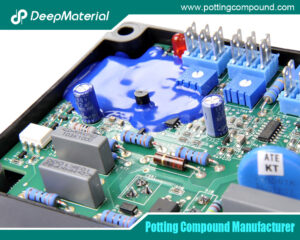
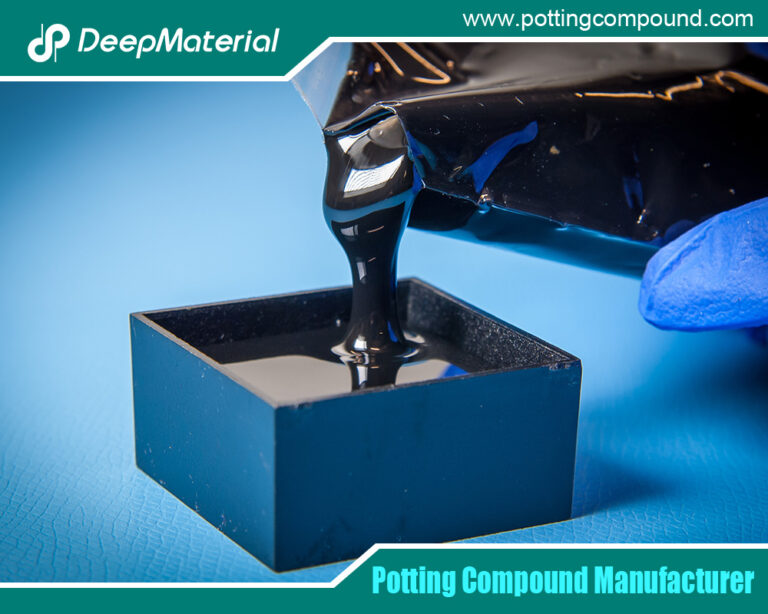
The Potting Process for Electronics: Ensuring Durability and Reliability
- Electronic Potting Material Manufacturer
- November 14, 2024
- circuit board potting, conformal coating for electronics, conformal coating pcb, conformal coating silicone, conformal coating spray, electronic epoxy encapsulant potting compounds, pcb potting, polyurethane potting compound for electronics, potting compound for pcb, potting compound vs epoxy, potting material for electronic components, potting material for electronics, potting pcb, potting process for electronic factory hotsale, potting process for electronic factory OEM, potting process for electronic factory wholesale, potting process for electronic manufacturer, potting process for electronic manufacturer hotsale, potting process for electronic manufacturer wholesale, potting process for electronic supplier, potting process for electronic supplier hotsale, potting process for electronic supplier wholesale, potting process for electronics, what is pcb potting
The Potting Process for Electronics: Ensuring Durability and Reliability
In today’s fast-paced technological landscape, the reliability and performance of electronic devices are paramount. Manufacturers increasingly turn to potting as the demand for robust and durable electronics grows. Potting is a technique that involves encapsulating electronic components in a protective material, providing critical safeguards against environmental challenges such as moisture, dust, and mechanical stress. This blog post will explore the potting process in detail, covering its benefits, materials used, steps involved, best practices, and applications in various industries.
What is Potting?
Potting encases electronic assemblies in a solid or gel-like substance to protect them from external factors. The process involves filling a mold or enclosure with a potting compound, which then hardens around the electronic components. This creates a protective barrier that enhances the device’s reliability, longevity, and performance.
Key Characteristics of Potting
- Encapsulation: Provides a protective layer around the components.
- Adhesion:Bonds well with different surfaces, ensuring durability.
- Thermal Management: Assists in heat dissipation.
- Electrical Insulation: Prevents short circuits and enhances safety.
Benefits of Potting Electronics
The potting process offers a wide range of advantages that make it essential in various applications:
Environmental Protection
- Moisture Resistance:Potting compounds create a barrier that prevents moisture ingress, which can lead to corrosion and failure.
