Silicone Conformal Coating
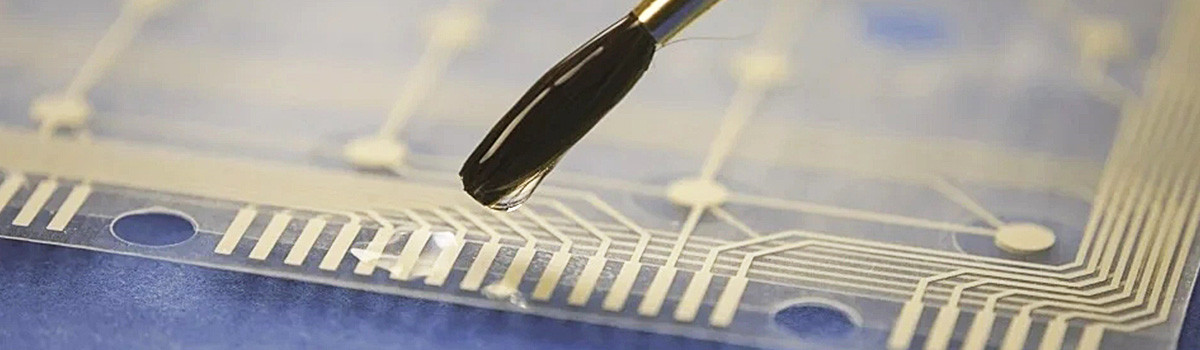
In the realm of protective coatings, silicone conformal coating stands out as a versatile and essential solution. From safeguarding delicate electronics to enhancing durability in harsh environments, its applications are as varied as they are indispensable. This guide aims to delve deep into the world of silicone conformal coating, exploring its composition, applications, benefits, and considerations. Whether you’re a seasoned engineer or a curious enthusiast, prepare to unlock the secrets behind this remarkable protective marvel.
Table of Contents
ToggleWhat is Silicone Conformal Coating?
Silicone conformal coating is a specialized method used in many industries to shield electronic components from the elements, including moisture, dust, chemicals, and temperature changes. This thin, protective film is applied to circuit boards and other electronic assemblies to enhance their durability and reliability. This coating is particularly popular in industries where electronics are exposed to harsh conditions, such as automotive, aerospace, marine, and industrial manufacturing.
The primary purpose of silicone conformal coating is to provide insulation and protection to sensitive electronic components. By forming a barrier over the surface of the circuit board, the coating prevents moisture from ingressing, which can cause corrosion and short circuits. Additionally, the coating shields the components from dust and debris, reducing the risk of malfunctions and extending the lifespan of the electronics.
One key benefit of silicone conformal coating is its flexibility and adaptability to various shapes and sizes of electronic assemblies. Unlike rigid coatings, silicone conforms to the contours of the components, ensuring complete coverage and protection. This functionality is beneficial for applications where space is premium or components have asymmetrical forms.
Moreover, silicone conformal coating offers excellent thermal stability, maintaining its protective properties even under extreme temperatures. Because of this capability, the product can be used in car engine compartments or outdoor installations where electronic devices are exposed to extreme heat or sudden temperature changes.
Another advantage of silicone conformal coating is its resistance to chemicals and solvents. It provides a barrier against corrosive substances, preventing them from damaging the delicate electronic components. This chemical resistance is crucial in industries where electronics are exposed to oils, fuels, cleaning agents, or other harsh chemicals.
Furthermore, silicone conformal coating is easy to apply by spraying, brushing, or dipping, and it cures quickly to form a durable protective layer. This solution becomes cost-effective in mass-production environments where efficiency and productivity are paramount.
Origins and Development: How Has History Evolved?
Silicone conformal coating has a rich history that traces its origins back to the mid-20th century. Developed initially as a solution to protect electronic components in military applications, its evolution has become vital in various industries where electronics are exposed to harsh environmental conditions. Let’s delve into the origins and development of silicone conformal coating:
- Early Formulations and Limitations:Early silicone conformal coatings were primarily solvent-based formulations. While effective in protecting against moisture and environmental contaminants, they often pose challenges related to application, curing times, and environmental impact due to volatile organic compounds (VOCs).
- Advancements in Formulation:Modern silicone conformal coatings have significantly improved with advancements in silicone chemistry and manufacturing processes. Developing solventless and low-VOC formulations has addressed environmental concerns while enhancing application ease and performance.
- Expansion into Diverse Industries:Initially confined to military and aerospace applications, silicone conformal coatings have expanded into diverse industries such as automotive, consumer electronics, medical devices, and industrial automation. The growing demand for electronics in harsh operating environments drives this expansion.
- Technological Enhancements:Technological advancements have propelled the evolution of silicone conformal coatings. Innovations such as UV-curable formulations and nanotechnology have further improved coating properties, offering enhanced protection, durability, and performance in demanding applications.
- Customization and Specialization:Manufacturers now offer a wide range of silicone conformal coatings tailored to specific industry requirements. These coatings may exhibit specialized properties such as high-temperature resistance, UV stability, or chemical resistance, catering to the unique needs of different applications.
- Global Adoption and Standardization:Silicone conformal coatings have gained worldwide acceptance and are subject to various industry standards and regulations governing their use. Standardization ensures consistent performance and reliability across different applications and facilitates interoperability in supply chains.
- Future Trends and Innovations:Ongoing research and development efforts aim to enhance silicone conformal coatings’ properties and capabilities. Emerging trends include using sustainable and eco-friendly formulations and integrating intelligent functionalities such as self-healing and sensing capabilities.
Composition Demystified: What Exactly Is Inside?
Composition, whether in art, music, or writing, is a complex interplay of various elements that create a cohesive whole. In essence, composition demystified reveals a structured arrangement of these components, each contributing uniquely to the final creation.
Composition encompasses several key elements: form, structure, harmony, rhythm, melody, texture, and dynamics. These elements serve as the building blocks upon which the composition is constructed.
The form provides the overarching blueprint, determining the overall organization and arrangement of the piece. It outlines the sections, their order, and how they relate to one another through repetition, contrast, or variation.
