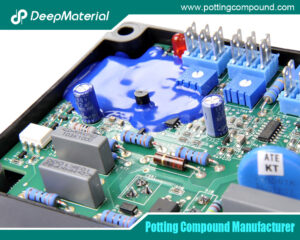
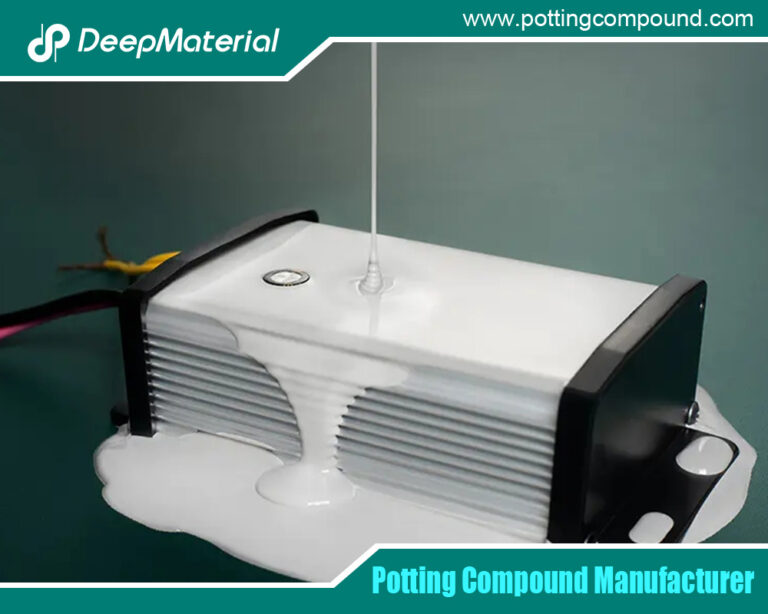
The Expanding Low VOC Conformal Coating Market: Trends, Benefits, and Challenges
- Electronic Potting Material Manufacturer
- November 6, 2024
- Acrylic Conformal Coating, adhesive glue manufacturer, conformal coating for electronics, conformal coating for pcb, conformal coating for pcb standards, conformal coating material, conformal coating pcb, conformal coating process, conformal coating silicone, conformal coating spray, conformal coating types, conformal coating waterproof, deepmaterial conformal coating, deepmaterial epoxy adhesive glue, deepmaterial PCB Potting, deepmaterial potting compound, Electronic Conformal Coating, epoxy conformal coating, industrial adhesive suppliers, Industrial Conformal Coating, Low VOC Conformal Coating, Low VOC Conformal Coating China Hotsale, Low VOC Conformal Coating China Wholesale, Low VOC Conformal Coating Factory Hotsale, Low VOC Conformal Coating Factory OEM, Low VOC Conformal Coating Market, pcb conformal coating, Silicone Conformal Coating, Urethane Conformal Coating, UV Cure Conformal Coating, Waterproof Conformal Coating
The Expanding Low VOC Conformal Coating Market: Trends, Benefits, and Challenges
The electronics industry is continually evolving, with new technologies requiring innovative solutions to ensure the longevity and reliability of devices. Conformal coatings have become critical in protecting sensitive electronic components from environmental damage. However, with increasing awareness about the ecological and health impacts of volatile organic compounds (VOCs), there has been a growing demand for low-VOC alternatives.
The low VOC conformal coating market is witnessing significant growth, driven by stringent regulations, rising consumer demand for environmentally friendly products, and advancements in coating technologies. In this blog post, we will explore the low VOC conformal coatings market, its importance, the key trends driving its growth, the challenges it faces, and what the future holds for this burgeoning industry.
What are Conformal Coatings?
Conformal coatings are protective films applied to electronic components to safeguard them from environmental hazards such as moisture, chemicals, dust, and extreme temperatures. These coatings are used in thin layers to ensure protection without compromising the components’ functionality.
Types of Conformal Coatings
Acrylic Coatings are popular due to their ease of application and reworkability. They also offer good moisture and insulation properties.
- Silicone Coatings:Known for their flexibility and thermal resistance, they are often used in high-temperature environments.
- Polyurethane Coatings:These provide excellent abrasion and chemical resistance, making them ideal for rugged environments.
- Epoxy Coatings:Offering superior adhesion and chemical resistance, they are often used in environments with harsh chemicals.
VOCs in Conformal Coatings
Traditionally, many conformal coatings contain VOCs, chemicals that evaporate into the atmosphere, contributing to air pollution and potentially harming human health. Common VOCs found in coatings include solvents that help in the application and drying. However, as environmental concerns and health risks have become more prominent, there has been a shift towards low VOC alternatives.
Why Low VOC Conformal Coatings Matter
Environmental Impact
VOCs contribute to air pollution, leading to the formation of ground-level ozone and smog. By reducing VOC content in conformal coatings, manufacturers are minimizing environmental degradation.
Health and Safety Benefits
- Reduced Health Risks:VOCs are linked to respiratory problems, headaches, and other health issues for workers applying the coatings. Low VOC coatings minimize these risks.
- Safer Work Environments:Low VOC coatings improve indoor air quality, ensuring safer working conditions for individuals involved in the application process.
Regulatory Compliance
Governments worldwide are imposing stricter regulations on VOC emissions. The European Union’s REACH regulation and the United States Environmental Protection Agency (EPA) have set stringent limits on VOC content in various products. Adopting low-VOC conformal coatings ensures compliance with these evolving regulations.
