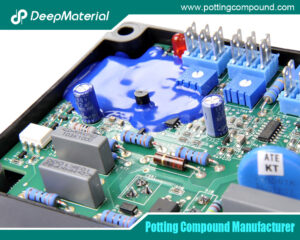
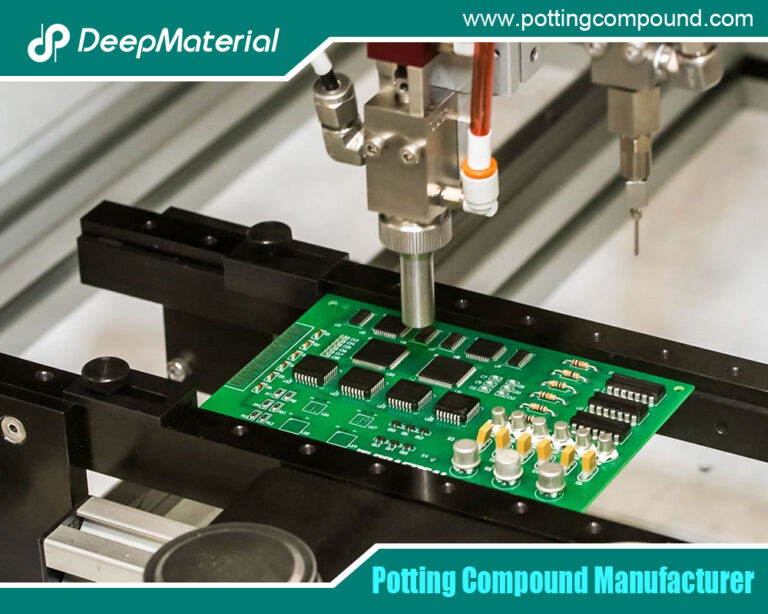
Silicone Sealant Manufacturers: An In-Depth Look
- Electronic Potting Material Manufacturer
- August 2, 2024
- acrylic vs silicone conformal coating, china electronic potting silicone manufacturer, china electronic potting silicone supplier, conformal coating for pcb, conformal coating silicone, customize china electronic potting silicone factories, customize china electronic potting silicone manufacturer, electronic epoxy encapsulant potting compounds, electronic potting silicone, electronic potting silicone china fabrication, electronic potting silicone china manufacturing, electronic potting silicone manufacturer, electronic potting silicone manufacturers china, electronic potting silicone products china companies, electronic potting silicone supplier, epoxy encapsulation electronic components, Industrial Potting Silicones Specialist Supplier, industrial silicone adhsive glue, ossila encapsulation epoxy, potting compound vs epoxy, Silicone Conformal Coating, silicone electronic adhesive glue, silicone epoxy adhesive glue, Silicone Potting Compound, Silicone Sealant Manufacturer
Silicone Sealant Manufacturers: An In-Depth Look
Silicone sealants are a type of adhesive widely used in various industries due to their excellent properties, such as flexibility, durability, and resistance to moisture and extreme temperatures. They are crucial in applications ranging from construction to electronics, automotive, and household repairs. The global market for silicone sealants has seen significant growth, driven by increasing demand in the construction and automotive sectors, among others. This article delves into the world of silicone sealant manufacturers, highlighting the major players, production processes, market trends, and prospects.
Major Players in the Silicone Sealant Industry
The silicone sealant industry is dominated by several vital manufacturers who have established themselves through innovation, quality, and extensive distribution networks. Some of the prominent manufacturers include:
Dow Corning (now Dow Inc.)
Dow Corning, now part of Dow Inc., has led the silicone industry for decades. Its silicone sealants are known for their superior quality and performance. Dow’s products are used in various applications, including construction, automotive, aerospace, and electronics. The company’s commitment to research and development has led to the introduction of advanced sealant solutions catering to specific industry needs.
Momentive Performance Materials
Momentive is another major player in the silicone sealant market. With a rich history and a strong focus on innovation, Momentive offers sealants designed for multiple applications. Their products are renowned for their durability and reliability, making them a preferred choice in construction, transportation, and electronics industries.
Shin-Etsu Chemical Co., Ltd.
Shin-Etsu Chemical, a Japanese multinational, is a leading manufacturer of silicone products, including sealants. It has a significant presence in the global market and offers high-quality silicone sealants used in the construction, automotive, and electronic industries. Shin-Etsu’s dedication to quality and innovation has made it a trusted name in the silicone industry.
Wacker Chemie AG
Wacker Chemie, a German chemical company, is known for its high-performance silicone sealants. Their products are widely used in construction and industrial applications. Wacker’s extensive research and development efforts have resulted in a range of sealants that meet the demanding requirements of various industries.
Sika AG
Sika, a Swiss specialty chemical company, provides a wide range of construction and industrial products, including silicone sealants. Their sealants are known for their excellent adhesion, flexibility, and resistance to environmental factors. Sika’s global presence and commitment to sustainability make them a key player in the silicone sealant market.
Production Process of Silicone Sealants
The production of silicone sealants involves several critical steps, ensuring the final product meets the required standards for performance and safety. The primary components of silicone sealants are silicone polymers, fillers, cross-linkers, and various additives. Here’s a brief overview of the production process:
Polymerization
The production begins with the polymerization of siloxanes to create silicone polymers. This process involves the reaction of silicon, oxygen, carbon, and hydrogen atoms, forming long chains of silicone molecules. These polymers are the backbone of silicone sealants, providing the essential properties of flexibility and durability.