Structure refers to the framework within which the composition operates. It encompasses the logical progression of ideas and motifs, guiding the listener through the narrative or thematic development.
Harmony deals with the simultaneous sounding of different musical notes and how they interact to create chord progressions and tonalities. It establishes the harmonic language of the piece, conveying emotions and establishing mood.
Rhythm is the heartbeat of the composition, dictating the flow and pacing through patterns of duration and accentuation. It infuses energy and movement, shaping the listener’s perception of time and space.
Melody is the primary musical theme or motif that captures the listener’s ear and serves as the composition’s focal point. It carries the emotional weight, conveying the piece’s essence through contour and phrasing.
Texture refers to the layers of sound within the composition and how they blend to create a rich sonic landscape. It encompasses the interplay between melody, harmony, and rhythm, shaping the overall auditory experience.
Dynamics deal with the variations in volume and intensity throughout the piece, adding depth and nuance to the musical expression.
Beyond these fundamental elements, composition is influenced by instrumentation, timbre, style, and cultural context, each contributing to its unique identity and impact.
In essence, composition demystified reveals a carefully crafted interplay of form, structure, harmony, rhythm, melody, texture, and dynamics, orchestrated by the composer to evoke emotions, provoke thought, and transport the listener on a journey of the imagination.
The Science Behind Conformal Protection: What Makes It Work?
Conformal protection is used in various industries, notably electronics and aerospace, to safeguard sensitive components from environmental factors such as moisture, dust, chemicals, and physical damage. Its efficacy lies in its ability to provide a conformal coating – a thin layer of protective material – that conforms precisely to the contours of the coated item, ensuring comprehensive coverage and protection. The science behind conformal protection primarily revolves around the properties of the coating material and the application process.
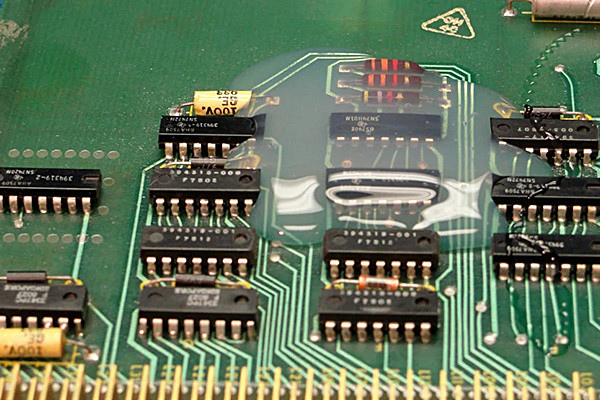
Firstly, the choice of coating material is critical. Common materials include acrylics, silicones, urethanes, and epoxies, each offering unique properties suited to different environmental challenges. For instance, silicone coatings resist moisture and temperature extremes, while acrylics provide excellent dielectric properties. These materials form barriers that shield components from external elements without compromising functionality.
Secondly, the application process is essential for ensuring the efficacy of conformal protection. Various methods, such as spraying, dipping, brushing, or automated dispensing, can be employed based on factors like the size and complexity of the components and the desired coating thickness. Precision is key during application to ensure uniform coverage and avoid bridging, pooling, or uneven coating, which could compromise protection or interfere with component performance.
Additionally, the curing process plays a crucial role in the effectiveness of conformal protection. Most coating materials require curing through heat, UV light, or chemical reactions to achieve their desired properties, such as hardness, adhesion, and resistance to environmental factors. Proper curing ensures that the coating forms a durable, cohesive layer that adheres securely to the substrate, preventing moisture ingress, corrosion, and other forms of damage.
The science behind conformal protection relies on carefully selecting coating materials, precise application techniques, and thorough curing processes. By understanding these principles and applying them effectively, industries can safeguard their critical components and prolong their operational lifespan in challenging environments.
Applications Across Industries: Where Can It Be Utilized?
Conformal protection finds extensive applications across diverse industries where protecting sensitive components from environmental factors is crucial for reliability and longevity. Its versatility and effectiveness make it a preferred choice in various sectors, including electronics, aerospace, automotive, medical devices, and military equipment.
In the electronics industry, conformal coatings are applied to printed circuit boards (PCBs), electronic assemblies, and components to safeguard them from moisture, dust, chemicals, and mechanical stress. These coatings prevent corrosion, electrical shorts, and premature failure, thus enhancing the reliability of electronic devices used in consumer electronics, industrial automation, telecommunications, and more.
Aerospace and aviation industries utilize conformal protection to shield critical avionics, sensors, and electronic systems from harsh conditions during flight, such as high altitude, temperature variations, humidity, and chemical exposure. Conformal coatings ensure the continued operation of aircraft systems, improving safety and reducing maintenance requirements.
In the automotive sector, conformal coatings are applied to electronic control units (ECUs), sensors, and other electrical components to enhance their durability and resistance to temperature fluctuations, vibration, and exposure to road chemicals. This ensures the reliability of vehicle electronics and contributes to overall vehicle performance and safety.
The medical device industry relies on conformal protection to safeguard electronic components in devices such as pacemakers, defibrillators, infusion pumps, and diagnostic equipment. These coatings help maintain the functionality of medical devices in challenging environments, ensuring patient safety and device reliability.
Military and defense applications extensively utilize conformal protection to protect electronics and sensors in military vehicles, weapons systems, communication equipment, and surveillance devices. Conformal coatings enhance the resilience of military electronics to withstand extreme conditions encountered in combat zones and harsh environments.
Moreover, conformal protection is also employed in sectors like marine, oil and gas, renewable energy, and consumer goods, where electronic components are exposed to challenging operating conditions.
The broad range of industries utilizing conformal protection underscores its significance in preserving the integrity and functionality of electronic components across various applications, ensuring reliability, safety, and performance in demanding environments.
Electronics: How Is the Heart of Innovation Protected?
The heart of innovation in electronics is protected through legal frameworks, industry standards, intellectual property rights, and organizational measures to safeguard ideas, inventions, and sensitive information.
Intellectual property (IP) rights are pivotal in protecting innovations in the electronics industry. Patents grant inventors exclusive rights to their creations, preventing others from making, using, or selling the patented technology without permission. Companies invest heavily in obtaining patents to protect their innovative ideas, ensuring they can capitalize on their inventions and maintain a competitive edge.
