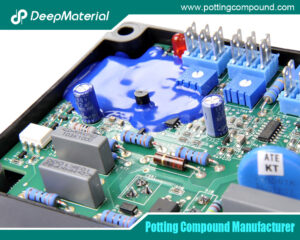
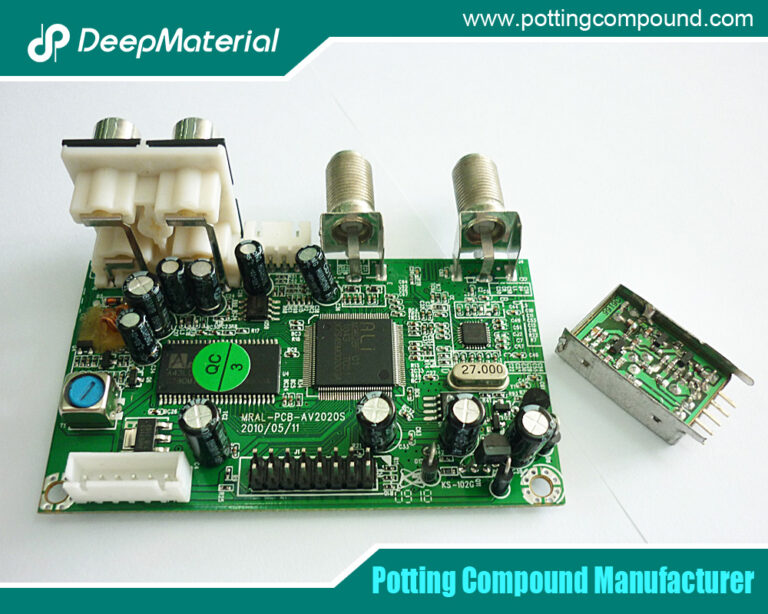
Silicone Potting Compound for Electronics: Uses, Benefits, and Applications
- Electronic Potting Material Manufacturer
- August 5, 2024
- Automotive potting material manufacturers, Benefits of Potting Electronics, circuit board potting compound, Connector Potting Compound, customize china electronic potting silicone manufacturer, deepmaterial PCB Potting, deepmaterial potting compound, electrical potting compound, electronic encapsulant potting compounds, electronic epoxy encapsulant potting compounds, electronic potting compound, Electronic Potting Compounds Manufacturer, encapsulant potting compounds, Encapsulants and Potting Compounds Suppliers, epoxy encapsulant potting compounds, epoxy potting compound, epoxy potting compound manufacturers, Flexible Potting Compound, LED Potting Compound, PCB Potting Compound and Conformal Coating Adhesive, polyurethane potting compound, Silicone Potting Compound, silicone potting compound for electronics
Silicone Potting Compound for Electronics: Uses, Benefits, and Applications
In electronics manufacturing, ensuring electronic components’ durability, reliability, and longevity is paramount. One critical method to achieve these goals is using silicone potting compounds. These compounds, known for their versatility and protective properties, are crucial in safeguarding sensitive electronic parts from environmental hazards such as moisture, dust, vibrations, and thermal stress. This article delves into the intricacies of silicone potting compounds, exploring their composition, uses, benefits, application methods, and considerations for selecting suitable compounds for various electronic applications.
- What is Silicone Potting Compound?
The silicone potting compound is an encapsulant that protects electronic components by encasing them in a solid material. Composed primarily of silicone polymers, these compounds are formulated to provide excellent environmental protection while maintaining electrical insulation properties. They are available in various forms, including room temperature vulcanizing (RTV) silicones, heat-cured silicones, and two-part silicones, each offering unique advantages depending on the application requirements.
1.1 Types of Silicone Potting Compounds
- RTV Silicones:Room-temperature vulcanizing silicones cure at ambient temperatures and are convenient for applications where heat curing is impractical. They offer flexibility and good adhesion to a variety of substrates.
- Heat-Cured Silicones:These compounds require elevated temperatures to cure fully. They are preferred for applications with a higher degree of mechanical strength and thermal stability.
- Two-Part Silicones:Consisting of a base and a curing agent, two-part silicones provide precise control over curing time and properties. They are suitable for complex or large-scale potting applications.
1.2 Properties of Silicone Potting Compounds
Silicone potting compounds exhibit several fundamental properties that make them ideal for electronic protection:
- Electrical Insulation:Silicones have inherently high dielectric strength, making them effective insulators that prevent electrical leakage and breakdown.
