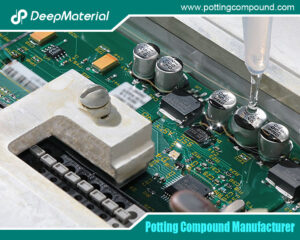
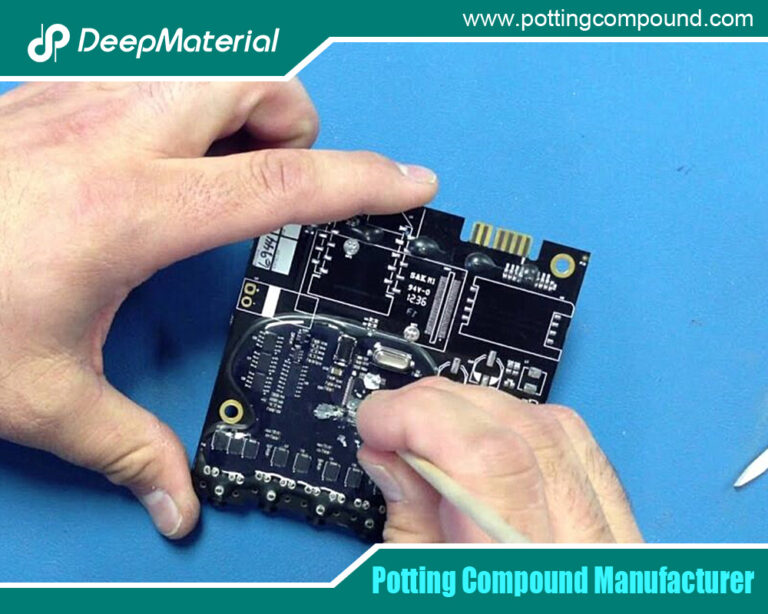
Solutions for Electrical Insulation with Epoxy Resins
- Electronic Potting Material Manufacturer
- September 12, 2024
- Acrylic Conformal Coating, acrylic vs silicone conformal coating, circuit board potting compound, conformal coating for pcb, Conformal Coating in Electronic, conformal coating material, conformal coating overspray, conformal coating pcb, conformal coating silicone, conformal coating waterproof, Connector Potting Compound, deepmaterial potting compound, electrical insulation coating, Electrical Insulation with Epoxy Resins, electrical potting compound, Encapsulant Potting Compound, epoxy coating for electrical insulation, Epoxy Encapsulant Potting Compound, epoxy powder coating for electrical insulation, Epoxy Powder for Electrical Insulation, Epoxy Resin, epoxy resin encapsulation, epoxy resin encapsulation solar panels, high temperature electrical insulation coating, potting compound, uv conformal coating, uv conformal coating manufacturer
Solutions for Electrical Insulation with Epoxy Resins
Electrical insulation is a critical component in the design and functionality of electrical systems, ensuring the safe and efficient operation of electrical components and devices. Epoxy resins have emerged as a popular solution for electrical insulation due to their superior properties, including high dielectric strength, mechanical robustness, and excellent thermal stability. This article explores the various solutions for electrical insulation using epoxy resins, highlighting their benefits, applications, and considerations for selecting the appropriate resin.
1. Understanding Epoxy Resins
1.1 What are Epoxy Resins?
Epoxy resins are a class of synthetic polymers derived from the reaction of epoxide compounds with curing agents. They are known for their strong adhesive properties, chemical resistance, and versatility. The basic structure of epoxy resins includes a backbone of epoxy groups (-C-O-C-), which can cross-link with other molecules during the curing process, forming a three-dimensional network that enhances their mechanical and electrical properties.
1.2 Types of Epoxy Resins
There are several types of epoxy resins used in electrical insulation, including:
- Bisphenol-A Epoxy Resins:The most commonly used type, known for its excellent electrical insulation properties and mechanical strength.
- Novolac Epoxy Resins:Characterized by higher thermal stability and chemical resistance, they are suitable for demanding environments.
- Cycloaliphatic Epoxy Resins:Known for their superior UV resistance and low viscosity, they are ideal for outdoor applications.
2. Critical Properties of Epoxy Resins for Electrical Insulation
2.1 Dielectric Strength
One of the most essential properties of epoxy resins for electrical insulation is their high dielectric strength, which measures the material’s ability to withstand electrical stress without breaking down. Epoxy resins typically exhibit dielectric strengths ranging from 10 to 30 kV/mm, making them suitable for high-voltage applications.
2.2 Thermal Stability
Epoxy resins offer excellent thermal stability, with some formulations capable of operating at temperatures up to 200°C. This property is crucial for electrical insulation in high-temperature environments, ensuring the resin maintains its insulating properties and mechanical integrity over time.
2.3 Mechanical Strength
Epoxy resins’ mechanical strength, including tensile strength, impact resistance, and hardness, contributes to their effectiveness as electrical insulators. Their cross-linked structure provides durability and resistance to mechanical stress, making them suitable for applications where physical protection is required.