Trade secrets are another critical component of protecting innovation. Companies guard proprietary information, such as manufacturing processes, algorithms, and formulas, as trade secrets. Confidentiality agreements, restricted access, and encryption techniques shield these from unauthorized access or disclosure.
Moreover, industry standards are a barrier to competitors, as compliance with these standards often necessitates access to specific technologies or methodologies. By contributing to or influencing these standards, companies can shape the industry landscape and maintain their position at the forefront of innovation.
Organizational measures are essential for safeguarding innovation within a company. This includes implementing robust cybersecurity protocols to protect against data breaches and industrial espionage. Employee training programs raise awareness about the importance of confidentiality and instill a culture of innovation protection throughout the organization.
Legal frameworks at national and international levels offer companies recourse for defending their intellectual property rights. Litigation can deter potential infringers and reinforce the value of innovation. Additionally, regulations governing exports and technology transfer help prevent the unauthorized dissemination of sensitive technologies to competitors or adversaries.
Collaboration between industry stakeholders, academia, and government agencies further bolsters innovation protection efforts. Joint research initiatives often involve agreements to protect intellectual property generated during collaboration, ensuring that participants can benefit from their contributions without fear of exploitation.
The heart of innovation in electronics is safeguarded through a multifaceted approach that encompasses legal, technological, and organizational measures. By leveraging intellectual property rights, trade secrets, industry standards, and collaborative partnerships, companies can nurture a culture of innovation while protecting their valuable creations from infringement and theft.
Automotive: What Components Are Shielded?
Various components are shielded in automotive engineering to ensure optimal performance, safety, and vehicle longevity. These shielding measures primarily protect sensitive electronic components, prevent electromagnetic interference (EMI), and mitigate heat-related issues. Let’s explore some of the critical components that are commonly shielded in automobiles:
- Electronic Control Units (ECUs):ECUs are the brains of modern vehicles, controlling various functions such as engine management, transmission, braking, and more. Shielding ECUs from electromagnetic interference is crucial to prevent malfunctions or erroneous signals that could compromise vehicle operation.
- Wiring Harnesses:The wiring harnesses in vehicles carry electrical signals to different components. Shielding these harnesses helps to minimize the risk of EMI affecting signal integrity, which could lead to electrical failures or glitches in various systems.
- Sensors:Sensors are vital in monitoring speed, temperature, pressure, and proximity. Shielding sensors from external interference ensures accurate readings and reliable performance, enhancing overall vehicle safety and efficiency.
- Ignition System:Shielding components of the ignition system, such as spark plug wires and ignition coils, helps prevent interference that could disrupt the ignition process, leading to engine misfires or reduced performance.
- Radio Frequency (RF) Components:With the proliferation of wireless communication systems in vehicles (e.g., keyless entry, tire pressure monitoring), shielding RF components becomes essential to prevent interference with other electronic systems and external signals.
- Heat Shields:While not directly related to EMI, heat shields protect sensitive components from excessive heat generated by the engine, exhaust system, or nearby components. This helps maintain optimal operating temperatures and prevents thermal damage or premature wear.
- Fuel System:Certain components, such as fuel lines and tanks, may also be shielded to avoid external factors from compromising fuel quality or causing leaks.
Shielding various automotive components is essential for maintaining the integrity and reliability of vehicle systems. By protecting against electromagnetic interference and heat-related issues, these measures contribute to the overall performance, safety, and durability of modern automobiles.
Aerospace: How Is Reliability Ensured in the Skies?
Reliability in aerospace is paramount, given the industry’s critical nature. Several stringent measures ensure safety and reliability in the skies.
- Stringent Regulations: Regulatory bodies like the Federal Aviation Administration (FAA) in the United States or the European Aviation Safety Agency (EASA) set rigorous standards that aerospace companies must meet. These regulations cover every aspect of aircraft design, manufacturing, maintenance, and operation.
- Design and Testing: Aerospace companies invest heavily in research, development, and testing phases. Aircraft undergo extensive simulations, wind tunnel tests, and prototype evaluations to identify and rectify potential issues before they enter service.
- Quality Control: Quality management systems ensure that each component meets precise specifications. Advanced technologies such as non-destructive testing and automated inspection systems help detect even minor defects.
- Maintenance Programs: Strict maintenance schedules and protocols ensure aircraft remain in optimal condition throughout their operational life. Regular inspections, preventive maintenance, and component replacements are carried out according to established guidelines.
- Monitoring and Data Analysis: Airlines employ sophisticated systems tracking real-time aircraft performance. Data analytics are used to identify trends, predict maintenance needs, and prevent failures before they occur.
- Pilot Training and Safety Protocols: Pilots undergo rigorous training to handle various scenarios, including emergencies. Standard operating procedures (SOPs) and checklists ensure that protocols are followed consistently, minimizing the risk of human error.
- Redundancy and Fail-Safe Systems: Aircraft are designed with redundant systems to ensure continued operation in case of component failure. Critical systems often have multiple backups, and fail-safe mechanisms are implemented to prevent catastrophic failures.
- Continuous Improvement: The aerospace industry is constantly evolving, with lessons learned from incidents and accidents leading to improvements in design, technology, and safety protocols. Feedback mechanisms ensure that best practices are shared and implemented across the industry.
Reliability in aerospace is achieved through stringent regulations, rigorous testing, quality control measures, comprehensive maintenance programs, advanced monitoring systems, pilot training, redundancy, and continuous improvement efforts. These measures work together to ensure the safety and reliability of aircraft in the skies.
Medical Devices: How Are Precision and Performance Preserved?
In medical devices, ensuring precision and performance is paramount to guaranteeing effective diagnosis, treatment, and patient safety. Preserving precision and performance involves a multifaceted approach encompassing design, manufacturing, testing, and ongoing monitoring.
- Design Phase: The foundation for precision and performance begins during the design phase. Thorough research, analysis of user requirements, and adherence to regulatory standards are essential. Design considerations include materials selection, ergonomic factors, and compatibility with other medical equipment.