- Dust and Contaminant Shielding:Protects components from dust and other environmental contaminants.
Mechanical Stability
- Vibration Resistance:Reduces the effects of vibrations and shocks, enhancing the durability of electronic devices.
- Impact Resistance:Protects against mechanical stress and impacts, making components more resilient.
Thermal Management
Heat Dissipation: Many potting materials are designed to dissipate heat, helping to maintain optimal operating temperatures for electronic components.
Thermal Insulation: Some materials provide insulation against temperature fluctuations.
Electrical Insulation
- Prevention of Short Circuits:Potting significantly reduces the risk of short circuits by insulating electrical components.
- Reduction of Electromagnetic Interference: Enhances the performance of sensitive electronics by shielding them from EMI.
Extended Lifespan
- Durability: Potting protects components from environmental stressors, significantly extending their operational life.
- Reliability: Enhances the overall reliability of devices, leading to lower maintenance costs and reduced downtime.
Materials Used in Potting
Choosing the suitable potting material is crucial to achieving the desired performance characteristics. The most commonly used potting materials include:
Epoxy Resins
Properties:
- High strength and durability.
- Excellent adhesion to various substrates.
- Good resistance to chemicals and heat.
Applications:
- Widely used in automotive, aerospace, and industrial applications.
Polyurethane
Properties:
- Flexible and impact-resistant.
- Good thermal stability and moisture resistance.
Applications
- Ideal for applications requiring flexibility and toughness.
Silicone
Properties:
- Highly flexible and resistant to extreme temperatures.
- Excellent electrical insulation properties.
Applications
- Commonly used in medical devices and outdoor electronics.
Acrylics
Properties:
- Fast curing and low viscosity.
- Good transparency and UV resistance.
Applications
- Often used in applications where clarity is essential.
The Potting Process
The potting process typically involves several key steps, each critical to achieving the desired results. Here’s a detailed breakdown:
Preparation
- Cleaning: Ensure the components are free from dirt, grease, and moisture. Solvents or cleaning agents suitable for the materials being used can be used.
- Drying: Components must be dehydrated before potting to prevent moisture entrapment, which can compromise the integrity of the potting material.
Selecting the Potting Compound
- Material Choice: Select a potting compound based on the application requirements, including thermal conductivity, flexibility, and chemical resistance.
- Testing: Conduct tests to verify the chosen compound’s performance characteristics.
Mixing the Potting Material
- Mixing Ratio:Follow the manufacturer’s instructions for mixing ratios. Precise measurements are crucial for achieving the desired properties of the cured potting material.
- Thorough Mixing:Ensure the compound is mixed thoroughly to achieve a homogeneous mixture, avoiding any inconsistencies that could affect performance.
Pouring the Potting Material
- Careful Application: Carefully pour the mixed compound into the mold or around the components. Pouring should be done slowly to minimize the risk of trapping air bubbles.
- Air Bubble Management: Use techniques such as vacuum degassing to eliminate air bubbles from the mixture before pouring, ensuring a smooth application.
Curing
- Curing Time: The potting material can cure according to the manufacturer’s specifications. Curing times may vary depending on the type of material and environmental conditions.
- Environmental Conditions:Maintain appropriate temperature and humidity levels during curing to ensure optimal results.
Quality Inspection
- Visual Inspection:After curing, inspect the finished product for defects such as air pockets, cracks, or uneven surfaces.
- Functional Testing: Conduct functional tests to ensure that the potting has not compromised the performance of the electronic components.
Best Practices for Potting Electronics
To achieve the best results in the potting process, consider the following best practices:
Conduct Preliminary Testing
- Prototype Testing: Small-scale tests identify potential issues with the potting process or materials before mass production.
Maintain Temperature Control
- Optimal Conditions: To ensure consistent results, maintain optimal temperatures during mixing and curing. This may require temperature-controlled environments.
