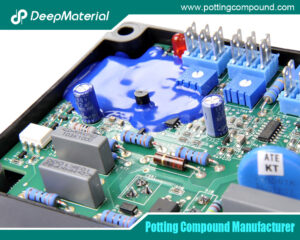
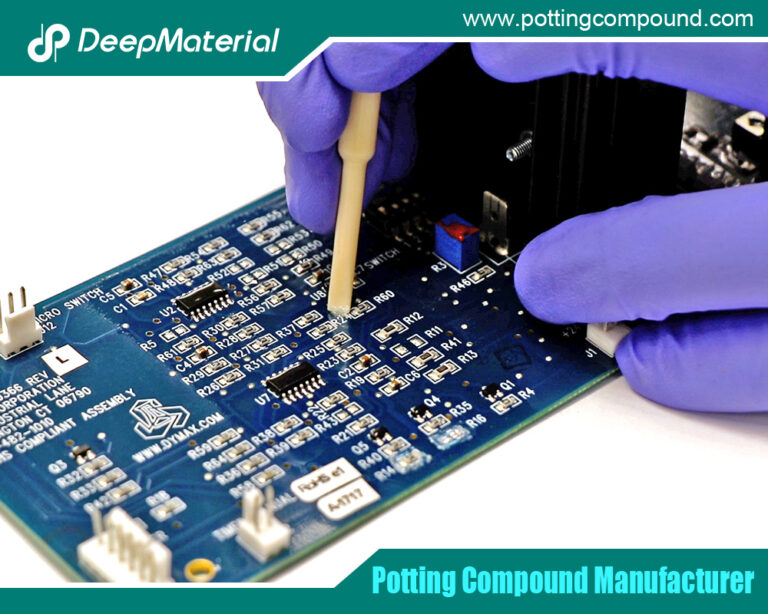
Solutions for Electrical Insulation with Epoxy Resins
- Electronic Potting Material Manufacturer
- August 12, 2024
- adhesive glue manufacturer, conformal coating waterproof, Electrical Insulation with Epoxy Resins, electrical potting compound, electronic epoxy encapsulant potting compounds, epoxy encapsulation, epoxy encapsulation electronic components, epoxy encapsulation for photovolatics and oleds, epoxy encapsulation led, epoxy encapsulation meaning, epoxy encapsulation molding compound, epoxy potting compound, epoxy potting compound manufacturers, Epoxy potting material manufacturers, Epoxy Resin, epoxy resin encapsulation, epoxy resin encapsulation solar panels, industrial adhesive suppliers, ossila encapsulation epoxy, pcb encapsulation epoxy, polyurethane potting compound, polyurethane potting compound for electronics, potting compound vs epoxy, potting material for electronic components, potting material for electronics, silicone potting compound for electronics, UV curing potting compound
Solutions for Electrical Insulation with Epoxy Resins
Electrical insulation is critical in various industries, mainly electrical and electronics engineering. The need to prevent unwanted electrical currents, protect components from environmental factors, and ensure overall system reliability makes insulation an essential consideration. Among the various materials used for insulation, epoxy resins have emerged as a highly effective solution. This article explores the role of epoxy resins in electrical insulation, their advantages, applications, and prospects.
Introduction to Epoxy Resins
Epoxy resins are a class of thermosetting polymers known for their strong adhesive properties, chemical resistance, and excellent mechanical performance. They are formed through a reaction between epoxide resin and a polyamine hardener. When cured, the resulting material forms a rigid, durable structure that withstands various environmental conditions.
Epoxy resins have become famous for electrical insulation due to their superior electrical properties, including high dielectric strength, low dielectric constant, and excellent resistance to electrical tracking and arcing. Additionally, epoxy resins can be formulated to provide specific properties such as enhanced thermal conductivity or flexibility, making them versatile for various insulation applications.
Advantages of Epoxy Resins for Electrical Insulation
- High Dielectric Strength: Epoxy resins exhibit high dielectric strength, which allows them to withstand high voltage without breaking down. This property is crucial for insulating high-voltage equipment and preventing electrical failures.
- Thermal Stability: Epoxy resins can maintain their insulating properties over a wide temperature range. This thermal stability makes them suitable for applications in harsh environments with common temperature fluctuations.
- Chemical Resistance: Epoxy resins highly resist chemicals, including acids, alkalis, and solvents. This resistance ensures that the insulation remains effective even in chemically aggressive environments.
- Mechanical Strength: The cured epoxy resin forms a rigid, durable material with excellent mechanical properties. This strength helps protect the insulated components from physical damage and mechanical stress.
- Moisture Resistance: Epoxy resins have low water absorption and excellent moisture resistance. This property is fundamental in preventing electrical shorts and insulation degradation in humid or wet conditions.
- Customizability: Epoxy resins can be formulated with various fillers and additives to tailor their properties to specific applications. This customizability allows for the development of specialised insulation solutions.
Applications of Epoxy Resins in Electrical Insulation
Transformers
Transformers are critical components in electrical power systems. They step voltage levels up or down to meet the needs of different stages of power distribution. The insulation of transformers must withstand high voltages, thermal cycling, and environmental exposure.