- Quality Manufacturing: Precision and performance are upheld through stringent manufacturing processes. Utilizing advanced technologies such as computer-aided design (CAD) and computer numerical control (CNC) machining ensures accuracy and consistency in production. Quality control measures, including rigorous testing and inspections, are integrated at every manufacturing stage to identify and rectify any deviations from specifications.
- Regulatory Compliance: Compliance with regulatory standards such as ISO 13485 and FDA regulations is obligatory for medical device manufacturers. Adherence to these standards ensures that devices meet strict safety, efficacy, and performance criteria. Regular audits and assessments are conducted to verify compliance and promptly address non-conformities.
- Validation and Verification: Thorough validation and verification processes confirm that devices meet predetermined specifications and perform as intended. This involves comprehensive testing under simulated and real-world conditions to assess functionality, accuracy, and reliability. Feedback from clinical trials and user evaluations further validates device performance.
- Continuous Improvement: Continuous monitoring and feedback mechanisms enable manufacturers to identify opportunities for enhancement. Post-market surveillance, including adverse event reporting systems, facilitates the detection of any issues or shortcomings in device performance. Iterative design refinements and updates are implemented based on collected data and user feedback to optimize precision and performance continually.
- Training and Support: Ensuring healthcare professionals are adequately trained in operating and maintaining medical devices is crucial. Training programs and support resources manufacturers equip users with the knowledge and skills to utilize devices effectively, thereby preserving precision and performance in clinical settings.
By integrating these principles into every stage of the medical device lifecycle, manufacturers uphold the standards necessary to preserve precision and performance, ultimately safeguarding patient outcomes and well-being.
Marine: How Are the Elements Confronted?
The confrontation of elements within marine ecosystems is a perpetual dance of balance and adaptation, shaped by intricate relationships between the environment’s living and non-living components. Four primary elements—water, air, Earth, and sunlight—interact dynamically, influencing marine life’s abundance, distribution, and diversity.
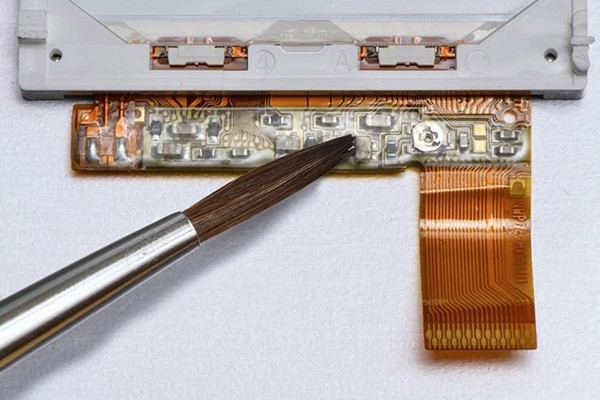
Water, the fundamental medium of marine environments, acts as a conduit for life processes and a habitat for myriad organisms. Its physical properties, such as temperature, salinity, and currents, significantly influence marine life. From the microscopic plankton to the giant whales, organisms have evolved unique physiological adaptations to thrive within the varying conditions of marine waters.
Although seemingly separate from the marine realm, air interacts intimately through atmospheric phenomena like wind patterns and storms. Oxygen exchange at the air-water interface supports aerobic respiration in aquatic organisms, while atmospheric circulation drives ocean currents that shape marine habitats and influence nutrient distribution.
In the form of the seabed and coastal zones, Earth provides substrate and shelter for marine life. From coral reefs teeming with biodiversity to the abyssal plains inhabited by strange deep-sea creatures, the geological features of the ocean floor shape ecosystems and determine the distribution of species.
Sunlight is the primary energy source driving photosynthesis in marine plants and algae, forming the base of the aquatic food web. Light penetration varies with water depth and clarity, influencing the distribution of photosynthetic organisms and, consequently, the entire ecosystem’s productivity.
Interactions between these elements create dynamic ecosystems with complex feedback loops. For example, temperature influences ocean currents, affecting climate patterns and ultimately influencing temperature again. Likewise, changes in one element can have cascading effects throughout the marine environment, such as alterations in water temperature impacting coral bleaching events.
Human activities, however, are increasingly disrupting these delicate balances. Pollution, overfishing, habitat destruction, and climate change are altering marine ecosystems at an unprecedented rate, threatening the resilience of life within them. Recognizing the interconnectedness of the elements within marine environments is crucial for devising sustainable management strategies to mitigate these impacts and preserve the richness of life beneath the waves.
Renewables: How Is Sustainability Enhanced?
Sustainability in renewable energy encompasses various principles aimed at reducing environmental impact, conserving resources, and fostering long-term viability. Several key strategies enhance sustainability within renewables, contributing to a cleaner, more resilient energy future.
- Reducing Greenhouse Gas Emissions: Renewable energy sources such as solar, wind, hydro, and geothermal power emit little to no greenhouse gases during electricity generation, unlike fossil fuels. By transitioning away from carbon-intensive energy sources, renewables help mitigate climate change and reduce overall environmental impact.
- Resource Conservation: Unlike finite fossil fuels, renewable energy sources are replenishable and abundant. Harnessing solar energy, for instance, relies on the sun’s inexhaustible radiation, while wind power utilizes the Earth’s atmospheric circulation. By tapping into these renewable resources, societies can conserve finite resources and reduce dependence on environmentally harmful extraction methods.
- Promoting Energy Independence: By diversifying energy sources and reducing reliance on imported fossil fuels, renewable energy enhances energy security and independence. Communities and nations can mitigate geopolitical risks associated with fossil fuel dependencies while fostering local economic development through domestic renewable energy infrastructure investment.
- Encouraging Technological Innovation: Pursuing renewable energy fosters innovation across various sectors, driving advancements in energy storage, grid integration, and efficiency. Continued research and development in renewable technologies enhance their performance, affordability, and scalability, making them increasingly competitive alternatives to fossil fuels.
- Creating Green Jobs and Economic Opportunities: The renewable energy sector offers substantial employment opportunities, ranging from manufacturing and installation to research and development. Governments and businesses stimulate job growth by investing in renewables while reducing environmental degradation and public health risks associated with traditional energy production.