Formulation
The silicone polymer is mixed with various fillers, cross-linkers, and additives in the formulation stage. Fillers such as silica enhance the sealant’s mechanical properties, while cross-linkers facilitate the curing process, transforming the sealant from a liquid to a solid state. Additives like adhesion promoters and UV stabilisers are included to improve the sealant’s performance under specific conditions.
Mixing and Compounding
The ingredients are thoroughly mixed and compounded to ensure a homogeneous blend. This step is crucial for achieving consistent quality and performance in the final product. Advanced mixing equipment and techniques eliminate air bubbles and achieve the desired viscosity and texture.
Packaging
After mixing, the sealant is packaged in various forms, such as cartridges, tubes, or bulk containers, depending on the application requirements. The packaging process is automated to ensure efficiency and accuracy, with quality control measures in place to inspect the final product.
Curing
The curing process involves exposing the sealant to moisture, heat, or ultraviolet (UV) light, depending on the type of sealant. This step transforms the sealant from a pliable state to a solid, elastic form. The curing time can vary based on the formulation and environmental conditions, but it typically ranges from a few hours to several days.
Market Trends and Applications
The silicone sealant market has grown significantly, driven by several key trends and increasing demand in various applications. Here are some of the notable trends and applications:
Construction Industry
The construction industry is the largest consumer of silicone sealants. These sealants are used in glazing, weatherproofing, and structural bonding applications. Their ability to withstand extreme temperatures, UV exposure, and moisture makes them ideal for interior and exterior use. The growing emphasis on energy-efficient buildings and green construction practices has further boosted the demand for high-performance silicone sealants.
Automotive Industry
In the automotive sector, silicone sealants seal and bond components, providing protection against moisture, dust, and vibrations. Their insulating properties are also crucial in electronic components and sensors. The rise of electric vehicles (EVs) has increased the demand for silicone sealants, essential for ensuring the reliability and safety of battery systems and electronic components.
Electronics Industry
Silicone sealants are critical in the electronics industry, providing insulation and protection for sensitive components. They are used in sealing enclosures, potting and encapsulating electronic assemblies, and protecting against environmental factors. The growth of the electronics industry, driven by advancements in technology and increasing demand for consumer electronics, has significantly contributed to the silicone sealant market.
Medical and Healthcare
The medical and healthcare sectors also utilise silicone sealants for various applications, including medical devices, prosthetics, and wound care. Silicone’s biocompatibility, flexibility, and resistance to sterilisation processes make it an ideal material for these applications. The increasing focus on healthcare and medical advancements has spurred this sector’s demand for high-quality silicone sealants.
Challenges and Future Prospects
While the silicone sealant market is poised for continued growth, several challenges and prospects need to be considered:
Raw Material Availability and Cost
The availability and cost of raw materials used in silicone sealants, such as silicon and other chemicals, can impact the final product’s overall production cost and pricing. Fluctuations in raw material prices and supply chain disruptions can challenge manufacturers.
Environmental and Regulatory Compliance
Manufacturers must comply with stringent environmental regulations and standards, especially concerning emissions of volatile organic compounds (VOCs). Developing eco-friendly and sustainable sealant formulations is a key focus area for the industry, aligning with global efforts to reduce environmental impact.
Technological Advancements
Technological and material science advancements continue to drive innovation in the silicone sealant industry. Manufacturers are investing in research and development to create sealants with enhanced properties, such as improved adhesion, faster curing times, and more excellent resistance to environmental factors. These innovations will open new opportunities and applications for silicone sealants.
Market Expansion
Emerging markets in Asia-Pacific, Latin America, and the Middle East are witnessing rapid industrialization and urbanisation, driving the demand for silicone sealants. Expanding into these regions presents significant growth opportunities for manufacturers. Additionally, the increasing adoption of silicone sealants in niche applications, such as renewable energy and aerospace, will further fuel market expansion.
Conclusion
Silicone sealant manufacturers are crucial in providing high-performance solutions for various industries. The market is characterised by continuous innovation, with manufacturers striving to meet their customers’ evolving demands. Despite challenges related to raw material availability, environmental regulations, and market competition, the future of the silicone sealant industry looks promising. With ongoing technological advancements and the expanding scope of applications, silicone sealants will continue to be indispensable in construction, automotive, electronics, healthcare, and beyond.
As industries evolve and new applications emerge, silicone sealant manufacturers will remain at the forefront of delivering reliable, durable, and sustainable solutions, driving progress and innovation across the globe.
For more about choosing the Top Silicone Sealant Manufacturers: An In-Depth Look, you can pay a visit to DeepMaterial at https://www.pottingcompound.com/ for more info.
Recent Posts
- Influence of Encapsulation Thickness on the Heat Dissipation Performance and Electrical Insulation Performance of PCB
- Causes and Avoidance Methods of Bubble Generation in the Potting Process
- Technical Details on Controlling Parameters such as Temperature, Pressure, and Speed in the Potting Process to Ensure Potting Quality
- A Comprehensive Analysis of PCB Pretreatment Before Potting Process: A Crucial Link to Ensure the Performance and Reliability of Electronic Devices
- A Comprehensive Analysis of the Performance Differences of Epoxy Resin, Silicone Rubber and Polyurethane Encapsulation Materials
- How to Select Suitable Potting Materials for PCB According to the Working Environment
- What is PCB Potting
- The Evolution of Smart Watch Assembly Adhesive: A Key Component in Modern Wearable Technology
- Laptop Tablet Assembly Adhesive: The Key to Durable and Reliable Device Construction
- Power Bank Assembly Adhesive: The Essential Component for Building Durable Power Banks