Sustainability Goals
The global shift towards sustainability has prompted industries to adopt greener practices. Low VOC conformal coatings align with these goals, offering environmentally friendly alternatives to traditional solvent-based coatings. Companies increasingly focus on reducing their carbon footprint, and switching to low VOC products is a significant step in that direction.
Key Market Trends
Growth in the Electronics Industry
The rise in demand for consumer electronics, automotive electronics, and IoT (Internet of Things) devices is driving the need for advanced conformal coatings. Manufacturers increasingly adopt low VOC coatings as more devices are produced to meet environmental standards.
Rise in Eco-Conscious Consumers
Consumers today are more aware of their product’s environmental impact. The growing emphasis on sustainability has led to a surge in demand for electronics manufactured with environmentally friendly processes, including low VOC conformal coatings.
Technological Advancements in Coating Application
- Spray Coating Technologies:These technologies have evolved to apply coatings more efficiently, reducing waste and VOC emissions during the application process.
- Automated Application Systems:Automation in coating application has become more prevalent, improving precision and minimizing the amount of coating material required.
- Water-Based and UV-Cured Coatings:Water-based coatings and UV-cured alternatives are being developed to further low VOC emissions. These innovations offer faster curing times and enhanced performance while meeting low VOC criteria.
Emerging Markets
Countries in Asia-Pacific, particularly China, India, and South Korea, are witnessing rapid industrialization and growth in the electronics sector. As these regions adopt more stringent environmental regulations, the demand for low VOC conformal coatings is expected to surge.
Focus on R&D
Manufacturers are investing in research and development to create high-performance, low VOC conformal coatings that meet industry demands for durability, flexibility, and environmental safety. New formulations combining performance with sustainability are entering the market, giving manufacturers more choices when protecting their devices.
Benefits of Low VOC Conformal Coatings
Environmental and Health Benefits
- Reduced Air Pollution:By using low VOC coatings, manufacturers can significantly reduce the amount of harmful chemicals released into the atmosphere.
- Improved Indoor Air Quality: Workers applying low VOC coatings benefit from better air quality, reducing exposure to harmful chemicals.
- Improved Performance
- Better Adhesion and Coverage:Many low VOC formulations provide enhanced adhesion and uniform coverage, ensuring better protection for electronic components.
- Longer Durability:Some low VOC coatings offer superior resistance to environmental factors, increasing the lifespan of coated devices.
- Resistance to Harsh Environments:Low VOC coatings are designed to withstand extreme conditions, such as high temperatures and chemical exposure, making them suitable for various applications.
Cost Efficiency
- Reduced Material Waste:Advances in application technologies and formulations mean less coating material is wasted during application.
- Lower Regulatory Costs:Compliance with VOC regulations can be costly if fines or penalties are incurred. Low VOC coatings help manufacturers avoid these costs.
Challenges in the Low VOC Conformal Coating Market
Cost of Development and Adoption
While low VOC coatings offer long-term environmental and health benefits, the upfront costs for research, development, and production can be higher than traditional coatings. Additionally, smaller manufacturers may face challenges switching to low VOC formulations due to equipment and training costs.
Performance Concerns
In some cases, low VOC coatings may not perform as well as their high VOC counterparts in extreme environments, such as those involving high heat or exposure to harsh chemicals. However, continuous advancements in low VOC formulations are addressing these concerns.
Awareness and Education
Many manufacturers and end-users may need to be made aware of the benefits of low VOC conformal coatings or need help understanding how to apply them properly. Education and training programs are essential to ensure the proper use of these products and maximize their benefits.
Limited Availability of Alternatives
While the market for low VOC coatings is growing, some regions may still need more access to these products. Expanding the distribution network and increasing awareness in underserved markets will be critical to the global adoption of low VOC solutions.
Conclusion
The low VOC conformal coating market is at the forefront of a global shift towards more sustainable and environmentally friendly manufacturing practices. With increasing regulations, growing consumer awareness, and technological advancements, the market is poised for significant growth in the coming years. As companies continue to innovate and develop new low VOC formulations, the future of conformal coatings looks brighter, offering enhanced protection for electronic components while reducing environmental impact.
For more about choosing the Top The Expanding Low VOC Conformal Coating Market: Trends, Benefits, and Challenges, you can pay a visit to DeepMaterial at https://www.pottingcompound.com/ for more info.
Recent Posts
- Influence of Encapsulation Thickness on the Heat Dissipation Performance and Electrical Insulation Performance of PCB
- Causes and Avoidance Methods of Bubble Generation in the Potting Process
- Technical Details on Controlling Parameters such as Temperature, Pressure, and Speed in the Potting Process to Ensure Potting Quality
- A Comprehensive Analysis of PCB Pretreatment Before Potting Process: A Crucial Link to Ensure the Performance and Reliability of Electronic Devices
- A Comprehensive Analysis of the Performance Differences of Epoxy Resin, Silicone Rubber and Polyurethane Encapsulation Materials
- How to Select Suitable Potting Materials for PCB According to the Working Environment
- What is PCB Potting
- The Evolution of Smart Watch Assembly Adhesive: A Key Component in Modern Wearable Technology
- Laptop Tablet Assembly Adhesive: The Key to Durable and Reliable Device Construction
- Power Bank Assembly Adhesive: The Essential Component for Building Durable Power Banks