- Enhancing Environmental Stewardship: Renewable energy projects can be designed and implemented with careful consideration for environmental conservation and ecosystem protection. Practices such as responsible siting, habitat restoration, and wildlife-friendly infrastructure minimize negative impacts on biodiversity, ensuring that renewable energy development aligns with broader sustainability objectives.
By embracing these principles and advancing renewable energy technologies, societies can foster a more sustainable energy landscape that meets current needs without compromising the well-being of future generations.
Benefits Beyond Protection: What Sets Silicone Apart?
Silicone, a versatile material with many applications, offers benefits beyond mere protection. Its unique properties make it stand out in various industries, from healthcare to consumer products. Here are some key reasons why silicone is unparalleled:
- Flexibility and Durability: Silicone’s inherent flexibility allows it to withstand extreme temperatures without losing its structural integrity. This durability makes it ideal for use in diverse environments, from cold to scorching heat, without degrading or becoming brittle.
- Chemical Resistance: Unlike many other materials, silicone exhibits remarkable resistance to chemicals, oils, and solvents. This property makes it suitable for applications where exposure to harsh substances is daily, such as medical devices, industrial equipment, and kitchenware.
- Biocompatibility: Silicone’s biocompatibility makes it widely used in medical and healthcare products. It is non-toxic, hypoallergenic, and does not support microbial growth, reducing the risk of infections. Medical-grade silicone is frequently employed in implants, prosthetics, catheters, and other surgical tools.
- Non-Stick Surface: Silicone’s non-stick surface properties make it an excellent choice for cookware, bakeware, and food storage containers. Its smooth texture prevents food from sticking, simplifying cooking and cleanup processes while reducing the need for excessive oil or grease.
- Electrical Insulation: Silicone’s high dielectric strength and electrical insulation properties make it indispensable in the electronics industry. It is used in cables, connectors, seals, and gaskets to protect delicate electronic components from moisture, dust, and electrical interference.
- Versatility and Moldability: Silicone can be easily molded into complex shapes with precision, allowing customized designs tailored to specific applications. Its versatility extends to various industries, including automotive, aerospace, cosmetics, and construction.
- Environmental Sustainability: Silicone’s durability and recyclability contribute to its eco-friendliness. It can endure long-term use and be recycled at the end of its lifecycle, reducing environmental impact and promoting sustainability.
Silicone’s exceptional properties go beyond mere protection, making it a preferred choice across industries for its versatility, durability, biocompatibility, and environmental sustainability. Its unique combination of characteristics drives innovation and enhances product performance in numerous applications.
Flexibility: Can It Bend Without Breaking?
Flexibility is one of silicone’s defining characteristics, allowing it to bend and deform without breaking. This property stems from silicone’s molecular structure and the way its polymer chains interact, making it exceptionally pliable compared to many other materials. Here’s how silicone achieves its remarkable flexibility:
- Polymer Structure: Silicone is composed of silicon atoms bonded with oxygen atoms, forming a backbone structure known as a siloxane chain. This highly flexible chain enables silicone to bend and stretch without rupturing. Additionally, organic side groups, such as methyl or phenyl groups, along the siloxane backbone enhance flexibility by reducing intermolecular forces.
- Cross Linking: Silicone polymers can undergo crosslinking, where adjacent polymer chains form covalent bonds, creating a three-dimensional network. Crosslinking strengthens the material while preserving its flexibility. Depending on the degree of crosslinking, silicone products can exhibit varying levels of flexibility, from soft and pliable to firm and resilient.
- Temperature Resistance: Silicone’s flexibility remains consistent across a wide temperature range, from extreme cold to high heat. Unlike many materials that become brittle in low temperatures or soften excessively in high temperatures, silicone maintains its elasticity and shape stability, making it suitable for applications in diverse environmental conditions.
- Tensile Strength: Despite its flexibility, silicone exhibits impressive tensile strength, meaning it can withstand stretching forces without tearing. This combination of flexibility and strength makes silicone well-suited for applications requiring resilience and durability, such as in seals, gaskets, and flexible tubing.
- Fatigue Resistance: Silicone’s molecular structure imparts excellent fatigue resistance, allowing it to endure repeated bending and flexing without undergoing mechanical failure. This property is essential for dynamic stress or cyclic loading applications, ensuring prolonged reliability and longevity.
Silicone’s ability to bend without breaking is attributed to its unique polymer structure, crosslinking capabilities, temperature resistance, tensile strength, and fatigue resistance. This inherent flexibility makes silicone an invaluable material across industries, enabling the development of products that can withstand deformation and movement without compromising performance or integrity.
Thermal Stability: How Does It Keep Cool Under Pressure?
Silicone’s exceptional thermal stability enables it to maintain its coolness under pressure, making it an invaluable material in applications where heat resistance is paramount. This property arises from several vital factors inherent to silicone’s molecular structure and composition:
- High Heat Resistance: Silicone exhibits outstanding resistance to elevated temperatures, remaining stable and retaining its mechanical properties even when exposed to extremes of heat. This heat resistance is due to the strength and stability of the silicon-oxygen (Si-O) bonds in the polymer backbone, which can withstand temperatures far beyond those tolerated by many organic materials without degrading or melting.
- Low Thermal Conductivity: Silicone has relatively low thermal conductivity compared to metals and other polymers. This means that heat energy does not readily transfer through silicone materials, allowing them to insulate against high temperatures and maintain cooler temperatures on the opposite side. This property is particularly advantageous in applications where thermal insulation is necessary to protect sensitive components or prevent heat transfer.
- Inertness to Thermal Expansion: Silicone’s low coefficient of thermal expansion contributes to its ability to stay calm under pressure. When subjected to temperature fluctuations, silicone expands and contracts minimally, minimizing the risk of thermal stress and ensuring dimensional stability. This inertness to thermal expansion makes silicone well-suited for applications requiring tight tolerances and precise engineering, such as automotive gaskets, electronic enclosures, and industrial seals.
- Resistance to Thermal Degradation: Unlike many organic polymers, silicone is highly resistant to thermal degradation, meaning it does not break down or decompose when exposed to high temperatures over prolonged periods. This resilience ensures silicone-based products’ long-term performance and reliability in demanding thermal environments, such as engine components, cooking utensils, and aerospace applications.
