics
- Control Units: Protects critical electronic control units from vibrations, moisture, and extreme temperatures, ensuring vehicle reliability.
- Sensors:Encapsulated sensors maintain functionality in harsh conditions, such as those encountered in automotive applications.
Industrial Equipment
- Power Supplies: Potting epoxy shields power supply components from dust and moisture, providing stable and reliable performance.
- Control Systems: Protects control systems and electronic circuits from environmental influences, improving operational efficiency.
Medical Devices
- Diagnostic Equipment: Potting epoxy encapsulates electronics in medical devices, ensuring safe and reliable operation in critical applications.
- Implantable Devices: Provides moisture resistance and biocompatibility, protecting electronics in devices such as pacemakers.
Aerospace and Defense
- Avionics:Potting epoxy protects sensitive electronic components in avionics systems from extreme conditions.
- Military Equipment:Ensures the reliability of electronic systems in defense applications where exposure to harsh environments is expected.
Benefits of Using Potting Epoxy
The use of potting epoxy in electronics offers numerous advantages that contribute to enhanced device performance and reliability:
Environmental Protection
- Moisture Barrier: Prevents water ingress, which can lead to corrosion and failure of electronic components.
- Dust and Contaminant Resistance: Keeps contaminants away from sensitive parts, ensuring optimal functionality.
Mechanical Protection
- Shock Absorption: The rigid structure of cured epoxy absorbs impacts and vibrations, safeguarding delicate components.
- Structural Support:Potting epoxy provides physical support for components, reducing the risk of damage from handling or environmental stresses.
Improved Electrical Performance
- Electrical Insulation: The excellent dielectric properties of potting epoxy prevent electrical shorts and enhance the safety of devices.
- Thermal Management:Some formulations of potting epoxy provide thermal conductivity, helping to dissipate heat from electronic components.
Cost-Effectiveness
- Reduced Failure Rates: Enhanced protection lowers warranty claims and manufacturer replacement costs.
- Extended Lifespan: Devices using potting epoxy often experience a longer operational life, resulting in a better return on investment.
Versatility
- Custom Formulations: Potting epoxies can be tailored with specific additives to meet unique application requirements, such as improved adhesion or specific curing characteristics.
Selecting the Right Potting Epoxy
Choosing the appropriate potting epoxy for a specific application involves several considerations:
Cure Time
- Fast-Curing Options:Ideal for applications requiring quick processing times, reducing downtime.
- Slow-Curing Options:Beneficial for larger applications where extended working time allows for adjustments during application.
Viscosity
- Low Viscosity: Suitable for applications requiring easy flow into intricate designs and gaps.
- High Viscosity: Preferred for applications where the material needs to hold its shape during curing.
Thermal Conductivity
- High Thermal Conductivity: Essential for applications where heat dissipation is critical, such as power electronics.
- Low Thermal Conductivity: This may be adequate for less demanding applications where heat management is not a primary concern.
Electrical Properties
- Dielectric Strength:Ensure the chosen potting epoxy meets the required dielectric strength for effective electrical insulation.
- Volume Resistivity: Select compounds with high volume resistivity to prevent electrical leakage.
Environmental Resistance
- Chemical Resistance:Choose potting epoxies that can withstand specific chemicals present in the operating environment.
- Temperature Range: Ensure the potting epoxy can operate effectively within the expected temperature range.
Application Techniques for Potting Epoxy
The method of applying potting epoxy can vary depending on the specific application and production scale:
Manual Dispensing
- Ideal for Small-Scale Projects:Useful for prototypes and small batches where precision application is necessary.
- Flexibility:Allows adjustments during the application process, making it suitable for unique designs.
Automated Dispensing
- Mass Production:Ensures consistency and efficiency in larger production runs.
- Precision:Automated systems can deliver precise amounts of material, reducing waste.
Injection Molding
- Complex Shapes: A method suitable for complex assemblies requiring complete encapsulation.
- Uniform Application: Ensures even coverage and consistent results.
Safety Considerations
When working with potting epoxy, safety precautions should be followed to ensure a safe working environment:
Personal Protective Equipment (PPE)
- Gloves:Wear protective gloves to prevent skin contact with uncured epoxy.
- Goggles:Use safety goggles to protect eyes from splashes during mixing and application.
- Respirators: In poorly ventilated areas, wear a respirator to avoid inhaling fumes.
Ventilation
- Adequate Airflow:Ensure proper ventilation in the workspace to dissipate any fumes released during mixing and curing.
Material Disposal
- Follow Regulations:Adhere to local regulations for the disposal of potting epoxy and related materials.
- Recycling Options:Explore recycling options for unused or cured materials where applicable.
Advancements in Potting Epoxy Technology
Recent advancements in potting epoxy technology have led to new formulations and additives that further enhance performance. Some noteworthy trends include:
Bio-Based Epoxies
- Sustainability: Developing bio-based epoxies from renewable resources offers an eco-friendly alternative to traditional petrochemical-based products.
Enhanced Thermal Conductivity
- Improved Heat Management: New additives are being developed to enhance the thermal conductivity of potting epoxies, improving heat dissipation for high-power electronics.
Fast-Curing Formulations
- Efficiency:Innovations in curing agents allow faster curing times, significantly reducing production cycle times.
Flexible Epoxy Formulations
- Adaptability:New flexible potting epoxies, such as wearable devices, are being developed for applications where flexibility is necessary.
Conclusion
Potting epoxy is vital in the electronics industry, providing a robust solution for protecting sensitive components from environmental hazards and mechanical stress. Its excellent properties, including durability, chemical resistance, electrical insulation, and moisture barrier capabilities, make it an ideal choice for various applications, from consumer electronics to medical devices and aerospace systems.
For more about choosing the Top Potting Epoxy for Electronics: Ensuring Reliability and Longevity in Electronic Applications, you can pay a visit to DeepMaterial at https://www.pottingcompound.com/ for more info.
Recent Posts
- Influence of Encapsulation Thickness on the Heat Dissipation Performance and Electrical Insulation Performance of PCB
- Causes and Avoidance Methods of Bubble Generation in the Potting Process
- Technical Details on Controlling Parameters such as Temperature, Pressure, and Speed in the Potting Process to Ensure Potting Quality
- A Comprehensive Analysis of PCB Pretreatment Before Potting Process: A Crucial Link to Ensure the Performance and Reliability of Electronic Devices
- A Comprehensive Analysis of the Performance Differences of Epoxy Resin, Silicone Rubber and Polyurethane Encapsulation Materials
- How to Select Suitable Potting Materials for PCB According to the Working Environment
- What is PCB Potting
- The Evolution of Smart Watch Assembly Adhesive: A Key Component in Modern Wearable Technology
- Laptop Tablet Assembly Adhesive: The Key to Durable and Reliable Device Construction
- Power Bank Assembly Adhesive: The Essential Component for Building Durable Power Banks