- Thermal Conductivity:Some formulations of silicone potting compounds offer good thermal conductivity, helping to dissipate heat generated by electronic components, thereby improving their reliability and lifespan.
- Flexibility and Durability:Silicones maintain flexibility over a wide temperature range, ensuring they can accommodate thermal expansion and contraction without cracking or compromising the seal.
- Chemical Resistance:They resist moisture, chemicals, and environmental contaminants, shielding electronic components from corrosive agents and prolonging their operational life.
- Uses of Silicone Potting Compound
Silicone potting compounds find widespread use across various industries and applications where the protection of electronic components is critical:
2.1 Consumer Electronics: In devices such as LED drivers, power supplies, and control modules, silicone potting compounds provide moisture protection and enhance reliability, which is crucial for consumer product longevity.
2.2 Automotive Electronics: In automotive applications, where electronics are exposed to extreme temperatures, vibrations, and moisture, silicone potting compounds ensure stable performance and longevity of critical components like sensors, ECUs (Electronic Control Units), and ignition systems.
2.3 Aerospace and Defense: In aerospace and defence sectors, where electronics must endure harsh environmental conditions, including high altitude, temperature extremes, and mechanical shock, silicone potting compounds offer robust protection to avionic controls, radar systems, and communication equipment.
2.4 Industrial Applications: Silicone potting compounds provide insulation against electrical interference and protection from industrial contaminants for industrial electronics used in manufacturing automation, robotics, and machinery control.
2.5 Renewable Energy: Silicone potting compounds safeguard electronics in solar inverters, wind turbine controls, and battery management systems from weather elements, UV radiation, and thermal cycling, ensuring reliable performance in renewable energy applications.
- Benefits of Silicone Potting Compound
Silicone potting compounds offer several benefits that contribute to their widespread adoption in electronics manufacturing:
3.1 Environmental Protection: The primary function of silicone potting compounds is to provide a barrier against moisture, dust, chemicals, and other environmental contaminants. This protection extends the operational life of electronic components, reducing the risk of failure due to environmental factors.
3.2 Thermal Management: Some silicone formulations exhibit excellent thermal conductivity, facilitating efficient heat dissipation from electronic components. This property is crucial in preventing overheating and maintaining optimal operating temperatures, enhancing reliability.
3.3 Mechanical Stability: Silicone potting compounds form a durable, resilient encapsulation around electronic assemblies, offering mechanical protection against physical shocks, vibrations, and mechanical stresses during handling or operation.
3.4 Electrical Insulation: With high dielectric strength and low dissipation factor, silicone potting compounds effectively insulate electronic circuits, preventing electrical leakage and breakdown, even in high-voltage applications.
3.5 Chemical Resistance: They resist degradation from exposure to oils, solvents, and other chemicals, maintaining their integrity and protective properties over extended periods.
- Application Methods
Achieving optimal performance from silicone potting compounds requires careful consideration of application methods:
4.1 Surface Preparation: Proper cleaning and priming of surfaces are essential to ensure adhesion and eliminate contaminants that could compromise the bond between the substrate and the potting compound.
4.2 Mixing and Dispensing: For two-part silicone compounds, accurate mixing ratios and thorough blending are critical to achieve uniform curing and desirable physical properties in the cured material.
4.3 Curing Techniques: The curing method—whether room temperature curing or heat curing—should be selected based on the specific requirements of the application, including production volume, time constraints, and desired properties of the cured material.
4.4 Considerations for Large-Scale Production: In high-volume manufacturing environments, automated dispensing systems may ensure consistent application and minimise material waste, optimising efficiency and cost-effectiveness.
- Factors to Consider When Choosing Silicone Potting Compounds
Selecting the appropriate silicone potting compound involves evaluating several vital factors to match the compound’s properties with the specific requirements of the application:
5.1 Environmental Conditions: Consider the operating environment, including temperature extremes, exposure to moisture or chemicals, UV radiation, and mechanical stresses.
5.2 Compatibility: Ensure compatibility with substrates, electronic components, and other materials used in the assembly to prevent adverse reactions or performance issues.
5.3 Physical Properties: Determine the desired flexibility or rigidity, thermal conductivity, and mechanical strength to meet the application’s performance requirements.