Silicone’s ability to stay calm under pressure stems from its high heat resistance, low thermal conductivity, inertness to thermal expansion, and resistance to thermal degradation. These properties make silicone a preferred choice for applications requiring thermal stability, insulation, and reliability in challenging operating conditions.
Chemical Resistance: Can It Defy Corrosive Forces?
Chemical resistance refers to a material’s ability to withstand the deteriorative effects of chemical substances. It is crucial in various industries, including manufacturing, construction, and healthcare. Materials with high chemical resistance can defy corrosive forces, ensuring durability, safety, and performance in challenging environments.
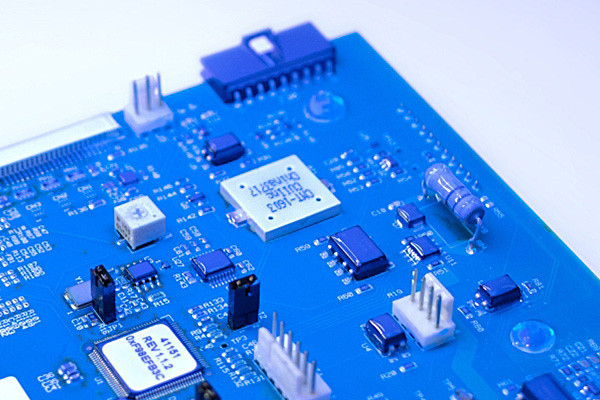
Polymers, metals, ceramics, and composites can exhibit varying degrees of chemical resistance. Polymers like polyethylene, polypropylene, and fluoropolymers are often used in applications requiring resistance to acids, bases, solvents, and other corrosive substances. These materials form tight molecular structures that prevent chemical penetration, thereby resisting degradation.
Metals such as stainless steel, titanium, and nickel alloys are renowned for their corrosion resistance. This property arises from passivation, a process where a thin oxide layer forms on the metal surface, acting as a protective barrier against further corrosion. Additionally, alloying elements can enhance corrosion resistance by altering the material’s microstructure and chemical properties.
Ceramics possess exceptional chemical resistance due to their inertness and hardness. Materials like alumina, zirconia, and silicon carbide are used in corrosive environments where metals and polymers would fail. Their crystalline structure and lack of porosity make them impervious to chemical attack, offering long-term stability and reliability.
Composites of two or more materials with distinct properties can be tailored to exhibit superior chemical resistance. Fiberglass-reinforced plastics (FRP), carbon fiber composites, and ceramic matrix composites are engineered for specific chemical environments. Composites can balance strength, stiffness, and chemical inertness by combining different constituents.
The resistance of a material to corrosion depends on factors such as temperature, concentration, and exposure duration of the corrosive substance. Proper material selection, based on a thorough understanding of environmental conditions, is essential to ensure optimal performance and longevity.
Chemical resistance enables materials to defy corrosive forces by preventing degradation and maintaining structural integrity in harsh environments. Whether in industrial processing, infrastructure, or medical devices, materials with high chemical resistance play a vital role in ensuring safety, reliability, and sustainability.
Moisture Barrier: How Does It Keep Intruders at Bay?
A moisture barrier is a protective layer or material designed to prevent moisture intrusion into a given space, structure, or product. It plays a crucial role in various applications, including construction, packaging, and electronics manufacturing. By effectively blocking moisture ingress, moisture barriers help maintain the integrity, functionality, and longevity of the protected items.
Moisture barriers utilize a variety of mechanisms to keep intruders, such as water vapor, liquid water, or humidity, at bay. One common approach is using impermeable materials that physically prevent moisture from passing through. Materials like plastic films, rubber membranes, and metal foils are commonly employed as moisture barrier layers due to their low permeability to water vapor.
Another strategy involves incorporating desiccants or moisture-absorbing materials within the barrier structure. Desiccants such as silica gel or molecular sieves absorb moisture in the surrounding environment, reducing humidity levels and preventing moisture intrusion. This approach is particularly effective in packaging applications where maintaining a dry environment is critical for preserving the quality of sensitive goods, such as electronics or pharmaceuticals.
Furthermore, moisture barriers may rely on coatings or treatments that enhance the surface’s hydrophobic or oleophobic properties. These coatings repel water and other liquids, preventing them from penetrating the underlying substrate. Examples include water-resistant paints, sealants, and fluoropolymer coatings on surfaces like walls, roofs, or electronic circuit boards.
In construction, moisture barriers are commonly installed in building envelopes to protect against water infiltration, leading to structural damage, mold growth, and indoor air quality issues. Vapor barriers, typically made of polyethylene or asphalt-impregnated paper, are installed in walls, floors, and ceilings to limit the movement of water vapor through building materials.
Moisture barriers employ various techniques, such as impermeable membranes, desiccants, and surface treatments, to keep moisture intruders at bay. Whether in packaging, construction, or electronics, these barriers play a critical role in safeguarding against the damaging effects of moisture, ensuring the longevity, performance, and quality of protected items or structures.
UV Resistance: How Does It Shield Against Solar Assault?
UV resistance refers to the ability of materials to withstand the damaging effects of the sun’s ultraviolet (UV) radiation. Solar assault, in this context, refers to the harmful impacts of UV radiation on various surfaces and materials, including plastics, textiles, coatings, and even human skin.
UV radiation is part of the electromagnetic spectrum emitted by the sun, along with visible light and infrared radiation. While UV radiation only accounts for a small fraction of the sun’s total output, it carries significant energy that can cause molecular damage when absorbed by certain materials.
Materials that lack UV resistance can degrade and undergo a range of detrimental effects when exposed to prolonged sunlight. These effects include discoloration, fading, embrittlement, cracking, and structural degradation. For example, unprotected plastics may become brittle and break, while fabrics can lose color and strength over time.
UV resistance is achieved through various means, including UV stabilizers, pigments, and protective coatings. UV stabilizers are chemical additives that absorb or dissipate UV radiation, preventing it from reaching sensitive materials. These additives can be incorporated into the material during manufacturing or applied as surface coatings.