Ensure Proper Ventilation
- Fume Control:Ensure proper ventilation when working with chemical compounds to avoid inhalation of potentially harmful fumes. Use fume hoods or personal protective equipment (PPE) as necessary.
Utilize Release Agents
- Mold Ease: If necessary, apply release agents to facilitate easy removal of components from molds after the potting process.
Follow Safety Guidelines
- Chemical Safety: Always adhere to safety protocols when handling chemicals. Use appropriate PPE, including gloves and goggles, and be aware of the safety data sheets (SDS) for the materials used.
Applications of Potting in Various Industries
The potting process finds applications across diverse industries, reflecting its versatility and importance:
Automotive Industry
- Electronic Control Units (ECUs): Potting protects sensitive ECUs from moisture, heat, and vibrations, enhancing their longevity and performance.
- Sensors:Potting encapsulates sensors, shielding them from environmental contaminants.
Aerospace and Defense
- Avionics Systems:Potting protects avionics components from extreme temperatures and mechanical stress.
- Communication Equipment:Potting is critical for ensuring the reliability of communication systems used in aerospace applications.
Telecommunications
- Circuit Boards: Potting protects circuit boards in telecommunication devices, ensuring their performance in various environments.
- Optical Fibers:Potting compounds can protect optical fibers from moisture and mechanical damage.
Consumer Electronics
- Mobile Devices:Potting helps protect smartphones and tablets from moisture and impacts.
- Home Appliances:Encapsulation is used in various home appliances to enhance durability.
Medical Devices
- Patient Monitoring Equipment: Potting protects sensitive electronics in patient monitoring systems from contamination and moisture.
- Implantable Devices: Potting is crucial for ensuring the reliability of electronic components in implantable medical devices.
Challenges and Considerations
While the potting process offers numerous benefits, it has challenges. Here are some considerations to keep in mind:
Material Compatibility
- Substrate Interaction:To prevent adhesion issues or chemical reactions, ensure the potting compound is compatible with the substrates used.
Potting Compound Selection
- Performance Requirements: When selecting a potting material, consider the application’s performance requirements carefully. Therm conductivity, viscosity, and cure time should be evaluated.
Curing Challenges
- Environmental Variability: Changes in temperature and humidity can affect curing times and material properties. Consistent ecological conditions are crucial for optimal results.
Cost Considerations
- Material Costs:High-performance potting materials may come at a premium, impacting the overall cost of production. Weigh the benefits against costs when making material selections.
Conclusion
The potting process is an essential technique in the electronics industry, offering significant advantages in terms of durability, reliability, and performance. By understanding the materials, benefits, and best practices involved in potting, manufacturers can enhance the longevity of their products and ensure optimal functionality even in challenging environments. As technology advances, the importance of effective potting will only grow, making it a crucial component in the design and manufacturing of electronic devices.
For more about choosing the potting process for electronics: ensuring durability and reliability, you can pay a visit to DeepMaterial at https://www.pottingcompound.com/ for more info.
Recent Posts
- Influence of Encapsulation Thickness on the Heat Dissipation Performance and Electrical Insulation Performance of PCB
- Causes and Avoidance Methods of Bubble Generation in the Potting Process
- Technical Details on Controlling Parameters such as Temperature, Pressure, and Speed in the Potting Process to Ensure Potting Quality
- A Comprehensive Analysis of PCB Pretreatment Before Potting Process: A Crucial Link to Ensure the Performance and Reliability of Electronic Devices
- A Comprehensive Analysis of the Performance Differences of Epoxy Resin, Silicone Rubber and Polyurethane Encapsulation Materials
- How to Select Suitable Potting Materials for PCB According to the Working Environment
- What is PCB Potting
- The Evolution of Smart Watch Assembly Adhesive: A Key Component in Modern Wearable Technology
- Laptop Tablet Assembly Adhesive: The Key to Durable and Reliable Device Construction
- Power Bank Assembly Adhesive: The Essential Component for Building Durable Power Banks