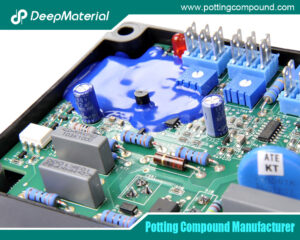
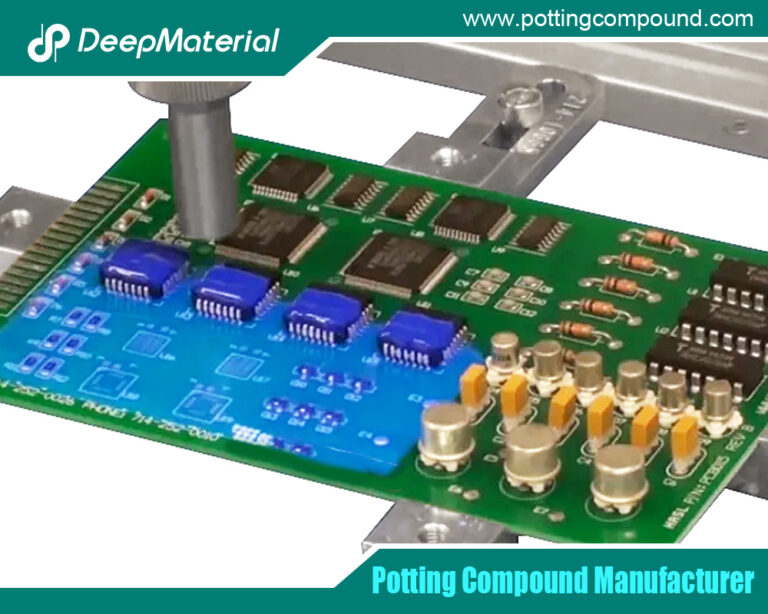
Potting Material for Electronic Components: An In-Depth Guide
- Electronic Potting Material Manufacturer
- September 13, 2024
- Automotive potting material manufacturers, circuit board potting compound, Connector Potting Compound, deepmaterial potting compound, electrical potting compound, Electronic Encapsulant Potting Compound, electronic encapsulant potting compounds, Electronic Epoxy Encapsulant Potting Compound, Electronic Epoxy Potting Compound, electronic potting compound, Electronic Potting Compounds Manufacturer, electronic potting material, electronic potting material manufacturer, Encapsulant Potting Compound, Encapsulants and Potting Compounds Suppliers, epoxy potting compound, epoxy potting compound manufacturers, Epoxy potting material manufacturers, potting material, potting material for components, potting material for electronic, potting material for electronic components, potting material for electronics, potting material manufacturer, Potting material manufacturers in usa, Potting Materials for Electronics
Potting Material for Electronic Components: An In-Depth Guide
Reliability and durability are paramount in the world of electronics. One critical technology ensuring these attributes is potting—a process where electronic components are encapsulated in a protective material to safeguard them from environmental and mechanical stress. This article delves into the various types of potting materials, their properties, and their applications in the electronics industry.
1. Understanding Potting and Its Importance
Potting is a technique for encasing electronic components within a protective substance. The primary purpose is to shield the components from environmental factors such as moisture, dust, and chemicals. Potting also provides mechanical support to prevent physical damage due to vibrations or shocks.
1.1 The Potting Process
The potting process involves placing electronic components into a mold or enclosure and filling it with a potting compound. The compound is typically a resin that hardens over time to form a solid, protective layer. The critical steps in potting include:
- Preparation:Cleaning and preparing the components and the mold.
- Mixing:Combining the potting resin and hardener (if applicable) in the correct proportions.
- Application:Pouring or injecting the mixture into the mold.
- Curing:Allowing the resin to cure and solidify, forming a protective layer around the components.
1.2 Benefits of Potting
- Environmental Protection:Potting materials provide a barrier against moisture, dust, and chemicals, enhancing the longevity of electronic components.
- Mechanical Support:The solidified potting material absorbs shock and vibration, preventing physical damage.
- Thermal Management:Potting compounds can help dissipate heat away from sensitive components.
- Electrical Insulation:The materials used in potting often provide excellent electrical insulation, preventing short circuits.
2. Types of Potting Materials
Various materials can be used for potting, each with unique properties suited for different applications. The most common types include:
2.1 Epoxy Resins
Epoxy resins are widely used due to their excellent adhesive properties and durability. They provide strong protection against environmental factors and mechanical stresses.
- Properties:Epoxies offer high thermal stability, chemical resistance, and mechanical strength. They also have good electrical insulating properties.
- Applications:Epoxy resins are commonly used in automotive, industrial controls, and consumer electronics.
2.2 Silicone Rubber
Silicone rubber is another popular choice for potting, particularly when flexibility and temperature stability are required.
- Properties:Silicone rubber is highly thermally stable, flexible, and resistant to extreme temperatures. It also provides good electrical insulation.
- Applications:Silicone is often used in applications requiring flexibility, such as aerospace and medical electronics.
2.3 Polyurethane Resins
Polyurethane resins offer a balance between flexibility and hardness, making them suitable for a variety of applications.
- Properties:Polyurethanes are known for their excellent adhesion, impact resistance, and resistance to moisture and chemicals.
- Applications:They are often used in consumer electronics, telecommunications, and automotive applications.
2.4 Acrylic Resins
Acrylic resins are valued for their clarity and ease of processing.