2.4 Chemical Resistance
Epoxy resins resist various chemicals, including solvents, acids, and alkalis. This property is essential for electrical insulation in environments where exposure to chemicals is likely, ensuring that the resin does not degrade or lose its insulating properties.
2.5 Adhesive Properties
Epoxy resins have strong adhesive properties, allowing them to bond effectively with different substrates, including metals, plastics, and ceramics. This characteristic benefits applications where the insulation must adhere firmly to the electrical components or substrates.
3. Applications of Epoxy Resins in Electrical Insulation
3.1 Electrical Insulation of Winding Coils
Epoxy resins are widely used to insulate winding coils in electrical transformers, motors, and generators. The resin is typically applied as a coating or impregnating material to protect the copper windings from electrical, thermal, and mechanical stresses. The cured epoxy provides a robust insulation layer that enhances the performance and longevity of the winding coils.
3.2 Insulation of Printed Circuit Boards (PCBs)
Epoxy resins are essential in manufacturing printed circuit boards (PCBs). They are the substrate material and the insulating layer between different circuit elements. The resin provides electrical insulation, mechanical support, and protection against environmental factors, ensuring the reliable operation of electronic devices.
3.3 Electrical Encapsulation
Encapsulation is when electrical components or assemblies are surrounded by epoxy resin to provide insulation and protection. This application is expected in electronic devices, sensors, and connectors, where the resin acts as a barrier against moisture, dust, and mechanical damage.
3.4 Insulation of Electrical Connectors and Terminals
Epoxy resins insulate electrical connectors and terminals, preventing electrical shorts and ensuring reliable connections. The resin is typically applied as a coating or encapsulating material to protect the connectors from environmental factors and mechanical wear.
3.5 High-Voltage Insulation
Epoxy resins insulate cables, busbars, and other electrical components in high-voltage applications. The resin’s high dielectric strength and thermal stability make it suitable for insulating high-voltage systems, ensuring safety and preventing electrical breakdowns.
4. Considerations for Selecting Epoxy Resins for Electrical Insulation
4.1 Electrical Requirements
The selection of epoxy resin for electrical insulation should be based on the application’s specific electrical requirements. Consider factors such as dielectric strength, insulation resistance, and voltage rating to ensure that the resin can withstand electrical stress without degradation.
4.2 Thermal Conditions
Evaluate the application environment’s thermal conditions to select an epoxy resin with appropriate thermal stability. Consider operating temperature, thermal cycling, and heat dissipation to ensure the resin maintains its insulating properties under varying temperatures.
4.3 Mechanical and Chemical Exposure
Assess the mechanical and chemical exposure that the epoxy resin will encounter. Choose a resin with adequate mechanical strength and chemical resistance to withstand the environmental conditions and prevent premature failure.
4.4 Curing Process
The curing process of epoxy resins can vary depending on the formulation and application method. Some resins require heat to cure, while others cure at room temperature. Consider the curing requirements and ensure the chosen resin is compatible with the manufacturing process and application.
4.5 Cost and Availability
Finally, consider the cost and availability of the epoxy resin. While high-performance resins may offer superior properties, they may also be more expensive. Balance the performance requirements with the cost constraints to select the most suitable resin for the application.
Conclusion
Epoxy resins offer a versatile and effective solution for electrical insulation, providing excellent dielectric strength, thermal stability, and mechanical durability. Their wide range of applications, from insulating winding coils and PCBs to encapsulating electronic components and high-voltage systems, underscores their importance in the electrical and electronics industries. When selecting epoxy resins for electrical insulation, it is crucial to consider factors such as electrical requirements, thermal conditions, mechanical and chemical exposure, curing process, and cost. By understanding these factors and choosing the appropriate resin, manufacturers and engineers can ensure the reliability and safety of their electrical systems.
For more about choosing the top solutions for electrical insulation with epoxy resins, you can pay a visit to DeepMaterial at https://www.pottingcompound.com/ for more info.
Recent Posts
- Silicone Potting Compound for Electronics
- Potting Compound vs. Epoxy: A Comprehensive Comparison
- Potting Compound for PCB
- In – depth Analysis of the Curing Characteristics of Electronic Potting Compounds
- A Comprehensive Analysis of the Environmental Performance of Encapsulating Materials: From Regulations to Practices
- A Comprehensive Analysis of PCB Encapsulation Quality Inspection: Innovative Application of Non-Destructive Testing Technologies
- Analysis of the Improvement of the Seismic and Impact Resistance Performance of PCB by Encapsulation
- A Comprehensive Guide to Evaluating the Reliability of Encapsulation Materials for Encapsulated PCBs
- In-depth Analysis of the Reparability of Encapsulation Materials
- A Comprehensive Analysis of Post-Potting PCB Issues and the Repair and Rework of Potting Materials