Pigments are another standard method of UV protection. They can absorb and scatter UV radiation, reducing its penetration into the material. By selecting UV-resistant pigments, manufacturers can enhance the durability and lifespan of their products.
Protective coatings are a barrier between the material and the sun, shielding it from direct UV exposure. These coatings may contain UV-blocking agents or reflective particles that deflect UV radiation from the surface.
UV resistance plays a crucial role in safeguarding materials against the damaging effects of solar assault. By incorporating UV stabilizers, pigments, and protective coatings, manufacturers can enhance the longevity and performance of various products exposed to sunlight, ensuring they remain durable and aesthetically pleasing.
Cost-Effectiveness: How Are Budgets and Performance Balanced?
Cost-effectiveness is critical in managing budgets and performance within any organization, whether a business, non-profit, or government agency. Achieving a balance between budgets and performance involves several vital strategies.
Firstly, setting clear and realistic performance goals is essential. These goals should be specific, measurable, achievable, relevant, and time-bound (SMART). By defining clear objectives, organizations can focus their resources on activities that directly contribute to achieving those goals, maximizing cost-effectiveness.
Secondly, regular monitoring and evaluation of performance metrics are crucial. This involves tracking key performance indicators (KPIs) to assess progress toward goals and identify areas where resources may need to be more effectively allocated. By continuously evaluating performance, organizations can make timely adjustments to their strategies to ensure that budgets are aligned with priorities and deliver maximum value.
Furthermore, cost-effectiveness can be enhanced through strategic resource allocation. This involves prioritizing investments in activities or projects that offer the highest return on investment (ROI) to achieve organizational objectives. Organizations can optimize their budget allocations and maximize performance outcomes by directing resources toward high-impact initiatives.
In addition, fostering a culture of efficiency and innovation can help improve cost-effectiveness. Encouraging employees to identify opportunities for process improvements, cost savings, and innovation can lead to more efficient operations and better performance outcomes. Moreover, investing in training and development programs can enhance employee skills and capabilities, further contributing to organizational effectiveness.
Effective communication and collaboration across departments are also essential for balancing budgets and performance. By fostering transparency and collaboration, organizations can ensure that resources are allocated based on strategic priorities and that performance goals are aligned across different functional areas.
Achieving a balance between budgets and performance requires a strategic approach that involves setting clear goals, monitoring performance, strategically allocating resources, fostering efficiency and innovation, and promoting collaboration. Organizations can maximize cost-effectiveness and achieve their desired outcomes by implementing these strategies.
Environmental Considerations: Is It Eco-Friendly Protection?
Eco-friendly protection” refers to practices, policies, and technologies that aim to safeguard the environment while achieving various objectives such as conservation, sustainability, and mitigation of environmental harm. Several factors must be considered when assessing whether a particular form of protection is eco-friendly.
- Impact Assessment: A thorough evaluation of the environmental impact of the protection measures is essential. This includes assessing potential harm to ecosystems, biodiversity, air and water quality, and soil health. Measures that minimize negative impacts or benefit the environment are considered more eco-friendly.
- Resource Efficiency: Eco-friendly protection strategies prioritize efficiently using resources such as energy, water, and raw materials. This may involve adopting renewable energy sources, implementing recycling and waste reduction measures, and optimizing resource consumption to minimize environmental footprint.
- Sustainability: Sustainable practices ensure that protection measures meet present needs without compromising the ability of future generations to meet their own needs. This involves considering the long-term effects of protection strategies on environmental health, resilience, and capacity for regeneration.
- Carbon Footprint: Evaluating the carbon footprint associated with protection measures is crucial in determining eco-friendliness. Strategies that reduce greenhouse gas emissions, such as promoting low-carbon transportation, implementing energy-efficient technologies, and conserving natural carbon sinks like forests, are considered more environmentally friendly.
- Adaptation and Resilience: Eco-friendly protection should also enhance the resilience of ecosystems and communities to environmental stressors and climate change impacts. This may involve restoring degraded habitats, conserving biodiversity, and implementing nature-based solutions that provide natural defenses against environmental risks.
- Social and Economic Considerations: Environmental protection measures should consider social equity and economic viability. Strategies that give co-benefits to local communities, such as creating green jobs, improving public health, and promoting equitable access to resources, contribute to a more sustainable and eco-friendly approach.
Eco-friendly protection involves adopting measures that minimize environmental harm, maximize resource efficiency, promote sustainability, reduce carbon emissions, enhance resilience, and consider social and economic factors. Organizations and governments can safeguard the environment by integrating these principles into protection strategies while achieving their objectives.
Challenges and Considerations: How Is the Terrain Navigated?
Navigating terrain involves many challenges and considerations, ranging from natural features to human-made obstacles. The approach to navigating terrain depends on various factors such as the terrain type, the purpose of navigation, available resources, and technological advancements. Here are some key considerations and challenges:
- Terrain Type: Terrain can vary widely, from rugged mountains to dense forests, barren deserts, and urban landscapes. Each type presents its challenges, requiring different strategies and equipment for navigation.
- Topography: Understanding the topography is crucial for successful navigation. This includes knowledge of elevation, slopes, valleys, ridges, and water bodies. Topographic maps and GPS technology are valuable tools for assessing and planning routes.
- Weather Conditions: Weather can significantly impact navigation, affecting visibility, terrain stability, and accessibility. Factors such as rain, snow, fog, and extreme temperatures can pose challenges and require adjustments to navigation plans.
- Obstacles and Hazards: Terrain may contain natural barriers like cliffs, rivers, swamps, and thick vegetation, as well as human-made hazards such as fences, roads, and buildings. Negotiating these obstacles safely often requires specialized skills and equipment.
- Navigation Techniques: Various navigation techniques are employed depending on the terrain and available resources. These may include map reading, compass navigation, GPS navigation, dead reckoning, celestial navigation, and terrain association.
- Resource Management: Navigating terrain efficiently requires careful management of food, water, fuel, and equipment. Long expeditions or traversals of challenging terrain may necessitate strategic planning and resupply points.