Epoxy resins are used to insulate transformer windings and core assemblies. The resin is applied as a liquid and then cured to form a solid, insulating barrier. This insulation provides electrical isolation and helps dissipate heat generated during operation, enhancing the efficiency and longevity of transformers.
Printed Circuit Boards (PCBs)
Printed circuit boards (PCBs) are the backbone of electronic devices, providing the foundation for mounting and interconnecting electronic components. Electrical insulation is vital to prevent short circuits and ensure the PCBs’ reliable operation.
Epoxy resins are commonly used as solder masks and encapsulants on PCBs. The solder mask is a layer of epoxy resin that covers the PCB, protecting the conductive traces from oxidation, moisture, and mechanical damage. Epoxy encapsulants cover sensitive components, protecting against environmental factors and mechanical stress.
Cable Jointing and Terminations
In electrical power distribution, cable jointing and terminations are critical points that require effective insulation to prevent faults and ensure safety. Epoxy resins are used to create insulating barriers at cable joints and terminations.
The resin is applied as a liquid, allowing it to flow into gaps and irregular surfaces, ensuring a complete and uniform insulation layer. Once cured, the epoxy resin provides robust mechanical and electrical protection, maintaining the integrity of the cable connections.
Motors and Generators
Motors and generators rely on effective insulation to ensure efficient and reliable operation. The insulation must withstand high temperatures, mechanical stresses, and environmental exposure.
Epoxy resins are used to insulate motors and generators’ windings. The resin is applied as an impregnating varnish or encapsulant, providing a solid, protective layer around the windings. This insulation enhances the motors and generators’ electrical performance, thermal stability, and mechanical durability.
Encapsulation and Potting
Encapsulation and potting are processes used to protect electronic components and assemblies by encasing them in a solid, insulating material. Epoxy resins are widely used due to their excellent electrical and mechanical properties.
In encapsulation, the electronic component is fully enclosed in epoxy resin, protecting against moisture, dust, chemicals, and mechanical damage. Potting involves filling a housing or enclosure with epoxy resin to protect the contained components. These processes are used in various applications, including sensors, connectors, and power supplies.
Future Prospects of Epoxy Resins in Electrical Insulation
The use of epoxy resins in electrical insulation is expected to grow, driven by advancements in material science and increasing demand for reliable and efficient electrical systems. Several trends and developments are likely to shape the future of epoxy resins in insulation applications:
- Advanced Formulations: Ongoing research is focused on developing epoxy resins with enhanced properties, such as higher thermal conductivity, improved flexibility, and excellent resistance to environmental factors. These advanced formulations will create more efficient and durable insulation solutions.
- Nanotechnology: Incorporating nanomaterials into epoxy resins is a promising area of research. Nanomaterials can significantly improve epoxy resins’ electrical, thermal, and mechanical properties, leading to better performance and reliability in insulation applications.
- Sustainability: As environmental concerns grow, an increasing focus is on developing eco-friendly epoxy resins. Bio-based resins, derived from renewable sources, are being explored as sustainable alternatives to traditional petroleum-based resins.
- Innovative Insulation: Integrating smart technologies into insulation systems is an emerging trend. Epoxy resins with embedded sensors and monitoring capabilities can provide real-time data on the condition of the insulation, allowing for predictive maintenance and early detection of potential issues.
- 3D Printing: The use of 3D printing technology to create custom insulation components from epoxy resins is gaining traction. This approach allows for precise control over the design and properties of the insulation, enabling the development of highly specialised solutions.
Conclusion
Epoxy resins have proven invaluable for electrical insulation. They offer a range of properties that ensure the reliability, efficiency, and longevity of electrical systems. Their high dielectric strength, thermal stability, chemical resistance, and mechanical durability make them ideal for various applications, from transformers and PCBs to cable joints and motors.
As technology advances and new challenges emerge, developing advanced epoxy resin formulations, incorporating nanomaterials, focusing on sustainability, integrating intelligent technologies, and adopting 3D printing is expected to drive the future of electrical insulation solutions. By leveraging these innovations, epoxy resins will play a pivotal role in the safe and efficient operation of electrical and electronic systems.
For more about choosing the Solutions for Electrical Insulation with Epoxy Resins, you can pay a visit to DeepMaterial at https://www.pottingcompound.com/ for more info.
Recent Posts
- Influence of Encapsulation Thickness on the Heat Dissipation Performance and Electrical Insulation Performance of PCB
- Causes and Avoidance Methods of Bubble Generation in the Potting Process
- Technical Details on Controlling Parameters such as Temperature, Pressure, and Speed in the Potting Process to Ensure Potting Quality
- A Comprehensive Analysis of PCB Pretreatment Before Potting Process: A Crucial Link to Ensure the Performance and Reliability of Electronic Devices
- A Comprehensive Analysis of the Performance Differences of Epoxy Resin, Silicone Rubber and Polyurethane Encapsulation Materials
- How to Select Suitable Potting Materials for PCB According to the Working Environment
- What is PCB Potting
- The Evolution of Smart Watch Assembly Adhesive: A Key Component in Modern Wearable Technology
- Laptop Tablet Assembly Adhesive: The Key to Durable and Reliable Device Construction
- Power Bank Assembly Adhesive: The Essential Component for Building Durable Power Banks