5.4 Regulatory Compliance: Verify that the selected silicone compound meets relevant industry standards and regulatory requirements, such as UL ratings, RoHS (Restriction of Hazardous Substances), and REACH (Registration, Evaluation, Authorization, and Restriction of Chemicals).
5.5 Cost Considerations: Balance performance requirements with budget constraints, considering material costs, processing costs, and long-term maintenance savings.
- Case Studies and Practical Examples
Real-world applications illustrate the effectiveness of silicone potting compounds in enhancing electronic reliability and longevity:
6.1 Case Study: LED Lighting SystemsIn LED driver modules for outdoor lighting applications, silicone potting compounds protect sensitive electronics from moisture ingress, thermal cycling, and UV exposure, ensuring prolonged operational life and consistent performance.
6.2 Case Study: Automotive SensorsSilicone potting compounds used in automotive sensors maintain signal integrity and reliability under harsh conditions of temperature variations, mechanical vibrations, and exposure to automotive fluids, contributing to vehicle safety and performance.
6.3 Case Study: Renewable Energy SystemsIn solar inverters and battery management systems, silicone potting compounds provide thermal management and environmental protection, enabling reliable operation in outdoor environments subjected to weather extremes and UV radiation.
- Challenges and Considerations
While silicone potting compounds offer significant advantages, several challenges should be considered during application and deployment:
7.1 Bubble Formation: Improper mixing or inadequate degassing can lead to the formation of air bubbles within the cured silicone, compromising its electrical insulation properties and mechanical strength.
7.2 Adhesion Issues: Proper surface preparation and selecting appropriate primers are crucial to achieving strong adhesion between the potting compound and substrate materials.
7.3 Shelf-Life and Storage Conditions:Silicone compounds have a finite shelf life and may require specific storage conditions (e.g., temperature-controlled environments) to maintain their properties before use.
7.4 Overcoming Application Constraints: Special dispensing techniques or customized formulations may be necessary for applications with complex geometries or delicate components to achieve uniform coverage and effective encapsulation.
- Future Trends in Silicone Potting Compounds
The evolution of silicone potting compounds continues to be driven by technological advancements and industry trends:
8.1 Enhanced Formulations: Ongoing research focuses on developing silicone formulations with improved thermal conductivity, flexibility, and sustainability, meeting the evolving needs of modern electronics.
8.2 Integration with Smart Technologies: Silicone potting compounds are increasingly integrated with intelligent electronics and IoT devices, where reliability, miniaturisation, and environmental resilience are critical for long-term performance.
8.3 Sustainability Initiatives: There is a growing emphasis on eco-friendly silicone formulations that minimise environmental impact through reduced emissions, energy-efficient production processes, and recyclability.
Conclusion
Silicone potting compounds protect electronic components from environmental hazards, ensuring their reliability and longevity across diverse applications. By providing effective insulation, mechanical stability, and thermal management, these compounds contribute significantly to the performance and durability of electronics in consumer products, automotive systems, aerospace technologies, and renewable energy solutions. As technologies evolve and demand for more robust electronic solutions grows, silicone potting compounds will continue to advance, meeting the challenges of tomorrow’s electronic designs with innovative formulations and enhanced performance capabilities.
For more about choosing the Top Silicone Potting Compound for Electronics: Uses, Benefits, and Applications, you can pay a visit to DeepMaterial at https://www.pottingcompound.com/ for more info.
Recent Posts
- Influence of Encapsulation Thickness on the Heat Dissipation Performance and Electrical Insulation Performance of PCB
- Causes and Avoidance Methods of Bubble Generation in the Potting Process
- Technical Details on Controlling Parameters such as Temperature, Pressure, and Speed in the Potting Process to Ensure Potting Quality
- A Comprehensive Analysis of PCB Pretreatment Before Potting Process: A Crucial Link to Ensure the Performance and Reliability of Electronic Devices
- A Comprehensive Analysis of the Performance Differences of Epoxy Resin, Silicone Rubber and Polyurethane Encapsulation Materials
- How to Select Suitable Potting Materials for PCB According to the Working Environment
- What is PCB Potting
- The Evolution of Smart Watch Assembly Adhesive: A Key Component in Modern Wearable Technology
- Laptop Tablet Assembly Adhesive: The Key to Durable and Reliable Device Construction
- Power Bank Assembly Adhesive: The Essential Component for Building Durable Power Banks