- Properties:Acrylics offer good mechanical strength, UV resistance, and electrical insulation. They are also known for their optical clarity.
- Applications:Acrylic resins, such as LED lights and displays, are used where visibility is crucial.
2.5 Thermoplastic Elastomers (TPEs)
Thermoplastic elastomers combine the properties of rubber with the processability of plastics.
- Properties:TPEs offer flexibility, chemical resistance, and good electrical insulation. They can be processed using conventional thermoplastic techniques.
- Applications:TPEs, such as connectors and sensors, are used in applications requiring flexibility and toughness.
3. Selecting the Right Potting Material
Choosing the appropriate potting material depends on several factors, including the application’s requirements and the operating environment.
3.1 Factors to Consider
- Temperature Range:The material should withstand the temperatures it will be exposed to during operation.
- Chemical Resistance:Consider the chemicals the potting material will encounter, such as in harsh industrial environments.
- Mechanical Properties:Depending on the application, the material may need to be flexible or rigid.
- Electrical Properties:Ensure the material provides adequate electrical insulation for the components.
- Curing Time:Some applications require fast curing, while others can accommodate longer.
3.2 Application-Specific Considerations
- Consumer Electronics:Materials like epoxy resins and silicones are often used for their durability and electrical insulation properties.
- Automotive Electronics:Polyurethane resins and silicones are standard due to their resistance to vibrations and extreme temperatures.
- Aerospace and Defense:Silicone rubber and epoxy resins are preferred for their thermal stability and resistance to harsh environments.
- Medical Devices:Biocompatible silicones and epoxies ensure safety and performance in medical applications.
4. Potting Techniques and Best Practices
Proper potting techniques are essential for achieving the desired performance and reliability. The following best practices can help ensure successful potting:
4.1 Mold Preparation
Ensure that molds are clean and free of contaminants before potting. Proper mold preparation helps achieve a smooth finish and prevents defects.
4.2 Mixing and Handling
Follow the manufacturer’s instructions for mixing the potting compound. Accurate measurement and thorough mixing are critical to ensure proper curing and performance.
4.3 Application Methods
Potting compounds can be applied using various methods, including:
- Pouring:The resin is poured directly into the mold, covering the components.
- Injection:The resin is injected into the mold under pressure, ensuring thorough coverage.
- Dipping:Components are dipped into the potting material, allowing it to coat the surfaces.
4.4 Curing
Allow sufficient time for the potting compound to cure fully. Curing times can vary depending on the material and environmental conditions. Proper curing ensures the potting material achieves its maximum strength and protective properties.
4.5 Quality Control
Implement quality control measures to inspect the finished potting. This includes checking for voids, bubbles, and uniform coverage. Testing for electrical insulation and mechanical strength can help verify the potting’s effectiveness.
5. Future Trends in Potting Materials
As technology advances, new potting materials and techniques are emerging to meet the electronics industry’s evolving demands.
5.1 Advanced Materials
Researchers are developing advanced materials with enhanced properties, such as improved thermal conductivity and flexibility. These materials aim to provide better protection and performance in increasingly complex electronic devices.
5.2 Environmentally Friendly Options
There is a growing emphasis on developing environmentally friendly potting materials. Biodegradable resins and low-impact manufacturing processes are being explored to reduce the environmental footprint of potting materials.
5.3 Smart Potting Materials
Innovative potting materials with embedded sensors and self-healing properties are being developed. These materials can monitor the health of electronic components and repair themselves in case of damage, enhancing reliability and longevity.
5.4 Integration with Emerging Technologies
Potting materials are integrated with emerging technologies such as flexible electronics and wearable devices. These materials need to accommodate the unique requirements of these applications, such as flexibility and lightweight.
Conclusion
Potting materials are crucial in protecting electronic components from environmental and mechanical stresses. By selecting suitable potting material and employing proper techniques, manufacturers can ensure the reliability and longevity of their electronic devices. As technology advances, developing new and improved potting materials will further enhance the performance and durability of electronic components, paving the way for innovative applications and technologies.
Understanding the different types of potting materials, their properties, and their applications is essential for making informed decisions in the design and manufacturing of electronic devices. Whether it’s ensuring the longevity of consumer electronics or enhancing the performance of aerospace systems, potting materials are a vital component in the electronics industry, providing protection and reliability for a wide range of applications.
For more about choosing the top potting material for electronic components: an in-depth guide, you can pay a visit to DeepMaterial at https://www.pottingcompound.com/ for more info.
Recent Posts
- Influence of Encapsulation Thickness on the Heat Dissipation Performance and Electrical Insulation Performance of PCB
- Causes and Avoidance Methods of Bubble Generation in the Potting Process
- Technical Details on Controlling Parameters such as Temperature, Pressure, and Speed in the Potting Process to Ensure Potting Quality
- A Comprehensive Analysis of PCB Pretreatment Before Potting Process: A Crucial Link to Ensure the Performance and Reliability of Electronic Devices
- A Comprehensive Analysis of the Performance Differences of Epoxy Resin, Silicone Rubber and Polyurethane Encapsulation Materials
- How to Select Suitable Potting Materials for PCB According to the Working Environment
- What is PCB Potting
- The Evolution of Smart Watch Assembly Adhesive: A Key Component in Modern Wearable Technology
- Laptop Tablet Assembly Adhesive: The Key to Durable and Reliable Device Construction
- Power Bank Assembly Adhesive: The Essential Component for Building Durable Power Banks