- Safety and Risk Management: Safety is paramount when navigating terrain, particularly in remote or hazardous environments. Assessing risks, maintaining communication, and having contingency plans are essential for minimizing accidents and responding to emergencies.
- Environmental Impact: Navigating terrain responsibly involves minimizing ecological impact. This includes adhering to Leave No Trace principles, respecting wildlife habitats, and avoiding activities that could cause environmental damage.
- Technological Advancements: Technology advancements, such as GPS navigation, satellite imagery, drones, and GIS mapping, have revolutionized terrain navigation, offering greater precision, efficiency, and safety.
- Training and Experience: Ultimately, successful terrain navigation often depends on the skills, knowledge, and experience of individuals or teams. Training in orienteering, survival skills, first aid, and outdoor leadership is invaluable for navigating diverse terrain effectively.
Conclusion
In conclusion, silicone conformal coating emerges as a shield and a guardian of innovation, reliability, and longevity. Its ability to adapt, endure, and protect in the face of diverse challenges underscores its significance across industries. From intricate circuitry to expansive aerospace systems, silicone conformal coating applications continue redefining the boundaries of protection and performance. As we navigate the ever-evolving landscape of technology and industry, one thing remains sure: silicone conformal coating will continue to play a pivotal role in safeguarding our advancements and shaping the future of innovation.
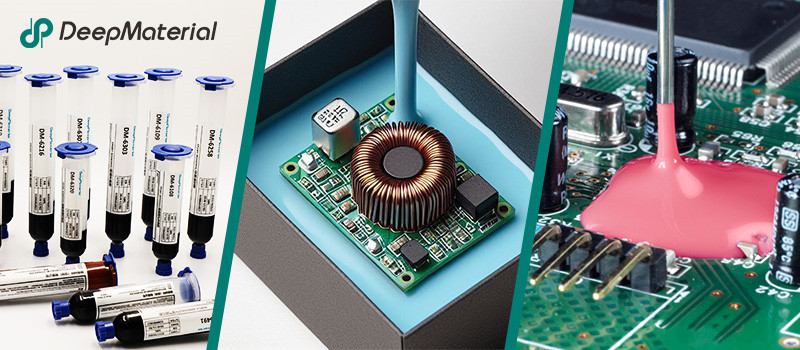
About DeepMaterial
DeepMaterial is a trusted supplier of encapsulant materials that are used in electronics manufacturing worldwide. From chip on board encapsulants such as glob top material to conformal coatings, underfills, low pressure molding, and potting solutions, DeepMaterial offers a full range of circuit board protection materials that effectively protect circuit boards while help reduce costs. More…Deepmaterial is a the manufacturer of epoxy adhesives including hardeners, metalbond, and metal filled resins. Structural, toughened medium viscosity, and non-sag adhesives are also offered. Some adhesives are resistant to thermal shock, chemical, vibration dampening, and impact. Suitable for metals, plastics, wood, and ceramics. Serves electronics, aerospace, automotive, tooling, marine, and construction industries. REACH and RoHS compliant. FDA approved. UL listed. Meets military specifications. We are the one of best adhesive manufacturers in China.
Blogs & News
Potting compounds are at the frontline of electronics assembly, delivering effective protection in challenging environmental conditions while improving mechanical strength and offering high electric insulation. Used within a variety of industries, electrical potting compounds are found within a broad range of consumer electronics, as well as used in applications across the automotive, aerospace, and other industries where electronic assemblies are prevalent.
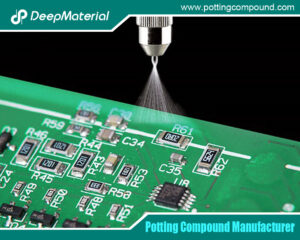
The Ultimate Guide to Electrical Potting Compound and Market Application
The Ultimate Guide to Electrical Potting Compound and Market Application In the modern world of electronics, where devices are increasingly compact and exposed to harsh
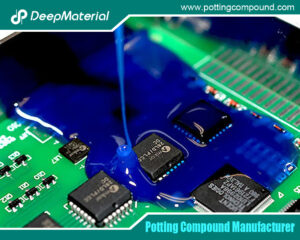
The Top Polyurethane Potting Compound
The Top Polyurethane Potting Compound In the fast-evolving world of electronics and industrial manufacturing, protecting sensitive components from environmental hazards is critical to ensuring reliability
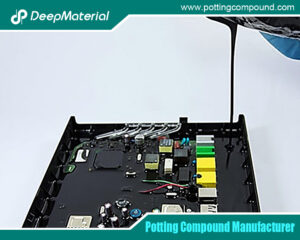
Advanced Epoxy Potting Compound for Superior Electronic Protection
Advanced Epoxy Potting Compound for Superior Electronic Protection In the realm of electronics and industrial manufacturing, protecting sensitive components from environmental hazards is critical to
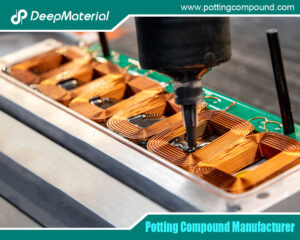
Waterproof Potting Compound: A Comprehensive Guide
Waterproof Potting Compound: A Comprehensive Guide In today’s technology-driven world, protecting sensitive electronic components from environmental hazards is paramount. One of the most effective solutions
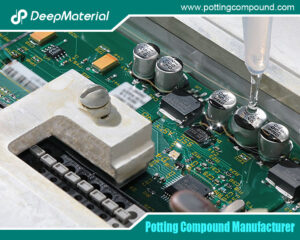
Silicone Potting Compound for Electronics
Silicone Potting Compound for Electronics In the rapidly evolving world of electronics, ensuring the reliability, durability, and performance of electronic components is paramount. One critical
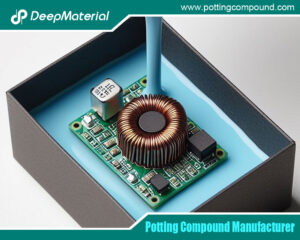
Potting Compound vs. Epoxy: A Comprehensive Comparison
Potting Compound vs. Epoxy: A Comprehensive Comparison In the world of electronics, manufacturing, and material encapsulation, two terms frequently come up: potting compounds and epoxy.